Galaxy GS-105HS User manual

1
Operation Manual
(GS-105HS)
Safety Instructions
When using your heat press,
basic precautions should be followed,
including the following:
1. Read all instructions.
2. Use heat press only for its intended use.
3. To reduce the risk of electric shock, do not immerse the heat press in water or
other liquids.
4. Never pull power cord to disconnect from outlet, instead grasp plug and pull to
disconnect.
5. Do not allow power cord to touch hot surfaces, allow heat press to cool completely
before storing.
6. Do not operate heat press with a damaged cord or if the equipment has been
dropped or damaged. To reduce the risk of electric shock, do not disassemble or
attempt to repair the heat press. Take it to a qualified service person for
examination and repair. Incorrect assembly or repair could increase the risk of fire,
electric shock, or injury to persons when the equipment is used.
7. This appliance is not intended to be used by persons (including children) with
reduced physical, sensory or mental capabilities, or lack of experience and
knowledge, unless they have been given supervision or instruction concerning
use of the appliance by a person responsible for their safety.
8. Close supervision is necessary for any heat press being used which can be sure
to keep children away from the equipment. Do not leave equipment unattended
while connected.
9. Burns can occur when touching hot metal parts.
10. To reduce the likelihood of circuit overload, do not operate other high voltage
equipment on the same circuit.
11. If an extension cord is necessary, then a 20-amp rated cord should be used.
Cords rated for less amperage may overheat. To arrange the cord in a correct way
so that it cannot be pulled or tripped over.

2
Table of Contents
Safety Instructions……………………….1
Technical Parameters……………………3
Machine View…………………………….4
Control Panel Guide……………………...5
Operating Instructions……………………6-10
⚫Assemble the Control Box……………………………………………6
⚫Connecting the System……………………………………………....7
⚫Ramspin system (Auto& Manual switch) …………………………...7
⚫Turning the System On…………………………………….…………8
⚫Adjusting the Temperature…………………………………………...8
⚫Adjusting the Time………………………………………………….....8
⚫Adjusting the Pressure………………………………………………..9
⚫Printing and Pressing………………………………………………....9
⚫Counter Setting………………………………………………………..9-10
⚫Switch Between F/C…………………………………………………..10
⚫Temperature Calibration……………………………….………………10
Exploded Views and Parts List…………12-16
Electrical Schematic……………………..17

3
Technical Parameters (GS-105HS)
Model:
GS-105HS-1620
Heater Size:
16’’×20’’
Pressure Display:
Yes
Auto Open:
Yes / Can also be setup as a Manual
Operation Press
Slide-out Lower Platen:
Yes
Power(110volt)
1800W/16.4Amps
Temperature Range:
Max. 430℉/ 221℃
Heating Up Time(180℃)
20 minutes
Time Range:
0~999S
Platen Exchange System
“Ramlock”quick change system
Optional Lower Platens (*Sold
Separately)
4’’×4’’
11’’×15’’
8’’×10’’
6’’×20’’
6’’×10’’
15” ×15”
Size (open) :
29.5”x 16.9”x 39.3”
Packing Size:
33.1”x 20.5”x 23.4”
Packing Weight:
119.0lbs
Certificate:
CE, FCC
Machine View

4

5
Control Panel Guide
Operation Instructions

6
Assemble the Control Box
1. ASSEMBLE THE CONTROL BOX
1.1 Take out control box inside of the
packing carton, then place the control
box on top of the machine in the right
position. (figure 1.1)
1.2 Fasten the control box onto the
machine with 4 screws tightly. (figure
1.2)
1.3 Connect 5 phase aviation plug and 2
phase aviation plugs, then fasten
tightly. (figure 1.3)
ATTNTION: the aviation plug must be
connected tightly. (figure 1.4)
CAUTION
A sway connector will cause burning.
Ensure the connector is secure.

7
Connecting the System
2. CONNECT THE POWER CORD
2.1 Connect the power cord into a properly grounded electrical outlet with a sufficient
amperage rating.
⚫VOLTAGE
110 Volt –The GS-105(HS) requires a full 20-amp grounded circuit for 110-volt
operation.
⚫EXTENSION CORDS If used, should be as short as possible and not less than
12 gauge. Heavy duty cords are recommended.
⚫CIRCUITS that have less than 15 amps or that have other high demand
equipment or appliances (especially more than one heat seal machine) plugged
in, should not be used.
NOTE: If the supply cord is damaged, be sure to contact the manufacturer, its service
agent or a similar qualified person for a replacement to avoid hazard
CAUTION Failure to follow these instructions will cause:
1) Erratic controller functions. 2) Inaccurate displays and slow heat-up. 3) The circuit
breaker to disengage.
Ramspin system (Auto& Manual switch)
11.1 When the Ramspin system (Auto
& Manual switch) is facing down,
the machine will automatically open
after pressing is complete. (fig.11.1)
11.2 When the magnetic plate is facing
up, the machine needs to be
opened manually. (fig.11.2)

8
Turn on the System
3. Switch the System On
Adjusting the Temperature
4. ADJUST THE TEMPERATURE
4.1 Press “SET” button. “Set Temp”
lights located in the display will
illuminate. (figure 4.1)
4.2 Next, press the UP and DOWN
Arrow to increase or decrease the
figure to set the Temperature. The
temperature setting range is 170° F
(76° C) to 430° F (220° C).

9
Adjusting the Time
5. ADJUST THE TIME
Counter Setting
6. COUNTER SETTING (Used to show how many completed presses you have
done)
5.1 Once you have set your target
Temp., press the “SET” button
again. “Set Time”lights located in
the display will illuminate. (figure
5.1)
5.2 Next, press UP and DOWN Arrow
to increase or decrease the figure
to set the Time. The time setting
range is from 0 to 999S.
6.1 Once you have adjusted the time, press
“SET” button again. “Counter”lights
located in the display will illuminate
indicating. (figure 6.1)
6.2 You can press “SET”button to quit the
setting if you do not want to set the
Counter or you can press UP and
DOWN Arrow to adjust the counter if
needed. The counter setting range can
be set from 0~999.

10
Adjusting the Pressure
7.ADJUST THE PRESSURE
PRESSURE READOUT
REMEMBER: To allow for the thickness of your garment when adjusting the pressure.
Printing and Pressing
8.PRESS
NOTE: Please be aware after time is complete, gas shocks will automatically release
the platen into the “UP” position.
7.1 First, locate the LED Display on the
Press. The Pressure Adjustment Knob
is located in the center of the heat platen
(See figure 7.1)
7.2 To adjust the Pressure, simply turn the
Pressure Adjustment Knob to the right
or clockwise to increase the Pressure
and to the left or counterclockwise to
decrease the Pressure. The readout will
display the Pressure when locked down
in the print position.
7.3 A visual Pressure Readout is located on
the lower right side of the LCD Display.
When the handle is locked into the Print
Position, a pressure number will be
displayed. Readout will be on a scale of
0 - 9.A 0 Pressure readout would
indicate no pressure at all and 9 would
indicate very heavy pressure. (See
figure 7.3)
⚫Once your equipment has reached the designated temperature.
⚫Position the garment and application on the lower platen.
⚫Lower and lock the heat platen into the press position. Closing the press will
start the automatic timing process.
⚫The timer will automatically count down and lift the heat platen into the “UP”
position when the press cycle is complete.
7.1

11
Switch Between Fahrenheit and Celsius
9.Switch Between F/C
Temperature Calibration
10.Temperature Calibration
10.1 Press the DOWN Arrow and “SET”
button together and hold for 3
seconds, “Calibrate”lights located
in the display will illuminate
indicating you are in the adjust
temperature calibration mode.
(fig.10.1)
9.1 Press the UP Arrow and “SET”
button together and hold for 3
seconds to switch between
Fahrenheit and Celsius. F/C
indicator in display will show the
result. (fig.9.1)
10.2 Press UP and Down Arrow to set
correct temperature value. Press
“SET”button to quit.

12
Exploded Views
No.
Part Name
Part No.
Qty.
1
Display overlay
1600549
1
2
Control box top
1200446
1
3
Circuit breaker 18A
1800349
1
4
On/off switch
1800346
1
5
Emergency stop button
1200579
1
6
socket
1800344
1
7
Triac
1800586
1
10
Cooing sheet
1300672
1
11
Terminal Block
1800345
1
12
Circuit Board
1800353
1
13
Magnet switch
1801814
1
14
Magnet
1800609
1
15
Control box base
1200685
1

13
16
5 phase aviation plug (Female) with wires welded
1800955
1
17
2 phase aviation plug (Female)with wires welded
1800962
1
18
Machine handle
J.03.05.0568
2
19
Machine arm
1200409
2
20
Washer 20-13-15
2000296
2
21
Lift links
1200139
2
23
Machine body
1200397
2
24
Supporting block
1200043
3
25
Rubber foot
1800317
4
26
Machine foot
1200649
2
27
Stud 10-72.5 GC1-21B
1200051
1
28
Bridle links
1200218
2
29
Lower platen holding base
1200230
1
30
Gas spring 350N
1800055
2
31
Position block
1200264
2
32
Threaded Pin 13-164
1200050
1
33
Threaded Pin 12-89
1200074
1
34
Handle shaft
1200145
1
35
Foam Grip
1300155
1
36
Screw M8*16
1901071
1
37
Adjustment spindle base
1800142
1
39
Adjustment spindle
1800087
1
40
Thermocouple
1800281
1
42
Balance screw
1901074
1
43
Thermostat
1800133
1
44
Lower platen
1800388
1
45
Adjustment knob
1800479
1
46
Silicon pad
1200539
1
47
Platen holding block
1200042
1
48
Heat platen 16*20
1800386
1
49
Electromagnet 800N
1200981
1
50
Electromagnet holding sheet
1200067
1
51
Rubber foot
1200605
1
52
Holding sheet
J.03.05.0571
1
53
Holding sheet screw
1200659
1
55
Heat platen cover 16*20
1200450
1
56
PP tube
1800835
1
57
5 phase aviation plugs (Male) with wires welded
1800954
1
58
Heating plate cover connecting plate 16*20
J.03.05.0633
1
59
Elastic glass bead screw M8
J.03.06.0210
2
60
Step bolt M6-8*12
J.03.06.0092
2
61
Cap nut M8
J.03.06.0086
2
62
Brace plate
J.03.05.0572
1

14
Sliding System
No.
Part Name
Part No.
Qty.
1
Cooper bush
1200075
4
3
Sliding Lower Platen Base
1200426
1
4
Supporting Block
1200052
1
4
Bearing block
1200648
4
5
Plated bar fixed board
1200044
2
6
Plated bar
1701037
2
7
O shape washer
1200309
4

15
“RAMLOCK”System
No.
Part Name
Part No.
Qty.
1
Ramlock base
1200958
1
2
Ramlock locking sheet
1200960
1
3
Ramlock locking set (male)
1200961
1
4
Ramlock locking screw
1900959
1
5
Ramlock handle
1200956
1
6
Ramlock locking set (female)
1200957
1
Optional Platens (*Sold Separately)
Part Name (SKU)
Size
LTPPLATENSETRAM-0404
4in x 4in
LTPPLATENSETRAM-0610
6in x 10in
LTPPLATENSETRAM-0620
6in x 20in
LTPPLATENSETRAM-0810
8in x 10in
LTPPLATENSETRAM-1515
15in x 15in
LTPPLATENSETRAM-1115
11in x 15in

16
Electrical Schematic
This manual suits for next models
7
Table of contents
Other Galaxy Power Tools manuals
Popular Power Tools manuals by other brands
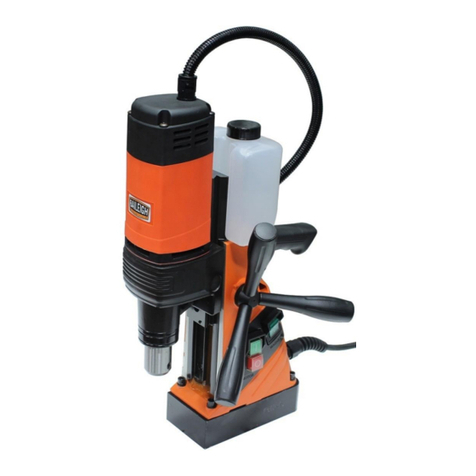
Baileigh
Baileigh MD-3510 Operator's manual
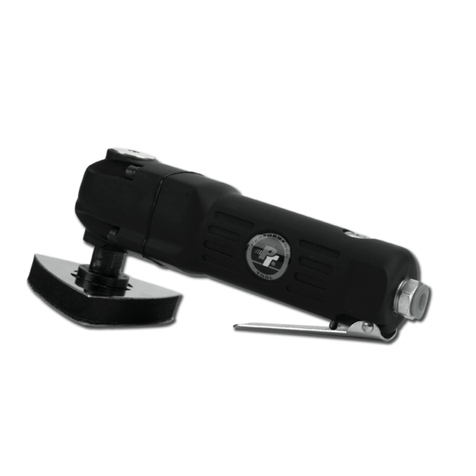
Performance Tool
Performance Tool M546 owner's manual

Baumuller
Baumuller b maxx BM4400 Instruction handbook
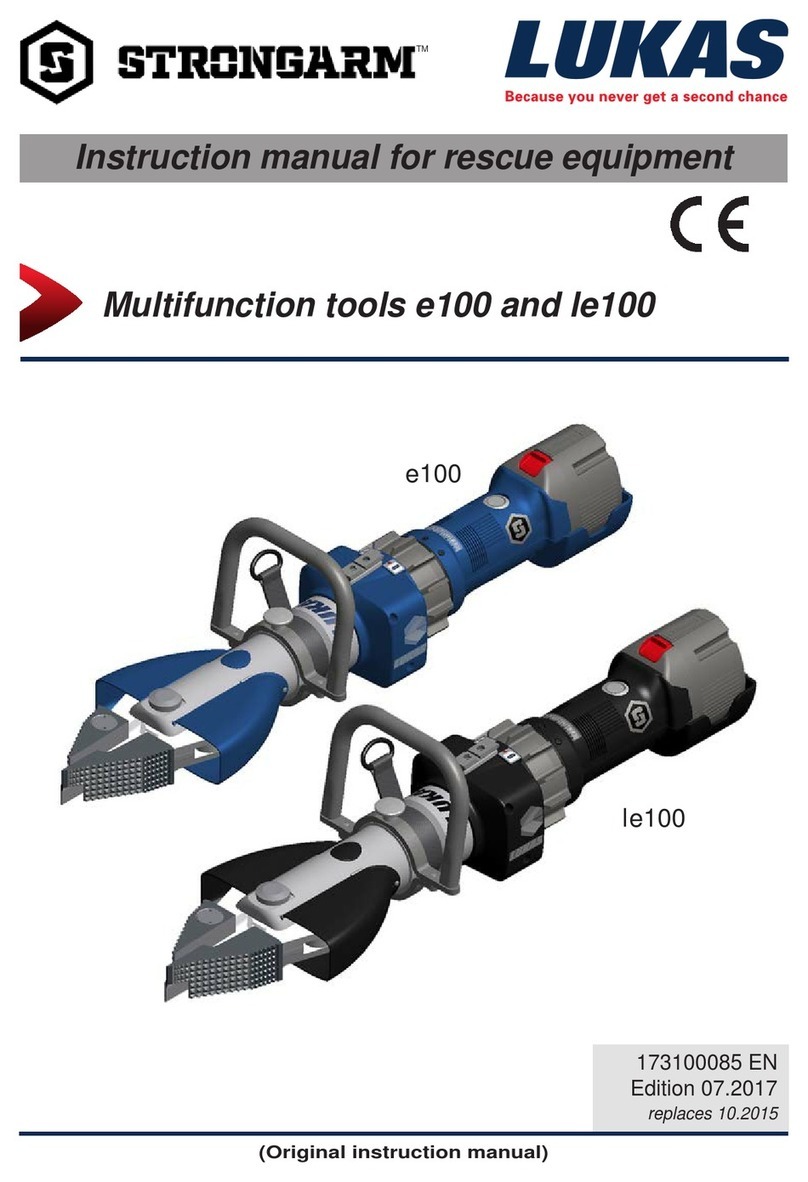
Lukas
Lukas STRONGARM e100 Original instruction manual
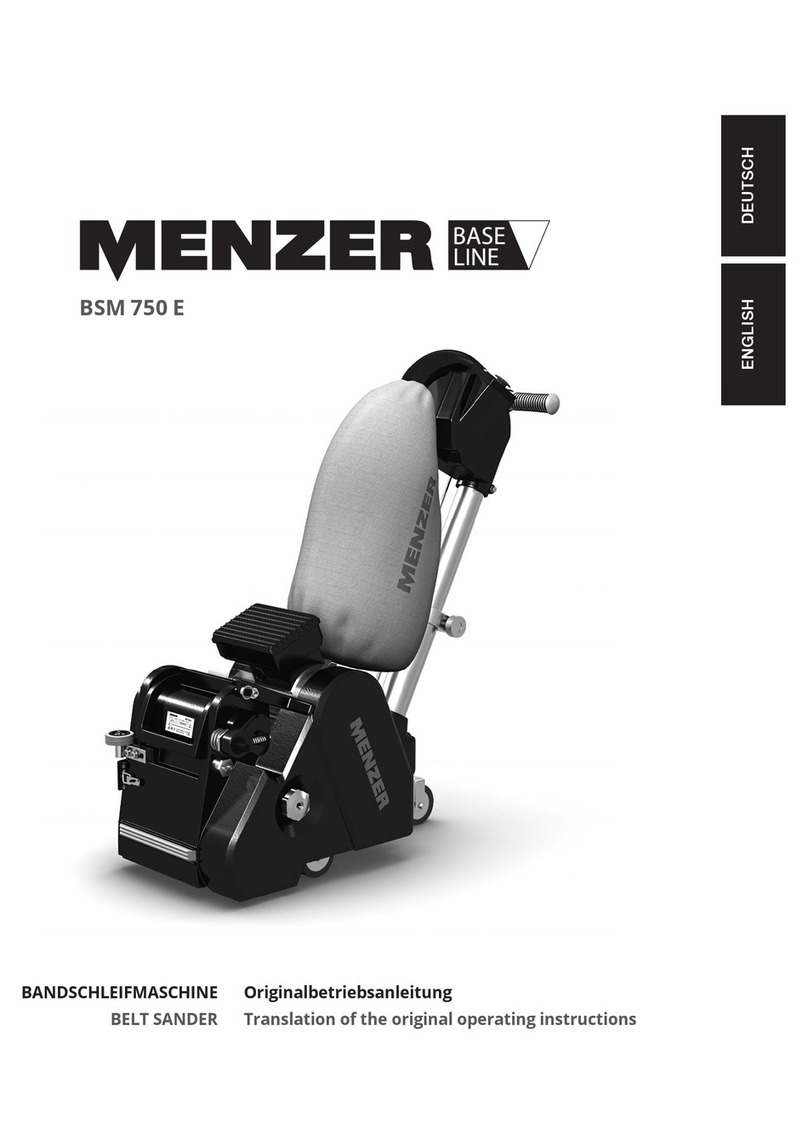
Menzer
Menzer BSM 750 E Original operating instructions
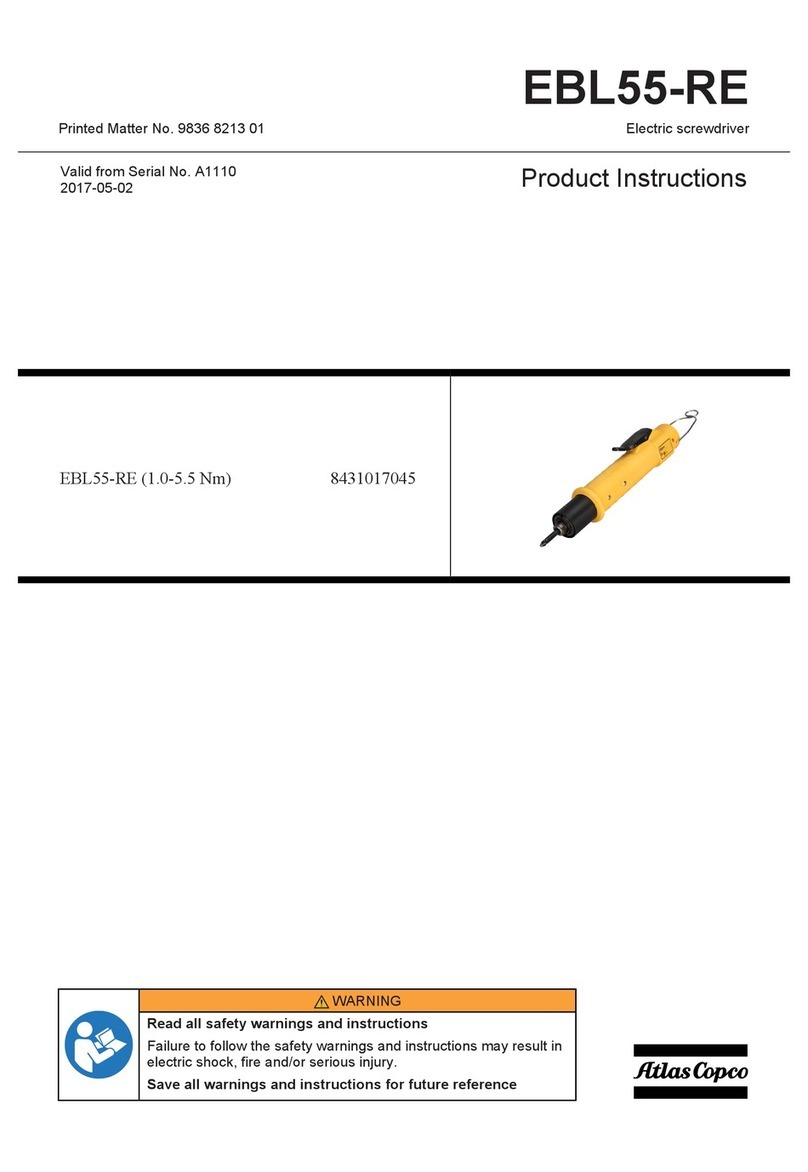
Atlas Copco
Atlas Copco EBL55-RE Product instructions