Grundig GHP-MM08 User manual

01M-8508043600-2422-01
01M-8508053600-2422-01
01M-8508063600-2422-01
01M-8503073600-2422-01
01M-8503083600-2422-01
GHP-MM08
GHP-MM10
GHP-MM12
GHP-MM14
GHP-MM16
EN
Service Manual
Heat Pump Monobloc Inverter

Please read this user manual first!
Dear Valued Customer,
Thank you for preferring this Grundig appliance. We hope that you get the best results
from your appliance which has been manufactured with high quality and state-of-the-art
technology. For this reason, please read this entire user manual and all other accompany-
ing documents carefully before using the appliance and keep it as a reference for future
use. If you handover the appliance to someone else, give the user manual as well. Follow
the instructions by paying attention to all the information and warnings in the user manual.
Remember that this user manual may also apply to other models. Differences between
models are explicitly described in the manual.
Meanings of the Symbols
Following symbols are used in various sections of this user manual:
CImportant information or useful hints
about usage.
AWarning for hazardous situations with
regard to life and property.
Warning to actions that must never
perform.
BWarning for electric shock.
Warning for hot surfaces.
Do not cover it.
This symbol shows that the operation
manual should be read carefully.
This symbol shows that a service per-
sonnel should be handling this equip-
ment with reference to the installation
manual.
(For R32/R290 gas type)
This symbol shows
that this appliance
used a flammable
refrigerant. If the ref-
rigerant is leaked and
exposed to an external
ignition source, there is
a risk of fire.

3 / EN
Heat Pump Monobloc Inverter / User Manual
1 Air Source Heat Pump 202202
TableofContents
Part 1 General Features .............................................................................................................................................. 4
1.1 Unit Capacities and Appearance ...................................................................................................................... 4
Part 2 Component Layout and Refrigerant Circuit ...................................................................................................... 5
2.1 Layout of Functional Components ................................................................................................................... 5
2.2 Piping Diagram ................................................................................................................................................. 8
2.3 Refrigerant Flow Diagram .............................................................................................................................. 10
Part 3 Control ............................................................................................................................................................ 11
3.1 Stop Operation ............................................................................................................................................... 11
3.2 Standby Control ............................................................................................................................................. 11
3.3 Startup Control .............................................................................................................................................. 11
3.4 Normal Operation Control ............................................................................................................................. 13
3.5 Protection Control ......................................................................................................................................... 13
3.6 Special Control ............................................................................................................................................... 14
3.7 Role of Temperature Sensors in Control Functions ....................................................................................... 16
3.8 EEPROM Parameter Setting ......................................................................................................................... 20
3.9 Electric Wiring Diagram ................................................................................................................................. 26
Part 4 Troubleshooting ............................................................................................................................................. 30
4.1 Unit Electric Control Box Layout .................................................................................................................... 30
4.2 Unit PCBs ........................................................................................................................................................ 33
4.3 Error Code Table ............................................................................................................................................ 39
4.4 Troubleshooting ............................................................................................................................................. 41
4.5 Appendixes to Part 4 ...................................................................................................................................... 80

4 / EN Heat Pump Monobloc Inverter / User Manual
202202 Heat Pump Space Heater 2
Part 1 General Features
1.1 Unit Capacities and Appearance
1.1.1 Unit Capacities
Table 1-1.1: Capacity range
Factory Model KS-80W/EN8BP KS-100W/EN8BP KS-120W/EN8BP KS-140W/EN8BP KS-160W/EN8BP
Model No. GHP-MM 08 GHP-MM 10 GHP-MM 12 GHP-MM 14 GHP-MM 16
Notes:
1. The full model names can be obtained by substituting the asterisk in the model name format
given in the left-hand column of the table above with the shortened model names given in the
table. For example, the model name for the 14kW model is GHP-MM14.
2. The presence or omission of the letter E and S in the model names indicates:
E: with internal backup heater; omitted: without internal backup heater.
3. Power supply:
220-240V, 50Hz, 1-phase.
1.1.2 Appearance
Table 1-1.2: Unit appearance
8kW
10/12kW 14/16kW

5 / EN
Heat Pump Monobloc Inverter / User Manual
3 Heat Pump Space Heater 202202
Part 2 Component Layout and Refrigerant
Circuit
2.1 Layout of Functional Components
GHP-MM08
Figure 2-1.1: top view
Figure 2-1.2: front view

6 / EN Heat Pump Monobloc Inverter / User Manual
202202 Heat Pump Space Heater 4
GHP-MM10
Figure 2-1.3: top view
Figure 2-1.4: front view
GHP-MM12
Figure 2-1.5: top view

7 / EN
Heat Pump Monobloc Inverter / User Manual
5 Heat Pump Space Heater 202202
Figure 2-1.6: front view
GHP-MM14/ GHP-MM16
Figure 2-1.7: top view

8 / EN Heat Pump Monobloc Inverter / User Manual
202202 Heat Pump Space Heater 6
Figure 2-1.8: front view
2.2 Piping Diagram
Figure 2-2.1: Piping diagram

9 / EN
Heat Pump Monobloc Inverter / User Manual
7 Heat Pump Space Heater 202202
Key components:
1. Compressor
Compress low temperature and low pressure refrigerant gas into high temperature and high
pressure refrigerant gas.
2. Electronic expansion valve (EEV)
Control refrigerant flow and reduce refrigerant pressure.
3. 4-way valve
Control refrigerant flow direction. Open in cooling mode and closed in heating mode. When
open, the air side heat exchanger functions as a condenser and water side heat exchanger
functions as an evaporator; when closed, the air side heat exchanger functions as an
evaporator and water side heat exchanger functions as a condenser.
4. High and middle pressure switch
Regulate refrigerant system pressure. When refrigerant system pressure rises above the
upper limit, the high or middle pressure switches will open and then turn off heat pump.
5. Low pressure sensor
Regulate refrigerant system pressure. When refrigerant system pressure falls below the
lower limit, low pressure sensor detects the limit value and then turns off heat pump.
6. Air purge valve
Automatically remove air from the water circuit.
7. Safety valve
Preventing excessive water pressure by opening at 43.5 psi (3 bar) and discharging water
from the water circuit.
8. Expansion vessel
Balance water system pressure. (Expansion vessel volume: 5L)
9. Water flow switch
Detect water flow rate to protect compressor and water pump in the event of insufficient
water flow.
10. Backup heater
Provide additional heating capacity when the heating capacity of the heat pump is
insufficient due to very low outdoor temperature. Also protects the external water piping
from freezing.
11. Internal water pump
Circulate water in the water circuit.

10 / EN Heat Pump Monobloc Inverter / User Manual
202202 Heat Pump Space Heater 8
2.3 Refrigerant Flow Diagram
Heating and domestic hot water operation (8,16KW for example)
Figure 2-3.1: Refrigerant flow during heating or domestic hot water operation
Cooling and defrosting operation (8,16KW for example)
Figure 2-3.2: Refrigerant flow during cooling and defrosting operations

11 / EN
Heat Pump Monobloc Inverter / User Manual
9 Heat Pump Space Heater 202202
Part 3 Control
3.1 Stop Operation
The stop operation occurs for one of the following reasons:
3.1.1 Normal shutdown: The heat pump will stop running when the set temperature has been
reached.
3.1.2 Abnormal shutdown: in order to protect the compressors, if an abnormal state occurs the
system makes a “turn off” operation and an error code are displayed on the user interface.
3.2 Standby Control
3.2.1 Water Pump Control
When the outdoor unit is on standby, the internal and external circulator pumps run
continuously.
3.2.2 Crankcase Heater Control
The crankcase heater is used to prevent refrigerant from mixing with compressor oil when the
compressors are stopped. The crankcase heater is controlled according to outdoor ambient
temperature and the compressor`s on/off state. When the outdoor ambient temperature is at or
above 7°C or the compressor is running, the crankcase heater is off; when the outdoor ambient
temperature is below 5°C and the unit has just been powered on (either manually or when the
power supply has been restored from a breakdown), the crankcase heater turns on and run by
half an hour on half an hour off cycle. When the compressor has been stopped for more than 3
hours and the outdoor ambient temperature is below 5°C, the crankcase heater turns on and run
for half an hour on half an hour off cycle.
3.3 Startup Control
3.3.1 Compressor Startup Delay Control
In initial startup control or restart control (except in oil return operation and defrosting operation)
or switching from on mode to another mode, compressor startup is delayed such that a 3 minute
delay time has elapsed since the compressor last stopped, in order to prevent frequent
compressor on/off and to equalize the pressure within the refrigerant system.
3.3.2 Compressor Startup Program
In initial startup control and restart control, compressor startup is controlled according to
outdoor ambient temperature. Compressor startup follows the startup steps below until the
target rotation speed is reached.
Figure 3-3.1: Compressor startup procedure

12 / EN Heat Pump Monobloc Inverter / User Manual
202202 Heat Pump Space Heater 10
3.3.3 Startup Control for Heating and Domestic Hot Water Operation
Table 3-3.1: Component control during startup in heating and domestic hot water modes
Component Control function and state
Inverter compressor Compressor startup program by
figure3-3.1
DC fan motor
Start the fan 10 seconds before the
compressor starts, and then run half of the
maximum speed, and then run at
maximum speed 60s after the compressor
startup
Electronic expansion valve
Position (steps) from 0 (fully closed) to 480
(fully open), controlled according to
outdoor ambient temperature and
in-water temperature
4-way valve ON
3.3.4 Startup Control for Cooling Operation
Table 3-3.2: Component control during startup in cooling mode
Component Control function and state
Inverter compressor Compressor startup program by
figure3-3.1
DC fan motor
Start the fan 10 seconds before the
compressor starts, and then run half of the
maximum speed, and then run at
maximum speed 60s after the compressor
startup
Electronic expansion valve
Position (steps) from 0 (fully closed) to 480
(fully open), controlled according to
outdoor ambient temperature and
in-water temperature
4-way valve OFF

13 / EN
Heat Pump Monobloc Inverter / User Manual
11 Heat Pump Space Heater 202202
3.4 Normal Operation Control
3.4.1 Component Control during Normal Operation
Table 3-4.1: Component control during heating and domestic hot water operations
Component Control function and state
Inverter compressor
Controlled according to load requirement from hydraulic
module
DC fan motor Controlled according to outdoor ambient temperature and
outdoor heat exchanger pipe temperature
Electronic expansion valve
Position (steps) from 0 (fully closed) to 480 (fully open),
controlled according to in-water temperature, out-water
temperature and discharge temperature
4-way valve ON
Table 3-4.2: Component control during cooling operation
Component Control function and state
Inverter compressor
Controlled according to load requirement from hydraulic
module
DC fan motor Controlled according to outdoor ambient temperature and
outdoor heat exchanger pipe temperature
Electronic expansion valve
Position (steps) from 0 (fully closed) to 480 (fully open),
controlled according to in-water temperature, out-water
temperature and discharge temperature
Four-way valve OFF
3.4.2 Compressor Output Control
The compressor rotation speed is controlled according to the load requirement. The compressor
follows a fixed starting procedure as shown in figure 3-3.1. After finishing the startup, the
compressor runs at the target rotation speed.
During normal operation the compressor speed is controlled according to inlet water
temperature, target water temperature set by the user interface, the rate of change in inlet water
temperature.
3.4.3 Compressor Step Control
The running speed of six-pole compressors (used on all models) in rotations per second (rps) is
one third of the frequency (in Hz) of the electrical input to the compressor motor. The frequency
of the electrical input to the compressor motors can be altered at a rate of 1Hz per second.
3.4.4 Four way Valve Control
The four-way valve is used to change the direction of refrigerant flow through the water side heat
exchanger in order to switch between cooling and heating/DHW operations.
During heating and DHW operations, the four-way valve is on; during cooling and defrosting
operations, the four-way valve is off.

14 / EN Heat Pump Monobloc Inverter / User Manual
202202 Heat Pump Space Heater 12
3.4.5 DC Fan Control
Start the fan before the compressor starts, and fan runs at the initial speed. After the compressor
runs a few minutes, the fan runs at a higher set speed.
3.4.6 Electronic Expansion Valve Control
The position of the electronic expansion valve (EEV) is controlled in steps from 0 (fully closed) to
480 (fully open).
! At power-on
EEV first closes fully,and then moves to the standby position. After a few seconds EEV
moves to an initial running position, which is determined according to operating mode, inlet
water temperature and outdoor ambient temperature. A few minutes further, EEV is
controlled according to inlet water temperature, outlet water temperature, discharge
temperature and compressor speed.
! When the unit is on standby
EEV keeps current position and delay a few seconds and opens fully.
! When the unit stops
EEV keeps current position first and delay a few seconds and opens fully.

15 / EN
Heat Pump Monobloc Inverter / User Manual
13 Heat Pump Space Heater 202202
3.5 Protection Control
3.5.1 Low Pressure Protection Control
Figure 3-5.1: Low pressure protection control
When the suction pressure drops below 0.14MPa the system displays P03 protection and the unit
stops running. When the suction pressure rises above 0.3MPa, the compressor enters re-start
control.
3.5.2 High Pressure Protection Control
This control protects the compress from the over-high refrigerant system pressure.
Figure 3-5.2: High pressure protection control
When the discharge pressure rises above 4.5MPa the system displays P02 protection and the unit
stops running. When the discharge pressure drops below 3.5MPa, the compressor enters re-start
control.
3.5.3 Discharge Temperature Protection Control
This control protects the compressor from abnormally high temperature.
Figure 3-5.3: High discharge temperature protection control

16 / EN Heat Pump Monobloc Inverter / User Manual
202202 Heat Pump Space Heater 14
When the discharge temperature rises above 115°C the system displays P05 protection and the
unit stops running. When the discharge temperature drops below 95°C, the compressor enters a
re-start control.
3.5.4 Compressor Current Protection Control
This control protects the compressor from abnormally high currents. When the compressor
current rises above maximum current the system displays E23 protection and the unit stops
running. When the compressor current drops below maximum current, the compressor enters
re-start control.
Table 3-5.1: Compressor current protection control
model
8-10kw
12kw 1ph
14-16kw 1ph
Maximum
current (A)
14 18 25
3.5.5 DC Fan Motor Protection Control
Check the feedback signal one minute after the fan starts. If the motor speed is lower than the
default minimum speed or there is no feedback for one minute, the motor fault P11 will be
displayed. If it occurred 10 times within 2hours, the unit will shut down and be locked.
3.5.6 Water Side Heat Exchanger Anti-freeze Control
This control protects the water side heat exchanger from ice formation. The water side heat
exchanger electric heater is controlled according to outdoor ambient temperature, inlet water
temperature and outlet water temperature.
! When all the conditions below are met, the unit will turn on the water side heat exchanger
electric heater:
" the current operation mode of the unit is shutdown or standby;
" outdoor ambient temperature is below 4°C;
" inlet water temperature or outlet water temperature(the minor one) is below 4°C;
! When any one of the conditions below is met, the unit will turn off the water side heat
exchanger electric heater:
" the current operation of the unit is neither shutdown nor standby;
" outdoor ambient temperature is above 6°C;
" inlet water temperature or outlet water temperature(the minor one) is above 6°C;
3.5.7 Module Temperature Protection Control
This control protects the module from abnormally high temperatures. When the module
temperature rises at or above the up limit value 96°C, the interface displays E29 protection code
and the unit stops running.
3.6 Special Control
3.6.1 Oil Return Operation
In order to prevent the compressor from running out of oil, the oil return operation is conducted
to recover oil that has flowed out of the compressor and into the refrigerant piping.
When the compressor cumulative operating time with running rotation speed less than 50Hz has
been reached 3 hours, the unit will start an oil-return operation.
The oil return operation ceases when any one of the following three conditions occurs:
! Oil return operation duration has been reached 4 minutes.

17 / EN
Heat Pump Monobloc Inverter / User Manual
15 Heat Pump Space Heater 202202
! The unit will turn off because of the protection.
! “TURN OFF” command is received.
Table 3-6.1 Component control during oil-return operation
Component Control functions and states
Compressor
Runs at oil return operation rotation speed
Electronic expansion valve
Fully open
DC fan motor Controlled according to outdoor heat
exchanger pipe temperature
4-way valve OFF
3.6.2 Defrosting Operation
In order to recover heating capacity, the defrosting operation is conducted when the air side heat
exchanger of the unit is performing as a condenser. The defrosting operation is controlled
according to outdoor ambient temperature, air side heat exchanger refrigerant outlet
temperature and the compressor running time.
Table 3-6.2: Component control during defrosting operation
Component
Control functions and states
Compressor Runs at defrosting operation rotation speed
Electronic expansion valve
Fully open
DC fan motor OFF
4-way valve OFF

18 / EN Heat Pump Monobloc Inverter / User Manual
202202 Heat Pump Space Heater 16
3.7 Role of Temperature Sensors in Control Functions
Figure 3-7.1: Location of the temperature sensors of all models 8-16kw

19 / EN
Heat Pump Monobloc Inverter / User Manual
17 Heat Pump Space Heater 202202
Table 3-7.1: All the temperature sensors
Item Name Label Mode Control functions
1 Suction temp. sensor TH Cooling Electronic expansion valve control
Heating Electronic expansion valve control
2 Discharge temp. sensor TP
Cooling Electronic expansion valve control
Discharge temp. protection control
Heating Electronic expansion valve control
Discharge temp. protection control
3 Coil temp. sensor T3
Cooling
Electronic expansion valve control
DC fan control
Compressor output control
Heating
Electronic expansion valve control
DC fan control
Defrosting operation control
4 Outdoor ambient temp. sensor T4
Cooling
Compressor startup control
Compressor output control
Electronic expansion valve control
DC fan control
Crankcase heater control
Heating
Compressor startup control
Compressor output control
Electronic expansion valve control
DC fan control
Defrosting operation control
Crankcase heater control
5 Liquid refrigerant temp. sensor T5 Cooling Anti-freezing protection control
Heating /
6 Inlet water temp. sensor TA
Cooling
Anti-freezing protection control
Compressor on/off and output control
Oil-returning control
Electronic expansion valve control
Heating
Compressor on/off and output control
Oil-returning control
Defrosting operation control
Electronic expansion valve control
7 Outlet water temp. sensor TB
Cooling Anti-freezing protection control
Electronic expansion valve control
Heating
Compressor output control
Defrosting operation control
Electronic expansion valve control
8 Domestic water tank temp. sensor TW DHW Compressor output/Backup electric heater
control
202202 Heat Pump Space Heater 16
3.7 Role of Temperature Sensors in Control Functions
Figure 3-7.1: Location of the temperature sensors of all models 8-16kw

20 / EN Heat Pump Monobloc Inverter / User Manual
202202 Heat Pump Space Heater 18
3.8 EEPROM Parameter Setting
Press “M” and “Up” two keys at the same time, and then enter the password “1212” to adjust
EEPROM parameter value. Refer to the table below for the detailed setting.
Item Name Code Default Unit Range Accuracy
1 Air conditioning water
temperature return difference Ta 2 ℃ 1~5 1
2 Hot water temperature
difference Tb 5 ℃ 2~15 1
3 Cooling target exhaust
temperature correction TargetTPc 0 ℃ -10~15 1
4 Heating superheat SHh -1 ℃ -5~10 1
5 Compressor frequency in
refrigeration test mode LCF_C 68 Hz 20~120 1
6 Compressor frequency in
heating test mode LCF_H 68 Hz 20~120 1
7 Compressor frequency in hot
water test mode LCF_W 68 Hz 20~120 1
8 Cooling test mode EEV opening
EEV_C 250/5 P (0~480)/5 1
9 Heating test mode EEV-1
opening EEV_H 150/5 P (0~480)/5 1
10 Hot water test mode EEV-1
opening EEV_W 150/5 P (0~480)/5 1
11 Defrost entry temperature DST -5 ℃ -15~0 1
12 Defrost enters temperature
difference Dt 12 ℃ 0~15 1
13 Judgment time of first defrost T1 40 min 20~90 1
14
Defrosting process EEV opening
Opl
480/5
P
(0
~
480)/5
1
15 Defrost compressor frequency FD 12 Hz 30~120 1
16 Maximum operating frequency
Fmax 85 Hz 30~120 1
17 Power-off memory PR 1 0/1 0-disable
1-enable /
18 Silent mode frequency limit Fs 55 Hz 30~120 1
19 Sterilization set temperature Tx 65 ℃ 55~75 1
20 Disinfection duration time Td 30 Min 20~120 1
21 Run mode priority Mp 0 0/1/2
0-DHW
1-Space AC
2-Preempt
/
This manual suits for next models
4
Table of contents
Popular Inverter manuals by other brands

Mitsubishi Electric
Mitsubishi Electric FR-E800 instruction manual

Huawei
Huawei SUN2000-3KTL-M0 quick guide
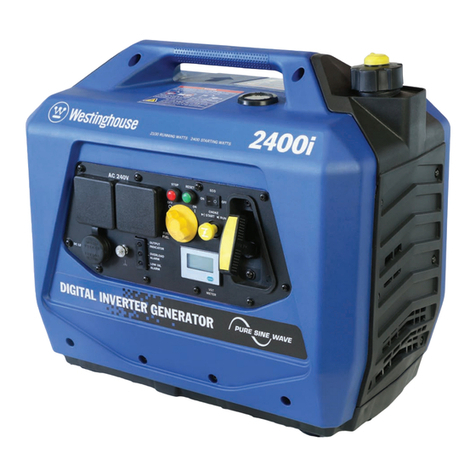
Westinghouse
Westinghouse 2400i instruction manual
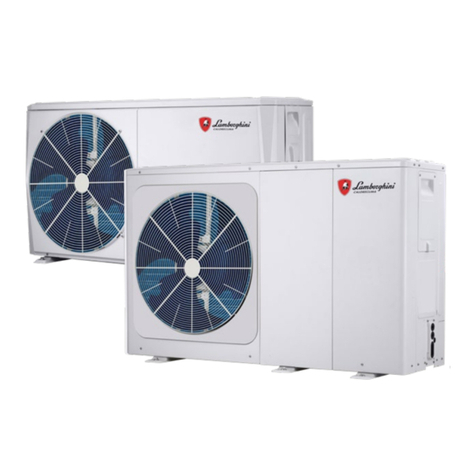
Lamborghini Caloreclima
Lamborghini Caloreclima IDOLA M 3.2 manual

Xantrex
Xantrex XW4024-230-50 Operation guide
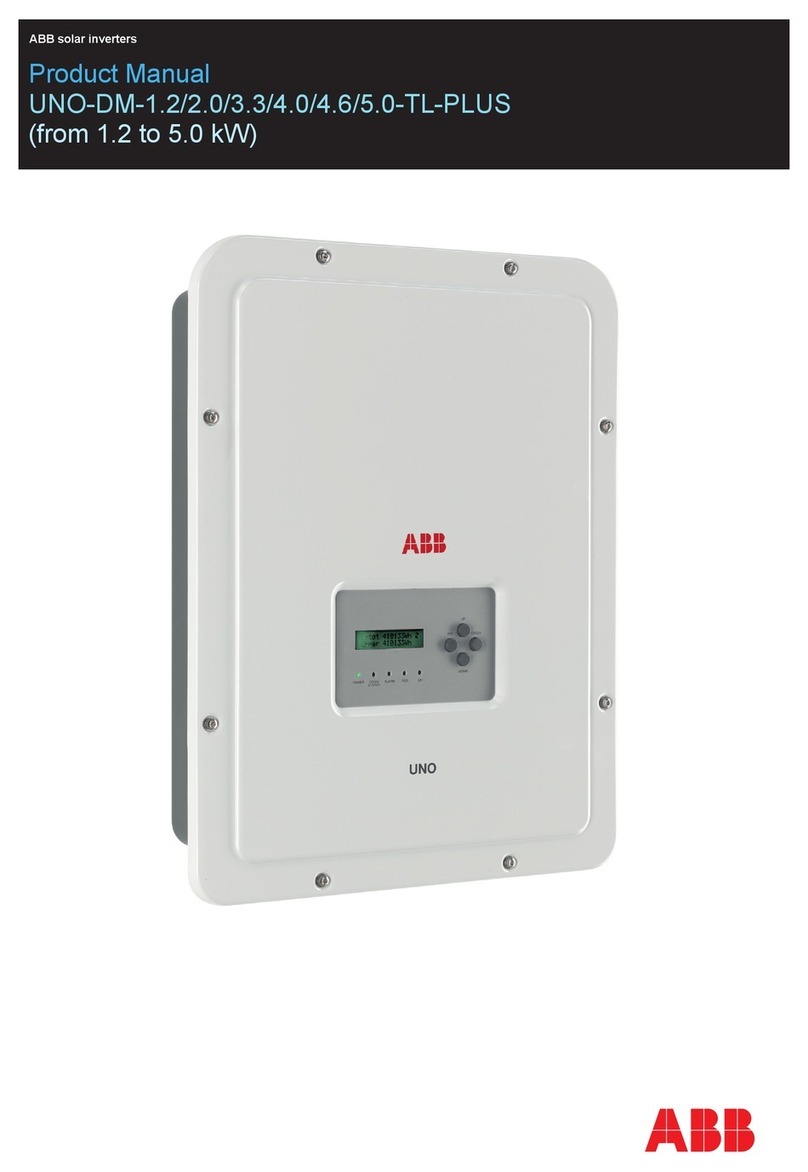
ABB
ABB UNO-DM-3.3-TL-PLUS product manual