GORBEL Tarca I Series Instruction manual

IMPORTANT!
DO NOT DESTROY
Installation, Operation,
& Maintenance Manual
Month Year
Gorbel®Dealer
Date
I Series
Tarca® Switch
Gorbel®Customer Order No. / Serial No.
®
Issued: 11/2018
Revised: 03/2019

11/2018
THIS PAGE INTENTIONALLY LEFT BLANK.

TABLE OF CONTENTS
Introduction............................................................................................................................ 1
Models and Options .............................................................................................................. 2
Installation
Step 1 - Pre-assembly ................................................................................................................ 3
Step 2 - Attachment and Hole Layout..........................................................................................4
Step 3 - Mounting.........................................................................................................................5
Step 4 - SAFPOWRBAR® Wiring (Option)..................................................................................6
Step 5 - Control Wiring (Option) ..................................................................................................7
Step 6 - Motorized Operator (Option) ...................................................................................... 8-9
Limit Switch Adjustment ............................................................................................. 8-9
Step 7 - Pneumatic Operator (Option) .......................................................................................10
Step 8 - Manual Operator (Option) ............................................................................................10
Appendix A - Beam End Prep Diagrams .................................................................. 11-14
Appendix B - Wiring Diagrams.................................................................................. 15-18
Crane Operator / Start Up Instructions ............................................................................... 19
General Safety Requirements............................................................................................. 19
Limited Warranty ................................................................................................................. 20
Inspection and Maintenance Schedule .......................................................................... 21-24
Questions? Concerns? Comments? Please call (800) 821-0086
11/2018

11/2018
THIS PAGE INTENTIONALLY LEFT BLANK.

INTRODUCTION
Thank you for choosing Gorbel® to solve your material handling needs. The innovative design and heavy-duty
construction of the Gorbel® product will provide a superior quality product that will offer years of long term value.
The hoist weight allowance is 15% of the crane’s capacity (for example, a crane rated for 6000 pounds, allows for a
6000-pound live load plus 900 pounds for the weight of the hoist). There is also an allowance of 15% of the crane
capacity for impact caused by hoist use. Gorbel® products will provide many years of dependable service by
following the installation and maintenance procedures described herein.
Gorbel® products are shipped in various stages of assembly and are installed under varying circumstances. As a
result, a complete guide with descriptions covering all variations is not possible. The following instructions are only to
be used as a general guide. Attention should be paid to the warnings and safety suggestions posted in this manual
and on the equipment.
Dimensions contained in this installation manual are for reference only and may differ for your particular
application.
Normal safety precautions: These include, but are not limited to:
• Checking for obstructions in travel
• Checking that all bolts and threaded rods are tight and have lock washers where applicable
• Making sure that end stops are in place and functional (i.e. stopping rolling equipment from exiting rail)
• Making sure that festooning cannot be snagged or pinched, whether it is electric or pneumatic
• For additional safety precautions, see page 19.
WARNING
Before installing any crane system, it is critical you determine that your building will safely support the loads.
1
11/2018
WARNING
Gorbel Inc. assumes no responsibility for adequacy or integrity of the mounting surfaces or the structure that the
crane may be mounted to. Gorbel Inc. will not be liable for any loss, injury or damage to persons or property, nor
for damages of any kind, resulting from the failure or defective operation of any materials not supplied directly by
Gorbel Inc. Bracing systems, if used, must be approved by a local professional engineer.
WARNING
Equipment described herein is not designed for, and should not be used for, lifting, supporting or transporting
humans. Failure to comply with any one of the limitations noted herein can result in serious bodily injury and/or
property damage. Check State and Local regulations for any additional requirements.
WARNING
Crane cannot be utilized as a ground: A separate ground conductor is required. For example, systems with 3 phase
power require three conductors plus one ground conductor.
WARNING
Reference the American Institute of Steel Construction (AISC) Manual of Steel Construction Specification
for Structural Joints using ASTM A325 or A490 Bolts, Installation, Pretensioned Joints, Calibrated Wrench
Pretensioning for the proper procedures to follow when using any torque tightening method.
WARNING
Please read entire manual prior to starting installation.

MODELS AND OPTIONS
Part Number:
PT.SWITCH.KIT - I -
5000 - R - M - 460 - H - 4 - G
211/2018
Power:
H = Manual
M = Motorized
P = Pneumatic SAFPOWRBAR® Position:
N = None
H = High
L = Low
Switch Style:
L = Left-Hand
R = Right-Hand
Y = Wye
T = 3-Way
SAFPOWRBAR
Quantity:
0, 4
Track Series:
See Runway Section of
Sales Manual
Voltage:
208, 230, 460, 575
Paint:
G = Gray Green
B = Blue
Y = Yellow
O = Orange
S = Special
N = None
SWITCH STYLE POWER VOLTAGE SAFPOWRBAR®
Left/Right Hand Manual None None
Left/Right Hand Manual None High/Low
Left/Right Hand Motorized 208/230 or 460/575 None
Left/Right Hand Motorized 208/230 or 460/575 High/Low
Left/Right Hand Pneumatic 208/230 or 460/575 None
Left/Right Hand Pneumatic 208/230 or 460/575 High/Low
Wye Manual None None
Wye Manual None High/Low
Wye Motorized 208/230 or 460/575 None
Wye Motorized 208/230 or 460/575 High/Low
Wye Pneumatic 208/230 or 460/575 None
Wye Pneumatic 208/230 or 460/575 High/Low
3-Way Manual None None
3-Way Manual None High/Low
3-Way Motorized 208/230 or 460/575 None
3-Way Motorized 208/230 or 460/575 High/Low
3-Way Pneumatic 208/230 or 460/575 None
3-Way Pneumatic 208/230 or 460/575 High/Low

STEP 1 - INSTALLATION
• It is recommended to install switch(es) first and align monorails to them.
• Read entire installation manual before you begin installing your switch.
• Study all instructions and drawings provided in this manual.
• Verify receipt of all materials in good condition. Check all hole punchings, beam dimensions
and suspension fittings prior to installation.
• Check packing list to make sure correct quantity of parts is included. Any missing items
should be noted and reported to a Gorbel® dealer.
• Tools and materials typically needed to assemble switch are as follows:
• Wrench/socket • Square
• Torque wrench • Tape measure
• Leveling tools • Ladders/man lifts
• Shims • Lifting device
• Standard switch throw is 11”. DO NOT ADJUST.
3
11/2018
NOTE: It is recommended to install switch(es) first and align monorails to them.

STEP 2 - ATTACHMENT AND HOLE LAYOUT
2.1 Attachment to support structure via 3/4” Grade A325 bolts. 3” long bolts are included.
Hardened washers and Anco lock-nuts are included and must be used. Maximum 1-3/8”
structural member thickness.
2.2 Layout and drill holes in support structures 13/16” nominal. 15/16” maximum hole diameter
per AISC.
411/2018
Diagram 2A. Switch support detail.

STEP 3 - MOUNTING
3.1 Shim frame to level the underside of the outer frame to prevent racking/twisting (shims
included).
3.2 Verify frame is square by checking diagonals.
3.3 Torque frame attachment hardware to 260 lb ft, Turn-of-Nut method is acceptable
3.4 If beams are not factory prepped, e
nd prep incoming beams. Additional parts required from
factory (see Appendix A on pages 11-14 for detail).
3.5 Use provided 3/4” A325 bolts, washers and nuts to loosely assemble monorail beam to
switch. Do not tighten yet.
3.6 Shim inlet and outlet beams 0” to 1/32” lower than switch track.
3.7 Set gap between inlets and switch track is 1/8” maximum. Ensure that beam ends do not
rub or bind as they pass each other.
3.8 Once beam is positioned, tighten beam attachment hardware. Torque to 260 lb ft. Turn-of
Nut method is acceptable.
5
11/2018
Diagram 3A. Shim detail.
OUTLETINLET

611/2018
STEP 4 - SAFPOWRBAR® WIRING (OPTION)
4.1 Prior to installing SAFPOWRBAR on monorail beams, flare/prep bar ends. Refer to
diagram 4A for flaring procedure.
4.2 Gap between bar ends should be adjusted to 1/2”. It may be necessary to adjust the
position of the bars to ensure smooth traversing of the shoes. Refer to diagram 4B for
finished bar layout.
4.3 Actuate inner frame to verify bar clearance.
4.4 Switch jumper harness and current
taps are provided from factory.
Refer to Monorail Tarca® system
install manual, page 20, for
mounting current taps to
SAFPOWRBAR.
Diagram 4A. SAFPOWRBAR® Flaring
Procedure.
Diagram 4B. SAFPOWRBAR®

STEP 5 - CONTROL ENCLOSURE (OPTION)
Note: 208/230 VAC 3 phase 60 Hz or 460, 575 VAC 3 phase 60 Hz offered as standard. Control
voltage is 120 VAC, if supplied by Gorbel. Controls are factory set. Do not adjust without consult-
ing factory.
5.1 Refer to wiring diagrams. See Appendix B on pages 15-18.
5.2
Punch/drill enclosure and wire per code. If SAFPOWRBAR® is used, power for the controls
can be tapped off jumper harness.
5.3 Refer to appropriate wiring diagram in appendix for operator interface to control panel. Wall
mounted pendant option is available upon request.
7
11/2018
Diagram 5A. Control Pendant.

811/2018
STEP 6 - MOTORIZED OPERATOR (OPTION)
6.1 Traversing speed is fixed and not adjustable.
6.2 Always verify:
• Incoming power phases are wired correctly
• Motor turns in correct direction
• Limit switches stop motor
It may be necessary to swap two legs of wiring if motor runs in reverse.
6.3 Install breather on reducer (diagram
6A).
6.4 Reducer comes filled with oil from
factory which should not need to be
changed over the life of the unit. In the
event of spillage or other condition
where addition of oil is necessary,
use synthetic gear oil, ISO 320 grade
(Mobil Glygoyle 30 or similar).
6.5 Lubricate ball screw periodically (once per year or
every 10,000 actuations) (diagram 6B).
6.6 Limit switches and end stops are set at the factory.
Some field adjustment may be required for proper
rail alignment. See Step 6.7 on page 9 for
instructions.
WARNING
Running motor in reverse direction may cause permanent damage to clutch/motor/controls, therefore
voiding warranty.
Diagram 6A. Installing breather on top of reducer.
Diagram 6B. Ball screw location.

9
11/2018
STEP 6 - MOTORIZED OPERATOR (OPTION) (CONTINUED)
6.7 Adjusting limit switches:
1. Locate limit switches. See diagram 6C (3-way switch shown).
2. Adjust the middle (plunger) limit switch first for 3-Way only (skip to step 3 for 2-Way
motorized switches).
a. See diagram 6D. Loosen both screws holding the limit
switch tab in place.
b. Shift limit switch tab so that the inner frame rail is
centered on outer frame and lined up with incoming and
outgoing Tarca® rails.
c. Tighten limit switch tab screws.
3. Adjust left lever limit switch. See diagram 6E.
a. Loosen limit switch lever bolt.
b. Adjust limit switch lever until inner frame stops
in correct position (rails are aligned).
c. Tighten limit switch lever bolt.
d. Adjust stop bolt (not shown) so it touches inner
frame cam roller plate.
4. Adjust right lever limit switch.
a. Repeat step 3.
6.8 Overrun clutch is factory set and not adjustable.
Diagram 6C. 3 Way Switch - Limit
Switch Locations
Diagram 6D. Limit switch tab for
plunger limit switch
(on 3 Way Switch only)
Diagram 6E. Lever Limit Switch
Left - Shown
Right - Opposite

STEP 7 - PNEUMATIC OPERATOR (OPTION)
7.1 Route 1/4” NPT air hose (by others) to inlet of FR. 80-120 psi supply required. 1.2 CFM
maximum consumption. Regulator and controls are factory set. Do not adjust without
consulting factory.
STEP 8 - MANUAL OPERATOR (OPTION)
8.1 Cut chains to desired height and install handles using included chain connectors.
Standard drop is 20 ft. If more drop is required, remove handle and splice in new chain
with chain link.
8.2 Outriggers are available as options through Application Engineering. Consult factory for
information.
10 11/2018
No. Part Number Description Qty
9 2-02174-000 Handle 2
10 2-02176-100 Chain Link 2
11 94298 Shackle 4
12 1-05772-000 Limit Ring 2
13 2-02176-000 Chain - Total Length 50 ft
13A - Cut to 16” Long
13B - Cut to 12” Long
13C - Leftover 47’-8”
Diagram 8A. Pull chain diagram.

11
11/2018
APPENDIX A - BEAM END PREP DIAGRAMS

APPENDIX A - BEAM END PREP DIAGRAMS (CONTINUED)
12 11/2018

13
11/2018
APPENDIX A - BEAM END PREP DIAGRAMS (CONTINUED)

APPENDIX A - BEAM END PREP DIAGRAMS (CONTINUED)
14 11/2018

15
11/2018
APPENDIX B - WIRING DIAGRAMS
2-Way Motorized Schematic

APPENDIX B - WIRING DIAGRAMS (CONTINUED)
16 11/2018
3-Way Motorized Schematic
Table of contents
Popular Switch manuals by other brands
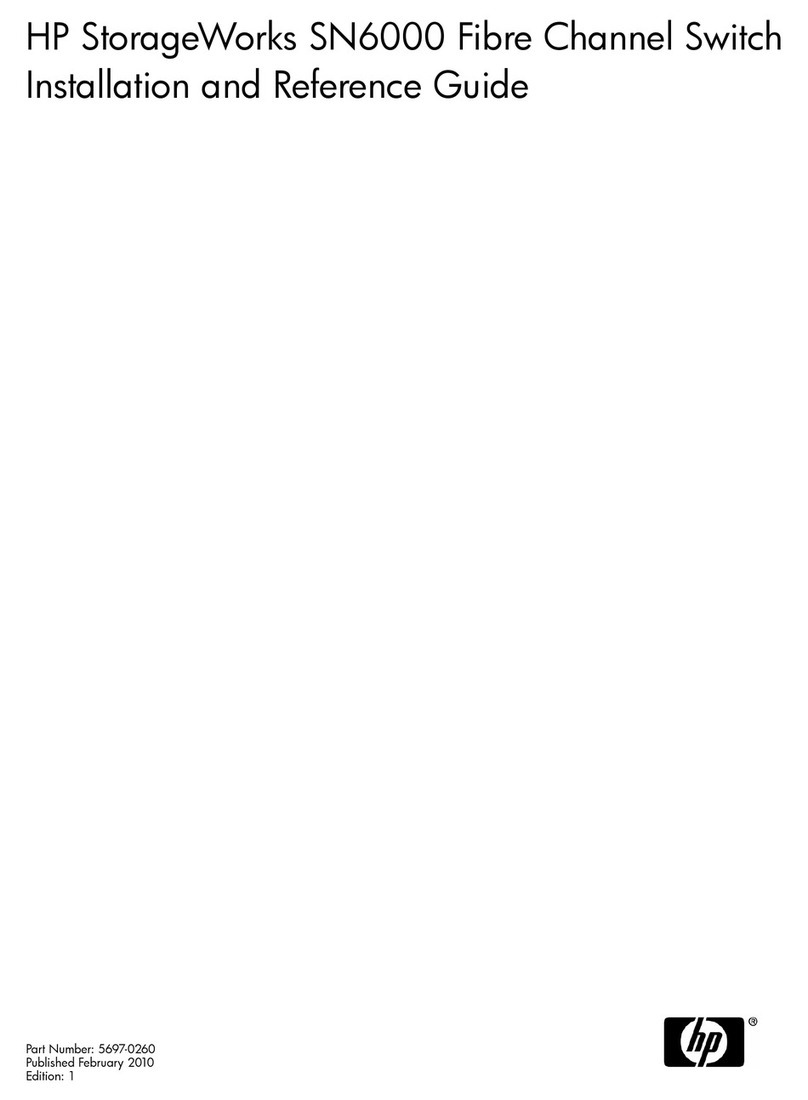
HP
HP StorageWorks SN6000 Installation and reference guide
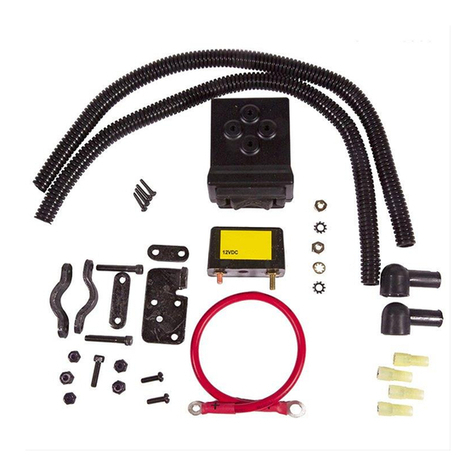
Superwinch
Superwinch 2233B installation instructions

Panasonic
Panasonic Swtich-M48eG Series installation guide
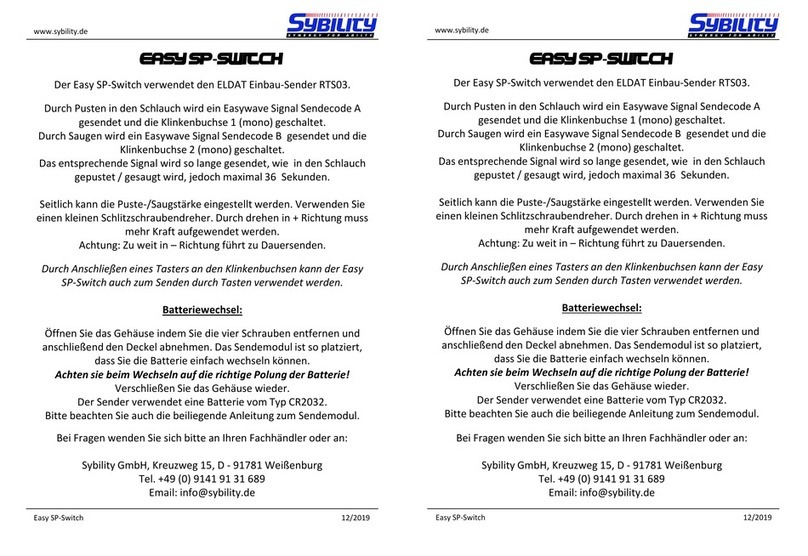
Sybility
Sybility Easy SP-Switch quick start guide
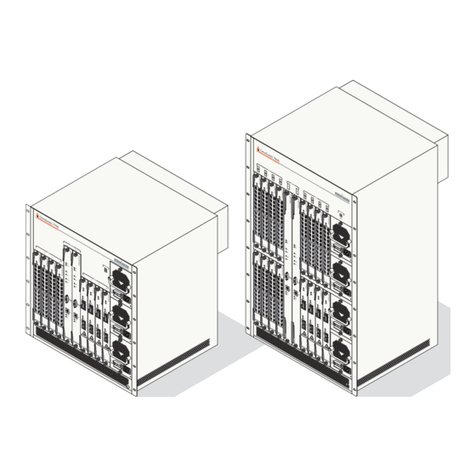
Alcatel
Alcatel OmniSwitch 7700 Hardware user's guide

LevelOne
LevelOne 55051007 user manual
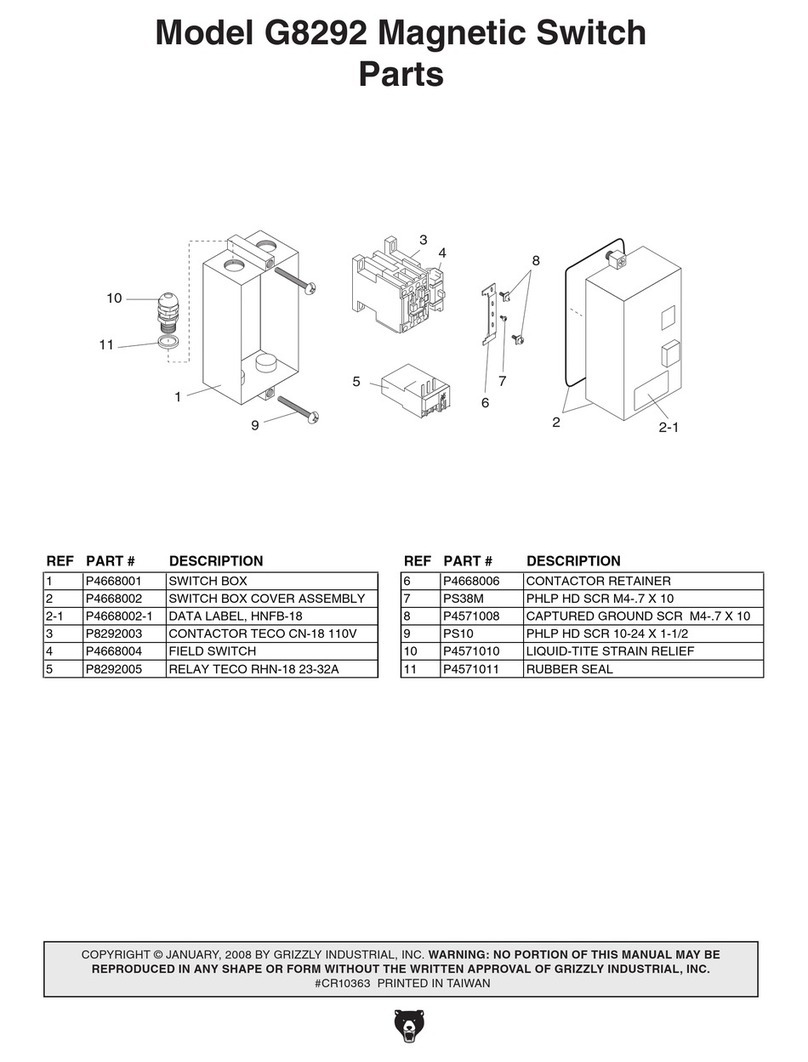
Grizzly
Grizzly G8292 parts list
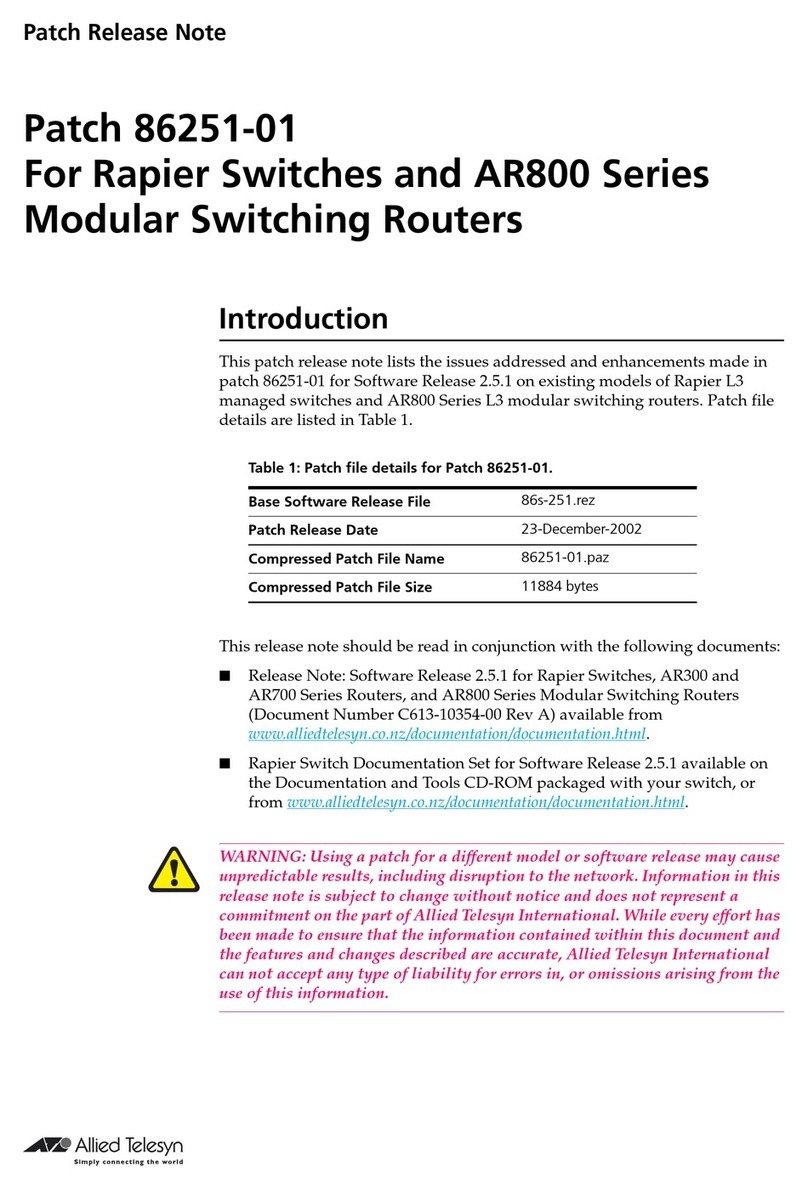
Allied Telesis
Allied Telesis Rapier AR 800 Series release note
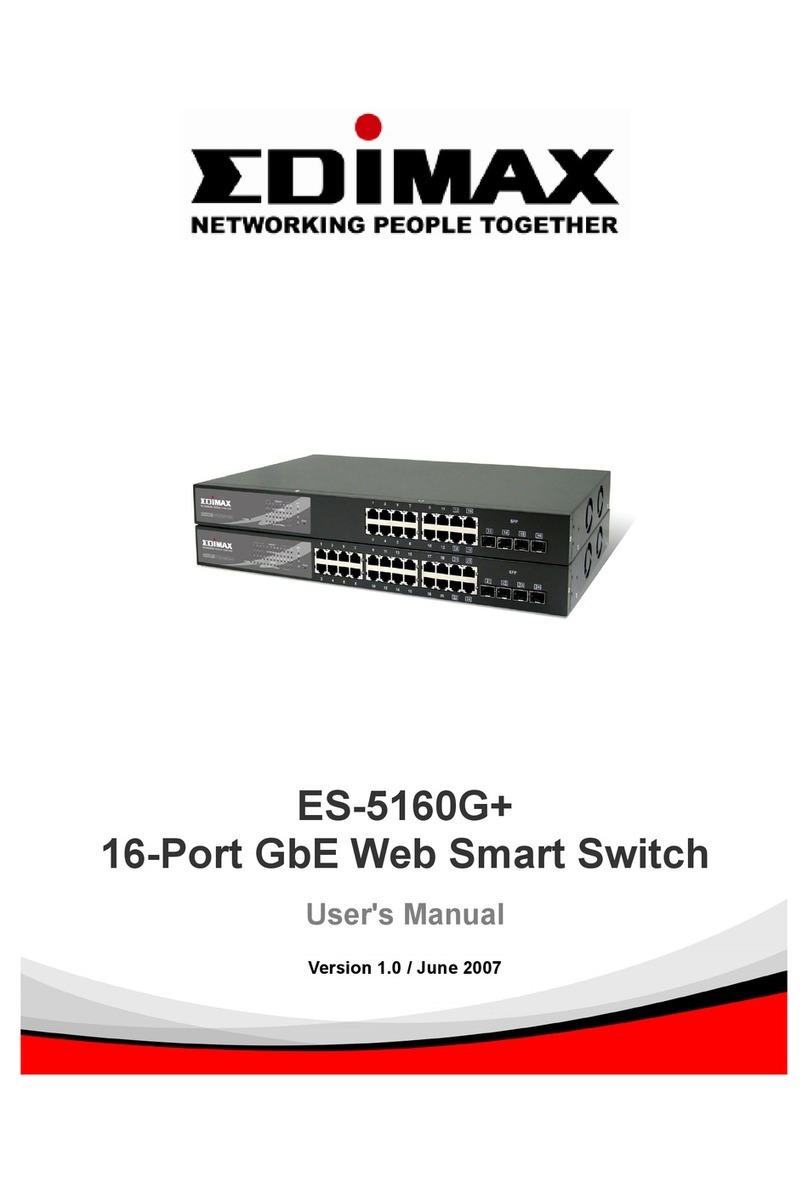
Edimax
Edimax ES-5160G+ user manual
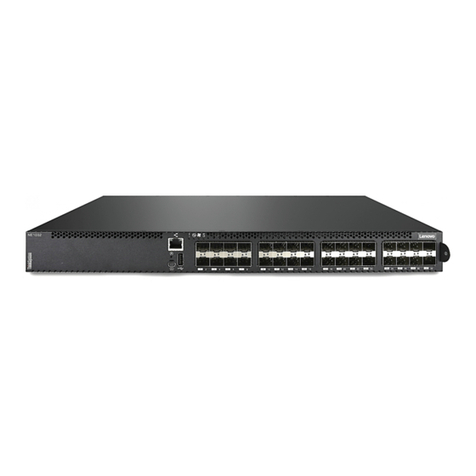
Lenovo
Lenovo ThinkSystem NE1032 quick start guide
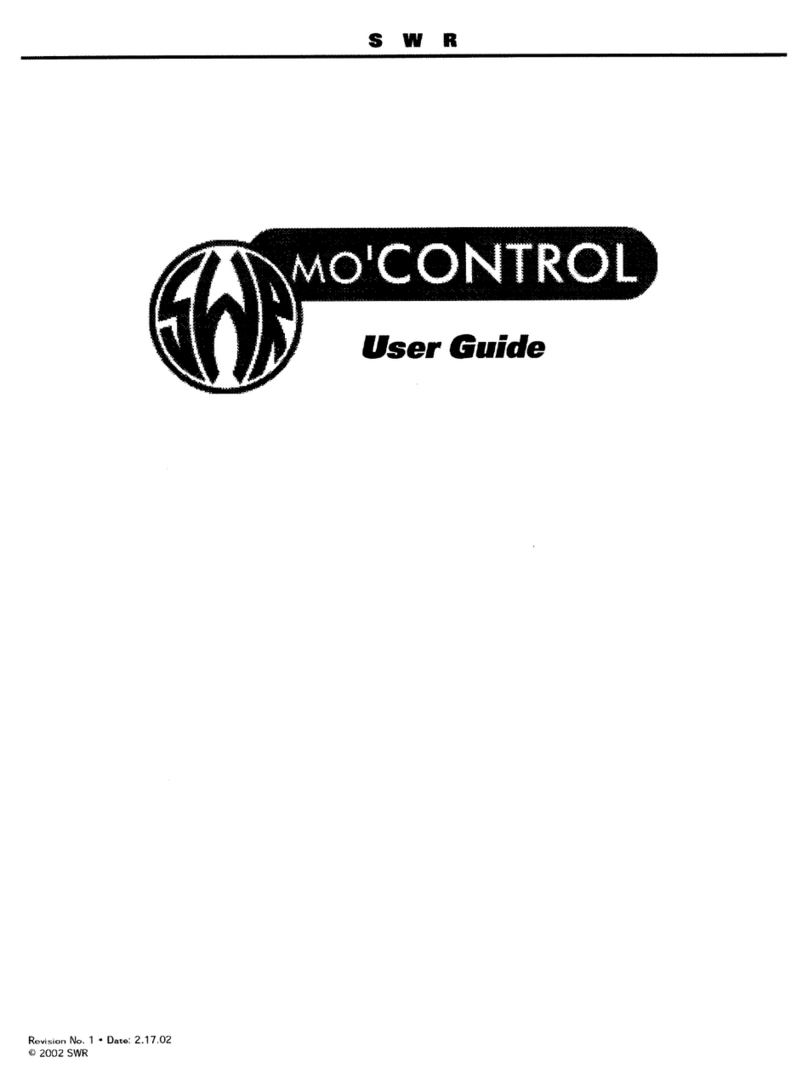
SWR
SWR mo'CONTROL user guide
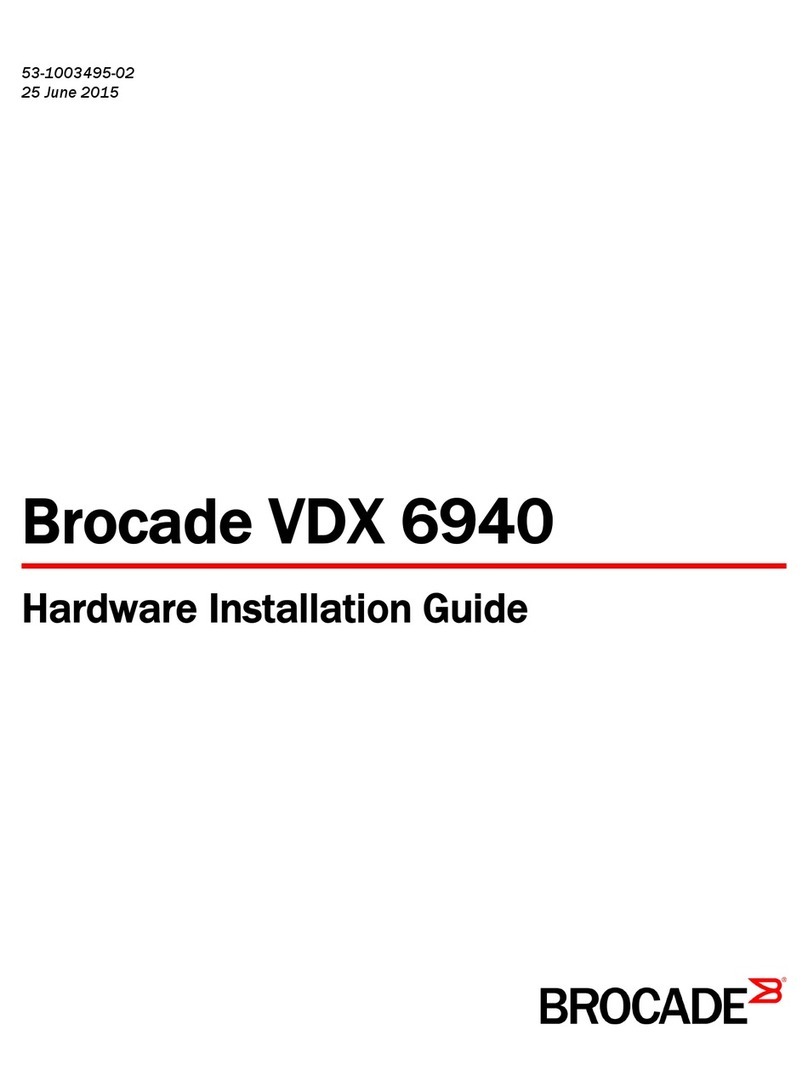
Brocade Communications Systems
Brocade Communications Systems VDX 6940 Series Hardware installation guide