Heathkit IT-12 User manual


HEATH COMPANY PHONE DIRECTORY
The following telephone number are direct lines into departments listed :
Kit order and delivery information
(616)982-3411
Credit
(616)982-3561
Replacement part
(616)982-3571
Technical assistance
R/C, Audio, and electronics organs
(616)982-3310
Amateur Radio
(616)982-3296
Test Equipment, Strobe lights, Calculators,
Clock, Weather Instruments
(616) 982-3315
Television
(616) 982-3307
Automotive, Marine, Appliances
Security, General Products
(616) 982-3496
YOUR HEATHKIT 90-DAY FULL WARRANTY
During your first ninety (90) days of ownership, Heath Company will replace or repair free of charge —as soon as
practical —any parts which are defective, either in materials or workmanship. You can obtain parts directly from
Heath Company by writing us or telephoning us at (616) 982-3571. And we'll pay shipping charges to get those
parts to you —anywhere in the world.
We warrant that, during the first ninety (90) days of ownership, our products, when correctly assembled,
calibrated, adjusted and used in accordance with our printed instructions, will meet published specifications.
If a defective part or error in design has caused your Heathkit product to malfunction during the warranty period,
through no fault of yours, we will service it free upon delivery at your expense to the Heath factory, Benton
Harbor, Michigan, or to any Heathkit Electronic Center (units of Schlumberger Products Corporation), or through
any of our authorized overseas distributors.
You will receive free consultation on any problem you might encounter in the assembly or use of your Heathkit
product. Just drop us a line or give us a call. Sorry, we cannot accept collect calls.
Our warranty, both express and implied, does not cover damage caused by use of corrosive solder, defective tools,
incorrect assembly, misuse, fire, customer-made modifications, flood or acts of God, nor does it include re-
imbursement for customer assembly or set-up time. The warranty covers only Heath products and is not extended
to non-Heath allied equipment or components used in conjunction with our products or uses of our products for
purposes other than as advertised.
And if you are dissatisfied with our service —warranty or otherwise —or our products, write directly to our
Director of Customer Services, Heath Company, Benton Harbor, Michigan, 49022. Telephone (616) 982-3524.
He'll make certain your problems receive immediate, personal attention.
HEATH COMPANY
BENTON HARBOR, Ml. 49022
Prices and specifications subject to change without notice
Numérisation, Pascal Chour, 01/2004 et 11/2005.

Page 1
ASSEMBLY AND OPERATION OF THE
HEATHKIT VISUAL-AURAL SIGNAL TRACER
MODEL IT-12
SPECIFICATIONS
Power Supply…………………………………………
Transformer operated
Power Requirements
117 volts AC, 50-60 cps, 25 watts.
Tube Complement
VI - 12AX7 high gain dual triode, input cascade
amplifier.
V2 - 12CA5 beam power output tube.
V3 - 1629 electron beam visual indicator.
Speaker
3 1/2" permanent magnet.
Probe and Test Leads
4' input lead for RF and audio w/switch in probe body.
Two 3' panel test leads with alligator clips.
Dimensions
4 1/2" wide x 7 1/2" high x 4" deep.
Net Weight
4 Ibs.

Page 2

Page 3
INTRODUCTION
The Heathkit Visual-Aural Signal Tracer is a compact, service-designed instrument incorporating many features that
meet the everyday needs of the service technician. Some of the features and applications are listed below:
High gain position for direct signal tracing in RF or IF circuits.
High gain position for signal tracing in audio circuits.
Convenient RF or audio switch in probe body.
Tracer may be used for AM, FM, and TV circuit exploration.
Visual signal indicator.
Noise locator circuit.
Utility amplifier for checking record changers, tuners, etc.
Useful for checking microphones, musical instruments, pick-ups, and speakers.
Substitution speaker and output transformer.
Output level indicator.
CIRCUIT DESCRIPTION
The Heathkit Signal Tracer is a transformer operated, quality instrument, consisting primarily of a high-gain audio
amplifier. A built-in 3-1/2" speaker is provided for sound and an electron ray tube permits visual observation of the
output level. Additional features are RF and audio inputs in one convenient probe, noise locator circuit, and substitution
speaker, and output transformer.
Observing the schematic it can be seen that the RF-audio switch S2, mounted directly in the shielded probe body,
switches condenser C1 and a crystal diode in or out of the circuit for RF or audio applications. Condenser C1 isolates the
crystal diode to prevent any voltage damage.
The Noise Switch S3, connects B+ to the probe lead through resistor R14 to provide the noise locator circuit. The switch
S2 in the probe must be in the audio position for this function.
Signals from the probe are coupler, through condenser C2 to the gain-control R1 and in turn through condenser C3 to the
input grid of VI. Condenser C2 and C3 prevent noisy operation of the gain-control.
The tube VI, 12AX7, is a high-gain dual triode with the plate of section A coupled through con-denser C4 to the grid of
section B.
The condenser C5 couples VI (B), to the grid of V2, 12 CA5 beam power output tube. The primary of the output
transformer is center tapped and all three primary leads are brought out to terminals on the front panel. The power switch
S1-B in the off position disconnects the B+ so the trans-former may be used as a substitute output transformer.
The secondary leads are connected to the speaker voice coil panel terminals, and one side may be disconnected with the
speaker switch S4 when the speaker is used as a substitute.
Resistor R9 and condenser C6 couple a small amount of the output signal to the grid of V3, 1629 eye tube.
The Signal Tracer is transformer operated, and uses a silicon diode in a half-wave rectifier circuit. The transformer also
supplies 12.6 volts AC for the tube filaments.

Page 4
CONSTRUCTION NOTES
This manual is supplied to assist you in every way to complete the instrument with the least possible chance for error.
We suggest that you take a few minutes now and read the entire manual through before any work is started. This will
enable you to proceed with the work much faster when construction is started. We suggest that you retain the manual in
your files for future reference, both in the use of the instrument and for its maintenance.
UNPACK THE KIT CAREFULLY AND CHECK EACH PART AGAINST THE PARTS LIST. In so doing, you will
become acquainted with each part. Refer to the charts and other information shown on the inside covers of the manual to
help you identify any parts about which there may be a question. If some shortage is found in checking the parts, please
notify us promptly.
Resistors generally have a tolerance rating of 10 unless otherwise stated in the parts list. Therefore a 100 KΩ resistor may
test anywhere from 90 KΩ, to 110 KΩ. (The letter K is commonly used to designate a multiplier of 1000.) Tolerances on
condensers are generally even greater. Limits of +100 and -20 are common for electrolytic condensers. The parts
furnished with your Heathkit have been specified so as to not adversely affect the operation of the finished instrument.
The Signal Tracer is not difficult to construct but it is extremely important that particular emphasis be placed on the
desirability of following parts placement and wiring dress as shown in the manual. This is important in order that the
operation of the Signal Tracer be hum free and that a motor boating condition is not induced. The wiring dress and parts
layout in the manual has been proven thoroughly satisfactory through the construction of a series of laboratory models.
While the arrangement shown is probably not the only satisfactory layout, it is the result of considerable experimentation
and trial. If followed carefully, it will result in a stable instrument operating at a high degree of accuracy and
dependability.
We suggest you do the following before work is started:
1. Attach the large fold-in pictorials to the wall above
your workbench.
2. Go through the entire assembly and wiring
instructions. This is an excellent time to read the entire
construction section through and familiarize yourself
with the procedure.
3. Lay out all parts so that they are readily available.
Refer to the general information inside the front and
back covers of this manual to help you to identify
components
Most kit builders find it helpful to separate the various parts
into convenient categories. Muffin tins or molded egg cartons
make convenient trays for small parts. Resistors and capacitors
may be placed in the edge of a piece of corrugated cardboard
until they are needed. Values can be written on the cardboard
next to each component. The illustration shows one method that
may be used.

Page 5
Leads on resistors, capacitors and transformers are generally much longer than they need to be to make the indicated
connections. In these cases, the excess leads should be cut off before the part is added to the chassis. In general, the leads
should be just long enough to reach their terminating points. Not only does this make the wiring much neater but in many
instances, the excessively long leads will actually interfere with proper operation of the instrument.
Space has been provided for you to check off each operation as it is completed. This is particularly important in wiring
and it may prevent omissions or errors, especially where your work is interrupted frequently as the wiring progresses.
Some kit builders have also found it helpful to mark each lead in colored pencil on the pictorial as it is added.
Unless otherwise indicated, all wire used is insulated. Wherever there is a possibility of the bare leads on resistors and
capacitors shorting to other parts or to chassis, the leads should be covered with insulated sleeving. This is indicated in the
instructions by the phrase "use sleeving." Bare wire is used where the lead lengths are short and the possibility of short
circuits are non-existent.
ROSIN CORE SOLDER HAS BEEN SUPPLIED WITH THIS KIT. THIS TYPE OF SOLDER MUST BE USED FOR
ALL SOLDERING IN THIS KIT. ALL GUARANTEES ARE VOIDED AND WE WILL NOT REPAIR OR SERVICE
EQUIPMENT IN WHICH ACID CORE SOLDER OR PASTE FLUXES HAVE BEEN USED. IF ADDITIONAL
SOLDER IS NEEDED, BE SURE TO PURCHASE ROSIN CORE (60:40 or 50:50 TIN-LEAD CONTENT) RADIO
TYPE SOLDER.
PROPER SOLDERING PROCEDURE
Only a small percentage of Heathkit purchasers find it necessary to return an instrument for factory service. Of these, by
far the largest proportion function improperly due to poor or-improper soldering.
Correct soldering technique is extremely important. Good solder joints are essential if the performance engineered into the
kit is to be fully realized. If you are a beginner with no experience in soldering, a hall-hour's practice with odd lengths of
wire and a tube socket will be a worthwhile investment.
If terminals are bright and clean and wires free of wax, frayed insulation and other foreign sub-stances, no difficulty will
be experienced in soldering. Crimp or otherwise secure the wire (or wires) to the terminal, so a good joint is made without
relying on solder for physical strength.

Page 6
To make a good solder joint, the clean tip of the soldering iron should be placed against the joint to be soldered so that the
terminal is heated sufficiently to melt solder. The solder is then placed against both the terminal and the tip of the iron and
will immediately flow out over the joint. Refer to sketches on page 6 and 7. Use only enough solder to cover wires at the
junction; it is not necessary to fill the entire hole in the terminal with solder. Excess solder may flow into tube socket
contacts, ruining the socket, or it may creep into switch contacts and destroy their spring action. Position the work so that
gravity tends to keep the solder where you want it.
A poor solder joint will usually be indicated by its appearance. The solder will
stand up in a blob on top of the connection with no evidence of flowing out
caused by actual "wetting" of the contact. A crystalline or grainy texture on the
solder surface, caused by movement of the joint before it solidified is another
evidence of a "cold" connection. In either event, reheat the joint until the solder
flows smoothly over the entire junction, cooling to a smooth, bright
appearance. Photographs in the adjoining picture clearly indicate these two
characteristics.
A good, clean, well-tinned soldering iron is also important to obtain
consistently perfect con-nections. For most wiring, a 25 to 100 watt iron, or the
equivalent in a soldering gun, is very satisfactory. Smaller irons generally will not heat the connections enough to flow
the solder smoothly over the joint and are recommended only for light work, such as on etched circuit boards, etc. Keep
the iron tip clean and bright. A pad of steel wool may be used to wipe the tip occasionally during use.
CRIMP WIRES

Page 7
In the step-by-step procedure the abbreviation "NS" indicates that the connection should not be soldered as yet, for other
wires will be added. "When the last wire is installed, the terminal should be soldered and the abbreviation "S" is used to
indicate this. Note that a number appears after each solder (S) instruction. This number indicates the number of leads
connected to the terminal in question. For example, if the instructions read, "Connect one lead of a 47 KO resis-tor to lug
1 (S2)" it will be understood that there will be two leads connected to the terminal at the time it is soldered. This
additional check will help avoid errors.
Use lockwashers under all 6-32 and 8-32 nuts. Lockwashers should be placed between controls and the chassis.
Whensolder lugs are mounted under 6-32 nuts, the use of lockwashers is unnec-essary.
Don't apply too much solder to the solder joint. Don't apply the solder to the iron only, expecting that it will roll down to
the connection. Try to follow the instructions and illustrations as closely as possible.
Don't bend a lead more than once around a connecting point. If it should have to come off due to a mistake or for
maintenance it will be much easier to remove.
Keep your soldering iron clean. Wipe it quickly from time to time with steel wool or a rag.
When two or more connections are made to the same solder lug a common mistake is to neglect soldering the connections
on the bottom. Make sure all the wires are soldered.
HOW TO MAKE PROPER SOLDER CONNECTION
Take these precautions and use reasonable care during assembly of the kit. This will insure the wonderful
satisfaction of having the instrument operate perfectly the first time it is turned on.

Page 8
PANEL ASSEMBLY
( ) Locate the short 6/32 screw and set aside to be used later.
( ) Locate the front panel and position it as shown in Pictorial 1.
( ) Mount binding post A using a 6-32 nut. Position solder lug as shown in Pictorial 1.
( ) In like manner, mount binding post F, G and H.
( ) Mount binding post C with a control solder lug under the bushing. See Pictorial 1.
( ) Mount the speaker switch S4 as shown in Pictorial 1. Use 6-32 screws.
( ) In like manner, mount the noise switch S3.
( ) Insert the 3/8 grommet I.
( ) Connect one lead of a .001 ceramic disc condenser to terminal H (NS). Connect the other lead to terminal G (NS).

Page 9
( ) Mount the output transformer on the speaker so the two black wires are next to the voice coil terminals. Use 6-32
hardware.
( ) Mount the speaker and the speaker grill to the panel. Place a spacer washer between speaker and grill. At the same
time mount ground lug B. Use 6-32 hardware.
( ) Connect one end of a 3" length of bare wire to speaker lug 2 (Sl). Feed the other end thru ground lug B (S2) thru
terminal lug Cl (S2) and wrap around panel ground lug C2 (Sl).
( ) Cut one of the black leads of the output transformer to length, strip the end and connect to speaker lug 1 (NS).
( ) Connect one end of a 2" length of hookup wire to terminal lug A (Sl). Connect the other end to speaker lug 1 (S2).
This completes the panel assembly and wiring. Set aside to be mounted on the chassis later.

Page 10
CHASSIS ASSEMBLY
NOTE: When mounting wafer tube sockets, be sure to mount each socket from the top of the chassis. If by mistake the
sockets are mounted so the lugs pass through the chassis, they will short to the chassis where they pass through the
mounting hole.
( ) Mount the 2 lug terminal strip X. Use 6-32 hardware.
( ) Turn the chassis over and mount the 2 lug terminal strip at L.
( ) Mount the 2 lug vertical terminal strip T and at the same time mount the 3 lug terminal strip Q. Use 6-32 hardware.
( ) Mount the 9 pin wafer tube socket VI on the
underside of the chassis as shown in Pic-torial 3. Use 3-
48 hardware. (Nolockwash-ers are used with 3-48
hardware.)
( ) In like manner mount the 7 pin wafer tube socket V2
as shown in Pictorial 3. Use 3-48 hardware.
( ) Mount the C7 condenser mounting wafer on top of
the chassis, observing ground lug slot location as shown
in Pictorial 3. Use 6-32 screws, lockwashers and nuts.

Page 11
( ) Slip the two speed nuts J and K over the corners of the rear apron of the chassis. Make sure that the flat side of the
clip is towards the back and the holes in the clips are centered over the holes in the chassis.
( ) Temporarily, mount the 1 meg level control Rl using a control solder lug. Position as shown in Pictorials 2 and 3.
( ) In like manner mount the off-on switch S-1 using a control lockwasher between chassis and switch.
( ) Mount the filter condenser C7 so the lug marked with a square is towards the rear of the chassis. Twist the mounting
lugs 1/8 turn only.
( ) Mount the power transformer on the bottom side of the chassis with the wires towards the V2 tube socket. Use 8-32
hardware.
This completes the parts mounting, check all parts for correct position and make sure all screws and nuts are tightened
securely.
CHASSIS WIRING
( ) Connect the short black wire of the power transformer to lug 3 (Sl) of the off-on switch Sl.
( ) Twist the two green filament wires of the transformer
together, and connect one wire to pin 3 (NS) and the other wire
to pin 4 (NS) of tube socket V2.
( ) Connect one red transformer wire to ground lug U (NS) of
condenser C7.
( ) Feed the other red wire from the power transformer through
hole P and connect to lug 1 (NS) of terminal strip T.
( ) Feed the remaining black wire through hole N and connect to lug 1 (NS) of terminal strip L.

Page 12
( ) Connect one end of a 2" length of bare wire to pin 3 (Sl) of VI tube socket. Feed the other end through the center
ground lug (S2), through pin 9 (S2) and connect to lug 2(NS) of terminal strip X.
( ) Cut two 6" lengths of hookup wire and strip both ends. Twist the wires together and connect one wire to pin 3 (S2) of
tube socket V2. Connect the other wire to pin 4 (S2). Connect the other ends to pin 4 (NS) and 5 (NS) of socket VI.
( ) Connect one end of a 4-1/2" length of hookup wire to pin 1 (Sl) of V2. Connect the other end to lug 3 (NS) of
filter condenser C7.
( ) Connect one lead of a 330 ohm resistor (orange-orange-brown) to lug 3 (S2) of C7. Connect the other lead to
ground lug U (S2).
( ) Connect one lead of a 10 K ohm resistor (brown-black-orange) to lug 1 (NS) of C7. Con-nect the other lead to lug
2 (NS).
( ) Strip both ends of a 5" length of hookup wire, and connect one end to lug 2 (NS) of C7. Dress the wire towards
the front of the chassis.
( ) Connect one lead of a 330 K ohm resistor (orange-orange-yellow) to pin 2 (NS) of socket VI. Connect the other
lead to ground lug W (Sl).
( ) Connect one lead of a 47 K ohm resistor (yellow-violet-orange) to pin 1 (NS) of socket VI. Connect the other
lead to lug 2 (NS) of C7. Use sleeving on both leads.

Page 13
( ) Connect one lead of a 68 K ohm resistor (blue-grey-orange) to pin 6 (NS) of VI.
( ) Connect the other lead to lug 2 of C7 (S4). Use sleeving on both leads. Connect one lead of a .005 mfd ceramic disc
condenser to pin 2 (S2) of VI. Connect the other lead to pin 6 (S2).
( ) Feed one lead of a 1 K ohm resistor (brown-black-red) through lug 3 (S2) of the level con-trol Rl and wrap around the
control solder lug Y (NS). Connect the other lead to pin 8 (Sl) of VI.
( ) Connect one lead of a 330 K ohm resistor (orange-orange-yellow) to pin 7 (NS) of VI. Wrap the other lead around
solder lug Y (S2).
( ) Connect one lead of a . 005 mfd ceramic condenser to pin 7 (S2) of VI. Connect the other lead to lug 2 (Sl) of control
Rl.
( ) Connect one lead of a .005 mfd ceramic condenser to lug 1 (Sl) of control Rl. Connect the other lead to lug 1 (NS) of
terminal strip X.
( ) Connect one lead of a . 001 mfd ceramic disc condenser to pin 1 (NS) of socket VI. Connect the other lead to lug 2
(NS) of terminal strip X.
( ) Connect one lead of a .01 mfd condenser to pin 1 (S3) of tube socket VI. Connect the other lead to pin 2 (NS) of tube
socket V2.
( ) Connect one lead of a 330 K ohm resistor (orange-orange-yellow) to pin 2 (S2) of socket V2. Use sleeving. Connect
the other lead to lug 2 (NS) of terminal strip Q.
( ) Connect one lead of a 330 K ohm resistor (orange-orange-yellow) to lug 3 (NS) of terminal strip Q. Connect the other
lead to lug 2 (NS).
( ) Connect one lead of a . 001 mfd ceramic condenser to lug 1 (NS) of terminal strip Q. Connect the other lead to lug 3
(NS).
( ) Connect one lead of a 3.3 megohm resistor (orange-orange-green) to lug 1 (S2) of terminal strip Q. Connect the other
lead to pin 7 (NS) of tube socket V2.
( ) Strip both ends of a 4" length of wire and connect one end to pin 7 of V2 (S2). Dress the wire towards front of chassis.
( ) Strip both ends of a 4 1/2" length of wire and connect one end to pin 6 (Sl) of V2. Dress towards the front center of
chassis.
( ) Strip both ends of a 2 1/2" length of wire and connect one end to lug 1 (Sl) of switch Sl.
( ) Connect one end of a 41/2" length of wire to lug 1 (NS) of condenser C7. Feed the other end through hole N and
connect to lug 2 (NS) of terminal strip T on the top side of the chassis.
( ) Connect one end of a 5 1/2" length of wire to lug 2 (NS) of terminal strip T. Connect the other end to lug 2 (Sl) of
switch Sl.
( ) Connect one end of a 5" length of wire to lug 2 (NS) of terminal strip L. Connect the other end to lug 4 (Sl) of switch
Sl.
( ) Connect the cathode lead of a silicon diode to lug 2 (S3) and the other lead to lug 1 (S2) of terminal strip T. The
cathode end is marked with a color end, a color dot, or a color band.
( ) Pass the line cord through hole M. Connect one wire to lug 1 (S2) and the other wire to lug 2 (S2) of terminal strip L.

Page 14
( ) Install the line cord strain relief in hole M. See Detail 5A.
PREPARING THE EYE TUBE ASSEMBLY
( ) Start the two #6 sheet metal screws in the eye tube mounting
bracket.
( ) Clip off the prongs of the spring tube holder as indicated in
Figure 2.
( ) Mount the spring tube holder on the bracket using the short 6-
32 screw and a lockwasher and nut.
( ) Prepare the 8 pin wafer tube socket by bend-ing the lugs as
shown with a pair of long nose pliers.
( ) Connect one end of a 1 meg resistor (brown-black-green) to
pin 3 (Sl). Connect the other end to pin 4 (NS).
( ) Prepare the 6" length of 8-wire cable by cutting 3" of the
plastic cover off one end and 2" off the other end.
( ) Pull the black, white and yellow wires out of the cable

Page 15
( ) Cut 2" off the red wire and strip both ends of all the wires.
( ) Connect the blue wire to pin 2 (Sl) of the eye tube.
( ) Connect the red wire to pin 4 (S2).
( )Connect the green wire to pin 5 (Sl).
( ) Connect the orange wire to pin 7 (Sl).
( ) Connect the brown wire to pin 8 (Sl).
( ) Plug the socket on the 1629 eye tube and push the tube into the spring clip holder.
PREPARING THE PROBE AND TEST LEADS
( ) Mount the RF-Audio switch S2 on the terminal board by bending the lugs on the swithch as shown.
( ) Push one end of a 1 3/4" length of wire through hole C of the terminal board. Connect the other end to lug 3 (Sl) of
switch S2.
( ) Connect one end of a 3" length of wire to lug 2 (Sl) of switch S2. Strip the other end approximately 1".
( ) Push one lead of a . 001 ceramic disc condenser through hole C of the terminal board, and the other lead through
hole B.
( ) Connect the lead closest to the marking bands of the crystal diode to lug 1 of switchS2 (Sl).
Caution: Crystal diodes can be damaged by excessive heat. Use as little heat as possible when soldering. Push the other
lead of the diode through hole B and twist together with the condenser lead. Solder the two leads on the switch side of
the board and trim off any excess lead. (Use an alligator clip to hold wires in board).
() Cut away one inch of the outer insulation of the coaxial cable.
Double the lead over and pull the center conductor through the side
of the braid as shown. Strip off 1/4" of the insulation from the
center conductor.
( ) Slip the black probe end over the opposite end of the cable and
cut off 2" of the outer insulation. Pull the center conductor through
the braid, strip off 1/4" of the center conductor insulation and feed
the wire through hole A in terminal board, from the switch side.
Push the end of the wire through hole C. Twist the three wires
together and solder on the switch side of the board trim off excess
lead.

Page 16
( ) Slip the length of flat braid through the probe end and bend over as shown. Wrap a short length of bare wire around
the flat braid and the cable shield and solder. Cut off excess cable shield. Do not cut off braid.
( ) Solder an alligator clip to the other end of the braid.
( ) Slip the terminal board and switch into the probe body and mount the switch with the two small 4-40 screws.
( ) Push the black probe end into the end of the probe body, making sure that the flat braid is between the probe body and
the flat side of the probe end. Fasten the end with two small self tapping screws.
( ) Screw the probe tip into the red probe end, and remove the collar from the tip. Slip the red end into the probe body,
making sure the wire comes through the hole in the tip. Secure the end in the probe body with the two self tapping screws.
Wrap the wire around the probe tip and replace the collar.
( ) Remove the paper backing from the RF-AUDIOdecal, and place it on the probe body with the audio end towards the
tip.
( ) Assemble the red and black test leads as shown.
( ) Remove the 3/8 nuts from control Rl and switch Sl. Mount the
chassis to the panel using a nickel control washer between the panel
and the 3/8 control nuts.
( ) Feed the four remaining wires from the out-put transformer
through the chassis slot behind switch Sl. Connect the black wire to
lug 1 (Sl) of speaker switch S4.
( ) Connect a short length of bare wire be-tween lug 2 (Sl) of switch
S4 and lug 2 (NS) to terminal strip X.
( ) Connect one lead of a 68 K ohm resistor (blue-grey-orange) to
lug 2 (Sl) of noise switch S3. Connect the other lead to lug 1 (NS) of
terminal strip X.
( ) Connect the wire from lug 2 of condenser C7 to lug 1 (NS) of
switch S3.
( ) Connect the wire from pin 6 of V2 to lug 1 (S2) of switch S3.
( ) Connect the lead from lug 1 ol the oti-on switch to panel terminal H (NS).
( ) Connect the green wire from the output translormer to terminal H (S3).
( ) Connect the red transformer lead to terminal F (Sl). Connect the wire from pin 7 of socket V2 to terminal G (NS).

Page 17
( ) Connect the blue transformer wire to terminal G (S3).
( ) Feed the probe cable through grommet I and connect the inner conductor to lug 1 (S3) of terminal strip X. Connect
the cable shield to lug 2 (S4)
( ) Twist the green and brown leads from the eye tube
socket and connect the green lead to lug 3 (S3) of terminal
strip Q. Connect the brown lead to lug 2 (S3).
( ) Connect the red lead to lug 1 (S3) of conden-ser C7.
( ) Twist the orange and blue leads together and connect the
orange lead to pin 4 (S2) of sock-et VI. Connect the blue
lead to pin 5 (S2). This completes the T-4 wiring. Check
over connections and make sure that all have been soldered.
( ) Install the 12AX7, VI and the 12CA5, V2 tubes.
( ) Mount the eye tube by sliding the two sheet metal screws
into the slots in the chassis and tightening down, and then
push the tube forward against the panel.
( ) Install an 8-32 x 1/4" setscrew in each of the two knobs.
( ) Install the level control and off-on switch knobs. Position
the pointers so they line up with panel markings.
( ) Install red binding post caps on the speaker and the C. T.
post.
( ) Install black caps on the B+ and P post.
( ) Slightly spread the open end of the binding posts with a
phillips screwdriver after the binding post caps have been
screwed on. Tap the screwdriver lightly. This will keep the
binding post caps from falling off.
( ) Install the four rubber feet on the bottom of the cabinet.
( ) Install the handle using the two #10 sheet metal screws.
NOTE: The blue and white identification label shows the Model Number and Productions Series Number of your kit.
Refer to these numbers in any communications with the Heath Company; this assures you that you will receive the most
complete and up-to-date information in return.
( ) Carefully peel away the backing paper from the blue and white identification label. Then press the label onto the rear
of the cabinet.
Before installing the instrument in the cabinet, using 6-32 screws, these preliminary tests should be performed. Turn on the instrument
and advance the level control. Turn the speaker switch on and the noise switch off. After a few seconds the 1629 eye tube should light
green, thus indi-cating that the B+ and filament circuits are functioning properly. The shadow position of the tube may be adjusted in
the panel by rotating the tube. A loud hum should be heard when the probe tip is touched with the hand.
( ) If operation is normal, install the cabinet with 6-32 screws. If the Signal Tracer did not operate properly, refer to the In
Case Of Difficulty section of the manual.
IN CASE OF DIFFICULTY
If the Signal Tracer failed to operate in the preliminary test, again check over all connections for unsoldered or poor
joints. Using the pictorial diagrams, trace each lead with a red pencil to make sure each one is connected properly. Make
sure that no component leads are shorted to each other or to the chassis. Trace through the instrument by touching the grid

Page 18
(pin 2) of the 12CA5 output tube with a screwdriver that is held in contact with your finger. A low level hum should be
heard. Move the screwdriver to the grid of the 12AX7 tube section B (pin 2) and then to the grid of section A (pin 7). The
hum or noise should become louder with each stage. If no sound is heard, look for trouble in that particular stage.
CAUTION: To avoid any shock hazard when making the above test, make sure that only the pins that are mentioned in
the text are touched with the screwdriver, and the other hand or any other part of the body is not in con-tact with the
chassis pr any other conductor that may provide a return path to ground.
If after careful checks the trouble is still not located, check voltage and resistance readings found on the schematic diagram. Note: All
voltage and resistance readings were taken with a Heathkit Vacuum Tube Volt Meter. Voltage and resistance readings may vary 20%
due to line voltage variations and the tolerance of components. A reading that is off more than 20% would indicate probable trouble in
that particular stage. A review of the circuit description may also be helpful in indicating where to look for the trouble. NOTE: In an
extreme case where you are unable to resolve a difficulty, refer to the "Customer Service" information inside the rear cover of the
Manual. Your Warranty is inside the front cover.
USING THE SIGNAL TRACER
The IT-12 Signal Tracer is one of the simplest, yet most effective instruments the service tech-nician can use for rapid,
accurate trouble-shooting in radio and TV circuits. The tracer is of the untuned type to simplify operation thus holding
control manipulation to an absolute minimum.
This instrument features a number of useful applications which will enable the service technician to quickly locate and
diagnose the trouble in the circuit under test. Many of the tests will be performed automatically, and will require only a
few seconds of the technician's time. It is suggested however, that the user familiarize himself with all phases of the
instrument's operation, so that maximum benefit can be realized from the investment in the kit.
The procedures to be followed when using the Signal Tracer are outlined in a general manner only, and do not represent
the limits of its applications. Each individual will develop his own procedures and applications by using the instrument.
RF Signal Tracing
To use the Signal Tracer for RF signal tracing, the probe switch should be in the RF position, the off "on switch and the
speaker switch to the ON position, and the noise switch to OFF. The level control should be adjusted as needed. In some
cases it may be desirable to turn off the speaker and observe the approximate signal level on the indicator tube. Note: At
near maximum settings of the level control a certain amount of hum will be present; this is due to the high sensitivity of
the unit and the fact that the input grid has been extended to the probe permitting it to pick up spurious AC fields.
To illustrate the use of this instrument, a typical radio schematic is presented so the test points may be clearly pointed out.
Let us assume that the receiver under test has a specific complaint of low volume. Since the receiver is in partial operating
condition, it could be turned on and tuned to a familiar station. The volume control should be turned down so that the-
speaker out-put will not interfere with the signal tracer results. The flexible ground lead of the probe should be clipped to
the B- or ground circuit of the receiver.
If the receiver is tuned to a strong station, and the probe connected, a signal should be present at the loop antenna, the
tuning condenser and at the grid (pin 7) of tube A. When the probe is moved to the plate, (pin 5 of tube A) a substantial
increase in signal should be observed. Note: At radio frequencies, the D. C. voltages used in the IF stages need not be
filtered 100%. Coupled with this fact, the signal at the mixer or converter plate (pin 5) is very weak and requires a high
Other manuals for IT-12
1
Table of contents
Other Heathkit GPS manuals
Popular GPS manuals by other brands
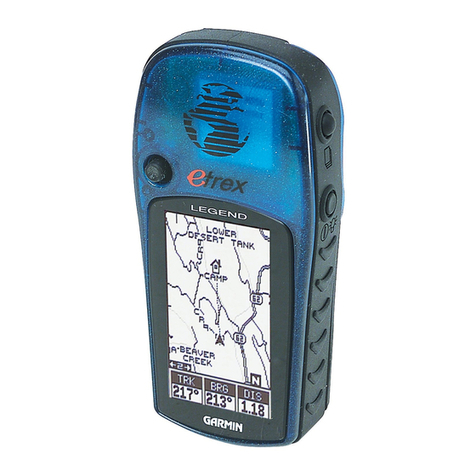
Garmin
Garmin Etrex Legend - GPS Receiver Owner's manual and reference guide

Packard Bell
Packard Bell Compasseo 370 quick start guide
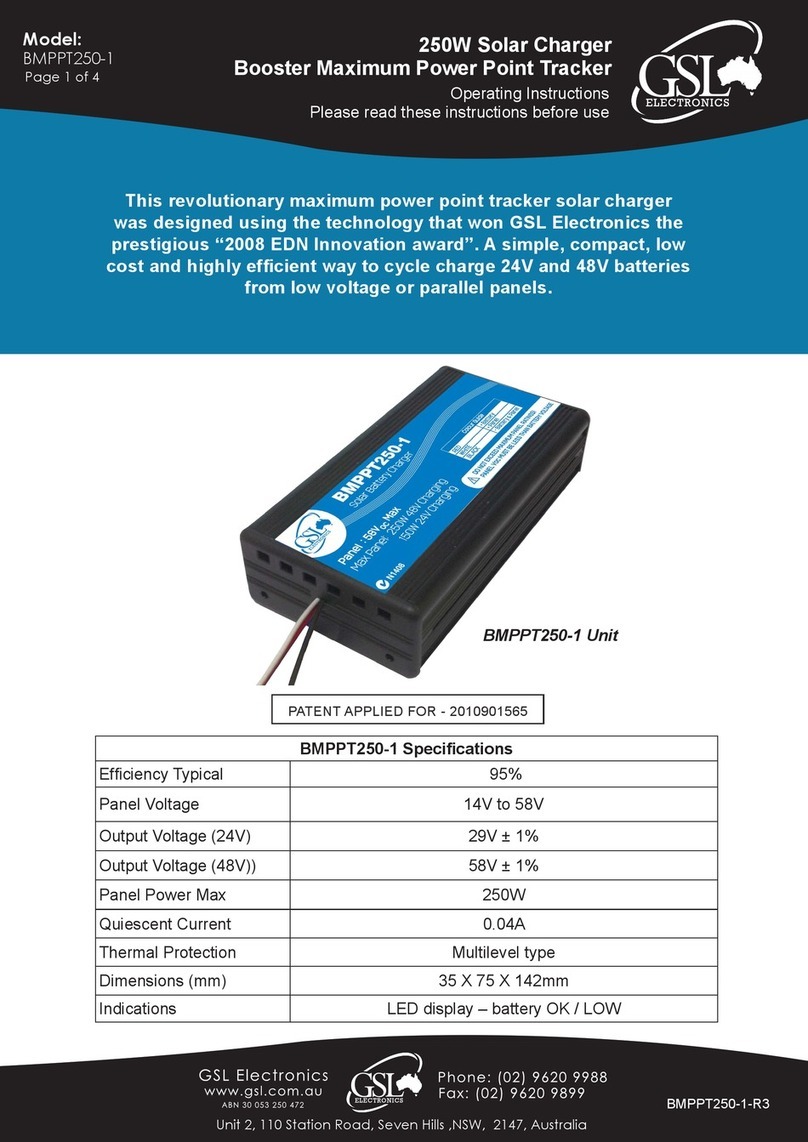
GSL
GSL BMPPT250-1 operating instructions

GoPass
GoPass GPT-810 user guide
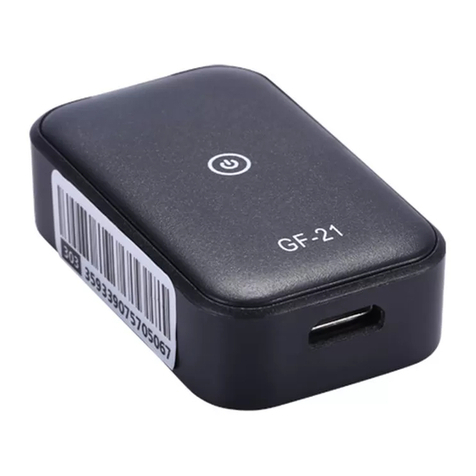
Canarmor
Canarmor GF21 operating instructions
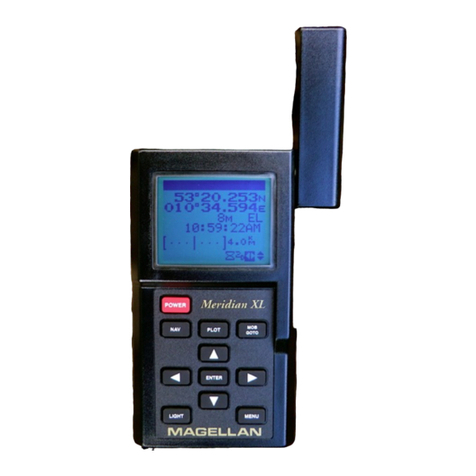
Magellan
Magellan GPS Satellite Navigator Meridian XL reference guide