H3C SR8800-X User manual

H3C High-End Routers Quick Start
Maintenance Guide
Document version: 6W100-20230524
Copyright © 2023 New H3C Technologies Co., Ltd. All rights reserved.
No part of this manual may be reproduced or transmitted in any form or by any means without prior written consent of New
H3C Technologies Co., Ltd.
Except for the trademarks of NewH3C Technologies Co., Ltd., any trademarks that may bementioned in this document are
the property of their respective owners.
The information in this document is subject to change without notice.

i
Contents
About this document······················································································1
Preparing for maintenance·············································································2
Maintaining the device···················································································3
Checking the LED status····································································································································3
SR8800-X/CR16000-F LEDs·····················································································································4
SR8800-X-S/SR8800-F LEDs····················································································································5
RX8800 LEDs ············································································································································6
CR16000-M/SR6600-G LEDs····················································································································7
Checking critical or minor alarms·······················································································································7
Checking the health status of the device ···········································································································8
Checking the status of cards and subcards·····································································································11
Collecting and reporting failure information··················································13
Collecting basic failure information ··················································································································13
Collecting log information·································································································································13
Collecting diagnostic information ·····················································································································14
Troubleshooting login failure········································································16
Checking for power supply system failure ·······································································································16
Checking for inconsistent serial communication parameter settings between the configuration terminal and the
console port······················································································································································16
Checking for MPU failure·································································································································17
Resetting the device·········································································································································17
Contacting H3C Support··································································································································17
Safety and configuration cautions and guidelines········································18
Hardware safety guidelines······························································································································18
CLI-based configuration cautions and guidelines ····························································································18

1
About this document
This document helps you maintain the high-end routers.
This document is not restricted to specific software or hardware versions. Procedures and
information in the examples might be slightly different depending on the software or hardware
version of the device.
Examples in this document might use devices that differ from your device in hardware model,
configuration, or software version. It is normal that the port numbers, sample output, screenshots,
and other information in the examples differ from what you have on your device.

2
Preparing for maintenance
1. Obtain the network topology graph and data plan (including interfaces, VLANs, and IP
addresses) and paste them at a place where it can be seen easily.
2. Prepare the tools and cables that might be required for maintenance. See Table 1.
Table 1 Tools and cables for maintenance
Item
Description
Cables
•One standard RS-232 serial port cable—Used to log in to the device
from the console port.
•Serial-to-USB adapter—Connects the USB port on the maintenance
terminal to the serial port on the device. Before the connection, install
the serial port driver on the maintenance terminal and verify that it can
operate correctly.
•Two straight-through network cables—Debug management network
ports or other services.
•Extension cable connectors—Used to extend cables when their
length is not enough.
•Optical fibers and transceiver modules such as
XFP/QSPF+/QSFP28/SFP28/CFP/CFP2/SFP+/SFP—Connect to the
peer device.
Maintenance terminal Typically, a maintenance terminal is a laptop used to install the serial
communication software for device login. To avoid license expiration, check
the serial communication terminal before you use it.
Auxiliary instruments,
meters, and tools
•Optical power meter—Test optical power and receiving sensitivity for
fiber ports.
•Hygrothermograph—Test the temperature and humidity of the
environment and fan outlet.
•Tweezers—Remove an optical fiber or transceiver module.
•Cleaning box for optical fiber end faces.
•Connector cleaning rod.
•Cable tie (cable clamp).
•Screwdrivers—Phillips screwdrivers and flat-head screwdrivers.
•Diagonal pliers.
3. Obtain contact information of H3C Support.
4. Access the H3C official website and apply for a user account as required. You can use the user
account to browse or download all product documents.

3
Maintaining the device
To check alarms, health status, and card status, and record failure information, log in to the device
through the console port, Telnet, or SSH. For how to log in to the device, see Fundamentals
Configuration Guide for the device. If you fail to log in to the device, see "Troubleshooting login
failure."
Figure 1 Maintenance flow
Checking the LED status
The device provides various LEDs to indicate the operating status of different objects. If a LED
indicates an abnormal state, record the failure information immediately and see the installation guide
for the router for how to troubleshoot and resolve the issue. If the issue persists, contact H3C
Support.
See the tables in this section to understand normal LED activity. The number and status of LEDs of
the same type for one type of card depend on the card model. For example, an MPU might provide
two fan tray status LEDs (OK and FAIL) or one fan tray status LED (OK/FAIL), depending on the
MPU model.
For more information about the descriptions of the LEDs, see the installation guide for the router.
Check LED status
Start
Check critical or minor alarms Check card and subcard
status
An exception has
occurred?
Resolvable?
Collect information
and contact H3C
Support
Yes
No
Check device health
status
End
Yes
No

4
SR8800-X/CR16000-F LEDs
Table 2 Descriptions for SR8800-X/CR16000-F LEDs indicating a normal state
Card
LED
LED status
Description
MPU
CF card status LED
(CFS)
On The CF card is present and idle. Do not
hot swap it.
Flashing The CF card is performing read/write
operations. Do not hot swap it.
Fan tray status LED
(FAN)
OK: On
FAIL: OFF All fan trays are operating correctly.
OK/FAIL: Green All fan trays are operating correctly.
Power status LED
(PWR)
OK: On
FAIL: OFF All power supplies are operating
correctly.
OK/FAIL: Green All power supplies are operating
correctly.
Card status LED
(SLOT)
RUN: Flashing (once per two
seconds)
ALM: Off The card is operating correctly.
RUN: Fast flashing (four times
per second)
ALM: On The card is loading software.
RUN: On
ALM: On The card might be starting up.
RUN/ALM: Flashing green The card is operating correctly.
RUN/ALM: Fast flashing green
(four times per second) The service module is loading
software.
RUN/ALM: Steady red The card might be starting up.
MPU status LED
(ACT)
On The MPU is operating in active mode.
Off The MPU might be operating in
standby mode.
Switching
fabric
module
Switching fabric
module LED
RUN: Flashing (once per two
seconds) The switching fabric module is
operating correctly.
RUN: Fast flashing (eight
times per second) The switching fabric module is starting
up.
RUN: Flashing (once per two
seconds)
ALM: Off
The switching fabric module is
operating correctly.
RUN: On
ALM: Off The switching fabric module is starting
up.
Service
module
Service module
LED
RUN: Slow flashing green
(once per second) The card is operating correctly.
RUN: Fast flashing green
(eight times per second)
The card is starting up. If the LED
keeps fast flashing green, the card fails
registration.
OAA module LED ALM: Off The system is operating correctly.

5
Card
LED
LED status
Description
RUN: Flashing green (once
per second) The system has started up and is
operating correctly.
Power
supply Power supply LED Steady green The power supply is operating
correctly.
Fan tray Fan tray LED
OK/FAIL: Steady green The fan tray is operating correctly.
OK: On
FAIL: OFF The fan tray is operating correctly.
SR8800-X-S/SR8800-F LEDs
Table 3 Descriptions for SR8800-X-S/SR8800-F LEDs indicating a normal state
Card
LED
LED status
Description
MPU
CF card status LED
(CFS)
On The CF card is present and idle. Do not
hot swap it.
Flashing The CF card is performing read/write
operations. Do not hot swap it.
Card status LED
(SLOT)
RUN/ALM: Flashing green
(once per two seconds) The card is operating correctly.
RUN/ALM: Fast flashing green
(four times per second) The service module is loading
software.
RUN/ALM: Steady red The card might be starting up.
RUN: Flashing
ALM: Off The card is operating correctly.
RUN: Fast flashing (four times
per second)
ALM: On
The service module is loading
software.
RUN: On
ALM: On The card might be starting up.
MPU status LED
(ACT) Off The MPU might be operating in
standby mode.
On The MPU is operating in active mode.
Fan tray status LED
(FAN)
OK: On
FAIL: OFF All fan trays are operating correctly.
OK/FAIL: Green All fan trays are operating correctly.
Power status LED
(PWR)
OK: On
FAIL: OFF All power supplies are operating
correctly.
OK/FAIL: Green All power supplies are operating
correctly.
Service
module Service module
LED
RUN: Slow flashing green
(once per second) The card is operating correctly.
RUN: Fast flashing green
(eight times per second)
The card is starting up. If the LED
keeps fast flashing green, the card fails
registration.

6
Card
LED
LED status
Description
OAA module LED ALM: Off The system is operating correctly and
no alarm has occurred.
RUN: Flashing green (once
per second) The system has started up and is
operating correctly.
Power
supply Power supply LED Steady green The power supply is operating
correctly.
RX8800 LEDs
Table 4 Descriptions for RX8800 LEDs indicating a normal state
Card
LED
LED status
Description
MPU
CF card status LED
(CFS)
On The CF card is present and idle. Do not
hot swap it.
Flashing The CF card is performing read/write
operations. Do not hot swap it.
Card status LED
(SLOT)
RUN: Flashing (once per two
seconds)
ALM: Off The card is operating correctly.
RUN: Fast flashing (four times
per second)
ALM: On The card is loading software.
RUN: On
ALM: On The card might be starting up.
MPU status LED
(ACT) Off The MPU might be operating in
standby mode.
On The MPU is operating in active mode.
Fan tray status LED
(FAN) OK: On
FAIL: OFF All fan trays are operating correctly.
Power status LED
(PWR) OK: On
FAIL: OFF All power supplies are operating
correctly.
Service
module Service module
LED
RUN: Flashing green (once
per second) The card is operating correctly.
RUN: Fast flashing green
(eight times per second)
The card is starting up. If the LED
keeps fast flashing green, the card fails
registration.
Switching
fabric
module
Switching fabric
module LED
RUN: Flashing (once per two
seconds) The switching fabric module is
operating correctly.
RUN: Fast flashing (eight
times per second) The switching fabric module is starting
up.
Power
supply Power supply LED Steady green The power supply is operating
correctly.
Fan tray Fan tray LED OK/FAIL: Steady green The fan tray is operating correctly.

7
CR16000-M/SR6600-G LEDs
Table 5 Descriptions for CR16000-M/SR6600-G LEDs indicating a normal state
Card
LED
LED status
Description
MPU
MPU running status
LED (RUN)
Flashing (once per two
seconds) The MPU is operating correctly.
Fast flashing (four times per
second) The MPU is starting up.
MPU
active/standby
status LED (ACT)
On The MPU is operating in active mode.
Off The MPU might be operating in
standby mode.
MPU alarm status
LED (ALM) Off The MPU is operating correctly.
Fan tray status LED
(FAN) Steady green All fan trays are operating correctly.
Power status LED
(PWR) Steady green All power supplies are operating
correctly.
Interface
module Interface module
LED (RUN)
Flashing (once per two
seconds) The module is operating correctly.
Fast flashing (four times per
second)
The module is loading software. If the
module stays in this state, it indicates
that software loading has failed.
Switching
fabric
module
Switching fabric
module LED (RUN)
Flashing (once per two
seconds) The switching fabric module is
operating correctly.
Fast flashing (four times per
second) The switching fabric module is starting
up and is loading software.
Fan tray Fan tray LED Steady green The fan tray is operating correctly.
Power
supply Power supply LED Steady green The power supply is operating
correctly.
Checking critical or minor alarms
If a network management system is deployed, you can also identify whether an alarm has occurred
from the network management system. For more information, see the user guide for the network
management system.
To identify whether an ERROR alarm has occurred, use the display alarm active command.
In daily maintenance, you must handle the ERROR alarms immediately. For alarms that cannot be
handled, contact H3C Support.
<Sysname> display alarm active
Seq Level Time Info
191 WARNING 2022-03-14 10:45:04 Temperature is greater than the high-tem
perature warning threshold on slot 3 sensor hotspot 1.
1 ERROR 2022-03-10 17:58:14 Power 2 is absent.

8
Table 6 Command output
Field
Description
Seq Alarm sequence number, assigned when an alarm occurs.
Level Alarm severity. Possible values include ERROR, WARNING, NOTICE,
and INFO, in descending order of severity.
Time Time when the alarm occurred.
Info
Detailed alarm information. The values include:
•Board state changed to Fault on slot xx—The state of the
specified slot changed to Fault. The slot might be starting up or
might be faulty.
•Slot xx fan xx is absent—The specified fan is absent.
•Slot xx fan xx is failed—The specified fan is abnormal.
•Slot xx power xx is absent—The specified power supply is
absent.
•Slot xx power xx failed—The specified power supply is abnormal.
•Temperature is higher than the high-temperature alarming
threshold on slot xx sensor inflow xx—The temperature of the
specified sensor has exceeded the high-temperature warning
threshold.
•Memory minor threshold has been exceeded on slot xx—The
amount of free memory space on the specified slot has exceeded
the minor alarm threshold.
•CPU usage is in minor alarm state on slot xx—The CPU usage
on the specified slot has exceeded the minor alarm threshold.
•Interface-name: RX power is high!—The optical power on the
specified interface is too high.
•Interface-name:The bit error ratio exceeds the upper
threshold—The bit error rate of the specified interface has
exceeded the upper limit.
Checking the health status of the device
Use the following commands to view the health status of the device:
•
display health
•
display memory
•
display fan
•
display power
•
display environment
# Use the display health command to verify that the CPU usage and memory usage of each
card are below 80% and 60%, respectively.
<Sysname> display health
Slot CPU Role CPU Usage(%) Memory Usage(%) Used/Total(MB)
1 0 MPU(Master) 7 23 1902504/8130012
2 0 LPU 9 48 963064/1991292
3 0 LPU 7 47 1913916/4052524
5 0 LPU 4 18 1538196/8158684
6 0 SFU 3 36 361296/984332
7 0 SFU 6 36 361348/984332

9
Table 7 Command output
Field
Description
Role
Card role:
•MPU(Master)—Active MPU. (In standalone mode.)
•MPU(Standby)—Standby MPU. (In standalone mode.)
•MPU(Master)—Global active MPU. (In IRF mode.)
•MPU(Standby)—Global standby MPU. (In IRF mode.)
•LPU—LPU.
CPU Usage(%) Average CPU usage during the past 5 seconds, in percentage.
Memory Usage(%) Memory usage in percentage.
Used/Total(MB) Used memory size and total memory size in MB.
If the CPU usage or memory usage is too high, wait for 5 to 10 minutes and check the CPU usage or
memory usage again. If the issue persists, contact H3C Support.
# Use the display fan command to verify that all present fan trays are in Normal state.
<Sysname> display fan
Fan Frame 0 State: Normal
Table 8 Command output
Field
Description
Fan Frame nState
Fan tray status:
•Absent—The fan tray is not installed.
•Normal—The fan tray is operating correctly.
•
Fault
—The fan tray is faulty.
If a fan tray is faulty, troubleshoot and resolve the issues as follows:
1. Verify that the fan tray is installed securely. If the fan tray is not installed securely, reinstall the
fan tray.
2. Verify that the fan does not have object intrusions. If the fan got stuck, remove the objects.
3. Verify that the fan tray is clean. If the fan tray has too much dust, clean the fan tray.
4. If the fan tray still operates incorrectly, replace the fan tray.
5. If the issue persists, record the failure information immediately and contact H3C Support.
# Use the display power command to verify that all present power supplies are in Normal state.
<Sysname> display power
Power 0 State: Normal
Power 1 State: Absent
Power 2 State: Absent
Power 3 State: Absent
Table 9 Command output
Field
Description
Power nState
Power supply status:
•Normal—The power supply is operating correctly.
•Absent—The slot is not installed with a power supply.
•Error—The power supply is faulty.
If a power supply is faulty, perform the following tasks:

10
1. Verify that the power supply is powered on.
2. Verify that the power cord is connected securely.
3. If the power supply still operates incorrectly, replace the power supply.
4. If the issue persists, record the failure information immediately and contact H3C Support.
# Use the display environment command to verify that the temperatures of temperature
sensors on each card are lower than the lower temperature limit.
<Sysname> display environment
System temperature information (degree centigrade):
----------------------------------------------------------------------
Slot Sensor Temperature Lower Warning Alarm Shutdown
0 inflow 1 25 0 48 60 NA
0 hotspot 1 31 0 80 95 NA
2 inflow 1 29 0 80 97 NA
2 outflow 1 26 0 80 97 NA
2 hotspot 1 31 0 80 97 NA
2 hotspot 2 42 0 80 97 NA
3 inflow 1 31 0 80 97 NA
3 outflow 1 32 0 80 97 NA
3 hotspot 1 47 0 80 97 NA
3 hotspot 2 38 0 80 97 NA
4 hotspot 1 30 0 75 90 NA
6 hotspot 1 41 0 88 100 110
Table 10 Command output
Field
Description
System Temperature
information (degree
centigrade) Temperature information (°C).
sensor
Temperature sensor:
•hotspot—Hotspot sensor.
•inflow—Air inlet sensor.
•outflow—Air outlet sensor.
Slot Sensor position. For a sensor on the chassis or fan tray, this field displays
Vent.
Temperature Current temperature.
Lower Lower temperature limit.
Warning Warning temperature threshold.
Alarm Alarming temperature threshold.
Shutdown Shutdown temperature threshold. When the sensor temperature exceeds the
limit, the card shuts down automatically.
If an exception has occurred, perform the following tasks:
1. Verify that the temperature in the equipment room is normal.
2. Verify that the device ventilation aisles are not obstructed.
3. Verify that the fan trays are operating correctly.
4. If the issue persists, record the failure information immediately and contact H3C Support.

11
Checking the status of cards and subcards
Use the display device command to verify that the present cards and subcards are in Normal
state.
<Sysname> display device
Slot No. Brd Type Brd Status Software Version
0 SR05SRP1L1 Master SR8800-CMW710-E8305
1 NONE Absent NONE
2 NONE Absent NONE
3 CSPEX-1504X-A Normal SR8800-CMW710-E8305
Sub1 MIC-CLP2L Normal
Sub2 MIC-GP4L Normal
Sub3 MIC-XP5L_A Normal
Sub4 MIC-ET16L Normal
4 NONE Absent NONE
5 IM-OAPX Normal SR8800-CMW710-E8305
6 NONE Absent NONE
7 NONE Absent NONE
8 NONE Absent NONE
9 NONE Absent NONE
Table 11 Command output
Field
Description
Slot No. Number of the slot where the card or subcard resides.
Brd Type Hardware type of the card or subcard.
Brd Status
Card or subcard status:
•Standby—The card is the standby MPU.
•Master—The card is the active MPU.
•Absent—The slot is not installed with a card or subcard.
•Fault—The card or subcard is faulty and cannot start up.
•Normal—The interface card or subcard is operating correctly.
•Off—The card or subcard is not powered on.
•Illegal—The card or subcard cannot operate correctly because it is not
supported by the current software version.
•Offline—The card is isolated.
Software version Software version of the card.
Use the display system stable state command to verify that all cards are in Stable state.
<Sysname> display system stable state
System state : Stable
Redundancy state : No redundance
Slot CPU Role State
10 Active Stable
2 0 Other Stable
13 0 Other Stable

12
Table 12 Command output
Field
Description
System state Operating status summary of all CPUs:
•Stable—All CPUs are operating stably.
•
Not ready
—A minimum of one CPU is not operating stably.
Redundancy state
Redundancy status:
•Stable—Both MPUs are operating stably. You can perform a switchover.
•No redundance—The system has only one MPU. You cannot perform a
switchover.
•Not ready—The system is not operating stably. You cannot perform a
switchover.
NSR state
Readiness of modules for nonstop routing (NSR):
•Stable—NSR is operating correctly.
•Not ready—NSR is not operating correctly. You cannot perform a
process or active/standby switchover.
Role
Role of the card in the system:
•Active—The card is the active MPU.
•Standby—The card is the standby MPU.
•Other—The card is a service module.
State
Card status:
•Stable—The card is operating stably.
•Board inserted—The card has just been installed.
•Kernel initiating—Card kernel is being initialized.
•Service starting—Services are starting.
•Service stopping—Services are stopping.
•HA Batch backup—An HAbatch backup is going on.
•Interface data batch backup—An interface data batch backup is in
progress.
•Service module data batch backup—A service module data batch
backup is in progress.
*
The object is not operating stably.
If an exception has occurred, record the failure information immediately and contact H3C Support.

13
Collecting and reporting failure
information
If an exception has occurred, first record the following failure information immediatelyand then report
them to H3C Support:
•
Symptom, time of failure, and configuration.
•
Network topology information, including the network diagram, port connections, and points of
failure.
•
Log messages and diagnostic information.
•
Steps you have taken and the result.
Collecting basic failure information
Table 13 shows the basic failure information to be collected if the device is faulty.
Table 13 Basic failure information
Item
Collection method
Time of failure Record the time when the failure occurred down to the minute.
Symptom Record detailed symptom of the failure.
Impact Record the failure severity and affected services.
Networking Draw a network diagram, including uplink and downlink devices and
connected interfaces.
Steps you have taken Record the steps you have taken and the results, including output from the
commands executed during the troubleshooting process.
Collecting log information
Log information records daily information, user actions, system failures, system safety, and system
debugging. It includes diagnosis monitoring log messages, diagnostic log messages, system log
messages, and debug log messages.
To obtain the most recent log information, save the collected log messages to a log file.
To collect log information:
1. The system automatically saves diagnosis monitoring log messages to a log file.
By default, diagnosis monitoring log files are saved in the drvmon folder under the root
directory of the storage device.
2. The system automatically saves maintenance information to a file.
By default, maintenance information is saved in the info folder under the root directory of the
storage device.
3. Save diagnostic log messages from the log buffer to a log file.
diagnostic-logfile save
By default, diagnostic log files are saved in the diagfile folder under the root directory of the
storage device.
4. Save system log messages from the log buffer to a log file.

14
logfile save
By default, system log files are saved in the logfile folder under the root directory of the storage
device.
5. Save trace log messages from the log buffer to a log file.
trace-logfile save
By default, trace log files are saved in the tracefile folder under the root directory of the storage
device.
6. Execute the dir command in user view to verify that the log files are generated correctly.
7. Transfer the log files to the desired destination by using FTP, TFTP, or SFTP. For more
information, see the configuration guide for the router.
Collecting diagnostic information
To collect all diagnostic information for the device, including boot configuration, current configuration,
interface information, time, and system version, execute the display
diagnostic-information command.
To shorten the time used for collecting diagnostic information when the device has many
configurations or a long operation time, execute the display diagnostic-information
key-info command to collect only key diagnostic information.
To collect diagnostic information:
1. Display diagnostic information for the device.
Display all diagnostic information for the device.
<Sysname> display diagnostic-information
Save or display diagnostic information (Y=save, N=display)? [Y/N]:n
===============================================
===============display clock===============
14:03:55 UTC Thu 01/05/2021
=================================================
===============display version===============
...
Display key diagnostic information for the device.
<Sysname> display diagnostic-information key-info
Save or display diagnostic information (Y=save, N=display)? [Y/N]:n
===============================================
===============display clock===============
15:03:55 UTC Thu 01/05/2021
=================================================
===============display version===============
...
2. Save diagnostic information to a diagnostic log file.
Save all diagnostic information to a diagnostic log file.
<Sysname> display diagnostic-information
Save or display diagnostic information (Y=save, N=display)? [Y/N]:y
Please input the file
name(*.tar.gz)[flash:/diag_Sysname_20211020-194410.tar.gz]:
Diagnostic information is outputting to
flash:/diag_Sysname_20211020-194410.tar.gz.
Please wait...

15
Save successfully.
Save key diagnostic information to a diagnostic log file.
<Sysname> display diagnostic-information key-info
Save or display diagnostic information (Y=save, N=display)? [Y/N]:y
Please input the file
name(*.tar.gz)[flash:/diag_Sysname_20211020-194412.tar.gz]:
Diagnostic information is outputting to
flash:/diag_Sysname_20211020-194412.tar.gz.
Please wait...
Save successfully.
By default, diagnostic log files are saved in the root directory of the storage device.
3. Execute the dir command in user view to verify that the diagnostic file is generated correctly.
4. Transfer the diagnostic file to the desired destination by using FTP, TFTP, or SFTP. For more
information, see the configuration guide for the router.

16
Troubleshooting login failure
CAUTION:
M
ake sure all user services have stopped before performing the following tasks.
If user services are
not interrupted, collect the failure information and contact H3C Support.
If you cannot log in to the device through Telnet or SSH, log in from the console port and modify
Telnet or SSH settings. If you cannot log in to the device from the console port, use this section to
troubleshoot the issue.
Checking for power supply system failure
Symptom
The LEDs on the cards are off and the fans on the cards do not operate (determined by the sound).
Solution
To resolve the issue:
1. Verify that the power supply is powered on. If the device is installed with multiple power supplies,
make sure the power supply that ensures device operation is powered on.
2. Verify that the LED that indicates a normal operating state for the power supply is on. See
"Checking the LED status." If the power supply is faulty, it might have issues such as output
short-circuit, output overcurrent, output overvoltage, input undervoltage, and overtemperature.
3. If the power supply has an input exception, contact electricians to examine and repair the power
supplysystem for the equipment room, rack, or cabinet. If the power supply is faulty, replace the
power supply.
4. If the issue persists, contact H3C Support.
Checking for inconsistent serial communication
parameter settings between the configuration
terminal and the console port
Symptom
Serial communication parameter settings between the configuration terminal and the console port
are inconsistent.
Solution
To resolve the issue, edit the serial communication parameter settings for the serial port on the
terminal.
By default, the communication parameter settings for the console port on the device are as follows:
•
Baud rate—9600.
•
Data bits—8.
•
Stop bits—1.
•
Parity—None.
•
Flow control—None.

17
If the communication parameter settings for the console port on the device have been changed, use
the most recent settings.
Checking for MPU failure
If an MPU failure occurs, perform the following tasks to resolve the issue:
1. Reinstall the MPU and fasten the screws to make sure the MPU is installed securely.
2. Press the RESET button to reboot the MPU.
3. If the device has an empty MPU slot, install the MPU in the emptyslot and check its operational
status.
4. Replace the MPU.
Resetting the device
If you cannot log in to the device after you reinstall, reset, or replace the MPU, you can reset the
device. To reset the device, power off the device and then power on the device after three minutes.
Contacting H3C Support
If the issue persists, contact H3C Support.

18
Safety and configuration cautions and
guidelines
This section describes important information that if not understood or followed can result in
undesirable situations, including bodily injury, device damage, service interruption, or service
anomalies. It contains hardware safety guidelines and CLI-based configuration cautions and
guidelines. Before you work on or configure your device, read the information in this section carefully.
Hardware safety guidelines
Only trained and qualified personnel are allowed to perform the operations described in this guide.
Table 14 Hardware safety guidelines
Category
Guidelines
Handling device and
modules Do not operate the device and modules without wearing an ESD wrist strap.
Handling cards
When the device is operating, remove the active MPU only when both MPUs
are operating stably. To view system stability and status information, execute
the
display system stable state
command.
Pressing the RESET button on an MPU will reset the MPU forcibly. This
operation can be performed only by qualified maintenance personnel when a
severe system failure occurs.
Handling transceiver
modules Do not stare into any open apertures of operating transceiver modules or
optical fiber connectors.
Handling cables
Network cables are used for the communication between the device and the
maintenance terminal. Network cable connection or disconnection can be
performed only by qualified maintenance personnel for service adjustment as
scheduled and they must be aware of the impact on the network.
Handling power supplies
Do not hot swap power supplies.
Operate the power switches on the PDUs in the cabinet only when upgrading
or expanding the device, replacing the components in the device, or when a
severe system failure occurs.
For devices that have two power switches, to power off the device for
maintenance, make sure the two power switches are both turned off.
CLI-based configuration cautions and guidelines
Only trained and qualified personnel are allowed to do the configuration tasks described in this guide.
For more information, see the safety and configuration cautions and guidelines for the router.
Table 15 CLI-based configuration cautions and guidelines
Feature
Command
Description
Usage guidelines
File system
management delete [/unreserved ]
file Deletes a file.
The
delete
/unreserved
file command
deletes a file
permanently. The file
Other manuals for SR8800-X
2
This manual suits for next models
6
Table of contents
Other H3C Network Router manuals

H3C
H3C SR6600 Series User manual
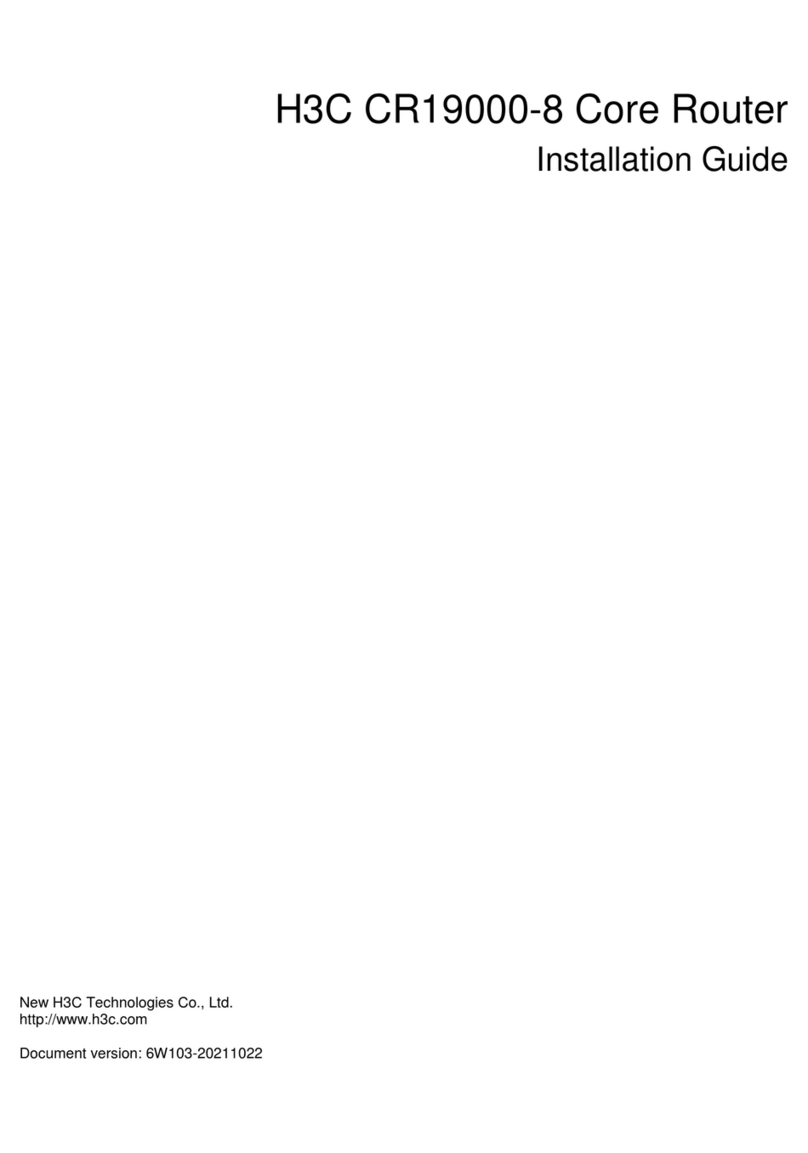
H3C
H3C CR19000-8 User manual
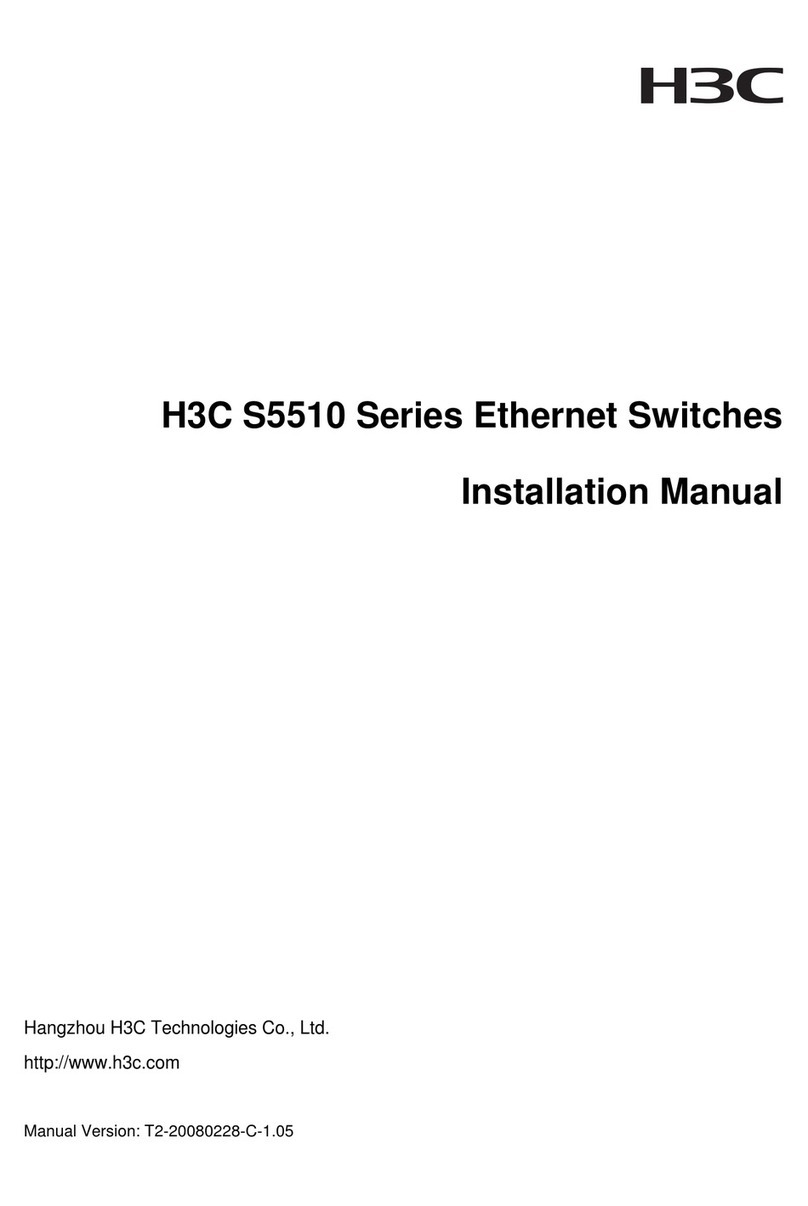
H3C
H3C S5510 Series User manual
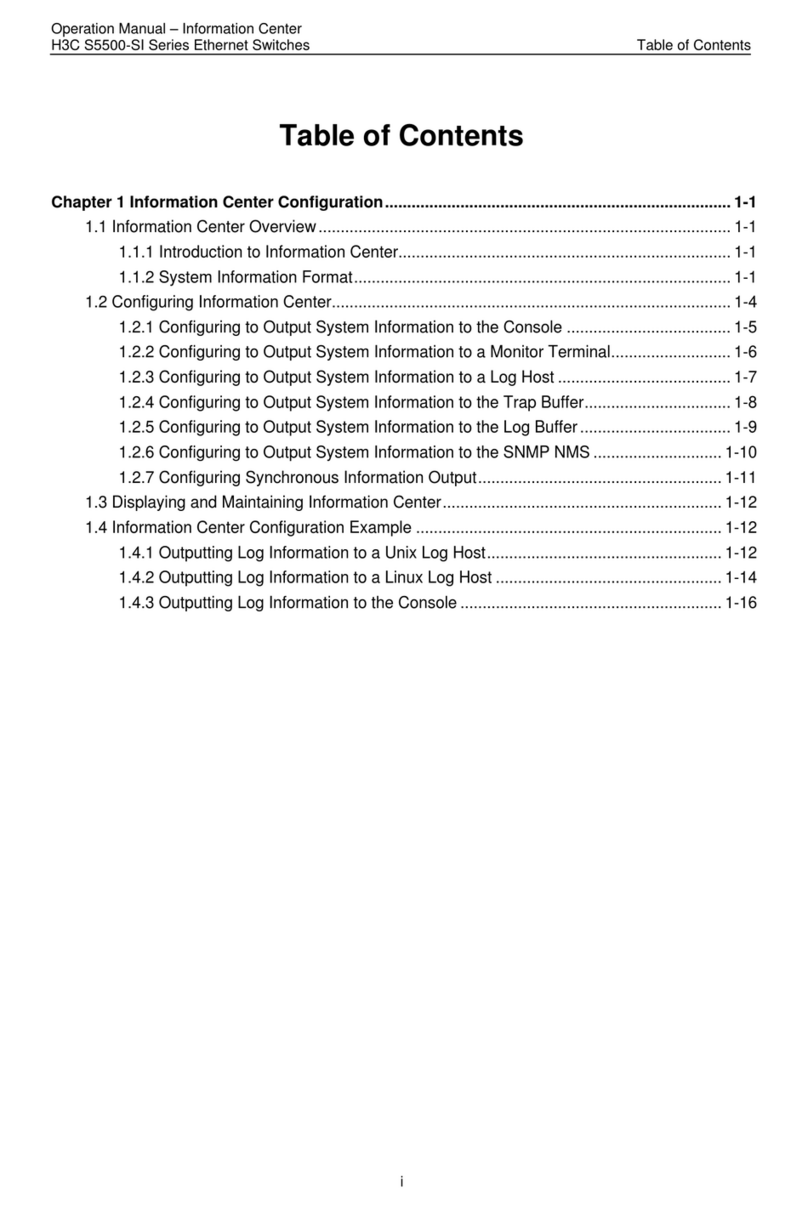
H3C
H3C S5500-SI Series User manual
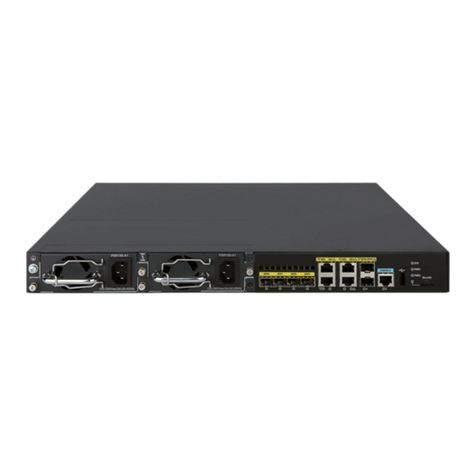
H3C
H3C MSR 3600 User manual

H3C
H3C s5820x series User manual

H3C
H3C SR6600 SPE-FWM Installation manual
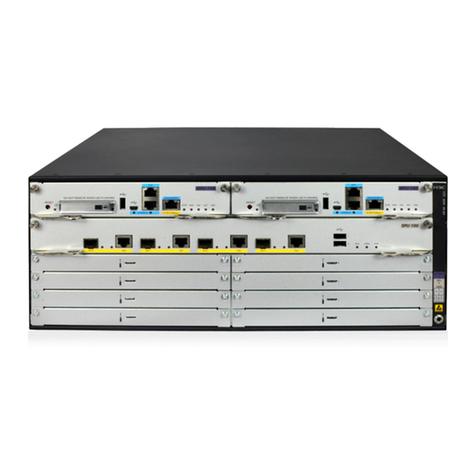
H3C
H3C MSR5620 User manual

H3C
H3C CR16000-F User manual
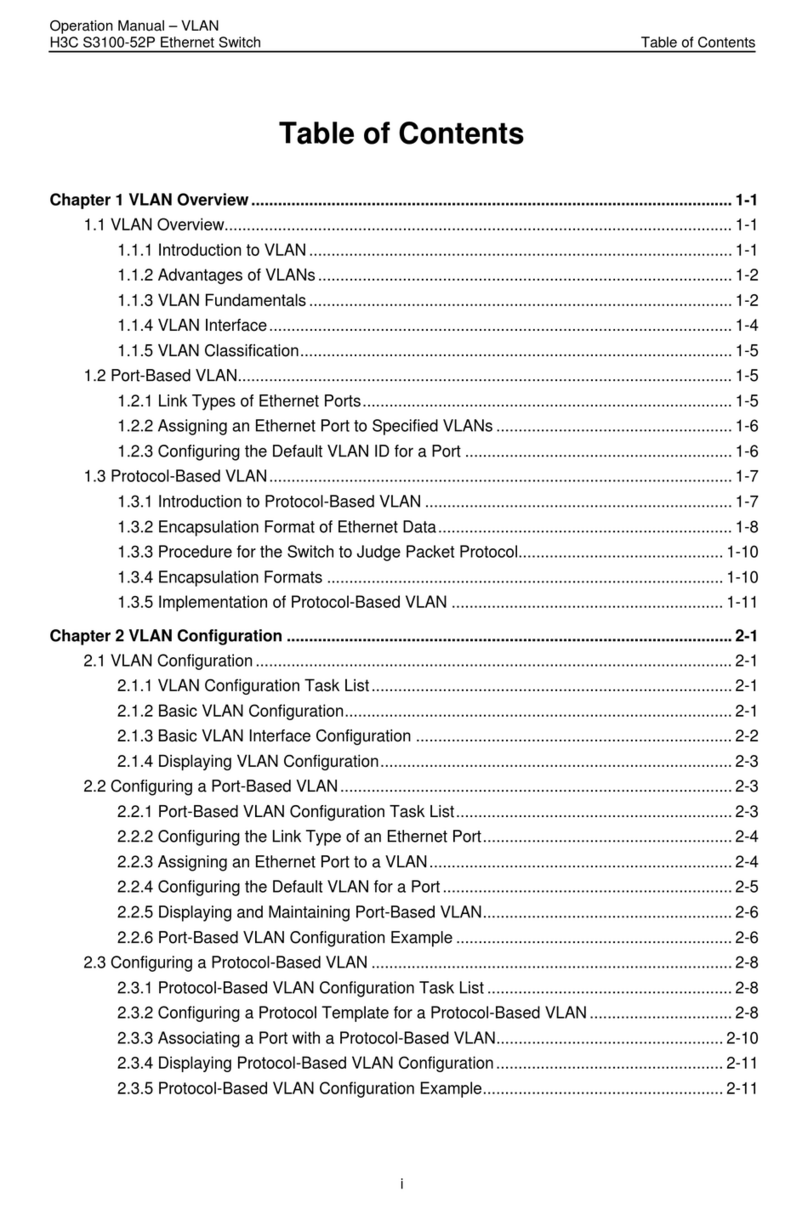
H3C
H3C S3100-52P User manual
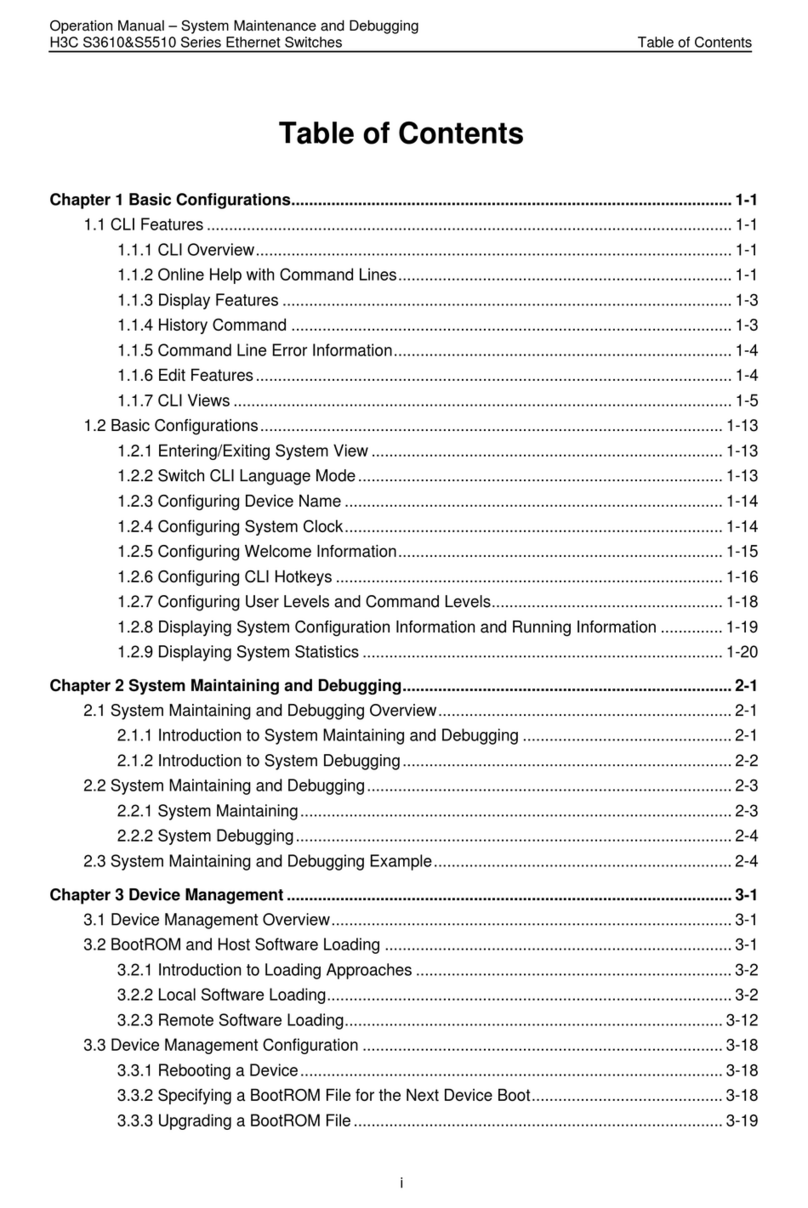
H3C
H3C S3610 Series User manual
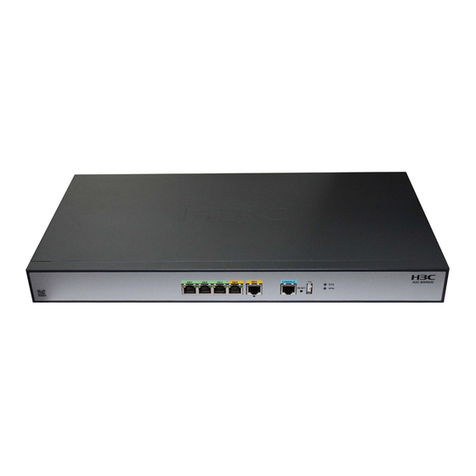
H3C
H3C MSR Series User manual
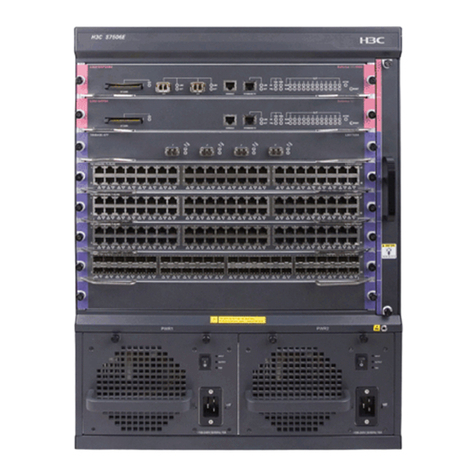
H3C
H3C H3C S7500E Series User manual
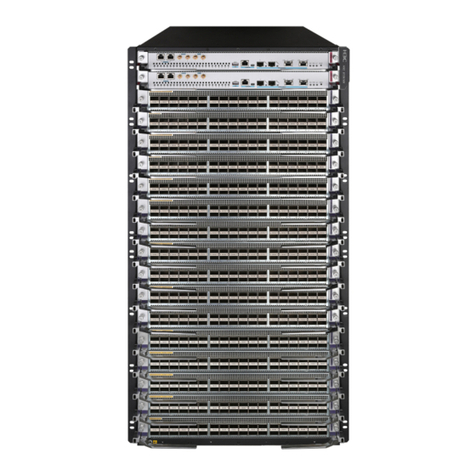
H3C
H3C S12500R Series Quick guide
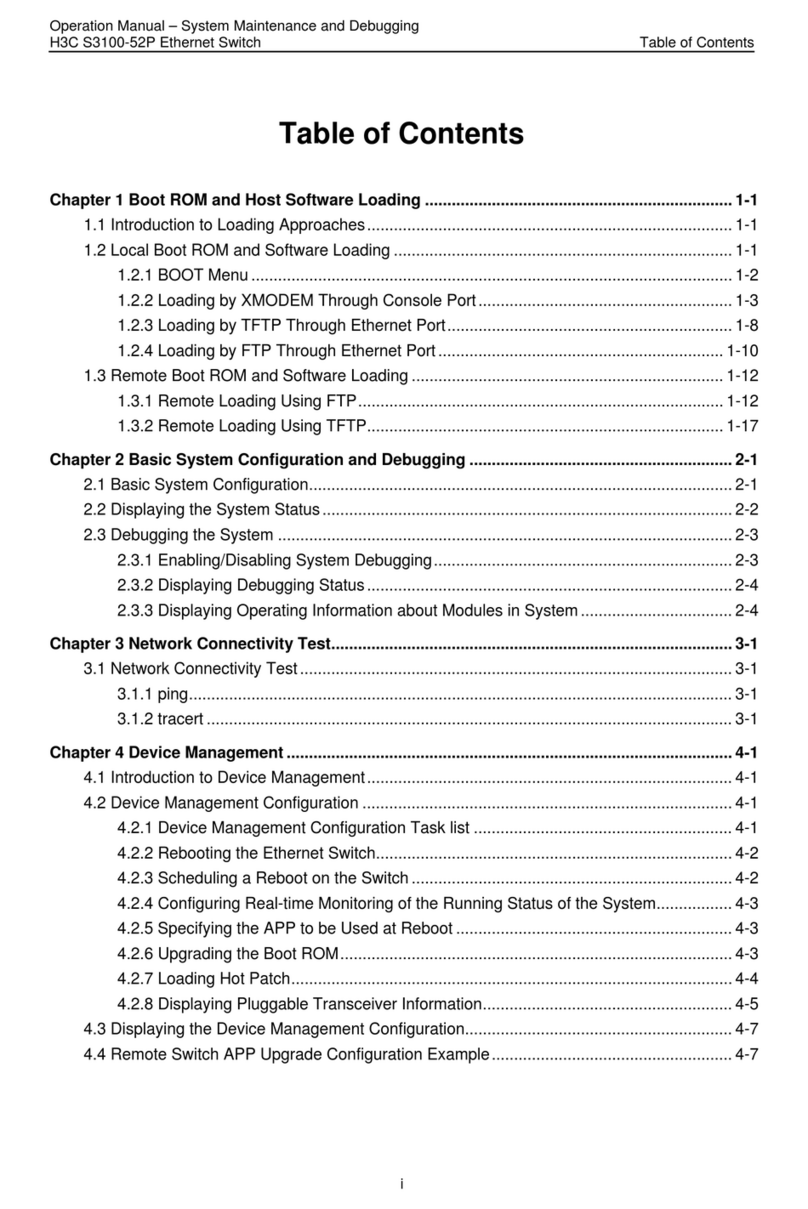
H3C
H3C S3100-52P User manual
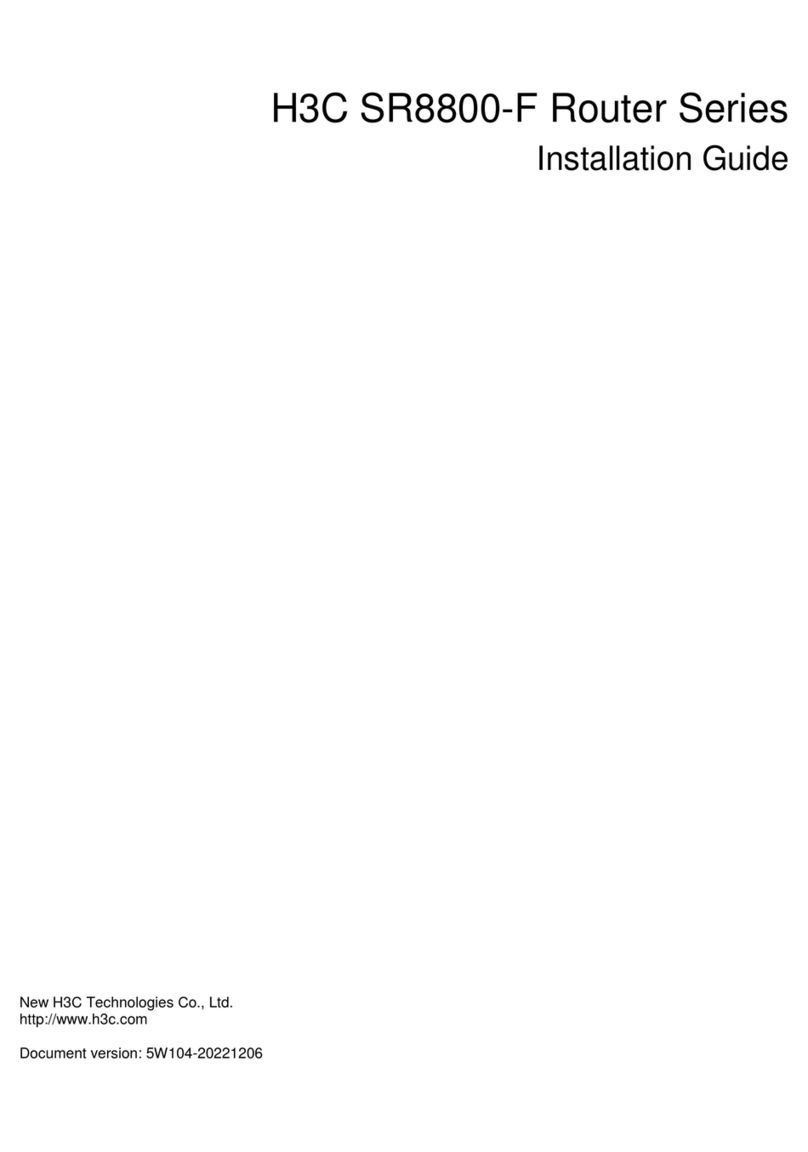
H3C
H3C SR8800-F User manual
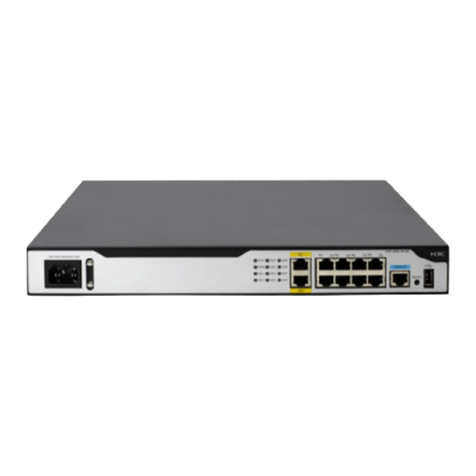
H3C
H3C MSR 2600 Series User manual
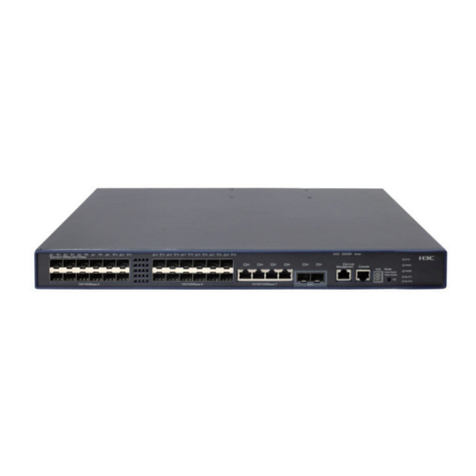
H3C
H3C S5500-HI Switch Series User manual
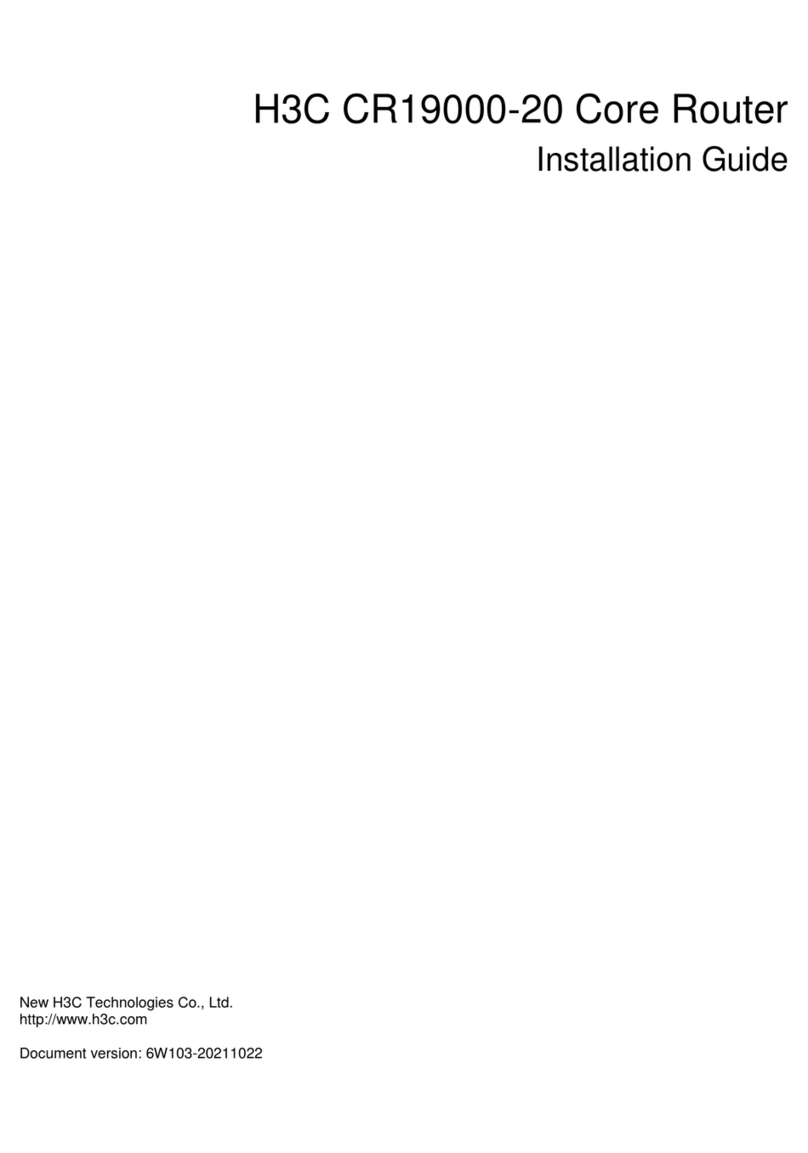
H3C
H3C CR19000-20 User manual
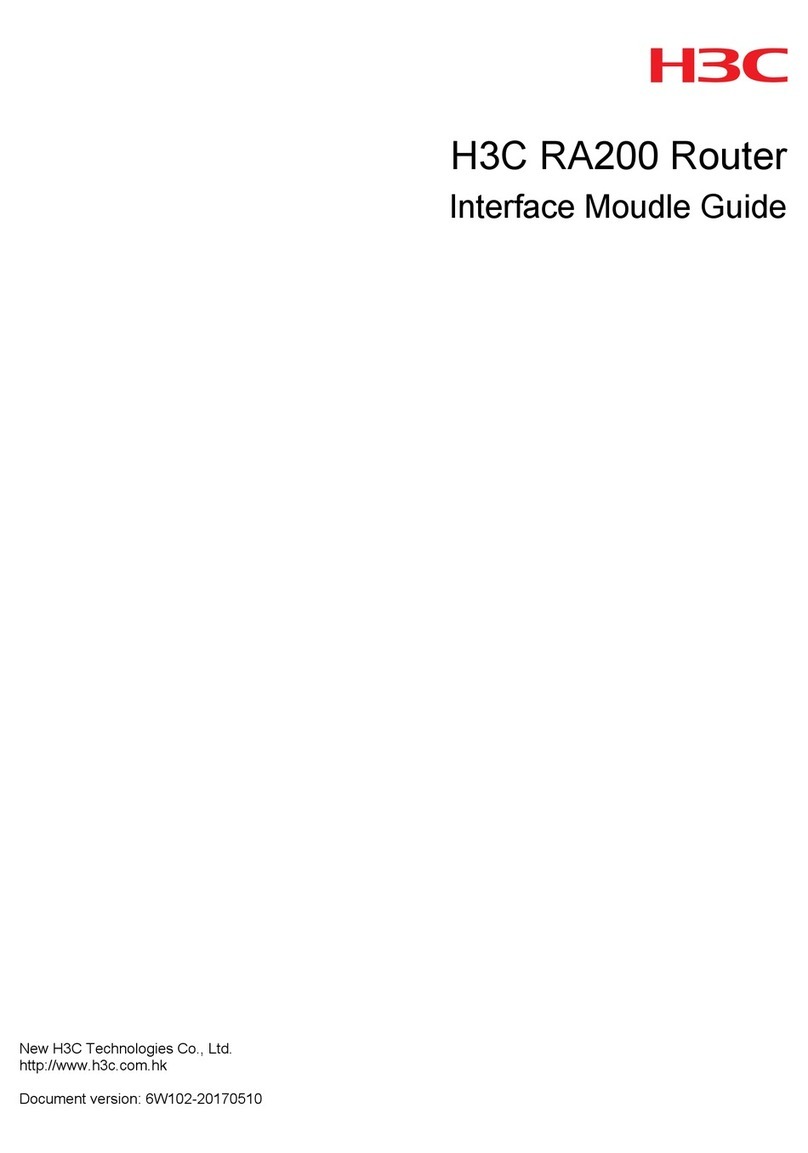
H3C
H3C RA200 User manual