FULTON Scope Instruction manual

Improving life through heat transfer solutions
SCOPE Sequencer Panel
This manual must be made available to the boiler operator at all times

SP-IOMM-2020-1
2
Table of Contents
I. Warning & Cautions Explained ...................................................................................................... 4
II. Warning & Cautions In Manual ..................................................................................................... 4
III. Safety ................................................................................................................................................. 5
IV. Regulations ....................................................................................................................................... 6
SECTION - 1 INTRODUCTION ........................................................................................................ 7
1.1 General .............................................................................................................................. 7
1.2 Technical Data ................................................................................................................. 7
1.3 Product Overview ........................................................................................................... 7
SECTION 2 - INSTALLATION ........................................................................................................... 9
2.1 General .............................................................................................................................. 9
2.2 Pre-Installation ................................................................................................................. 9
2.2.1 Receiving Inspection .................................................................................................... 9
2.2.2 Siting ............................................................................................................................... 9
2.3 Electrical Requirements ................................................................................................ 10
2.4 Standard Electrical Customer Connections ............................................................. 10
2.5 Enviromental Requirements ........................................................................................ 10
SECTION 3 – POST INSTALLATION ............................................................................................. 11
3.1 Electrical Installation Testing ...................................................................................... 11
3.2 Mechanical Installation Testing .................................................................................. 11
SECTION 4 - COMMISSIONING .................................................................................................... 12
4.1 Commissioning The Panel ........................................................................................... 12
4.2 Connecting To Boilers .................................................................................................. 12
4.3 Connecting To Slow Open Valves ............................................................................. 12
4.4 Connecting To Thermcouples .................................................................................... 12
4.5 Connecting To Steam Flow Rate Sensor .................................................................. 12
4.6 Connecting To BMS ...................................................................................................... 12

SP-IOMM-2020-1
3
SECTION 5 - OPERATION ............................................................................................................... 13
5.1 General ............................................................................................................................ 13
5.2 Controls ........................................................................................................................... 13
5.2.1 Scope Panel Controls ................................................................................................ 13
5.2.2 Start-Up ........................................................................................................................ 14
5.2.3 Main Screen ................................................................................................................ 16
5.2.3.1 Login .......................................................................................................................... 17
5.2.3.2 Individual Boiler Status .......................................................................................... 18
5.2.3 Status ............................................................................................................................ 19
5.2.4 I/O ................................................................................................................................. 20
5.2.5 Option ........................................................................................................................... 21
5.2.5.1 Logging ...................................................................................................................... 22
5.2.6 Lag / Lead .................................................................................................................... 23
5.2.7 Settings ......................................................................................................................... 24
5.2.7.1 Settings Screen One .............................................................................................. 25
5.2.7.2 Settings Screen Two .............................................................................................. 26
5.2.8 Engineer ....................................................................................................................... 27
5.2.8.1 Engineer Screen One ............................................................................................. 27
5.2.8.2 Engineer Screen Two ............................................................................................. 28
5.2.8.3 Engineer Screen Three .......................................................................................... 29
5.3 Scope Functions ............................................................................................................ 30
5.3.1 Setting Set Points ....................................................................................................... 30
5.3.2 Boiler Change Over ................................................................................................... 30
5.3.3 Slow Opening Valve Control ................................................................................... 30
5.3.3 Scope Shut Down In Emergency Situation .......................................................... 31
5.4 Scope Panel Monitoring ............................................................................................... 31
SECTION 6 - MAINTENANCE ........................................................................................................ 32
6.1 Cleaning ........................................................................................................................... 32
6.2 Weekly ............................................................................................................................. 32
6.3 Six-Monthly ..................................................................................................................... 32
SECTION 7 - TROUBLESHOOTING ............................................................................................. 33
APPENDIX A – SCOPE SPECIFICATION ..................................................................................... 34
Specification ........................................................................................................................... 34
Mechanical Drawing ............................................................................................................ 35
Electrical Drawing - Complete ........................................................................................... 36

SP-IOMM-2020-1
4
I. Warnings & Cautions Explained
For your safety!
The following WARNINGS, CAUTIONS and NOTES appear in various sections of this manual.
•
WARNINGS
must be observed to prevent serious injury or death to personnel.
•
CAUTIONS
must be observed to prevent damage or destruction of equipment or loss of operating
effectiveness.
•
NOTES
must be observed for essential and effective operating procedures, conditions and as a
statement to be highlighted.
It is the responsibility and duty of all personnel involved in the operation and maintenance of this equipment
to fully understand the
WARNINGS, CAUTIONS and NOTES
by which hazards are to be eliminated or
reduced.
Personnel must become familiar with all aspects of safety and equipment prior to operation or maintenance
of the equipment.
II. Warnings & Cautions in Manual
! WARNING !
This product is designed and constructed to withstand the forces encountered during normal use. Use of
the product other than as a Sequencer, or failure to install the product in accordance with these
Instructions, product modifications or repair could:
•Cause personal injury or loss of life
•Cause damage to the product and/or property
•Invalidate
CE
marking
These precautions must, at all times, be stored in a safe place near the product installation.
Product complies with Low Voltage Directive (LVD) 2014/35/EU by meeting requirements found within
BS EN 60204-1:2018
Product complies with Restriction of Hazardous Substances (RoHS) 2011/65/EU by meeting
requirements found within EN IEC 63000:2018
Product complies with Electromagnetic Compatibility Directive (EMC) 2014/30/EU.
This product is suitable for Industrial Class A environments. However, it may be exposed to interference
above the Heavy Industrial Immunity limits if:
•The product or wires to or from are near a radio transmitter
•If excessive electrical noise is present on the mains supply.
•Cellular telephones and mobile radios could cause interference if used within 1 meter of the
product or wires to or from it.
!CAUTION !
It is vitally important that the instructions given in this manual are strictly adhered to. Failure to carry out
the routine maintenance checks could result in a drastic reduction in the life expectancy of the system
and increase the possibility of fire, explosion, property damage, personal injury or loss of life.

SP-IOMM-2020-1
5
III. Safety
The instructions provided for the operation and maintenance of the boiler MUST be observed. Failure to do
so could result in damage to the boiler and serious personal injury.
! WARNING !
! WARNING !
Do not try to do repairs or any other
maintenance work you do not understand.
Obtain a service manual from Fulton Ltd or call a
Fulton service engineer.
Key to gain access to the inside of the panel
should be left with the senior member of staff
responsible for the equipment, or one that has
been empowered by this member and knowing
the risks within an electrical panel.
It is the responsibility of the installer to ensure all
parts supplied with the boiler are fitted in a
correct and safe manner
Adequate lighting should be provided when
access the internals of panel before any work is
completed.
Understand the electrical circuit before
connecting or disconnecting an electrical
component. A wrong connection can cause injury
and or damage.
Correct tools should be used for any work that is
completed upon the panel; these should be listed
in a method statement before work is carried
out.
A defective panel can injure you or others. Do
not operate a panel which is defective or has
missing parts. Make sure that all maintenance
procedures are completed before using the
panel.
ALL Parts and cables before the Isolator may still
be live even when this is turned to off, if work is
to be carried out on this section this must be
isolated first.
LIFTING EQUIPMENT
Make sure that lifting
equipment complies with all local regulations and
is suitable for the job. You can be injured if you
use faulty lifting equipment. Make sure the lifting
equipment is in good condition.
Steam leaks should be frequently looked for
within the facility, this panel can allow steam to
enter the plant based on the program that has
been set up and thus personnel may not be
present to view when this happens and locate
risks.
Operating the panel beyond its design limits can
damage the panel, it can also be dangerous. Do
not operate the panel outside its limits. Do not
try to upgrade the panel performance by
unapproved modifications.
If slow opening valves are fitted these should be
tested as frequently as possible, minimum of
monthly tests, this can be tested via the program.
Non-approved modifications can cause injury and
damage. Contact your Fulton dealer before
modifying the boiler.
Panel has a mass of 23kg, care should be taken
when handling and life risk assessments and
method statements should be completed if
anything beyond the normal handling for the
personnel involved is completed. All parties who
should lift this needs to have access to the mass
of the unit and relevant PPE.

SP-IOMM-2020-1
6
! WARNING !
! WARNING !
Never attempt to operate equipment that has
failed to pass all the safety checks.
Panel in packaging will have a minimum mass of
25kg, care should be taken when handling and
lift risk assessments and method statements
should be completed if anything beyond the
normal handling for the personnel involved is
completed. All parties who should lift this needs
to have access to the mass of the unit.
If any “Manual Reset” limit device trips, DO NOT
reset without determining and correcting the
cause. (Manual Reset Limits may include flame
safeguard, high or low gas pressure, high
pressure limit.)
This equipment should only be used with Fulton
VSRT boilers, unless specified in writing by
Fulton that this is not the case for an application.
Commissioning of the sequencer panel should
only be completed by Fulton personnel or
supervised by Fulton personnel.
!CAUTION !
! CAUTION !
Do not try and amend, remove or change the
program on the PLC.
Obey all laws and local regulations which affect
you and your boiler.
Proper electrical power and type must be
supplied to the panel as per the specification, if
unknown request information from Fulton.
IV. Regulations
Observe the following when working on this system:
•Work on gas equipment must only be carried out by a qualified gas engineer
•Work on electrical equipment must only be carried out by a qualified electrician
•All legal instructions regarding the prevention of accidents
•All legal instructions regarding environmental protection
•The Code of Practice of relevant trade associations
•All current safety regulations as defined by PED, DIN, EN, DVGW, TRGI, TRF, VDE and all locally
applicable standards
•Gas Safety (Installation & Use) Regulations - The appropriate Building Regulation either the Building
regulations, the Building Regulation (Scotland) or Building Regulations (Northern Ireland). - The
Water Fittings Regulation or Water Bylaws in Scotland, - The current I.E.T. Wiring Regulations
! CAUTION !
In case of emergency this panel has been designed and constructed to meet all of the essential
requirements of the applicable European Directives and subject to proper maintenance should not give
occasion to any hazardous conditions.
If such a condition should occur during commissioning or during subsequent operation of this product,
whatever the cause, then the electrical supply to the panel should be isolated immediately, until the fault
has been investigated by a competent person and rectified.

SP-IOMM-2020-1
7
SECTION - 1 INTRODUCTION
1.1 General
Prior to shipment, the following inspections and tests are made to ensure the highest standards of
manufacturing for our customers:
•Material inspections
•Manufacturing process inspections
•Electrical components inspection
•Packing, inspection and final check
This manual is provided as a guide to the correct operation and maintenance of your Fulton equipment, and
should be read in its entirety and be made permanently available to the staff responsible for the operation
of the boiler. It should not, however, be considered as a complete code of practice, nor should it replace
existing codes or standards which may be applicable. Fulton reserves the right to change any part of this
installation, operation and maintenance manual.
Installation, start-up, and maintenance of this equipment can be hazardous and requires trained, qualified
installers and service personnel. Trained personnel are responsible for the installation, operation, and
maintenance of this product, and for the safety assurance of installation, operation, and maintenance
processes. Do not install, operate, service or repair any component of this equipment unless you are
qualified and fully understand all requirements and procedures.
1.2 Technical Data
For a specification, refer to Appendix A – Scope Specification
1.3 Product Overview
The sequencer panel is fitted into a metal industrial electrical cabinet, with a touch screen HMI on the
outside. It is designed to monitor the functions of multiple boilers that are working on the same system,
monitoring normal occurrences such as pressure and flow rate - also errors, faults and alarms.
The sequencer panels purpose is to ensure the boilers are ready for process normally when left overnight so
they don’t fully cool down and can be safely and gradually brought to temperature/pressure. This is because
in normal operation, the boilers be will be powered up quickly when required, if this is done it can cause
fatigue on the boilers and will also cost more money due to the added energy of start-up.
Optional slow opening steam valves can also be installed after the boilers, these will gradually open when
slowly powering up, this will allow the steam system to slowly re-pressurise. This is an advantage because in
a lot of cases as many boiler locations being quickly powered up, the pressure is released very quickly from
the boilers, this causes the condensate within the system’s pipework to be transported through it very
quickly (water hammer) which can lead to significant damage to the system, potentially health and safety
risks and very loud and uncomfortable noises within the system.
The sequencer also automatically switches which boiler(s) (depending on how many are fitted and steam
demand) are taking the lead, which are assisting, and which are in reserve (banked); this will help to ensure
that they are evenly utilised over their life. The SCOPE sequencer panel will also automatically change a
boiler from assist or reserve up to lead or assist with an increased steam demand, so manual intervention is
not required. It will do the opposite in a low demand situation from a high demand. It can also change a
boiler over to a new lead or assist if the current lead or assist is in an alarm situation to ensure seamless
supply of steam, providing of course, that the remaining boilers can cope.
The SCOPE Sequencing panel has optional extras that can be utilised such as controlling of valves after
boilers, hotwell and boiler room temperature monitoring and feedback to BMS central system.

SP-IOMM-2020-1
8
Figure 1.1 - SCOPE Mechanical Drawing

SP-IOMM-2020-1
9
SECTION 2 - INSTALLATION
2.1 General
The installation of a SCOPE Sequencer Panel should be carried out by competent personnel in accordance
with all relevant safety regulations. It is the responsibility of the installer to ensure that these regulations are
complied with.
2.2 Pre-Installation
Prior to delivery, consideration should be given to the following: (planning regulations may call for more
consents than those listed below, always check with your Local Planning Authority).
A. Local Planning consents where appropriate
B. Consideration given to access for delivery and positioning of the panel
C. Preparation of a suitable structure to fit to (see mechanical drawing in 1.3), which must be able to
support the total weight (max 23kg) of the panel under operating conditions. The locations of
services to the site required for the system, under operating conditions. The entirety of the Panel
must be located between 0.6m and 1.7m from the level at which the user will stand on, the boilers
should be visible from the panel location without moving
D. Electricity supply check the loading required/available
E. Suitable access for delivery and off-loading
F. Safe access to the plant when installation is complete. Appropriate front, side and top clearances
must be maintained (see mechanical drawing in 1.3). This will allow access around the equipment to
facilitate maintenance and a safe work environment
2.2.1 Receiving Inspection
The customer should examine the equipment for any damage. It is the responsibility of the installer to
ensure all parts supplied with the equipment are fitted in a correct and safe manner.
2.2.2 Siting
! WARNING !
Failure to provide required and safe access to the equipment could impede commissioning and
maintenance. Service technicians are instructed not to commence commissioning if hazardous conditions
exist.
The panel must be kept closed at all times unless maintenance, installation or commissioning work is being
carried out.
! CAUTION !
The Panel must only be fitted in the orientation shown in Appendix A.
(Reference should be made to Utilisation Procedures as stated in IGE/UP/10 Part 1 Communication 1676,
and in particular to Section 5, Location of Appliances).
The boiler house should be sufficiently sized to allow easy and safe access to all parts of the panel for
operational and maintenance purposes.
Reference should be made to Appendix A – SCOPE Specification and data product submittals to ascertain
the relevant dimensions and weights.

SP-IOMM-2020-1
10
2.3 Electrical Requirements
! CAUTION !
Any electrical work should be undertaken by a qualified electrician to current local regulations.
! WARNING !
Assure all electrical connections are powered down prior to attempting replacement or service of
electrical components or connections of the equipment.
An individual wiring diagram for the boiler is sent with the panel (also in Appendix A). Make sure the
information on the electrical drawing corresponds to your voltage and frequency.
Check the supply voltage and make sure that there is no over-or under-voltage exceeding 10% of the
nominal value.
Note: The power ratings and requirements are given in Appendix A - SCOPE Specification and affixed to the
CE plate.
2.4 Standard Electrical Customer Connections
Steam flow rate - Input
Connect the steam flow rate as per the electrical drawing. This will then receive the 4-20mA signal from the
sensor and log the steam flow rate after the steam header if the sensor is fitted.
Thermocouple plant room temperature - Input
Connect the thermocouple plant room as per the electrical drawing. This will then receive the k-type
thermocouple input signal from the sensor and log the plant room temperature if the sensor is fitted.
Common alarm out - Output
Connect the common alarm out as per the electrical drawing. This will then feedback to the BMS if a
common alarm has occurred on any of the boilers.
Steam pressure re-transmission - Output
Connect the Steam pressure re-transmission as per the electrical drawing. This will then provide an analogue
output to the BMS of the header steam pressure.
2.5 Environmental Requirements
The effects of heat, vibration, shock and electrical interference need to be minimised to as low as possible,
for further information read the safety precautions at the start of the manual.
! CAUTION !
Do not install outdoors without contacting Fulton first and adding further weather protection.

SP-IOMM-2020-1
11
SECTION 3 – POST INSTALLATION
3.1 Electrical Installation Testing
Earth bonding should be tested.
Electric terminals should be tightened.
Cables should be inspected to ensure no exposed conductors are accessible by a small screwdriver or larger.
Internally and externally.
3.2 Mechanical Installation Testing
Supports for the panel must be tested to ensure they can cope with any vibration in the environment.
Any external cable trunking used must be fit for purpose and properly supported.

SP-IOMM-2020-1
12
SECTION 4 - COMMISSIONING
! WARNING !
Commissioning by qualified persons only.
4.1 Commissioning the Panel
It is essential that the commissioning procedures listed below are carried out by a Fulton service engineer
who will have the necessary experience and testing equipment to ensure that the installation is not only
correct but is operating safely and at optimum efficiency.
4.2 Connecting to Boilers
Connect as per electrical drawing.
4.3 Connecting to Slow Open Valves
Connect as per electrical drawing and SOV installation manual. Please note the SOV will need their own
power source and will not be powered via the SCOPE sequencer panel.
4.4 Connecting to Thermocouples
Connect as per electrical drawing and thermocouple installation manual.
4.5 Connecting to Steam Flow Rate Sensor
Connect as per electrical drawing and steam flow rate sensor installation manual.
4.6 Connecting to BMS
Modbus can be connected into the communication port of the HMI screen inside the panel. This feature
must be turned on and enabled in order to use.
Contact your service engineer to ensure this can be used.

SP-IOMM-2020-1
13
SECTION 5 - OPERATION
! CAUTION !
The following instructions are given for the guidance of the operator in the use of the Fulton steam
boiler. No responsibility can be accepted by Fulton Ltd if these instructions are ignored.
5.1 General
The following instructions are given for the guidance of the competent operator in the use of the SCOPE
Sequencing panel and to provide adequate information to ensure that when the panel is put into use it will
be done safely and without risk to health. Where original equipment service manuals are supplied, they must
be read and understood in conjunction with this manual. All warnings and cautions must be observed.
5.2 Controls
The following description of the controls used on the SCOPE Sequencing panel is intended to provide the
operator with a basic understanding of the operating principles, which is essential for the continued efficient
operation of the panel.
5.2.1 Scope Panel Controls
Common alarm input
This is an input from the boiler to say the common alarm has triggered. If the sequencing panel receives this
and the boiler that sends it is the lead it will, after a short delay, switch a boiler in lag/standby to lead. If the
alarm is reset, which requires manual intervention at the boiler, the lead will be switched back to the original
boiler. Up to 4 Inputs. Digital input.
Boiler firing input
Send a signal to the sequencer. Will show on the sequencer HMI that the boiler is running, it will count the
run time of the boiler for records and display purposes. Up to 4 Inputs. Digital input.
Fully opened valve input
Fitted if SOV are fitted. Signal received from the valve that will tell the sequencer panel a valve is fully open;
the sequencer panel will stop sending the signal to open the valve. Up to 4 Inputs. Digital input.
Fully closed valve input
Fitted if SOV are fitted. Signal received from the valve that will tell the sequencer panel a valve is fully
closed; the sequencer panel will stop sending the signal to close the valve. Up to 4 Inputs. Digital input.

SP-IOMM-2020-1
14
Low water indication input
Signal received that the boiler has low water. Will display that it has occurred and count occurrences.
Sequencer panel will not action from this as common alarm will also be received in this circumstance and the
program will take action from this. Up to 4 Inputs. Digital input.
Boiler pressure input
A 4-20mA Input, representing the boiler pressure. Sequencer panel will display this data. If a boiler can’t
maintain the pressure set point for a nominal time (usually 30 minutes) then a further boiler will have its set
point increase to help maintain the demand. Up to 4 Inputs. Analogue input.
Boiler demand input
A 4-20mA Input, representing the demand on the boiler. This is a signal received from the boiler and based
off the burner duty. If the boiler shows a demand of 80% or over for a customer set time, then a further
boiler will have its set point increased to help with the demand. If demand changes back and is considerably
more than needed it will drop the set point of the secondary boilers. Up to 4 Inputs. Analogue input.
Steam header pressure input
A 4-20mA Input, that will be set from 0-100%, fitted at the steam header after all valves join that will
display and record on the panel the pressure going to the plant (if steam header pressure sensor is fitted).
Analogue input.
Steam flow rate input
A 4-20mA Input, that will be set from 0-100%, set based on input upon commissioning. Will be used if a
flow rate monitor is fitted after a boiler. Logged and displayed visually on the sequencer panel Analogue
input.
Thermocouple plant room temperature input
A K-type thermocouple, based on min to max temperature set on site. Always set in a high position which is
above the boiler(s), must be fitted near the boilers. Will visually show the temperature on the sequencer
panel and log it (if plant room thermocouple is fitted).
5.2.2 Start-Up
! CAUTION !
It is recommended that the first power up is completed by a Fulton Engineer.
Steam leaks within the overall system should be thoroughly checked for and prevented before powering
up the SCOPE system.
If Slow Opening Valves are installed, they should be checked to be in good operation and condition
before being brought into service.
Before the SCOPE panel is switched on all boilers should be turned on and brought up to normal operating
pressure/temperature as per the boiler instruction manual.
The initial set up must be completed by a trained Fulton engineer to ensure that the Control methodology in
place matches that of the steam generation and distribution system. Once this initial set up has taken place,
it will be safe to power up the SCOPE system and put it online.
The SCOPE start-up routine can vary depending on what equipment is installed. The longest will be if slow
opening steam distribution control valves are installed as these must home themselves, so the SCOPE panel
knows their location.

SP-IOMM-2020-1
15
After approximately 60 seconds the SCOPE animated logo will appear on screen and a push button as
indicated below.
At this point further checks should be made that the Steam System is both safe and ready to be put into
operation.
! CAUTION !
Before the SCOPE system is brought online ensure all boilers and associated equipment’s safety checks
according to their respective operation manual have been completed, only then can SCOPE be started, if
in doubt
do not
enable.
The start button can now be pressed.
If the Slow opening valve system is being employed, then at this point the steam valves will all be driven to
the closed position if they are not already.
Once this action has been completed the SCOPE system will either commence automatically sequenced
operation of the steam boilers or if the sequencing has not been set up the panel will await the inputs in
order to begin sequencing.
The “Main Screen will then be shown (Figure 5.1). This shows a graphical representation of the boilers
connected to scope. The picture will be representative of the boiler that is installed.
Figure 5.1 - SCOPE

SP-IOMM-2020-1
16
5.2.3 Main Screen
Below (figure 5.2) is the main screen for SCOPE.
•
Menu – Left hand side
o The “Main” button returns to the Main/Home page seen in figure 5.2
o The “Status” button takes the user to a screen giving information on the boilers
o The “I/O” button takes the user to a breakdown of what options are available and on
o The “Option” button allows the viewing of data relating to the installed options
o The “Lag/Lead” button allows the change of set-points
o The “Settings” button allows the user to change basic configurations
o The “Engineer” button allows the engineer to change advanced configurations
•
Middle Section
o Along the top of the screen there is the Fulton logo, date and time
o If the Fulton logo is pressed it will provide the contact details of Fulton
o At the top right is the date and time, if this is pressed access can be gained to the login
o Below this is the readouts there are two system overviews displayed:
o Header pressure after the boilers
o Total demand as a percent
o Below this is the boiler read outs which shows the following
o A graphical representation of the boiler – if pressed takes to the individual boiler status –
5.2.5
o Demand on boiler - bar chart
o Pressure of boiler from 0-13.8 bar g for VSRT - bar chart
o Position of slow opening valve if fitted, fully blue means fully open - bar chart
o Four indicators:
o Highest one indicates setpoint Lead (green), Banked (yellow), Lag (yellow), off (red)
o Middle one is Valve position open or closed; Open (green), Shut (red), Opening or Closing
o Bottom one is whether this boiler is being sequenced; SEQON – green, SEQOFF red
Figure - 5.2 Main Screen

SP-IOMM-2020-1
17
5.2.3.1 Login
To access the login screen to gain further functionality the date and time can be pressed. There are four
login statuses:
•
Operator
o Very limited functionality, predominantly a viewing login
•
Manager
o Can change functionality
•
Service
o Can change functionality as to how the SCOPE sequencer panel works within the
“Engineer” section
•
Admin
o Full functionality

SP-IOMM-2020-1
18
5.2.3.2 Individual Boiler Status
If a boiler is pressed on the “Main” screen the individual boiler status will be shown. To return to the original
screen press “Main” on the left-hand side.
There are a number of statuses:
• The screen shows the boiler type, serial number and date of manufacture
• The time since last service (set during service engineer visit)
• Whether the boiler is powered up or off (status)
• Whether the burner is on or off
• The total hours the boiler has run for and its pressure
• Whether a service is due soon, immediately or not at all
It is also possible to change to next or previous boiler by pressing the respective buttons.
Figure 5.3 – Individual Boiler

SP-IOMM-2020-1
19
5.2.3 Status
This screen shows the current functionality of all boilers connected to the SCOPE sequencer panel. It will be
split down per boiler.
From top to bottom the screen shows:
• Current status of the boiler with respect to its setpoint:
o Lead
o Assist
o Lag
o Banked
o Off
• Steam pressure inside the boiler
• The total hours the boiler has run while connected to the panel
• Total number of common alarm occurrences
• Total number of low water occurrences
• Total number of boiler lockouts occurrences
• Individual boiler demand on each individual boiler
• Slow open valve position, can be:
o Open
o Closed
o Fault
Figure 5.4 - Status

SP-IOMM-2020-1
20
5.2.4 I/O
The I/O screen is for fault finding and shows the current status of all I/O functions to and from the
sequencer panel. For info on each see electrical drawing in appendix.
The ones in the middle section are inputs and outputs and will either be on or off.
The ones on the right-hand side are analogue inputs and outputs.
Figure 5.5 – I/O
Table of contents
Popular Recording Equipment manuals by other brands

Panasonic
Panasonic WJHD309A - DIGITAL DISK RECORDER Network set instructions
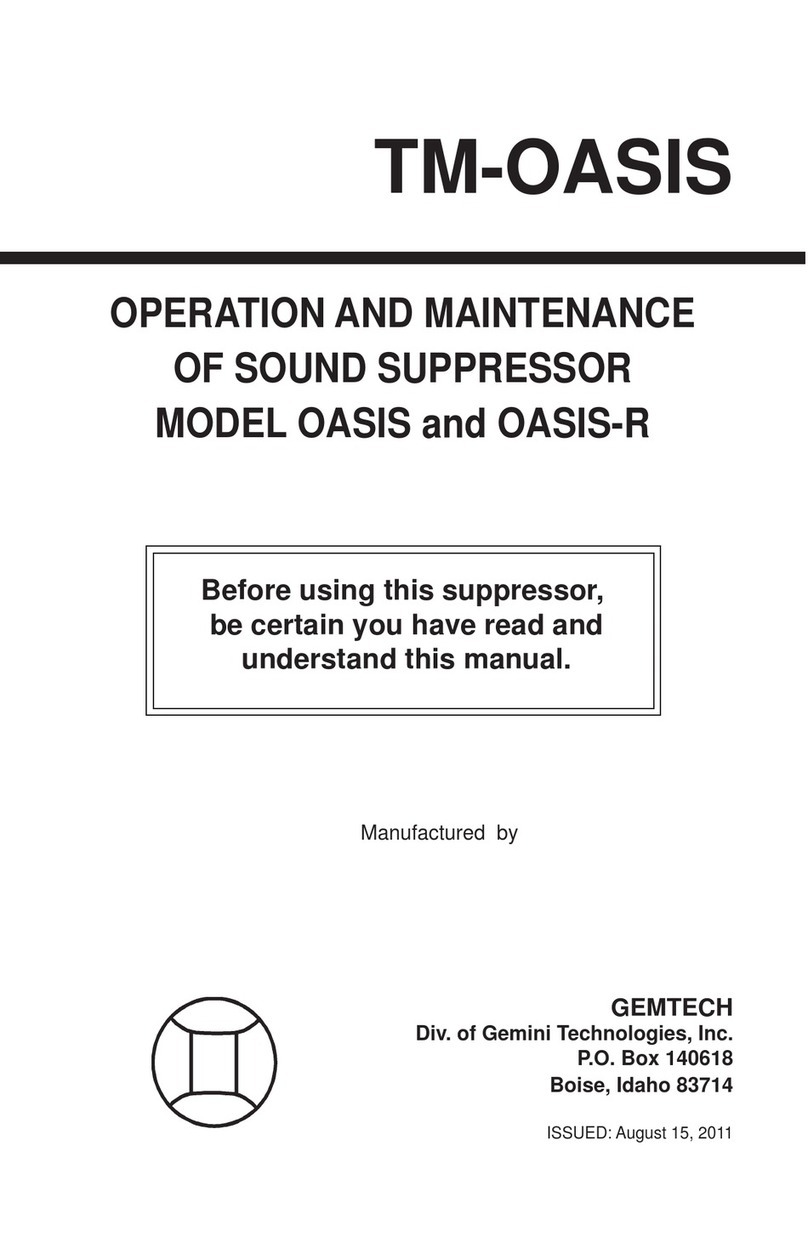
Gemtech
Gemtech OASIS Operation and maintenance instruction
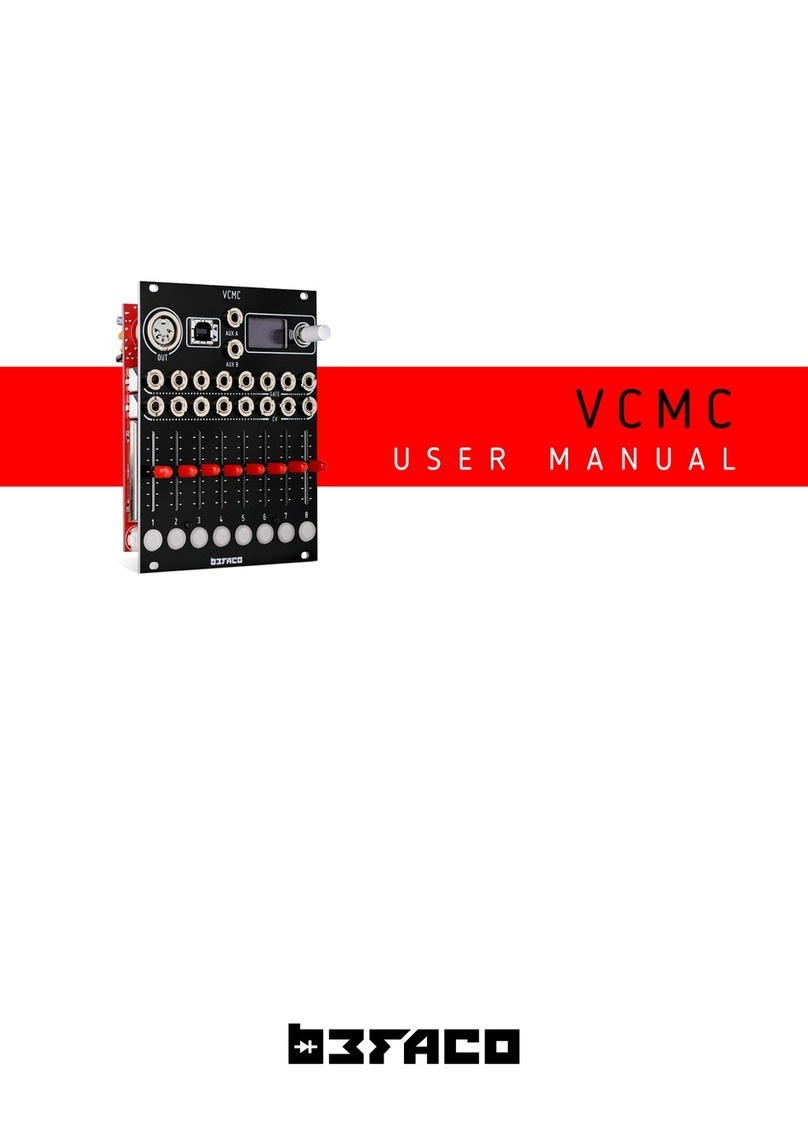
Befaco
Befaco VCMC user manual
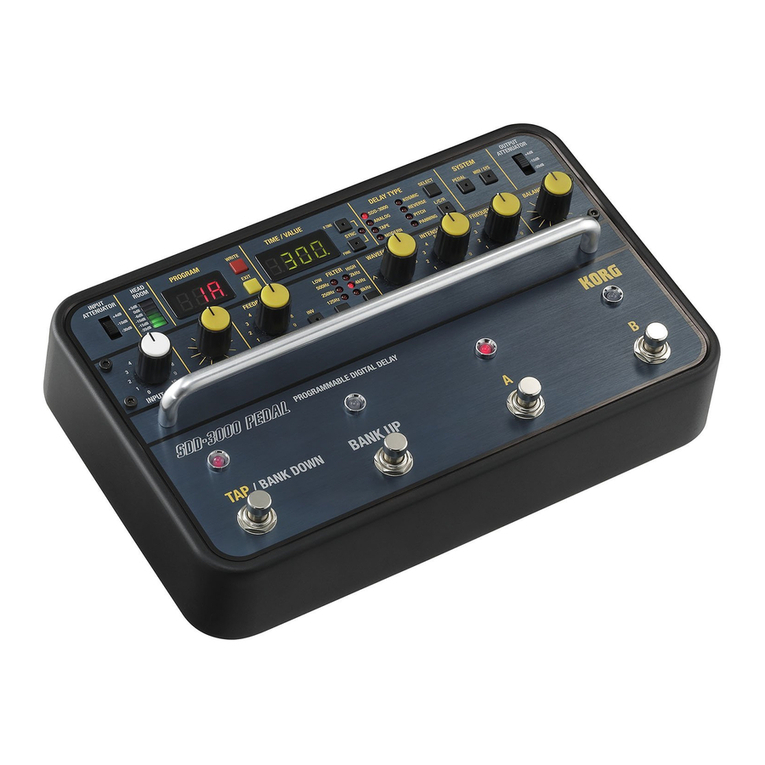
Korg
Korg SDD-3000 owner's manual
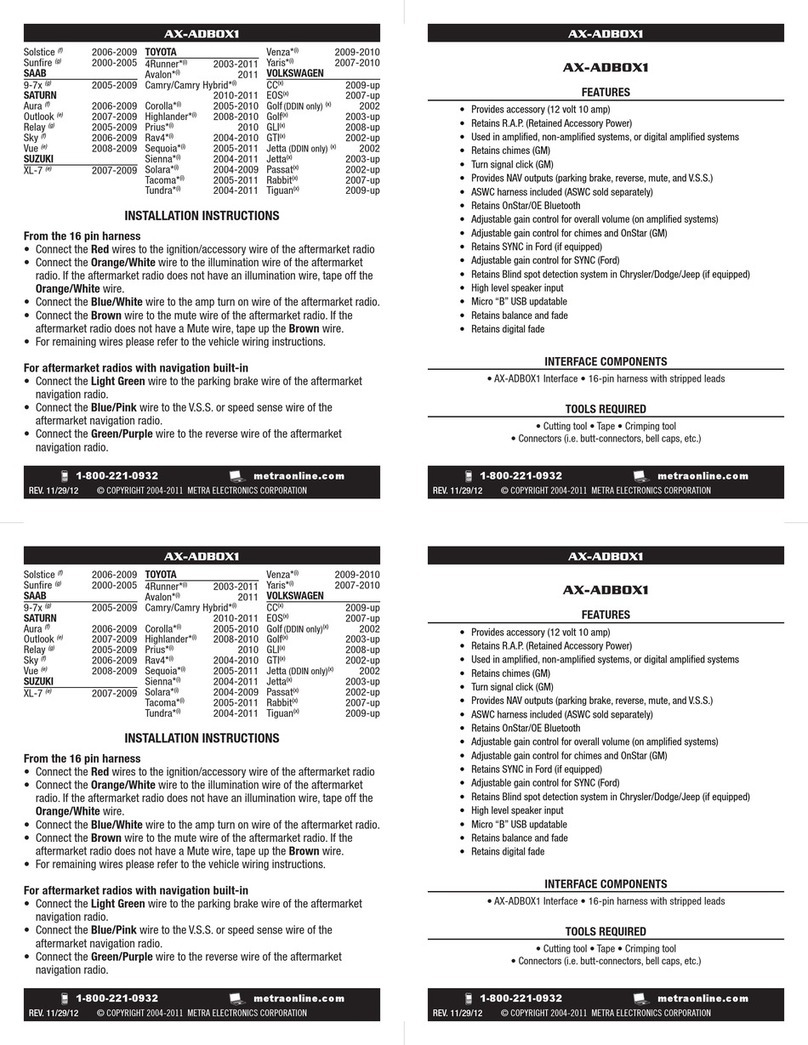
Metra Electronics
Metra Electronics AX-ADBOX1 installation instructions

Riedel
Riedel RiFace installation guide