GE Grid Solutions Multilin 9450 User manual

*1601-0159-A7*
GE
Grid Solutions
Multilin™ 9450/9650
Advanced Power Quality Metering System
Instruction Manual
Software Revision: 1.32
Manual P/N: 1601-0159-A7
Manual Order Code: GEK-113281F
LISTED

ii
Copyright © 2017 GE Multilin Inc. All rights reserved.
EPM 9450/9650 Instruction Manual for product revision 1.32.
The contents of this manual are the property of GE Multilin Inc. This documentation is
furnished on license and may not be reproduced in whole or in part without the permission
of GE Multilin. The manual is for informational use only and is subject to change without
notice.
Part number: 1601-0159-A7 (May 2017)

iii
GENERAL SAFETY PRECAUTIONS
Note • Failure to observe and follow the instructions provided in the equipment manual(s)
could cause irreversible damage to the equipment and could lead to property
damage, personal injury and/or death.
• Before attempting to use the equipment, it is important that all danger and
caution indicators are reviewed.
• If the equipment is used in a manner not specified by the manufacturer or
functions abnormally, proceed with caution. Otherwise, the protection provided by
the equipment may be impaired and can result in Impaired operation and injury.
• Caution: Hazardous voltages can cause shock, burns or death.
• Installation/service personnel must be familiar with general device test practices,
electrical awareness and safety precautions must be followed.
• Before performing visual inspections, tests, or periodic maintenance on this device
or associated circuits, isolate or disconnect all hazardous live circuits and sources
of electric power.
• Failure to shut equipment off prior to removing the power connections could
expose you to dangerous voltages causing injury or death.
• All recommended equipment that should be grounded and must have a reliable
and un-compromised grounding path for safety purposes, protection against
electromagnetic interference and proper device operation.
• Equipment grounds should be bonded together and connected to the facility’s
main ground system for primary power.
• Keep all ground leads as short as possible.
• At all times, equipment ground terminal must be grounded during device
operation and service.
• In addition to the safety precautions mentioned all electrical connections made
must respect the applicable local jurisdiction electrical code.
• Before working on CTs, they must be short-circuited.
This product cannot be disposed of as unsorted municipal waste in the European
Union. For proper recycling return this product to your supplier or a designated
collection point. For more information go to www.recyclethis.info.

iv
Safety Words and Definitions
The following symbols used in this document indicate the following conditions.
Note Indicates a hazardous situation which, if not avoided, will result in death or serious
injury.
Note Indicates a hazardous situation which, if not avoided, could result in death or serious
injury.
Note Indicates a hazardous situation which, if not avoided, could result in minor or
moderate injury.
Note Indicates significant issues and practices that are not related to personal injury.
NOTE
Indicates general information and practices, including operational information and
practices, that are not related to personal injury.
For further assistance
For product support, contact the information and call center as follows:
GE Grid Solutions
650 Markland Street
Markham, Ontario
Canada L6C 0M1
Worldwide telephone: +1 905 927 7070
Europe/Middle East/Africa telephone: +34 94 485 88 54
North America toll-free: 1 800 547 8629
Fax: +1 905 927 5098
Website: http://www.gegridsolutions.com/multilin
Warranty
For products shipped as of 1 October 2013, GE warrants most of its GE manufactured
products for 10 years. For warranty details including any limitations and disclaimers, see
our Terms and Conditions at https://www.gegridsolutions.com/multilin/warranty.htm
For products shipped before 1 October 2013, the standard 24-month warranty applies.

EPM 9450/9650 ADVANCED POWER QUALITY METERING SYSTEM – INSTRUCTION MANUAL TOC–1
Table of Contents
1: THREE-PHASE POWER
MEASUREMENT
THREE PHASE SYSTEM CONFIGURATIONS ........................................................................... 1-1
WYE CONNECTION .......................................................................................................................... 1-1
DELTA CONNECTION ...................................................................................................................... 1-3
BLONDEL’S THEOREM AND THREE PHASE MEASUREMENT ......................................... 1-5
POWER, ENERGY AND DEMAND ............................................................................................... 1-6
REACTIVE ENERGY AND POWER FACTOR ............................................................................. 1-9
HARMONIC DISTORTION .............................................................................................................. 1-11
POWER QUALITY .............................................................................................................................. 1-14
2: METER OVERVIEW THE EPM 9450/9650 SYSTEM ..................................................................................................... 2-1
DNP V.3.00 LEVEL 1 AND 2 .......................................................................................................... 2-2
FLICKER ................................................................................................................................................ 2-2
COMM OPTION 2: INTERNAL MODEM WITH DIAL-IN/DIAL-OUT OPTION ............... 2-3
HARDWARE OVERVIEW ....................................................................................................... 2-3
DIAL-INFUNCTION ............................................................................................................. 2-3
DIAL-OUT FUNCTION ......................................................................................................... 2-3
TOTAL WEB SOLUTIONS ............................................................................................................... 2-4
HARDWARE OVERVIEW ....................................................................................................... 2-4
HARDWARE CONNECTION .................................................................................................. 2-4
SOFTWARE OVERVIEW ........................................................................................................ 2-4
NETWORK SETTINGS ........................................................................................................... 2-5
MEASUREMENTS AND CALCULATIONS .................................................................................. 2-6
DEMAND INTEGRATORS ............................................................................................................... 2-9
ORDERING ........................................................................................................................................... 2-12
ORDER CODES ..................................................................................................................... 2-12
EXTERNAL MODULES .......................................................................................................... 2-12
ACCESSORIES ....................................................................................................................... 2-13
EPM 9450/9650 METER SPECIFICATIONS ............................................................................. 2-14
POWER SUPPLY ................................................................................................................... 2-14
INPUTS .................................................................................................................................. 2-14
PHYSICAL .............................................................................................................................. 2-14
ENVIRONMENTAL ................................................................................................................. 2-15
TESTING AND CERTIFICATION ............................................................................................. 2-15
EPM P40NPLUS LED EXTERNAL DISPLAY SPECIFICATIONS ............................................. 2-16
EPM P60N LCD EXTERNAL DISPLAY SPECIFICATIONS ..................................................... 2-16
UPGRADING THE EPM 9650 METER’S SOFTWARE OPTION ........................................... 2-16
3: HARDWARE
INSTALLATION
MOUNTING THE EPM 9450/9650 METER .............................................................................. 3-1
MOUNTING THE EPM P40NPLUS LED EXTERNAL DISPLAY .............................................. 3-4
MOUNTING THE EPM P60N LCD EXTERNAL DISPLAY ...................................................... 3-5
MOUNTING THE EPM EXTERNAL I/O MODULES ................................................................. 3-7
4: ELECTRICAL
INSTALLATION
CONSIDERATIONS WHEN INSTALLING METERS ................................................................. 4-1
WIRING THE MONITORED INPUTS AND VOLTAGES .......................................................... 4-3
FUSING THE VOLTAGE CONNECTIONS .............................................................................. 4-3
WIRING THE MONITORED INPUTS - VREF ....................................................................... 4-3

TOC–2 EPM 9450/9650 ADVANCED POWER QUALITY METERING SYSTEM – INSTRUCTION MANUAL
WIRING THE MONITORED INPUTS - VAUX ...................................................................... 4-3
WIRING THE MONITORED INPUTS - CURRENTS .............................................................. 4-3
ISOLATING A CT CONNECTION REVERSAL ............................................................................ 4-4
INSTRUMENT POWER CONNECTIONS .................................................................................... 4-5
WIRING DIAGRAMS ......................................................................................................................... 4-6
5: COMMUNICATION
WIRING
COMMUNICATION OVERVIEW .................................................................................................... 5-1
RS232 CONNECTION (PORT 1) .................................................................................................... 5-5
RS485 COMMUNICATION ............................................................................................................. 5-6
RS485 CONNECTION ......................................................................................................... 5-7
CONNECTION TO AN RS485 MASTER ............................................................................. 5-7
RS485 CONNECTION TO THE EPM P40NPLUS OR P60N EXTERNAL DISPLAY .... 5-8
RJ11 (TELEPHONE LINE) CONNECTION—EPM METER WITH INTERNAL MODEM OPTION
(COMM OPTION 2) TO A PC .......................................................................................................... 5-9
RJ45 CONNECTION—EPM METER WITH INTERNAL NETWORK OPTION (COMM OPTION 1)
TO MULTIPLE PCS - 10/100BASET ............................................................................................ 5-9
COMMUNICATION PORTS ON THE EPM I/O MODULES ................................................... 5-9
RS485 CONNECTION—EPM METER TO EPM I/O MODULES .................................... 5-9
STEPS TO DETERMINE POWER NEEDED ........................................................................... 5-10
LINKING MULTIPLE EPM METERS IN SERIES ......................................................................... 5-11
REMOTE COMMUNICATION OVERVIEW ................................................................................. 5-11
REMOTE COMMUNICATION—RS232 ............................................................................... 5-12
REMOTE COMMUNICATION-RS485 ................................................................................. 5-12
PROGRAMMING MODEMS FOR REMOTE COMMUNICATION ........................................... 5-13
HIGH SPEED INPUTS CONNECTION .........................................................................................5-15
IRIG-B CONNECTIONS .................................................................................................................... 5-16
TIME SYNCHRONIZATION ALTERNATIVES ............................................................................. 5-18
6: USING THE EXTERNAL
DISPLAYS
OVERVIEW ........................................................................................................................................... 6-1
USING THE EPM P60N LCD EXTERNAL DISPLAY ................................................................ 6-2
EPM P60N DISPLAY GROUPS OF READINGS ................................................................. 6-3
EPM P60N DISPLAY NAVIGATIONAL MAP (ALL OPTIONS) ........................................... 6-10
USING THE EPM P40NPLUS LED EXTERNAL DISPLAY ...................................................... 6-11
USING THE EPM P40NPLUS USB PORT ........................................................................ 6-11
CONNECT MULTIPLE DISPLAYS .......................................................................................... 6-14
EPM P40NPLUS DISPLAY MODES ................................................................................. 6-14
EPM P40NPLUS DYNAMIC READINGS MODE ............................................................. 6-15
EPM P40NPLUS INFORMATION MODE ......................................................................... 6-18
DISPLAY FEATURES MODE ................................................................................................. 6-20
7: TRANSFORMER LOSS
COMPENSATION
INTRODUCTION ................................................................................................................................ 7-1
EPM 9450/9650 METER'S TRANSFORMER LOSS COMPENSATION ............................ 7-4
LOSS COMPENSATION IN THREE ELEMENT INSTALLATIONS .......................................... 7-4
8: TIME-OF-USE
FUNCTION
INTRODUCTION ................................................................................................................................ 8-1
THE EPM 9450/9650 METER'S TOU CALENDAR .................................................................8-2
TOU PRIOR SEASON AND MONTH ............................................................................................8-2
UPDATING, RETRIEVING AND REPLACING TOU CALENDARS ....................................... 8-3
DAYLIGHT SAVINGS AND DEMAND .........................................................................................8-3

EPM 9450/9650 ADVANCED POWER QUALITY METERING SYSTEM – INSTRUCTION MANUAL TOC–3
9: EXTERNAL I/O
MODULES
HARDWARE OVERVIEW ................................................................................................................. 9-1
PORT OVERVIEW .................................................................................................................. 9-2
I/O MODULE INSTALLATION ........................................................................................................9-4
POWER SOURCE FOR I/O MODULES ................................................................................ 9-4
USING THE PSIO WITH MULTIPLE I/O MODULES ............................................................... 9-6
STEPS FOR ATTACHING MULTIPLE I/O MODULES .......................................................... 9-6
FACTORY SETTINGS AND RESET BUTTON ............................................................................. 9-8
ANALOG TRANSDUCER SIGNAL OUTPUT MODULES ........................................................ 9-9
OVERVIEW ............................................................................................................................ 9-9
NORMAL MODE ................................................................................................................... 9-10
ANALOG INPUT MODULES ...........................................................................................................9-11
OVERVIEW ............................................................................................................................ 9-11
NORMAL MODE ................................................................................................................... 9-12
DIGITAL DRY CONTACT RELAY OUTPUT (FORM C) MODULE ......................................... 9-12
OVERVIEW ............................................................................................................................ 9-13
COMMUNICATION ................................................................................................................ 9-13
NORMAL MODE ................................................................................................................... 9-13
DIGITAL SOLID STATE PULSE OUTPUT (KYZ) MODULE ..................................................... 9-13
OVERVIEW ............................................................................................................................ 9-14
COMMUNICATION ................................................................................................................ 9-14
NORMAL MODE ................................................................................................................... 9-14
DIGITAL STATUS INPUT MODULE .............................................................................................. 9-15
OVERVIEW ............................................................................................................................ 9-16
COMMUNICATION ................................................................................................................ 9-16
NORMAL MODE ................................................................................................................... 9-16
10: METER WITH
INTERNAL MODEM
OPTION (COMM OPTION
2)
HARDWARE OVERVIEW ................................................................................................................. 10-1
HARDWARE CONNECTION .......................................................................................................... 10-2
DIAL-IN FUNCTION .......................................................................................................................... 10-2
DIAL-OUT FUNCTION ..................................................................................................................... 10-3
11: METER WITH
OPTIONAL INTERNAL
NETWORK (COMM
OPTION 1)
HARDWARE OVERVIEW ................................................................................................................. 11-1
NETWORK CONNECTION .............................................................................................................. 11-3
12: FLICKER AND
ANALYSIS
OVERVIEW ........................................................................................................................................... 12-1
THEORY OF OPERATION ................................................................................................................ 12-2
SUMMARY ............................................................................................................................. 12-3
FLICKER SETTING (EPM 9450 AND EPM 9650 OPTION A) ............................................... 12-5
FLICKER POLLING SCREEN .......................................................................................................... 12-6
LOGGING ............................................................................................................................................. 12-8
POLLING THROUGH A COMMUNICATION PORT ................................................................ 12-9
LOG VIEWER ....................................................................................................................................... 12-9
PERFORMANCE NOTES .................................................................................................................. 12-9
EN50160/IEC61000-4-30 POWER QUALITY COMPLIANCE ANALYSIS (EPM 9650 OPTION
B) ............................................................................................................................................................. 12-10
EN50160/IEC61000-4-30 CONFIGURATION ............................................................ 12-10
EN50160/IEC61000-4-30 ANALYSIS ........................................................................ 12-11

TOC–4 EPM 9450/9650 ADVANCED POWER QUALITY METERING SYSTEM – INSTRUCTION MANUAL
A: MANUAL REVISION
HISTORY
RELEASE NOTES ................................................................................................................................ A-1

EPM 9450/9650 ADVANCED POWER QUALITY METERING SYSTEM – INSTRUCTION MANUAL 1–1
EPM 9450/9650
Chapter 1: Three-Phase Power
Measurement
GE
Grid Solutions
Three-Phase Power Measurement
This introduction to three-phase power and power measurement is intended to
provide only a brief overview of the subject. The professional meter engineer or meter
technician should refer to more advanced documents such as the EEI Handbook for
Electricity Metering and the application standards for more in-depth and technical
coverage of the subject.
1.1 Three Phase System Configurations
Three-phase power is most commonly used in situations where large amounts of
power will be used because it is a more effective way to transmit the power and
because it provides a smoother delivery of power to the end load. There are two
commonly used connections for three-phase power, a wye connection or a delta
connection. Each connection has several different manifestations in actual use.
When attempting to determine the type of connection in use, it is a good practice to
follow the circuit back to the transformer that is serving the circuit. It is often not
possible to conclusively determine the correct circuit connection simply by counting
the wires in the service or checking voltages. Checking the transformer connection will
provide conclusive evidence of the circuit connection and the relationships between
the phase voltages and ground.
1.2 Wye Connection
The wye connection is so called because when you look at the phase relationships and
the winding relationships between the phases it looks like a Y. Figure 1.1 depicts the
winding relationships for a wye-connected service. In a wye service the neutral (or
center point of the wye) is typically grounded. This leads to common voltages of 208/
120 and 480/277 (where the first number represents the phase-to-phase voltage and
the second number represents the phase-to-ground voltage).

1–2 EPM 9450/9650 ADVANCED POWER QUALITY METERING SYSTEM – INSTRUCTION MANUAL
WYE CONNECTION CHAPTER 1: THREE-PHASE POWER MEASUREMENT
Figure 1-1: Three-phase Wye Winding
The three voltages are separated by 120oelectrically. Under balanced load conditions
the currents are also separated by 120o. However, unbalanced loads and other
conditions can cause the currents to depart from the ideal 120oseparation. Three-
phase voltages and currents are usually represented with a phasor diagram. A phasor
diagram for the typical connected voltages and currents is shown in Figure 1.2.
Figure 1-2: Phasor Diagram Showing Three-phase Voltages and Currents
The phasor diagram shows the 120oangular separation between the phase voltages.
The phase-to-phase voltage in a balanced three-phase wye system is 1.732 times the
phase-to-neutral voltage. The center point of the wye is tied together and is typically
grounded. Table 1.1 shows the common voltages used in the United States for wye-
connected systems.
Table 1.1: Common Phase Voltages on Wye Services
Phase to Ground Voltage Phase to Phase Voltage
120 volts 208 volts
277 volts 480 volts
2,400 volts 4,160 volts
7,200 volts 12,470 volts
N
Phase 1
Phase 3
Phase 2
V
C
V
A
V
B
V
A
V
C
V
B
N
I
C
I
A
I
B

CHAPTER 1: THREE-PHASE POWER MEASUREMENT DELTA CONNECTION
EPM 9450/9650 ADVANCED POWER QUALITY METERING SYSTEM – INSTRUCTION MANUAL 1–3
Usually a wye-connected service will have four wires: three wires for the phases and
one for the neutral. The three-phase wires connect to the three phases (as shown in
Figure 1.1). The neutral wire is typically tied to the ground or center point of the wye.
In many industrial applications the facility will be fed with a four-wire wye service but
only three wires will be run to individual loads. The load is then often referred to as a
delta-connected load but the service to the facility is still a wye service; it contains
four wires if you trace the circuit back to its source (usually a transformer). In this type
of connection the phase to ground voltage will be the phase-to-ground voltage
indicated in Table 1, even though a neutral or ground wire is not physically present at
the load. The transformer is the best place to determine the circuit connection type
because this is a location where the voltage reference to ground can be conclusively
identified.
1.3 Delta Connection
Delta-connected services may be fed with either three wires or four wires. In a three-
phase delta service the load windings are connected from phase-to-phase rather
than from phase-to-ground. Figure 1.3 shows the physical load connections for a
delta service.
Figure 1-3: Three-phase Delta Winding Relationship
In this example of a delta service, three wires will transmit the power to the load. In a
true delta service, the phase-to-ground voltage will usually not be balanced because
the ground is not at the center of the delta.
Figure 1.4 shows the phasor relationships between voltage and current on a three-
phase delta circuit.
In many delta services, one corner of the delta is grounded. This means the phase to
ground voltage will be zero for one phase and will be full phase-to-phase voltage for
the other two phases. This is done for protective purposes.
7,620 volts 13,200 volts
Table 1.1: Common Phase Voltages on Wye Services
Phase to Ground Voltage Phase to Phase Voltage
V
C
Phase 1
Phase 3
Phase 2
V
A
V
B

1–4 EPM 9450/9650 ADVANCED POWER QUALITY METERING SYSTEM – INSTRUCTION MANUAL
DELTA CONNECTION CHAPTER 1: THREE-PHASE POWER MEASUREMENT
Figure 1-4: Phasor Diagram, Three-Phase Voltages and Currents, Delta-Connected
Another common delta connection is the four-wire, grounded delta used for lighting
loads. In this connection the center point of one winding is grounded. On a 120/240
volt, four-wire, grounded delta service the phase-to-ground voltage would be 120
volts on two phases and 208 volts on the third phase. Figure 1.5 shows the phasor
diagram for the voltages in a three-phase, four-wire delta system.
Figure 1-5: Phasor Diagram Showing Three-phase Four-Wire Delta-Connected System
I
A
V
CA
V
AB
V
BC
I
C
I
B
V
A
V
C
V
B
V
CA
V
AB
N
V
BC

CHAPTER 1: THREE-PHASE POWER MEASUREMENT BLONDEL’S THEOREM AND THREE PHASE MEASUREMENT
EPM 9450/9650 ADVANCED POWER QUALITY METERING SYSTEM – INSTRUCTION MANUAL 1–5
1.4 Blondel’s Theorem and Three Phase Measurement
In 1893 an engineer and mathematician named Andre E. Blondel set forth the first
scientific basis for polyphase metering. His theorem states:
If energy is supplied to any system of conductors through N wires, the total power in
the system is given by the algebraic sum of the readings of N wattmeters so arranged
that each of the N wires contains one current coil, the corresponding potential coil
being connected between that wire and some common point. If this common point is
on one of the N wires, the measurement may be made by the use of N-1 Wattmeters.
The theorem may be stated more simply, in modern language:
In a system of N conductors, N-1 meter elements will measure the power or energy
taken provided that all the potential coils have a common tie to the conductor in
which there is no current coil.
Three-phase power measurement is accomplished by measuring the three individual
phases and adding them together to obtain the total three phase value. In older
analog meters, this measurement was accomplished using up to three separate
elements. Each element combined the single-phase voltage and current to produce a
torque on the meter disk. All three elements were arranged around the disk so that the
disk was subjected to the combined torque of the three elements. As a result the disk
would turn at a higher speed and register power supplied by each of the three wires.
According to Blondel's Theorem, it was possible to reduce the number of elements
under certain conditions. For example, a three-phase, three-wire delta system could
be correctly measured with two elements (two potential coils and two current coils) if
the potential coils were connected between the three phases with one phase in
common.
In a three-phase, four-wire wye system it is necessary to use three elements. Three
voltage coils are connected between the three phases and the common neutral
conductor. A current coil is required in each of the three phases.
In modern digital meters, Blondel's Theorem is still applied to obtain proper
metering. The difference in modern meters is that the digital meter measures each
phase voltage and current and calculates the single-phase power for each phase. The
meter then sums the three phase powers to a single three-phase reading.
Some digital meters measure the individual phase power values one phase at a time.
This means the meter samples the voltage and current on one phase and calculates a
power value. Then it samples the second phase and calculates the power for the
second phase. Finally, it samples the third phase and calculates that phase power.
After sampling all three phases, the meter adds the three readings to create the
equivalent three-phase power value. Using mathematical averaging techniques, this
method can derive a quite accurate measurement of three-phase power.
More advanced meters actually sample all three phases of voltage and current
simultaneously and calculate the individual phase and three-phase power values. The
advantage of simultaneous sampling is the reduction of error introduced due to the
difference in time when the samples were taken.

1–6 EPM 9450/9650 ADVANCED POWER QUALITY METERING SYSTEM – INSTRUCTION MANUAL
POWER, ENERGY AND DEMAND CHAPTER 1: THREE-PHASE POWER MEASUREMENT
Figure 1-6: Three-Phase Wye Load Illustrating Kirchoff’s Law and Blondel’s Theorem
Blondel's Theorem is a derivation that results from Kirchoff's Law. Kirchoff's Law states
that the sum of the currents into a node is zero. Another way of stating the same thing
is that the current into a node (connection point) must equal the current out of the
node. The law can be applied to measuring three-phase loads. Figure 1.6 shows a
typical connection of a three-phase load applied to a three-phase, four-wire service.
Kirchoff's Law holds that the sum of currents A, B, C and N must equal zero or that the
sum of currents into Node "n" must equal zero.
If we measure the currents in wires A, B and C, we then know the current in wire N by
Kirchoff's Law and it is not necessary to measure it. This fact leads us to the
conclusion of Blondel's Theorem- that we only need to measure the power in three of
the four wires if they are connected by a common node. In the circuit of Figure 1.6 we
must measure the power flow in three wires. This will require three voltage coils and
three current coils (a three-element meter). Similar figures and conclusions could be
reached for other circuit configurations involving Delta-connected loads.
1.5 Power, Energy and Demand
It is quite common to exchange power, energy and demand without differentiating
between the three. Because this practice can lead to confusion, the differences
between these three measurements will be discussed.
Power is an instantaneous reading. The power reading provided by a meter is the
present flow of watts. Power is measured immediately just like current. In many digital
meters, the power value is actually measured and calculated over a one second
interval because it takes some amount of time to calculate the RMS values of voltage
and current. But this time interval is kept small to preserve the instantaneous nature
of power.
Energy is always based on some time increment; it is the integration of power over a
defined time increment. Energy is an important value because almost all electric bills
are based, in part, on the amount of energy used.
Phase B
Phase C
Phase A
A
B
C
N
Node "n"

CHAPTER 1: THREE-PHASE POWER MEASUREMENT POWER, ENERGY AND DEMAND
EPM 9450/9650 ADVANCED POWER QUALITY METERING SYSTEM – INSTRUCTION MANUAL 1–7
Typically, electrical energy is measured in units of kilowatt-hours (kWh). A kilowatt-
hour represents a constant load of one thousand watts (one kilowatt) for one hour.
Stated another way, if the power delivered (instantaneous watts) is measured as 1,000
watts and the load was served for a one hour time interval then the load would have
absorbed one kilowatt-hour of energy. A different load may have a constant power
requirement of 4,000 watts. If the load were served for one hour it would absorb four
kWh. If the load were served for 15 minutes it would absorb ¼ of that total or one
kWh.
Figure 1.7 shows a graph of power and the resulting energy that would be transmitted
as a result of the illustrated power values. For this illustration, it is assumed that the
power level is held constant for each minute when a measurement is taken. Each bar
in the graph will represent the power load for the one-minute increment of time. In
real life the power value moves almost constantly.
The data from Figure 1.7 is reproduced in Table 1.2 to illustrate the calculation of
energy. Since the time increment of the measurement is one minute and since we
specified that the load is constant over that minute, we can convert the power
reading to an equivalent consumed energy reading by multiplying the power reading
times 1/60 (converting the time base from minutes to hours).
Figure 1-7: Power Use over Time
Table 1.2: Power and Energy Relationship over Time
Time Interval
(minute) Power (kW) Energy (kWh) Accumulated Energy
(kWh)
1300.500.50
2500.831.33
3400.672.00
4550.922.92
5601.003.92
6601.004.92
0
10
20
30
40
50
60
70
80
1 2 3 4 5 6 7 8 9 10 11 12 13 14 15
Time (minutes)
sttawolik

1–8 EPM 9450/9650 ADVANCED POWER QUALITY METERING SYSTEM – INSTRUCTION MANUAL
POWER, ENERGY AND DEMAND CHAPTER 1: THREE-PHASE POWER MEASUREMENT
As in Table 1.2, the accumulated energy for the power load profile of Figure 1.7 is
14.92 kWh.
Demand is also a time-based value. The demand is the average rate of energy use
over time. The actual label for demand is kilowatt-hours/hour but this is normally
reduced to kilowatts. This makes it easy to confuse demand with power, but demand
is not an instantaneous value. To calculate demand it is necessary to accumulate the
energy readings (as illustrated in Figure 1.7) and adjust the energy reading to an
hourly value that constitutes the demand.
In the example, the accumulated energy is 14.92 kWh. But this measurement was
made over a 15-minute interval. To convert the reading to a demand value, it must be
normalized to a 60-minute interval. If the pattern were repeated for an additional
three 15-minute intervals the total energy would be four times the measured value or
59.68 kWh. The same process is applied to calculate the 15-minute demand value.
The demand value associated with the example load is 59.68 kWh/hr or 59.68 kWd.
Note that the peak instantaneous value of power is 80 kW, significantly more than the
demand value.
Figure 1.8 shows another example of energy and demand. In this case, each bar
represents the energy consumed in a 15-minute interval. The energy use in each
interval typically falls between 50 and 70 kWh. However, during two intervals the
energy rises sharply and peaks at 100 kWh in interval number 7. This peak of usage
will result in setting a high demand reading. For each interval shown the demand
value would be four times the indicated energy reading. So interval 1 would have an
associated demand of 240 kWh/hr. Interval 7 will have a demand value of 400 kWh/
hr. In the data shown, this is the peak demand value and would be the number that
would set the demand charge on the utility bill.
7701.176.09
8701.177.26
9601.008.26
10 70 1.17 9.43
11 80 1.33 10.76
12 50 0.83 12.42
13 50 0.83 12.42
14 70 1.17 13.59
15 80 1.33 14.92
Table 1.2: Power and Energy Relationship over Time
Time Interval
(minute) Power (kW) Energy (kWh) Accumulated Energy
(kWh)

CHAPTER 1: THREE-PHASE POWER MEASUREMENT REACTIVE ENERGY AND POWER FACTOR
EPM 9450/9650 ADVANCED POWER QUALITY METERING SYSTEM – INSTRUCTION MANUAL 1–9
Figure 1-8: Energy Use and Demand
As can be seen from this example, it is important to recognize the relationships
between power, energy and demand in order to control loads effectively or to monitor
use correctly.
1.6 Reactive Energy and Power Factor
The real power and energy measurements discussed in the previous section relate to
the quantities that are most used in electrical systems. But it is often not sufficient to
only measure real power and energy. Reactive power is a critical component of the
total power picture because almost all real-life applications have an impact on
reactive power. Reactive power and power factor concepts relate to both load and
generation applications. However, this discussion will be limited to analysis of reactive
power and power factor as they relate to loads. To simplify the discussion, generation
will not be considered.
Real power (and energy) is the component of power that is the combination of the
voltage and the value of corresponding current that is directly in phase with the
voltage. However, in actual practice the total current is almost never in phase with the
voltage. Since the current is not in phase with the voltage, it is necessary to consider
both the inphase component and the component that is at quadrature (angularly
rotated 90o or perpendicular) to the voltage. Figure 1.9 shows a single-phase voltage
and current and breaks the current into its in-phase and quadrature components.
0
20
40
60
80
100
12345678
Intervals (15 mins.)
sruoh-ttawolik

1–10 EPM 9450/9650 ADVANCED POWER QUALITY METERING SYSTEM – INSTRUCTION MANUAL
REACTIVE ENERGY AND POWER FACTOR CHAPTER 1: THREE-PHASE POWER MEASUREMENT
Figure 1-9: Voltage and Complex Current
The voltage (V) and the total current (I) can be combined to calculate the apparent
power or VA. The voltage and the in-phase current (IR) are combined to produce the
real power or watts. The voltage and the quadrature current (IX) are combined to
calculate the reactive power.
The quadrature current may be lagging the voltage (as shown in Figure 1.9) or it may
lead the voltage. When the quadrature current lags the voltage the load is requiring
both real power (watts) and reactive power (VARs). When the quadrature current leads
the voltage the load is requiring real power (watts) but is delivering reactive power
(VARs) back into the system; that is VARs are flowing in the opposite direction of the
real power flow.
Reactive power (VARs) is required in all power systems. Any equipment that uses
magnetization to operate requires VARs. Usually the magnitude of VARs is relatively
low compared to the real power quantities. Utilities have an interest in maintaining
VAR requirements at the customer to a low value in order to maximize the return on
plant invested to deliver energy. When lines are carrying VARs, they cannot carry as
many watts. So keeping the VAR content low allows a line to carry its full capacity of
watts. In order to encourage customers to keep VAR requirements low, some utilities
impose a penalty if the VAR content of the load rises above a specified value.
A common method of measuring reactive power requirements is power factor. Power
factor can be defined in two different ways. The more common method of calculating
power factor is the ratio of the real power to the apparent power. This relationship is
expressed in the following formula:
Total PF = real power / apparent power = watts/VA
This formula calculates a power factor quantity known as Total Power Factor. It is
called Total PF because it is based on the ratios of the power delivered. The delivered
power quantities will include the impacts of any existing harmonic content. If the
voltage or current includes high levels of harmonic distortion the power values will be
affected. By calculating power factor from the power values, the power factor will
include the impact of harmonic distortion. In many cases this is the preferred method
of calculation because the entire impact of the actual voltage and current are
included.
V
I
I
R
I
X
0

CHAPTER 1: THREE-PHASE POWER MEASUREMENT HARMONIC DISTORTION
EPM 9450/9650 ADVANCED POWER QUALITY METERING SYSTEM – INSTRUCTION MANUAL 1–11
A second type of power factor is Displacement Power Factor. Displacement PF is
based on the angular relationship between the voltage and current. Displacement
power factor does not consider the magnitudes of voltage, current or power. It is solely
based on the phase angle differences. As a result, it does not include the impact of
harmonic distortion. Displacement power factor is calculated using the following
equation:
where q is the angle between the voltage and the current (see Fig. 1.9).
In applications where the voltage and current are not distorted, the Total Power
Factor will equal the Displacement Power Factor. But if harmonic distortion is present,
the two power factors will not be equal.
1.7 Harmonic Distortion
Harmonic distortion is primarily the result of high concentrations of non-linear loads.
Devices such as computer power supplies, variable speed drives and fluorescent light
ballasts make current demands that do not match the sinusoidal waveform of AC
electricity. As a result, the current waveform feeding these loads is periodic but not
sinusoidal. Figure 1.10 shows a normal, sinusoidal current waveform. This example
has no distortion.
Figure 1-10: Nondistorted Current Waveform
Figure 1.11 shows a current waveform with a slight amount of harmonic distortion.
The waveform is still periodic and is fluctuating at the normal 60 Hz frequency.
However, the waveform is not a smooth sinusoidal form as seen in Figure 1.10.
Displacement PF θcos=
Time
Amps
– 1000
– 500
0
500
1000

1–12 EPM 9450/9650 ADVANCED POWER QUALITY METERING SYSTEM – INSTRUCTION MANUAL
HARMONIC DISTORTION CHAPTER 1: THREE-PHASE POWER MEASUREMENT
Figure 1-11: Distorted Current Waveform
The distortion observed in Figure 1.11 can be modeled as the sum of several
sinusoidal waveforms of frequencies that are multiples of the fundamental 60 Hz
frequency. This modeling is performed by mathematically disassembling the distorted
waveform into a collection of higher frequency waveforms.
These higher frequency waveforms are referred to as harmonics. Figure 1.12 shows
the content of the harmonic frequencies that make up the distortion portion of the
waveform in Figure 1.11.
Figure 1-12: Waveforms of the Harmonics
The waveforms shown in Figure 1.12 are not smoothed but do provide an indication of
the impact of combining multiple harmonic frequencies together.
When harmonics are present it is important to remember that these quantities are
operating at higher frequencies. Therefore, they do not always respond in the same
manner as 60 Hz values.
–1000
–500
0
500
1000
t
)s
p
m
a(
tner
r
u
C
a2a
–1500
1500
Time
Amps
3rd harmonic
5th harmonic
7th harmonic
Total
fundamental
– 500
0
500
1000
This manual suits for next models
1
Table of contents
Popular Measuring Instrument manuals by other brands

Ripley
Ripley Miller UPM100 user guide
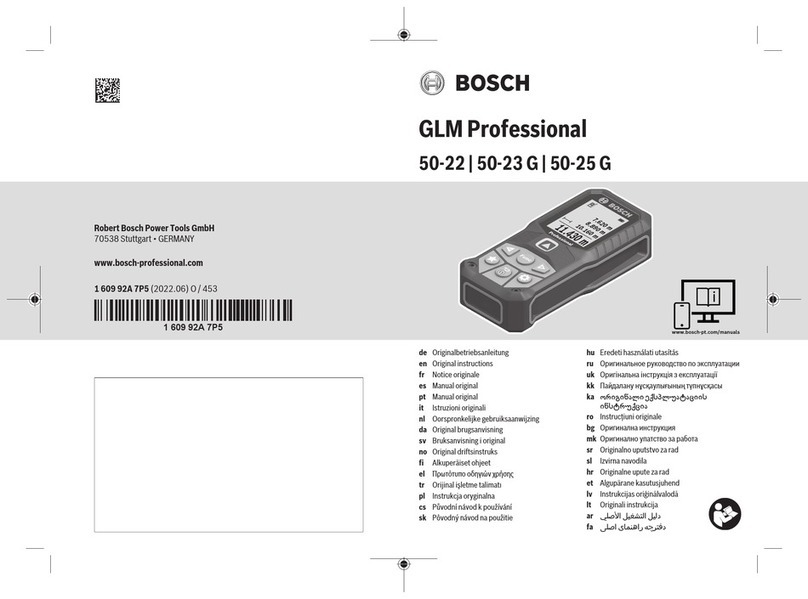
Bosch
Bosch Professional GLM 50-25 G Original instructions

LANDTEC
LANDTEC GEOTECH DIVEAIR 2 operating manual
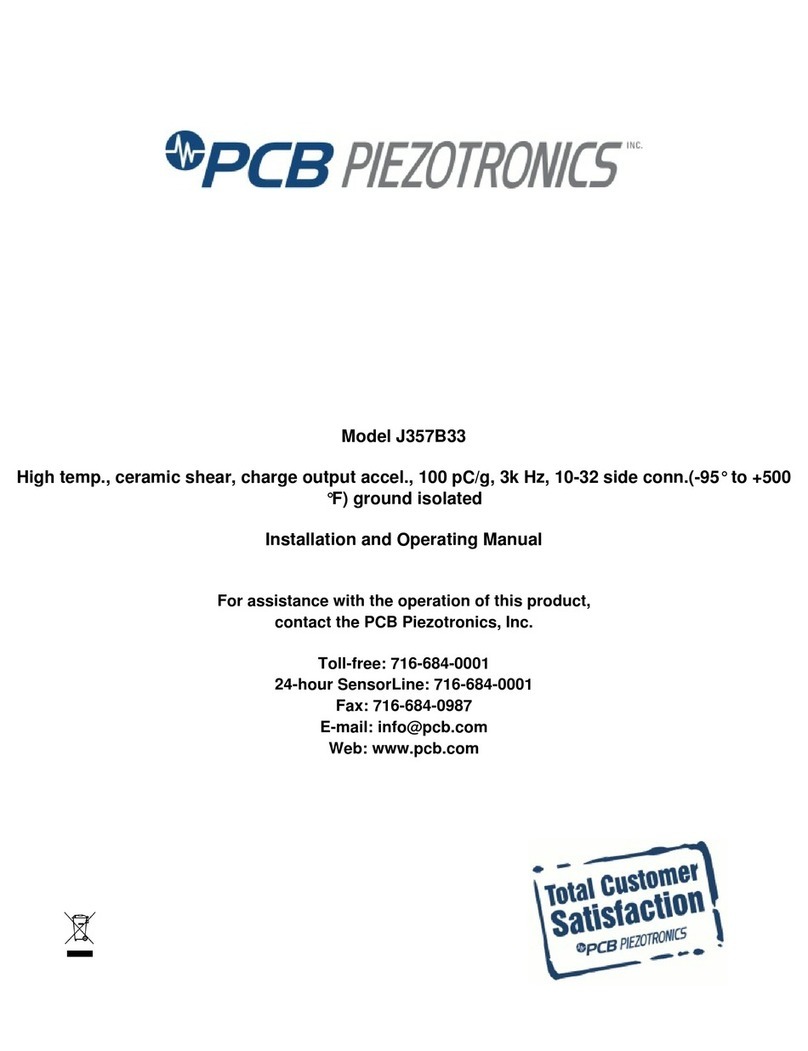
PCB Piezotronics
PCB Piezotronics J357B33 Installation and operating manual
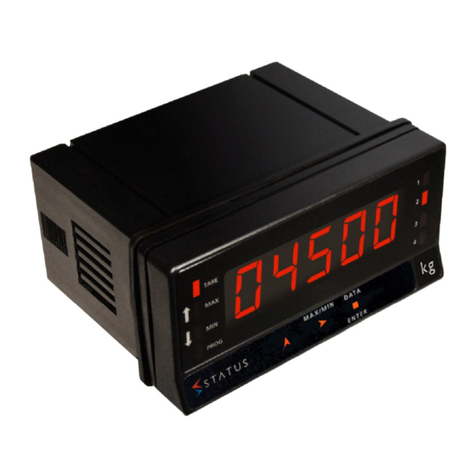
Status Instruments
Status Instruments DM4500U instruction manual
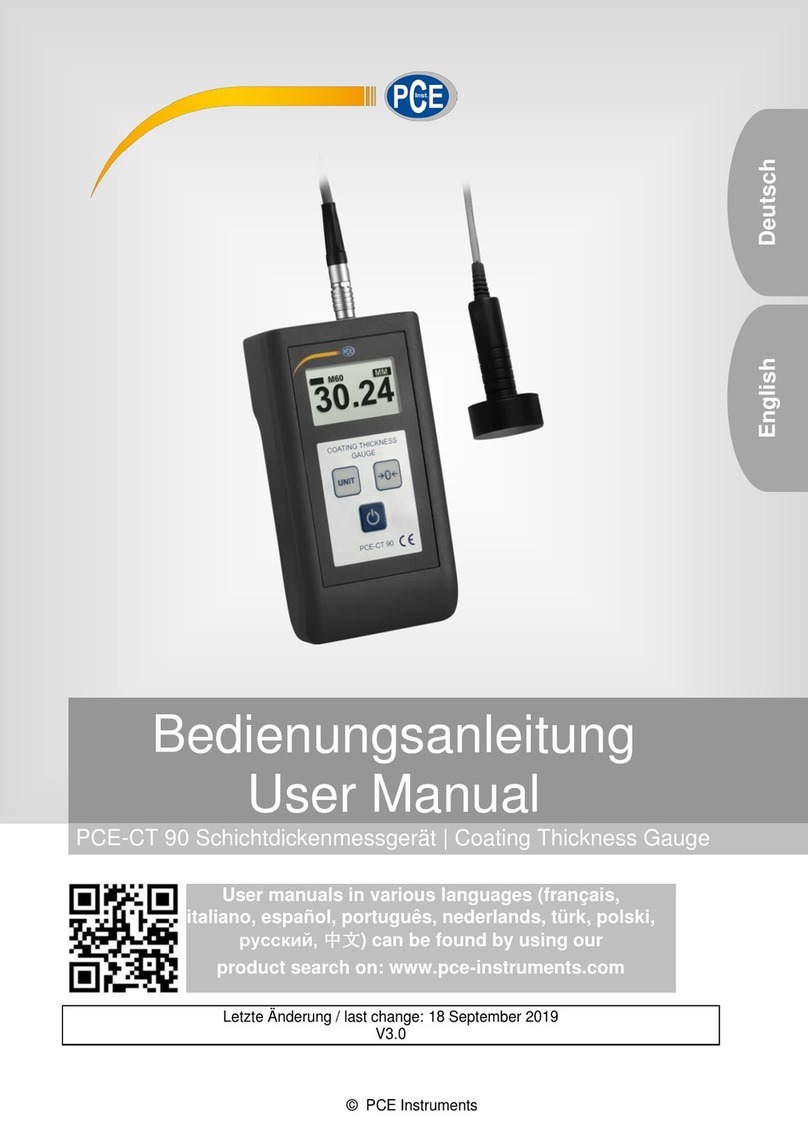
PCE Instruments
PCE Instruments PCE-CT 90 user manual