HMS Networks Intesis INMBSMHI048O000 User manual

Mitsubishi Heavy Industries Air Conditioning
Gateway for integration of Mitsubishi Heavy Industries air conditioning systems
into Modbus (RTU and TCP) systems
USER MANUAL
Issue date: 05/2012 r1.0 ENGLISH

IntesisTM Modbus Server –Mitsubishi Heavy Industries AC
User’s Manual r1.0 eng
© HMS Industrial Networks S.L.U - All rights reserved
This information is subject to change without notice
URL https://www.intesis.com
2 / 26
Important User Information
Disclaimer
The information in this document is for informational purposes only. Please inform HMS Industrial
Networks of any inaccuracies or omissions found in this document. HMS Industrial Networks disclaims
any responsibility or liability for any errors that may appear in this document.
HMS Industrial Networks reserves the right to modify its products in line with its policy of continuous
product development. The information in this document shall therefore not be construed as a
commitment on the part of HMS Industrial Networks and is subject to change without notice. HMS
Industrial Networks makes no commitment to update or keep current the information in this document.
The data, examples and illustrations found in this document are included for illustrative purposes and are
only intended to help improve understanding of the functionality and handling of the product. In view of
the wide range of possible applications of the product, and because of the many variables and
requirements associated with any particular implementation, HMS Industrial Networks cannot assume
responsibility or liability for actual use based on the data, examples or illustrations included in this
document nor for any damages incurred during installation of the product. Those responsible for the use
of the product must acquire sufficient knowledge in order to ensure that the product is used correctly in
their specific application and that the application meets all performance and safety requirements
including any applicable laws, regulations, codes and standards. Further, HMS Industrial Networks will
under no circumstances assume liability or responsibility for any problems that may arise as a result from
the use of undocumented features or functional side effects found outside the documented scope of the
product. The effects caused by any direct or indirect use of such aspects of the product are undefined and
may include e.g. compatibility issues and stability issues.

IntesisTM Modbus Server –Mitsubishi Heavy Industries AC
User’s Manual r1.0 eng
© HMS Industrial Networks S.L.U - All rights reserved
This information is subject to change without notice
URL https://www.intesis.com
3 / 26
Gateway for integration of Mitsubishi Heavy
Industries air conditioning systems into Modbus
(RTU and TCP) systems.
ORDER CODE
LEGACY ORDER CODE
INMBSMHI048O000
MH-AC-MBS-48
INMBSMHI128O000
MH-AC-MBS-128

IntesisTM Modbus Server –Mitsubishi Heavy Industries AC
User’s Manual r1.0 eng
© HMS Industrial Networks S.L.U - All rights reserved
This information is subject to change without notice
URL https://www.intesis.com
4 / 26
Index
Description ....................................................................................................... 5
Introduction .................................................................................................... 5
Integration signals ........................................................................................... 5
Functionality ................................................................................................... 6
Capacity of IntesisTM ........................................................................................ 7
Modbus interface of IntesisTM............................................................................... 8
Description ..................................................................................................... 8
Functions supported......................................................................................... 8
Modbus RTU.................................................................................................... 8
Modbus TCP .................................................................................................... 8
Address Map ................................................................................................... 8
2.5.1 Modbus addresses related to IntesisTM .......................................................... 9
2.5.2 Modbus addresses related to each Indoor Unit............................................... 9
2.5.3 Modbus addresses related to ALL indoor units ............................................. 10
IntesisTM Device Connections ............................................................................. 11
Connect to Mitsubishi Heavy Industries Interface ............................................... 12
Connect to Modbus Interface........................................................................... 12
3.2.1 Connect to Modbus RTU............................................................................ 12
3.2.2 Connect to Modbus TCP ............................................................................ 13
3.2.3 Connect to PC (LinkBoxMB)....................................................................... 14
Power Device ................................................................................................ 14
LinkBoxMB. Configuration & monitoring tool for IntesisTM Modbus Server series ....... 15
Introduction .................................................................................................. 15
Connections configuration............................................................................... 15
4.2.1 Configuration tab ..................................................................................... 15
4.2.2 Modbus map tab ...................................................................................... 17
Sending the configuration to IntesisTM .............................................................. 18
Signals viewer............................................................................................... 19
Files............................................................................................................. 20
Setup process and troubleshooting .................................................................... 21
Pre-requisites................................................................................................ 21
Setup procedure ............................................................................................ 21
Troubleshooting............................................................................................. 22
5.3.1 Physical checking..................................................................................... 22
5.3.2 Software checking ................................................................................... 22
Functional characteristics summary.................................................................... 23
Mechanical & Electrical characteristics ................................................................ 24
AC Unit Types compatibility .............................................................................. 25
Error codes ..................................................................................................... 26

IntesisTM Modbus Server –Mitsubishi Heavy Industries AC
User’s Manual r1.0 eng
© HMS Industrial Networks S.L.U - All rights reserved
This information is subject to change without notice
URL https://www.intesis.com
5 / 26
Description
Introduction
IntesisTM Modbus Server –Mitsubishi Heavy Industries AC is a communication gateway for
Mitsubishi Heavy Industries air conditioning (AC) systems to Modbus slave (RTU and TCP).
This gateway allows integrating a Mitsubishi Heavy Industries AC system inside a
supervision/control/automation system through PLC, SCADA and, in general, through any
device or system with Modbus mastering (TCP or RTU) interface.
The aim of this integration is to make accessible several Mitsubishi Heavy Industries air
conditioning indoor units communicating with the Superlink protocol as if they were part of
a Modbus system. Therefore, the IntesisTM Modbus Server acts as a Modbus slave in the
Modbus interface, allowing the Modbus master read and write in the Modbus registers.
Moreover, IntesisTM includes all hardware required to manage/control Mitsubishi Heavy
Industries indoor units without extra components needed.
Integration signals
Following is the list of parameters that can be monitored/controlled on the indoor units
using IntesisTM:
▪For each indoor unit in the system:
oCommunication Status (read-only)
oOn/Off (R/W)
oOperation Mode (R/W)
oSetPoint Temperature (R/W)
oFan Speed (R/W)
oRemote Controller Lock/Unlock (R/W)
oLouver Control (R/W)
oRoom Temperature (read-only)
oFilter Sign Status (read-only)
oError Code (read-only)
oCompressor Status (read-only)
oFilter Sign Reset (write-only)
oRemote Controller Error Reset (write-only)
oThermo On/Off Status (read-only)
Apart from these, the IntesisTM also implements some extra signals (functions):
▪For all indoor units
1
in the system:
oHW Communication Status (read-only)
oOn/Off (write-only)
oOperation Mode (write-only)
oSetPoint Temperature (write-only)
oFan Speed (write-only)
oRemote Controller Lock/Unlock (write-only)
1
These signals work as master signals controlling all connected units at the same time

IntesisTM Modbus Server –Mitsubishi Heavy Industries AC
User’s Manual r1.0 eng
© HMS Industrial Networks S.L.U - All rights reserved
This information is subject to change without notice
URL https://www.intesis.com
6 / 26
Functionality
Each of the mentioned signals in section 1.2 is associated to a predefined and fixed Modbus
address. Therefore, all the system is seen as a single Modbus slave unit with a fixed Modbus
address map from the Modbus system point of view.
Two Modbus mode connection types can be active in IntesisTM: Modbus RTU or Modbus TCP,
or both simultaneously.
IntesisTM continuously polls all signals provided by each indoor unit and maintains the
updated values to be served in Modbus.
In the continuous polling of each indoor unit, if no response of a certain device is detected,
the corresponding virtual signal inside the gateway will be activated indicating
communication error between the gateway and that precise device (see 0).
When a write order is done from Modbus in a gateway's write-enabled Modbus address, the
corresponding order is sent to the associated Mitsubishi Heavy Industries signal (Superlink).
Each Mitsubishi Heavy Industries Indoor Unit has a unique address (0 to 127). These
addresses need to be configured inside IntesisTM using the LinkBoxMB tool (see 4.2.2).
IntesisTM is capable of managing up to two simultaneous Modbus master connections.
IntesisTM includes all hardware needed to connect directly with the Mitsubishi Heavy
Industries indoor units connecting with Superlink network.
0
1
47
127
Superlink
Figure 1.1 Integration of Mitsubishi Heavy Industries AC into Modbus system using IntesisTM
EIA232/EIA485
2-wire no polarity
EIA232
TCP/IP
Intesis
Modbus Server

IntesisTM Modbus Server –Mitsubishi Heavy Industries AC
User’s Manual r1.0 eng
© HMS Industrial Networks S.L.U - All rights reserved
This information is subject to change without notice
URL https://www.intesis.com
7 / 26
Capacity of IntesisTM
Element
Max.
Notes
Number of indoor units
128 *
Maximum number of AC indoor units that
can be controlled
Number of points per indoor unit
14
Modbus addresses per indoor unit
Maximum number of points
1797*
Valid Modbus addresses
Maximum TCP master connections
2
Maximum number of TCP simultaneous
Modbus Master connections
Maximum RTU master connections
1
Maximum number of RTU simultaneous
Modbus Master connections
Table 1.1 IntesisTM capacity
* There are two different models of IntesisTM Modbus Server –Mitsubishi Heavy Industries
AC each one with different capacity. The table above shows the capacity for the top model
(with maximum capacity).
Their order codes are:
▪INMBSMHI048O000:
▪Model supporting up to 48 indoor units
▪For Superlink-I (Previous Superlink) or Superlink-II (New Superlink).
▪Indoor Unit actual address range is 00 to 47
▪INMBSMHI128O000:
▪Model supporting up to 128 indoor units
▪For Superlink-II (New Superlink)
▪Indoor Unit actual address range is 000 to 127
Check available combination of Mitsubishi Heavy Industries Central Control and BMS
interface units in the next tables.
In the case of SL2NA or SL3NA, it is necessary to erase registration of non-connected indoor
unit. For SL2NA and SL3NA, change is required for the setup deprived of the rights of
instruction of Remocon control Lock/Unlock.
New Superlink connections:
INMBSMHI128O000
INKNXMHI128O000
SC-LGWNA-A
SC-BGWNA-
A/B
etc.
SC-SL3NA-AE/BE
etc.
SC-SL2NA-E
etc.
SC-SL1N-E
etc.
Max
Indoor
Units
Address
No.
1
Non connect
2
0
0-8
128
000-127
1
0-2
0
0-4
INMBSMHI048O000
INKNXMHI048O000
SC-LGWNA-A
SC-BGWNA-A/B
etc.
SC-SL3NA-AE/BE
etc.
SC-SL2NA-E
etc.
SC-SL1N-E
etc.
Max
Indoor
Units
Address
No.
1
Non connect
2
0
0-8
48
00-47
1
0-2
0
0-4
Previous Superlink connections:
INMBSMHI---O000
INKNXMHI---O000
SC-LGWNA-A
SC-BGWNA-A/B
etc.
SC-SL3NA-
AE/BE
etc.
SC-SL2NA-
E
etc.
SC-SL1N-E
etc.
Max
Indoor
Units
Address
No.
1
Non connect
Non connect
1
0
32
00-47
0
1,2
0
0
48

IntesisTM Modbus Server –Mitsubishi Heavy Industries AC
User’s Manual r1.0 eng
© HMS Industrial Networks S.L.U - All rights reserved
This information is subject to change without notice
URL https://www.intesis.com
8 / 26
Modbus interface of IntesisTM
Description
IntesisTM acts as a slave device in the Modbus interface. The physical interface can be either
Ethernet, if using Modbus TCP, or the EIA485 (or EIA232), if using Modbus RTU.
Functions supported
This part is common for Modbus RTU and TCP:
•Modbus functions 03 and 04 (read holding registers and read input registers) can
be used to read Modbus registers.
•Modbus function 06 (Single Multiple Holding Registers) must be used to write
Modbus registers.
•As per Modbus standard specification, register contents are always expressed in
MSB..LSB (Bid Endian).
•Modbus error codes are fully supported, they will be sent whenever a non-valid
Modbus action or address is required (see section 9).
Modbus RTU
Baud rate can be selected from 1200, 2400, 4800, 9600, 19200 and 38400.
Information structure:
•Data Bits: 8
•Parity Bit: Selectable from non, even, odd or second stop bit (2stop).
•Stop Bit: 1
Modbus slave number can be configured.
Physical connection (EIA232 or EIA485) can also be selected.
Only the lines RX, TX and GND of the EIA232 connector are used (TX and RX for EIA485).
Modbus TCP
The TCP port to use can be configured (by default 502 is used).
The IP address, subnet mask and default gateway address to use by IntesisTM can be also
configured.
Address Map
Address map is fixed for each indoor unit and can be consulted as explained in the following
tables. Please, remember that in the tables R/W stands for Read and Write, Rstands for
Read Only and Wstands for Write Only.

IntesisTM Modbus Server –Mitsubishi Heavy Industries AC
User’s Manual r1.0 eng
© HMS Industrial Networks S.L.U - All rights reserved
This information is subject to change without notice
URL https://www.intesis.com
9 / 26
2.5.1 Modbus addresses related to IntesisTM
Modbus
address
(base addr is 1)
Modbus
register
type (R/W)
Signal description and values
2995
R
Hw Communication Status
•0: No Hardware Communication Error
•1: Hardware Communication Error
2.5.2 Modbus addresses related to each Indoor Unit
1
Indoor unit
number
Modbus
address
(base addr is 1)
Modbus
register
type (R/W)
Signal description and values
0
1
R
Communication Status
▪0: Communication OK
▪1: Communication ERROR
2
R/W
Indoor Unit On/Off
▪0: Off
▪1: On
3
R/W
Operation Mode
▪0: Cool
▪1: Heat
▪2: Fan
▪3: Auto
▪4: Dry
4
R/W
SetPoint Temperature
▪Celsius value (16ºC to 30ºC)
5
R/W
Fan Speed
▪0: Low
▪1: Medium
▪2: High
▪3: Powerful
6
R/W
Remote Controller Lock/Unlock
▪0: Remote Controller Locked
▪1: Remote Controller Unlocked
7
R/W
Louver Control2
▪0: Swing
▪1: Pos1
▪2: Pos2
▪3: Pos3
▪4: Pos4
8
R
Room Temperature
▪Celsius value (0ºC to 30ºC)
9
R
Filter Sign status
▪0:Off
▪1:On
10
R
Error Code
▪0: No Error
▪0-99: Error Code3
11
R
Compressor Status
▪0: Off
▪1: On
12
W
Filter Sign Reset
▪1: Clear Filter Alarm
(When reading, always 0)
13
W
Remote Controller Error Reset
▪1: Clear Remote Controller Error
(When reading, always 0)
14
R
Thermo On/Off Status (Inverter Type Only)
▪0: Off
▪1: On
…
…
…
…
Indoor unit
number
Modbus address
(base addr is 1)
Modbus
register type
Signal description and values
1
Supported number of indoor units varies according to IntesisTM model
2
During transition between positions, Swing signal will turn on indicating the Louver is moving
3
See list of indoor unit error codes and their meaning in section 9

IntesisTM Modbus Server –Mitsubishi Heavy Industries AC
User’s Manual r1.0 eng
© HMS Industrial Networks S.L.U - All rights reserved
This information is subject to change without notice
URL https://www.intesis.com
10 / 26
(R/W)
…
…
…
…
n*
( n*) x 20 + 1
R
Communication Status
( n*) x 20 + 2
R/W
Indoor Unit On/Off
( n*) x 20 + 3
R/W
Operation Mode
( n*) x 20 + 4
R/W
SetPoint Temperature
( n*) x 20 + 5
R/W
Fan Speed
( n*) x 20 + 6
R/W
Remote Controller Lock/Unlock
( n*) x 20 + 7
R/W
Louver Control
( n*) x 20 + 8
R
Room Temperature
( n*) x 20 + 9
R
Filter Sign status
( n*) x 20 + 10
R
Indoor Unit Error Code
( n*) x 20 + 11
R
Compressor Status
( n*) x 20 + 12
W
Filter Sign Reset
( n*) x 20 + 13
W
Remote Control Error Reset
( n*) x 20 + 14
R
Thermo Status (Inverter Type Only)
…
…
…
…
127
(max number of
supported indoor
units depends on
Intesis model)
2541
R
Communication Status
2542
R/W
Indoor Unit On/Off
2543
R/W
Operation Mode
2544
R/W
SetPoint Temperature
2545
R/W
Fan Speed
2546
R/W
Remote Controller Lock/Unlock
2547
R/W
Louver Control
2548
R
Room Temperature
2549
R
Filter Sign status
2550
R
Indoor Unit Error Code
2551
R
Compressor Status
2552
W
Filter Sign Reset
2553
W
Remote Control Error Reset
2554
R
Thermo Status (Inverter Type Only)
*n is the indoor unit address number.
2.5.3 Modbus addresses related to ALL indoor units
Indoor unit
number
Modbus address
(base addr is 1)
Modbus register
type (R/W)
Signal description and values
ALL
2996
W
All Indoor Units On/Off
▪0: Off
▪1: On
2997
W
All Indoor Units Operation Mode
▪0: Cool
▪1: Heat
▪2: Fan
▪3: Auto
▪4: Dry
2998
W
All Indoor Units SetPoint Temperature
▪Celsius value (16ºC to 30ºC)
2999
W
All Indoor Units Fan Speed
▪0: Low
▪1: Medium
▪2: High
▪3: Powerful
3000
W
All Indoor Units Remote Controller Lock/Unlock
▪0: Remote Controller Locked
▪1: Remote Controller Unlocked

IntesisTM Modbus Server –Mitsubishi Heavy Industries AC
User’s Manual r1.0 eng
© HMS Industrial Networks S.L.U - All rights reserved
This information is subject to change without notice
URL https://www.intesis.com
11 / 26
IntesisTM Device Connections
Figure 3.1 IntesisTM device front view
Next, there is the list with the device physical interface connector’s description
1.- Modbus RTU master EIA485 (C1)
8.- Reset button (Non supported)
2.- Modbus RTU master EIA232 (C2)
9.- Superlink selector (SLK)
New: Superlink-II
Old: Superlink-I
3.- Console serial port EIA232
10.- A-B connector (for Superlink, no polarity)
4.- Operation LED
11.- Modbus TCP master Ethernet (ETH)
5.- Error LED
12.- Power supply On/Off button
6.- Host LED
13.- Power supply fuse (250V, 1.5A)
7.- Pac LED
14.- Power supply connector
2
3
4
5
6
7
8
9
10
11
1
Figure 3.2 IntesisTM device back view
12
14
13
100-240VAC~
50-60Hz 5W max
FUSE:
250V 1.5A(T)
20x5mm

IntesisTM Modbus Server –Mitsubishi Heavy Industries AC
User’s Manual r1.0 eng
© HMS Industrial Networks S.L.U - All rights reserved
This information is subject to change without notice
URL https://www.intesis.com
12 / 26
Connect to Mitsubishi Heavy Industries Interface
Use the A-B connector in the right top corner of the front side of the IntesisTM device in
order to connect the Mitsubishi Heavy Industries network (Superlink) to the IntesisTM.
Recommended specifications of the cable for the Superlink are shown as follows:
•Size of cable : 0.75 to 1.25 square mm
•Max length of wiring : total 1000m (loop wiring is not allowed)
•Cable materials :
Twisted Vinyl Cabtyre Cable
VCTF 2 core 0.75 to 1.25 square mm
Twisted Vinyl Cabtyre Cable
VCT 2 core 0.75 to 1.25 square mm
Twisted Vinyl Cable for Control
CVV 2 core 0.75 to 1.25 square mm
Table 3.1 Cable types recommended for Superlink connection
•For prevention of electromagnetic noise malfunctions, parallel wiring with the power
line should be avoided
Select the appropriate Superlink mode in the SLK selector. If you are using latest Air
Conditioner of the Mitsubishi Heavy Industries network (New Superlink) select NEW, if not
select OLD.
LEDs placed in the top left corner will show connection status as follows:
LED
Status
IntesisTM behavior
OP
Blinking
Power supply OK
ERR
Off
No error
HOST
Blinking
Internal communication OK
PAC
Blinking
Communication with the Superlink network OK
Table 3.2 IntesisTM LED status information
OP LED behavior must defer depending on the Superlink version, as shown in Figure 3.3
Figure 3.3 OP LED blinking behavior depending on Superlink version
If LEDs (except ERR) are not in the states described above, check section 5.3.
For further information about the Superlink network, look up the Mitsubishi Heavy
Industries Manual or contact your nearest Mitsubishi Heavy Industries supplier.
Connect to Modbus Interface
3.2.1 Connect to Modbus RTU
Connect the communication cable coming from the Modbus RTU network to IntesisTM device
(see Figure 3.1). There are 2 existing modes available:
Superlink-II
Superlink-I
On
Off
On
Off
1 sec

IntesisTM Modbus Server –Mitsubishi Heavy Industries AC
User’s Manual r1.0 eng
© HMS Industrial Networks S.L.U - All rights reserved
This information is subject to change without notice
URL https://www.intesis.com
13 / 26
•EIA485 connection: Use the C1 connector (see Figure 3.1) if the Modbus interface is
a 2-wire EIA485 connector. Connect the + and –to the respective port in the master
device and in the IntesisTM device (polarity matters).
•EIA232 connection: Use the C2 connector (see Figure 3.1) if the Modbus interface is
point-to-point to one single master.
Intesis
(DB9 M)
C2
Modbus RTU Connection
Master RTU
(DB9 M)
Cable
(DB9 F)
EIA232
(Crossed)
Cable
(DB9 F)
RX
2
2
RX
TX
3
3
TX
GND
5
5
GND
Table 3.3 EIA232 cable pin assign
Cable
(2-wire)
EIA485
TX/RX+
TX/RX+
TX/RX-
TX/RX-
Table 3.4 EIA485 cable pin assign
To check connectivity and correct functioning, use LinkBoxMB software (see LinkBoxMB User
Manual).
3.2.2 Connect to Modbus TCP
Connect the communication cable coming from the hub, switch or device of the Modbus
Ethernet network to the ETH connector from the IntesisTM device (see Figure 3.1). The
cable to be used may vary depending on where the IntesisTM is being connected:
•Connecting directly to a Modbus TCP master device: Crossover Ethernet UTP/FTP
CAT5 cable.
•Connecting to a hub or switch of the LAN of the building: Straight Ethernet UTP/FTP
CAT5 cable.
Intesis
(RJ45 F)
ETH
Modbus TCP Connection
Master TCP
(RJ45 F)
Cable
(RJ45 M)
Ethernet
Cable
(RJ45 M)
Cable UTP/FTP Cat5 Crossover
1 device
Modbus
master
Cable UTP/FTP Cat5 Straight
Hub
N devices
Modbus
master
Table 3.5 TCP cable connection

IntesisTM Modbus Server –Mitsubishi Heavy Industries AC
User’s Manual r1.0 eng
© HMS Industrial Networks S.L.U - All rights reserved
This information is subject to change without notice
URL https://www.intesis.com
14 / 26
In case there is no communication with the IntesisTM, check that the Modbus TCP devices
are operative and reachable from the network connection used by IntesisTM. You can also
check that the IntesisTM Ethernet interface is sending Pings to its IP address using a PC
connected to the same Ethernet network.
3.2.3 Connect to PC (LinkBoxMB)
Connect the IntesisTM device to the PC serial port using the serial cable provided. One end
should be connected to the Console EIA232 port of the IntesisTM device (see Figure 3.1)
and the other end to the PC serial port.
Intesis
(DB9 F)
EIA232
Serial
Console
PC Connection (LinkBoxMB)
PC
(DB9 M)
Cable
(DB9 M)
EIA232
(Straight)
Cable
(DB9 F)
TX
2
2
RX
RX
3
3
TX
GND
5
5
GND
Table 3.6 EIA232 serial connection pin assign
Power Device
To power up the device, what you need is to plug properly the Power Supply connector to
the IntesisTM device using a proper cable and connecting one end to the power supply
connector (see Figure 3.2) and the other end to the power line. After that, just press the
power supply On/Off button to turn it on.

IntesisTM Modbus Server –Mitsubishi Heavy Industries AC
User’s Manual r1.0 eng
© HMS Industrial Networks S.L.U - All rights reserved
This information is subject to change without notice
URL https://www.intesis.com
15 / 26
LinkBoxMB. Configuration & monitoring tool for IntesisTM Modbus Server
series
Introduction
LinkBoxMB is a Windows®compatible software developed specifically to monitor and
configure IntesisTM Modbus Server series.
The installation procedure and main functions are explained in the LinkBoxMB User Manual.
This document can be found in the Doc folder or can be downloaded from the link indicated
in the installation sheet supplied with the IntesisTM device.
In this section, only the specific case of Mitsubishi Heavy Industries indoor unit’s integration
to Modbus networks will be covered.
Connections configuration
To configure the IntesisTM's connection parameters and to see the points list, press on the
Config button in the menu bar (see Figure 4.1). The Mitsubishi Heavy Industries
Configuration window will open (see Figure 4.2). For integrations with large number of
points, there is available an alternative CSV installation procedure explained in the
LinkBoxMB User Manual.
Figure 4.1 LinkBoxMB menu bar
4.2.1 Configuration tab
Select the Connection tab to configure the connection parameters. Two subsets of
information are shown in this window: Modbus RTU, Modbus TCP and Mitsubishi Heavy
Industries interfaces parameters (see Figure 4.2).
Figure 4.2 LinkBoxMB configuration tab
Next, there is an explanation for each of the configuration parameters in each mode.
Modbus
interface
configuration
MHI
interface
configuration

IntesisTM Modbus Server –Mitsubishi Heavy Industries AC
User’s Manual r1.0 eng
© HMS Industrial Networks S.L.U - All rights reserved
This information is subject to change without notice
URL https://www.intesis.com
16 / 26
•Modbus interface configuration parameters:
Figure 4.3 Modbus interface configuration
1. Select the type of Modbus communication to use (TCP, RTU or both).
If Modbus TCP is selected, then:
2. IP Intesis: Enter the IP address for IntesisTM.
3. Net Mask: Enter the IP netmask for IntesisTM.
4. Gateway: Enter the default gateway address for IntesisTM; leave it blank if no router
is needed.
5. Port: Enter the TCP port to use (default for Modbus TCP is 502).
6. Timeout Keep Alive: Enter the time (expressed in seconds) that IntesisTM will wait,
upon no TCP activity, to send a Keep Alive packet. Enter 0 if you don’t want IntesisTM
to send any Keep Alive packet (default 30 seconds).
If Modbus RTU is selected, then:
7. Connection: Select the physical media (EIA232 or EIA485)
1
.
8. Baud rate: Enter the baud rate of the serial communication.
9. Parity: Enter the byte parity of the serial communication.
10. Slave: Introduce the Slave number for the Modbus interface.
•Mitsubishi Heavy Industries interface configuration parameters:
1
In the LinkboxMB this connection is labeled as RS232 and RS485 respectively.
2
3
4
5
6
7
8
9
1
10

IntesisTM Modbus Server –Mitsubishi Heavy Industries AC
User’s Manual r1.0 eng
© HMS Industrial Networks S.L.U - All rights reserved
This information is subject to change without notice
URL https://www.intesis.com
17 / 26
Figure 4.4 Mitsubishi Heavy Industries interface configuration
1. Devices: In this list, you can individually enable each of the 128 indoor units
available on the system. The index in the column “Indoor unit” (i.e. the number x
in “Indoor Unit xxx”) is the reference that will be used later on (in tab “Signals”)
to refer to this AC indoor unit. You can also change the name of the indoor Unit to
facilitate integration tasks.
2. Gateway version: Selection of the Intesis Modbus Server –Mitsubishi Heavy
Industries gateway you are setting up. (128AC for INMBSMHI128O000, 48AC for
INMBSMHI048O000)
3. Timeout response: Maximum amount of time permitted before activating the
Communication Error signal. It is expressed in milliseconds (ms) and ranges can
vary from 2000 ms to 10000 ms.
4. Delay interframe: Maximum amount of time permitted between End Of
Transmission (EOT) and a new frame. It is expressed in milliseconds (ms) and
ranges can vary from 500 ms to 3000 ms.
5. Monitoring cadence: Cadence of monitoring and subscription. It is expressed in
seconds (s) and ranges can vary from 60 s to 600 s.
Additional configuration parameters should generally be left to their default value. They only
might need to be tuned in some very specific cases (installations with large number of units,
scenarios with large bursts of commands sent at once …)
4.2.2 Modbus map tab
In order to know the Modbus map that is going to be used by the interface, the Modbus
map tab can be consulted.
1
2
3
4
5

IntesisTM Modbus Server –Mitsubishi Heavy Industries AC
User’s Manual r1.0 eng
© HMS Industrial Networks S.L.U - All rights reserved
This information is subject to change without notice
URL https://www.intesis.com
18 / 26
Content in this tab is just informative: no information has to be set up.
Figure 4.5 Modbus signal list
1. Address Formula: Formula used by IntesisTM to define the Modbus address for
the point. Use this address (obtained with this formula) to access the point from
your Modbus master device.
2. R/W:Indicates if the signal is read-only, or if it can be read and written (from the
Modbus system point of view).
3. Signal: Signal description.
4. Values: Possible values for the signal.
See section 2.5 for further detail on address mapping and the possible values on each
signal.
Sending the configuration to IntesisTM
When the configuration is finished, follow the next steps.
1.- Click on Save button to save the project to the project folder on your hard disk
(more information in LinkBoxMB User Manual).
2.- You will be prompted to generate the configuration file to be sent to the gateway.
a.- If Yes is selected, the binary file (MHI.Lbox) containing the configuration
for the gateway will be generated and saved also into the project folder.
b.- If NO is selected, remember that the binary file with the project needs to
be generated before the IntesisTM starts to work as expected.
3.- Once in the configuration window again, click on exit. Configuration file is ready
to be sent to the IntesisTM device.
1
2
3
4

IntesisTM Modbus Server –Mitsubishi Heavy Industries AC
User’s Manual r1.0 eng
© HMS Industrial Networks S.L.U - All rights reserved
This information is subject to change without notice
URL https://www.intesis.com
19 / 26
4.- Press the Send File button to send the binary file to the IntesisTM device. The
process of file transmission can be monitored in the IntesisTM Communication
Console window. Intesis will reboot automatically once the new configuration is
loaded.
After any configuration change, do not forget to send the configuration file
to the IntesisTM using button Send File.
Signals viewer
Once the gateway is running with the correct configuration, to supervise the status of the
configured signals, press the Signals button on the menu bar (see Figure 4.1). The Signals
Viewer window will open (see Figure 4.6).
This window shows all signals active within the gateway with its main configuration
parameters and its real time value
1
in the Value column.
Figure 4.6 LinkBoxMB Signals Viewer
The signals viewer can be used even though only one system is connected to the IntesisTM,
Modbus or Mitsubishi Heavy Industries AC. Therefore, it becomes convenient for supervision
and testing the system.
In order to force a specific value to a signal, double-click its row in the table. This will
display a dialog in which the desired value can be entered (see Figure 4.7). Changing its
value in this way, will make:
•The content of the corresponding Modbus address will be changed to this value.
•If the signal is write-enabled, it will trigger a suitable command to Mitsubishi Heavy
Industries AC system.
1
In case you connect to the IntesisTM when it’s been running for a certain time, you should press the Refresh
button to get updated values. After pressing Refresh, all signal values will keep continuously updated until the
connection is closed.

IntesisTM Modbus Server –Mitsubishi Heavy Industries AC
User’s Manual r1.0 eng
© HMS Industrial Networks S.L.U - All rights reserved
This information is subject to change without notice
URL https://www.intesis.com
20 / 26
Figure 4.7 Signal value change window
Files
LinkBoxMB saves the integration configuration in the following files inside the project folder:
PROJECT.INI
INI file containing general information related to the project
MHI.INI
INI file containing information related with the values configured
through the “Connection” tab in IntesisTM configuration
MHI.LBOX
Binary file created from the information in the files described
above. This is the file downloaded to the IntesisTM.
Table 4.1 LinkBoxMB generated files during Project creation
It is strongly recommended to back up the project folder containing these files in external
media, once the installation process is finished. This way you will be able to do future
configuration changes in case of reinstallation of LinkBoxMB due, for example, to a failure of
the hard disk in the PC where LinkBoxMB was installed.
The configuration cannot be uploaded from the gateway to LinkBoxMB, it can only
be downloaded.
This manual suits for next models
3
Table of contents
Other HMS Networks Server manuals
Popular Server manuals by other brands

Black Box
Black Box LES1102A quick start guide
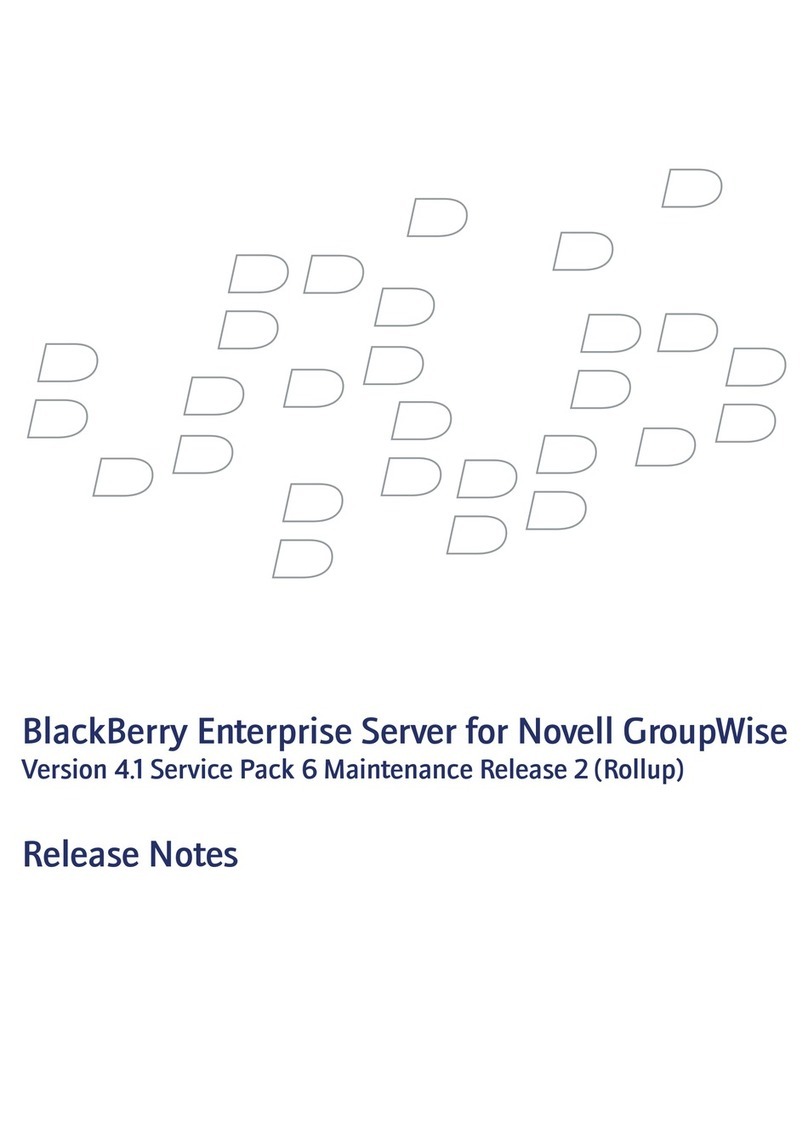
Blackbe;rry
Blackbe;rry ENTERPRISE SERVER FOR NOVELL GROUPWISE - - MAINTENANCE RELEASE... release note

Avtech
Avtech AVX931B installation guide
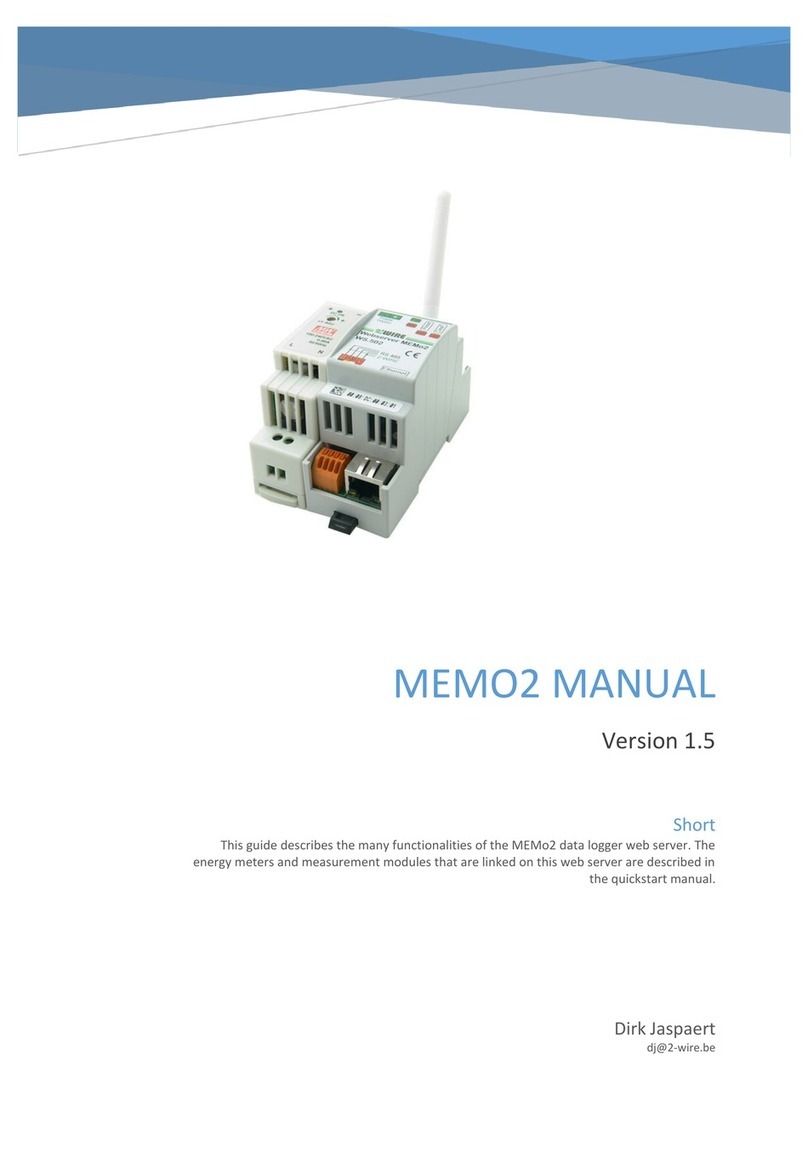
2-Wire
2-Wire MEMO2 WS.502 manual
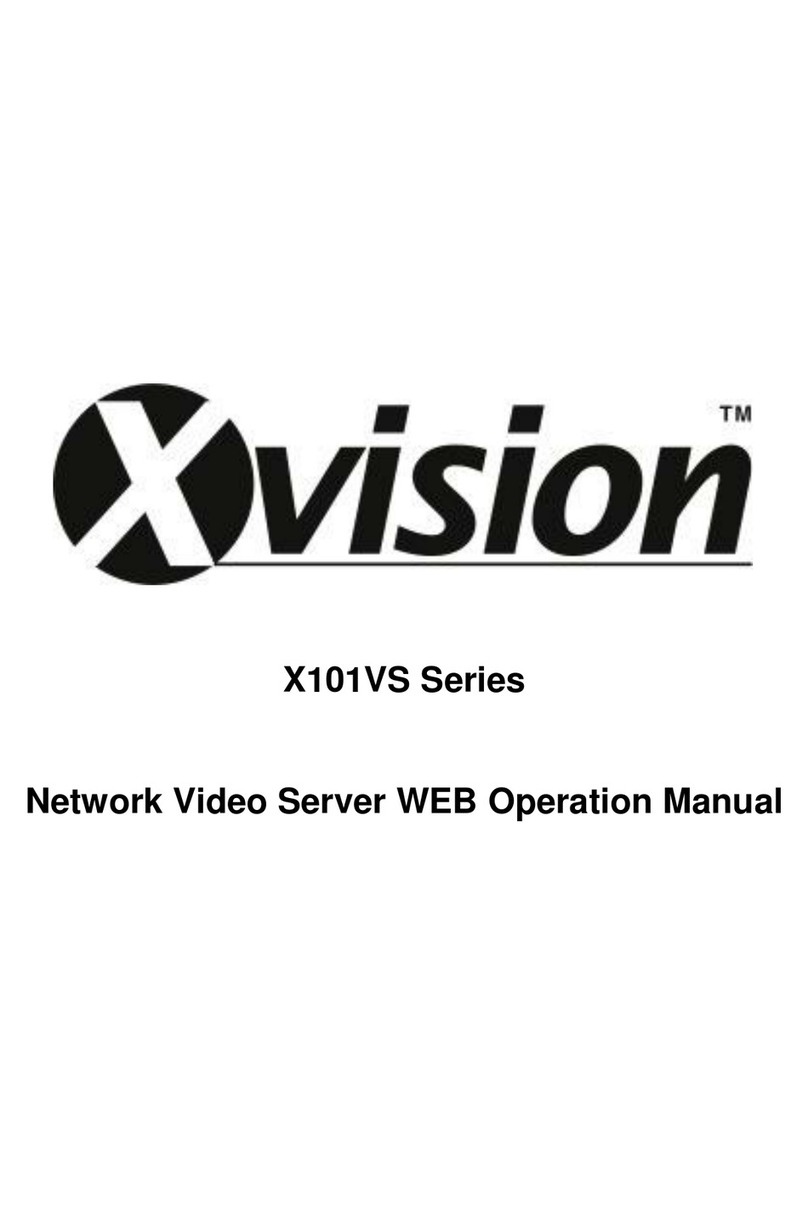
X-Vision
X-Vision X101VS Operation manual
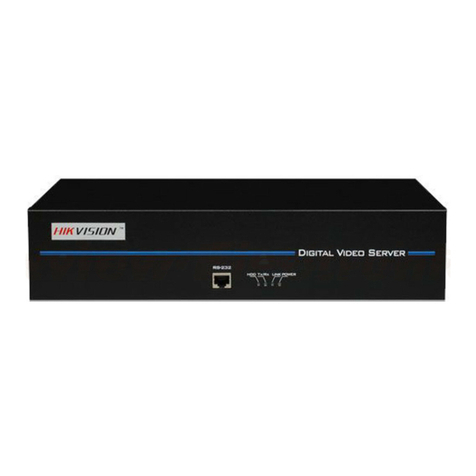
HIK VISION
HIK VISION DS-6101HFI-SATA user manual