FLYLINE MoCo User manual

Copyright © 2017 PhotoShip One LLC - www.PhotoShipOne.com2
© 2017 PhotoShip One, LLC. All rights reserved.
PhotoShip One, LLC!
Mesa, AZ 85209!
USA
www.photoshipone.com
!
Except as expressly provided herein, no part of this guide may be
reproduced, transmitted, disseminated, downloaded or stored in
any storage medium, for any purpose without the express written
permission of PhotoShip One. PhotoShip One grants permissions to
download a single copy of this guide onto an electronic storage
medium to be viewed for personal use, provided that the complete
text of this copyright notice is retained. Unauthorized commercial
distribution of this manual or any revision hereto is strictly
prohibited.
IN NO EVENT, SHALL PHOTOSHIP ONE, LLC BE LIABLE FOR ANY
INCIDENTAL, SPECIAL, INDIRECT OR CONSEQUENTIAL DAMAGES,
WHETHER RESULTING FROM THE USE, MISUSE OR INABILITY TO
USE THE PRODUCT OR FROM DEFECTS IN THE PRODUCT.

Copyright © 2017 PhotoShip One LLC - www.PhotoShipOne.com3
MANUAL REVISION HISTORY
REVISION
DATE
COMMENTS
DOWNLOAD LINK
1
4/15/2017
Initial Release
X
2
05/23/2017
• Firmware version 1.1 changes
• Added Manual Revision History & Firmware Changelog
• Added DX6 switch location graphic
• Revised Ping-Pong Mode Operation
• Added AR8000 rx setup information
X
FIRMWARE CHANGELOG
VERSION
DATE
COMMENTS
1.0
4/15/2017
Initial Release
1.1
05/23/2017
• Remote entry/exit of Ping-Pong Mode
• Ping-Pong Mode Gain adjustment set to 1/2 of gain pot value
• Throttle values to accommodate control transmitters end-point value at 100%.
PWM scaling changed from 1000us/2000us to 1100us/1900us
• Serial Protocol Added
• 2 sec. Startup Delay added to prevent motor from spinning on power-up
• Fail Safe sensing added for AR610 rx
• LED light bug fixes

Copyright © 2017 PhotoShip One LLC - www.PhotoShipOne.com4
The MoCo Module allows the FlyLine trolley to ‘know’ its position on the rope. This is useful for
automatic control of the system.
The user can set endpoints at each end of the rope that the trolley will not cross when properly
configured.
The MoCo module also has an automatic ‘ping-pong’ mode which will automatically and
repeatedly drive the trolley between two user set end points at a user set speed. This is perfect
for live event coverage at concerts or festivals where you want continuous motion of the trolley
and only want a single operator to control the camera gimbal.
It is extremely important to follow these instructions carefully and
conduct operation in accordance with all local safety regulations and
best practices.
You MUST read thoroughly the Safety Section at the end of this
instruction manual before operation. If you are unsure of any part of
the operation of the MoCo, do NOT operate the system. Contact us for
assistance.
Improper operation of the system can result in damage to property
and/or injury/death to persons.

Copyright © 2017 PhotoShip One LLC - www.PhotoShipOne.com5
TABLE OF CONTENTS
1. INSTALLATION
1.1 Mount Sensor Disc to Outrigger Wheel
1.2 Mount Sensor to FlyLine Frame
1.3 Mount MoCo Module to FlyLine Frame
1.4 Connect RC Control Cables
1.5 Connect & Route Sensor Cable
2. MOTOR CONTROLLER SETUP
2.1 DIP Switch Assignments
2.2 Current Limiter Adjustment
2.3 Data Cable Connection
2.4 Connections Diagram AR610 rx
2.5 Connections Diagram AR8000 rx
2.6 Motor Wire Connections
3. SPEKTRUM CONTROLLER SETUP
3.1 Servo Setup > Reverse
3.2 Servo Setup > Travel
3.3 D/R and Expo
3.4 Switch Assign
3.5 Switch Assign Aux 2 (AR8000 rx only)
"
4. MODE SELECTION
4.1 End Point Mode
4.2 Ping-Pong Mode
4.3 Sensor Test Mode
"
5. OPERATION
5.1 Manual Control/Auto End Point Mode
5.2 Gain Calibration
5.3 Ping-Pong Mode

Copyright © 2017 PhotoShip One LLC - www.PhotoShipOne.com6
1. MOCO MODULE INSTALLATION
1.1 Mount Sensor Disc to Front Outrigger Wheel!
If looking at the FlyLine trolley with the motor controller and end of the motor facing you, the front of the
trolley is to your right.
Front
Attach the sensor disc to the outrigger wheel. Place the
spacer in between the wheel and the disc. Use 3x22 screws. !
!
We recommend using thread locking compound like Loctite.
1.2 Mount Sensor to FlyLine Frame!
The sensor mounts to the inside of the right side frame of the
FlyLine next to the front outrigger wheel. Use M3x10 screws.
You will notice there are two M3 tapped holes in the FlyLine frame
next to the wheel. The sensor has four hole selections that can be
used.
The hole selections used with the sensor depend which of the four
axle hole selections are used on the frame.
If the axle is in the lowest hole position on the frame, then use
top holes in the sensor. Conversely, if the axle is placed in the top
Sensor
Any other axle positions will correspond to the other holes in the sensor respectively. The idea is to keep the
sensor aligned with the axle of the outrigger wheel so that the sensor is properly aligned with the sensor disc
on the wheel.
The sensor cable should NOT be bent or flexed sharply. Bending or flexing
the cable near the ends can damage the connections inside the sensor or at
the connector. Handle the sensor cable gently.

Copyright © 2017 PhotoShip One LLC - www.PhotoShipOne.com7
1. MOCO MODULE INSTALLATION
1.3 Mount MoCo Module to FlyLine Frame
The MoCo module mounts to the right FlyLine frame with double sided tape. Place the module in the
position shown.
1.4 Connect RC Control Cables
Connect the RC control cables from the Spektrum AR610 to the left side of the MoCo as follows:
Position 1 on MoCo to Elev on receiver!
Position 2 on MoCo to Gear on receiver!
Position 3 on MoCo to Aux 1 on receiver!
Position 4 on MoCo to Thro on receiver
WHITE wires of the cables should
be oriented to the top of the MoCo.!
!
BLACK wires should be at the bottom. !
1.5 Connect & Route Sensor Cable
Connect the wheel sensor cable to the connector on the right side of the MoCo unit. Route the cable along
the trolley frame and secure with cable ties. The cable will need to route from the outside of the frame to
inside of the frame at the sensor. The cable can be flexed smoothly. Do NOT sharply bend or flex the cable!!
!
Failure to secure the cable properly could result in the cable being pulled from the sensor or MoCo
which could result in a dangerous crash. Be sure the cable is properly secured!
AR610 connections

Copyright © 2017 PhotoShip One LLC - www.PhotoShipOne.com8
5
2. MOTOR CONTROLLER SETUP
2.1 - DIP SWITCH ASSIGNMENTS!
In order for the MoCo unit to operate properly it is important
that the motor controller DIP switches be configured.
The DIP switches on the motor controller circuit board MUST
be configured with switches 1 & 2 in the ‘OFF’ position and
switches 3, 4, 5, 6 in the ‘ON’ position as shown below.
Look for the ‘ON’ printed on the DIP switch block above
switches 1 & 2. Switches flipped towards this direction are
‘ON’.
2.2 - CURRENT LIMITER ADJUSTMENT!
Locate the current limiter adjustment potentiometer on the
motor controller. It is blue with a yellow adjustment screw in
the middle.
Set the adjustment screw to 50% by rotating it so the arrow
portion of the screw points to the ’50’ on the motor controller
circuit board.
2.3 - Data Cable Connection!
Install the supplied Data Cable to the terminals on the motor controller marked 0V, 5V,
S1. !
!
Black wire connects to 0V!
Red wire connects to 5V!
White wire connects to S1
Connect the plug end of the data cable to Position 5 on the MoCo unit with the WHITE
signal wire on the top position, BLACK at the bottom.

Copyright © 2017 PhotoShip One LLC - www.PhotoShipOne.com9
2. MOTOR CONTROLLER SETUP
2.4 - Connections Diagram for Spektrum AR610!
When all connections are made the system should be as follows:
Verify RC controls and data cables are oriented correctly with WHITE, RED, BLACK wires in proper position.
S+ -

Copyright © 2017 PhotoShip One LLC - www.PhotoShipOne.com10
2. MOTOR CONTROLLER SETUP
2.5 - Connections Diagram for Spektrum AR8000/AR8010T!
When all connections are made the system should be as follows:
Verify RC controls and data cables are oriented correctly with WHITE, RED, BLACK wires in proper position.
S+ -

Copyright © 2017 PhotoShip One LLC - www.PhotoShipOne.com11
2. MOTOR CONTROLLER SETUP
2.6 - Motor Wire Connections Diagram!
You may NOT ignore this page if you have ordered the MoCo module separately from a FlyLine and you are
installing it yourself.!
You MAY ignore this page if you have received a prebuilt FlyLine system from PhotoShip One with the MoCo
already installed as we have already completed this verification.!
Depending on the motor you have please set the motor wire +/- as shown below. If you are unsure which
motor you have you can determine by looking at the back of the motor opposite the shaft.
If the motor has four black plastic caps on a silver housing, the motor is the A28-150.
If the motor does not have plastic caps on a silver housing and the end is black, the motor is the E30-150
FAILURE TO VERIFY THESE CONNECTIONS CAN RESULT IN THE FLYLINE TROLLEY
GOING FULL SPEED IN AN UNCONTROLLED ‘RUNAWAY’. THIS IS EXTREMELY
CRITICAL STEP. DO NOT IGNORE IT!

Copyright © 2017 PhotoShip One LLC - www.PhotoShipOne.com12
3. SPEKTRUM CONTROLLER SETUP
We use exclusively Spektrum RC controllers. The instructions below are for a DX6 but other Spektrum
systems like the DX7, DX8, DX9 will be similar or exactly the same. We have made model files available for
Spektrum DX6, DX7S, DX8 (silver & black), and DX9 here:
http://www.photoshipone.com/documentation/Spektrum_MoCo.zip
Other RC systems (Futaba, JR, etc) have not been tested and may not work properly with the MoCo
module.
If you purchased your FLyLine system from us with the Motion Control module installed, disregard this
Section.
3.1 - Servo Setup -> Reverse!
Enter the ‘Servo Setup’ menu on the Spektrum. (refer to Spektrum
manual on how to enter this menu).
Then, scroll to the ‘Reverse’ menu.
Verify all channels are in the normal and not reversed setting.
3.2 - Servo Setup -> Travel!
From the ‘Servo Setup’ menu, scroll to the ‘Travel’ menu.
Set all channels to 100/100 if they are not already at that value.
3.3 - D/R and Expo!
Enter the ‘D/R and Expo’ menu.
Set the dual rate for Elevator channel as follows:
Position 0 - Dual Rate: 100% 100%!
Expo: 45% 45%
Position 1 - Dual Rate: 50% 50%!
Expo: 25% 25%
Assign the switch to whatever switch you prefer. We recommend a
two position switch. See Spektrum manual for assigning switches.
NOTE - The values above are settings to start with. You may adjust
them to suit your preference for control response and feel.

Copyright © 2017 PhotoShip One LLC - www.PhotoShipOne.com13
3. SPEKTRUM CONTROLLER SETUP
3.4 - Switch Assign Aux 1 Channel to Button!
We recommend the Aux 1 channel (used for setting end points) be
assigned to the ‘Bind’ button on the Spektrum controller. On the DX 6
this button is defined as button ‘I’.
Go to System Menu > Channel Assign, press roller button.
Select NEXT under RX Port Assignments
Select Aux 1 under Channel Input Config menu and change to button
‘I’. Button ‘I’ is the Bind button on the top left of the controller.
3.5 - AR8000 RECEIVERS ONLY !
Assign Aux 2 Channel to Button ‘A’!
If you are using an AR8000 receiver you must be also using a
Spektrum DX8 or DX9 and assign the Aux 2 channel to switch ‘A’.
In the Switch Assign menu you will need to first set Gear to something
other than ‘A’ so that Aux 2 can be set to ‘A’. In the example shown
here, ‘E’ was used.
Now, Aux 2 can be set to ‘A’.
Important note for AR8000 users! - You MUST bind your AR8000
receiver to the transmitter in Fail Safe mode with the throttle stick set
to low position, and Switch ‘A’ in position 1. Failure to do so can result
in a crashed trolley if the system were to go into Fail Safe. See
AR8000 manual for details on how to bind in Fail Safe mode.

Copyright © 2017 PhotoShip One LLC - www.PhotoShipOne.com14
4. MODE SELECTION
There are three operating modes with the MoCo Module. This section explains how to enter the modes.
For instructions on operation of the modes see Section 5.!
1. Manual Control/Auto End Point - With this mode the user sets end points on the rope where they
want them while in manual control. Then when Auto End Point is toggled the FlyLine trolley will not
exceed the endpoints once the gain setting is correct and End Point mode toggled. LED color GREEN.!
2. Ping-Pong Mode - With this mode the user sets end points on the rope where they want them and
when activated the Ping-Pong mode will drive the FlyLine trolley automatically between the two points
continuously at a speed set by the user. The trolley will “ping-pong” until the battery dies or until the
user deactivates the mode. LED color BLUE.
3. Sensor Test Mode - This mode is recommended to be used only once per session/rigging. It allows
the user to verify the wheel sensor is collecting pulses from the wheel sensor disc. LED color RED.
4.1 - Manual Control/Auto End Point Mode!
The MoCo defaults to Manual/End Point Mode each time it is powered up.
The LED indicator will illuminate GREEN when Manual Control/Auto End Point
Mode is entered.
Any end points stored from a previous session are erased upon power up.
Thus, it is required that upon powering up the unit each time, new end points
must be set.
For information on setting end points and operating in Manual Control/Auto End Point Mode, please refer
to section 5.2.
4.2 - Ping-Pong Mode!
To enter Ping-Pong Mode there are two methods. Manually & Remotely:
MANUALLY
1. Set the throttle stick (left stick on the Spektrum) all the way to the down/low
position.
2. Set the GEAR Switch to the OFF position.
3. Push and hold the left ‘Circle’ button on the MoCo Module for 2 seconds.
REMOTELY
1. Set the throttle stick (left stick on the Spektrum) all the way to the down/low position.
2. Set the GEAR Switch to the ON position.
3. Push and hold the AUX button on the Spektrum for 2 seconds.
The LED indicator will illuminate BLUE and the beeper will beep two short tones when Ping-Pong Mode is
entered. Any end points stored from a previous session are erased upon power up. Thus, it is required
that upon powering up the unit each time, new end points must be set.
For information on setting end points and operating in End Point Mode, please refer to section 5.2.!
To exit Ping-Pong mode push and hold the left ‘Circle’ button on the MoCo Module or AUX button on
Spektrum for 2 seconds. The LED indicator will illuminate GREEN and you will hear one short tone from
beeper letting you know you are back in Manual Control/Auto End Point Mode.

Copyright © 2017 PhotoShip One LLC - www.PhotoShipOne.com15
4. MODE SELECTION
4.3 - Sensor Test Mode!
To Enter Sensor Test Mode:
Simultaneously push and hold the left ‘Circle’ button and the right ‘Square’
button on the MoCo Module for 2 seconds.
The LED indicator will illuminate RED and you will hear three tones from
beeper when Sensor Test mode is entered.
For information on conducting sensor test please refer to section 5.4!
To exit Sensor Test mode simultaneously push and hold the left ‘Circle’ button and the right ‘Square’
button on the MoCo Module for 2 seconds. The LED indicator will illuminate GREEN and you will hear one
tone from the beeper letting you know you are in Manual Control/Auto End Point Mode.

Copyright © 2017 PhotoShip One LLC - www.PhotoShipOne.com16
5. OPERATION
5.1 - Manual Control/Auto End Point Mode
The MoCo Module is in full manual control when the ‘Gear’
switch on the Spektrum controller is in the ‘Off’ position. The
LED indicator will be solid GREEN.
When in manual control the operator has complete manual control. It is possible to drive the
trolley and crash into attach points at either end of the rope! Be VERY careful when operating in
manual control.
When in manual control the ‘Aux’ and ‘Gear’ switches work as follows:
Gear switch is a two position switch. In the ‘OFF’ position the trolley is operated in Manual Control. With
the Gear switch in the ‘ON’ position the trolley is operated in Auto End Point mode.
The Aux 1 switch is a momentary push button (Bind button). When the Gear switch is in the ‘OFF’ position
and the Aux 1 button is pushed the first end point is set where the trolley is on the rope. When the Aux 1
button is pushed a second time the second end point is set where the trolley is on the rope.
Thus, to set end points for Auto End Point mode, do the following:
1. With the Gear switch ‘OFF’ drive the trolley in Manual Control mode to a desired end point.
2. Press the Aux 1 (bind) button. You will hear one long tone from the beeper indicating that position on
the rope has been set as end point 1.
3. Drive the trolley to the desired end point position at the other end of the rope.
4. Press the Aux 1 (bind) button. You will hear two long tones from the beeper indicating that position on
the rope has been set as end point 2.
!
At this point the end points have been stored and the system is ready for Auto End Point mode.!
!
To activate Auto End Point Mode, flip the Gear switch to the ‘ON’ position.
Once Auto End Point Mode is activated the system is ready for Gain Calibration. See Section 5.2.
ONLY AFTER GAIN CALIBRATION CAN YOU USE AUTO END POINT MODE!
!
AUX 1
GEAR (AR610)!
AUX 2 (AR8000)
OFF (0)
ON (1)

Copyright © 2017 PhotoShip One LLC - www.PhotoShipOne.com17
5. OPERATION
5.2 - Gain Calibration!
After the end points have been set as described in Section 5.1, the
next step is to adjust the gain calibration.
Gain calibration adjusts the brake start point. If the FlyLine trolley is
loaded down with heavy camera and equipment and/or would be
traveling at a fast speed it would require an earlier brake start point
than lightly loaded and/or slower speed. Thus, you MUST calibrate the
Gain setting on the MoCo unit every time the system is rigged or the
weight/speed operating profile changes. !
!
The Gain is adjusted via a potentiometer on the MoCo module. The Gain potentiometer is located near
the upper right corner of the module.
Adjustment is done with a small flat blade screw driver.
Gain has settings of fully counterclockwise of a value of 1, through fully clockwise to a value of 10.
To know which number value the Gain is currently set to, simply push the right Square button on the
MoCo module for 1/2 second then release. You will hear a series of tones from the beeper that denote
what value the gain is set. 1 beep = Gain Value 1, 2 beeps = Gain Value 2, 3 beeps = Gain value 3, and
so on to 10.
Rotating counterclockwise towards 1 reduces the Gain. Reducing Gain has the effect of setting the brake
start point closer to the end point.!
Rotating clockwise towards 10 increases the Gain. Increasing Gain has the effect of setting the brake
Press and release,
listen for number of beeps
to determine Gain value
A system with low mass and/
or low speed operation will
require a LOW Gain value
GAIN VALUE
1
2
3
4
5
6
6
7
8
9
10
A system with high mass and/
or high speed operation will
require a HIGH Gain value

Copyright © 2017 PhotoShip One LLC - www.PhotoShipOne.com18
5. OPERATION
5.2 - Gain Calibration (continued)!
The Gain calibration procedure should be conducted as follows:
1. Set the Gain value fully clockwise to 10. Take care not to over rotate the Gain adjustment. Applying
too much force with the screwdriver can damage the adjustment potentiometer.
2. Verify the Gain value is set to 10 by pressing and releasing the right ‘Square’ button on the MoCo
module and listening for the number of tones from the beeper. There will be 10 tones if the Gain value
is set to 10.
3. Be sure end points have been set as described in Section 5.1 and that Auto End Point Mode is active!!
4. Drive the trolley at a medium speed towards an end point. The trolley will begin to decelerate to a stop
before reaching the end point.!
If the rate of deceleration is very slow and the system takes a long period of time to reach a stop, you
may increase the Gain value by one increment and try the test again. !
!
Subsequent tests can be conducted at a faster speed, but be sure the first test is no more than a medium
speed since until the Gain value is set, the risk of crash is still present.
Repeat the test a couple of times, increasing the Gain value each time so that at fast speed the system
will safely bring the trolley to a smooth stop before reaching an end point.
Once the Gain value is set the system is ready for operation in Auto End Stop or Ping-Pong Mode.
NOTE - Any changes to the mass of the system (adding a heavier lens for example) would require a
recalibration of the Gain value.
NOTE - If the rope rigging/installation is sloped at an angle, conduct all Gain calibration tests with the
trolley system driving DOWNHILL.
It is important to understand how end points work. The location of end point 1 and end point 2 are NOT the
locations where the trolley will stop, but rather the locations where the trolley should not exceed.
In normal operation, with the Gain value adjusted correctly, the trolley will start braking before the Safety Zone
and come to a stop INSIDE the Safety Zone BEFORE reaching an end point. The Safety Zone size and brake
start points are dependent on the Gain value.
ALWAYS set end points at least 3 meters from the last rigging point! NEVER operate a system with less
than 3 meters Danger Zone. Ever!

Copyright © 2017 PhotoShip One LLC - www.PhotoShipOne.com19
5. OPERATION
5.3 - Ping-Pong Mode
Ping-Pong mode is useful for live events and where only a single operator is available and that operator must
focus attention to operating the camera gimbal. With Ping-Pong mode the operator let Ping-Pong mode
automatically drive the trolley continuously back and forth at a desired speed.
To use Ping-Pong mode:
1. Set end points as described in Section 5.1
2. Calibrate Gain value as described in Section 5.2
3. Enter Ping-Pong mode as described in Section 4.2
4. Set the throttle stick (left stick on the Spektrum) to the desired speed
5. Activate Ping-Pong mode by flipping the Gear switch to the ‘ON’ position
To cease operating Ping-Pong mode:
1. Set the throttle stick to the low throttle position
2. Flip the Gear switch to the ‘OFF’ position
If the trolley stops at an end but will not begin to move back to the other end, the gain value is set too high.
Reduce the gain value by one and try again.
NOTE - Anytime the Gear switch is in the ‘OFF’ position, the MoCo Module is in Manual Control mode!
NOTE - Over distance traveled the end points may drift slightly. Average drift is approximately 25mm per 1
kilometer traveled. After traveling several kilometers total, check that the trolley does travel into the Danger
Zone.
5.4 - Sensor Test Mode
Sensor test mode is used to verify the sensor is sensing the magnets on the sensor disc mounted on the front
outrigger wheel.
To use Sensor Test mode:
1. Install the front outrigger wheel onto the trolley. Tighten the axle nut only enough to make contact. Do not
over tighten.
2. Enter Sensor Test mode as described in Section 4.3
3. Slowly rotate the front outrigger wheel. You will see the LED alternate between blue and green each time a
magnet passes the sensor. The beeper will beep each time a magnet passes the sensor.
4. Rotate the outrigger wheel one revolution and count the number of beeps you hear. You should hear 24
beeps with one full revolution.
Sensor test mode should be done each time the FlyLine is rigged on a rope to verify the sensor, sensor disc,
and sensor cable are properly functioning.

Copyright © 2017 PhotoShip One LLC - www.PhotoShipOne.com20
6. SAFETY
While we’ve done a great deal of work designing the MoCo Module and tested the system extensively, it
is impossible for us to test every combination of parameters. !
As such, we urge you to take extra care and precautions when operating the FlyLine with the MoCo. !
!
It is important that the FlyLine trolley be attached to a secondary safety rope rigged above the primary
line. A zipline trolley and tether are perfect for this purpose.
Before operating the system please verify the motor wire connections at the motor controller as
specified in Section 2.5. Failure to verify the connections can result in a runaway scenario.!
!
The effectiveness of the end point braking with MoCo is dependent upon proper Gain calibration.
DO NOT operate the FlyLine until a thorough Gain calibration procedure has been completed! Failure to
complete a proper Gain calibration can result in a trolley crash and damage/injury to property and
persons.
Be sure your Spektrum controller will set the channels as follows in Fail Safe Mode (See spektrum
manual for Fail Safe setup):
Elev- NEUTRAL!
Gear - ON
Aux1- OFF
Thro - LOW
With these settings stored in Fail Safe of the Spektrum, a loss of signal would force the MoCo unit into
Auto End Point or Ping-Pong mode with motor power set to off or very slow.
Do NOT operate the trolley if the motor temperature is in excess of 165F (74C).
Use Locktite thread locker on all pulley set screws. If a set screw works loose, all control can be lost!
Operation in wet or icy conditions will affect traction severely. Take extra precautions and watch speed
in these conditions.
It is recommended to reset the end points after the system has travelled a total distance of 5 kilometers
due to the possibility for a slight drift of end points. It is normal for the system to drift the end points by
an average of 25mm per 1 kilometer traveled. !
Table of contents
Popular Controllers manuals by other brands
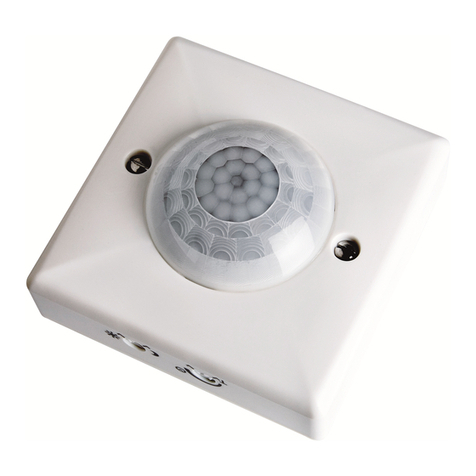
Timeguard
Timeguard PDSM1500 Installation & operating instructions
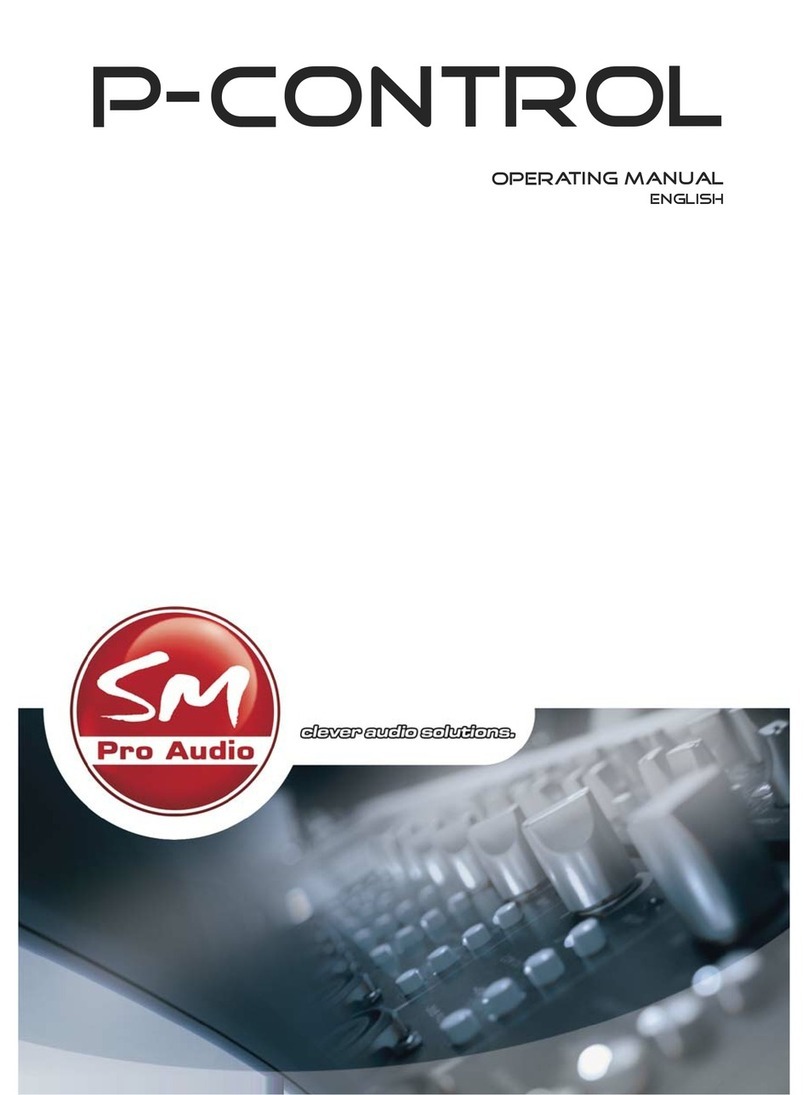
SM Pro Audio
SM Pro Audio P-Control operating manual
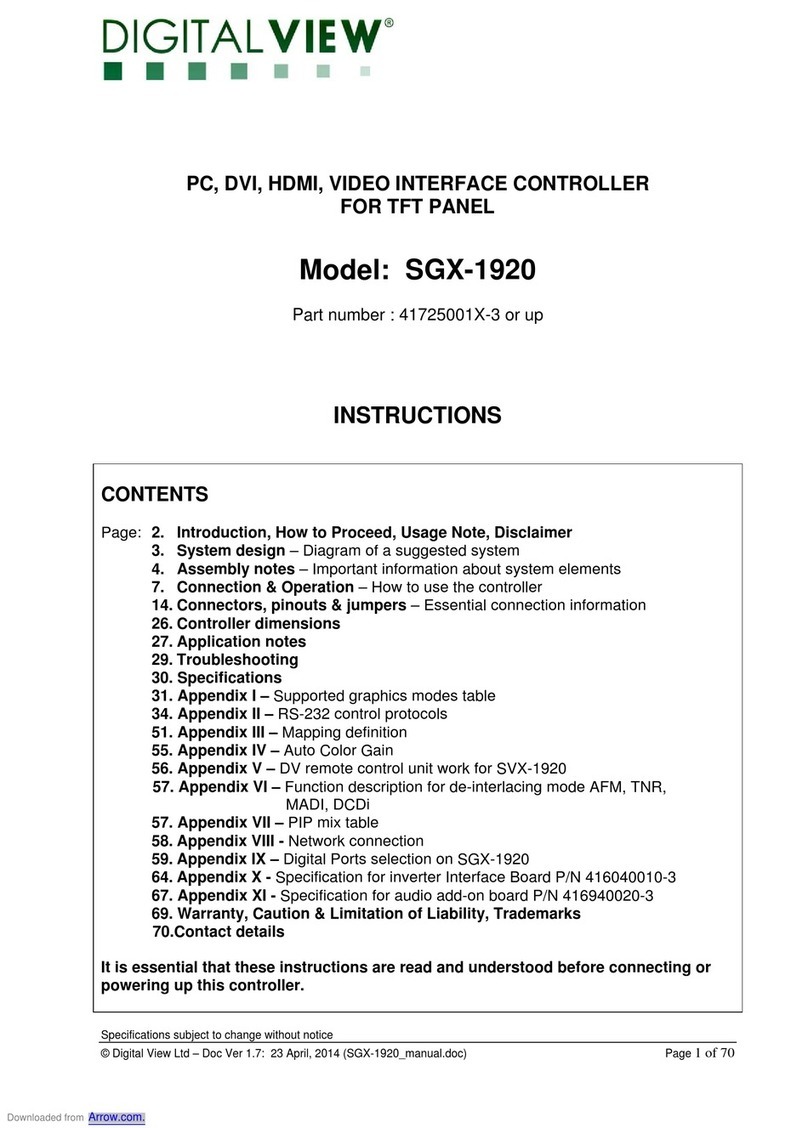
digitalview
digitalview SGX-1920 instructions
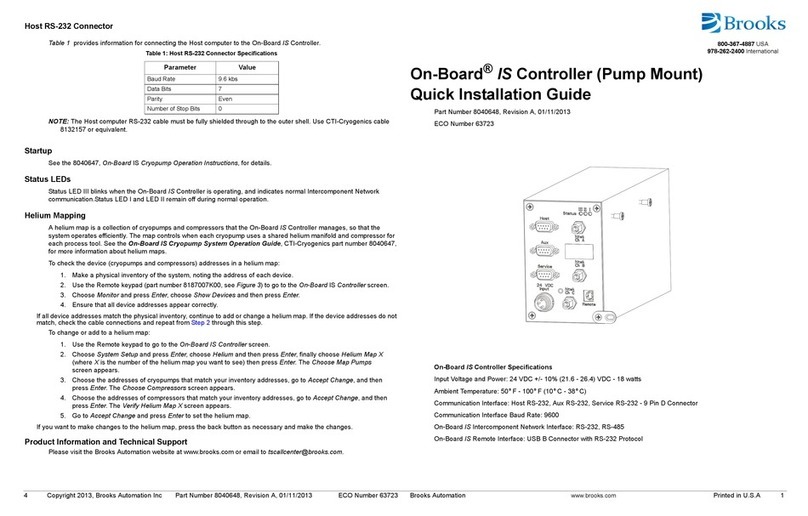
Brooks
Brooks On-Board IS Quick installation guide
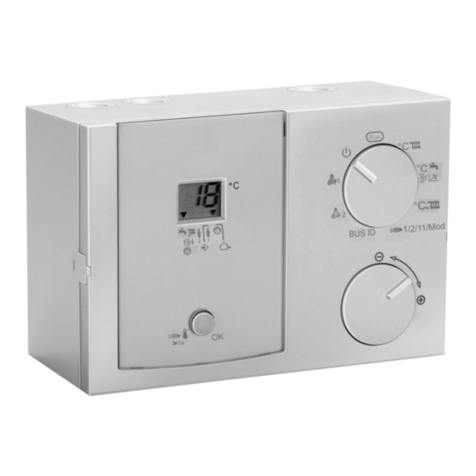
Krom Schroder
Krom Schroder Lago Basic 0201 R V1 Operating and installation instructions
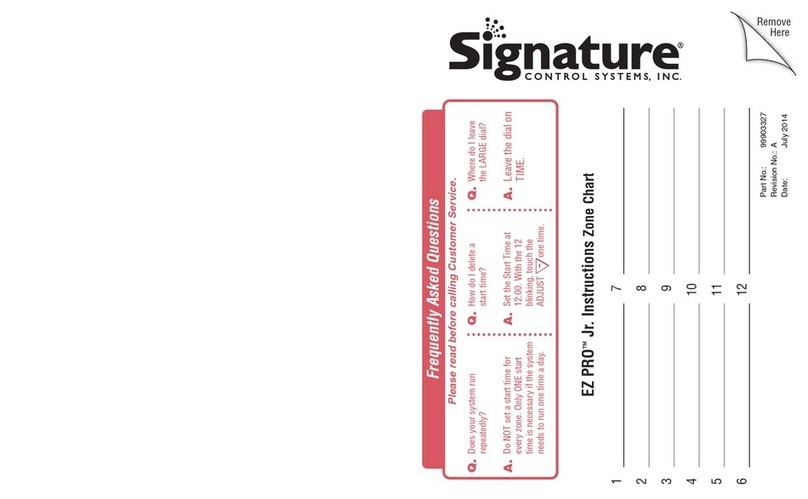
Signature Control Systems
Signature Control Systems EZ Pro Jr. 8300 Series Installation and programming guide