FOAMICO SATELLITE SYSTEM PSU 0127 User manual

1 PSU 0127- 7003313-16-19-20 15-04-2019
Operation Manual
Foamico SATELLITE SYSTEM PSU 0127
PSU 0127-4 (7003313)
PSU 0127-7 (7003316)
PSU 0127-6 (7003319)
PSU 0127-9 (7003320)

2 PSU 0127- 7003313-16-19-20 15-04-2019
Table of contents
1Introduction 3
Condition of liability 3
Guarantee conditions 3
Protection against frost 3
Safekeeping 3
Declaration of conformity 4
Safety 4
Precautionary measures 4
Appropriate utilization 4
2Installation 4
SAFETY INSTRUCTIONS FOR MOUNTING AND INSTALLATION 4
Location and Mounting 4
Water Supply 5
Air supply 5
Supply of Detergent and sanitizer 5
3Operation 6
Rinsing 6
Foaming chemical 1 6
Foaming chemical 2 6
Foaming chemical 3 only (7003311-12-14-15-17-18) 7
Stop procedure 7
4Maintenance 10
RINSING HOSE 10
NOOZLES 10
LOW PRESSURE VALVES / GUNS 10
Couplings. 10
BALL VALVES 10
NON-RETURN VALVES / CHECK VALVES 10
SUCTION FILTER / CHEMICAL HOSE 11
5TECHNICAL DATA 11
6Spare parts Satellite system 12
Spare parts 12
Pipe system –rinse circuit. Part number: 1002303 -1002280. 15
Pipe system –rinse circuit. Part number: 1001883 -1001886. 17
Ersatzteile Sprühschaum kreis Teilnummer 1001787-1001793 18
Flow diagram PSU 0127-1 19
Flow diagram PSU 0127-2 19
Flow diagram PSU 0127-3 20
Flow diagram PSU 0127-4 and 7 20
Flow diagram PSU 0127-5 and 8 21
Flow diagram PSU 0127-6 and 9 21
7Name plate 23
8Decleration of conformity 24

3 PSU 0127- 7003313-16-19-20 15-04-2019
1 Introduction
FOAMICO congratulates you with your new FOAMICO Cleaning system. The PSU 0127-1-9 series is
developed to be used for professional cleaning purpose.
The system is manufactured mainly of high-grade stainless steel. It is designed to meet today’s high hygiene
standards
Attention! To use and operate the system this manual must be read carefully.
Condition of liability
The responsibility for the treatment and operation in an appropriate manner rests with each individual user.
Thus it is of great importance that this manual is available to the sanitary employee at any time.
Guarantee conditions
For a period of 12 months from the date of delivery your dealer warrants for parts which don’t function due
to defects of material or production. This guarantee does not cover wearing parts (as described in the section
about spare parts). This guarantee is covering the replacement or repair of the defect part. Any dismounting,
forwarding, and mounting expenses are paid by the purchaser. The costs for any possible return from
FOAMICO after finished repairs rest with FOAMICO. The defect parts are the property of FOAMICO.
Claims which might be raised for any other legal reason, or normal wear and tear, as well as damage on parts
which can be related to negligent or wrong treatment, are not covered by this guarantee. This guarantee does
not cover at all, if the system has been exposed to frost.
This guarantee becomes void if changes or repairs have been implemented by non-authorized persons. Any
claims under the guarantee will only be accepted if they are announced to FOAMICO immediately after the
damage has been observed. This guarantee becomes void as soon as the system changes ownership.
Dealers and FOAMICO cannot be held responsible for personal injuries, damages to equipment, loss of
earning including those caused by production loss, loss of stock or the like, which might arise from
inappropriate or delayed delivery of the sold product, regardless the reason, including defects in production
or material. In addition, please read our usual terms of sale and delivery
Protection against frost
The equipment should only be installed in frost free rooms.
Prior to being exposed to frost, the system must be emptied for water (frost protected). Even shorter periods
of exposure to frost can damage the equipment.
This symbol refers to safety and danger moments. Neglect of these instructions can cause damage on persons
and objects.
Safekeeping
You are requested to store this manual in a place where it is at your disposal at any time, and it
should be handed over to the person responsible for this product. Should the manual get lost, please
don’t hesitate to require another one from your agent

4 PSU 0127- 7003313-16-19-20 15-04-2019
Declaration of conformity
We Foamico declare that this product is in conformity with the following directives:
- Machinery (2006/42/EG).
Safety
Attention! Use only original FOAMICO Nozzles, hoses, couplings and spare parts.
Precautionary measures
The construction of the system is in accordance with the generally adopted, technical requirements and the
stipulations concerning working environment and accident prevention. Therefore the equipment must be in
its best technical state before being used, and must only be utilized according to its requirements and by
observance of the precautionary measures and operational instructions. Disturbances, which might influence
the safety in particular, must be rectified immediately.
Appropriate utilization
FOAMICO low-pressure system is manufactured with the purpose of:
Rinsing with water, spreading foam and sanitizer within the stated boundaries.
Any other kind of application or use beyond this is considered to be inappropriate and deviant concerning
the requirements, and may lead to dangerous situations. FOAMICO is not liable for any sequential damages
brought about by this. Appropriate utilization includes the following:
The instructions, regulations, and recommendations given in this manual.
The observance of the prescribed intervals for inspection and maintenance.
The correct maintenance for good operational condition of the system.
The observance of the prescribed conditions for the environment and operation
2 Installation
SAFETY INSTRUCTIONS FOR MOUNTING AND INSTALLATION
IMORTANT!
Never install or apply damaged products. Claims concerning damages must be made to the carrier
immediately.
IMPORTANT!
Work in the connection with installations, start up, and maintenance on the Foamico cleaning systems should
only be done by authorized electricians, because the valid national regulations concerning prevention of
working accidents. (e.c. high voltage regulations: EN 60204, VBG4 DIN-VDE 0100/0113/0160) must be
respected. In cases of irregular installations there is a risk for major damages on both material and people.
Location and Mounting
The system should always be located in a frost-free room.
Stationary system must always be mounted where the surfaces are of solid quality, and when applicable the
fastening must always be done with the delivered bolts and raw plugs. Holes for wall brackets must be
drilled according the dimensional drawing.
The satellite should be connected to an adequate pipe system. This should correspond to distance from the
water supply, the maximum water flow and vertical distance from the boosting System. The pressure loss

5 PSU 0127- 7003313-16-19-20 15-04-2019
from the booster system to the satellite should be kept on a minimum. It is recommended to keep it under
1,50 bar.
It is recommended to install a strainer and a stop valve just before the mainstation. Use Foamico filters and
valves
Water Supply
ATTENTION! Connection to water supply should always be done in according to local or national
standards.
If the legislation in your country requests safeguards for reverse current, this must be provide for.
BEFORE mounting the system, the piping must be flushed with water in order to remove possible parts or
dirt.
AFTER mounting the system, flushing of the pipes must always be done with the system in “rinsing mode”,
in order to avoid any impurities in the injector system. Please keep rinsing until the rinsing nozzle shows an
invariable clean water jet coming out.
The water connection should be connected with the in POS. A, fig. 4.1 shown inlet.
For machines (7003312-15-18) with separate injector for concentrated chemicals The water connection
should be connected with the in POS. L, fig. 4.1
Air supply
ATTENTION! Connection to air supply should always be done in according to local or national standards.
ATTENTION! The cleaning system shall always have its own air supply system. Failure in the cleaning
system could accidentally lead to water and/or detergent can flow back in the air system. To avoid damage
on other installations. it is mandatory to make a separate air supply system for the cleaning equipment.
BEFORE mounting the system, the piping must be cleaned with air in order to remove possible parts or dirt.
The air should be connected to the inlet shown in POS B fig. 4.1
Supply of Detergent and sanitizer
ATTENTION! The handling and use of Detergent should always be done according to the local and national
standards.
BEFORE Mounting the system the pipes must be rinsed with water, in order to remove possible parts or dirt.
ATTENTION! The handling and connection should be done according to description from the Detergent
supplier.
The connection for disintegrated chemicals 1 should be connected with the in POS. J, fig 4.1 shown inlet.
The connection for disintegrated chemicals 2 should be connected with the in POS. K, fig 4.1 shown
inlet.
The connection for disintegrated chemicals 3 should be connected with the in POS. L, fig 4.1 shown
inlet.

6 PSU 0127- 7003313-16-19-20 15-04-2019
3 Operation
Rinsing
1. ATTENTION! Make always sure that the valve, POS. K, POS. A, POS. E and POS J, fig. 4.1 are closed.
2. Mount the rinsing hose with the coupling in POS. E, fig. 4.1 and make sure the valve is closed.
3. Check the low-pressure valve/gun and make sure it is closed.
4. Mount the rinsing nozzle or rinsing pipe in the coupling at the low-pressure valve/gun (marked with blue
or green protection)
5. Turn the handle POS. D, fig. 4.1 into the position/function “rinsing” .
6. Open the ball valve POS. A, fig. 4.1 and the ball valve POS. E, fig. 4.1
7. The System is now ready for rinsing. Rinse by opening the low-pressure valve/gun
8. ATTENTION! After rinsing, the hose must be depressurized. Close the valve POS. A fig. 4.1 and open the
low pressure valve/gun.
9. Close the Valve POS. E fig. 4.1 after the system has been depressurized. The hose can now be
disconnected.
Foaming chemical 1
1. ATTENTION! Make sure that the valves POS. K, POS. A, POS. E und POS J, fig. 4.1 are closed.
2. Mount the rinsing hose with the coupling POS. E, fig. 4.1
3. Make sure the low-pressure valve/gun at the end of the hose is closed.
4. Mount the foam nozzle (marked with white protection) into the coupling of the low-pressure valve/gun
5. Turn the handle POS. D, fig. 4.1 into the position/function “foaming” .
6. Open the ball valve POS J, and POS. E, fig. 4.1.
7. Adjust the air pressure to 4-6 bar on the regulator pos H fig 4.1 (differs from detergent to detergent. Often
has to be fine-tuned during first time foaming)
8. The system is now ready to foam. Apply foam by opening the low pressure valve/gun.
9. ATTENTION! The air supply is always to be closed while the foaming function is not in use. POS. B, fig,
4.1
10. ATTENTION! After foaming, the hose must be depressurized. Close the valve POS. J fig. 4.1 and open
the low pressure valve/gun.
11. Close the Valve POS. E fig. 4.1 after the system has been depressurized. The hose can now be
disconnected.
Foaming chemical 2
1. ATTENTION! Make sure that the valves POS. K, POS. A, POS. E und POS J, fig. 4.1 are closed.
2. Mount the rinsing hose with the coupling POS. E, fig. 4.1
3. Make sure the low-pressure valve/gun at the end of the hose is closed.
4. Mount the foam nozzle (marked with white protection) into the coupling of the low-pressure valve/gun
5. Turn the handle POS. D Abb. 4.1 into the position/function “foaming” .
6. Open the ball valve POS K, and POS. E, fig. 4.1.
7. Adjust the air pressure to 4-6 bar on the regulator pos H fig 4.1 (differs from detergent to detergent. Often
has to be fine-tuned during first time foaming)
8. The system is now ready to foam. Apply foam by opening the low pressure valve/gun.
9. ATTENTION! The air supply is always to be closed while the foaming function is not in use. POS. B, fig,
4.1
10. ATTENTION! After foaming, the hose must be depressurized. Close the valve POS. K fig. 4.1 and open
the low pressure valve/gun.
12. Close the Valve POS. E fig. 4.1 after the system has been depressurized. The hose can now be

7 PSU 0127- 7003313-16-19-20 15-04-2019
disconnected.
Foaming chemical 3 only (7003311-12-14-15-17-18)
1. ATTENTION! Make sure that the valves POS. L, fig. 4.1 are closed.
2. Mount the rinsing hose with the coupling POS. M, fig. 4.1
3. Make sure the low-pressure valve/gun at the end of the hose is closed.
4. Mount the foam nozzle (marked with white protection) into the coupling of the low-pressure valve/gun
5. Open the ball valve POS L, and POS. M, fig. 4.1.
6. Adjust the air pressure to 4-6 bar on the regulator pos H fig 4.1 (differs from detergent to detergent. Often
has to be fine-tuned during first time foaming)
7. The system is now ready to foam. Apply foam by opening the low pressure valve/gun.
8. ATTENTION! The air supply is always to be closed while the foaming function is not in use. POS. B, fig,
4.1
11. ATTENTION! After foaming, the hose must be depressurized. Close the valve POS. L fig. 4.1 and open
the low pressure valve/gun.
12. Close the Valve POS. M fig. 4.1 after the system has been depressurized. The hose can now be
disconnected.
Stop procedure
1. ATTENTION! The Water- and chemical supply is to be turned off after operation. Close the valves
POS. K, POS.A, POS. J, fig. 4.1.
2. Depressurize the hose by opening the low pressure valve /gun.
3. After the hose is depressurized, close the valve POS. E, fig. 4.1
4. Disconnect the hose.
5. ATTENTION! The air valve POS. H, fig. 4.1 must be closed

8 PSU 0127- 7003313-16-19-20 15-04-2019
Figure 4.1
A: Connection for water supply
J: Coupling for the disintegrated chemicals foam
chemicals 1
B: Connection for air supply
K: Coupling for the disintegrated chemicals foam
chemicals 2
D. Handle for choosing between rinsing and
foaming operation.
L: Coupling for the disintegrated chemicals foam
chemicals 3 Ore Water supply local chemical
E: Connection for rinsing hose
M: Connection for hose for chemical 3
H: Air pressure reducer to adjust the foam
consistency
N: Connection for limiting nozzles. Adjust
concentrations
Table 4.1

9 PSU 0127- 7003313-16-19-20 15-04-2019
TROUBLESHOOTING
Fault
Cause
Action
No rinsing pressure.
Booster or main station not
started.
Start booster/or main station.
Too many users on the same
time.
Check maximum number of users.
The ball valve at the inlet of the
system is not opened.
Open the ball valve.
Unstable rinsing pressure.
Unoriginal rinsing nozzle with
too high water consumption is
used.
Change to master rinsing nozzle –
observe technical data for model.
No foam
The turning handle POS.D fig.1
is not in the position “foaming"
Turn the handle into the position
“foaming”
Leaking pipeline for the
disintegrated chemicals
Check the pipeline for
disintegrated chemicals
Booster or pumping station for
disintegrated chemicals is
inactive
Activate the Booster or pumping
station
The Ball valve for the
disintegrated chemicals at the
inlet or outlet for the cleaning
hose is closed.
Open the ball valves for
disintegrated chemicals or the ball
valve at the outlet from at the
cleaning hose.
Suction filter above fluid level in
the chemical container.
Lead the suction filter underneath
the fluid level.
Schlechte Schaumqualität
Wrong product.
Change to a foam product.
Injector system is blocked by
chemical remains.
Injector system and water nozzle
in the injector must be
disassembled and cleaned.
Cleansing hose is damaged,
pinched or kinked.
Replace the cleansing hose
No compressed air to the system.
Open the air inlet to the system.
Unoriginal foam nozzle is
installed.
Change to original foam nozzle,
installed with white nozzle guard.
Insufficient air supply to the
system.
Min. 150 l/min. and max. 200
l/min. at 4-6 bars is requested.
Air pressure not set correct.
Is adjusted on the air regulation
valve to be 4-6 bars.

10 PSU 0127- 7003313-16-19-20 15-04-2019
4 Maintenance
RINSING HOSE
ATTENTION! The rinsing hose should be checked for any damage or week point before taking it into use
every day. A damaged hose can potential be dangerous.
Do not drive across the hose. Be careful not to damage the hose on any sharp edged or corners.
After use clean the outside of the hose. Store it on a hose hanger.
For security reasons it is recommended to change the hose at least once every 12 month.
NOOZLES
Nozzles are warned over time. And warned out nozzle is less effective. It can result in less rinsing power,
higher water usage, higher chemical consumption. Check the nozzles on a regular basis. 1 to 2 times every
month is recommended. Change the nozzle if they are damaged. To be sure you will get the optimized result
we recommend using Foamico nozzles.
LOW PRESSURE VALVES / GUNS
They must be checked regular. The nut on the handle has to tighten regularly. Check couplings, swivels,
handles for any damaged. A damaged part must be changed for security reasons.
Couplings.
Couplings should be cleaned and greased on a regularly basis. Use only approved grease. This will
extend the live time of couplings. Always make sure there is a nozzle or lance mounted in the
coupling before opening. Rinsing through an open coupling can damage the O-rings.
BALL VALVES
Every ball valve on the inlet for water inlet for air outlet for water/foam and outlet for sanitizer must be
adjusted.
First time, after one week, and then, once every month. Tight the nut on the handle to avoid leakage.
NON-RETURN VALVES / CHECK VALVES
ATTENTION! Non-return valves are very important to secure a correct function of the system.
Non return valves for air: The system has 2 non- return valves for air. The purpose of these is to prevent
water running back into the air system. Due to the potential risk, the air system for the cleaning system must
be separate from other air systems.
ATTENTION! Never leave the valve for air open. Always secure it is closed when not foaming!
If leakage of water is observed anywhere in the airline, both non-return valves must be changed.
- Non-return valve for chemical: The system has one for each chemical intake. The purpose is to prevent
water running back into to chemicals. It will dilute the chemical and result in none or bad foam quality and to
low concentration
ATTENTION! Non- return valves should be checked once every week. It is recommended to change every
1-2 year
Use only Original Foamico non-return valves.

11 PSU 0127- 7003313-16-19-20 15-04-2019
SUCTION FILTER / CHEMICAL HOSE
The suction filter for chemical should be clean once every week. It is recommended to change filter
5 TECHNICAL DATA Unit PSU 0127-
Water:
Min./Max. Inlet pressure bar 12/25
Max. Water consumption l/min. 50
Max. Temperature °C 70
Pipe dimension inlet inch ½"
Pipe dimension outlet inch ½"
Disintegrated chemicals coupling:
Min./Max. Inlet pressure bar 5/8
Pipe dimensions inlet inch ½"
Air:
Pipe dimensions inlet mm 8
Air supply bar 5/10
Air consumption l/min. 150-200
Accessories:
Standard rinsing nozzle 25/30 Material: Stainless steel
Standard foam nozzle 50/200 Material: Stainless steel
Standard Sanitizer nozzle 40/30 Material: Stainless steel
Dimensions (WxHxD) mm 436x393x207
Weight kg 11

12 PSU 0127- 7003313-16-19-20 15-04-2019
6 Spare parts Satellite system
Spare parts

13 PSU 0127- 7003313-16-19-20 15-04-2019
Figure 8.1 Overview Satellite system

14 PSU 0127- 7003313-16-19-20 15-04-2019
QTY.
NO:
Description
Description1
Beschreibung
1
1001551
Satellite cabinet welded
Prediluted detergent
Gehäuse
1
1002303**
Block
Prediluted chemicals 2 foam
Block komplett
1
1001887**
Block
Prediluted chemicals foam - des.
Block komplett
1
1002280**
Block
Prediluted chemicals 1 foam
Block komplett
2
1001219
Connection tube for satellite
3 Injector system
Verbindungsrohr für Satelliten
4
1000719
Nut for union
Blok part
Schraube für Verschraubung
4
1000720
Union
Blok part
Verschraubung
3
1000260
Foam Lance
1/2" RG Male - Female
Schaumlanze
1
1001337
Inlet pipe for Satellite
1/2" RG Male - Female
Eingangsrohr für Satellit
2
1000189
Male elbow 90 degrees
1/2" RG
Winkel 90° - 1/2" RG
4
1000718
Union
for block
Verschraubung
2
1000072
Nipple 1/2"
120mm
Nippel 1/2" 120mm
1
1000134
Pressure regulator with
Filter- Manometer. fittings
Druckreduzierventil mit
1
1002127
Pressure regulator with
Filter- Manometer. T - fittings
Druckreduzierventil mit
1
1001556
Front plate satellite
Prediluted detergent
Frontabdeckung
1
1700138
Labels
Set
Symbole
1
1000334
Button Head Screw
ISO 7380 - M6 x 10 - 10N
Schraube
1
1001886*
Block Foam
for prediluted chemicals
Block Schaum
1
1001883*
Block Foam
concentrated chemicals
Block Schaum
4
1000069
Ball valve
1/2" RG female female
Kugelhahn
1
1001234
Air inlet assembly
All models
Lufteinlassanordnung
1
1700074
Connector
Ø8 Hose - 1/4"RG
Gerade Steckkupplung AG
1
1001557
Top bracket satellite
Satellite L=300 mm
Obere Halterung für Satellit
4
1000643
Union strait 1/2"RG
Stainless steel
Verschraubung ½"
1
1001948
Front Label Foamico
Prediluted Satellite
Vorderen Etikett Foamico
Table 8.1 Overview Satellite system
*1001886 for machines (7003312-15-18)
*1001883 for machines (7003311-14-17)
** 1002303 for machines (7003313-14-15-16-17-18)
** 1002280 for machines (7003310-11-12)

15 PSU 0127- 7003313-16-19-20 15-04-2019
Pipe system –rinse circuit. Part number: 1002303 -1002280.
Figure 6.2 Spare parts –pipe system –rinsing circuit

16 PSU 0127- 7003313-16-19-20 15-04-2019
QTY.
NO:
Description
Description1
Beschreibung
1
1001666
Ball / shaft for
2 injector system
Kugle - Welle für
4
1002337
Ball gasket for
2 Injector system
Kugeldichtung
1
1002279
Block part
2 prediluted chemicals
Hauptteil für
1
1002174
Top plate for block
2 Injector system
Top für block
1
1000533
Bearing for shaft
3 injector system
Lager für Welle
2
1001899
Spring f. position ball
Position disk
Feder f. Positionierung Scheibe
2
1001819
Ball f. Check valve
1/4"- 6,35mm
Kugel f. Rückschlagventil
1
1001002
Check valve
1/4" x 1/4" male - male EPDM
Rückschlagventil Luft
1
1001577
Air valve
Ø6
Luft Ventile
1
1001649
Position plate 2 foam for
2 Injector system
Positionierung Plate für
1
1001683
Bracket for block
2 Injector system
Halter für
1
1000726
Nope for shaft
-
Achse
1
1000727
Handel for
3 Injector block
Griff
1
1000840
Nipple 1/2"
70mm
Nippel 1/2" 70mm
1
1000069
Ball valve
1/2" RG female female
Kugelhahn
1
1000037
Quick connect coupling
1/2"RG male
Schnellverschlusskupplung 1/2" AG
3
1000576
O-Ring
Ø11,0 x 1,78
O-Ring
1
1000534
Pressure ring for
3 Injector system
Druckring für
1
1001681
O-Ring
Ø39,45 x 1,78
O- Ring
4
1001750
Socket Head Cap Screw
EN ISO 4762 M6 x 16
Zylinder Schraube
4
1000495
Washer
DIN 125 -A 6,4
Unterlegscheibe
1
1001816
Bottom part
2 prediluted chemicals
Platte
2
1001787
Chek valve
Detergent
Rückschlagventil
1
1001793
Chek valve
Water
Rückschlagventil
2
1000541
O-seal
Ø4,8 x 1,78
O- Ringe
2
1001205
Button Head Screw
Schraube
1
1001788
Elbow
90 Degrees Ø6 - 1/4" Female
Winkel
2
1001276
Capscrew
ISO 7045 - M4 x 18
Schraube
1
1001196
Socket Head Cap Screw
EN ISO 4762 M5 x 45
Zylinder Schraube
Table 8.2 Spare parts –pipe system –rinsing circuit

17 PSU 0127- 7003313-16-19-20 15-04-2019
Pipe system –rinse circuit. Part number: 1001883 -1001886.
Figure 6.3 Spare parts –pipe system –rinsing circuit
QTY.
NO:
Description
Description1
Beschreibung
1
1001793*
Check valve
Water
Rücksclagventil
1
1001787*
Check valve
Detergent
Rücksclagventil
1
1000078
Nipple
1/2" out of cabinet
Nippel speziell
1
1000069
Ball valve
1/2" RG female female
Kugelhahn
1
1000037
Quick connect coupling
1/2"RG male
Schnellverschlusskupplung 1/2" AG
2
1000062
Nut
1/2"RG
Mutter
1
1001075
Injector house
Version Automatic
Injektor Haus für Automatik
1
1001002
Check valve
1/4" x 1/4" male - male EPDM
Rückschlagventil Luft
1
1001788
Elbow
90 Degrees Ø6 - 1/4" Female
Winkel
1
1000540**
Ø1,8 Injector for
3 Injector system
Ø1,8 Injektor für
1
1000790
Check valve
1/4" male x ø6 hose Hi Flour
Rückschlagventil Chemie
Table 6.3 Spare parts –pipe system –rinsing circuit
*1001793 for machines (7003312-15-18)
*1001787 for machines (7003311-14-17)
** 1000540 for machines (7003312-15-18)

18 PSU 0127- 7003313-16-19-20 15-04-2019
Ersatzteile Sprühschaum kreis Teilnummer 1001787-1001793
Figure 8.4 Spare parts Foam circuit
QTY.
NO:
Description
Description1
Beschreibung
1
1001786
House for
Prediluted chemical
Gehäuse
1
1001794*
House for
Water
Gehäuse
1
1000719
Nut for union
Blok part
Schraube für Verschraubung
1
1001684
Ball for check valve
Ø14mm Ceramic
Kugel f. Pos. Platte und Rückschlagventil
1
1001677
Union part for
2 Injector system
Verschraubung
1
1001682
O-ring
11,5 x 3,0mm
O-ring
1
1001912
Support f. check valve
Injector system
Plate für Rückschlagventil
1
1001913
Support f. check valve
Injector system
Plate für Rückschlagventil
1
1001685
Spring f. check valve
2 Injector system
Feder für Rückschlagventil
2
1000684
O-Ring
16,3 x2,4
O-Ring
1
1001947
Support ring for
Check valve - 1/2"
Unterstützung ring
Table 8.4 Spare parts Foam circuit

19 PSU 0127- 7003313-16-19-20 15-04-2019
Flow diagram
Flow diagram PSU 0127-1
Flow diagram PSU 0127-2

20 PSU 0127- 7003313-16-19-20 15-04-2019
Flow diagram PSU 0127-3
Flow diagram PSU 0127-4 and 7
This manual suits for next models
8
Table of contents
Popular Control Unit manuals by other brands
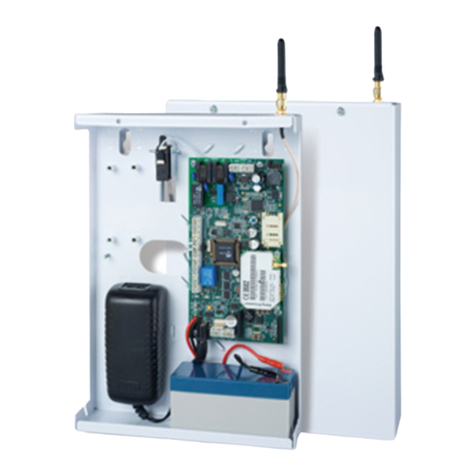
Risco
Risco AGM Advanced Installation and programming instructions

ThermOmegaTech
ThermOmegaTech CSUA Installation instructions manual
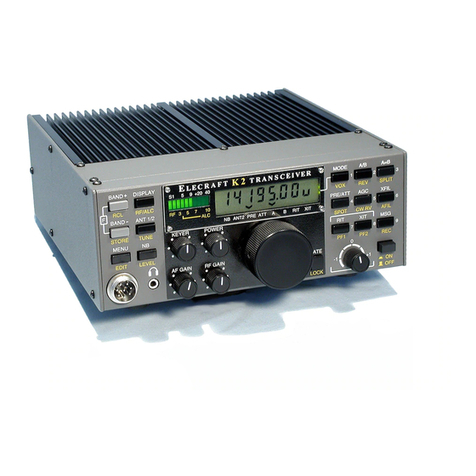
ELECRAFT
ELECRAFT KAT2 Notes
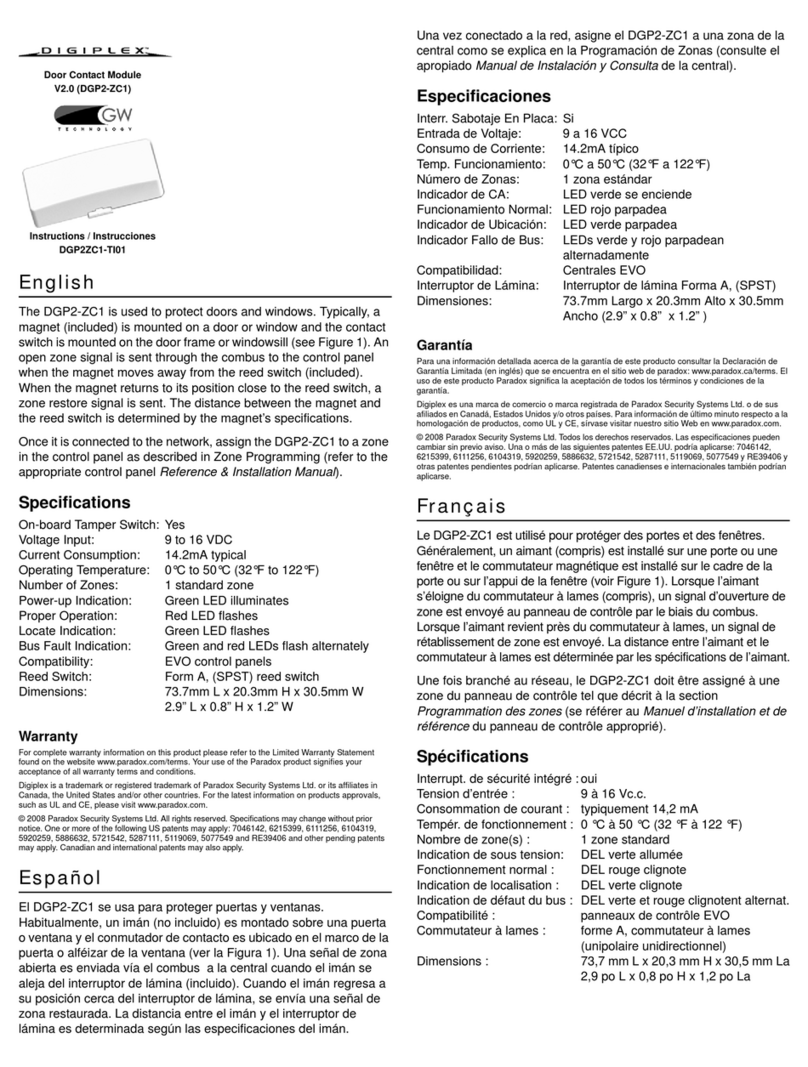
Digiplex
Digiplex DGP2-ZC1 instructions
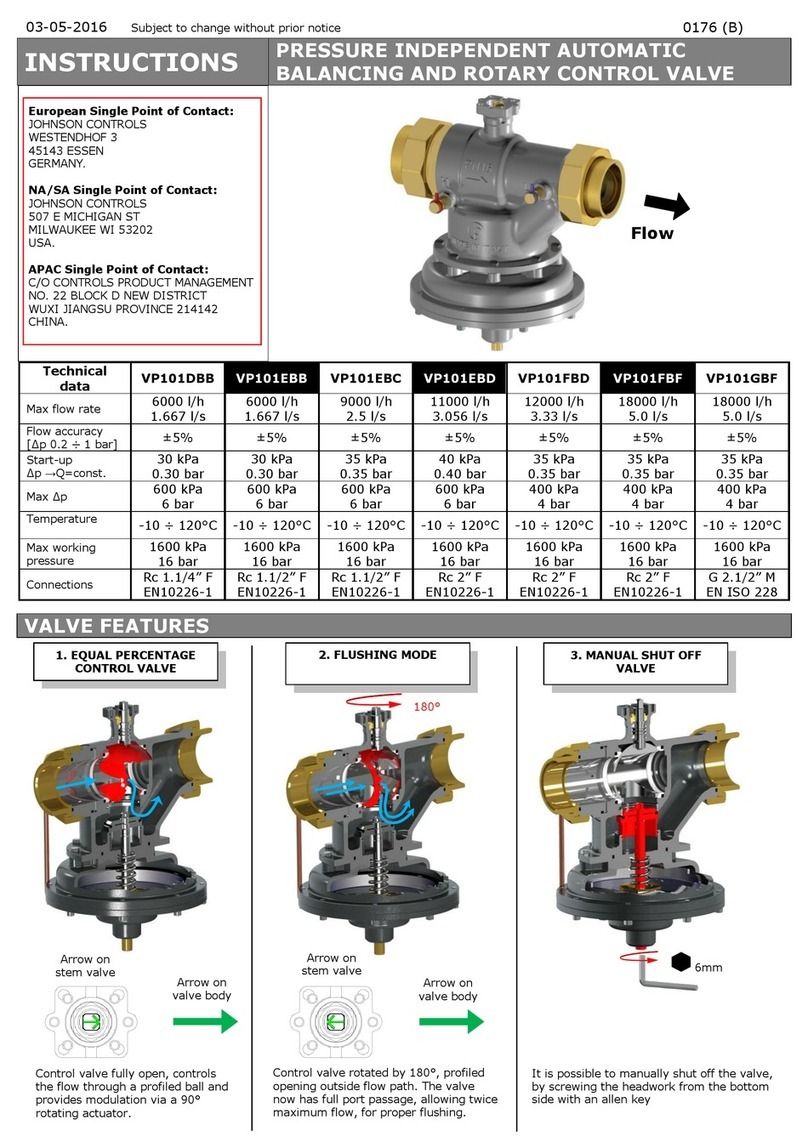
Johnson Controls
Johnson Controls VP101DBB instructions
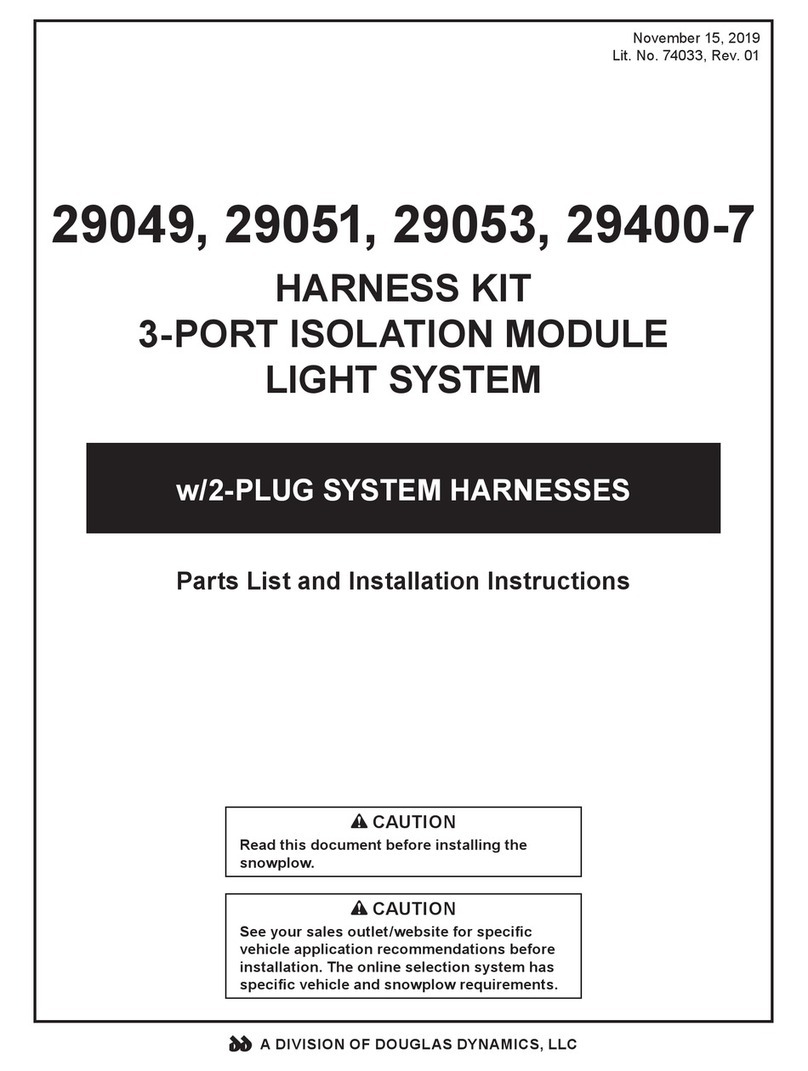
Douglas Dynamics
Douglas Dynamics 29049 Parts List and Installation Instructions