Geovent MULTIBOX IV User manual

FAN
LSFG/MSFG 146 - 250
INSTRUCTION MANUAL
www.geovent.com
Version 1.0 09.02.2023
MULTIBOX IV
Pressure switch and control

2

3
Contents
1.0 Introduction ..............................3
2.0 Safety ..................................3
2.1 General safety .......................... 3
2.2 Danger .................................3
3.0 Machine overview ........................ 3
3.1 Description ............................. 3
3.2 Intended use ............................ 4
3.3 Machine specifications .................... 4
3.3.1 Design ............................... 4
3.3.2 Technical data ......................... 4
4.0 Transport, handling and storage . . . . . . . . . . . . . 4
5.0 Assembly, installation and start of operation ... 4
5.1 Location ............................... 4
5.2 Installation ............................. 4
5.2.2. Adjustment and regulation.................5
5.2.3 Installation of MultiBox IV for
Frequency Regulation ....................6
5.3 Control and test of the security system ........7
6.0 Commissioning .......................... 7
6.1 After installation ......................... 7
7.0 Control, test and maintenance .............. 7
7.1 Control ................................ 7
7.2 Maintenance .............................7
8.0 Cleaning ...............................18
9.0 Troubleshooting ........................ 18
10.0 Dismantling, disabling and scrapping ....... 18
11.0 Dimensions ........................... 18
12.0 Liability .............................. 19
13.0 Declaration of conformity ................ 19
1.0 Introduction
This manual is made and designed in order to facilitate
the best and most secure interaction with the product.
The manual is relevant for people involved in transpor-
tation, stocking, installation, using, maintaining and all
other thinkable interaction with the product.
The manual must be read in full and understood before
interacting with the product.
When the manual has been read and understood in full,
the table of contents can be used to find the relevant
information in each case.
The product is manufactured by:
Geovent A/S
Hovedgaden 86
DK-8861 Løgstrup
DENMARK
Tel.: (+45) 86 64 22 11
E-mail: [email protected]
www.geovent.com
This manual is to be used for all interactions with the
product including: Transportation, stocking, installation,
operation and maintenance.
This product is marked with: (example)
2.0 Safety
2.1 General safety
Carefully read this manual before use and observe the
safety instructions in order to avoid injuries!
Keep this manual in a safe place!
Secure that all users of the product have read this ma-
nual and that they follow the instructions as described.
Observe all instructions marked on the product!
Observe the indications of the manufacturer.
Never use the product if you are in doubt about how it
works or what you should do.
When doing maintenance follow the instructions in chap-
ter 7.0.
Do not modify the product or use spare parts from other
suppliers than Geovent, as this may hamper the product
and the function.
2.2 Danger
The product is not to be used in areas categorised as
ATEX zones, e.g. with dust from aluminium, flour, wood,
and other mediums that present an explosion hazard.
If a repair is not possible you should dispose of the pro-
duct. Please follow the instruction for disposal in chapter
10.0.
3.0 Machine overview
3.1. Description
Proven construction
Geovent MultiBox IV is a 6th generation ventilation con-
trol unit based on the latest microprocessor
technology.

4
More options in one box
Geovent MultiBox IV can be used for pressure measure-
ment, control, regulation and monitoring with alarm in
process ventilation systems in the pressure range from
0-4000 Pa.
Easy to use
The Geovent MultiBox IV is particularly suitable for dy-
namic pressure control in systems with control dampers
and/or fans with frequency inverters. The desired pres-
sure or flow (pressure differential) is entered as set point,
after which the built-in controller will adjust the damper
or frequency inverter. The alarm is activated if the pres-
sure/flow does not stay within the selected alarm limits.
3.2 Intended use
Most process exhaust systems can be controlled to con-
stant suction pressure, using a frequency inverter or reg-
ulating damper. The inlet air ow and room exhaust are
balanced with the process exhaust using slave control or
feedback control to a variable set point, calculated based
on 0-10V signals from one or more suction points..
The MultiBox IV is recommended for the following:
- Frequency control of exhaust systems
- Control of DC motors in ventilation systems
- Control of rotary dampers and diaphragm dampers
- Balanced supply with multiple process extractors
- Feedback control with up to 3 set points
- Slave control of supply and extract air
- Pressure control in booths with exhaust and supply air
MultiBox IV has a built-in pressure sensor (0 - 4000 Pa).
It can combine several exhaust and supply systems
and regulate according to 3 set points. MultiBox IV has 3
digital inputs and 2 analogue and 4 relay outputs.
The alarm function complies with the requirements of
the Danish Working Environment Authority.
3.3 Machine specifications
3.3.1 Design
MultiBox IV is made of hard plastic material.
3.3.2 Technical data
Dimensions
Model/Dimension A
[mm]
B
[mm]
Weight
[kg]
MultiBox IV 150 150 0,55
4.0 Transport, handling and storage
During transport in a truck or in another means of trans-
portation the product must be securely packed in a box
or a pallet and covered with a water proff material.
The product must be securely stowed in the truck so that
it will neither tilt nor shift during transport.
When moved it must be secured that the product does
not tilt or shift.
The product must be placed in a dry place and covered
securely, in order to secure that moist, metal parts or
other substances do not damage the product.
It is not allowed to place anything on top of the product.
5.0 Assembly, installation and start of
operation
5.1 Location
MultiBox IV is mounted on a fixed base, preferably a
wall.
5.2 Installation
Installation of MultiBox IV as process ventilation
control
MultiBox IV is used for PID feedback control of process
extraction (or supply) by means of a frequency inverter
or an electric or pneumatic damper. In addition, it con-
tains a transmitter for slave control of balanced supply
air or room extract air.
5.2.1. Setup and start-up
230V supply is connected to terminals N, L and if neces-
sary PE. The installation is carried out according to the
diagrams.
Normal Operation
Setpoint: 0
0 Pa
0 %
Fan speed
0.00 V
0 Pa
Status
FILTER
ALARM
PRESS OK
MOTOR
Dato
Clock
i
1
2
3
4

5
Current pressure and setpoint are read on the MultiBox
display.
1: Main menu
2: View all alarms, delete alarm list
3: Settings
4: Device information with statistics list
5.2.2. Adjustment and regulation
General:
Note that there are 7 pages for setup in the settings
menu.
To scroll through the pages, press the arrows on the
right.
Press the Settings button and start setting up.
Page 1/7
Select language: DK, GB, DE, ES, FR
Enter setpoint 1
Enter setpoint 2
Enter setpoint 3
Example for entering values:
It is recommended to follow the instructions below for
setting up setpoints and other settings in MultiBox IV.
1. When the desired setpoint value is set, press ok on
the check mark and the value is saved.
2. In Settings, all values can be changed or reset to
default.
Page 2/7
Alarm limits are set here:
Set monitor alarm min. limit (Pa)
Set monitor alarm max. limit (Pa)
Set time delay for shutdown
Set neutral zone from setpoint
Page 3/7
Set controller P-factor (speed)
Set controller I-time (damping)
Set controller D-factor (speed)
Set OFF 0-10V / ON invert 10-0V - Applies to output 2
only
It is recommended that P-factor be set to 0.001 and that
I-factor be set to 0.001
Settings
Page 1/7
Language English
Setpoint 1 (Pa) 500
Setpoint 2 (Pa) 1.000
Setpoint 3 (Pa) 1.400
Setpoint 1 (Pa)
1
4
7
2
5
8
3
6
9
-
´
0
1.200
Settings
Page 2/7
Min. alarm (Pa) 20
Max. alarm (Pa) 4000
Shutdown delay (s) 10
Neutral zone (Pa) 3
Settings
Page 3/7
P-factor (PID) 3.000
I-factor (PID) 30.000
D-factor (PID) 0.000
Invert output #2 O

6
Settings
Page 4/7
Output 1 Min (V) 0.000
Output 1 Max (V) 10.000
Output 2 Min (V) 0.000
Output 2 Max (V) 10.000
Settings
Page 6/7
Disable alarm O
Mute alarm O
Enable Slave Fan O
DP Sens Oset 735
Settings
Page 7/7
PIN code O
Restore to Defailt
Save Settings
Settings
Page 5/7
Start output value (V) 5.000
Start delay (s) 5
Start mode On
Alarm delay (sec) 10
Page 4/7
Adjust min. value for output 1
Adjust max. value of output 1
Adjust min. value for output 2
Adjust max. value for output 2
Page 5/7
Set regulator start voltage
Set controller start time in seconds
Set start type ON/OFF
Set time delay before alarm signal
Page 6/7
Set turn alarm on/o
Turn alarm signal on/o
Set fan slave signal option on/o 2
Calibration of pressure sensor - Not to be changed
Page 7/7
Turn PIN code on/o
Restore to factory settings if desired.
Save settings
Press the tool icon at the bottom right to enter the ser-
vice settings
Reset delta P
Set date/time - Date - Month - Year - Hour - Min - Sec
Selftest - test the system
Reset statistics
In order to follow alarm recordings and statistics, it is
important to set the date/time before the MultiBox is put
into operation.
5.2.3 Installation of MultiBox IV for
Frequency Regulation
The following instructions describe the installation of the
MultiBox IV for pressure regulation with a xed setpoint
of the frequency inverter.
Installation and start-up
The following start-up procedure is recommended:
• 230V supply is connected to terminals N, L and possi-
bly PE
• The installation is carried out according to the dia-
grams.
• The alarm function is activated by changing the setting
• Enable in the display
• Electric damper requires separate power supply.
Service
Delta P nulstil: 0Pa
Setup dato/tid Selftest
Reset stats.

7
• AO1 is connected to frequency inverter for balanced
inlet and provides ow.
• Alarm output connected to external alarm lamp
• R3 output changes simultaneously with control
• Control is activated from DI1, DI2 or DI3
• Alarm function is active if Enable is chosen in Settings
Installation with supply fan
Installation with supply fan and external extraction
5.3 Control and test of the security system
• Extraction and supply systems are started
• MultiBox IV is connected to the filter or fan control
• Control is activated from DI1
• Connect measuring hose from (-) measuring socket to
ventilation duct. The measuring point is selected on a
straight piece of pipe, in the middle of the suction duct.
• The main display shows the actual measured pressure
and the desired pressure: Setpoint I (Pa)
• The main screen displays the control signal (0-10V)
from DI1
• Main screen displays slave signal (0-10V) from DI2
• The menu displays DI1, which is adapted to min. and
max. limits for output 1 control signal
• The MultiBox IV controller should keep the frequency
inverter stable at setpoint I after a short settling
• I time to be set according to recommendation
• P-factor to be set according to recommendation if un-
stable
• Neutral zone to be set as recommended if unstable
• Output 2 sends control signal (0-10V) to control supply
fan to achieve balance with current process extraction
and fixed room exhaust
6.0 Commissioning
Once the MultiBox IV is installed, set up and tested, it
can be put into operation.
If the process runs as expected, no further adjustments
are required.
It is possible to change settings when this is desired.
See chapter 5.0.
It is possilbe to read statistics when desired.
If statistics on operation and alarms are desired, press
the ”i” icon on the main menu.
On the following screen: Press the ”Statistic” icon and
this will show
7.0 Control, test and maintenance
7.1 Control
Check the installation according to chapter 5.3.
7.2 Maintenance
Alarm
The alarm function is activated when the measured
pressure is below min. or above max.
• The alarm function can be cancelled (stopped) by pres-
sing the (Arrow-down) button on the main display.
• The alarm function can be tested by pressing the (ESC)
button on the main screen for more than 10 seconds.
• Alarm limits can be adjusted as described in chapter
5.0.
Process air extractions
Electric
on/off dampers
VESD
FV50X
VESD
FV50X
Freq.Inv
FV56X
Tryk måling
0-10V
signal
Freq.Inv
Slave signal 0-10V
til balanceret indblæsning
fra terminal T8
Balanced Fresh Inlet Air
Flow (l/s) signal 0-10V
eller slave signal 0-10V
til Rum udsugning
fra Terminal T9
FV 56X i version V530/630 eller V540/640 eller V550/650
MultiBox IV
MultiBox IV
PowerBox
PowerSmart
VESD
FV50X
Power
sensor
Process air extractions
Electric
on/off dampers
VESD
FV50X
VESD
FV50X
Freq.Inv
V530
Feedback control
+ alarm
0-10V
signal
Freq.Inv
Modified
0-10V signal
for Inlet air
slave control
Constant room air
Balanced Fresh Inlet Air
Flow rate
0-10V
signal for
Sumbox
MultiBox IV
PowerSmart /
PowerBox
PowerSmart /
PowerBox
PowerSmart /
PowerBox
Statistic
Total System Time (h:m): 647:44
Operation Time:
Total 5d 90d 365d
03:33 00:00 03:25
Average Operation Time Pr. Day
5d 90d 365d
00:00 00:07
Avg. time pr. startup (h:m): 00:04
Avg. amount startups pr. day: 00
i

8
Parametre
Headline Def. Min. Max. Description
Language Choose DK, GB, DE, ES, FR
Setpoint 1 (Pa) 500 0 4000 Setpunkt 1
Setpoint 2 (Pa) 1000 0 4000 Setpunkt 2
Setpoint 3 (Pa) 1400 0 4000 Setpunkt 3
Min. alarm (Pa) 20 0 4000 Monitor alarm min. limit (Pa)
Max. alarm (Pa) 4000 0 4000 Monitor alarm max. limit (Pa)
Shutdown delay (s) 10 0 3600 Time delay to shut down
Neutral zone (Pa) 3 0 1000 Neutral zone from set point
P-factor (PID) 3 0 200 Regulator P-factor (speed)
I-factor (PID) 30 0 1.000 Regulator I-tid (dæmpning)
D-factor (PID) 0 0 1.000 Regulator D-factor (speed)
Invert output #2 OFF OFF ON No = normal PID ; Yes = invert
Output 1 Min (V) 0 0 10 Adjust voltage limit for AO1
Output 1 Max (V) 10 0 10 Adjust voltage limit for AO1
Output 2 Min (V) 0 0 10 Adjust voltage limit for AO2
Output 2 Max (V) 10 0 10 Adjust voltage limit for AO2
Start output value (V) 5 0 10 Regulator starting voltage
Start delay (s) 5 0 240 Regulator start time in seconds
Start mode ON OFF OFF Start output value (V) / Start delay (s) ON/OFF
Alarm delay (sec) 10 0 3600 Time delay before alarm signal
Disable alarm OFF OFF ON Turn alarm on/o
Mute alarm OFF OFF ON Turn alarm sound on/o
Enable Slave Fan OFF OFF ON Enable fan slave signal on/o
DP Sens Oset 735 200 1000 Calibration of pressure sensor
- Not to be changed
PIN KODE OFF OFF ON PIN code: 2211
DP Zero 0-point calibration
Setup date/time Date - Month - Year - Hour - Min - Sec
Reset statistics Reset statistics

9
Multibox IV
23-06-2021
Digitale indgange:
DI1: Setpunkt 1 (boksen aktiveres og
der reguleres efter setpunkt 1)
DI2: Setpunkt 2
DI3: Setpunkt 3
DI4: Ledig
12V: fælles potentiale
Analoge udgange:
AO1: 0-10V hastighedssignal
AO2: 0-10V slavesignal
G: GND
Relæ udgange(C, NO, NC):
R1: Aktivering af filterstyring (f.eks. til
GEOVENT selvrensende filtre (GFB/GFH..)
R2: Alarm (dp for lav/høj). For tilslutning af
eksternt lampe/sirene (f.eks. 230V op til 4A)
R3: Tryk ok (dp indenfor grænse). Indikerer
at anlægget kører som planlagt
R4: Start signal til omformer (slutter, når
boksen er aktiv.
Når DI1 + 12V sluttes (er aktiv), aktiveres
boksen og regulerer efter setpunkt 1
Driftsignal til
omformer (start/stop)
0-10V signal til omformer.
Bestemmer ventilatorhastighed ud fra setpunkt 1
Driftsignal til filterstyring (start/stop).
Fortæller filteret, om ventilator er i drift
1x230V
forsyning
Digital inputs:
DI1: Setpoint 1 (MultiBox is activated and set-
point 1 is controlled)
DI2: Setpoint 2
DI3: Setpoint 3
DI4: Free
12V: Common potential
Note: If setpoint 2 is activated while setpoint 1 is
active, setpoint 2 is controlled. If setpoint 3 is ac-
tivated while other setpoints are active, setpoint 3
is controlled.
Analogue outputs:
AO1: 0-10V speed signal
AO2: 0-10V slave signal (NB: can be inverted)
G: GND
Input for operation activation. When DI1 + 12V
is connected (is active), the box is activated and
regulates according to setpoint 1.
Relay outputs (C, NO, NC):
R1: Activation of lter control (e.g. for GE-
OVENT self-cleaning lters (GFB/GFH..)
R2: Alarm (dp for low/high). For connection of
external lamp/siren (e.g. 230V up to 4A)
R3: Press ok (dp within limit). Indicates that the
installation is running as planned
R4: Start signal to inverter (ends when box is
active.
Wiring diagram
1x230V
supply
Operating signal for lter control (start/stop).
Tells the lter if the fan is running
Operation signal for
inverter (start/stop)
0-10V signal to inverter.
Determines fan speed from setpoint 1
When DI1 + 12V is connected (is active),
the box is activated and regulates according
to setpoint 1

10
+24V
CTS relay -
activated when
the box is
activated.
T2 - 24V out
230V
10 11
Machine/welder
Note: If error, switch terminal 2 and 3 on freqency converter. This will typically solve the problam as 0V is sent in to AI
Control on GFB2 Filter
12 13 15 16
J N 0
230 V
Multibox IV
JN 0
230 V
Terminals
123
GFD Damper
1 2 3
54
Sensing coil
Machine/welder
N F
380 V
N F J FF
Power Smart II
START/STOP SIGNAL FOR FAN/MULTIBOX - connected in parallel
U + V + W +PE
1
2
3
4
5
6
7
8
9DI2
Start/Stop signal
Input Start/Stop
PowerBox III
230 V
GND +24V +24V
GFD Damper
123
NO
CNC
Power coil connects to
10 and 11
One phase from the
welding plant is looped
through the sensing coil
MULTICOUPLING DIAGRAM - TERMINALS, MULTIBOX AND FREQUENCY INVERTERS
SRC
AI1
AGND
GND
DCOM
DI1
400 V
L1
L1
L1
PE
Fi
R-
R+
ABB ACH 580
Start/Stop signal
U + V + W +PE
1
2
3
9
10
11
12
13
24V
DI1 is only used
in MultiboxDI1 is only used
in Multibox
DI1 is only used
in Multibox
SRC
AI
GND
GND
COM
DI1
400 V
L1
L1
L1
PE
Fi
R-
R+
ABB ACS 150
0-10V
Connect one of the
following frequency
inverters
N L
Quick guide - also see manual
Adjustment set point [Pa]
Min. Alarm limits [s] at too low pressure
Max. Alarm limit [s] at too high pressure
shows current pressure.
Adjusting the frequency inverter:
See manual - important parameters to adjust:
Motor data: Typically parameter group 99
Ramp up/down: Typically parameter group 22.
Frequency Max/Min:
Typically parameter group 20 and 11
IMPORTANT
Jumper on the bottom (S1) must be
switched from “I” to “U”
This will change output from current to voltage.
Remember to bridge GND and COM.
Enable input
Fan input
Adjusting Multibox IV:
Fi
R-
R+
SRC
AI2
COM
PW
COM
S1
400 V
T
S
R
PE
INVT GD20
Start/Stop
signal
U + V + W +PE
+24V
SRC
AI1
COM
PW
COM
S1
400 V
T
S
R
PE
INVT GD350
Start/Stop
signal
U + V + W +PE
+24V
R1 lter R4 INVT
start
NO
NO D1 12V AO1 G

11
3
1
3
2
4
Contact set.
Terminals
1 2 3
GFD Damper
1 2 3
54
Sensing coil
Machine/welder
N F
380 V
N F J FF
Power Smart
230 V
GFD Damper
1 2 3
1
3
2
4
Contact set.
Micro Switch
Ect.
230 V
GFD Power
1 2
GFD Damper
1 2 3
NO - blue
Common
- (Black)
NC - Grey
Terminals: Max.
external connection
250V, 6A
Functions:
Black/blue=Connect
Black/grey=break
MULTI COUPLING DIAGRAM - TERMINALS, MULTIBOX AND FREQUENCY INVERTERS
N L
GFD Power
1 2
N L N L
START/STOP SIGNAL FOR
FAN/MULTIBOX
230 V230 V
GFD Power
1 2
GFD Damper
1 2
GTE Hose Reel GTS Hose Reel
Multibox IV
J N 0
230 V
Start/Stop signal
SRC
AI
GND
GND
COM
DI1
380 V
L1
L1
L1
PE
Fi
R-
R+
ABB ACS 150
Start/Stop signal
U + V + W +PE
1
2
3
4
5
6
7
8
9DI2
SRC
AI1
AGND
GND
DCOM
DI1
380 V
L1
L1
L1
PE
Fi
R-
R+
Fi
R-
R+
ABB ACH 580
Start/Stop
signal
U + V + W +PE
1
2
3
9
10
11
12
13
24V
+24V
SRC
AI2
COM
PW
COM
S1
400 V
T
S
R
PE
INVT GD20
Start/Stop
signal
U + V + W +PE
+24V
SRC
AI1
COM
PW
COM
S1
400 V
T
S
R
PE
INVT GD350
Start/Stop
signal
U + V + W +PE
+24V
230 V
GFD trafo
1 2
1 2 3
N L
1
3
2
4
Connect one of the
following frequency
inverters
DI1 is only used
in MultiboxDI1 is only used
in Multibox
DI1 is only used
in Multibox
DI1 is only used
in Multibox
Balance
contact
Contact set.
GFD Damper
R1 lter R4 INVT
start
NO
NO D1 12V AO1 G
Input start/stop

12
Quick guide for
frequency inverter setup.
ABB ACS 150
”AI” adjustment type is set to ”U” on the micro switch (0-10V)
If Multibox II is used, control mode
is set at ”REM”.
”LOC” = Control using front panel.
”REM” = External PID control.
Access parameter list.
Press menu and select Par L
Menu
Exit Arrows
Now it is possible to scroll through the parameter list using arrows.
(Shown: example)

13
Quick guide for
frequency inverter setup.
ABB ACS 150
”AI” adjustment type is set to ”U” on the micro switch (0-10V)
If Multibox II is used, control mode
is set at ”REM”.
”LOC” = Control using front panel.
”REM” = External PID control.
Access parameter list.
Press menu and select Par L
Menu
Exit Arrows
Now it is possible to scroll through the parameter list using arrows.
(Shown: example)
Operation Limits
Setup the allowed current. In many cases the same as
indicated on the label on the motor. For example. 2,6A
Setup minimum frequency.
Set at 15Hz. If set lower, both fan and frequency inverter may
suffer damage.
Set max. frequency.
Set at max allowed frequency for the current fan.
Setup the motor´s rated voltage as indicated on
the motor label. For example 400V
Setup the motor´s rated current as indicated on
the motor label. For example 2,6A
Setup the motor´s rated frequency as indicated on
the motor label. For example 50Hz
Setup the motor´s rated speed as indicated on
the motor label. For example. 2830 rpm
Setup the motor´s rated power consumption as indicated on
the motor label. For example 4Kw
Motor data setup

14
Setup ramp up time.
Normally about 20 seconds.
(Ramp time correlates with fan size –the larger the fan, the longer the ramp time)
Setup ramp down time.
Normally about 50 seconds
(Ramp time correlates with fan size –the larger the fan, the longer the ramp time
Ramp time setup.
Setup max reference.
Setup the value(Hz) of max reference voltage (10V).
If you want the fan to run at for ex. 55Hz set it at 55Hz.
(If you do not set this parameter the fan will not run faster
than 50Hz)
This is a quick guide for setting up the frequency inverter with the minimu required settings.
These settings apply to a typical Geovent product constellation, and are not directly applicable for use with other products.
For settings of other parameters/macros and detailed explanation hereof, see the instructions manual from ABB.
Setup ramp up time.
Normally about 20 seconds.
(Ramp time correlates with fan size –the larger the fan, the longer the ramp time)
Setup ramp down time.
Normally about 50 seconds
(Ramp time correlates with fan size –the larger the fan, the longer the ramp time
Ramp time setup.
Setup max reference.
Setup the value(Hz) of max reference voltage (10V).
If you want the fan to run at for ex. 55Hz set it at 55Hz.
(If you do not set this parameter the fan will not run faster
than 50Hz)
This is a quick guide for setting up the frequency inverter with the minimu required settings.
These settings apply to a typical Geovent product constellation, and are not directly applicable for use with other products.
For settings of other parameters/macros and detailed explanation hereof, see the instructions manual from ABB.

15
Setup ramp up time.
Normally about 20 seconds.
(Ramp time correlates with fan size –the larger the fan, the longer the ramp time)
Setup ramp down time.
Normally about 50 seconds
(Ramp time correlates with fan size –the larger the fan, the longer the ramp time
Ramp time setup.
Setup max reference.
Setup the value(Hz) of max reference voltage (10V).
If you want the fan to run at for ex. 55Hz set it at 55Hz.
(If you do not set this parameter the fan will not run faster
than 50Hz)
This is a quick guide for setting up the frequency inverter with the minimu required settings.
These settings apply to a typical Geovent product constellation, and are not directly applicable for use with other products.
For settings of other parameters/macros and detailed explanation hereof, see the instructions manual from ABB.
Setup ramp up time.
Normally about 20 seconds.
(Ramp time correlates with fan size –the larger the fan, the longer the ramp time)
Setup ramp down time.
Normally about 50 seconds
(Ramp time correlates with fan size –the larger the fan, the longer the ramp time
Ramp time setup.
Setup max reference.
Setup the value(Hz) of max reference voltage (10V).
If you want the fan to run at for ex. 55Hz set it at 55Hz.
(If you do not set this parameter the fan will not run faster
than 50Hz)
This is a quick guide for setting up the frequency inverter with the minimu required settings.
These settings apply to a typical Geovent product constellation, and are not directly applicable for use with other products.
For settings of other parameters/macros and detailed explanation hereof, see the instructions manual from ABB.
Quick guide for
Frequency inverter setup.
ABB ACH 580
If Multibox is used, set control mode to
”AUTO”.
”Hand” = Control using front panel.
”Auto” = External PID control.
Access setup menu.
Press ”menu”
Now choose The parameter groups you need to setup. On the
following pages you will be guided through the parameters we
Recommend you setup.
Select ”Primary settings”.
Function keys

16
Operation limits
Maximum current
Setup the max allowed current. In many cases this is the same
as indicated on the motor nameplate. For example 2.6A
Minimum frequency
Setup minimum allowed frequency. Set at 15Hz. If set lower,
both fan and inverter may suffer damage.
Maximum frequency
Set maximum frequency.
Set maximum allowed frequency for the selected fan.
Voltage
Current
Frequency
Speed
Power
Setup the motor´s rated voltage as indicated on the motor
nameplate. For exampel 400V
Setup the motor´s rated current as indicated on the motor
nameplate. For exampel 2.6A
Setup the motor´s rated frequency as indicated on the motor
nameplate. For exampel 50Hz
Setup the motor´s rated speed as indicated on the motor
nameplate. For exampel 2830 rpm
Setup the motor´s rated power comsumption as indicated on
the motor nameplate. For exampel 4Kw
Motor data setup
In ”primary settings” select ”motor”.
In ”Primary settings” select ”Limits”.
9906
9909
9907
9908
9910
3013
3014
3017

17
This is a quick guide for setting up the frequency inverter with the minimum required settings.
These settings apply to a typical Geovent product constellation, and are not directly applicable for use with other products.
For settings of other parameters/macros and detailed explanation hereof, see the instructions manual from ABB.
Setup ramp up time. Normally 20 seconds. Acceleration time
Deceleration time
Setup ramp down time. Normally 50 seconds.
Ramp time setup
Setup max reference.
Max scale
Setup the value(Hz) of max reference voltage(10V). If you set the
parameter 2008 to ex. 55Hz then set this parameter to 55Hz too.
Activate/deactivate DI4 as start condition.
Standard setting is DI4 is activated as start condition. We recommend
removing the checkmark.
Setup start conditions.
Use start interlock 1
In ”Primary settings” select ”Ramps”.
In ”Primary settings” select ”Start, stop,reference”. In the following page
select ”Primary auto control location” and then ”AI1 -scale”
In ”Start, stop, reference” select ”Interlocs/permissives”.
(Ramp time correlates with fan size – larger fan = more ramp time)
(Ramp time correlates with fan size – larger fan = more ramp time)
2872
2873
1220
2041
2211

1818
10.0 Dismantling, disabling and scrapping
Deactive the product by disconnection the electrical
mains. Dismantle compressed air pipes and other pipes
or wires etc.
Dismantle the filter cartridge by unscrewing the finger
screws and remove the service hatch.
Turn the filter cartridge so that is loosens from the lat-
ches at the top of the cartridge.
Carefully remove the contaminated filter cartridge, place
it in a plastic bag and seal the bag.
Dispose of it according to local regulations.
The inside of the product must be cleaned by means of
a vacuum cleaner with a filter which suits the purpose.
The inside of the product must be cleaned by means of
a vacuum cleaner with a filter which suits the purpose.
Dismantle plastic parts and dispose of it according to
local regulations.
Dismantle the metallic parts by unscrewing screws and
bolts. Afterwards cut the larger pieces into smaller pie-
ces and dispose of it according to local regulation.
Dismantle plastic parts and dispose of it according to
local regulations.
The packing material must be sorted according to local
regulation in order to be able to reuse the material.
11.0 Dimensions
MultiBox IV
8.0 Cleaning
The outside of the product is cleaned with a vacuum
cleaner or a cloth.
9.0 Troubleshooting
For problems with operation, please refer to installation,
setup and testing in section 5.0.
Sometimes commuting is experienced
Pendulum may be caused by an imbalance in the sy-
stem, where individual components get out of balance,
and therefore fine tuning may be necessary.
Follow the guide below:
1. Always start by examining the measuring point. I.e.
where is the pressure hose? This should be in a place
where there is no turbulence.
This is checked by putting the frequency converter in
manual and reading if the fluctuations become smaller.
If the measurements in the MultiBox are stable, this
fault can be ruled out.
If it continues to fluctuate, the measurement point
must be moved.
2. The parameters P, I and D are changed in the Multi-
Box.
• Neutral zone is set to e.g. 30 Pa
• P-factor is set to 0,001
• I-factor is set to 0,001
3. In most cases it is not necessary to change the neutral
zone, but if the measuring point is very unstable, it
may be helpful to set it to e.g. 30Pa.
4. The ramp times in the frequency converter are chan-
ged.
Typically, longer ramp times will help.
This could be changing the ramp up and down, for
example from 10 to 20 seconds.
The correct ramp time depends on the wheel size and
rotation speed.
The bigger the wheel, the longer the ramp time.
• For ABB converters this is usually changed in para-
meter group 22-02 and 22-03, but always check the
manual.
• For GeoDrive inverters this is usually changed in
parameter group P00.11 and P00.12, but always
check the manual.
150 mm
150 mm

19
12.0 Liability
Warranty
Geovent A/S grants a warranty for products, which are
defective, when it can be proved that the defects are due
to poor manufacture or materials on the part of Geovent.
The warranty comprises remedial action (reparation or
exchange) until one year after the date of shipment.
No claims can be made against Geovent A/S in relation
to loss of earnings or consequential loss as a result of
defects on products from Geovent.
Wear on parts such as filter cartridges and hose is not
included in the warranty.
User liability
In order for Geovent to be capable of granting the decla-
red warranty, the user/fitter must follow this instruction
manual in all respects.
Under no circumstances may the products be chan-
ged in any way, without prior written agreement with
Geovent A/S.
Please refer to the current sales and delivery conditions
at www.geovent.com
13.0 Declaration of conformity
The manufacturer: GEOVENT A/S
HOVEDGADEN 86
DK-8831 LØGSTRUP
Hereby declares that:
The product: MultiBox
Model: IV
Complies with the relevant parts of the following directi-
ves and standards:
Directive 2006/42 / EC of the European Parliament and
of the Council of 17 May 2006 on machines and amen-
ding directives 95/16 / EC.
This declaration is no more valid if changes are made to
the product by others than the manufacturer.
Authorized to collect the technical file:
Lise Cramer
Date: 09.02.2023
Position: Director
Name: Thomas Molsen
Signature: ____________________________

20
Table of contents
Other Geovent Controllers manuals
Popular Controllers manuals by other brands

Kobelt
Kobelt 6505 Owner's Operation, Installation & Maintenance Manual
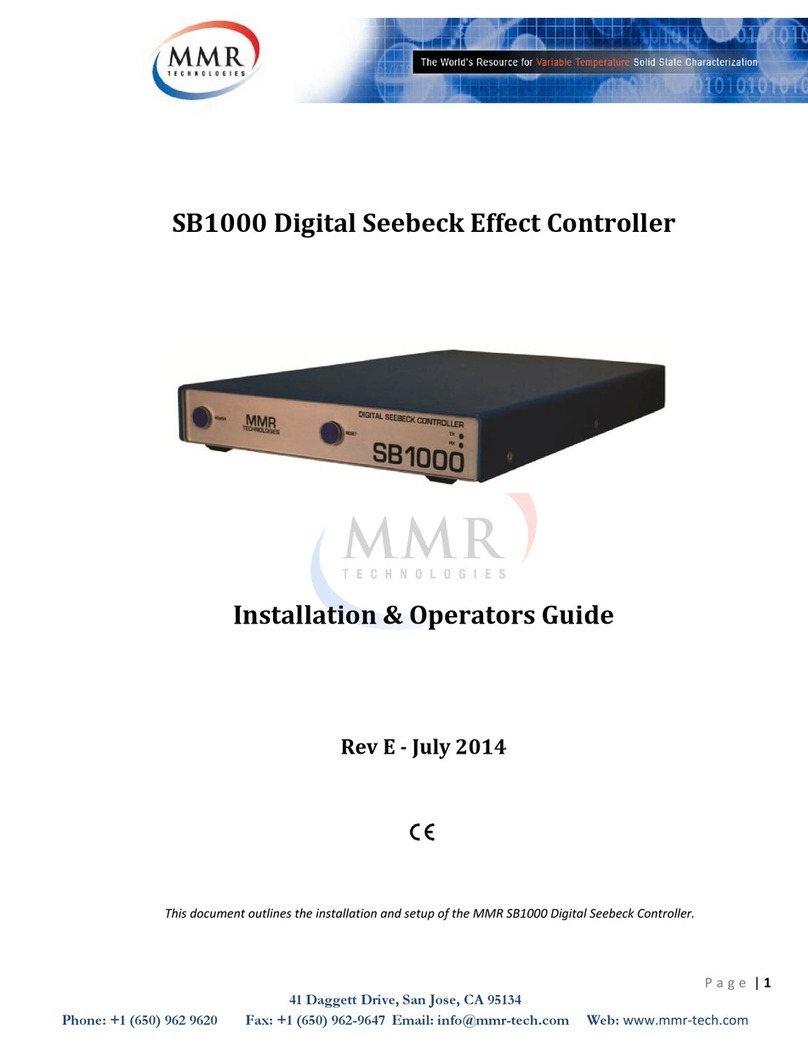
MMR
MMR SB1000 Installation & Operator’s Guide
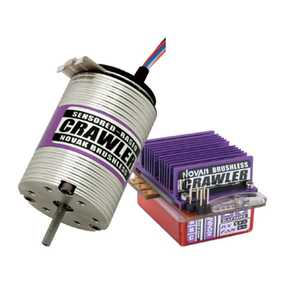
NOVAK
NOVAK GOAT CRAWLER BRUSHLESS SYSTEM Setup guide
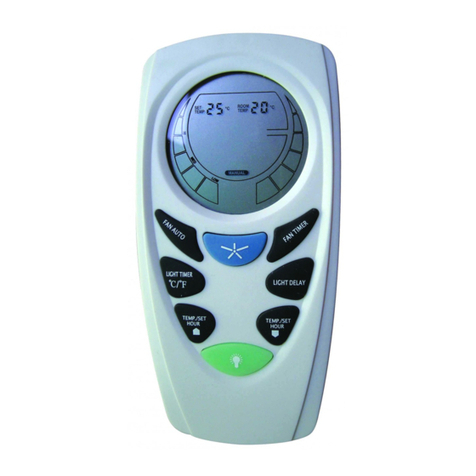
Beacon
Beacon LUCCI LCD Installation and use instruction

Emerson
Emerson Dixell XF330M Installing and operating instructions
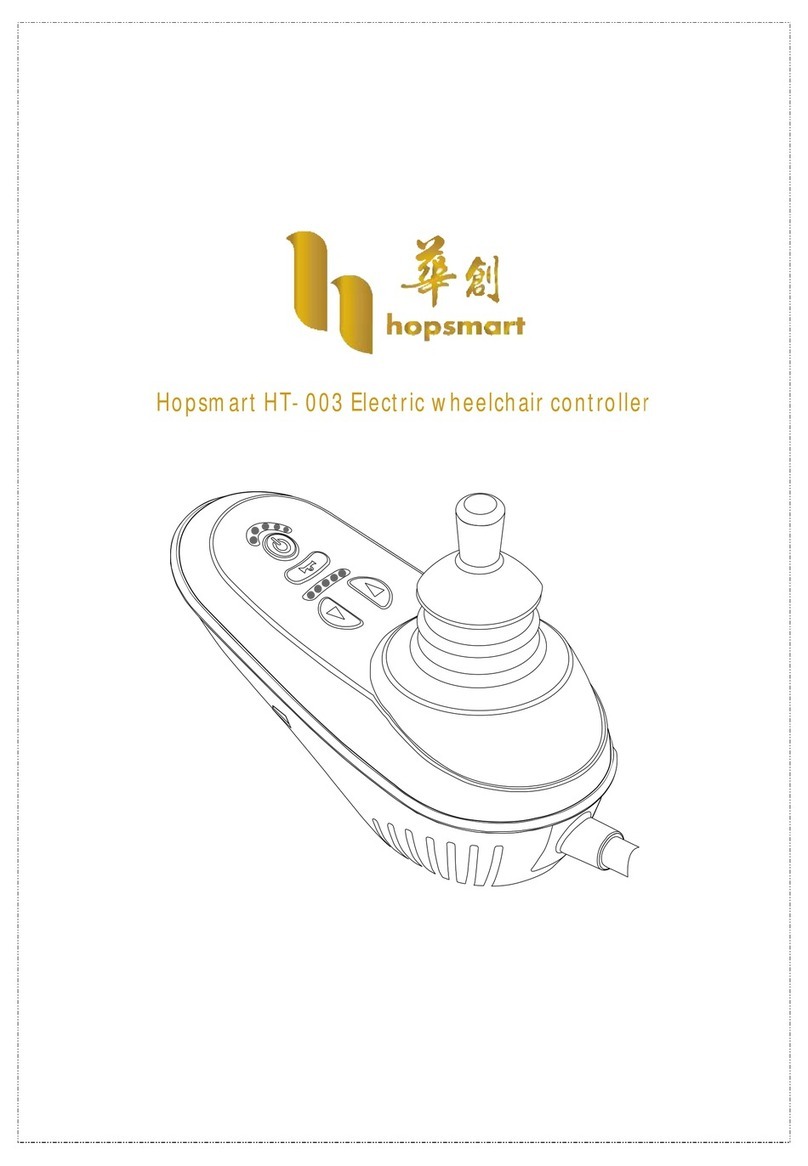
hopsmart
hopsmart HT-003 manual