Hawk Gladiator User manual

Sultan Sonar Manual Rev 1.0
A Higher Level of Performance
www.hawkmeasure.com
For more information, please visit >
Gladiator
Acoustic Switch Series
Manual

Table of Contents
2
Contents
Overview 3
Principle of Operation 3
Typical Uses 3
Function 3
Features 3
System Components 4
Remote Amplifier 4
Junction Box 4
Acoustic Switch Remote Transducers 4
Wiring 5
Gladiator Amplifier 5
HAWK AWRT-JB-01 Junction Box 5
Transducer Cable Extension 6
Dimensions 7
Remote Amplifier 7
Remote Transducer with UHMW Sleeve 7
AWRT-JB Junction Box 7
Mounting Dimensions 8
Blocked Chute Mounting 8
Minimum Range 8
HAWK FA4A-4 Flange 8
Mounting Instructions 9
Flush Mount 9
Setup Procedure 10
Facia Controls 10
Setting Maximum Range 12
Flow Chart 13
Software Tree 13
Diagnostics 14
Quickset Flow Chart 15
Quickset Parameters 16
App Type 16
Advanced Menu Flow Chart 17
Advanced Menu Parameters 18
Maintenance / Cleaner 19
Concept 19
Troubleshooting 20
Error Codes 20
Transducer Re-initialisation 21
Part Numbering 22
Remote Amplifier 22
Junction Box 22
Mounting Flange 22
Extra Cable (Length in metres) 22
Remote Transducer 23
Specications 25
Gladiator Acoustic Switch Series
PROPRIETARY NOTICE
The information contained in this publication is derived in part
from proprietary and patent data. This information has been
prepared for the express purpose of assisting operating and
maintenance personnel in the efficient use of the instrument
described herein. Publication of this information does not convey
any rights to use or reproduce it, or to use for any purpose
other than in connection with the installation, operation and
maintenance of the equipment described herein.
WARNING
This instrument contains electronic components that are
susceptible to damage by static electricity. Proper handling
procedures must be observed during the removal, installation, or
handling of internal circuit boards or devices:
Handling Procedure:
1. Power to unit must be removed prior to commencement of
any work.
2. Personnel must be grounded, via wrist strap or other safe,
suitable means, before any printed circuit board or other
internal devices are installed, removed or adjusted.
3. Printed circuit boards must be transported in a conductive
bag or other conductive container. Boards must not be
removed from protective container until the immediate time of
installation. Removed boards must be placed immediately in a
protective container for transport, storage, or return to factory.

Overview
Principle of Operation
The Gladiator Acoustic Switch uses Acoustic Wave technology in a new Sender / Receiver form for blocked
chute detection and anti collision for heavy machinery. The Gladiator Amplifier powers two Transducers
which use special HAWK developed software where both units pulse & receive each others Acoustic echoes.
When the path between the Transducers is blocked the units immediately detect the presence/absence
change of the return signal and trigger a communications relay for indication or control purposes.
HAWK’s Acoustic Wave Transducers are self cleaning. The Acoustic Switch is designed for continuous
operation in dusty, wet environments where other technologies fail. The power of each pulse (pressure wave)
blows the water, moisture & build-up off the face of the diaphragm.
• No contact with the product required
• Self cleaning Transducers
• Heavy duty titanium version available
• Designed for dusty, wet environments
• LCD setup/diagnostics on remote amplier
• Blocked chute ranges up to 15 meters (50 ft)
• Simple ‘1-minute’ setup
• 2 Relay outputs
• Remote test function
• Adjustable ON and OFF delays
• Communication options: GosHawk, Modbus, HART,
Probus DP, DeviceNet
• Remote GSM connection option & support
• Remote Amplier to Transducer separation up to
500 meters (1640 ft)
Typical Uses
• Blocked chute detection in wet or
dry environments
• Wet screen blocked chute detection
• Nucleonic/tilt switch replacement
• Hi level alarm / Low level alarm
• Truck/machine detection
(ROM bins, Primary Crusher Dump Pockets)
• Sewage sludge handling
Features
3
Gladiator Acoustic Switch Series
Function
Detection of objects or material between two points. Can be used for blockage detection, barrier detection,
machine detection / protection and point level detection.

System Components
4
RemoteAmplier
Gladiator Acoustic Switch Series
CAL
RUN
Junction Box
AcousticSwitchRemoteTransducerslabeledTD1andTD2withUHMWushmountsleeve
FA4A4”ANSIstandardange
Acoustic Switch Remote Transducers
Transducer
Transducer
RED
BLACK
BLUE
WHITE
RED
BLACK
BLUE
WHITE
RED
BLACK
BLUE
WHITE
Transducer
Transducer
RED
BLACK
BLUE
WHITE
RED
BLACK
BLUE
WHITE
RED
BLACK
BLUE
WHITE

Wiring
5
GladiatorAmplier
Gladiator Acoustic Switch Series
HAWK AWRT-JB-01 Junction Box
Relay 1 - Output Relay
Relay 2 - FailSafe Relay
TRANSDUCER 1 TRANSDUCER 2
AMPLIFIER
Connect colour to colour
RED
BLACK
BLUE
WHITE
RED
BLACK
BLUE
WHITE
RED
BLACK
BLUE
WHITE
+–
A
1L
+
–
N
B
RED
BLACK
BLUE
WHITE
Is
SENSOR DC-In AC-In*4-20mA (N/A)
COMMS
SLAVE IN
MASTER OUT
TEST IN
RELAY 1
NC
COM
NO
RELAY 2
NC
COM
NO
1 2 3 4 5 6 7 8 9 10 11 12 13 14 15
16 17 18 19 20 21 22 23 24 25 26 27 28 29 30
Use long nose pliers to
extract terminals
*AC-In is replaced by 36-60VDC
with Power Input Option ‘C’.

Wiring
Gladiator Acoustic Switch Series
6
OPTIONAL
JUNCTION
BOX
(for cable extension)
All cable shields
connect to
BLACK WIRE
at transmitter end
Cable
Shield
Re-connect
Cable Shield
to at AWRT-JB
Hawk Junction Box
‘Black’ terminal
TRANSDUCER
Seperate
Black/Shield
WHITE
BLUE
BLACK
RED
SHIELD
Cable Type
BELDEN 3084A
DEKORON IED183AA002
or quality shielded
instrumentation cable
TRANSDUCER 1 TRANSDUCER 2
AMPLIFIER
RED
BLACK
BLUE
WHITE
RED
BLACK
BLUE
WHITE
RED
BLACK
BLUE
WHITE
Transducer Cable Extension
Note: Cable length between Transducer and AWRT-JB Hawk Junction should not exceed 30m.
Additional cable extension should be the single cable run between AWRT-JB Junction Box 'Amplifier'
terminal and the Remote GSA Amplifier.

Dimensions
7
Gladiator Acoustic Switch Series
RemoteAmplier
14 mm (0.6”)
74 mm (2.9”)
78 mm (3.1”)
107 mm (4.2”)
111.5 mm (4.4”)
4 mm (0.2”)
50 mm (2”)
131.5 mm (5.2”)
7.5 mm (0.3”)
192.5 mm (7.6”)
141.5 mm (5.6”)
190 mm (7.5”)
182.5 mm (7.2”)
147 mm (5.8”)
167.5 mm (6.6”)
147 mm (5.8”)
30.7 mm (1.2”)
158 mm (6.2”)
108 mm (4.3”)
190 mm (7.5”)
174 mm (6.9”)
192.5 mm (7.6”)
182.5 mm (7.2”)
30.0
20.2
33.029.029.033.0
16
.2
350mm
13.8”
350mm
13.8”
100mm
75mm 3”
15kHz
See ‘blocked chute mounting’ for
sleeve dimensions
Remote Transducer with UHMW Sleeve AWRT-JB Junction Box
RED
BLK
BLUE
WHIT
RED
BLK
BLUE
WHIT
RED
BLK
BLUE
WHIT
AMP TX1 TX2
8mm
Open
170mm
80mm
3 x M20 x 1.5
or 3/4” NPT adaptor
Top
87mm
Closed (side)
Hawk
AWRT-JB Junction Box Dimensions
4mm
Bottom
150mm
60mm

8
Blocked Chute Mounting
Mounting Dimensions
Gladiator Acoustic Switch Series
4” ANSI FLANGE
D
A B
C*
STANDARD 4” ANSI FLANGE DIMENSIONS
FLANGE A (PCD) B (OD)
TYPE mm in. mm in.
C (ID)
mm in.
D (Hole)
mm in.
FA4A 190.5 7.5 228 9.0 100 4 19 0.75
SIZE
4”
UHMW
Sleeve
with O-ring
100.00mm
102.00mm
95mm
Locking Ring
Pipe
with
4” ANSI
interface
C* Interior diameter does not include HAWK’s
threaded decoupled connection flange
PipeSpecication
4-00” Z40 ID
100-102mm Black Pipe
Minimum Range
Min. 400mm
4” ANSI FLANGE
D
A B
C*
STANDARD 4” ANSI FLANGE DIMENSIONS
FLANGE A (PCD) B (OD)
TYPE mm in. mm in.
C (ID)
mm in.
D (Hole)
mm in.
FA4A 190.5 7.5 228 9.0 100 4 19 0.75
SIZE
4”
UHMW
Sleeve
with O-ring
100.00mm
102.00mm
95mm
Locking Ring
Pipe
with
4” ANSI
interface
C* Interior diameter does not include HAWK’s
threaded decoupled connection flange
HAWK FA4A-4 Flange

9
Mounting Instructions
Gladiator Acoustic Switch Series
Flush Mount
For vessels with falling product the transducers
should be installed out of the main product flow
where possible. For heavy falling product chutes the
titanium face version is recommended along with
welding a protective hood above each transducer (not
in front of). Avoid mounting immediately next to the
perpendicular wall.
The transducer has a specially designed UHMW seal
which must be flush with the vessel wall interior. It
should not be recessed. Pipe Specification: 4-00”
Z40 ID = 100mm Black Pipe. Ideally the transducer
should be a snug fit without excessive insertion force
required during installation.
The closest point of the mounting flange when
fully screwed on will be 95mm from the face of
the transducer. Take note that this 95mm should
theoretically be the flush mount point for the
transducer face in the vessel. HAWK’s flanges are
specially decoupled to reduce ‘noise’ created by
mounting related vibration.
Alignment - The transducers need to be as accurately
facing each other as possible. No special rotation
required. ‘Alignment’ software not required.
See page 7 'Blocked Chute Mounting' for mounting
dimensions.
CAL
RUN
RED
BLACK
BLUE
WHITE
TRANSDUCER1
TRANSDUCER2
AMPLIFIER
RED
BLACK
BLUE
WHITE
WHITE
BLUE
BLACK
RED
CAL
RUN
RED
BLACK
BLUE
WHITE
TRANSDUCER1
TRANSDUCER2
AMPLIFIER
RED
BLACK
BLUE
WHITE
WHITE
BLUE
BLACK
RED
CAL
RUN
RED
BLACK
BLUE
WHITE
TRANSDUCER1
TRANSDUCER2
AMPLIFIER
RED
BLACK
BLUE
WHITE
WHITE
BLUE
BLACK
RED
Min. 400mm

Setup Procedure
Gladiator Acoustic Switch Series
10
Facia Controls
GladiatorAmplier
CAL
RUN
RELAY 1 RELAY 2 STATUS A STATUS B
1
2
3
4
67
5
1
2
3
4
5
6
7
Calibrate button
Down button
Up button
Relay LEDs 1 and 2
Run button
Display (LCD with backlight)
Status LEDs A and B
Status A blinking indicates units are pulsing correctly.
Status B is not used
In Run Mode
(A) Press and hold - interrupts normal operations and allows access to software menu headings.
In Calibrate Mode
(B) Steps into a menu selection to allow editing (down one level)
(C) Saves selected value and moves onto the next menu item.
In Run Mode
(A) Hides diagnostics if they are in view and returns to the standard running display.
In Calibrate Mode
(B) Steps out of a menu or selection (up one level). Parameter value will be stored automatically
when stepping up.
(C) Returns to running mode from the top level menu.
In Run Mode
(A) Scrolls through operating diagnostics on display LCD.
In Calibrate Mode
(B) Scrolls through software parameters when browsing the menus.
(C) Changes display value when editing a parameter.
All software adjustments can be made by the push buttons on the amplifier facia.

11
Setup Procedure
Gladiator Acoustic Switch Series
1. Mount the unit in its actual position
(see mounting - pages 7-8)
2. Check where the actual level or target is
relative to the sensors.
Make sure that the material or target is not blocking
the path between the transducers.
4. Turn the power on
The display will turn on and the fail-safe relay will
switch. The display will scroll through the following
messages: HAWK, Amp SerialNo, Type, Amp Soft
Ver, Device ID, SensorSerial, SensorModel, Sens
SoftVer, Sensor Addrs, Gladiator System Amp.
The unit will then go into operational mode
displaying ‘Switch’ with a % value. This % value
represents the changing amount of signal
loss between the transducers.
If you see an error code, see ‘troubleshooting’.
5. Simple “1-minute” Setup - Follow the flow chart
!
QuickSet
Cal Mounting
Relay Action
Unlock
0
App Type
CAL
CAL
CAL
CAL
CAL
CAL
CAL
CAL
CAL
CAL
RUN
Switch Point
CAL
On Delay Adj
OffDelay Adj
CAL
CAL
Select the Switch point
• The output relay will switch at the entered % value.
• The default value of 75% will be suitable for detecting most media.
• For detection of lighter / fine products select a lower % value and vice versa.
• For heavy materials almost any setting will work a higher % setting may be required. When
the level or target falls below the sensors the relay will switch back on.
Select the Switch Time Delay
Set the delay time for the relay switching on and off.
Mounting Calibration
• Do not proceed with this step unless the material or target position is well beneath the line
between the sender and receiver.
• Select ‘Yes’ to start the mounting calibration.
• ‘Wait’ will be displayed during the calibration for up to 30 seconds.
• Unit is now able to cancel the influence of the mounting.
• The % reading on the back lit display has been zeroed with the existing process conditions
and the measurement history log has been cleared.
• Always CAL MOUNT after changing application type or moving the transducers.
Select the required relay action
The Relay action can be defaulted to either ‘ON’ or ‘OFF’ and switch ‘ON’ or ‘OFF’ in response
to an instrument failure.
• Failsafe High - Relay is energised during normal operation and de-energised during blocked
conditions or unit failure.
• Failsafe Low - Relay is de-energised during normal operation and energised during blocked
conditions or unit failure.
Choose Application Type
• Alignment - For transducer alignment at long range (boom protection applications)
• Blocked Chutes - Configures the unit for blocked chute applications.
• Boom Protection - For anti collision / machinery detection.
• Switch - Allows selection of Sensitivity% for standard switch application.
Note: If prompted to ‘re-calc app params’ this means the unit is already set to that app type -
the unit is asking if you wish to re-configure the settings.

12
Setting Maximum Range
Gladiator Acoustic Switch Series
• After a calibration the unit has a high & fluctuating switch%
• Check the echo distance diagnostic (while the unit is RUNNING, press down arrow until the top line
reads E: x.xx. If this value (distance) is double the approximate space between sensors or greater you
will need to adjust the ‘empty distance’ to restrict the maximum range.
• The setting is called ‘Empty Dist’ in the main menu labelled ‘Advanced’.
• Press CAL to edit, then the arrow to adjust this distance to 125% of the space between the sensors
(example, if there is approximately 4.00m between the sensors adjust this value to 5.00m).

13
Flow Chart
Gladiator Acoustic Switch Series
Software Tree
QuickSet Advanced
To Calibrate
UnLock
0
Sensor Value
0.0%
Advanced Menu
covers less commonly
used or advanced
parameters.
CAL
CAL
Press
Press
QuickSet Menu
covers all parameters
required for standard
setups.
On first start up there is
no security code protection.
Press
CAL
Press
To QuickSet
flow chart CAL
Press
To Advanced
flow chart
Normal Running Display
Press to view unit
operation diagnostics
to return to normal operation
RUN
Press

14
Diagnostics
Gladiator Acoustic Switch Series
While the unit is in RUN mode you can press to view information about current unit settings &
operating characteristics.
Signal 1.86V
0.0%
Current switch
delay time
Received Signal strength
Sensor Value
0.0%
Max/Min captured
Sensor Value % since
Last history log reset,
or last Cal Mounting
operation
Gain 10.2%
0.0%
Gain result of mounting
calibration
Noise 0.04V
0.0%
Background Noise received
Percentage below
which the Relay
will be in State 1*.
Percentage above
which the Relay
will be in State 2*.
}
Remote
0.0%
Device operating mode
Remote/Master/Slave
BlockedChute
Sensor Value
Current detected signal in %
0% full signal
100% all signal blocked
Sensor 1
E1Distance
Signa1
Recov1
Noise1
Gain1
Signal
Selected Application
Currently selected sensor for diagnostics
Press at the same time to switch
between sensor 1 & 2 (in this menu only)
Distance between sensors.
May be displayed as double or triple
value depending on chute conditions.
Signal strength in voltage.
2.5V max
Current recover gain% of sensor. Unit applies recover
gain to maintain maximum possible signal strength.
External noise interference % detected by sensor.
Value may fluctuate during inactive process & empty
chutes due to transducer ringing.
Total Gain% useage of sensor.
Calibrated starting gain + recover gain.
Average signal strength
beween both sensors.
2.5V max
Normal
Diagnostic
0%
Current sensor value
is always displayed
on 2nd line
Unit Status
Normal / CommRetry
Temp
Delay
Min
Max
SW Off
SW On
Ambient temperature
at sensor
Minimum recorded sensor
value % in log
Maximum recorded sensor
value % in log
Sensor value required
for switch off condition
Sensor value required
for switch on condition
Current switch delay
count down. Value will be
slightly lower due to
response time

Quickset Flow Chart
Gladiator Acoustic Switch Series
15
CAL
CAL
CAL
CAL
CAL
CAL
QuickSet
Cal Mounting
Relay1 Action
App Type
CAL
RUN
Switch Point
On Delay Adj
OffDelay Adj
Select application type
Alignment
Blocked Chute
Anti Collision
Switch
Calibrates unit gain to
current conditions
Yes / No
Switch point condition
Auto = default 75%
High value recommended
for blocked chutes.
Switch on time delay
Switch off time delay
Failsafe High - Relay1 is energised during normal
operation and de-energised during blocked conditions.
Failsafe Low - Relay1 is de-energised during normal
operation and and energises during blocked conditions.
Recalculate
App type?
CAL
If you re-select the existing app type
you will be prompted to confirm that
you wish to adjust existing settings
Yes / No
CAL Sensitivity
High value - Unit requires less signal
blockage to switch
Low value - Unit requires more signal
blockage to switch
Software Rev 7.41
Failsafe Conditions
• Power / Comms problems
• Transducer failure
• Transducers stop communicating

Quickset Parameters
16
Gladiator Acoustic Switch Series
Alignment
• For Aligning the unit in long range
(boom protection applications).
• Unit is set to 1.2V signal (~48% sw value).
• Move the unit face to get the sw value reading low
(0% indicates perfect alignment at current gain
setting).
• Calibrate & re-select this mode and repeat till you
cannot improve the alignment.
• This mode is only for alignment, not for an active
process.
Blocked Chute
• Configures the unit for blocked chute applications
Boom Protection
• Sets the unit to Boom Protection mode.
• This can also be used for machinery or object
detection
Switch
• For standard switch applications where blocked
chute or boom protection is not appropriate.
• A high value will make the unit more sensitive to
switching and responding to lighter materials.
• A low value will make the unit more resilient and
ignore dust / build up.
Cal Mounting
• Do not proceed with this step unless the material
or target position is well beneath the line between
the transducers.
• Select ‘Yes’ to start the mounting calibration.
• ‘Wait’ will be displayed during the calibration during
the procedure and the Status A & B lights will flash
while the unit is pulsing.
• The unit then performs a final check.
• The Cal Mounting process configures the system to
the optimum settings to achieve a 2.4V signal
(signal in volts viewable in the diagnostics).
Switch Point
Auto:
• The output relay will switch on at displayed %
value (default 75%) Auto settings will be suitable for
detecting most media.
• Adjusting the switch on % will automatically adjust
the switch off %.
• For blocked chute applications a higher % switch on
value is recommend such as 90%.
Manual:
• To adjust both switch point values see ‘Switch Mode’
in the ‘Advanced’ menu.
On & Off Delay Adjustment
• Set the time to be used for both switch on and
switch off delays (default: 1 second).
Relay1 Action
• Relay1 can be set to Low or High.
• When the Relay is in high mode it is always
switched on (EN) and will switch off (DEN) when
there is a blocked chute condition or unit failure.
• High is recommended.
• When in Low mode the Relay will be switched off
(DEN) during normal operation and will switch on
(EN) when there is a blocked chute condition or unit
failure.
App Type

17
Advanced Menu Flow Chart
Gladiator Acoustic Switch Series
Software Rev 7.41
CAL
CAL
CAL
CAL
CAL
CAL
Advanced
Relay2Action
ProbeAVG
Switch Mode
CAL
View Log
Reset Log
Comms Type
Failsafe - Relay2 is always energised and will de-energise
in the event of unit failure.
Relay2 - Relay will operate same as Relay1 setting.
Yes - Displays recently logged data
Yes - Resets logged data
Devicenet
Profibus
HART
Modbus
The number of pulses the unit uses to average the
display measurement.
Device ID
Baud Rate
CAL
Initilize TX
Yes / No
Run Transducer initialisation sequence.
See page 19 for further information on
transducer initialisation.
CAL
LoadDefaults
Yes / No
Restores the Transducer settings to factory default.
You will be prompted to seset each Transducer
individually. Load defaults does not reset TX address.
CAL
FieldBusAdds
Comms type
will not work without
correct module.
Different Comms types
display all or two of the
following.
Auto - Recommended setting
Manual - Manually select switch on & off % value
RUN
For Maintnce Chk, GainOpt Clng, TimeOpt Clng see ‘Maintenance/Cleaner’
Empty Dist
Distance (default 15.000m)
Sets the max possible range for the application.
Use if the system has calibrated to a longer echo
CAL

18
Advanced Menu Parameters
Gladiator Acoustic Switch Series
Switch Mode
• Switch mode alters the switch on/off display %
condition for the relay.
• Auto is the recommended HAWK default with switch
on at 75%.
• Manual mode allows you to specify the on & off %
condition.
Relay2Action
• The second relay can be set for failsafe conditions
or as another switch.
• Usually failsafe is the preferred option.
• The relay will always be switched on but will switch
off if there is a fail condition with the system.
Failsafe Conditions:
• Power / Comms problems
• Transducer failure
• Transducers stop communicating
• The second relay2 action is relay2.
• This programs the relay to mirror the action of
relay1.
• See ‘Maintenance/Cleaner’ on next page for
information about Maintnce Chk, GainOpt
& TimeOpt Cleaning
View Log
• View log displays the highest & lowest logged
values for the display % and temperature since the
last log reset.
Reset Log
• Clears the logged data.
Comms Type
• If your unit has an additional comms module
(Modbus is standard with switch only units) such as
DeviceNet, Profibus PA or HART you can
select and configure the address / ID / line speed for
the comms option.
Back Light
• The LCD back light can be switched on or off.
• The display will be bright green when switched on.
ProbeAVG
• This setting is similar to a ‘damping’ setting.
• The unit display reading will be an average of the
ProbeAVG figure.
• The figure is measured in transducer pulses.
• The default setting is 2.
• Increasing this setting will slow the unit response
time for switching and give a more stable switch %
value.
Initilize TX (see page 20)
• If you need to re-initialize the transducer address
connection sequence you can run this program.
• You will have the option to clear each transducer
address.
• If the transducers are already correctly addressed
within the amplifier the unit will cycle through and
display ‘found’ and then ‘too many transducers’.
• In this event press and hold RUN firmly to return to
the menus.
V In Chk
• V in Chk ensures the minimum required voltage for
unit operation (9.5V) is being supplied to the unit.
• If switched off the LCD will display ‘volt fail’ when
voltage drops below 9.5V.
• When switched on the unit will enter failsafe mode
and display volt fail when input voltage drops below
9.5V.
Empty Dist
• See ‘setting maximum range’ on Page 11
LoadDefaults
• Restores factory default settings to amplifier, sensor
1 and sensor 2.
• You will be prompted to set each individually.

19
Maintenance / Cleaner
Gladiator Acoustic Switch Series
• The Gladiator Amplifier has received a firmware
update to utilise the Relay 2 as a trigger mechanism
to notify the user or activate a cleaning system
based on time or conditions within the application
which require cleaning.
• There are three software options using two
different concepts. The first concept is based on
total Gain used and the second is based on a Time
interval.
• The options are located in the Advanced menu as a
sub menu for Relay2Action.
The selectable software options are as follows:
[Maintnce Chk]
• The unit will switch on the relay when total Gain is
greater than the CleanGainHigh % - the relay will
switch off when Gain falls below CleanGainLow %.
[GainOpt Clng]
• When total Gain exceeds the CleanGainHigh point
the unit activates the relay for 1/2 of the On Delay
time and then switches off.
• The unit will then count the Clean Time interval time
before repeat the process until total Gain is below
CleanGainLow point.
[TimeOpt Clng]
• At every Clean Time interval the unit will switch on
the relay for 1/2 of the On Delay time and
then switch off.
Setup Example - Gain Based
• In ‘Quickset’ Set ‘On Delay’ to 4.0 seconds - this will
provide a 2.0 second water blast.
• In ‘Advanced’ set ‘Relay2Action to ‘GainOptCln’ with
a ‘CleanGainHi’ of 80%, ‘CleanGainLo’ of 70% and
‘Clean Timer’ to 5.0min
• This will trigger the water spray for 2 seconds when
Gain goes above 80%.
• The spray will repeat every 5 minutes until Gain
goes below 70%.
• You can view Gain while the unit is running by using
the arrow key to locate the diagnostic display
Concept

Troubleshooting
Gladiator Acoustic Switch Series
20
Error Codes
Too Many Transducers
• This code can be displayed if both transducers are
already correctly initialised when run the Initialise
TX program. Press and hold the RUN button to exit
this code loop.
Com Retry
• Unit is attempting to communicate with a transducer.
Failed
• Unit has failed to communicate with both
transducers.
• Check amplifier & junction box wiring connections.
• Pull each wire to ensure they are locked in correctly.
Error No 01:
• Amplifier cannot communicate with transducer 1.
Error No 11:
• Amplifier cannot communicate with transducer 2.
Existing installation
• For both error codes 1 and 11 the first thing to check
is the amplifier & junction box wiring connections,
both HAWK and customer supplied if applicable.
• Pull each wire to ensure they are locked in correctly.
• Check sensor for damage.
New installations
• You may need to re-initialise the transducers.
• The re-initialisation sequence assigns each an ID
which the amplifier is looking to communicate with.
• The re-initialise program is in the ‘Advanced’ Menu.
• While an error code is on the screen you will need
to push and firmly hold the CAL button to access the
unlock screen. This may take 5-10 seconds.
Error 02:
• Amplifier can talk to transducer but transducer gives
incorrect response.
• This can indicate a communication data corruption
between Amplifier and Transducer.
• It can be a result of noise in data lines or one of data
lines (blue or white) being open circuit.
Error 03:
• A communications option in output adjustment has
been selected (eg Profibus, FF) but the module is
not present, connected or responding.
Error 04:
• Amplifier is programmed with incorrect software.
Error 08:
• Incorrect transducer - ensure connected transducer
is Acoustic Switch (AS).
Power Supply
• LCD / LEDs / Relays dimming or dropping out in
non-blocked conditions.
• The GSASUS when powered by AC will output a DC
voltage from the DC +/- terminals.
• You should read approx 16V stable from DC +/-
while under AC power. If your AC power is stable
and the DC is outputting a lower or unstable value
there is likely a problem with the internal AC power
supply.
• You can use a 24DC regulator and power the unit
via DC terminals.
• High / Inconsistence switch % after calibration
• See ‘setting maximum range’
Other manuals for Gladiator
5
Table of contents
Other Hawk Switch manuals
Popular Switch manuals by other brands
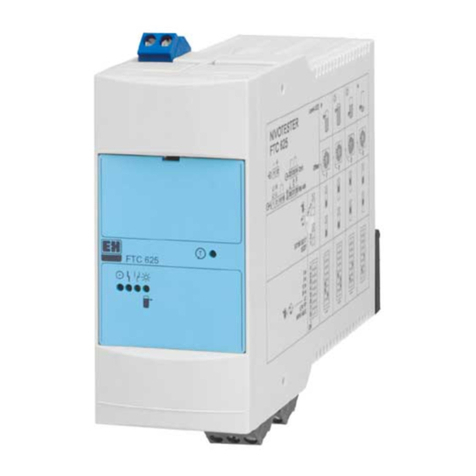
Endress+Hauser
Endress+Hauser Nivotester FTC625 operating instructions
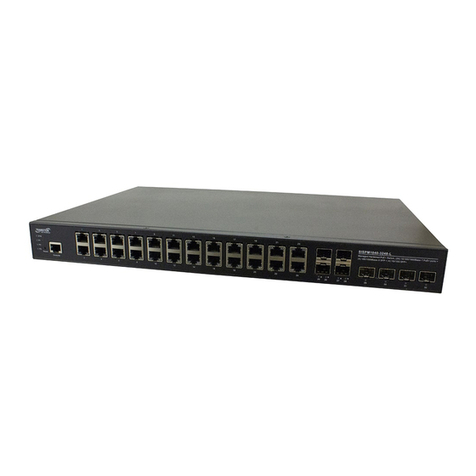
Lantronix
Lantronix SISPM1040 L3 Series Web user guide
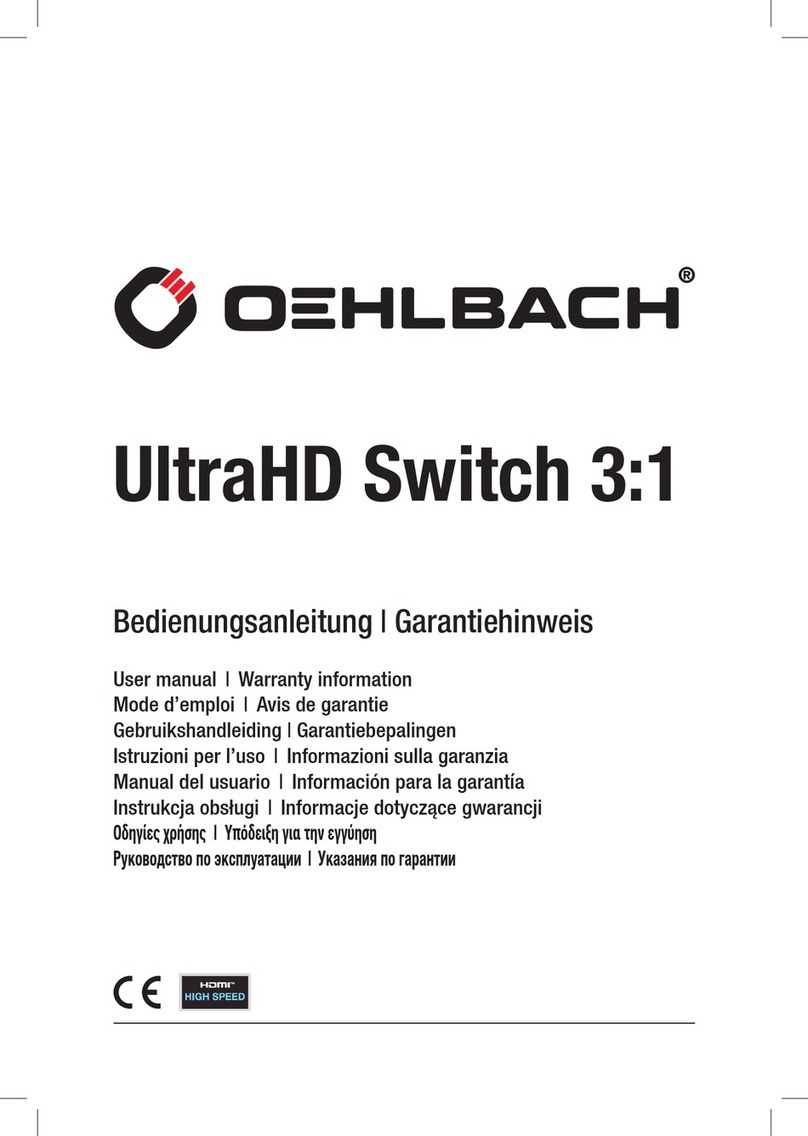
Oehlbach
Oehlbach UltraHD Switch 3:1 user manual
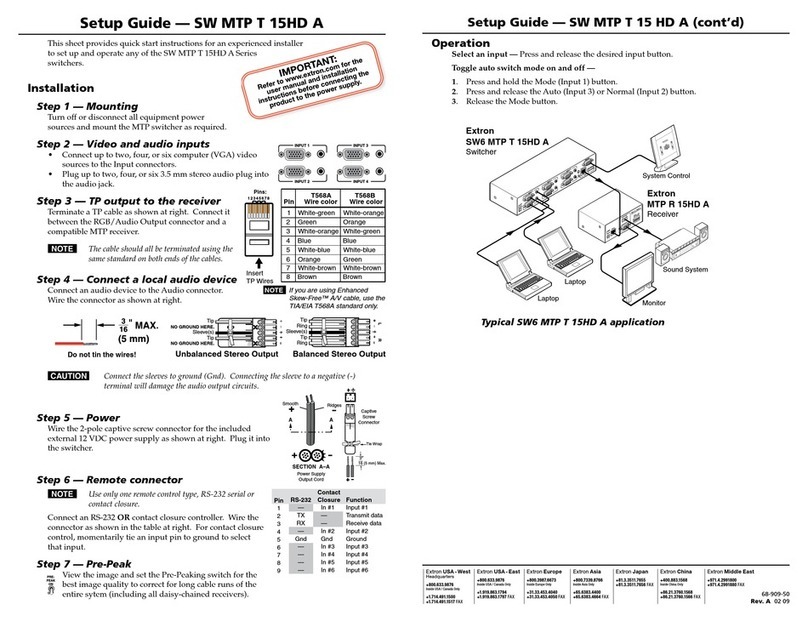
Extron electronics
Extron electronics SW MTP T 15HD A Setup guide

epico
epico 6in1 Aluminium Hub 8K manual
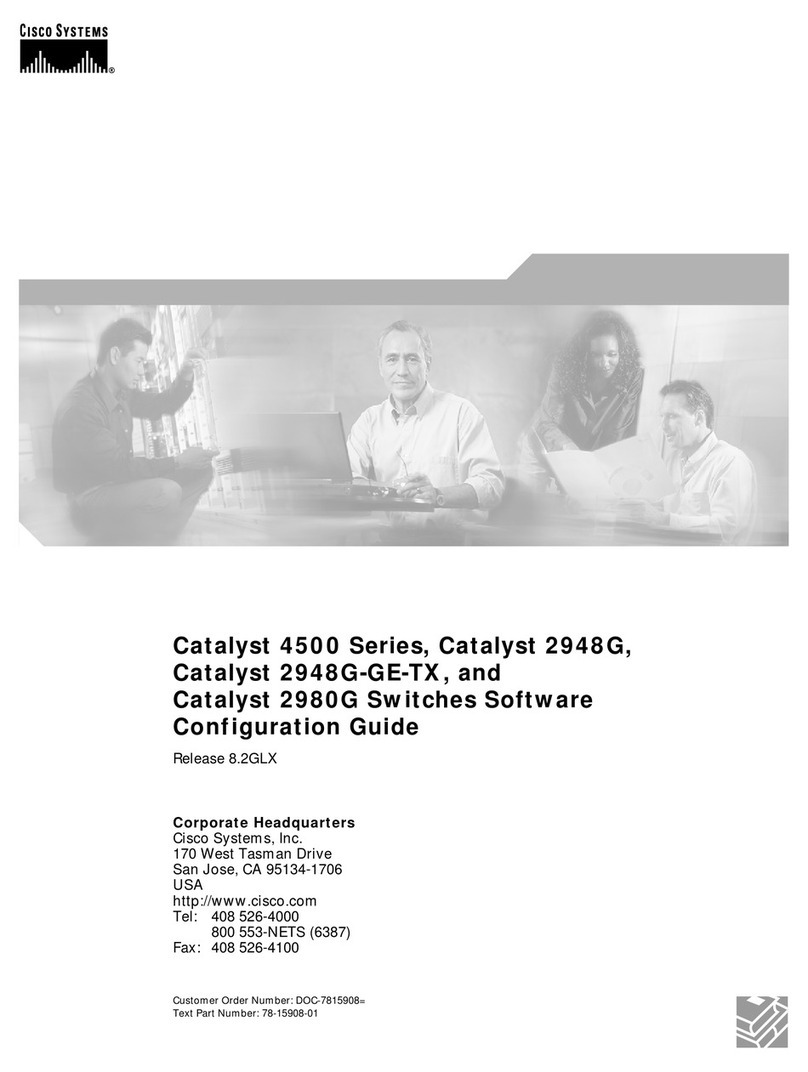
Cisco
Cisco WS-C2948G-GE-TX Configuration guide
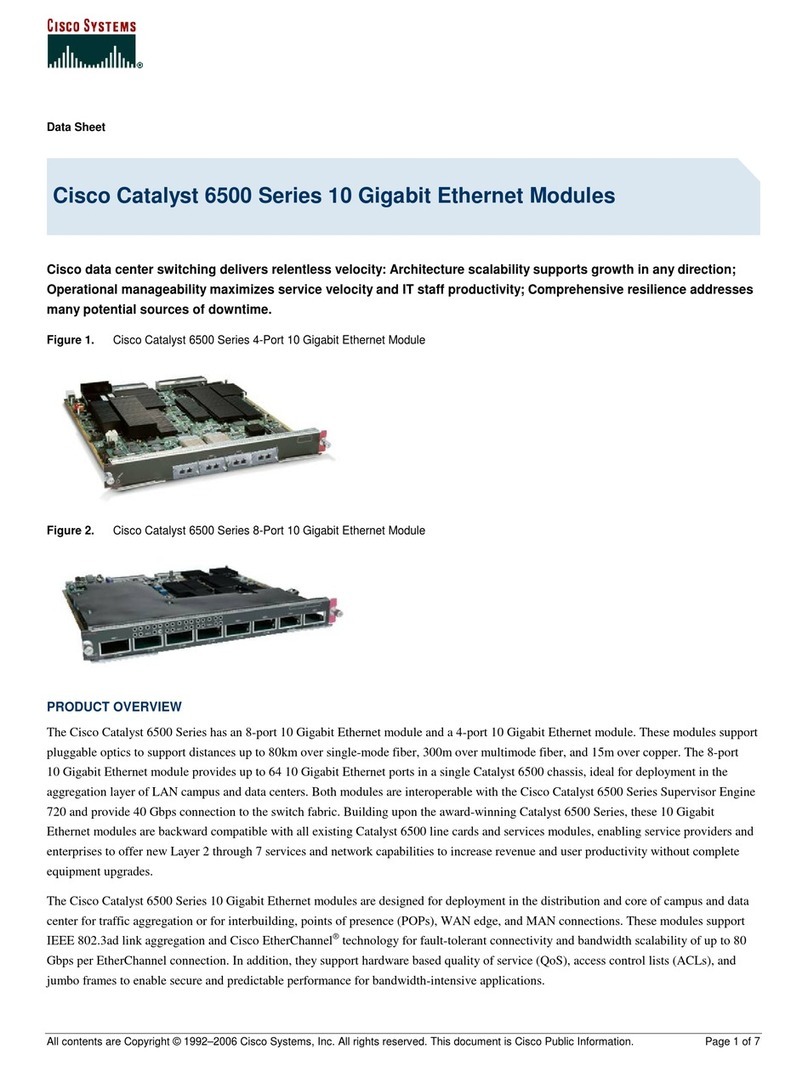
Cisco
Cisco Catalyst WS-X6704-10GE datasheet
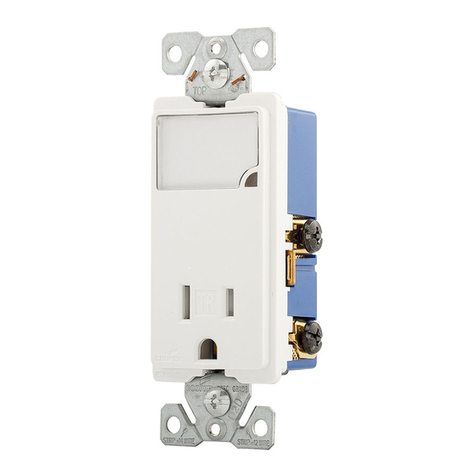
Eaton
Eaton TR7735 manual
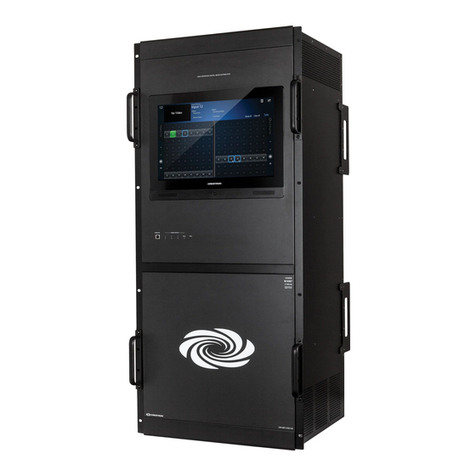
Crestron
Crestron DigitalMedia DM-MD64X64 Supplemental guide
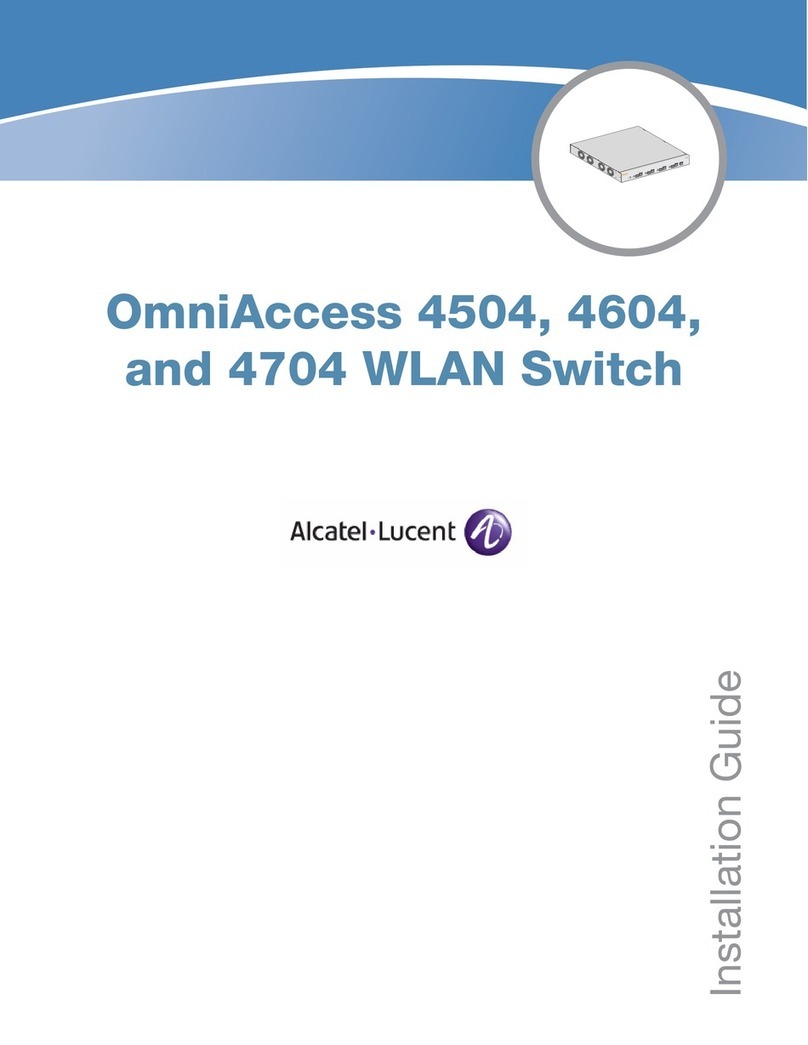
Alcatel-Lucent
Alcatel-Lucent OmniAccess 4504 installation guide
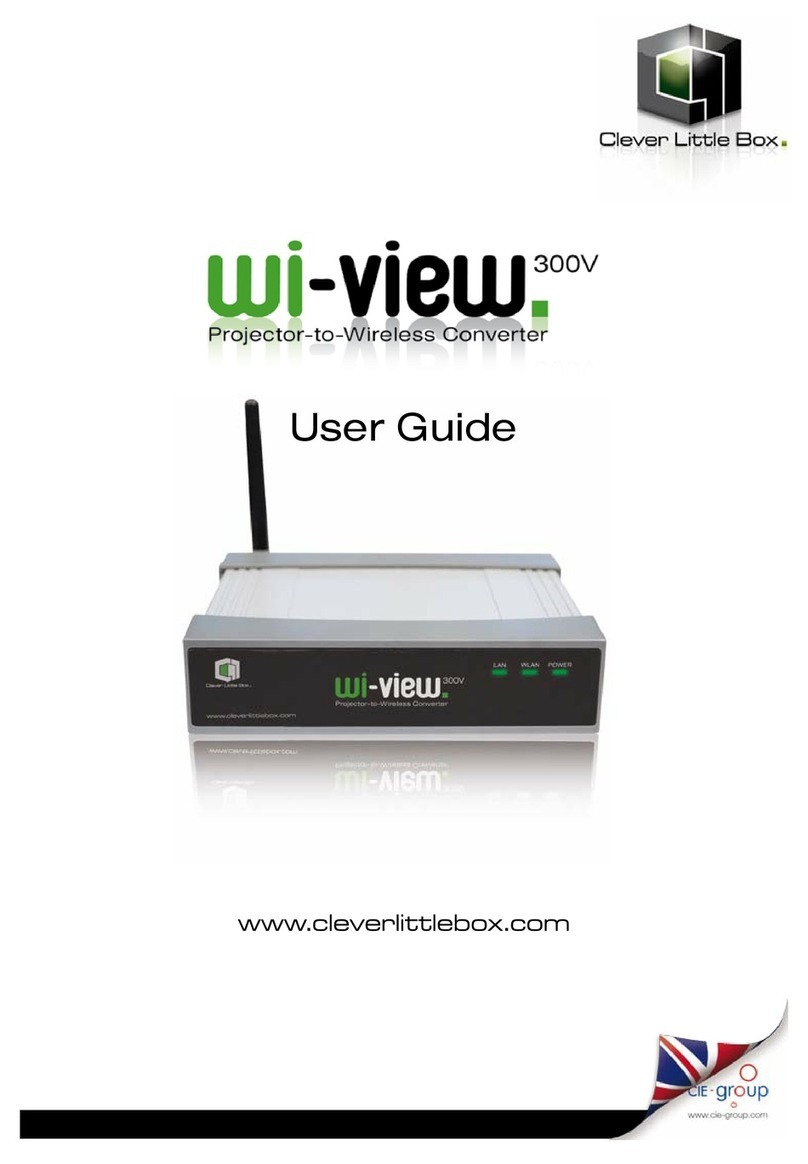
Clever Little Box
Clever Little Box Wi-View 300V user guide
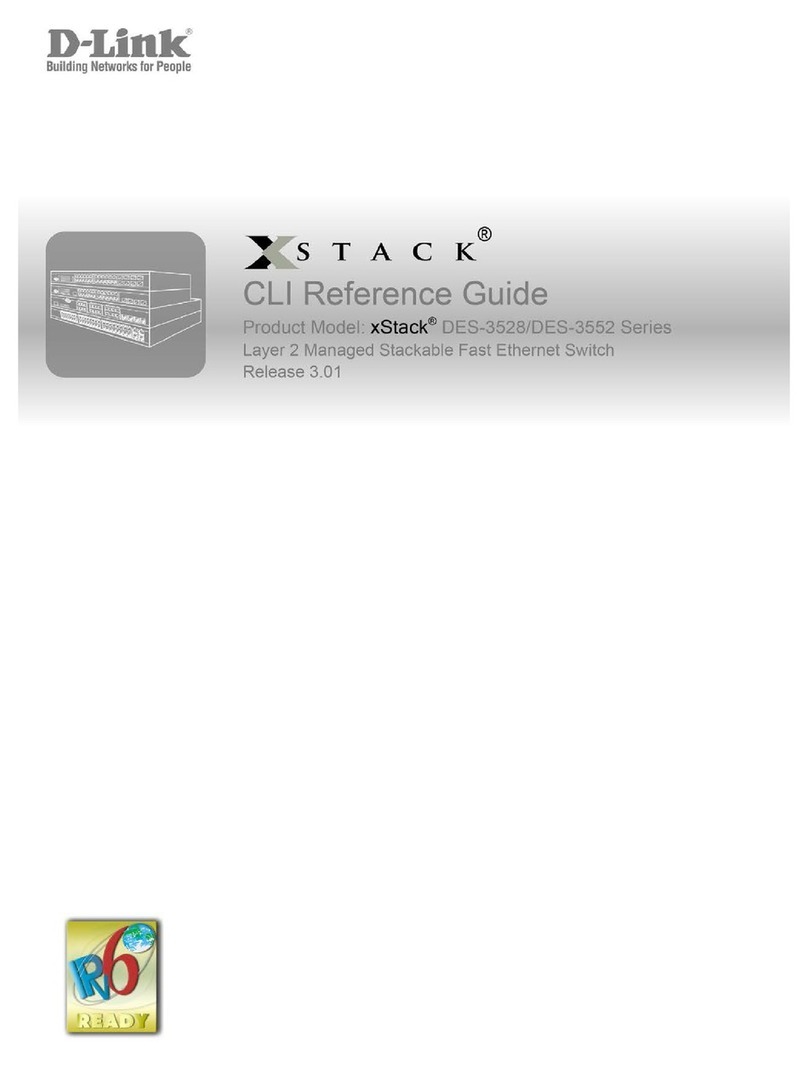
D-Link
D-Link DES-3528 - xStack Switch - Stackable Cli reference guide