Hawk Gladiator series User manual

Sultan Sonar Manual Rev 1.0
A Higher Level of Performance
www.hawkmeasure.com
For more information, please visit >
Gladiator
Conductivity Switch Series
A Level Switch for Liquids and Slurries
Manual

Table of Contents
2
Contents
Gladiator Conductivity Switch Series
PROPRIETARY NOTICE
The information contained in this publication is derived in part
from proprietary and patent data. This information has been
prepared for the express purpose of assisting operating and
maintenance personnel in the efficient use of the instrument
described herein. Publication of this information does not convey
any rights to use or reproduce it, or to use for any purpose
other than in connection with the installation, operation and
maintenance of the equipment described herein.
WARNING
This instrument contains electronic components that are
susceptible to damage by static electricity. Proper handling
procedures must be observed during the removal, installation, or
handling of internal circuit boards or devices:
Handling Procedure:
1. Power to unit must be removed prior to commencement of
any work.
2. Personnel must be grounded, via wrist strap or other safe,
suitable means, before any printed circuit board or other
internal devices are installed, removed or adjusted.
3. Printed circuit boards must be transported in a conductive
bag or other conductive container. Boards must not be
removed from protective container until the immediate time of
installation. Removed boards must be placed immediately in a
protective container for transport, storage, or return to factory.
Comments:
This instrument is not unique in its content of ESD (electrostatic
discharge) sensitive components. Most modern electronic
designs contain components that utilize metal oxide technology
(NMOS, CMOS, etc.). Experience has proven that even small
amounts of static electricity can damage or destroy these
devices. Damaged components, even though they appear to
function properly, exhibit early failure
Overview 3
General Description 3
Principle of Operation 3
Primary Areas of Application 3
Features 3
Typical Applications 4
Non-metallic Tank 4
Non-metallic Tank 4
Dimensions 5
Remote Amplifier 5
Optional Flange 5
Single Probe 5
Two Probe 5
Two Probe 5
Mounting 6
Dimensions 7
Mounting 7
Wiring 8
Smart Probe 8
Remote Probe to Amplifier 9
Relay Functions 10
Multidrop Connections* 11
Test Terminal Function Selection 12
Setup Procedure 13
Smart Probe Functionality Layout 13
Smart Probe Version 14
Smart Probe Version 15
Remote Functionality Layout 16
Remote Version 17
Software Menu 18
Remote Amplifier 18
Flow Chart 19
Software Tree 19
Quickset 20
Advance Menu 21
Advance Menu 22
Diagnostic Displays (Remote type only) 23
Diagnostic Displays 24
Part Numbering 25
Smart Probe Version 25
Remote Version 26
Specications 27
Conductivity Table 28

Overview
General Description
The Gladiator Smart Conductivity Switch is a third generation, state-of-the-art level probe, designed to
operate in tough industrial environments. The probe of the Conductivity Switch forms one part of an electric
circuit, with the vessel wall or a reference probe making another part. A conductive liquid between the probe
and the vessel wall (or between the probe and the reference probe) links the two parts of the circuit and the
output will switch in response. The output has adjustable hysteresis and delays for ‘on’ or ‘off’ switching.
A test function is available to remotely confirm the probe integrity by switching the relay contacts.
The Gladiator Smart Switch Series includes communications capability for remote adjustment,
control and monitoring.
• No moving parts - low maintenance
• Low voltage on probe for operational safety
• Simple ‘1-minute’ setup
• Remote sensor or Smart ‘all in one’ types
• Relays outputs:
Smart probe (1), Remote (2)
• Remote test function
• Adjustable ON and OFF delays (0-20 sec)
• Modbus, GosHawk
• Remote 3G Connection option
• Remote amplier to probe separation up to
500m (1640ft)
• Bright visual status indication on probe
• Independent housing alignment after
mounting thread locked.
Features
3
Gladiator Conductivity Switch Series
Principle of Operation
A low voltage AC signal is applied between the probe electrode and the tank wall or reference electrode in
the case of a non-metallic tank. When the liquid comes into contact with the electrode tip, a conductive path is
established between the sense electrode and the metallic tank wall/reference electrode.
Current flow due to the conductive path is sensed, amplified and used to switch a relay for indication or
control purposes.
Primary Areas of Application
• Brewing
• Chemical
• Dairy
• Edible Oil
• Fertilizer
• Glass
• Food & Beverage
• Mining & Metals
• Oil & Gas
• Packaging
• Paint
• Paper
• Pharmaceutical
• Power Generation
• Refining
• Semiconductor
• Sugar
• Textile
• Water & Wastewater.

Typical Applications
4
Gladiator Conductivity Switch Series
Sump pump control
Non-metallic Tank
High level switch in water tank
Non-metallic Tank
*
*Mounting must be electrically connected to tank wall for a
single rod probe to work. Dual probe will work without
electrical connection.

5
Dimensions
Gladiator Conductivity Switch Series
RemoteAmplier
14 mm (0.6”)
74 mm (2.9”)
78 mm (3.1”)
107 mm (4.2”)
111.5 mm (4.4”)
4 mm (0.2”)
50 mm (2”)
131.5 mm (5.2”)
7.5 mm (0.3”)
192.5 mm (7.6”)
141.5 mm (5.6”)
190 mm (7.5”)
182.5 mm (7.2”)
147 mm (5.8”)
167.5 mm (6.6”)
147 mm (5.8”)
30.7 mm (1.2”)
158 mm (6.2”)
108 mm (4.3”)
190 mm (7.5”)
174 mm (6.9”)
192.5 mm (7.6”)
182.5 mm (7.2”)
30.0
20.2
33.029.029.033.0
16
.2
A B
C
Flange Dimensions - 50mm (2”)
A B C
ANSI (Class 150) 120.7 4.75” 152.4 6” 19.1 0.75”
DIN (PN40) 125 4.9” 165 6.5” 18 0.7”
JIS (10K) 120 4.7” 155 6.1” 19 0.75”
Optional Flange
Standard probe lengths
(L1 or L2):
• 30 cm (11.8”)
• 50 cm (19.7”)
• 100 cm (39.4”)
Single Probe Two Probe
Single Switch Points
Bare probe
50mm (2”)
85mm (3.3”)
probe length = L1
M20 cable gland
or 3/4” NPT adaptor
on smart type.
Window for
viewing status
LEDs
Mounting
thread
90mm (3.5”)
50mm (2”)
5mm (0.2”)
85mm (3.3”)
Window for
viewing status
LEDs
Optional
Flange
90mm (3.5”)
50mm (2”)
2 x M20
cable glands
or 3/4” NPT adaptors
on remote type.
8mm (0.3”)
teflon isolated probe
for build-up protection
Bare probe
50mm (2”)
probe length = L1 = L2
teflon isolated probe
for build-up protection
85mm (3.3”)
Window for
viewing status
LEDs
90mm (3.5”)
50mm (2”)
probe length L2
probe length L1
10mm (0.3”)
teflon isolated probe
for build-up protection
Mounting
thread, 1.5” NPT
or BSP only
Mounting
thread, 1.5” NPT
or BSP only
Bare probe
50mm (2”)
85mm (3.3”)
probe length = L1
M20 cable gland
or 3/4” NPT adaptor
on smart type.
Window for
viewing status
LEDs
Mounting
thread
90mm (3.5”)
50mm (2”)
5mm (0.2”)
85mm (3.3”)
Window for
viewing status
LEDs
Optional
Flange
90mm (3.5”)
50mm (2”)
2 x M20
cable glands
or 3/4” NPT adaptors
on remote type.
8mm (0.3”)
teflon isolated probe
for build-up protection
Bare probe
50mm (2”)
probe length = L1 = L2
teflon isolated probe
for build-up protection
85mm (3.3”)
Window for
viewing status
LEDs
90mm (3.5”)
50mm (2”)
probe length L2
probe length L1
10mm (0.3”)
teflon isolated probe
for build-up protection
Mounting
thread, 1.5” NPT
or BSP only
Mounting
thread, 1.5” NPT
or BSP only
Two Probe
Dual Switch Points

6
Mounting
Gladiator Conductivity Switch Series
Probes can be mounted from the top,
side and bottom.
Points to consider when mounting:
A. Material Infeed Clearance
Install the probe away from the infeed to minimize the
influence of build-up and impact forces, and to avoid
false triggering from product flow.
B. Wall Clearance
Install the probe far enough away from the vessel wall
to prevent the probe from coming into contact with the
wall and prevent conductive build-up from bridging
the probe to the wall over time. Avoid creating a
confined area where material could build-up.
See note
C. Nozzle Clearance
Ensure the probe does not come in contact with the
mounting nozzle.
D. Top mounting
When top mounting, ensure adequate clearance is
provided between probe and wall. Avoid creating a
confined area where material could build-up over
time.
See note
E. Side mounting
It is highly recommended to install any side mounted
probe at a downward angle of 30-45º. Use a
protection plate for side mounting where the probe
may be subject to impact damage.
F. Bottom mounting
Bottom mounting is not recommended. Only mount
from the bottom if no build-up of material occurs. If
low level mounting is required, suitable options are
shown in the diagram on next page.
INCORRECT MOUNTING NOTES:
(Refer to diagram on next page)
Incorrect mounting because the probe is too close
to the wall or roof. Positioning too close to a wall or
roof may allow material build-up between the probe
and the vessel.
Incorrect mounting because the probe is touching
the nozzle. The probe must not touch the nozzle or
any part of the vessel. Conductive build-up must
not bridge from the probe to the nozzle or reference
probe.
Recommended 50mm (2”)
Correct Mounting in a Nozzle
min. 100mm (4”)

7
Dimensions
Gladiator Conductivity Switch Series
Mounting
Probes can be mounted from above or from the side.
Use a protection plate for side mounting where the probe may be subject to impact damage.
Install the Probe far enough away from the vessel wall to prevent the probe from coming into contact with the
wall, and prevent conductive build-up from bridging the probe to the wall over time.
Correct
Correct (non-preferred
low level mounting)
Incorrect
1
2
Correct Correct
If necessary, mount a
protection plate to
prevent direct impact.
1
Housing can be rotated
within 200º after the
mounting thread is
tightened, to allow cable
entries to face downwards
or allow optimal cable
clearance.
30-45º
Possible
product
build-up
Possible conductive
build-up
Correct
Correct
Incorrect
Incorrect
Incorrect
2

8
Wiring
Gladiator Conductivity Switch Series
Smart Probe
1 2 3 4 5 6 7 8 9 10
S
E
N
S
I
T
I
V
I
T
Y
D
E
L
A
Y
HI FSH TESTCAL
1. NC
RELAY
2. COM
3. NO
COMMS DC-IN AC-IN
4. Test
12-30Vdc
80-265Vac
+
7.
8.
N
9.
L1
10.
RS 485
5.
B
6.
A
-
GLADIATOR SMART PROBE TERMINAL LAYOUT
Hole for securing of
optional identification tag
M4 grounding screw
Ground the housing to
vessel, if vessel is metallic.
Ground the housing to
plant ground, if vessel is
non-metallic.
The AC earth/ground
cable must be connected
to the ground screw
inside the housing when
using AC power.
If only one cable is used for both
power and output signal, then the
second entry port must be
plugged or blinded. Every Smart
unit is supplied with two M20
glands (or 3/4”NPT adaptors)
mounted on the unit and one
blind plug loose.
Remove Plug-In terminal
block for easier wiring.
!
D
e
l
a
y
FSHHI
LO FSL
CAL TEST
OFF OFF
Signal
S
e
n
s
i
t
i
v
i
t
y
ON
1 2
ON
1 2
1 2 3 4 5 6 7 8 9 10
User pliers to extract
terminal blocks

9
Wiring
Gladiator Conductivity Switch Series
RemoteProbetoAmplier
1 2 3 4 5 6 7 8 9 10
GLADIATOR REMOTE PROBE TERMINAL LAYOUT
M4 grounding screw
7.1. 2. 3. 4. 5. 6. 8. 9. 10.
RED
WHITE
BLUE
BLACK
Cable type between Amplifier and Probe
4 conductor shielded twisted pair instrument cable.
Conductor size dependent on cable length.
BELDEN 3084A, DEKORON or equivalent.
Max: BELDEN 3084A = 500m (1640ft)
Max: DEKORON IED183AA002 = 350m (1150ft)
Hole for securing of
optional identification tag
Ground the housing to
vessel, if vessel is metallic.
Ground the housing to
plant ground, if vessel is
non-metallic.
Remove Plug-In
terminal block for
easier wiring.
Terminals 1, 2, 3, 4, 9, 10 not used.
Gladiator Remote Amplifier
Relay 1 - Output Relay
Relay 2 - FailSafe Relay
+–
A
1L
+
–
N
B
RED
BLACK
BLUE
WHITE
BROWN
Is
SENSOR DC-In AC-In*4-20mA (N/A)
COMMS
MIC-SENDER
RED
BLACK
BROWN
SLAVE IN
MASTER OUT
TEST IN
RELAY 1
NC
COM
NO
RELAY 2
NC
COM
NO
1 2 3 4 5 6 7 8 9 10 11 12 13 14 15
16 17 18 19 20 21 22 23 24 25 26 27 28 29 30
remote
Signal
STATUS
1 2 3 4 5 6 7 8 9 10
User pliers to extract
terminal blocks
CabletypebetweenAmplierandProbe
• Cable type between Amplifier and Probe
• 4 conductor shielded twisted pair instrument cable
• Conductor size dependent on cable length
• BELDEN 3084A, DEKORON or equivalent
• Max: BELDEN 3084A = 500m (1640 ft)
• Max: DEKORON IED183AA002 = 350m (1150 ft).
*AC-In is replaced by 36-
60VDC with Power Input
Option ‘C’.

10
Wiring
Gladiator Conductivity Switch Series
Relay Functions
HI
OFF
TEST
LOW
EN
DEN
CALOFF
DELAY
SENSITIVITY
FailSafe Low
FSL
123
1 2 3
123
1 2 3
FailSafe High
FSH (default)
123
123
123
123
RISING LEVEL
NC NO
NC NO
NC NO
NC NO
NC NO
NC NO
NC NO
COMMS DC-IN
AC GND to metal case
12-30VDC
+
7.
8.
RS 485
5.
B
6.
A
1 2 3 4 5 6 7 8 9 10
+–
4-20mA
AC-IN
A
1L
+
–
DC-IN
4-20mA COMMSTRANSDUCER
N
B
RELAY 1
NC
COM
NO
RELAY 2
NC
COM
NO
RELAY 3
NC
COM
NO
RELAY 4
NC
COM
NO
RELAY 5
NC
COM
NO
Test in
Is
RED
BLACK
BLUE
WHITE
REMOTE AMPLIFIER
GLADIATOR TERMINAL
COM COM
COM
COM COM
COM COM
POWER FAILURE
NC NO NC NOCOM COM
INTERNAL FAILURE
POWER FAILURE
OR
SYSTEM OPERATING
NORMALLY
NC NOCOM NC NOCOM
Relay Status
LED Status
State 1State 2State 1
Single Switch Point Dual Switch Points
FALLING LEVEL
OR
FALLING LEVEL
CONTACT LEVEL CONTACT LEVEL
RISING LEVEL
Smart Probe
terminal numbers
Remote Amplifier
terminal function
labels
Relay Action
FailSafe Switch Contact Action
Relay 2 - For Remote version only.
For Smart Probes the Test terminal can act as a
solid state output with a similar function.
(See page 14)
Level Switch
Contact Action
Relay - for Smart
Probe Version
(Set Relay Action
selection switch -
pages 15 and 16)
Relay 1 - for Remote
Version (Set Relay
Action parameter
pages 19 and 22)

Wiring
Gladiator Conductivity Switch Series
11
Multidrop Connections*
Laptop or PC Communications using
PCMCIA card or wired (PSTN) modem
and remote GSM/CDMA connection
with GosHawk software.
A B Gnd A B Gnd A B Gnd
Laptop or PC Communications using
HawkLink USB or RS485 / 232 converter
with GosHawk software.
HawkLink
USB
A B Gnd A B Gnd A B Gnd
PLC / DCS / SCADA for Remote
Communication with Modbus.
A B Gnd A B Gnd A B Gnd
HawkLink
HLRUG6
GPRS modem
White
Blue
Black
Multidrop Connection Using HawkLink USB*
Multidrop GPRS Connection*
Multidrop Connection to PLC/DCS/SCADA*
* Wiring installation should follow
RS-485 standards for layout and
termination.
D
e
l
a
y
FSHHI
LO FSL
CAL TEST
OFF OFF
Signal
S
e
n
s
i
t
i
v
i
t
y
ON
1 2
ON
1 2
1 2 3 4 5 6 7 8 9 10
D
e
l
a
y
FSHHI
LO FSL
CAL TEST
OFF OFF
Signal
S
e
n
s
i
t
i
v
i
t
y
ON
1 2
ON
1 2
1 2 3 4 5 6 7 8 9 10
CAL
RUN
RELAY1 RELAY2 STATUS A STATUSB
D
e
l
a
y
FSHHI
LO FSL
CAL TEST
OFF OFF
Signal
S
e
n
s
i
t
i
v
i
t
y
ON
1 2
ON
1 2
1 2 3 4 5 6 7 8 9 10
D
e
l
a
y
FSHHI
LO FSL
CAL TEST
OFF OFF
Signal
S
e
n
s
i
t
i
v
i
t
y
ON
1 2
ON
1 2
1 2 3 4 5 6 7 8 9 10
CAL
RUN
RELAY1 RELAY2 STATUS A STATUSB
CAL
RUN
LINK
CAL
RUN
LINK
D
e
l
a
y
FSHHI
LO FSL
CAL TEST
OFF OFF
Signal
S
e
n
s
i
t
i
v
i
t
y
ON
1 2
ON
1 2
1 2 3 4 5 6 7 8 9 10
D
e
l
a
y
FSHHI
LO FSL
CAL TEST
OFF OFF
Signal
S
e
n
s
i
t
i
v
i
t
y
ON
1 2
ON
1 2
1 2 3 4 5 6 7 8 9 10
CAL
RUN
RELAY1 RELAY2 STATUS A STATUSB

12
Wiring
Gladiator Conductivity Switch Series
Test Terminal Function Selection
Terminal Block
PLC / SCADA / DCS Output
Test
Terminal Block
Test
Test
Coil rating
500mW max
or 50mA max
Test
To switch an external relay
+12-24Vdc
PLC
SCADA
DCS Input
Pull up
12-24Vdc
max 50mA
To a PLC input
Externally provided
test button
!
!
PLC/SCADA/DCS GROUND MUST
CONNECT BACK TO GLADIATOR
GROUND OR DC ‘-’ TERMINALS
EXTERNAL PUSH BUTTON GROUND
MUST CONNECT BACK TO GLADIATOR
GROUND OR DC ‘-’ TERMINALS
Test terminal will provide an output which is able to switch an external failsafe relay or PLC/SCADA/DCS
input. During normal system operation this terminal will internally switch a solid state (transistor) output to
ground (or DC ‘-’). If power fails or an internal system failure occurs, the terminal will act as an open circuit.
Relay will turn on during
normal system operation
or off in failed or unpowered
conditions.
Input will detect ‘0’ state during normal system
operation, or ‘1’ in failed or unpowered conditions.
Test input mode
Test switch must be in ‘TEST’ (ON) position on Smart Probe - function always enabled on Remote Amplifier.
Test terminal acts as an input for remote testing of the instrument’s switching function. Used to check for
malfunction of unit from a remote position, PLC, SCADA etc. For more information see page 17.
TEST INPUT FROM PLC/SCADA/DCS DIGITAL OUTPUT
OPERATOR CONTROLLED PRESS TO TEST
FAILSAFE OUTPUT MODE (Test switch must be in the ‘OFF’ position - default setting)

13
Setup Procedure
Gladiator Conductivity Switch Series
Smart Probe Functionality Layout
1
2
3
4
5
6
7
8
9
10
11
Mounting Calibration switch CAL/OFF
Relay action selection
switch
FSH - FailSafe High
FSL - FailSafe Low
Sensitivity Potentiometer
Default 50% = 12 o’clock
HI / LO sensitivity switch
BLUE LED:
Blinking indicates calibration function is on.
Continuously ON indicates failed calibration.
AC Ground - must be used for
AC powered installations
GREEN LED: Power / Status
Blinks to indicate the functioning
is correct and no media is detected.
Continuously ON when media is detected.
Removable terminal block - plug in type
Delay Potentiometer (0-20 sec)
(Default 0 sec. at minimum
position)
Test input function select TEST/OFF
RED LED: Relay status
ON when relay coil is energised
Functionality Description (bold is default)
12 Signal voltage test point
D
e
l
a
y
FSHHI
LO FSL
CAL TEST
OFF OFF
Signal
S
e
n
s
i
t
i
v
i
t
y
1 2 3 4 5 6 7 8 9 10
ON
1 2
ON
1 2
9
4
6
3
12
8
10 711
2
5
1
- Not used in Gladiator Conductivity products

14
Setup Procedure
Gladiator Conductivity Switch Series
Smart Probe Version
1. Mount the unit in its actual position.
(See mounting procedure - pages 6-7)
• Make sure that external ground wire is connected
between the outside ground screw on the Gladiator
housing and the roof/wall/side of the silo/tank/
vessel/chute. (For non metallic tanks make sure that
external ground wire is connected between the
same outside ground screw on the housing and the
general plant ground potential).
2. Check where the actual level is relative to
the probe
• Make sure that the liquid is not touching the probe
or probes.
3. Turn the power on
• The green LED will either stay on for 2 seconds
then begin flashing or stay on permanently to
indicate operation.
4. Select the required relay contact action
• The Relay can switch ‘ON’ or ‘OFF’ as the product
approaches the probe and switch ‘ON’ or ‘OFF’ in
response to an instrument failure (for details
see page 10).
• Set the relay action selection switch position (FSL or
FSH) depending on your requirements.
5.Cancelinuenceofmounting
• Do not proceed with this step unless the liquid is not
touching the probe or probes.
• Switch the Mounting Calibration switch to ‘CAL’
(ON) position. The Blue LED will blink to indicate
that mounting calibration is now in progress.
• Wait for at least 10 sec. then switch the mounting
calibration switch to ‘OFF’ position.
• The blue LED should turn off after a short time.
• The blue LED will stay on if there was a calibration
error.
• If this is the case please check that the probe is not
touching the product or the mounting, then try the
calibration again.
• If mounting calibration was successful the blue LED
should be off and the Green LED should blink every
2 sec.
• Unit is now able to cancel influence of mounting and
probe history has been cleared.

15
Smart Probe Version
6. Select the sensitivity
There are two adjustments controlling the sensitivity
of the switch point:
6.1. The ‘HI/LO’ sensitivity switch is used to
set your unit depending on the conductivity of the
product to be measured. This switch sets the range of
adjustment possible with the sensitivity potentiometer.
• If the material to be detected has a lower
conductivity than 1750µS/cm (4400µS/inch) -
set the switch to ‘HI’ (ON) - default.
• If material to be detected has a higher conductivity
than 1750µS/cm (4400µS/inch) - you may set the
switch to ‘LO’.
• If you are not aware of your material’s conductivity –
set the switch to ‘HI’ (ON) - default.
6.2 The sensitivity potentiometer
• Set the potentiometer according to your requirements.
• A 12 o’clock setting (50%) - default, will cover the
majority of instances - for the remaining instances,
turning the potentiometer clockwise will increase
sensitivity.
• Increasing sensitivity maybe necessary if the liquid is
not detected when touching the probe.
7. Select the time delay
• Set the required delay using the Delay
potentiometer. (Default is 0 sec. at minimum
position) Turn the potentiometer clockwise if any
delay is required.
• Maximum rotation is ¾ of a revolution.
• Max delay is 20 sec. The selected delay will be used
for both an ON delay and an OFF delay.*
8. Test function
(used to check for malfunction of unit from
remote position, PLC, SCADA etc)
• Select the desired Test function by switching the
‘Test’ switch (Default = ‘OFF’).
• TEST’ (ON) Position:
• Test function is selected.
• Test terminal (terminal number 4 of Smart probe) is
used as an input to the unit.
• The test function allows you to check the
functionality of the unit.
• Applying a ground wire to the Test terminal will
change the state of the relay. It will hold this state
until the ground is removed, then it will change
back to the standard running mode.
• If the unit was in a Fail mode then the relay will not
change status.
• ‘OFF’ (Default) Position:
• Fail safe output function is selected.
• Test terminal (terminal number 4 of Smart probe)
will function as an open drain drive.
• This can be used to drive a relay or an active low
PLC input to detect a Fail condition.
• In normal operation mode the Test terminal will
output Zero Volts (Short to GND).
• In Fail or unpowered mode the Test terminal will be
open circuit.
See page 14 for further information.
Setup Procedure
Gladiator Conductivity Switch Series
*Setting of different time ranges for the delay
potentiometer for ON delay and OFF delay is possible
using a PC connected via GosHawk2 software. By
default, both will have the same time adjustment range
(20 sec max) and adjustment will result in equal ON
delay and OFF delay.

16
Setup Procedure
Gladiator Conductivity Switch Series
Remote Functionality Layout
remote
Signal
STATUS
1 2 3 4 5 6 7 8 9 10
8
9
8
9
Calibrate button
Down button
Up button
Relay status LEDs 1 and 2
Run button
Removable terminal block - plug in type
CAL
RUN
RELAY 1 RELAY 2 STATUS A STATUS B
3
REMOVABLE REMOTE PROBE TERMINAL BLOCK
7.1. 2. 3. 4. 5. 6. 8. 9. 10.
RED
WHITE
BLUE
BLACK
Display (LCD with backlight)
Terminals 1, 2, 3, 4, 9, 10 not used.
1
2
3
4
5
6
7Status LEDs A and B
- Status A flashes with probe to amplifier communications
- Status B has no function in this product
1
4
2
567
GREEN LED: Power / Status
Blinks every 1/2 second to indicate that functioning
is correct and no medium is detected.
LED on continuously indicates correct functioning and media is detected.

17
Setup Procedure
Gladiator Conductivity Switch Series
Remote Version
1. Mount the unit in its actual position.
(See mounting procedure - page 6-7)
• Make sure that external ground wire is connected
between the outside ground screw on the Gladiator
housing and the roof/wall/side of the silo/tank/
vessel/chute (for non metallic tanks make sure that
external ground wire is connected between the
same outside ground screw on the housing and the
general plant ground potential.).
2. Check where the actual level is relative to
the probe.
• Make sure that product is not touching the probe
- ideally it needs to be > 500mm away (if the silo/
vessel/tank/chute is very small you must ensure that
the material is as far away as possible - it must not
be touching the probe).
3. Turn the power on
• The display will turn on and the failsafe relay will
switch.
• The display will scroll through the following
messages: Hawk, Amp SerialNo, Type, Amp Soft
Ver, Device ID, SensorSerial, SensorModel, Sens
SoftVer, Sensor Addrs, Gladiator System Amp.
• The unit will then go into operational mode
displaying ‘Switch’ with a % value. This % value
represents the changing admittance reading.
4.Simple“1-minute”Setup-Followtheowchart
QuickSet
Cal Mounting
Yes / No
Relay Action
FailSafe Hi
UnLock
0
Sensor Value
0.0%
CAL
CAL
Press
Press
CAL
CAL
CAL
Press
Press
Press
Press CAL
CAL
Press
CAL
CAL
CAL
RUN
Press
Press
Press
Press
Twic e
Switch Point
50%
Delay Adjust
0.1S
Yes
50%
0.1S
FailSafe Hi
FailSafe Low
Select the Switch point (sensitivity)
The output relay will switch at the entered % value. The default value of 50% will be suitable
for detecting most media. For detection of products having low conductivity, select a lower %
value and vice versa. A higher % value will require a more conductive product. When the level
falls the relay will switch back at half of the entered switch point % value (when the liquid no
longer touches the probe).
Select the Time Delay
Set the time to be used for both switch on and switch off delays (default: 0.1 seconds).
Maximum Delay is 40 seconds.
Cancel Influence of Mounting
Do not proceed with this step unless the product is not touching the probe or probes.
Select ‘Yes’ to start the mounting calibration. ‘Wait’ will be displayed during the calibration for
up to 30 seconds.
Unit is now able to cancel the influence of the mounting. The % reading has been zeroed with
the existing process conditions and probe history log has been cleared.
Select the required relay action
The Relay can switch ‘ON’ or ‘OFF’ as the product approaches the probe and switch ‘ON’
or ‘OFF’ in response to an instrument failure. For details see page 10. Set the parameter to
FailSafe Low or FailSafe Hi depending on your requirements.

18
Gladiator Conductivity Switch Series
Software Menu
RemoteAmplier
Entering Data
All software adjustments are achieved via the four PUSHBUTTONS on the front panel.
In Run Mode
(A) Press and hold - interrupts normal operations and allows access to software menu
headings.
In Calibrate Mode
(B) Steps into a menu selection to allow editing (down one level)
(C) Saves selected value and moves onto the next menu item.
In Run Mode
(A) Scrolls up through operating diagnostics on display LCD.
In Calibrate Mode
(B) Scrolls up through software parameters when browsing the menus.
(C) Increases display value when editing a parameter.
In Run Mode
(A) Scrolls down through operating diagnostics on LCD display.
In Calibrate Mode
(B) Scrolls down through software parameters when browsing the menus.
(C) Decreases display value when editing a parameter.
In Run Mode
(A) Hides diagnostics if they are in view and returns to the standard running display.
In Calibrate Mode
(B) Steps out of a menu or selection (up one level). Parameter value will be stored
automatically when stepping up.
(C) Returns to running mode from the top level menu.

19
Software Tree
Software version 7.14
QuickSet Advanced
To Calibrate
UnLock
0
Sensor Value
0.0%
Advanced Menu
covers less commonly
used or advanced
parameters.
CAL
CAL
Press
Press
QuickSet Menu
covers all parameters
required for standard
setups.
On first start up there is
no security code protection.
Press
CAL
Press
To QuickSet
flow chart CAL
Press
To Advanced
flow chart
Normal Running Display
Press to view unit
operation diagnostics
to return to normal operation
RUN
Press
(see page 22) (see page 23)
Flow Chart
Gladiator Conductivity Switch Series

20
Flow Chart
Gladiator Conductivity Switch Series
Quickset
Relay 1 will switch at the entered Switch Point
value and switch back at half of this
value. Manual will be displayed if you
have set the parameter ‘Switch Mode’ to Manual in
Advanced menu. The Manual setting can only be
removed or adjusted from the Advanced menu.
CAL
CAL
Relay Action
FailSafe Hi
Lock Code
0
Relay Action (FailSafe Hi or FailSafe Low)
CAL Set switch delay time 0.1-72.8sec
Security code lock
Adjustable 0-200
Default 0
CAL
Calibrate mount will cancel the mounting influence
and zero the % reading with the existing process
conditions. Probe history log will be cleared.
Vessel must be empty before calibration. Yes / No
CAL
Default values/settings in bold and underlined
QuickSet
Switch Point
75%
Delay Adjust
2.0S
Cal Mounting
No
CAL
CAL
CAL
CAL
CAL
CAL
*When CAL is pressed ‘ edit’ will flash on the
bottom line of the display for a short time to indicate
that the parameter is being opened for editing.
(see page 10)
Table of contents
Other Hawk Switch manuals
Popular Switch manuals by other brands
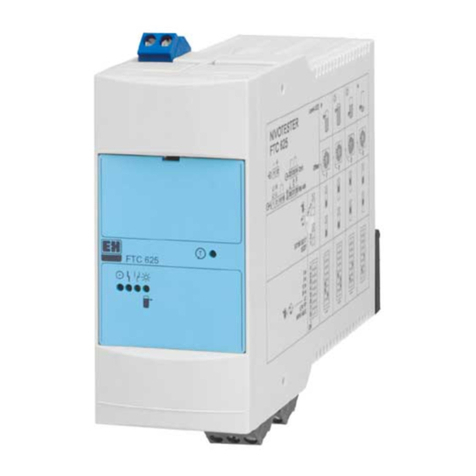
Endress+Hauser
Endress+Hauser Nivotester FTC625 operating instructions
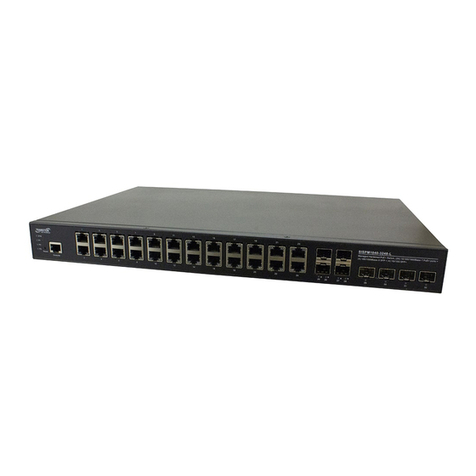
Lantronix
Lantronix SISPM1040 L3 Series Web user guide
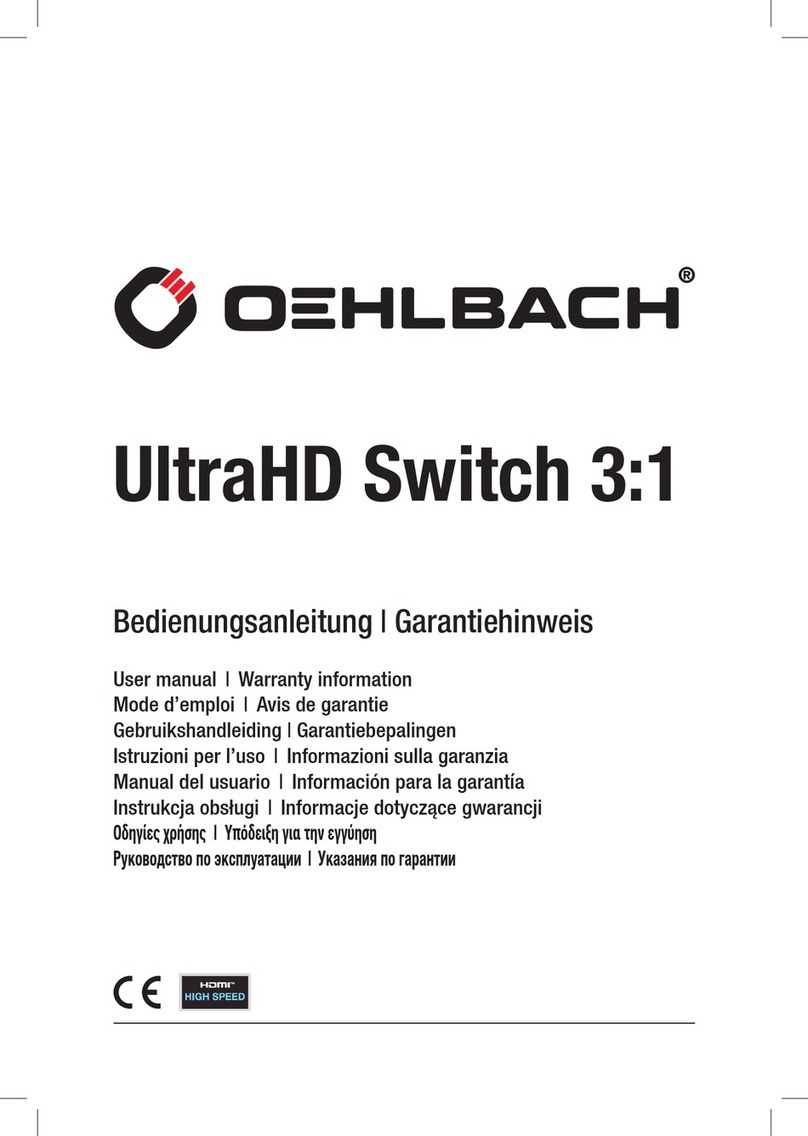
Oehlbach
Oehlbach UltraHD Switch 3:1 user manual
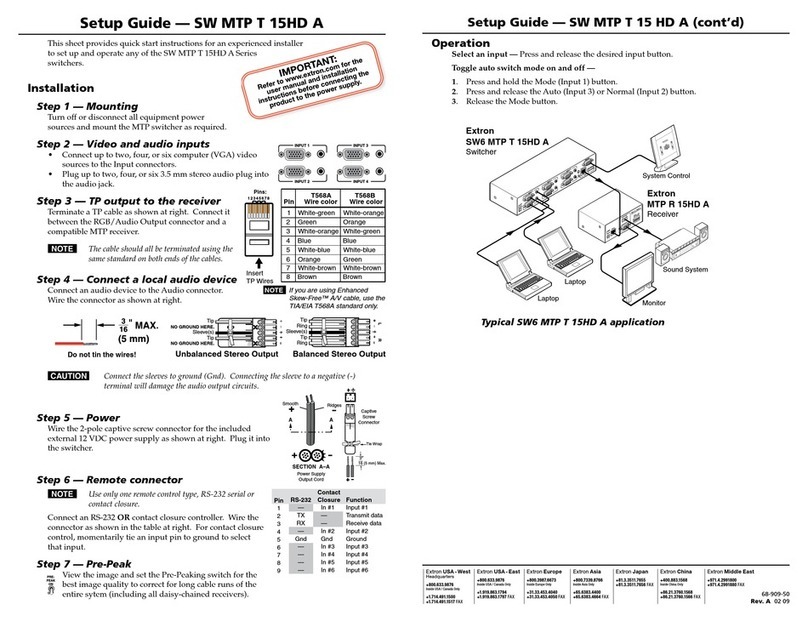
Extron electronics
Extron electronics SW MTP T 15HD A Setup guide

epico
epico 6in1 Aluminium Hub 8K manual
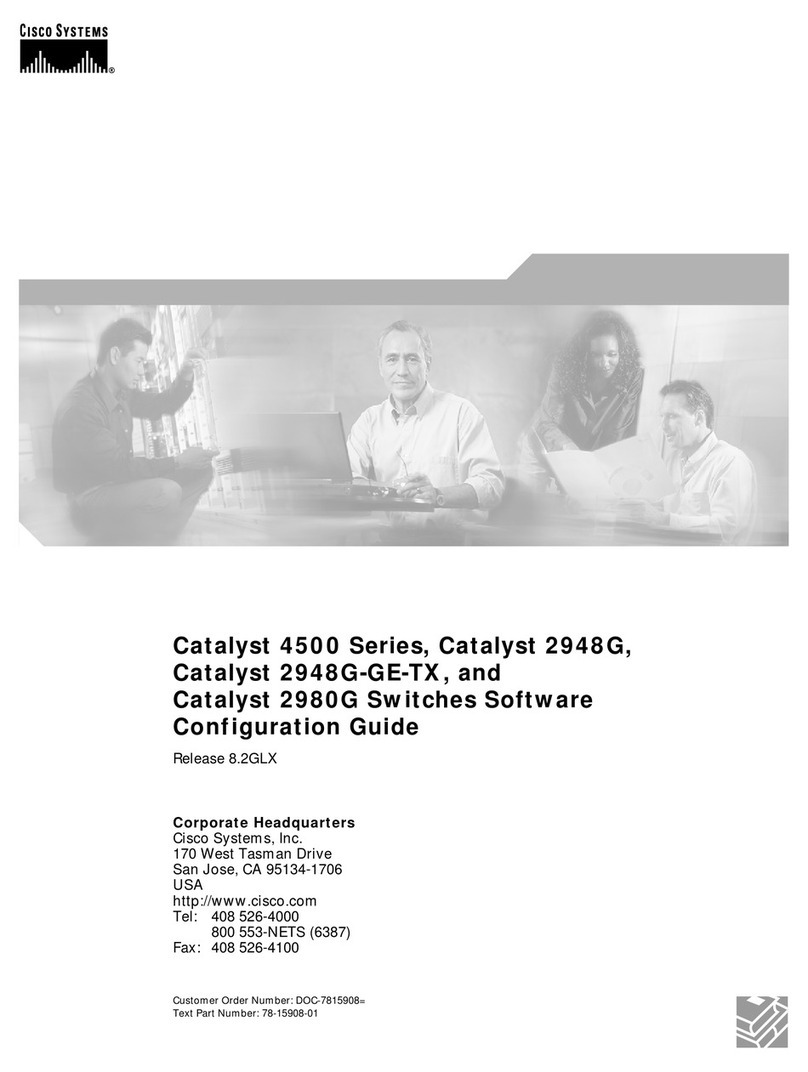
Cisco
Cisco WS-C2948G-GE-TX Configuration guide
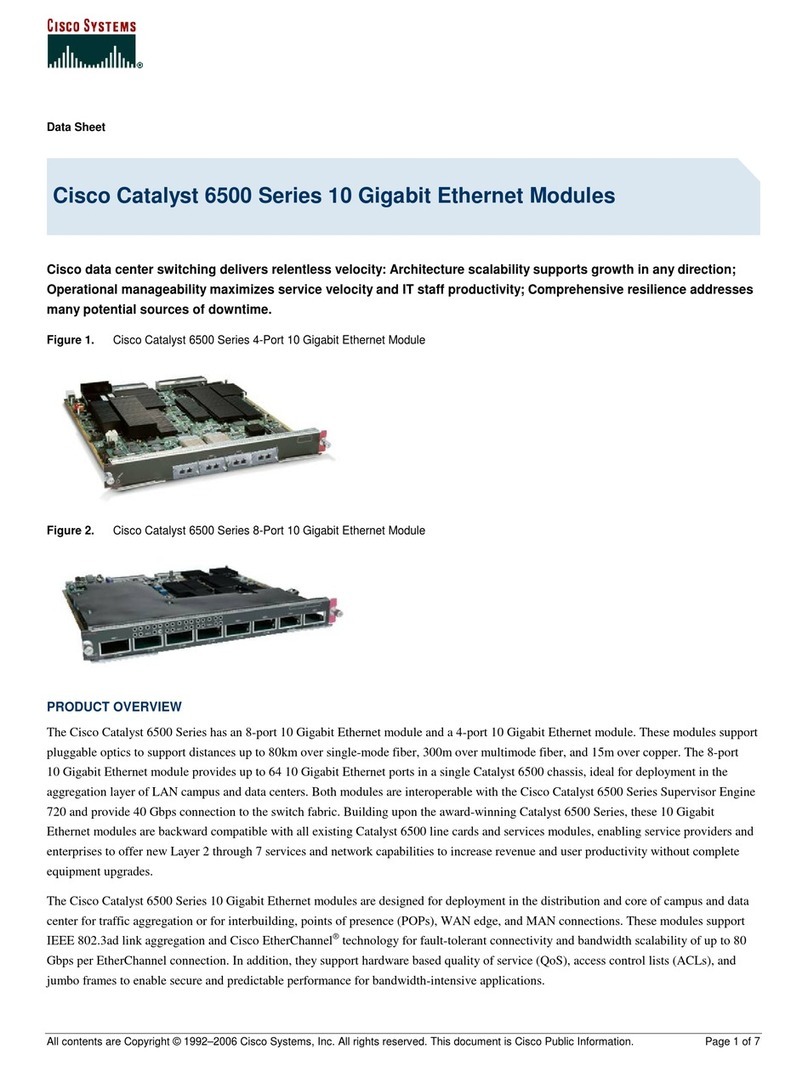
Cisco
Cisco Catalyst WS-X6704-10GE datasheet
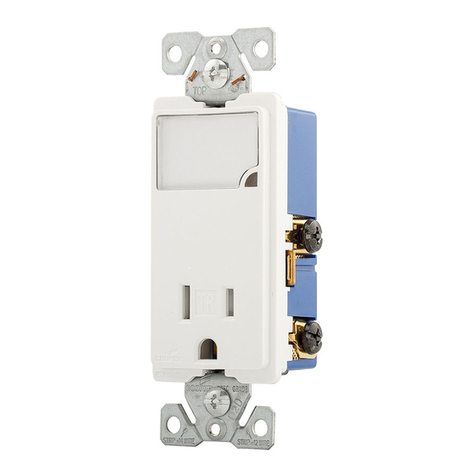
Eaton
Eaton TR7735 manual
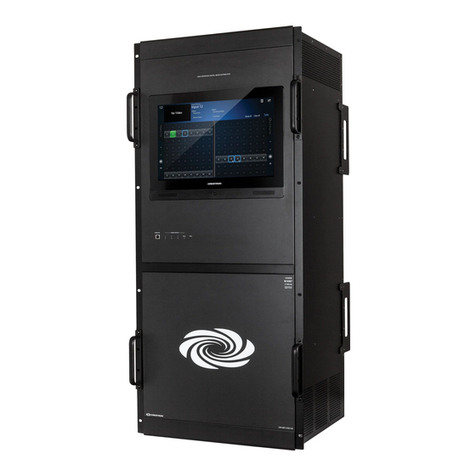
Crestron
Crestron DigitalMedia DM-MD64X64 Supplemental guide
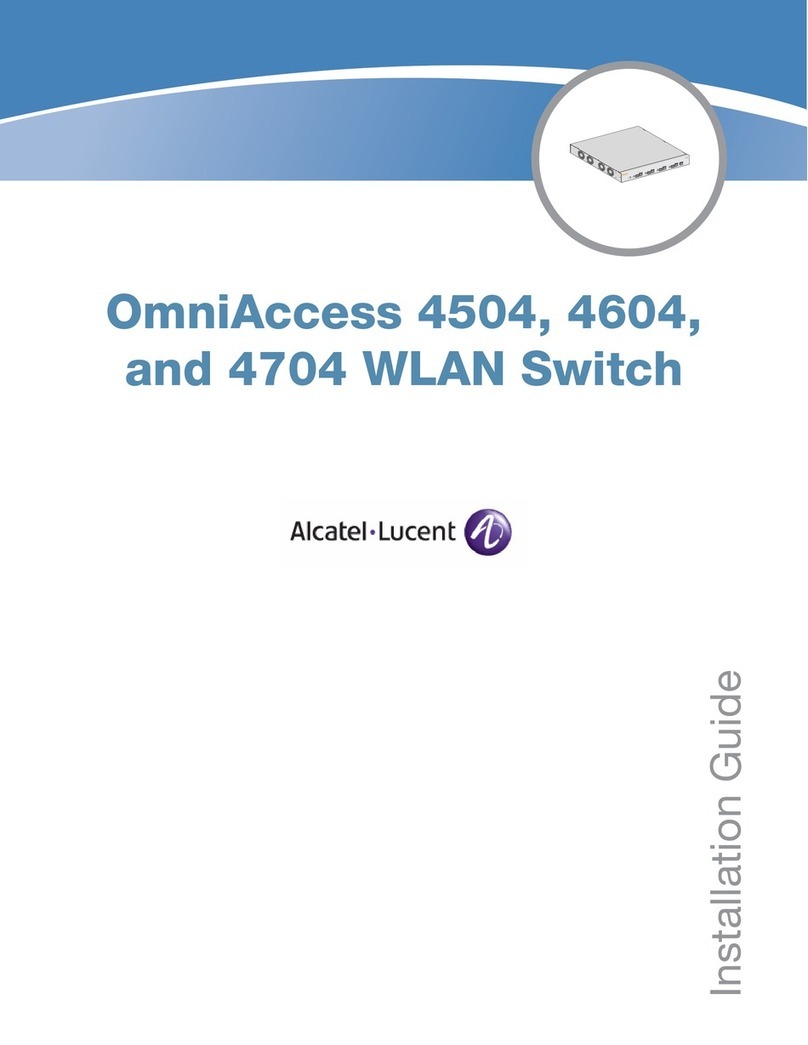
Alcatel-Lucent
Alcatel-Lucent OmniAccess 4504 installation guide
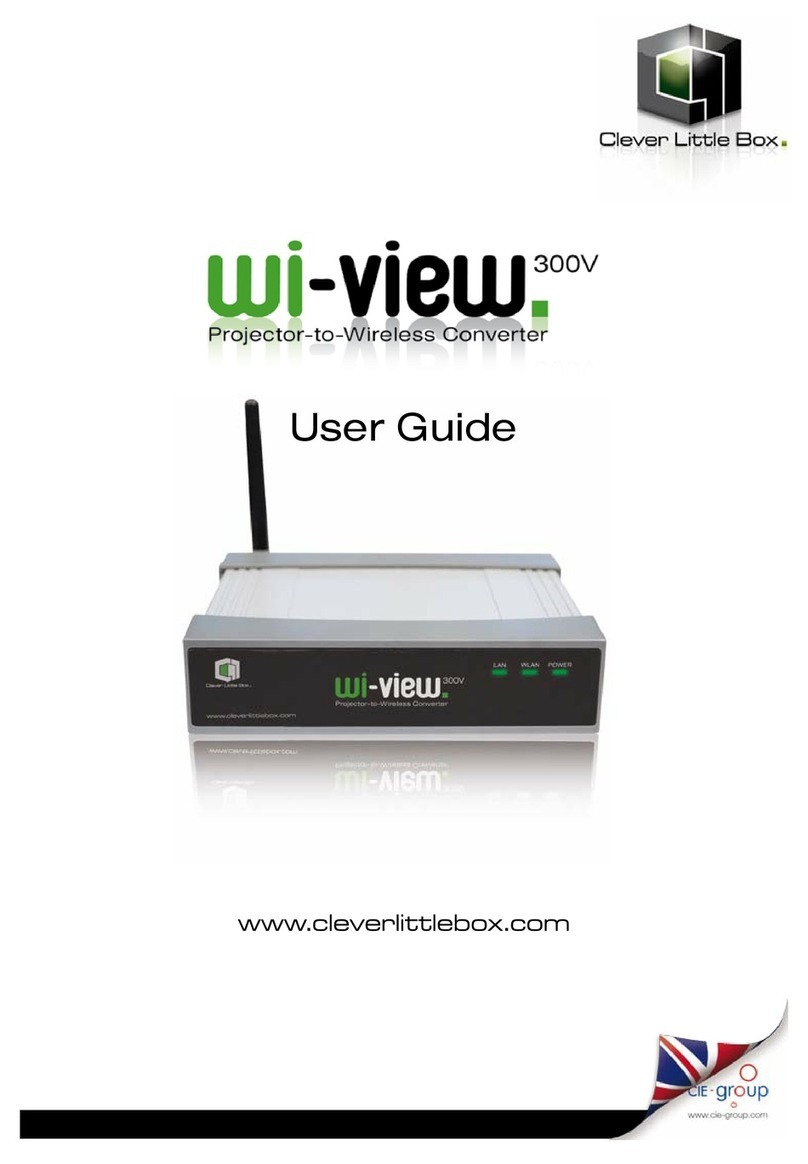
Clever Little Box
Clever Little Box Wi-View 300V user guide
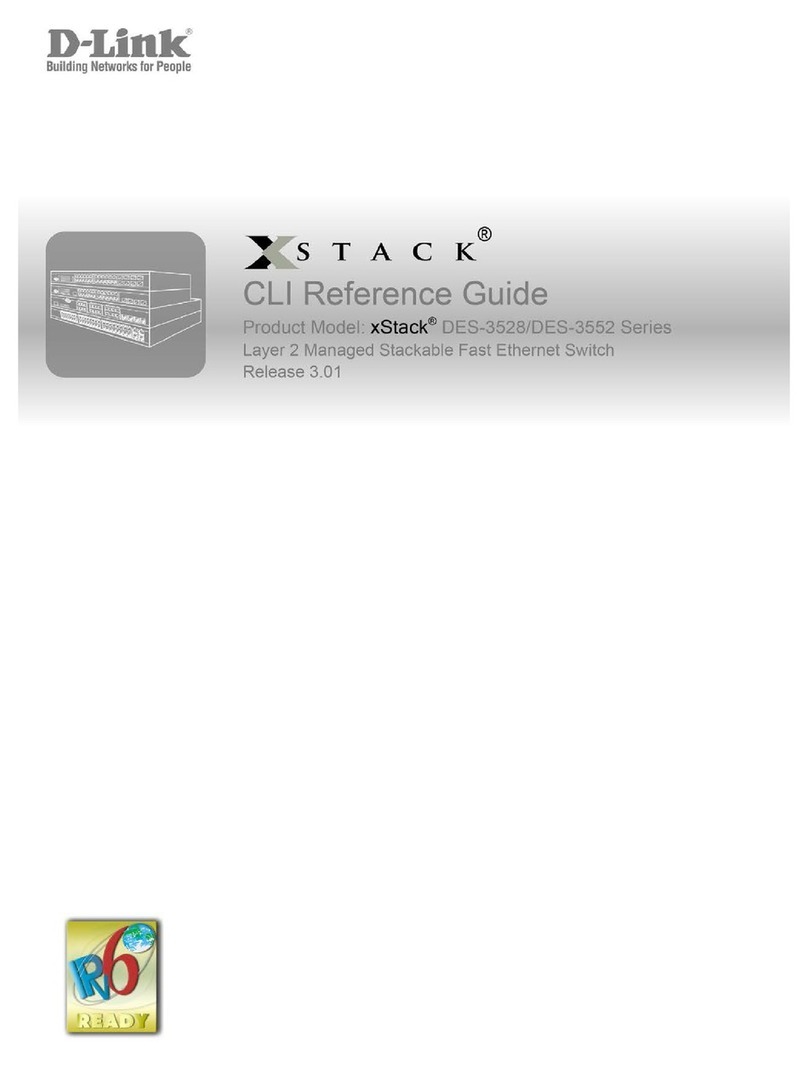
D-Link
D-Link DES-3528 - xStack Switch - Stackable Cli reference guide