Fulling Motor FD542 User manual

Changzhou Fulling Motor Co, Ltd
Add:No.69 KunLun Road, New District, Changzhou City, 213032, China
Tel:+86-519-85132957
Fax: +86-519-85132956
Web site:www.fullingmotor.com
Email
:info@fullingmotor.com
User’s Manual
For FD542
Digital 2-Phase Stepper Driver
All Rights Reserved, No reproduction
Attention:Please read this manual carefully before using the drive!

User’s Manual For FD542 Digital 2-Phase Stepper Driver User’s Manual For FD542 Digital 2-Phase Stepper Driver
1 2
Contents
Ⅰ.Product introduction..............................................................................................3
1. Overview .................................................................................................................3
2. Features....................................................................................................................3
3. Applictaions.............................................................................................................3
Ⅱ.Electrical, Meachanical, Environment Specifications ..................................... 3
1. Electrical Specifications ..........................................................................................3
2. Operating Environment and Other Parameters........................................................3
3. Mechanical Installation Dimensions Diagram...........................................................4
4. Elimination of Heat..................................................................................................4
Ⅲ.Driver Interface and Wiring Introduction..........................................................4
1. Interface Description ...............................................................................................4
2. Control Signal Interface Circuit............................................................................... 5
3. Sequence Chart of Control Signals..........................................................................5
4. Control Signal Mode Setting...................................................................................5
5. Wiring Require.........................................................................................................5
Ⅳ.Selecting Microstep Resolution , Driver Output Current and Parameter
auto-tuning................................................................................................................. 6
1. Current Settings....................................................................................................... 6
2. Microstep Resolution Selection...............................................................................6
3. Parameter atuo-tuning function ...............................................................................6
Ⅴ.Power Supply Selection........................................................................................ 7
Ⅵ.Motor Option ........................................................................................................7
1. Motor option............................................................................................................7
2. Motor Wiring...........................................................................................................7
2)Set value of output curren......................................................................................8
Ⅶ.Typical Connection............................................................................................... 8
Ⅷ.Protection Functions.............................................................................................8
Ⅸ.Frequently Asked Questions................................................................................8
1. Problem Symptoms and Possible Causes ................................................................9
2. Drive FAQ ...............................................................................................................9
Product warranty terms..........................................................................................9

User’s Manual For FD542 Digital 2-Phase Stepper Driver User’s Manual For FD542 Digital 2-Phase Stepper Driver
3 4
FD542
Digital 2-Phase Stepper Driver
Ⅰ. Introduction, Features and Applications
1. Introduction
The FD542 is the company’s new digital stepping driver based on the latest 32-bit
ARM digital processing technology, Drive control algorithm uses advanced variable
current technology and advanced frequency conversion technology. The driven
motors can run with low heating, small noise, smooth movement. Thanks to the
built-in micro-resolution technology, the effect of high resolution can be achieved
and the driven motors can run with much smaller noise, lower heating, smoother
movement at low to high speed even under low resolution conditions. Motor
auto-identification and parameter auto-configuration technology offers optimum
responses with different motors and easy-to-use.
2. Features
●New 32-bit DSP Technology ●Suitable for 4,6,8 lead 2-phasemotors
●Ultra-low vibration noise ●Optically isolated input signals,
●Built-in high resolution
●pulse frequency up to 500 KHz(default 200KHz)
●Motor auto-identification and parameter auto-configuration technology.
●Output current programmable, from 0.1A to 5A
●Variable current control for less motor heating
●Micro-step resolutions programmable range, from 200 to 51200 steps/rev
●Automatic idle-current reduction in half.
●Over-voltage, Under-voltage, over-current protections
3. Applications
It can be used in various kinds of small and medium-sized equipment and machines,
such as engraving machines, labeling machines, laser cutters, laser typesetting,
plotting instrument, CNC machine, automatic assembly equipment, and so on.
Particularly adapt to the applications desired with low noise, high speed.
Ⅱ.Electrical, Mechanical, Environment Specifications
1. Electrical Specifications
Parameters
FD542
Min
Typical
Max
Unit
Output Current
0.1
-
4.5
A
Input Voltage
24
36
50
VDC
Logic Signal Current
6
10
16
mA
Logic Signal Voltage
4.5
5
28
Vdc
Minimum Pulse Width of
logic signal
1.5
-
-
us
Pulse input frequency
0
-
200
KHz
Isolation resistance
100
MΩ
2. Operating Environment and other Parameters
Cooling
Natural Cooling or Forced cooling
Operating
Environme
nt
Environment
Don’t place next to other heating equipment, Avoid dust,
oil fog and corrosive gases, excessive humidity and strong
vibration, No flammable gas and conductive dust.
Ambient
Temperature
-5℃~+50℃(23℉~122℉)
Humidity
40 ~90%RH
Vibration
5.9m/s2MAX
Storage Temperature
-20℃~80℃(-4℉~176℉)
Altitude
Below 1000 meters
Weight
Approx. 0.280 Kg (9.9 oz)

User’s Manual For FD542 Digital 2-Phase Stepper Driver User’s Manual For FD542 Digital 2-Phase Stepper Driver
5 6
3. Mechanical Dimensions (unit:mm, 1 inch = 25.4 mm)
Figure 1: Mechanical dimensions
*Recommended to use side mounting for better heat dissipation, When designing
the installation size, pay attention to the terminal size and wiring.
4. Elimination of Heat
1) Driver’s reliable working temperature should be<60 ℃,and motor working
temperature should be <80℃(176℉);
2) It is recommended to use automatic idle-current mode, namely current automatically
reduce to 50% when motor stops, so as to reduce driver heating and motor heating;
3) It is recommended to mount the driver vertically to maximize heat sink area. Use
forced cooling method to cool the system if necessary, Ensure that the drives
operation in a reliable operating temperature range.
Ⅲ.Pin Assignment and Description
1. Interface description
1)Control Signal Connector
Signal
Functions Details
PUL+
Pulse signal: This input represents pulse signal, each rising edge active,
4.5~28Vdc when PUL-HIGH, 0~0.5V when PUL-LOW, For reliable
response, pulse width should be longer than 1.5μs.
PUL-
DIR+
Direction signal: this signal has low/high voltage levels, representing two
directions of motor rotation; For reliable motion response, DIR signal
should be ahead of PUL signal by 2μs at least. 4.5V-28Vdc when
DIR-HIGH, 0-0.5V when DIR-LOW. Please note that rotation direction is
also related to motor-driver wiring match. Exchanging the connection of
two wires for a coil to the driver will reverse motion direction.
DIR-
ENA+
Enable signal: This signal is used for enabling/disabling the driver. High
level for enabling the driver and low level for disabling the driver. When
ENA-HIGH is connected to 4.5V-28Vdc, ENA-LOW is connected to
0-0.5V (or Internal optical coupling is conducted), the driver will cut off
the current of each phase of the motor to make the motor in a free state,
step pulses are not responded at this time. Usually left unconnected
(enabled).
ENA-
2)Power Connector Configurations
Signal
Functions Details
GND
Power Ground.
+Vdc
power supply, +20V~ +50Vdc Including voltage fluctuation and EMF
voltage, Recommended 36Vdc supply.
A+、A-
Motor coil A (leads A+ and A-)
B+、B-
Motor coil B (leads B+ and B-)
3)Status Indication
The green LED is Power indicator light, The LED turns on when the driver is powered on
and functions normally. When driver is powered off, the LED is off. The FD542 uses one
RED LED to indicate what protection has been activated. The red LED blinks
118
112
34
112
22.5
4.5
4-Ф3.5
75.5
25.3
47.8

User’s Manual For FD542 Digital 2-Phase Stepper Driver User’s Manual For FD542 Digital 2-Phase Stepper Driver
7 8
periodically (in every 3 seconds)to indicate the error type. When the fault is cleared by
the user, the red LED is always off. The specific relationship is shown in the following
table.
Number
Time(s) of
Blink
Sequence wave of Red LED
Description
1
1
Over-current protection
or Single short circuit
between two phases
2
2
Over Voltage protection
3
3
No definition
4
4
Motor power lines
wrong & not connected
will activate this
protection.
2. Control Signal Connector Interface
This FD542 driver uses differential inputs to increase noise immunity and interface
flexibility. Single-ended (common-cathode or common- anode) control signals from the
controller can also be accepted by this interface. The input circuit has built-in high-speed
opto-coupler, and can accept signals in the format of line driver, open-collector, or PNP
output. Recommend use line driver control signals to increase noise immunity of the
driver in interference environments.
In the following figures, connections to open-collector and PNP signals are illustrated.
Note: When VCC is 4.5V~28Vdc., R is connected or not.
3. Sequence Chart of Control Signals
In order to avoid some fault operations and deviations, PUL, DIR and ENA should
abide by some rules, shown as following diagram:
Note:
1)t1:ENA must be ahead of DIR by at least 5us. Determined high level. Usually,
ENA+ and ENA- are NC (not connected).
2)t2:DIR must be ahead of PUL active edge by 2ms to ensure correct direction;
3)t3:Pulse width not less than 2s;
4)t4:Low level width not less than 2us.
4. Control Signal Mode Setting
Pulse trigger edge and single/double pulse selection: By PC software(ProTuner
software) or STU debugger set the rising or falling edge trigger of the pulse is a valid,
and set single or double pulse mode. In the double-pulse mode, the signal at the direction
control terminal must be kept high or left floating.
5. Wire Connection
1)In order to improve anti-interference performance of the driver, it is recommended to
use twisted pair shield cable, and the shield is shorted to ground, Except for special
requirements, the shielded wire of the control signal cable is also shorted to
single-ended ground. The upper end of the shielded wire is grounded, and the driver
end is floating. Only allowed on the same point grounding in the same machine, If it is
not a real ground wire, the interference may be serious, and the shielding layer is not
connected at the time.
2)To prevent noise incurred in PUL/DIR signal, pulse/direction signal wires and motor
270
Ω
270
Ω
270
Ω
Driver
PUL+
PUL-
DIR+
ENA+
DIR-
ENA-
VCC
R
R
R
脉冲信号
方向信号
使能信号
Common Anode connection
Common cathode connection
控
制
器
270
Ω
270
Ω
270
Ω
Driver
PUL+
PUL-
DIR+
ENA+
DIR-
ENA-
VCC
R
R
R
脉冲信号
VCC
方向信号
VCC
使能信号
Figure 3: Input interface Circuit
t2
t4
t1
t3
t2
PUL
DIR
ENA
>2us
>2us
>5us
高电平高于 3.5V
高电平高于 3.5V
低电平低于 0.5V
低电平低于 0.5V
Figure 4 Sequence chart of control signals

User’s Manual For FD542 Digital 2-Phase Stepper Driver User’s Manual For FD542 Digital 2-Phase Stepper Driver
9 10
wires should not be tied up together. It is better to separate them by at least 10 cm,
otherwise the disturbing signals generated by motor will easily disturb pulse direction
signals, causing motor position error, system instability and other failures.
3)If a power supply several drivers, parallel connection is recommend instead of
daisy-chaining.
4)It is prohibited to pull and plug power connector P2 while the driver is powered ON,
because there is high current flowing through motor coils (even when motor is at
standstill). Pulling or plugging power connector P2 with power on will cause
extremely high back-EMF voltage surge, which may damage the driver.
5) It is strictly forbidden to add lead to the terminal after adding tin, otherwise the
terminal may be damaged due to the increased contact resistance.
6) Lug must not be exposed outside the terminal to prevent accidental short circuit and
damage to the driver.
Ⅳ.Driver Current Output, Selecting Microstep Resolution
and Parameter auto-tuning function
This FD542 driver uses an 8-bit DIP switch to set microstep resolution, motor dynamic
current, standstill half-current, motor parameters and internal adjustment parameters
atuo-tuning, as shown below:
SW1
SW2
SW3
SW4
SW5
SW6
SW7
SW8
1.Current Setting
1)Dynamic current Setting
Peak Current
RMS Current
SW1
SW2
SW3
Current Setting
Default[1.0A,PK]
on
on
on
When SW1,SW2.SW3 are
set to off, it can be set to
the required current by PC
Software, Maximum value
is 4.2A and resolution is
0.1A, If it is not set, the
default is 1A.
1.46A
1.04A
off
on
on
1.91A
1.36A
on
off
on
2.37A
1.69A
off
off
on
2.84A
2.03A
on
on
off
3.31A
2.36A
off
on
off
3.76A
2.69A
on
off
off
4.20A
3.00A
off
off
off
2)Standstill Current Setting
SW4 is used for this purpose. off means that the standstill current is set to be half of the
selected dynamic current, and on means that standstill current is set to be the same as the
selected dynamic current. In general , SW4 should be set to off to enable the heat
generation of the motor and driver to be reduced and the reliability to be improved. The
current automatically reduced to 60% of dynamic current setting 400 millisecond after
the last pulse. Theoretically, This will reduce motor heating to 30% (due to P=I2*R)) of
the original value.
2. Microstep Resolution Selection
Steps/rev.
SW5
SW6
SW7
SW8
Resolution Description
Default
on
on
on
on
When SW5,SW6,SW7
and SW8 are on, the driver
uses the default number of
resolution within the
driver. Use PC ProTuner
software or STU debugger
to set the number of
resolutions, the minimum
value is 1, the resolution is
1, and the maximum value
is 51200.
400
off
on
on
on
800
on
off
on
on
1600
off
off
on
on
3200
on
on
off
on
6400
off
on
off
on
12800
on
off
off
on
25600
off
off
off
on
1000
on
on
on
off
2000
off
on
on
off
4000
on
off
on
off
5000
off
off
on
off
8000
on
on
off
off
10000
off
on
off
off
20000
on
off
off
off
25000
off
off
off
off
3. Parameter auto-tuning function
When the driver is an open-loop step, each parameter of the motor can be automatically
identified once at each instant of powered-on, and the driver can automatically complete
the auto-tuning of the motor parameters and internal adjustment parameters. To get the
optimized performance, please repower the driver will auto-identify the new motor and
auto-configure related control parameters when the motor power supply voltage and other
conditions change.
Note that pulse can’t be input, the direction signal should not be changed, and the
enable signal can’t be connected at this time.
Dynamic current Setting
Microstep Resolution Setting
Half current/Full current selection

User’s Manual For FD542 Digital 2-Phase Stepper Driver User’s Manual For FD542 Digital 2-Phase Stepper Driver
11 12
Ⅴ. Power Supply Selection
It is important to choose appropriate power supply to make the driver operate properly
and deliver optimal performance. Both unregulated and regulated power supplies can be
used to supply DC power to the FD542 driver. If regulated power supply is indeed used,
voltage ripple peak value after rectification doesn’t exceed its specified maximum voltage.
Therefore, it is suggested to use power supplies with theoretical output voltage of no
more than its defined voltage, leaving room for power line fluctuation.
If regulated power supplies (such as most switching supplies.) are indeed used, it is
important to have large current output rating to avoid problems like current clamp.
Please Note:
1) Power Supply polarity not then reversed.
2) Best to use an unregulated power supply.
3) If unregulated supply is used, The power supply current output capacity should be
greater than 60% of the driver setting current.
4) If regulated supply is used, the average current withdrawn from power supply is
more than or equal to driver current.
5) It is recommended to have two or three drives to share one power supply to reduce
cost, if the supply has enough capacity.
Ⅵ.Motor option
The FD542 can drive any 2-phase and 4-phase of 4, 6, 8-lead hybrid stepping motors,
which is suitable for 1.8°and 0.9°step angle motor. When selecting a motor, it is mainly
determined by the torque and rated current of the motor. The torque is determined by the
size of the motor, the larger the size of the motor, the larger the torque.
While the current is mainly related to the inductance, the small-inductance motor has
good high-speed performance, but larger currents.
1. Motor Option
1)Determine load torque, transmission ratio and working speed range.
T电机=C(Jε+T 负载)
J:Moment of inertia of load
ε:Maximum angular acceleration of the load
C:Safety factor, recommend 1.2~1.4
T负载:Maximum load torque, Contains resistance torque such as payload, friction,
transmission efficiency.
2)What factors determine the motor output torque
For a given stepping motor and coil connection, the output torque has the following
characteristics.
●For a given motor, higher driver current will make the motor to output more torque,
but at the same time causes more copper loss heating in the motor and driver.
●Higher supply voltage can increase motor torque at higher speeds, thus helpful for
avoiding losing steps.
●From the torque-frequency characteristic diagram of the stepper motor, the
High-speed torque is smaller than that of the medium-low speed.
2. Connecting the Motor
For 6, 8 lead step motors, there are considerable differences in motor performance for
different coil connections.
3. Power supply Selection, Driver Voltage and Current Selection
1)Power Supply Selection
Generally Speaking, Higher supply voltage can increase motor torque at higher speeds,
V(Speed)
I
I+∆I
T(Torque
)
I-∆I
V-∆V
T(Torque
)
V(Speed)
V
V+∆V
Figure 5 T/F Characteristic diagram
4线电机
8线电机并行接法
高速性能好
8线电机串行接法
低速力矩大
6线电机高力矩模式
6线电机高速模式
Figure 6 Motor Wiring
A+
A-
B+
B-
A+
A-
B+
B-
A+
A-
B+
B-
A+
A-
B+
B-
A+
A-
B+
B-

User’s Manual For FD542 Digital 2-Phase Stepper Driver User’s Manual For FD542 Digital 2-Phase Stepper Driver
13 14
thus helpful for avoiding losing steps. However, higher voltage may cause bigger motor
vibration at lower speed, and it may also cause over-voltage protection or even driver
damage.
2)Set Value of output current
For a given motor, higher driver current will make the motor to output more torque, but at
the same time causes more heating in the motor and driver. Therefore, output current is
generally set to be such that the motor will not overheat for long time operation. Phase
current rating supplied by motor manufacturer is important to selecting driver current, but
the selection also depends on leads and connection. In principle, If the temperature
(<40℃)is very low, you can appropriately increase the current setting value to increase
the motor output power as required(Torque and high-speed response).
●4-lead motor: the output current is set to be equal to or less than the rated current of the
motor.
●6-lead motor high torque Mode: the motors should also be run at only 50% of their rated
current which is unipolar connection.
●6-lead motor high speed Mode: the motors should also be run at only 100% of their
rated current which is unipolar connection.
●8-lead motor Series Connections: the motors should also be run at only 70% of their
rated current which is unipolar connection.
●8-lead motor Parallel Connections: the motors should also be run at only 140% of their
rated current which is unipolar connection.
Note: After the current setting, please run the motor for 15~30 minutes, if the
temperature rise of the motor is too high(>70℃), reduce the current setting value.
Therefore, the general situation is to set the current to the value when the motor is
warm for a long time, but it is not too hot.
Ⅶ.Typical Wring
The FD542 driver with 57HS22 motor which may be connected in series or parallel, If
the motor direction is different from the expected direction, just exchange A+ and A-.
FD542 driver can drive any 2-phase or 4-phase of 4, 6, 8- lead hybrid step motors. The
following diagrams illustrate connection to various kinds of motor leads:
Note:
1) Different motors have different phase wire colors. When using the motor, the motor
data description shall be prevail, For example, the color of 57 and 86 motor wires is
different.
2) The phase is relative, but the windings of different phases can not be connected to
the terminals of the same phase of the driver(A+,A- is one phase, B+,B- is another
phase). 57HS22 motor lead definition, Series and Parallel Connections method is
shown below.
1)FD542 driver can only drive 2-phase hybrid step motors, which can’t drive 3-phase
and 5-phase stepping motor.
2)The method of judging whether the stepping motor is connected in series or in
parallel is correct, When the driver is not connected, directly rotate the motor shaft
by hand, If it can rotate easily and evenly, then the wiring method is correct; If the
resistance is large and uneven rotation with a certain sound, then the wiring method
is incorrect.
Lead definition
Tandem
Parallel
57HS22
57HS22
57HS22
蓝
S45
红
S45
黄
S45
绿
S45
白
S45
橙
S45
棕
S45
黑
S45
Figure8 Tandem and Parallel connection
控
制
器
R
R
R
FD542
PUL+
PUL-
DIR+
ENA+
DIR-

User’s Manual For FD542 Digital 2-Phase Stepper Driver User’s Manual For FD542 Digital 2-Phase Stepper Driver
15 16
Ⅷ.Protection Functions
1)Short Circuit Protection / Over-current Protection
Over-current protection will be activated when continuous current exceeds the limit
current value or in case of short circuit between motor coils or between motor coil
and ground, and RED LED will turn on once within each periodic time (3 s). Reset
the driver by repowering it to make it function properly after removing above
problems.
2)Over-voltage protection
When power supply voltage exceeds 60VDC, protection will be activated and RED
LED will turn on twice within each periodic time (3 s). Reset the driver by
repowering it to make it function properly after removing above problems.
3)Phase Error Protection
Motor power lines wrong & not connected will activate this protection. RED LED
will turn on four times within each periodic time (3 s). Reset the driver by
repowering it to make it function properly after removing above problems.
Attention: since there is no protection against power leads (﹢, ﹣) reversal, it is critical
to make sure that power supply leads correctly connected to driver. Otherwise, the driver
will be damaged instantly.
Ⅸ.Frequently Asked Questions
1. Problem Symptoms and Possible Causes
Symptoms
Possible
Problems
Solution
Motor is not
rotating
No Power
Check the power supply circuit for normal
power supply
The motor shaft
strong, Control
signal is too weak.
Control pulse signal is too weak, Signal
current increased to 7~16mA
microstep
resolution is too
small
select the right microstep resolution setting
Current setting is
too small
Select the right current setting
Drive is protected.
Power on again
Enable signal is
low high.
Enable signal is high or not connected.
Does not respond
to Input control
signals.
Not powered.
Motor rotating
in the wrong
direction
Motor phases may
be connected in
reverse
Exchanging the connection of two wires for
a coil to the driver will reverse motion
direction.
Alarm
indicator is on
Wrong motor
connection
Check connection
Power supply is
too high or too
low.
Check Power Supply
Motor or Driver is
bad.
Replace motor or driver
Inaccurate
location
Control signal is
disturbed
Eliminate interference
Shielded ground is
not connected or
disconnect
Reliable grounding.
Open winding of
motor
Check motor wire
Micro-step
resolution setting
is wrong.
select the right micro-step resolution setting
Current setting is
too small, losing
steps
Choose another power supply with lager
power or increase the output current of drive.
Motor stalls
During
acceleration
Acceleration is set
too high
Reduce the acceleration
Motor is
undersized for the
application
Choose another motor with higher torque
Power supply
voltage
too low or
Current setting is
too small.
Choose another power supply with larger
power or increase the output current of drive
2. Drive Frequently Asked Questions
1)What are Stepper Motor and Stepper Driver?
A stepper motor is a particular type of DC motor that can achieve very precise
positioning and/or speed control. When a discrete DC voltage is applied, the stepper

User’s Manual For FD542 Digital 2-Phase Stepper Driver User’s Manual For FD542 Digital 2-Phase Stepper Driver
17 18
motor rotates in a particular angle called the step angle. Therefore calls Stepping motor
which is characterized by no cumulative error. Receive each a pulse of electric from
controller, the motor is driven at a fixed angle by the diver, So it is widely used in various
open loop control.
The stepping driver is a power amplifier that enables the stepping motor to run, It
can convert the pulse signal from the controller into the power signal of the stepping
motor. The speed of the motor is proportional to the pulse frequency, So the control pulse
frequency can be adjusted precisely speed, the number of control pulses can be accurately
positioned.
2)What is the drive resolution? What is the relationship between the speed of
the stepping motor and the pulse frequency?
Because of its unique structure, the stepping motor is marked with the inherent step
angle when it leaves the factor. The step angle such as 0.9 degree/1.8 degree, it means
that the angle turned by each step of the half-step work is 0.9 degree, and the full-step is
1.8 degree. However, in many precision control situations, the angle of the entire step is
too large, which affects the control accuracy and the vibration is too large. Therefore, it is
required to complete a motor’s inherent step angle via in many subdivision steps. This is
the so-called subdivision drive, the electronic device capable of this function is called a
micro-step resolution driver.
V:Motor Speed(r/s)
P:Pulse frequency(Hz)
θe:Motor inherent step angle
m:Number of subdivisions(1 for full-step, 2 for half-step)
3)What are the benefits of subdivision driver?
●Reduce the step angle of each step, improve the step uniformity, so the control accuracy
can be improved.
●The method can make the rotor run smoothly, so this method can be considered as one
of the effective methods to reduce vibration at low speed.
●Can effectively reduce torque ripple and increase output torque.
4)Why does my motor only turn in one direction?
●The direction signal may be too weak, or the wiring polarity is wrong, or the signal
voltage is too high which lead to burn-out direction current limiting resistor.
●The pulse mode does not match, The signal is in the pulse/direction, So the driver must
be set to this mode. If the signal is CW/CCW(double pulse mode), the driver must also be
in this mode, otherwise the motor will only run in one direction.
Product warranty terms
1.Twelve Month Limited Warranty
Changzhou Fulling Motor Co, Ltd. Warrants its products against defects in materials
and workmanship for a period of 12 months from shipment out of factory. During the
warranty period, Fulling Motor will either, at its option, repair or replace products
which proved to be defective.
2 Exclusions
The above warranty does not extend to any product damaged by reasons of improper or
inadequate handlings by customer, improper or inadequate customer wiring, unauthorized
modification or misuse, or operation beyond the electrical specifications of the product
and/or operation beyond environmental specifications for the product. And poor ambient
heat dissipation.
3 .Obtaining Warranty Service
If your product fail during the warranty period, need to obtain a returned material
authorization number before returning product for service. Please include a written
description of the problem along with contact name and address.
4 .Warranty Limitations
●The warranty coverage of the product is limited to the device and process (i.e.
consistency)
●Fullingmotor specifically disclaims the implied warranties of merchantability and
fitness for a particular purpose. Because the suitability is also related to the technical
indicators of the use and the conditions of the use and environment.
P*θe
360*m
V=
Table of contents
Other Fulling Motor Control Unit manuals
Popular Control Unit manuals by other brands
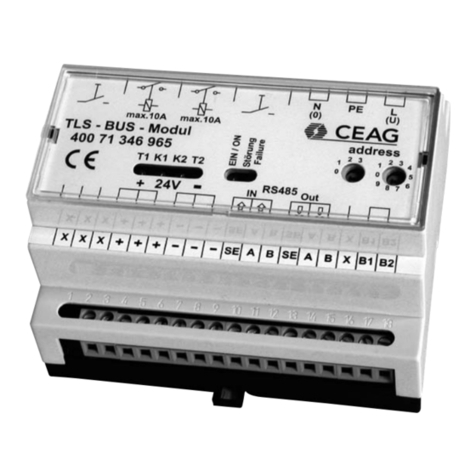
Eaton
Eaton CEAG TLS-BUS-Module Mounting and operating instructions
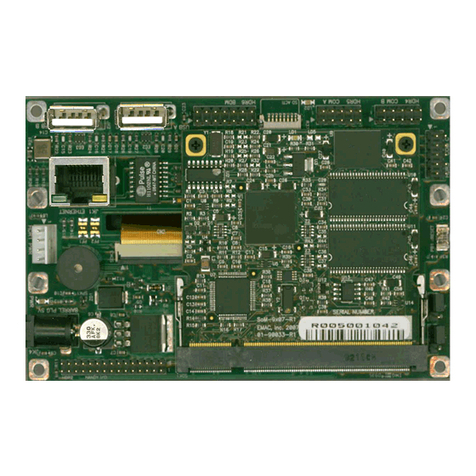
EMAC
EMAC SoM-210ES user manual
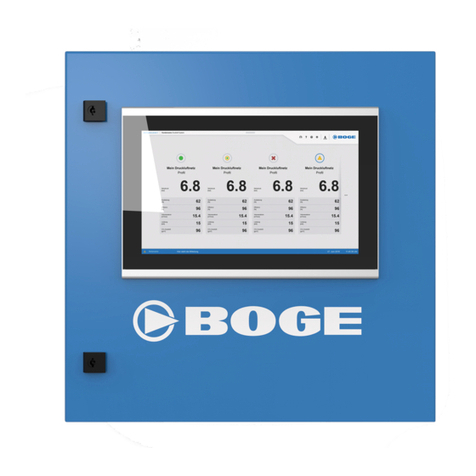
Boge
Boge airtelligence provis 3 operating instructions
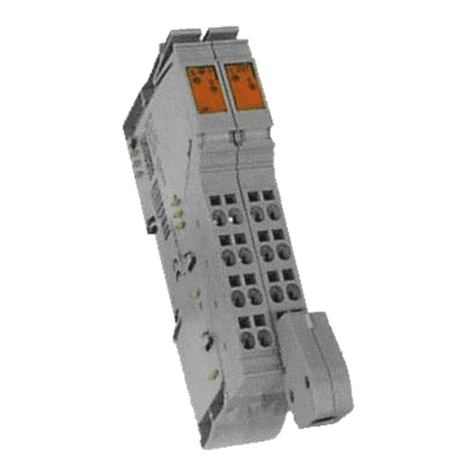
Bosch
Bosch Rextroth Indramat RECO R-IB IL CNT Applications manual
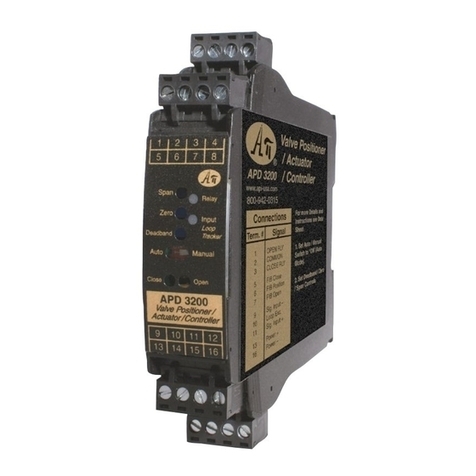
API
API APD 3200 Series quick start guide
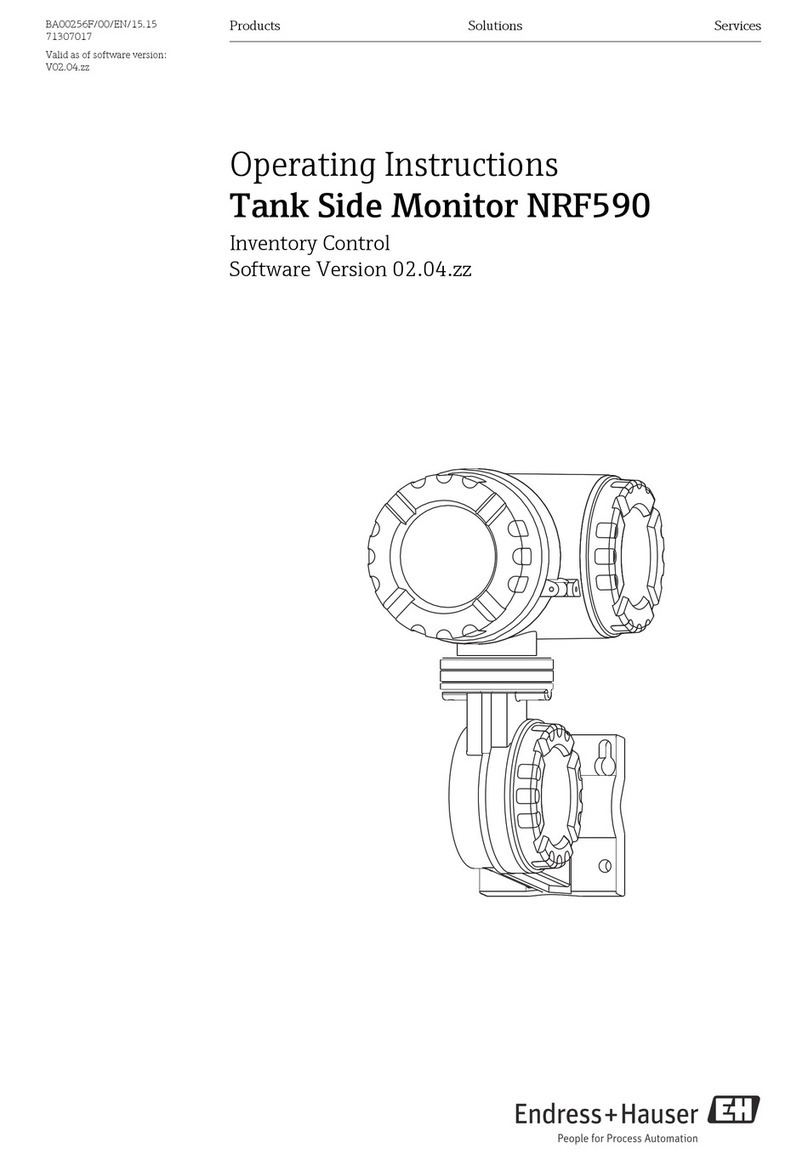
Endress+Hauser
Endress+Hauser Tank Side Monitor NRF590 operating instructions