Gen3 AutoCAF2+ Technical Document

Page 1of 42
AutoCAF2+
INSTRUCTION MANUAL &
OPERATING GUIDE
ISSUED: 2021-23-06

Page 2of 42
Contents Page
1. Introduction
Page 4
1.1
Software Licence
1.2
Copyright
1.3
Extent of Warranty
2. Guarantee
3. Unpacking the System
Page 5
3.1
Introduction
3.2
Packing List
Page 6
3.3
Electrical Supply
3.4
Operating Environment
Page 7
3.5
Computer Requirement
4. Installation
Page 8
4.1
Operating System
4.2
Safety
4.3
Hardware Installation
Page 9
4.3.1
Safety Interlock
4.4
Technical Assistance
Page 10
4.5
Limitation of Liability
4.6
Copyright
5. AutoCAF2+ Software
Page 11
5.1
Software Installation
5.2
Language Selection
Page 12
5.3
Software Information
Page 13
5.4
Manual
Page 14
5.5
Communication Setup
Page 15
5.6
X-Axis Format Selection
Pages 16 & 17
5.7
Output Value & Low Measurement Alarms
Page 18
5.8
Temperature & Humidity Interval/Limit Setup
Page 19
5.9
Board/Channel naming & selection
Page 20
5.10
Standard Measurement Test
Page 21
5.11
Multiple Bias Test
Page 22
5.12
Templates
Page 23
5.13
Test Running Indication
Page 24
5.14
Live User Interface
Page 25
5.15
Low Measurement Log
Page 26
5.16
Live Data Chart
Pages 27 & 28
5.17
Adjustable Results Graph
Pages 29 & 30
5.18
Maximum Resistance Measurement
Page 31
5.19
Screenshot & Print Function
Pages 32 & 33
5.20
Export Functions
Pages 34 – 36
5.21
.Gen3 File Loading & Manipulation
Page 37
5.22
Settings Reset
Page 38
6. Connections
Page 39
6.1
Cabling for Direct Hard Wiring Between AutoCAF2+ and Test
Specimens
6.1.1
Bias Connection
Page 40
6.2
AutoCAF2+ Test Rack
Page 41
6.2.1
Construction

Page 3of 42
6.2.2
Connectors
6.2.3
Cables
6.2.4
Design
6.3
High Voltage Testing
7.
AutoCAF2+ Technical Specification
Page 42
8.
High Voltage Testing – CLR1250 Bridge
Page 43

Page 4of 42
1INTRODUCTION
1.1 Software Licence
Gen3, suppliers of the enclosed software, grants you a non-transferable, non-exclusive right to use this on
only 1 single system.
Title and all intellectual proprietary rights remain the property of Gen3.
You may not modify the licensed software in any way.
You may modify data files and system support files if you desire or if directed by Gen3.
1.2 Copyright
You may not use, copy, or modify the enclosed licensed software or any copy, in whole or in part except as
provided in this agreement.
Gen3 allows you to make one backup copy of the software for archival purposes only. The backup copy may
only be used with the original system supplied.
1.3 Extent of Warranty
Gen3 warrants that the licensed software conforms to its program specification provided that the software is
properly used on the AutoCAF2+ System.
Gen3 shall remedy any breach of the warranty conditions by provision of a replacement software package
provided that the notified fault is reproducible under normal use according to the instructions given in the
manual.
2GUARANTEE
All Gen3 equipment hardware and software is fully guaranteed to meet the CE standards of the European
Union, and the warranty insures against faulty workmanship, operation or performance for a period of ONE
YEAR from date of purchase by the user of the product.
All claims against this guarantee MUST be supported by evidence of purchase, such as a bill of sale or
invoice, and it is the responsibility of the claimant to furnish such proof.
In the first instance claims should be made through the original agent from whom it was purchased. In the
event of difficulty, users are requested to contact Gen3 direct, quoting the Serial Number of the system.
Gen3 or an appointed distributor will, at their discretion, repair or replace part or the entire product to
provide, in their judgement, a satisfactory performance of the system consistent with its age and apparent
usage.
This guarantee covers the cost of both parts and labour required to correct the malfunction, but specifically
excludes wear and tear, consumables, physical damage due to incorrect use or misuse and damage or faulty
operation due to unauthorised or inexpert repairs.

Page 5of 42
This guarantee is limited to the performance of the system only, Gen3 accepts no responsibility for any
consequential loss or damage, nor claimed or implied performance, when the system is used with any other
equipment or software.
This guarantee may be invalidated if the system is subject to inappropriate use, used in adverse
environments or conditions outside the specification or the system has been subjected to unauthorised
modifications.
This guarantee does not cover the expense of service engineers’ visits to the site to repair or commission the
system.
3UNPACKING THE SYSTEM
This section details the unpacking and installation procedures required for the correct operation of the
AutoCAF2+. It also includes the hardware and software installation instructions. Failure to follow these
instructions may result in inaccurate results and operational difficulties.
3.1 Introduction
Your unit should be received in a sealed wooden crate (64 x 54 x 39cm in size). Before opening, check the
crate for any external damage that may have occurred during delivery. If the crate has sustained any serious
damage, the carrier should be contacted immediately.
Gen3 employ “Tip n’Tell” and other similar devices that are intended to show if the package has not been
transported correctly. If there is any evidence of mishandling and/or as shown by these devices, you must
notify Gen3 immediately. DO NOT open the package any further until you receive instructions to do so.
Such instructions will be given by Gen3 or its officially appointed agent.
Ensure that the crate is the right way up then, taking a screwdriver with a number 2 pozi-drive head, undo
the screws that retain the lid of the crate.
Remove the "Packing list" from the crate and read through, checking that all of the items on the list have
been included.
Remove the USB flash drive, measurement cables and bias plug. Carefully lift the AutoCAF2+ unit along with
its foam chassis from the packing crate. Remove the foam chassis from each end of the AutoCAF2+.
Put the AutoCAF2+ unit down on a stable bench, close to a power socket. Retain the crate for future use.

Page 6of 42
3.2 Packing List
Please check that all of the following items are present:
PACKING LIST
Item #
Description
1
AutoCAF2+ unit, fitted with requested number of measurement boards
2
IEC mains lead
3
Safety interlock plug
4
USB Cable
5
Temperature/Humidity Probe
6
Cabling: Optional
a. Halogen Free measurement cables (1 off per measurement board)
b. AutoCAF2+ Test rack with pre-fitted cables
7
Red bias lead
8
Bias Power Supply Red Plugs (4 off)
9
Bias Power Supply Black Plug (1 off)
10
1-Amp Anti-surge fuses (2 off)
11
USB Flash drive containing –
•AutoCAF2+ Software
•Microsoft .net framework 4.7.2 installer
•MCP 2221 Windows Driver
•Operating Manual
•Facts and Data book – SIR & CAF Testing
Note: If you are not permitted to use USB Flash drives please contact
techsupport@gen3systems.com and the software will be provided in an alternative format
12
Software Licence Agreement
13
Calibration Certificate
14
CE Statement
15
Option:
c. Calibration coupon
d. Demo Box (including connection cable)
e. Resistance test box
3.3 Electrical supply
The AutoCAF2+ is factory configurable for use with a 120 or 230V ac supply, at 50 or 60Hz. Before the unit is
dispatched the voltage is set to the correct voltage for the country to which the unit is being shipped.
IF THE VOLTAGE MARKED ON ANY COMPONENT DOES NOT CORRESPOND TO YOUR POWER SUPPLY
DO NOT CONNECT THE INSTRUMENT TO THE MAINS.

Page 7of 42
3.4 Operating Environment
The AutoCAF2+ is a precise measuring instrument, and as such, care should be taken not to subject it to any
harsh environment (i.e., hot, cold, oily or damp).
The system relies upon the accurate measurement of leakage currents across the test-site tracks, to calculate
the resistance value, and therefore it is important not to place the unit into an area of high Electro-
Magnetic Interference (EMI), or run measurement cables too close to electrical supply cabling.
EMI on a large scale, can cause inaccurate or unstable resistance readings, therefore, the measurement
cabling should always be fully screened.
The unit should be placed onto a stable surface, and away from areas where it could be disturbed. If the
AutoCAF2+ is placed close to an Environmental Chamber, care should be taken not to allow condensation
from the chamber to run down the measurement cables to the back of the unit.
3.5 Computer Requirement
Computer: Minimum recommended requirements are 1.5GHz processor – 4Gb RAM – Windows® 10 –
Microsoft® .net framework 4.7.2.
The AutoCAF2+ and its software are designed to be used with a Windows® computer. Our software is
backward compatible down to Windows® 7.
It is essential that properly authorised Windows® software is used. Unauthorised versions can
adversely affect system performance.

Page 8of 42
4INSTALLATION
The AutoCAF2+ (image below) is a bench top instrument designed to be connected to a PC with the
following minimum requirements: 1.5GHz processor – 4Gb RAM – 1Gb Free Hard disc space –Windows® 10.
Figure 1
4.1 Operating system:
Windows® 10. Note: The instrument software is backward compatible to Windows® 7
4.2 Safety
The Gen3 AutoCAF2+ meets the relevant requirements defined in the European Low Voltage Directive (LVD)
2014/35/EU. The apparatus has been designed for indoor use only.
The mains plug shall only be inserted in a socket outlet provided with a protective earth contact. Any
interruption of the protective conductor inside or outside the apparatus or disconnection of the protective
earth terminal is likely to render the apparatus dangerous. This unit must be earthed.
When the apparatus is connected to its supply, terminals may be live and the opening of covers or removal
of parts (except those to which access can be gained by hand) is likely to expose live parts.
The apparatus shall be disconnected from all voltage sources before it is opened for any adjustment,
replacement, maintenance or repair. Capacitors inside the apparatus may still be charged even if the
apparatus has been disconnected from all voltage sources. Any adjustment, maintenance and repair of the
opened apparatus under voltage should be avoided as far as possible and, if unavoidable, shall be carried
out only by a skilled person who is aware of the hazard involved.
Only fuses with the required current rating and of the specified type may be used for replacement. The use
of makeshift fuses and the short-circuiting of fuse holders are prohibited.
Whenever it is likely that the protection has been impaired, the apparatus shall be made inoperative,
secured against any unintended operation and returned to the manufacturer for testing. Protection is likely
to be impaired if, for example, the apparatus, shows visible damage, fails to perform the intended
measurements, has been subjected to prolonged storage under unfavourable conditions, or has been
subject to severe transport stresses.
AutoCAF2+

Page 9of 42
4.3 Hardware Installation
Place the AutoCAF2+ on a stable bench, close to a power supply and to the PC.
Check that the unit has been set for the correct voltage (factory set), and that the unit is switched off, before
plugging the other end of the mains lead into the power supply.
4.3.1 Safety Interlock
It is Gen3 recommendation that there is a safety interlock between the AutoCAF2+ and the test chamber
such that if the chamber door is opened during a test, then the entire test operation will be arrested and
stopped.
For test voltages up to 300V, we include a safety interlock. Connect the safety interlock plug to the chamber
interlock system as per diagram below.
Whether the safety interlock is used in this way or not, it is important that this be fitted to the
instrument.
Take the IEC mains lead and plug it into the mains socket at the rear of the unit
Connect USB cable between AutoCAF2+ and USB port in the PC.
Switch on the unit using the on/off switch located to the rear of the unit
The AutoCAF2+ is ready to run.
4.4 Technical Assistance
If you encounter a problem review all the system installation, operation and troubleshooting procedures. If
the problem persists, you can obtain technical support from your local representative or from Gen3 direct:
Gen3
B2, Armstrong Mall
Southwood Business Park
FARNBOROUGH
Hampshire GU14 0NR England
Tel: +44 (0)1252 521500
E-mail: techsupport@gen3systems.com
Ensure that you have a full description of the problem, test conditions and operation sequence available
before you call for assistance. Remember to have the serial number of the system available before you
contact us.
Safety Interlock Plug:
Bias 1 and Bias 2 are routed through this plug and the safety
interlock switches on the environmental chamber, before arriving
at the Bias sockets on the Bias Power Supply

Page 10 of 42
4.5 Limitation of Liability
Gen3 believes the information contained in this publication is accurate, and reserves the right to make
changes in specification and information without prior notice. Gen3 is not responsible for any inadvertent
errors.
The terms and conditions governing the sale of Gen3 hardware products, and the licensing of Gen3
Software, consists solely of those set forth in the written contracts between Gen3 and its customers. No
representation or affirmation of fact contained in this publication, including but not limited to statements
regarding capacity, sensitivity, suitability of use, or performance of product described herein shall be
deemed to be a warranty by Gen3 for any purpose or give rise to any liability by Gen3 whatsoever.
In no event shall Gen3 be liable for any accidental, indirect, special, or consequential damages whatsoever,
including but not limited to lost profits, arising out of or relating to this publication or the information
contained in it, even if Gen3, has been advised, or knew of, or should have known of the possibility of such
damages.
4.6 Copyright
The software programmes contained in this manual are confidential information and proprietary products of
Gen3, or its licensors.
No portion of this document, or the software, may be copied or distributed in any form or by any means
stored in a data base or retrieval system, in whole or in part, without the written consent of Gen3.
Copyright 2021 – All rights reserved – Printed in the UK

Page 11 of 42
5AutoCAF2+ SOFTWARE
5.1 Software Installation
Open the ‘AutoCAF2+’ folder on the provided USB and open the .exe file to begin software installation, on
the first screen choose the desired filepath for installation then select next.
Figure 2
On the ready to install page select install.
Figure 3

Page 12 of 42
After installing successfully, the completion screen will appear, at this stage select Finish.
Figure 4
5.2 Language Selection
Upon opening the AutoCAF2+ software for the first time a language selection screen will appear, once
selected the software will upon.
N.B. Once language is selected this screen will not appear again unless a hard reset is done.
Figure 5

Page 13 of 42
5.3 Software Information
To confirm what version of AutoCAF2+ software the user is running, select the Gen3 logo in the top right
corner of the user interface.
Figure 6
This will open the following window which contains the version of software that is installed, it also contains a
link to the Gen3 website.
Figure 7
N.B The version pictured may not be the current revision of software received on the USB stick.
5.4 Manual
The AutoCAF2+ Manual is provided as a PDF on the supplied USB drive, however alternatively the manual
can be opened also as a PDF within the software simply by selecting the ‘question mark’ icon in the top
right-hand corner of the software.
Figure 8

Page 14 of 42
5.5 Communication Setup
Upon opening the AutoCAF2+ software to enter the settings window select the ‘settings Cog’ in the top
right-hand corner of the software.
Figure 9
This will then open the settings window, at this point the user must select which communication port the
AutoCAF2+ is connected to (this will automatically appear in the drop-down menu) and which machine
type, either a 64, 128 or 256. The user will also have the option to choose (if applicable) which CLR bridge to
attach.
N.B. The correct machine type must be selected even if the user is not going to monitor all channels.
Figure 10
5.6 X Axis format Selection
During this setup stage the desired format of the user for the graph X-Axis can be selected, there are 3 axis
options available to the user which are: -
1. Measurement Number
2. Time in Minutes
3. Time in Hours

Page 15 of 42
Figure 11
The following shows an example of a graph with ‘Measurement’ set as the X-Axis; this test shows 1min
intervals for 10 measurements.
Figure 12

Page 16 of 42
The following shows an example of a graph with ‘Minutes’ set as the X-Axis, this test shows 1 min intervals
for 10 measurements.
Figure 13
The following shows an example of a graph with ‘Hours’ set as the X-Axis.
Figure 14

Page 17 of 42
5.7 Output Value & Low Measurement Alarms
During this set up process the required output value format and Low measurement resistance alarm limit
can be set, if Log10 Resistance is selected then the low measurement must be set in Log scale.
N.B. Any measurement record that falls below this limit will be recorded in the Alarms Log.
Figure 15
Alternatively, if ‘Resistance MΩ’ is selected then the Low measurement resistance must be set in resistance
MΩ/
Figure 16

Page 18 of 42
5.8 Temperature & Humidity Limit Setup
During this setup process, if a Temperature/Humidity probe is required, the Minimum and Maximum alarm
limits must be set.
N.B. Any T/H measurement that falls outside of the desired ranges will be recorded in the Alarms Log.
Figure 17

Page 19 of 42
5.9 Board/Channel naming & selection
The user has the option to rename board and channels, also the user has the ability to turn off monitoring of
desired boards and channels. On the settings window select ‘Boards & Channels’ to change the window to
the board and channels settings.
On this screen to turn on and off desired boards and channels simply click on the tick boxes to turn on and
off, to rename boards and channels double click on the name to highlight then it can be changed to desired
text.
N.B. To avoid confusion, no two channels on any one board can have the same name. The same name
is possible on different boards.
Figure 18

Page 20 of 42
5.10 Standard Measurement Test
Once all communication and board settings etc from sections 5.5 to 5.9 have been chosen select OK and the
user will be taken back to the main user interface. From here, note that the text has changed to ‘Connected
to COM’ which indicates that the software has successfully connected to the AutoCAF2+ system under the
chosen settings. From here select ‘Start’ to begin a test.
Figure 19
This will open the ‘Test Parameters’ window. At this stage the following options must be chosen by the user:
1. The location of the saved results file, and the results file name for the upcoming test.
2. Test Length (24-hour format)
3. Number of Measurements (this is not editable; it is a calculation between the test length and
measurement interval)
4. Measurement Interval (24-hour format)
5. External Voltage (greyed out unless either is selected in option 11)
6. Temperature & Humidity measurement interval (24-hour format)
7. Stabilisation time required in 24-hour clock format N.B. a stabilisation time is not required but is
recommended if the measurement and conditioning bias are different.
8. Soak time (time between selecting test start and the first measurement)
9. Single/Multiple Bias selection (see page 22, section 5.11)
10. Number of measurements per row (see example on page 22)
11. Measurement and conditioning bias selection.
12. Add another voltage selection to measurements (see example on page 22)
13. Select a predefined template. (see example on page 23)
14. Begin test or cancel to return to main menu.
Figure 20
This manual suits for next models
1
Table of contents
Popular Test Equipment manuals by other brands
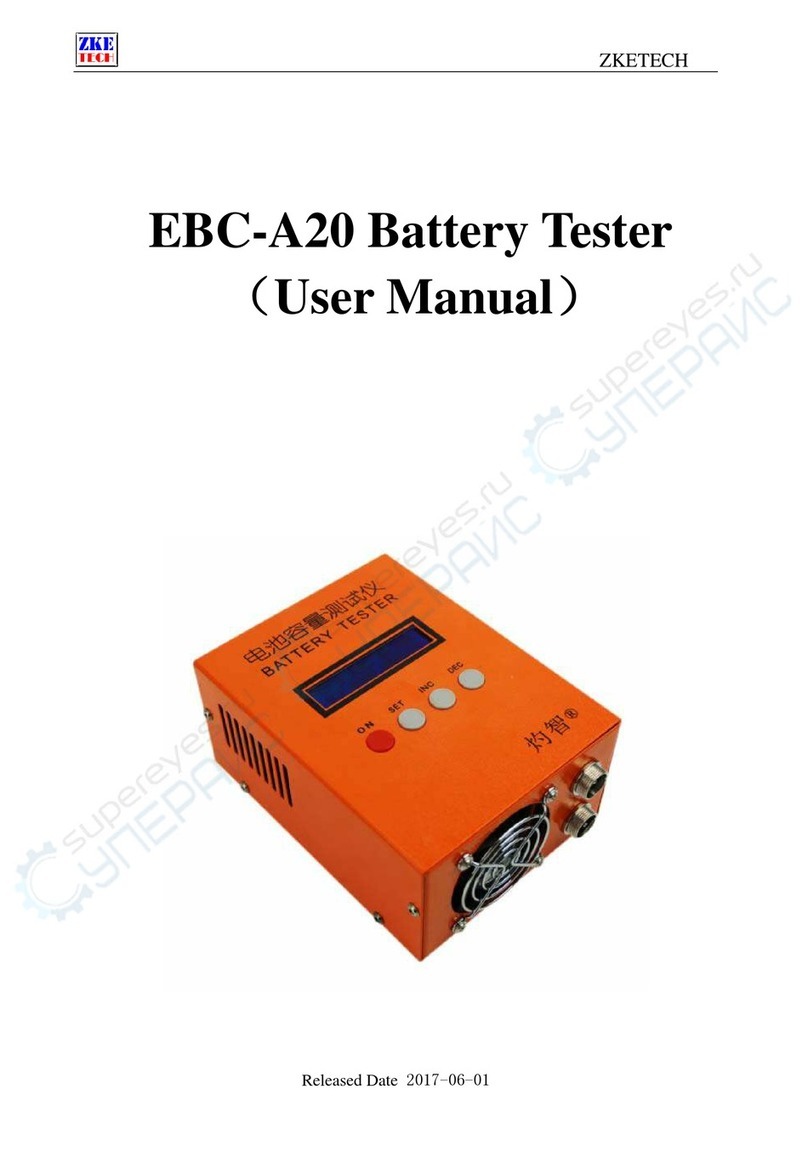
ZKETECH
ZKETECH EBC-A20 user manual
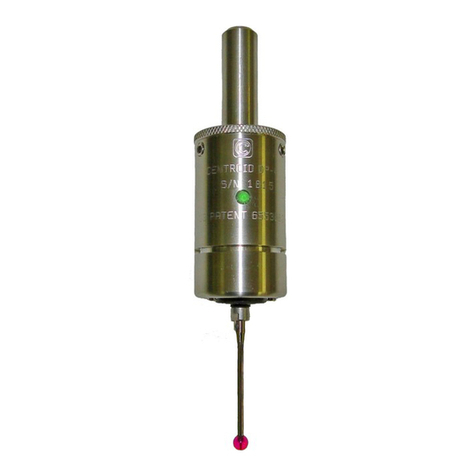
Centroid
Centroid DP-4 Operator's manual

HeartSciences
HeartSciences MyoVista Wavelet ECG user manual
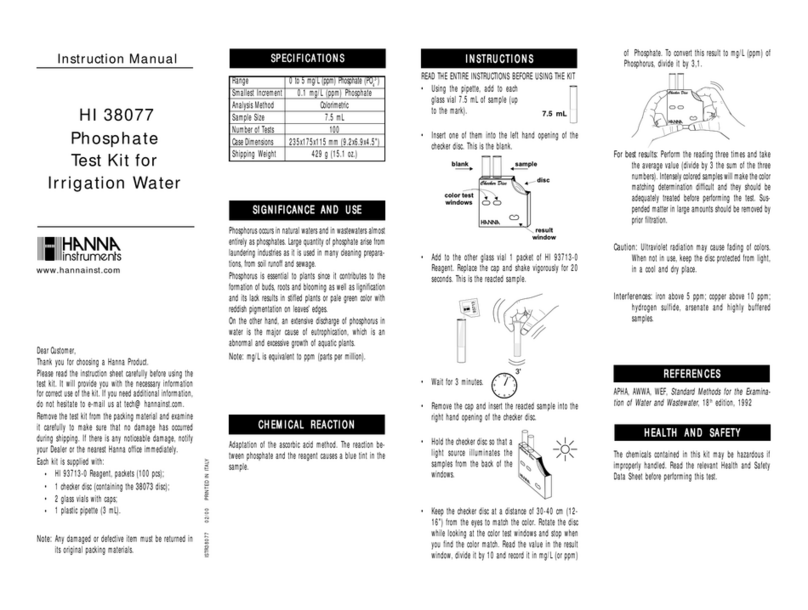
Hanna Instruments
Hanna Instruments HI 38077 instruction manual

CREATIVE ELECTRONICS
CREATIVE ELECTRONICS ELT 1091 owner's manual
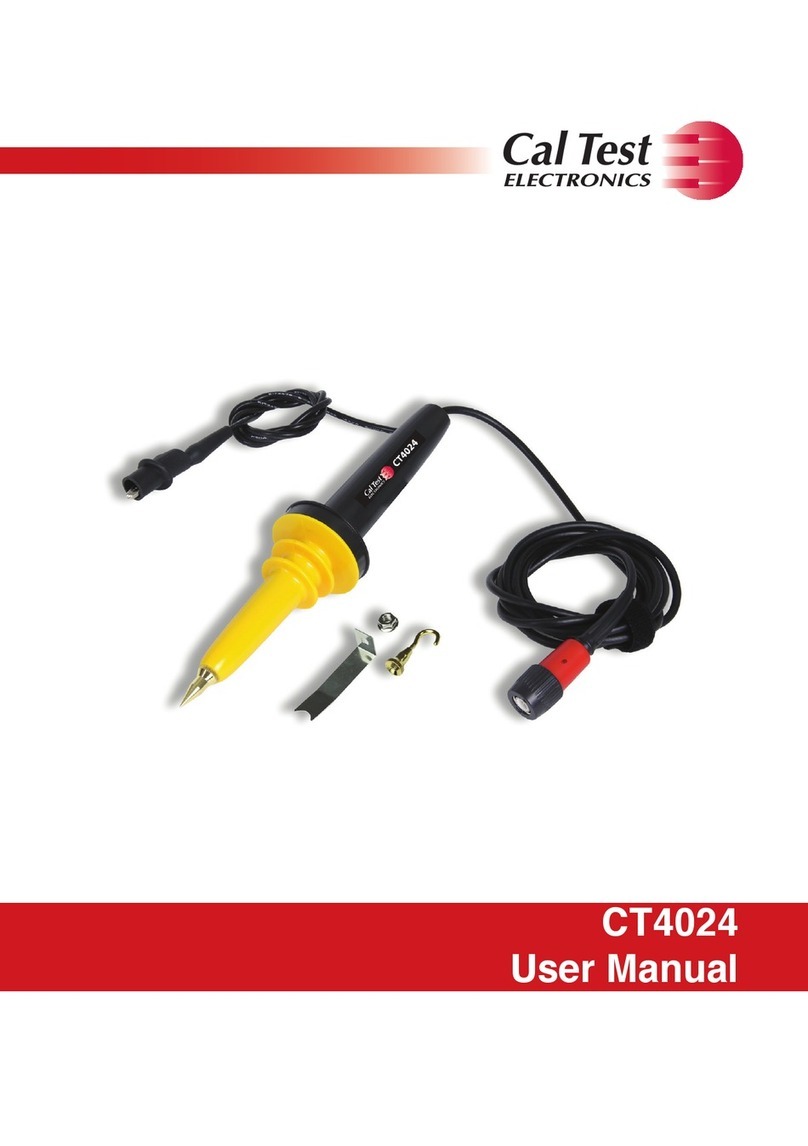
Cal Test Electronics
Cal Test Electronics CT4024 user manual