GMP PULLDOG 70625 Installation guide

Operation and Maintenance
Model 70625
All rights reserved. No part of this publication may be copied, reproduced or transmitted in any form whatsoever without
the written permission of General Machine Products (KT), LLC
General Machine Products (KT), LLC • 3111 Old Lincoln Hwy • Trevose, PA 19053 • USA
TEL: +1-215-357-5500 • FAX: +1-215-357-6216 • WEB:www.gmptools.com
PULLDOG
Overhead Line Winch Trailer
5/16/2018 Ver 2 USA AK
36202

2
General Machine Products (KT), LLC • 3111 Old Lincoln Hwy • Trevose, PA 19053 • USA
TEL: +1-215-357-5500 • FAX: +1-215-357-6216 • www.gmptools.com
Rev.no Date Details Author
19/21/15 First U.S. Version A Konschak
207/18/17 Changed company name A Konschak
CONTENTS
1. Introduction
2. Safety Instructions
3. General Description
4. Specification
5. Operating Procedures
6. Maintenance
7. Towing Instructions
8. Equipment Layout
GMP Limited Warranty can be found at hp://www.gmptools.com/warranty/
QC Final Inspecon by:_________________________ Date:__________________
Unit Serial Number:__________________
Build Date:__________________

3
General Machine Products (KT), LLC • 3111 Old Lincoln Hwy • Trevose, PA 19053 • USA
TEL: +1-215-357-5500 • FAX: +1-215-357-6216 • www.gmptools.com
Founded by engineer George M. Pfundt in 1936, GMP started operations in a
downtown Philadelphia building as a specialty machine shop doing work for
the local Bell Telephone company and for the electric utility company. GMP
expanded to a production shop after landing a contract with Western Electric
Company and, subsequently, form-
ing a close relationship with Bell
Telephone Laboratories in Murray
Hill, N.J., which enabled it to manufacture prototypes of
products for experimental use within the Bell System.
Having outgrown the original factory building, the company
built a 100,000 square foot plant in Trevose, PA (a Phila-
delphia suburb) and moved there in 1957. Today GMP is
recognized as a premier worldwide supplier of specialty
tools and equipment for the outside plant marketplace.
The company's products are known for their robust design
and durability to withstand many years of frequent use.
1.0 INTRODUCTION

4
General Machine Products (KT), LLC • 3111 Old Lincoln Hwy • Trevose, PA 19053 • USA
TEL: +1-215-357-5500 • FAX: +1-215-357-6216 • www.gmptools.com
2.0 SAFETY INSTRUCTIONS
THIS EQUIPMENT MUST ONLY BE USED BY AUTHORIZED PERSONNEL, WHO
HAVE BEEN SUITABLY TRAINED AND COMPETENT TO DO SO.
1. Read and understand the operation and maintenance manual supplied with this
equipment. Keep it in a convenient place for future reference.
2. Keep children and untrained personnel away from this equipment while in operation.
3. Keep all guards and safety devices in place. Do not operate this equipment with
guards removed or damaged.
4. Keep hands, feet and loose clothing away from moving parts.
5. Always stop the machine to carry out lubrication or servicing.
6. Check machine before starting for worn or damaged parts. Check that all nuts and
bolts are tight.
7. If machine is left unattended, ensure that unauthorized use is prevented.
8. Never leave the machine unattended while in use.
9. Consider the use of safety barriers, especially when used in public places.
10.Beware of pinch points involved with rotating components, e.g. rope/cable drums,
capstans, bull wheels, shafts and chain drives.
11.Beware of hot surfaces, especially around the engine, engine exhaust pipe and hy-
draulic oil tank.
12.Some component and assembly parts are in excess of 55 lbs. (25kg) . When lifting
care must be taken, ensure sufficient man power/lifting gear is available, to pre-
vent personal injury and damage to the machine.
13.Beware of exposed electrical contacts especially around the engine. Do not
touch, or allow metal objects to come into contact.
14.Waste engine and hydraulic oils are to be disposed of via an environmental-
ly acceptable method – e.g. passed on for recycling.
15.Wear ear protection when engine is running to prevent ear damage.
16.Machine may cause additional fire hazard if involved in an existing fire due to gaso-
line, diesel, oil and hydraulic oils involved.
17.No personnel are to be in manholes or ducts when the winch is being operated.
18.The machine must be operated on firm ground.
19.Stay clear of cables or lines under tension.
20.Only use the machine for its intended purpose.
21.Do not tamper with pressure relief valves or pressure reducing valves.
22.Rear stabilizing props must be down and on solid surface before use.
THESE INSTRUCTIONS ARE TO BE MADE AVAILABLE TO
OPERATORS OF THIS EQUIPMENT AT ALL TIMES, FAILURE TO
OBSERVE THESE SAFETY INSTRUCTIONS COULD RESULT IN
SERIOUS PERSONAL INJURY AND / OR PROPERTY DAMAGE.

5
General Machine Products (KT), LLC • 3111 Old Lincoln Hwy • Trevose, PA 19053 • USA
TEL: +1-215-357-5500 • FAX: +1-215-357-6216 • www.gmptools.com
3.0 GENERAL DESCRIPTION
4.0 SPECIFICATION
Max. Pulling Capacity (Bare Drum) 1100 lbs. (500kg)
Max. Pulling Capacity (Full Drum) 400 lbs. (181kg)
Rope Speed Max. (Bare Drum) 170 ft./min (52m/min)
Rope Speed Max. (Full Drum) 470 ft./min (143m/min)
Take-up Drum Capacity 2000 ft. X 5/16” rope 610m X 8mm rope
Dimensions: Length: 91.5” (2325mm)
Overall Width: 55” (1400mm)
Height: 40” (1016mm)
Weight: 650 lbs. ( 295kg)
Tire Size: 5.70 x 8
Coupling: 1 7/8 ball
Lighting Adapter: 4-Way flat (others available by request)
Power Supply: Honda GX390 11.7 HP, Recoil Start, Overhead Valve, Cast
Iron Cylinder Sleeve, 1.5 Gallon tank
Main Drive: Fixed displacement tandem pump to fixed displacement high
torque motor.
Controls: Pay-in / pay-out spring centered control valve.
Hydraulic Circuit: Closed circuit system with full filtration and overload protection
Hydraulic Oil Tank Capacity: 2.9 Gal. (11 liters)
Hydraulic Oil Grade: Tellus S2V32
Four Way Plug Wiring
Right Turn
Le Turn
Tail Lights
Ground (White)
The Pulldog winch is a compact, transportable unit for any
number of outside plant activities that’s easily pulled behind
a small SUV or truck. The self-contained winch is powered
by an 11.7 hp gasoline engine and the precise control
required is provided by the hydraulic circuit.
The Honda GX390 engine drives a fixed displacement
pump, which in turn drives a fixed displacement high torque
motor. The circuit is controlled by a spring centered
hydraulic valve, which provides selective direction of drum
rotation. The lever acts as a dead mans handle in that letting
go stops everything in a safe mode. The circuit design also
includes the ability to provide inching or very slow speed control in both directions under tension, ideal
for overhead line use.
The sturdy steel construction chassis is equipped with manually operated stabilizing props to assist
when pulling.
The Pulldog Winch is designed to meet the needs of overhead line engineers. The various options permit
use on aerial bundle (ABC), Copper, Aluminum and ACSR Conductors.

6
General Machine Products (KT), LLC • 3111 Old Lincoln Hwy • Trevose, PA 19053 • USA
TEL: +1-215-357-5500 • FAX: +1-215-357-6216 • www.gmptools.com
5.0 OPERATING PROCEDURE
IT IS IMPERATIVE THAT ALL PERSONS USING, OPERATING OR MAINTAINING THIS WINCH BE
FULLY TRAINED AND COMPETENT TO DO SO, AND HAVE READ THE ENTIRE OPERATING MANUAL.
GENERAL MACHINE PRODUCTS (KT), LLC CANNOT BE HELD RESPONSIBLE FOR MIS-USE OF THIS
EQUIPMENT.
To enable safe and trouble free operation the following points should be followed.
Prior to employing the winch for any hauling applications it is important to ensure that the winch is suita-
bly anchored to a Vehicle.
5.1 Ensure that the ball coupling and the center of the drum width is
oriented with the line of pull. See Fig 5.1. This ensures that reeling
of the rope takes place without undue pressure on the layering de-
vice and extends rope life.
5.2 Vehicle Anchoring - Preferred method of anchoring
Align the winch as in 5.1 keeping the ball coupling securely attached
to the vehicle. Lower the rear prop legs and lift winch weight off
wheels onto legs and fix. Ensure winch is level from side to side.
5.3 Ground Rod Anchoring (if vehicle anchoring is not obtainable)
Lower the rear prop legs and front prop to the ground, such that the winch is level from side to side and
the weight is off the wheels. Drive a ground anchor through each chassis anchor bracket at the tow eye
end of the chassis, See Fig 5.3A, The quality of the ground needs to be assessed with regards suitability
for winch anchoring prior to winch operation.
5.4 Loading/Unloading drums
To load/unload a drum it is necessary to remove the rear spool guard. This
should be stored in a suitable place and re-fitted when the trailer is to be
used in transit again. Open the split bearing and slide the drum to the right.
Lift the drum vertically initially favoring the side with the split bearing. Re-
verse to install.
Remove pins and remove spool guard Open split bearing Slide drum out of coupling Remove drum
Fig 5.3A
Fig 5.1

7
General Machine Products (KT), LLC • 3111 Old Lincoln Hwy • Trevose, PA 19053 • USA
TEL: +1-215-357-5500 • FAX: +1-215-357-6216 • www.gmptools.com
5.5 Pulling Out Winch Line
Place the drum free wheel mode by disengaging the coupling and the winch
line can be simply pulled out as required.
5.6 Starting Engine
The engine fuel tank should be filled with the correct grade of fuel before
commencing, refer to the Engine Operating Manual for details. Switch the ig-
nition, switch it ‘ON’. Turn on the choke, set the throttle to half and pull starting handle in a long steady
stroke to start. For further details refer to the Engine Operating Manual.
5.7 Driving Drum
Rotate the drum until the couplings on drum and motor align
and slide drum towards motor, and then rotate drum to ensure
the drum is engaged.
With engine running the control valve can now be engaged.
Pulling the handle back wards towards the towing eye will com-
mence drum rotation, pulling the rope in. The handle controls
direction and speed. Pushing handle toward reverses direction
of rotation.
5.8 Layering Device
The arrangement fits to the side arm with the motor mounted
on, and is secured with a ‘R’ clip. The layering device is used to assist layering of the winch line. Careful
setting of the equipment will prevent excessive forces on the layering device. Always wear protective
gloves when operating the layering arm.
The layering arm MUST NOT be used for conductor recovery.
5.9 Holding Ratchet
This device is fitted to the drum drive coupling and should be kept in the
open position (i.e. non operational). The holding ratchet should only be
used after pulling through heavy conductor when winching has stopped
and conductor is held ready for sagging.
To remove holding ratchet after engaging, it is necessary to start the winch
and pull further to remove load, prior to removal of ratchet.
IN OUT

8
General Machine Products (KT), LLC • 3111 Old Lincoln Hwy • Trevose, PA 19053 • USA
TEL: +1-215-357-5500 • FAX: +1-215-357-6216 • www.gmptools.com
6.0 MAINTENANCE
IT IS IMPERATIVE THAT ALL PERSONS USING, OPERATING OR MAINTAINING THIS WINCH BE FUL-
LY TRAINED AND COMPETENT TO DO SO, AND HAVE READ THE ENTIRE OPERATING MANUAL.
GMP CANNOT BE HELD RESPONSIBLE FOR MIS-USE OF THIS EQUIPMENT.
It is recommended that this winch is serviced every 12 months, regardless of its condition or
the number of operating hours used. This will help to ensure reliable, trouble free service.
6.1 PRE-WINCHING MAINTENANCE CHECK
This should be carried out each day prior to the start of winching.
• Check hydraulic oil level. Oil should be visible within the black lines marked on the oil level sight
gauge. Replenish if necessary with the correct grade of hydraulic oil to suit the climatic conditions.
(Refer to the section 4 for grades of hydraulic oil required)
• Check the engine oil level as indicated in the Engine Operating Manual. Replenish if necessary.
• Check that there is enough fuel in the tank to complete the planned winching schedule.
• Check the condition of the hydraulic hoses, replace if damaged.
• Check that the drum arm split bearing is clean and lightly greased.
• Check that the drum shaft bearing spigot is clean.
• Check the tire condition and tire pressures, refer to section 4 of details.
b) MONTHLY MAINTENANCE
•
This should be carried out at intervals not exceeding 12 weeks. These intervals will
depend upon the degree of use of the winch.
• Carry out all the pre-winching checks as detailed above.
• Apply a general purpose, medium grade grease to the towing hitch grease nipples (if applicable)
and also to the towing ball up if fitted.
• With the engine and drum running, check the return filter condition indicator. This is red/green
indicator mounted on the hydraulic oil tank filter. If the indicator is well over into the red area, re-
place the filter.
• Apply grease to the layering arm spindle.
!
!

9
General Machine Products (KT), LLC • 3111 Old Lincoln Hwy • Trevose, PA 19053 • USA
TEL: +1-215-357-5500 • FAX: +1-215-357-6216 • www.gmptools.com
6.3 ANNUAL SERVICING
This service should be carried out at approximately 12 monthly intervals by a qualified and
experienced workshop team.
• Carry out all the work as specified above in section 6.2
• Drain the hydraulic circuit of oil. Clean the filler/breather and replace. Renew the suction filter
element and the return filter element. Refill with fresh oil, refer to specification Section 4 for fur-
ther details. Check and reset all relief valves.
• Service the engine as per the engine manufacturers manual supplied as part of this manual.
• Check the condition of the tires and running gear. Adjust and reset if necessary.
• Check the condition of the towing breakaway cable. If frayed, kinked or damaged, replace imme-
diately.
!
Typical User Replaceble Parts: Part Number:
Oil Tank Filler Breather 36268
Oil Tank Suction Filter 36269
Return Line Filter Element 36270
Sight Level Gauge 36271
Return Line Filter Element Replacement
Replace the Return Line Filter Element when the
arrow of the clogging indicator is in the red range.
1. Unscrew the return
line lter top cap using a
suitable wrench.
2. Remove the clogged ele-
ment and plasc carrier.
Twist and pull the element
to separate it from the car-
rier. Install new element in
carrier and drop in lter
housing.
3. Replace the top cap mak-
ing sure not to cross the
thread. Check for leaks aer
USER REPLACEABLE PARTS
Indicator showing need for filter
element replacement.
Return Line Filter Element

10
General Machine Products (KT), LLC • 3111 Old Lincoln Hwy • Trevose, PA 19053 • USA
TEL: +1-215-357-5500 • FAX: +1-215-357-6216 • www.gmptools.com
7.0 TOWING INSTRUCTIONS
BEFORE TOWING
a) Check that the ball coupler cup is well greased.
b) Lower the trailer’s coupler on the towing vehicles towing hitch ball.
c) Grasp locking handle on top of coupling and press trigger backwards with thumb.
Then lift handle (you can now release trigger). With handle still raised wind up
jockey wheel until ball on towing vehicle enters ball cup on coupling. Now release
handle and continue winding up jockey wheel until locking handle automatically
drops down and trigger snaps shut. If this does not occur lift handle again and
check if ball seats this time and trigger snaps shut. If there is still no success,
check if ball or head is worn.
SERVICING
a) Apply grease to ball and to cup of ball head after cleaning each item. (Alternatively towing
eye and jaw if fitted). This to be carried out each time the trailer’s to be towed.
b) Oil all moving parts weekly having wiped away all corrosion and dirt deposits.

11
General Machine Products (KT), LLC • 3111 Old Lincoln Hwy • Trevose, PA 19053 • USA
TEL: +1-215-357-5500 • FAX: +1-215-357-6216 • www.gmptools.com
8.0 EQUIPMENT LAYOUT
1
12
10
7
4
5
6
11
12
9
8
3
1. HYDRAULIC OIL TANK
2. ENGINE
3. HYDRAULIC PUMP
4. WINCH IN / OUT CONTOL LEVER
5. LAYERING ARM
6. HITCH COUPLING
7. HYDRAULIC MOTOR
8. HYDRAULIC OIL TANK SIGHT LEVEL GLASS
9. HYDRAULIC OIL TANK FILLER BREATHER
10. RETURN LINE FILTER
11. ROPE DRUM
12. REAR PROP
13. FRONT PROP
14. SUCTION FILTER
15. REMOVABLE REAR BUMPER
15
2

12
General Machine Products (KT), LLC • 3111 Old Lincoln Hwy • Trevose, PA 19053 • USA
TEL: +1-215-357-5500 • FAX: +1-215-357-6216 • www.gmptools.com
Table of contents
Other GMP Winch manuals
Popular Winch manuals by other brands

POWERWINCH
POWERWINCH BH12 owner's manual
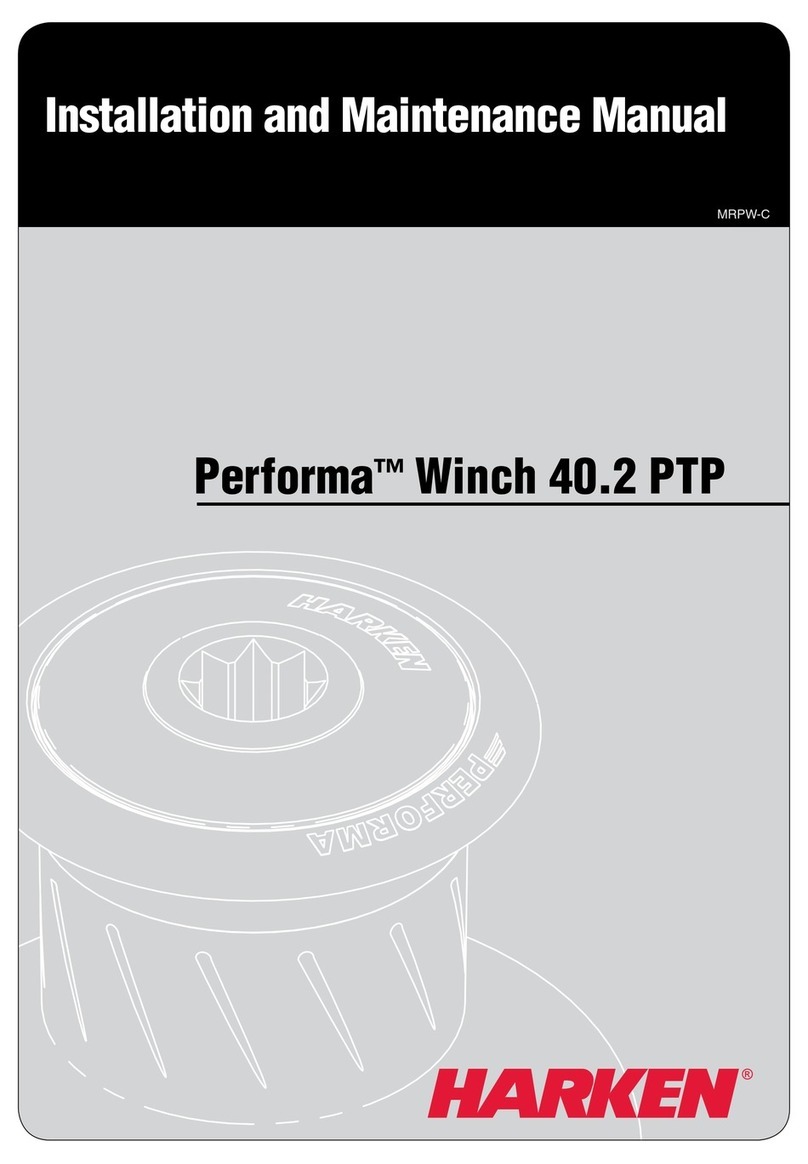
Harken
Harken Performa Winch 40.2 PTP Installation and maintenance manual
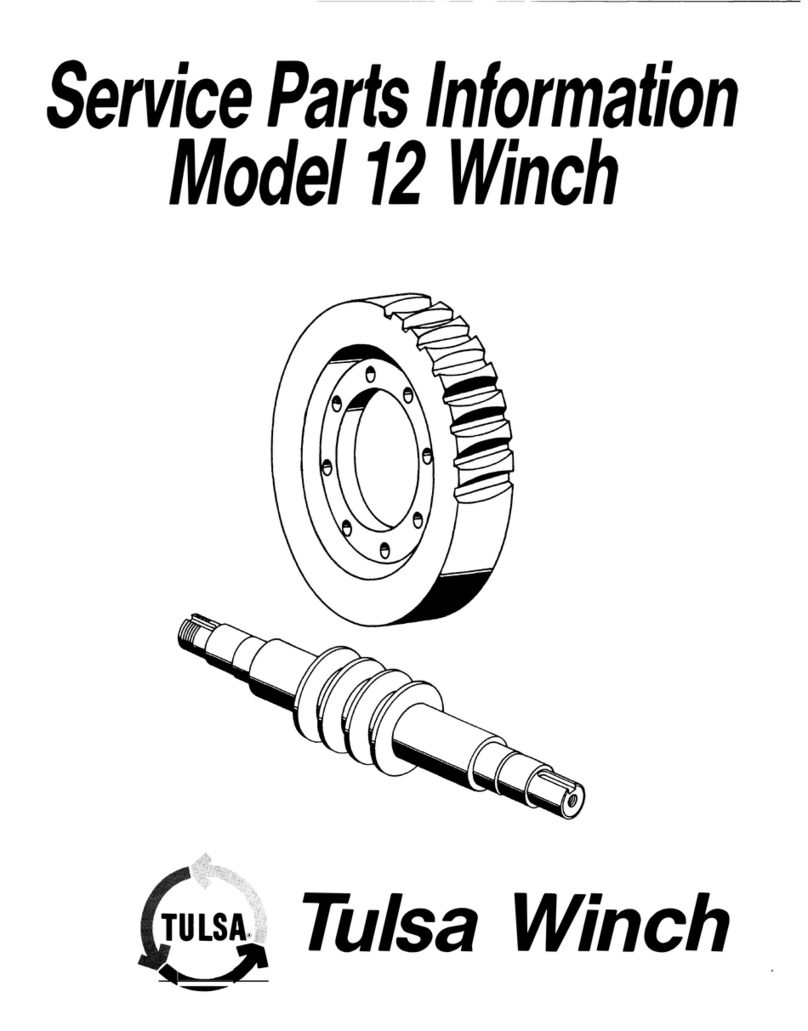
Dover
Dover TWG Tulsa 12-SLLRO Series Parts information
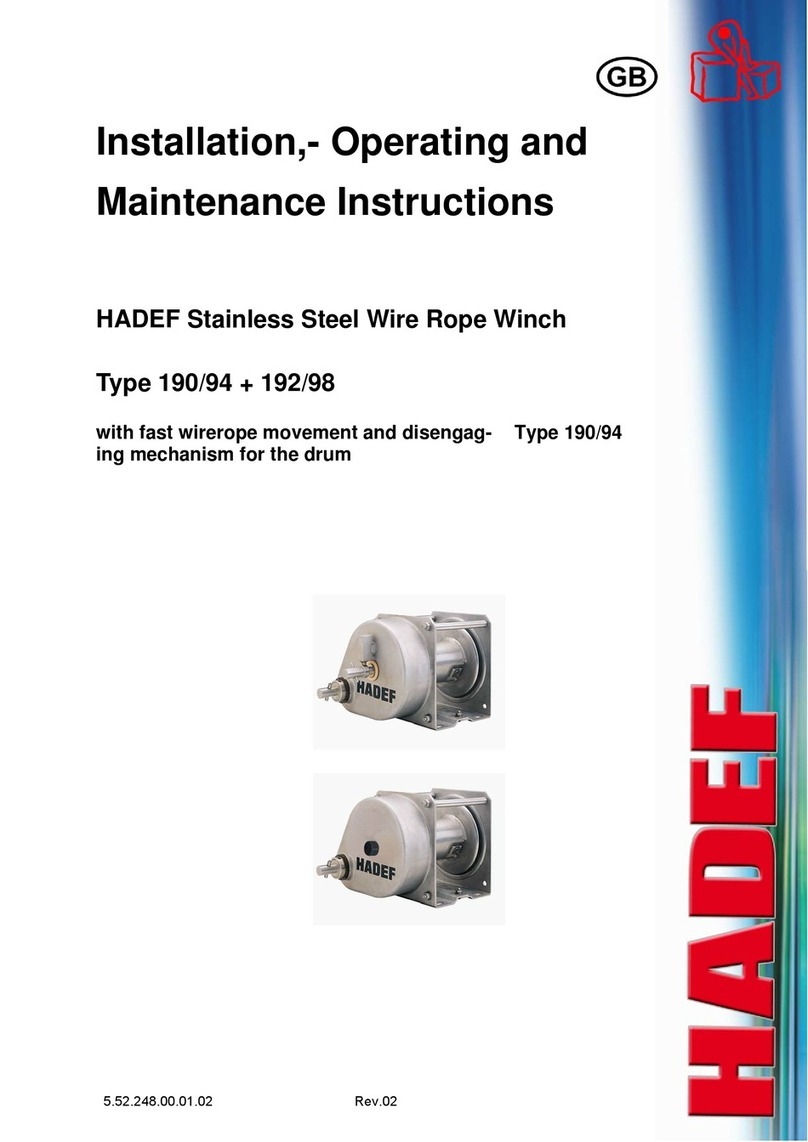
HADEF
HADEF 190/94 Installation, operating and maintenance instructions

Ingersoll-Rand
Ingersoll-Rand LIFTSTAR FG 1500/CN Series Parts, operation and maintenance manual
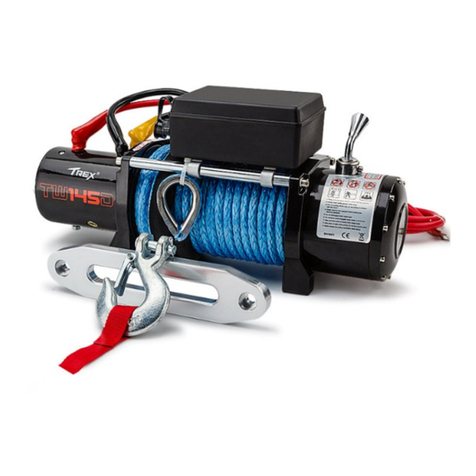
TREX
TREX TB75 user manual