Hirschmann PAT TRS 05 User manual

www.hirschmann.com
P/N 031-300-190-188 Revision B 08/30/2005
TRS 05
OPERATOR’S / SERVICE MANUAL


Operator’s/Installation/Service Manual TRS 05
© Hirschmann TRS 05 REV B 08/30/2005 190188_B
NOTICE
Hirschmann makes no warranty of any kind with regard to this material, including, but not limited to,
the implied warranties of merchantability and/or its fitness for a particular purpose.
Hirschmann will not be liable for errors contained in this manual or for incidental or consequential
damages in connection with the furnishing, performance, or use of this manual. This document
contains proprietary information, which is protected by copyright, and all rights are reserved.
No part of this document may be photocopied, reproduced, or translated to another language without
the prior written consent of Hirschmann.
Hirschmann reserves proprietary rights to all drawings, photos and the data contained therein. The
drawings, photos and data are confidential and cannot be used or reproduced without the written
consent of Hirschmann. The drawings and/or photos are subject to technical modification without prior
notice.
All information in this document is subject to change without notice.
MANUAL REVISIONS
REV DATE NAME DESCRIPTION
- 03/15/05 CSH ECN 05-056
A 06/17/05 SB ECN 05-109
B 08/30/05 CSH/SB ECN 05-152
© 2005 Hirschmann, Chambersburg, PA 17201, USA


General Information
© Hirschmann TRS 05 REV B 08/30/2005 190188_B
5
TABLE OF CONTENTS
1GENERAL INFORMATION ............................................................................................................ 1
2WARNINGS .................................................................................................................................... 1
3FEATURES..................................................................................................................................... 2
4SYSTEM DESCRIPTION................................................................................................................ 2
4.1 Receiver Module.......................................................................................................................... 2
4.1.1 LEDs .....................................................................................................................................................3
4.1.2 Control Identification .............................................................................................................................3
5OPERATION................................................................................................................................... 4
5.1 Receiver ...................................................................................................................................... 4
5.2 Transmitter .................................................................................................................................. 5
5.2.1 Load Cell...............................................................................................................................................5
5.2.2 Two-block Switch..................................................................................................................................5
5.3 Repeater...................................................................................................................................... 5
6COMPONENT INSTALLATION ..................................................................................................... 6
6.1 Receiver ...................................................................................................................................... 6
6.2 Repeater...................................................................................................................................... 7
6.3 Central Unit Installation ............................................................................................................... 7
6.3.1 TRS 05 Installation on the DS350 modular system central unit...........................................................7
6.3.2 TRS 05 Installation on the DS350 standard system central unit..........................................................9
6.4 TRS 05 Setup overview............................................................................................................. 11
6.5 Sensor Output Setup ................................................................................................................. 12
6.5.1 Hardware ............................................................................................................................................12
6.5.2 Software..............................................................................................................................................12
7TRS 05 SENSOR INSTALLATION .............................................................................................. 13
7.1 Install Sensor / Transmitter........................................................................................................ 13
7.2 Uninstall Sensor / Transmitter ................................................................................................... 13
8LOAD CELL INSTALLATION ...................................................................................................... 14
9LOAD SENSOR CALIBRATION .................................................................................................. 14
9.1 Load Sensor Zero point ............................................................................................................. 15
9.1.1 Additional Zero Point Adjustment for the DS350G standard system. ................................................16
9.2 Load Sensor gain Adjustment to a 70% permissible load ......................................................... 17
9.2.1 Accuracy and Test Requirements ......................................................................................................17
10 SERVICE AND TROUBLESHOOTING ........................................................................................ 18
10.1Service....................................................................................................................................... 18
10.2Troubleshooting......................................................................................................................... 19
10.2.1 Receiver..............................................................................................................................................19
10.2.2 Repeater .............................................................................................................................................20
10.3Troubleshooting Moisture .......................................................................................................... 20
11 MAINTENANCE............................................................................................................................ 21
11.1Battery Replacement ................................................................................................................. 21
12 SPARE PART NUMBERS............................................................................................................ 22


General Information
© Hirschmann TRS 05 REV B 08/30/2005 190188_B
1
1 GENERAL INFORMATION
The PAT TRS 05 system interface has been designed to use radio communication for load sensors.
The TRS 05 receives a radio signal from a transmitter sensor and converts a signal as a replacement
for the existing hardwired sensor.
Review system operator’s manual for system description and operation. All system functions and error
codes will remain the same for the DS350 system.
This manual will describe the operation, sensors setup and calibration, and additional troubleshooting
points for the TRS 05.
2 WARNINGS
Review system operator’s manual for system warnings.
The responsibility for the safe operation of the crane remains with the crane operator who must ensure
that all warnings and instructions supplied are fully understood and observed.
Prior to operating the crane, the operator must carefully and thoroughly read and understand the
information in this manual and the system manual to ensure that the operation and limitations of the
system and the crane are known.
The system can only work correctly, if all sensors/transmitters have been properly set. For
correct setup, the operator has correctly complete all procedures in this manual, the system
manual, and the setup procedure in accordance with the real rigging state of the crane. To
prevent material damage and serious or even fatal accidents, the correct adjustment of the
system has to be ensured before starting the crane operation.
Always refer to operational instructions and load charts provided by the crane manufacturer
for specific crane operation and load limits.

Operator’s/Installation/Service Manual TRS 05
© Hirschmann TRS 05 REV B 08/30/2005 190188_B
2
3 FEATURES
The PAT TRS 05 has the following features:
•Can be hardwired to most PAT systems, and certain crane systems.
•Wireless operation of 4 sensors.
•Minimum of 500 feet LOS.
•Easily and clearly shows the operator required information for the radio sensor.
oPower LED (red)
oLink condition LED (green), LED on sensor installed and linked, LED flashing installed
but link or communication has been lost, and LED off sensor not installed.
oLow battery indication LED (yellow)
oWarning of Error LED (red)
4 SYSTEM DESCRIPTION
4.1 RECEIVER MODULE
The receiver module has the following functions:
•Visual indication of receiver power, radio links (sensor on line), sensors low battery, and alarm
conditions.
•Installs/uninstalls a sensor
•Allows a zero point and output adjustment of a load sensor.
Red Power LED
Red Alarm LED
Sensor On Line
Green LED 1
Green LED 2
Green LED 3
Green LED 4
Sensor Low Battery
Yellow LED 1
Yellow LED 2
Yellow LED 3
Yellow LED 4

System Description
© Hirschmann TRS 05 REV B 08/30/2005 190188_B
3
4.1.1 LEDs
Red Power LED Power is applied to the circuit board.
Red alarm LED An installed sensor is indicating an alarm, or communication as been
lost to an installed sensor.
Green LED 1 ON Sensor on channel #1 is installed and communicating correctly.
Green LED 1 FLASHING Sensor #1 is not communicating correctly.
Green LED 1 OFF No sensor is installed on channel #1.
Yellow LED 1 ON Sensor #1 batteries are low and need replaced. Note that the sensor
is still operating correctly.
Green LED 2 ON Sensor #2 is installed and communicating correctly.
Green LED 2 FLASHING Sensor #2 is not communicating correctly.
Green LED 2 OFF No sensor is installed on channel #2.
Yellow LED 2 ON Sensor #2 batteries are low and need replaced. Note that the sensor
is still operating correctly.
Green LED 3 ON Sensor #3 is installed and communicating correctly.
Green LED 3 FLASHING Sensor #3 is not communicating correctly.
Green LED 3 OFF No sensor is installed on channel #3.
Yellow LED 3 ON Sensor #3 batteries are low and need replaced. Note that the sensor
is still operating correctly.
Green LED 4 ON Sensor #4 is installed and communicating correctly.
Green LED 4 FLASHING Sensor #4 is not communicating correctly.
Green LED 4 OFF No sensor is installed on channel #4.
Yellow LED 4 ON Sensor #4 batteries are low and need replaced. Note that the sensor
is still operating correctly.
Green Heartbeat LED This will flash during normal operation. If it is a solid or off, the
receiver has a software error or the board has a component failure.
4.1.2 Control Identification
Sensor/Channel #1 output jumper J4
Sensor/Channel #2 output jumper J3
Sensor #3/Channel #2 output jumper J2
Sensor #4/Channel #2 output jumper J1
ID button
power (red), sensor on-line 1-4 left to
right (green)
LEDS
1-4 left to right (yellow)
LEDS Green Heartbeat LED (located just
under radio module)
software chip
radio module 031-300-300-024

Operator’s/Installation/Service Manual TRS 05
© Hirschmann TRS 05 REV B 08/30/2005 190188_B
4
Heartbeat LED: When blinking, this small surface board mounted green LED indicates the system is
operation properly.
ID button: The red ID button, located below the software chip on the receiver board, is used to setup
the sensor transmitter to the receiver.
5 OPERATION
5.1 RECEIVER
Upon switching on crane ignition switch, the system starts with an automatic test of the receiver board,
LEDs and electronic components. The red power LED should be on and the green LEDs that sensors
have been linked to should also be on.
If an alarm condition exists investigate and clear the condition before operation and using the system.
During the normal operation of the system, the POWER and SENSOR ON LINE (if linked to a sensor)
LEDs should be on.
POWER LED
The POWER LED shows that the receiver is getting power from the crane. The receiver is on any time
the crane is operating and supplying power to the system.
SENSOR ON LINE LED
The SENSOR ON LINE LED indicates the status of communication of the transmitter(s). During
normal operation of the system, the LED will be on. The LED will flash if communication or
transmission between the sensor transmitter and the receiver is interrupted or lost. The system should
not be operated if the SENSOR ON LINE LED is flashing. If the LED is off no sensor is linked to this
channel.
LOW BATTERY LED
The low battery indicator will light indicating that you have a limited time to operate before the sensor
battery life ends. When the battery level is to the point that it is too low to operate, the system will stop
functioning. Use any off-the-shelf alkaline C-cells; Duracell, Eveready, etc.
ALARM LED
This LED will light simultaneously with the engaging of the lock out solenoids (if installed).
Test the electronics
Cycle the power to the system, each LED on the receiver will light for 2 seconds when the system is
powered. All of the indicator lights must come on or the system is not functioning properly. If any light
does not function, do not use the system until it has been repaired.
Refer to receiver operating manual for pre-operational inspection.
If a green sensor on line LED starts to flash, this means a sensor is installed and the communication
link has been lost. When communication has been lost to a load cell, the receiver will output the
maximum voltage signal for the output sensor (9VDC).
If a low battery LED is on, replace the batteries in the linked transmitter, refer to Battery Replacement.
The TRS 05 setup/calibration procedure allows the operator to input the type of sensors being used,
and adjust the zero point and output adjustment of a load sensor. The operator must complete the
setup procedure for each sensor.

Operation
© Hirschmann TRS 05 REV B 08/30/2005 190188_B
5
5.2 TRANSMITTER
The transmitter has an LED that will flash when a signal is transmitted to the receiver. Our system
transmits an OK signal every two seconds via three separate channels. This is to ensure accurate and
consistent reception of data and to reduce the possibility of unnoticed failure. The separate channels
greatly reduce the probability of failure due to external interferences. The receiver cycles through the
three channels, when software logic and/or lost signal, system will indicate a communication error.
5.2.1 Load Cell
The load cell transmits once every 1 to 2 seconds when in standby, and 2 times a second when the
load changes. It will continue at 2 times a second for less than a 1 minute before dropping back to one
transmission every 1 to 2 seconds. There is no time it goes to sleep.
Note: To extend battery life, remove batteries from transmitter(s) if load cell(s) will not be used for
extended periods of time. Reinstalling batteries into the transmitter will not require a set up.
NOTE: If the load cell is installed or reinstalled it will require
5.2.2 Two-block Switch
The PAT radio Anti-two Block (A2B) system works to prevent a two block condition using a weight and
switch. During normal operation the weight closes the A2B switch. The transmitter has an LED that
flashes approximately every 2 seconds when the switch is transmitting. If the weight is lifted and the
switch opens, the transmitter immediately (<100milliseconds) sends a two-block signal condition to the
receiver to be displayed on the console and lockout the crane movements (if connected to solenoid).
The LED will flash rapidly during a two-block condition and will stop flashing after 15 seconds when
the switch goes into sleep mode. While in sleep mode, the receiver will stay in a two-block or
communication loss condition. Sleep mode increases battery life by reducing the number of radio
transmissions. To wake the switch, simply close the switch by lowering the weight.
5.3 REPEATER
The purpose of the repeater is to reduce the possibility of a communication loss error by receiving the
load cell transmitted ID code and re-transmitting the same ID code out to the TRS 05. To do this, the
repeater is positioned at the boom tip, up the hoist rope from the load cell and up the boom from the
TRS 05. If the load cell does not have a direct line of sight or blocked by a wall/structure from the TRS
05 then there is less chance of the signal absorption/interference.
The repeater is setup from the factory to repeat signals from the load cells to the TRS 05 receiver.
TRS 05 can receive both transmissions (load cell and repeater) and output the load signal to the
system computer.
After switching power on to the repeater from the crane ignition switch, the system starts with an
automatic test of the repeater board, LEDs, and electronic components. The red power LED should be
on and other red LED blinks when the repeater is transmitting a signal.

Operator’s/Installation/Service Manual TRS 05
© Hirschmann TRS 05 REV B 08/30/2005 190188_B
6
6 COMPONENT INSTALLATION
6.1 RECEIVER
The TRS 05 receiver module should be mounted so the operator can view the LED’s.
Securely attach the receiver onto a solid surface using the mounting holes.
Model: PAT TRS 05
This device complies with Part 15 of the FCC rules.
Operation is subject to the following two conditions:
(1) This device may not cause harmful interference,
and (2) this device must accept interference that may
cause undesired operation.
ALARM
POWER
SENSOR LOW BATTERY
SENSOR ON LINE
1
1
2 3
23
4
4
Power cable connections are show above.

Component Installation
© Hirschmann TRS 05 REV B 08/30/2005 190188_B
7
6.2 REPEATER
The repeater module is mounted on the boom tip in line of sight to the receiver and the load cell. The
main purpose of the repeater is to receive and transmit the load cell ID code of the load cell during
operation. If the load cell line of sight is obstructed by a barrier (i.e. wall or building), the repeater
should prevent and signal loss.
Power cable connections: PIN 1 - +UB (9 to 30VDC), PIN 2 - GND
6.3 CENTRAL UNIT INSTALLATION
The power supply will be from 10- 30 volt DC. The signal output of the TRS 05 is dependent on the
placement of red bridges installed on the channel jumpers: 1 (for signal #1), 2 (signal #2), 3(signal #3),
and 4(signal #4). Each jumper has 4 bridge positions as follows:
1-2 voltage output 0..5V (required for the standard DS350 system)
3-4 amperage output 4..20mA (required for the modular DS350 system)
5-6 digital output
7-8 A2B switch output
6.3.1 TRS 05 Installation on the DS350 modular system central unit.
1. Remove breather element, use a M21
wrench to hold the PG11 nut inside the
central unit.
2. Insert PG11 strain relief and tighten nut.
3. Insert cable as shown, so the shield will
ground on the strain relief cone. There
should be about 12 inches of cable inside
the central unit to make the proper
connections.
4. Connect to the central unit as shown below.
Refer to system wiring below
Breather
Element

Operator’s/Installation/Service Manual TRS 05
© Hirschmann TRS 05 REV B 08/30/2005 190188_B
8
Wiring information:
Power: the TRS 05 wires on X1:1 and X1:2 will need to be added to the existing wiring. Do not
remove the existing wire on these terminals.
Radio Load Cell wires on signal sensor 1 and 2: Remove the existing wires from terminal X1:25,
X1:36, X1:22, and X1:24 and add the TRS 05 wire as shown.
Hardwired Anti Two-Block Switch: If the hardwired A2B switch is being used; do NOT remove the
existing wires from X1:31 and X1:32. Do NOT wire # 7 and 8 from the TRS 05.
Radio Anti Two-Block Switch: If one or two radio A2B switch(es) are being used; remove the
existing wires from X1:31 and X1:32 and add the TRS 05 wire as shown. The second switch on signal
sensor 4 does not need to be wired. The TRS 05 software recognizes an A2B switch is connected to
signal sensor channel 3 and 4; therefore, if either switch is opened the signal is sent to the central unit.

Component Installation
© Hirschmann TRS 05 REV B 08/30/2005 190188_B
9
6.3.2 TRS 05 Installation on the DS350 standard system central unit.
Metal shaving inside the central unit could cause a short or damage electrical components inside the
central unit. Use some type of protective plastic cover to shield the board from metal shavings, drill a
23/32” (0.718”) hole in the central unit housing in the location shown. Clean all metal shavings from
the central unit. Insert PG11 strain relief and tighten nut. Insert cable in the strain relief as shown,
leaving about 12” of wire in the central unit. The shield will ground on the strain relief cone and strain
relief will be tightened around the red/white insert.

Operator’s/Installation/Service Manual TRS 05
© Hirschmann TRS 05 REV B 08/30/2005 190188_B
10
Wiring information:
Power: the TRS 05 wires on X1:2 and X1:3 will need to be added to the existing wiring. Do not
remove the existing wire on these terminals.
Radio Load Cell wires on signal sensor 1 and 2: Remove the existing wires from terminal X1:34,
X1:33, X1:24, and X1:23 and add the TRS 05 wire as shown.
Hardwired Anti Two-Block Switch: If the hardwired A2B switch is being used; do NOT remove the
existing wires from X1:39 and X1:40. Do NOT wire # 7 and 8 from the TRS 05.
Radio Anti Two-Block Switch: If one or two radio A2B switch(es) are being used; remove the
existing wires from X1:39 and X1:40 and add the TRS 05 wire as shown. The second switch on signal
sensor 4 does not need to be wired. The TRS 05 software recognizes an A2B switch is connected to
signal sensor channel 3 and 4; therefore, if either switch is opened the signal is sent to the central unit.

Component Installation
© Hirschmann TRS 05 REV B 08/30/2005 190188_B
11
6.4 TRS 05 SETUP OVERVIEW
This section is a basic overview for the following Sections (TRS 05 Sensor Output Setup and Load
Sensor Calibration). Press and hold ID button, release the button at the desired indication (or the
number seconds) defined in the following table. The following table can be use as a quick reference
guide when setting up the sensors on the TRS 05 and calibrating the load cell.
NOTE: If an incorrect menu is activated or the button is released accidentally, simply cycle the power
and start over.
Menu Selection Release ID Button Indication
Indication
Starts (Sec)
Indication
Ends (Sec)
Install/setup sensor on channel 1 blinking green LED 1 3 6
Install/setup sensor on channel 2 blinking green LED 2 6 9
Install/setup sensor on channel 3 blinking green LED 3 9 12
Install/setup sensor on channel 4 blinking green LED 4 12 15
Uninstall a sensor on channel 1 solid LED 1 16 19
Uninstall a sensor on channel 2 solid LED 2 19 22
Uninstall a sensor on channel 3 solid LED 3 22 25
Uninstall a sensor on channel 4 solid LED 4 25 28
Set all the analog outputs for voltage 0-5V All 4 green LEDs blinking 29 32
Set all the analog outputs for 4..20ma All 4 green LEDs solid 33 36
Set all the analog outputs for voltage 1-9V All 4 yellow LEDs blinking 37 40
Set all the analog outputs for voltage 0-9V All 4 yellow LEDs solid 40 43
Calibrate load/angle sensor on channel 1 blinking yellow & green LEDs 1 43 46
Calibrate load/angle sensor on channel 2 blinking yellow & green LEDs 2 46 49
Calibrate load/angle sensor on channel 3 blinking yellow & green LEDs 3 50 53
Calibrate load/angle sensor on channel 4 blinking yellow & green LEDs 4 53 56
Service information on channel 1 blinking yellow LED 1 56 59
Service information on channel 2 blinking yellow LED 2 59 63
Service information on channel 3 blinking yellow LED 3 63 66
Service information on channel 4 blinking yellow LED 4 67 70
Exit/No action LEDs off no 71
ID button
LEDS
power (red), sensor link 1-4 left to right (green),
indication of load adjustment (up red LED
lit/down red LED off)
1-4 left to right (yellow)
LEDS Green Heartbeat LED
(located just under radio module)
software chip
radio module 031-300-300-024

Operator’s/Installation/Service Manual TRS 05
© Hirschmann TRS 05 REV B 08/30/2005 190188_B
12
6.5 SENSOR OUTPUT SETUP
The sensor output is setup for the hardware (bridge place on jumpers 1 & 2, as shown below) for the
load cells and software (use the ID button software output). If the hardware and software do not match
an error will occur.
6.5.1 Hardware
Install the bridge in the in the correct position; modular system – current or standard system – voltage
on jumpers 1 and 2, as show above. If a sensor is not installed, the bridges and jumpers will not effect
the operation of the unit.
6.5.2 Software
Setup the software for the output of the TRS 05:
Standard System – voltage: Hold the ID button for about 29-32 seconds until all 4 green LEDs are
blinking and released ID button to set all the analog outputs for 0-5VDC voltage.
Modular System – current: Hold the ID button for about 33 36 seconds until all 4 green LEDs are
solid and released ID button to set all the analog outputs for 4...20mA current.
Voltage position
Standard CU
Current position
Modular CU
Voltage position
Standard CU
Current position
Modular CU
A2B 4.7K position
ID Button

TRS 05 Sensor installation
© Hirschmann TRS 05 REV B 08/30/2005 190188_B
13
7 TRS 05 SENSOR INSTALLATION
7.1 INSTALL SENSOR / TRANSMITTER
Setup the sensors on the 4 channels with the sensor as described below and mark the sensors, i.e.
CH1, MAIN, or LOAD 1. Note: The following list corresponds with the installation wiring in this manual.
Tip: bring the sensor close to the TRS 05 receiver/cab, not necessary but will simplify the procedure.
Remove the battery covers from the sensors to be installed.
Main load cell - channel 1; Press and hold the ID button for 3-6 seconds until the 1st green LED’s will
begin blinking and release the ID button. The receiver begins to search for a transmitter ID code. On
the load sensor/transmitter, remove the card from the batteries or remove two batteries for 10 seconds
and replace them. In less than 10 seconds, the 1st green LED will become solid when the transmitter is
linked.
Auxiliary load cell - channel 2; Press and hold the ID button for 6-9 seconds until the 2nd green
LED’s will begin blinking and release the ID button. The receiver begins to search for a transmitter ID
code. On the load sensor/transmitter, remove the card from the batteries or remove two batteries for
10 seconds and replace them. In less than 10 seconds, the 2nd green LED will become solid when the
transmitter is linked.
Main A2B switch - channel 3 (If included as system option); Press and hold the ID button for 9-12
seconds until the 3rd green LED’s will begin blinking and release the ID button. The receiver begins to
search for a transmitter ID code. On the A2B switch/transmitter, remove the card from the batteries or
remove two batteries for 10 seconds and replace them. In less than 10 seconds, the 3rd green LED will
become solid when the transmitter is linked.
Auxiliary A2B switch - channel 4 (If included as system option); Press and hold the ID button for
12-15 seconds until the 4th green LED’s will begin blinking and release the ID button. The receiver
begins to search for a transmitter ID code. On the A2B switch/transmitter, remove the card from the
batteries or remove two batteries for 10 seconds and replace them. In less than 10 seconds, the 4th
green LED will become solid when the transmitter is linked.
NOTE: A new sensor or transmitter maybe install over an existing sensor on a channel, when
this occurs the previous link/ID code are removed from memory and the new one stored.
7.2 UNINSTALL SENSOR / TRANSMITTER
If a sensor is setup on the channel the LED will be ON, press and hold the ID button (16-28 seconds)
through the Install Sensor mode (blinking LEDs1-4) until the correct 1-4 LED is solid. When the correct
LED is solid, channel to be uninstalled, release the ID button. The sensor for the selected
channel/LED 1-4 will be uninstalled and the system will be in normal operating mode.
As the ID button is held (16-28 seconds) through the Install Sensor mode (blinking LEDs1-4) and
released at the solid LED, the following actions will occur:
Green LED 1 solid: Uninstall sensor 1.
Green LED 2 solid: Uninstall sensor 2.
Green LED 3 solid: Uninstall sensor 3.
Green LED 4 solid: Uninstall sensor 4.

Operator’s/Installation/Service Manual TRS 05
© Hirschmann TRS 05 REV B 08/30/2005 190188_B
14
8 LOAD CELL INSTALLATION
NOTE: After installation the load cell will need to be zeroed with no force applied and adjusted
to a permissible heavy load.
The load cell and plates are installed at the dead end of the wire rope that is being used to lift the load.
The appropriate pins (length and diameter) for the type and size of socket, block, or ball must be used.
Ensure that the correct pin used is rated for the maximum line pull capacity and the side load plates
will be straight when attaching the dead end lug and the load cell. Install the side plates using the 2-
1/4” pin so the pin head is on the antenna side. Ensure all safety pins are installed properly with
washers and bushing to fit the hole diameter and pin length.
9 LOAD SENSOR CALIBRATION
While the ID button is held or in the calibration process, the sensor outputs will not correctly indicate
the status of other installed sensors. Correct operation will return when the menu is exited or
calibration process is complete or system is powered off/on.
The load cell must be calibrated to ensure accuracy. The load sensor calibration is completed
complete the following steps:
1. Installing the load cell sensor (refer to 7.1 Install Sensor, if not complete)
2. Zero the load cell. The zero point adjustment will have an even affect across the entire range
(for example, 200 lb at both low and high loads).
3. Adjust the gain to a 70% permissible load. The gain adjustment will have only a small effect on
light loads, but a large effect on heavy loads.
Note: If an incorrect menu is activated or the button is released accidentally, simply cycle the power
and start over.
Note: When the system is in calibration mode, the RCL system NOT in operation; therefore, crane
operating guide line and load charts must be followed during calibration mode or other crane
operations.
NOTE: The unit will remain in main or auxiliary calibration mode until power is cycled off/on. After
completing the main load cell calibration, cycle power off/on and complete the auxiliary load
calibration.
Main load cell calibration: Press and hold the ID button for 43-46 seconds until the 1st yellow and
green LED’s will begin blinking and release the ID button. The 1st yellow and green LED will become
solid, showing the receiver is now in calibration mode for the main load cell on channel 1. Complete
sensor zero and gain adjustments in this section.
Auxiliary load cell calibration: Press and hold the ID button for 46-49 seconds until the 2nd yellow
and green LED’s will begin blinking and release the ID button. The 2nd yellow and green LED will
become solid, showing the receiver is now in calibration mode for the auxiliary load cell on channel 1.
Complete sensor zero and gain adjustments in this section.
Other manuals for PAT TRS 05
1
This manual suits for next models
1
Table of contents
Other Hirschmann Receiver manuals
Popular Receiver manuals by other brands
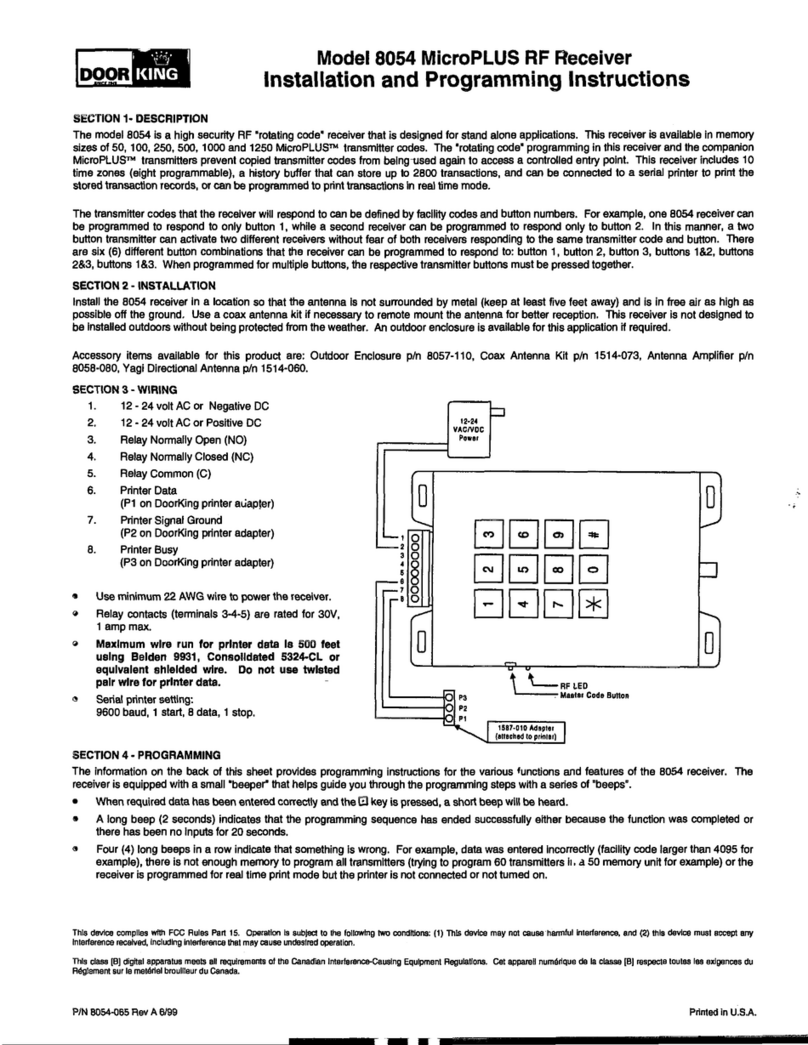
DoorKing
DoorKing 8054 MicroPlus Installation and programming instructions
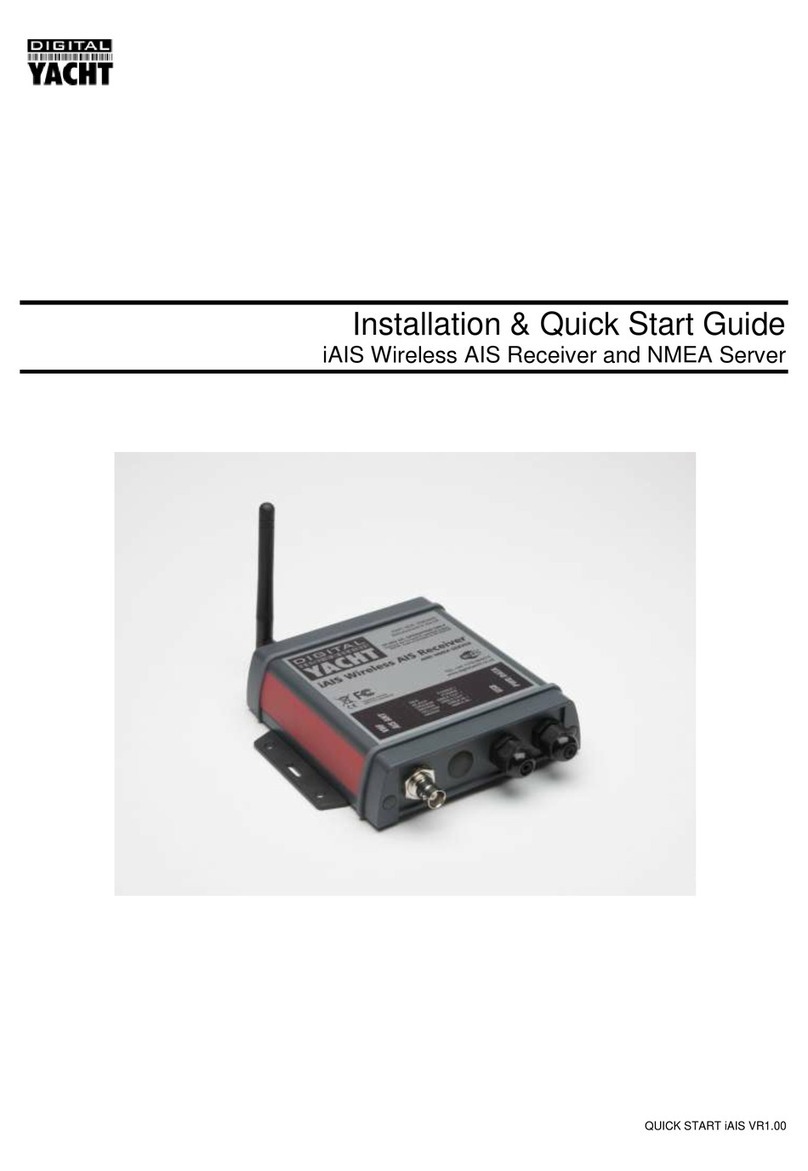
DIGITAL YACHT
DIGITAL YACHT iAIS Installation & quick start guide
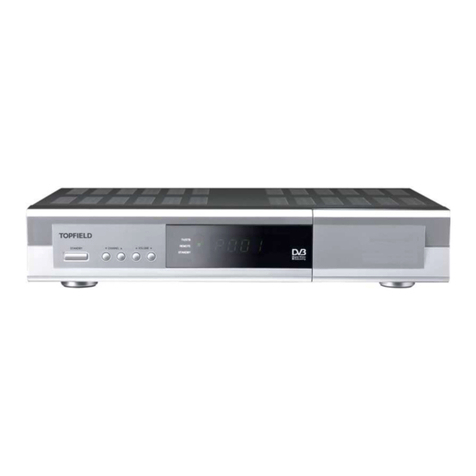
Topfield
Topfield TF 5000 CIP user guide
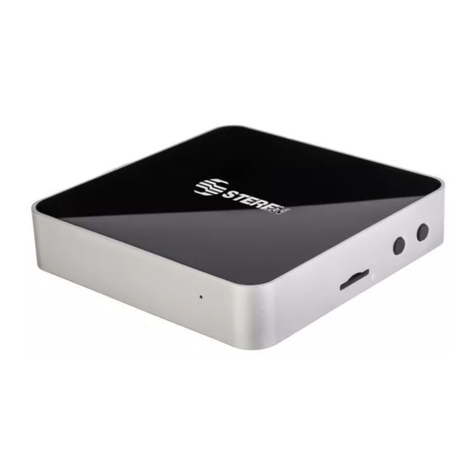
Steren
Steren MOV-180 instruction manual

ENFORCER
ENFORCER SK-910RBQ installation manual
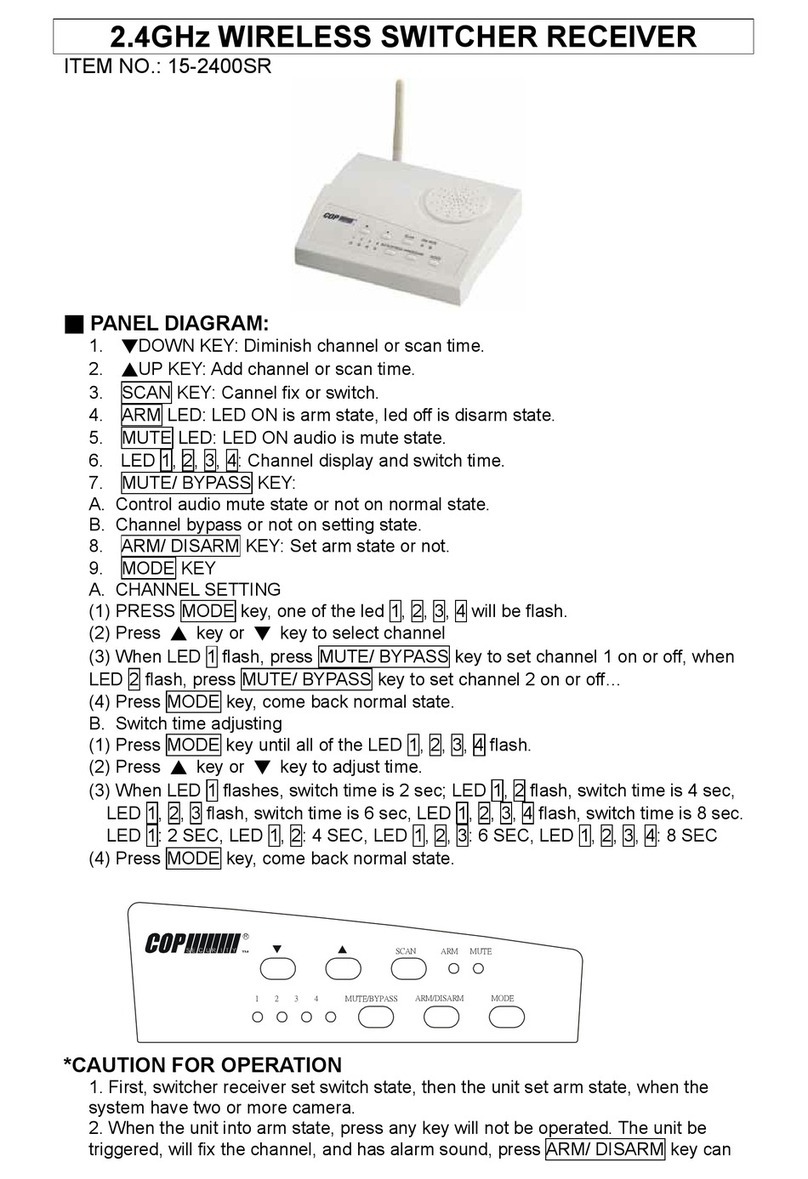
COP Security
COP Security 15-2400SR quick start guide