Holtek HT45F0058 User manual

Low Component Cost Single Tube Induction Cooker
WAS-2041EN V1.00 1 / 19 February 25, 2021
Low Component Cost Single Tube
Induction Cooker
D/N: WAS-2041EN
Introduction
A traditional kitchen stove heats foods over an open flame while the induction cooker utilises an
electromagnetic induction method to implement a heating function. In this way foods are cooked
by the heat of the cookware itself. Compared to the open flame heating method, an induction cooker
can increase the heating efficiency by 90%. As a safety feature, the induction cooker will be
automatically shut off if the cookware has been removed for a certain period of time. During
cooking, the cooktop surface temperature is much lower than a traditional kitchen stove and in
addition, the induction cooker and cookware are more easily cleaned than a traditional stove.
A traditional single-tube induction cooker pursues a higher power, however in an IGBT resonance
circuit the reverse interference signal is also increased. The traditional way to solve this is to improve
the component specifications to enhance the induction cooker EMI circuit reverse interference signal
filtering capabilities. This reference design utilises a frequency jittering function to adjust the induction
cooker IGBT switching frequency, thus effectively decreasing the reverse voltage generated due to the
induction cooker IGBT switching as well as reducing the EMI CE conducted interference. In this way,
a lower component cost EMI circuit solution is provided. As the HT45F0058 includes an integrated
hardware frequency jittering circuit, this can effectively reduce the software load when compared with
the method whereby a software frequency jittering function is used.
Figure 1. Application Block Diagram

Low Component Cost Single Tube Induction Cooker
WAS-2041EN V1.00 2 / 19 February 25, 2021
Application Areas
Induction cookers, IH rice cookers, IH milk frothers.
Solution Feature
1. Dedicated hardware for frequency jittering: reduced software load, higher precision control.
If a software frequency jittering function is used, the software will occupy a section of the
program space and the CPU resources in order to achieve precise control. However, this
generally fails to obtain good control effects in actual product development due to software
resource limitations. This solution provides a PPG hardware frequency jittering circuit, which
uses a zero-crossing comparator to trigger a timer, the PPG width will be changed by
hardware at corresponding time points, which will eliminate the need to have frequency
jittering software. In this way, good control can be ensured and in addition, the software
execution time and program space requirements can be reduced. Using this method,
development difficulties can be reduced and the development time can be shortened.
2. Lower component costs: the MCU includes several integrated comparators and an operational
amplifier and the frequency jittering can reduce the component specifications.
The HT45F0058 includes several integrated comparators and an operational amplifier which
can be used for induction cooker over voltage and over current protection. In addition to
reduced external components, the PCB layout is also simplified. Enabling the hardware
frequency jittering function when the induction cooker operates at its maximum power can
effectively reduce the IGBT reverse voltage and the EMI conducted interference. As a result,
the IGBT component can be selected to have a lower voltage-resistant specification and the
safety capacitors can also select a lower capacitance value specification.
Operating Principles
By using a rectifier circuit in the induction cooker, the 50/60Hz alternating current can be converted
to direct current, which will pass through the resonance circuit and the IGBT switching circuit and
then be converted to a 20~35kHz high-frequency voltage. The high voltage results in a high-speed
varying current on the induction cooker coil panel which then generates a high speed varying
magnetic field. The magnetic field lines pass through the metal cookware on the cooktop surface
and generate eddy currents on the bottom of the metal cookware due to electromagnetic induction.
It is this which implements the heating function. The principle diagram is shown in Figure 2.
Cookware
Eddy Current
Eddy CurrentMagnetic Field Line
Cooktop Surface
Figure 2. Induction Cooker Heating Principle

Low Component Cost Single Tube Induction Cooker
WAS-2041EN V1.00 3 / 19 February 25, 2021
When the induction cooker operates at higher power levels of more than 1600W, the Holtek low
EMI component induction cooker solution can change the induction cooker IGBT resonance circuit
switching frequency using a frequency jittering function. As a result, when it is close to the peak
value of the mains voltage at 90 degrees, the IGBT VCE voltage can be effectively reduced as shown
in Figure 3. In addition, the higher electromagnetic interference signal energy will be dispersed into
different frequency spectrums, thus increasing the EMI CE conducted test margin.
Figure 3. Frequency Jittering Waveform
Functional Description
Solution Features
Input voltage range: AC 150V~265V 50/60Hz
Standby power consumption: < 5W
Communication interface: I2C – the power heating board is the software emulated master while
the touch & display board is the hardware circuit slave
Heating power: 100W~2000W (>1000W: continuous heating is used; <1000W: intermittent
heating is used.)
Protection functions: over/under voltage protection, over current protection, cooktop surface
overheating protection, IGBT overheating protection, surge voltage protection
EMI test: CE conducted interference test margin (2000W): > 2.82dB (avg.)
DP power interference test margin (2000W): > 10dB
Solution Function
An induction cooker solution is shown in Figure 4. This solution is suitable for general household
and commercial small hot pot cooking. The induction cooker supports multiple cooking modes,
such as fast heating, slow heating, soup, steam, porridge, hot pot and super high heating. The
differences between these modes are in the different heating power levels, time settings and
temperature control.

Low Component Cost Single Tube Induction Cooker
WAS-2041EN V1.00 4 / 19 February 25, 2021
Table 4. Induction Cooker
Operation Description
After the power cord is plugged in, the induction cooker enters the standby mode in which the fan
remains off, the buzzer sounds once and the 7-segment display and LEDs are all on and flashing.
After this, the “on/off” LED button on the control panel starts to flash, indicating that the induction
cooker initialisation has been completed. After pressing the “on/off” button, the LEDs will remain
on and the panel displays “----” waiting for further operations. When an error occurs, the display
area will display an error code.
Functional Key
Description
Pause Stop the current cooking mode, press again to resume the cooking mode
Smart
Press this button to switch between the following modes.
Fast heating mode: 100W~2000W adjustable power
>1000W: continuous heating is used; <1000W: intermittent heating is used.
Slow heating mode: 100W / 300W / 600W adjustable power
Soup mode: auto-adjustable power, use the time setting to setup a heating time,
ranging from 10 to 240 minutes in 10-minute increments.
Steam mode: auto-adjustable power, use the time setting to setup a heating
time, ranging from 10 to 240 minutes in 10-minute increments.
Porridge mode: The heating temperature in the pot can be adjusted, ranging
from 60℃ to 240℃ in 20°C increments.
Hot Pot 100W~2000W adjustable power
>1000W: continuous heating is used; <1000W: intermittent heating is used.
Super High Heating
2000W output power
Table 1. Solution Function Table
Error
Code Description
Error
Code
Description
E0
No cookware: Triggered when no cookware
is detected or the cookware is outside the
valid cooking zone.
E3
IGBT overheating: Triggered when the NTC
detected temperature is higher than 110℃
(±10℃)
E4
Triggered when an IGBT NTC open circuit
or short circuit condition occurs (2 minutes
for pre-heating is required)
E5
Cooktop surface overheating: Triggered when
the NTC detected temperature is higher than
the setup value of 160℃ (±10℃)
E6
Triggered when a cooktop surface NTC open
circuit or short circuit condition occurs (2
minutes for pre-heating is required)
E7
Mains supply over current: Triggered when
the A/D sampled current value is higher than
the setup value of 10A (±1A)
E8
Mains supply over voltage: Triggered when
the A/D sampled voltage value is higher
than the setup value of 265V(±10V)
E9
Mains supply under voltage: Triggered when
the voltage supply is lower than the setup
value of 150V (±10V)
EA
Communication failure: Triggered when an
I2C communication is interrupted or a
communication error occurs
Table 2. Induction Cooker Error Code Introduction

Low Component Cost Single Tube Induction Cooker
WAS-2041EN V1.00 5 / 19 February 25, 2021
Reference Design Description
The induction cooker can be divided into two parts, the power heating board and the touch & display
board. The power heating board contains the complete system power supply for the induction
cooker as well as the heating power control. The selection of the heating power and the induction
cooker on/off state on the power heating board are adjusted by the current heating power and other
settings on the touch & display board obtained via the I2C communication interface. The touch &
display board uses touch keys and LED display functions to provide a human-machine interface
(HMI) control. The touch keys can be used to select the desired operating mode while the LED
display function displays the current selected operating mode and power setting. The induction
cooker function error is also displayed on the touch & display board. In this solution, when the
induction cooker operates at a high power level of 1600W~2000W, the IGBT switching frequency
can be adjusted by a frequency jittering function thus reducing the maximum reverse voltage across
the IGBT VCE and the EMI conducted interference.
Hardware Description
1
5
23
8
10
11
4
7
6
9
Figure 5. Power Heating Board Schematic Diagram
The AC supply for the power heating board is divided into two paths after passing through the EMI
circuit. This is used as the heating main power for the switching power supply circuit(11) and the
resonance circuit(2). The switching power supply circuit(11) outputs two kinds of power supplies,
+18V and +5V. The +18V power is supplied to the buzzer & fan control circuit(4) and the IGBT
driving circuit(3). The +5V power is supplied to the HT45F0058 peripherals such as the cooktop
surface overheating protection circuit(6), IGBT overheating protection circuit(7) and the
communication circuit(9).

Low Component Cost Single Tube Induction Cooker
WAS-2041EN V1.00 6 / 19 February 25, 2021
The induction cooker power control is implemented depending upon the current detection circuit(5)
and the voltage detection circuit(10). These two circuits are used to detect the present operating
current value and the voltage value, which are used to calculate the present power. The system will
determine whether to increase or decrease the IGBT on-time to adjust the power according to the
present operating power. The measured current and voltage values are also used as the reference
source for the over/under voltage protection and for the over current protection functions.
In addition to the over/under voltage protection and over current protection functions, this solution
also contains a surge voltage protection circuit(8), a cooktop surface overheating protection circuit(6)
and an IGBT overheating protection circuit(7), etc. When any of the above protection functions are
triggered during induction cooker operation, the system determines whether to reduce power or stop
heating for safety reasons.
Touch & display board: The power heating board provides the power supply to the touch & display
board via the communication circuit. This voltage supply is regulated to a 5V voltage output by a
voltage regulation filtering circuit and is supplied as the touch & display board main power. The
LED display circuit displays the current induction cooker operating mode and function. The touch
keys are provided as a human-machine operating interface, with which functions can be selected.
The induction cooker will then control the power heating board operation according to the selected
function.
LED display circuit
Buzzer Control Circuit
(N.C.)
Communication
circuit
Voltage regulation
filtering circuit
Touch key circuit
Figure 6. Touch & Display Board Schematic Diagram

Low Component Cost Single Tube Induction Cooker
WAS-2041EN V1.00 7 / 19 February 25, 2021
Layout and Hardware Considerations
There are some important considerations for the power heating board.
1. The filter capacitors next to the MCU should be located as close to VDD and VSS as possible
and the ground of the peripheral circuit should be a single point grounded to the source capacitor
ground. The resonance circuit ground should be separated from other peripherals to avoid the
IGBT switching interference signal influencing other peripherals. Also ensure that the routes go
through a voltage regulation filtering capacitor to filter out any noise.
2. Routes from the bridge rectifier to resonance circuit should be widened as these routes carry
larger currents. The resonance capacitor should be as close as possible to the induction cooker
resonance coil.
3. Routing which is close to the high power area and the low power zone should be separated via
the KEEPOUT layer.
4. The IGBT E pin and the ground of the bridge rectifier IC should be widened and a single point
connected via a constantan wire, which is then single point routed to the current detection circuit.
Figure 7. Power Heating Board PCB
There are some considerations for the Touch MCU BS86D12C on the touch & display board.
1. The filter capacitors next to the MCU should be located as close to VDD and VSS as possible.
2. When there are multiple touch keys on the PCB, the MCU should be located to the center position
among these touch keys, thus shortening the route to reduce any effects of interference. Using
capacitors between the MCU corresponding KEY pins and VSS is an effective method of adjusting
the touch sensitivity. Wires can be routed from the MCU to the KEY pins on the copper floor to
reduce any interference on the touch keys caused by signal wires. It should be noted that any touch
key routing should be located as far as possible from the high frequency signal paths.
Figure 8. Touch & Display Board PCB

Low Component Cost Single Tube Induction Cooker
WAS-2041EN V1.00 8 / 19 February 25, 2021
PCB BOM Table
Table 3. Power Heating Board PCB BOM Ta b le

Low Component Cost Single Tube Induction Cooker
WAS-2041EN V1.00 9 / 19 February 25, 2021
Table 4. Touch & Display Board PCB BOM Table
Software Description
Software Resource Utilisation Introduction
HT45F0058 - Power Heating Board
BS86D12C - Touch & Display Board
V
DD
5.0V
5.0V
Oscillators
16MHz
8MHz
ROM
Uses 2868×16, occupancy rate: 70%
Uses 3043×16, occupancy rate: 37%
RAM
Uses 153×8, occupancy rate: 59%
Uses 307×16, occupancy rate: 59%
Stack
Uses 4 levels
Uses 4 levels
Timer
Uses TM(0~2)
Uses CTM0, Time Base 0
Other
Peripherals
1. ADC - AN1、AN3、AN4、AN5 for mains
supply, current and temperature measurement
2. PPG - IGBT switching signal source
3. CMP0, CMP1, CMP2, CMP3 used for resonance
circuit and induction cooker protections
4. OPA - current signal amplification
5. OVP - mains supply AC zero-crossing detection
6. PCK - passive buzzer signal source
7. I/Os - I2C Master end emulation
1. Touch Keys (KEY1~KEY8)
2. I2C
3. I/Os - for 7-segment display and
LED display
Table 5. Software Resource Utilisation
Power Heating Board Main Program Flowchart Description
As shown in Figure 9, the power heating board main program first executes initialisation, which
includes the I/O port settings related to the induction cooker register functions, power calculation
curves, etc. After initialisation, the voltage, current, IGBT temperature and cooktop surface
temperature are measured. Protection mechanisms will be triggered if the measurement results
exceed the limit range, then the corresponding flags will be set high, the corresponding error codes
will be stored into the communication memory and be sent to the touch & display board in the next
communication. The induction cooker main function control includes protection mechanisms, I2C
communication, power adjustment, etc.

Low Component Cost Single Tube Induction Cooker
WAS-2041EN V1.00 10 / 19 February 25, 2021
Comparator hardware protection interrupt: The surge voltage protection and IGBT reverse voltage
protection functions are implemented by hardware for a faster response speed. When these
protections are triggered, the system will turn off the heating function or reduce the heating power
first, further processing will be executed by software interrupt routines. If surge voltage protection
is triggered, the induction cooker heating function will be turned off to protect the induction cooker
from damage. If an IGBT reverse voltage protection is triggered, the induction cooker power will
be reduced by hardware to avoid the IGBT from being damaged.
Set high the corresponding protection
flags / store the error codes into the
communication memory
Measure the voltage (Mains supply),
current, IGBT temperature, cooktop
surface temperature
Measurement results trigger
the protection mechanism?
Induction cooker main
function control
N
System setting
initialis atio n
Start
CMP: surge voltage/IGBT over
voltage protection interr upt
Comparator
hardware protection
interrupt
Y
Figure 9. Power Heating Board Main Program Flowchart
Induction Cooker Main Function Control Flowchart Description
As shown in Figure 10, the induction cooker main function control flowchart executes specific
functions in several fixed periods. Over current protection detection, IGBT overheating protection
detection, NTC detection and protection release, etc., are executed every 1s. The I2C
communication, cookware detection and induction cooker power adjustment are executed every
100ms. The induction cooker On/Off and power setting, cookware removal detection as well as I2C
communication time-out processing are executed every 20ms. The system will determine if the time
has reached a value of 1s, 100ms and 20ms respectively every 1ms and then set high any
corresponding flags. The corresponding functions will be executed according to these flags in the
next process.
The system determines every second whether a mains supply over voltage or under voltage
condition occurs, whether an over current condition occurs and whether the IGBT temperature and
cooktop surface temperature requiring protection. It will then execute the corresponding protection
functions, such as adjusting the power or turning off the induction cooker heating function. For the

Low Component Cost Single Tube Induction Cooker
WAS-2041EN V1.00 11 / 19 February 25, 2021
IGBT overheating protection, when the IGBT temperature exceeds 68°C and such a condition lasts
for more than 5 minutes, the system will reduce the induction cooker heating power until the IGBT
temperature reduces to lower than 68°C, after which it will resume the heating power to its normal
level. As the temperature protection and control is the key protection feature, an error on the
temperature sensor NTC may result in the induction cooker component being damaged by an
overheating condition, which is likely to lead to a dangerous situation. The NTC detection is
implemented by checking if the maximum or minimum values of the read back A/D values exceed
the range to determine if there is an open circuit or short circuit problem on the NTC sensor. For
the protection release procedure, if the mains supply and current has triggered an induction cooker
protection function, and the protection mechanism trigger condition has been eliminated for a
certain period of time, the induction cooker will resume normal operation and clear the error code.
I2C communication: The power heating board acts as the master, which transmits the current IGBT
temperature and cooktop surface temperature A/D measurement values as well as the induction
cooker state code to the touch & display board. It also receives the current selected induction cooker
function from the touch & display board.
Cookware detection: The system sends a pulse signal to the coil panel through the IGBT switch and
detects the number of times the Comparator 0 output state changes within a 2ms period. If the
number is less than a fixed value, this is taken as proof that there is cookware present, otherwise it
will be taken that no cookware is present.
Power calculation and adjustment: This function is implemented by comparing the power calculated
using the A/D sampled voltage and current values, AD_Vac & AD_Iac, with the target power. If
these values do not match, the PPG pulse width should be adjusted to obtain a power value close to
the setup power.
Induction cooker on/off and power setting: Check the current induction cooker on/off state. If the
induction cooker is on, users can setup the target induction cooker heating function on the touch &
display board. The induction cooker heating function will adjust the PPG width according to the setup
power to reach the desired power. If the power is more than 1600W, the frequency jittering function
will be turned on.
Cookware removal detection: During heating, if the current instantly decreases sharply, this will be
taken to be a situation where the cookware has been removed.
I2C communication time-out processing: If the I2C communication times-out, the induction cooker
heating function will be disabled.

Low Component Cost Single Tube Induction Cooker
WAS-2041EN V1.00 12 / 19 February 25, 2021
Induction cooker main function
control
RET
1ms time counting
function processing
Induction cooker On/Off
and power setting
I
2
C communication
t im e-out processing
Cookware removal
detection
Cookware detection Power calculation and
adjustment
NTC detection
IGBT overheating
protection detection Protection release
I
2
C communication
Time counting reaches 1s?
Time counting reaches 100ms?
Time counting reaches 20ms?
Time counting reaches 1ms?
N
N
N
Y
Y
Y
N
Power calculation and
adjustment function:
PowerControl_Task( );
Over current protection
detection
Y
Figure 10. Induction Cooker Main Function Control Flowchart
Touch & Display Board Main Program Flowchart Description
As shown in Figure 11, the touch & display board main program flowchart executes a touch
program function library initialisation and a system setting initialisation. After this the system enters
the main program, which includes “Execute key actions”, “Update LED display”, “Error code
processing” and “Function menu processing”. In the “Execute key action” procedure, it should be
determined which touch key is pressed for which the corresponding descriptions are listed in Table
6. The system executes the relevant key function according to the touch function returned value and
updates the data to be transmitted for the next I2C communication to the power heating board. After
this, the touch & display board updates the LED display. The “Error code processing” procedure
determines if there is an error on the power heating board according to the present data acquired
from the power heating board and modifies the value on the LED display panel in the next display.
The “Function menu processing” procedure operates in the present operating mode and counts if
there is a preset timing function. When the time has elapsed, the system will inform the power
heating board to turn off the heating function in the next communication.
Function
On/Off Super High
Heating
Start/Pause
+ Key - Key Hot Pot Smart
Returned
value
0x008 0x004 0x002 0x001 0x080 0x020 0x010
Tabl e 6. Touch Function Returned Value Corresponding Key Function Table

Low Component Cost Single Tube Induction Cooker
WAS-2041EN V1.00 13 / 19 February 25, 2021
Touch program
initialis atio n
Start
Receive the induction
cooker state value and
transmit the display board
setup values
I2C Slave
Interrupt
USER_PROGRAM
System setting
initialisation
Execute key action
Update LED d is play
Error code processing
Function menu
processing
Figure 11. Touch & Display Board Main Program Flowchart
Function Library Description
In the power heating board, the power calculation curve initialisation and the power calculation and
adjustments are implemented using a function library. The descriptions for these functions,
including input, output, relevant memory and function description are listed in the following tables.
1. PowerCalculation_Init( )
Function Name
void PowerCalculation_Init( )
Function
Power calculation curve initialisation
Input
NULL
Output NULL
Description initialise the relevant variables of power control
Tabl e 7. PowerCalculation_Init( ) Function Description
2. PowerControl_Task( )
Function Name
void PowerControl_Task( )
Function
Power Control Function
Input
AD_Iac, AD_Vac, PowerStep, bPowerStepChanged
Output
PPGTA_copy
Description
1. The target power can be adjusted either by users setting the touch & display
board or value modification caused by a triggered protection.
2. Calculate the actual power according to the voltage and current A/D values
3. Compare the actual power with the target power, adjust the PPG variable
PPGTA_copy
4. Variable descriptions
AD_Iac: operating current A/D value
AD_Vac: operating voltage A/D value
PowerStep: target power intermediate variable, target power = PowerStep×20
bPowerStepChanged: target power changed flag
Tabl e 8. PowerControl_Task( ) Function Description

Low Component Cost Single Tube Induction Cooker
WAS-2041EN V1.00 14 / 19 February 25, 2021
In the touch & display board, the touch key state reading function in the touch function library is
used. It can be determined which key was pressed by the user via the return value of the touch key
state reading function.
1. BS86D12C used library function description
Function Name
void GET_KEY_BITMAP( )
Function Read the touch key state and output the corresponding value in bitmap form
Input
NULL
Output
DATA_BUF[0] = KEY8(MSB) ~ KEY1(LSB)
DATA_BUF[1] = KEY12(MSB) ~ KEY9(LSB)
(0=released, 1=pressed)
Description Use this function to read the touch key state to determine whether the touch key is
pressed or not.
Tabl e 9. GET_KEY_BITMAP( ) Function Description
Solution Communication Description
The power heating board and touch & display board communicate with each other using the I2C
protocol. The power heating board uses the MCU I/Os to emulate the I2C master ends while the
touch & display board has an integrated hardware I2C slave function. The communication is
executed once every 100ms. Table 10 shows the communication formats between the power heating
board and the touch & display board. The “S” indicates the I2C start bit, the “Address & R/W bit”
is 1 byte data, in which bit [7:1] is the I2C communication address and bit[0] is the R/W bit. Values
in the data field are all in 1 byte format. The “Checksum” is the sum of the data values in the data
filed. The “P” indicates the I2C stop bit. Table 11 shows the data format in the power heating board
data field. The “IGBT value” and “BOT Value” are temperature A/D values, the “IHStatus” includes
the cookware detection condition and induction cooker operating state error codes. Table 12 shows
the data format in the touch & display board data field. When the power heating board transmitting
data is received, the touch & display board will return its current settings which includes the
induction cooker on/off state, buzzer setting, induction cooker fan setting, target heating power as
well as the power heating mode setting of either continuous heating or intermittent heating. In
addition, the communication data validity can be checked using two methods. One is to determine
whether the checksum value is equal to the sum of the data values in the data field and the other is
to determine whether the one’s complement of the IHStatus[7:5] value is equal to the IHStatus[2:0]
value, or whether the one’s complement of the ControlSet[7:4] value is equal to the ControlSet[3:0]
value.
Power Heating Board transmitting data format (I2C Master)
S Address &
R/W bit
Data Field
Checksum
P
IGBT Value
BOT Value
IH Status
Checksum
P
Touch & Display Board transmitting data format (I2C Slave)
S Address &
R/W bit
Data Field Checksum P
ControlSet
PowerSet
ModeSet
Checksum
P
Tabl e 10. Solution Communication Format

Low Component Cost Single Tube Induction Cooker
WAS-2041EN V1.00 15 / 19 February 25, 2021
Power Heating Board transmits the operating state, IGBT temperature and cooktop surface temperature
A/D sampled values
Data Field
Parameter Data Content
IGBT Value
IGBT temperature A/D sampled value
BOT Value
Cooktop surface temperature A/D sampled value
IHStatus
(Operating
state)
Bit7
Bit6
Bit5
Bit4
Bit3
Bit2
Bit1
Bit0
Checksum
Cookware
detection
Power heating board operating state
error code
One’s complement of the
bit[2:0] value of the
Power heating board
operating state error code
0: Cookware
present
1: No cookware
present
0000: Normal operation
0011: IGBT overheat
0100: IGBT temperature sensor fault
0101: Cooktop surface overheating
0110: Cooktop surface temperature sensor fault
0111: Resonance over current
1000: Mains supply over voltage
1001: Mains supply under voltage
Tabl e 11. Power Heating Board Data Field Data Format
Touch & Display Board transmits induction cooker control settings, heating power and heating mode
Data Field
Parameter Data Content
ControlSet
Bit7
Bit6
Bit5
Bit4
Bit3
Bit2
Bit1
Bit0
Checksum
ON/OFF
BUZ[1:0]
FAN
One’s complement of the
ControlSet[3:0] value
Switch control
0: Off
1: On
Buzzer
00: No sound
01: Sounds for 200ms
10: Sounds twice continuously
11: Sounds for 1s
Fan control
0: Off
1: On
PowerStep
PowerStep is used for both power and temperature. Values 1~9 are for temperature setting,
values 10~100 are for power setting value M. The power setting value corresponding setup
power can be calculated by the equation P=M×20, in which P is the induction cooker heating
power value. For example, when M=50, the heating power is 1000W.
ModeSet
1: Continuous power
2: Intermittent power
Tabl e 12. Touch & Display Board Data Field Data Format
Test Data
EMI Circuit Condition
The test results shown below show the EMI test data when the induction cooker operates at a power
level of 2000W. The EMI circuit condition is shown in Figure 12. The C3(D) component is an 8µF
safety capacitor and the C10(D) component is a 5µF safety capacitor. The CE and DP test results,
which are tested with or without frequency jittering respectively, are compared.
Figure 12. EMI Circuit Condition

Low Component Cost Single Tube Induction Cooker
WAS-2041EN V1.00 16 / 19 February 25, 2021
Test Waveforms
No Frequency Jittering
With Frequency Jittering
IGBT VCE Voltage(Max.)= 1.180kV
IGBT VCE Voltage(Max.)= 1.132kV
Yellow waveform (CH1) MCU PPG output waveform
Green waveform (CH4) IGBT VCE waveform (Induction Cooker LC parallel resonance reverse voltage)
Red waveform (CH M) MCU PPG output negative pulse width trend line
Under the same power condition, the IGBT VCE voltage when using frequency jittering can be effectively reduced by about 48V.
Tabl e 13. Waveform Differences with & without Frequency Jittering
CE Data
Comparing the following table data, when the power is 2000W, the CE minimum average margin
without frequency jittering is only 1.39dB while the one with frequency jittering is 2.82dB. This
shows that the minimum average margin with frequency jittering is increased by 1.43dB when
compared to the minimum average margin without frequency jittering.
No Frequency Jittering
With Frequency Jittering
Tabl e 14. Comparison of the CE Test Results Tested with & without Frequency Jittering

Low Component Cost Single Tube Induction Cooker
WAS-2041EN V1.00 17 / 19 February 25, 2021
DP Data
The DP test results with and without frequency jittering are shown below, the margins are all more
than 10dB.
No Frequency Jittering
With Frequency Jittering
Tabl e 15. Comparison of the DP Test Results Tested with & without Frequency Jittering
Difference Comparison of Frequency Jittering Influence on EMI
Condition
Component No Frequency Jittering With Frequency Jittering
C3(D)
8µF / 275V
AC
C10(D)
5µF / 275V
AC
L2(D) 360µH
Conducted Interference
CE margin (@2000W) AVG: +1.39dB(Pass) AVG: +2.82dB(Pass)
Power Interference
DP margin (@2000W) >10dB(Pass) >10dB(Pass)
Note: 1. The conducted/power interference margin +x dB represents the minimum margin to the limit is x
db, while the –x dB represents the limit exceeding the maximum x dB.
2. These results originate from the Holtek laboratory. The test regulations adopted are the EU
certification EN55014-1. There may by 1~2dB difference in test results between different
laboratories.
Tabl e 16. Difference Comparison of Frequency Jittering Influence on EMI
Solution Comparison
Compared with traditional solutions, the HT45F0058 frequency jittering solution can reduce the
IGBT reverse voltage value by about 48V using its integrated frequency jittering function with the
same function, cost and maximum power conditions. In addition, the EMI conducted test CE margin
is also increased by 1.42dB. Traditional solutions do not support frequency jittering functions and
as a result, a higher safety capacitance value is required to increase the EMI conducted test CE
margin, which leads to higher PCBA costs. The Holtek solution can use the frequency jittering
function to reduce the voltage across the IGBT VCE and increase the EMI conducted test CE margin
without the need for increased circuit costs. In this solution, users can use lower voltage-resistance
IGBT components and lower safety capacitance values which will also result in lower costs.

Low Component Cost Single Tube Induction Cooker
WAS-2041EN V1.00 18 / 19 February 25, 2021
Item
Holtek HT45F0058 Solution
with Frequency Jittering
Traditional Solution
without Frequency Jittering
Function
Same
EMI CE difference Same
2000W IGBT maximum
reverse voltage
Lower Higher
BOM table cost
Can choose lower voltage-resistance IGBT and
lower capacitance value safety capacitors
Higher costs for IGBT and
safety capacitors
Tabl e 17. Solution Comparison Table
Conclusion
This document has provided a low EMI component cost single tube induction cooker solution and
has introduced a single tube induction cooker power heating board and touch & display board
operating principles, hardware description, software description as well as communication
protocols. When the induction cooker operates at a high power level, a voltage drop will be
generated across the C and E terminals of the IGBT due to the resonance circuit charging and
discharging. Here, a frequency jittering function can be used to effectively reduce the maximum
voltage across the IGBT C and E terminals. In addition, the frequency jittering function can reduce
the influence of EMI CE conducted interference. As a result, the component cost, including the
IGBT voltage-resistance specification and the safety capacitance value in the EMI circuit, can be
reduced. Using the HT45F0058 hardware frequency jittering circuit can also greatly reduce the
MCU program loading, thus improving the MCU efficiency.
Reference Files
Reference files: HT45F0058, BS86D12C Datasheet.
Reference application note: HT45F0058 Frequency Jittering Applications.
For more information, refer to the Holtek official website: www.holtek.com .
Version and Modification Information
Date
Author
Issue
2020/10/19 陳世諭 Rekkles V1.00

Low Component Cost Single Tube Induction Cooker
WAS-2041EN V1.00 19 / 19 February 25, 2021
Disclaimer
All information, trademarks, logos, graphics, videos, audio clips, links and other items appearing
on this website ('Information') are for reference only and is subject to change at any time without
prior notice and at the discretion of Holtek Semiconductor Inc. and its related companies
(hereinafter 'Holtek', 'the company', 'us', 'we' or 'our'). Whilst Holtek endeavors to ensure the
accuracy of the Information on this website, no express or implied warranty is given by Holtek to
the accuracy of the Information. Holtek will bear no responsibility for any incorrectness or leakage.
Holtek will not be liable for any damages (including but not limited to computer virus, system
problems or data loss) whatsoever arising in using or in connection with the use of this website by
any party. There may be links in this area, which allow you to visit the websites of other companies.
These websites are not controlled by Holtek. Holtek will bear no responsibility and no guarantee to
whatsoever Information displayed at such sites. Hyperlinks to other websites are at your own risk.
Limitation of Liability
In no event shall Holtek Limited be liable to any other party for any loss or damage whatsoever or
howsoever caused directly or indirectly in connection with your access to or use of this website, the
content thereon or any goods, materials or services.
Governing Law
The Disclaimer contained in the website shall be governed by and interpreted in accordance with
the laws of the Republic of China. Users will submit to the non-exclusive jurisdiction of the
Republic of China courts.
Update of Disclaimer
Holtek reserves the right to update the Disclaimer at any time with or without prior notice, all
changes are effective immediately upon posting to the website.
Table of contents
Popular Cooker manuals by other brands
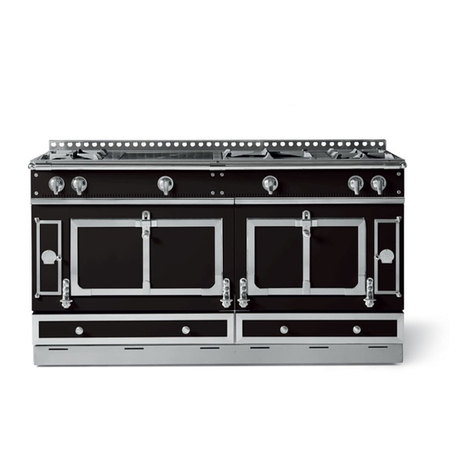
La Cornue
La Cornue Chateau 150 G45 installation guide
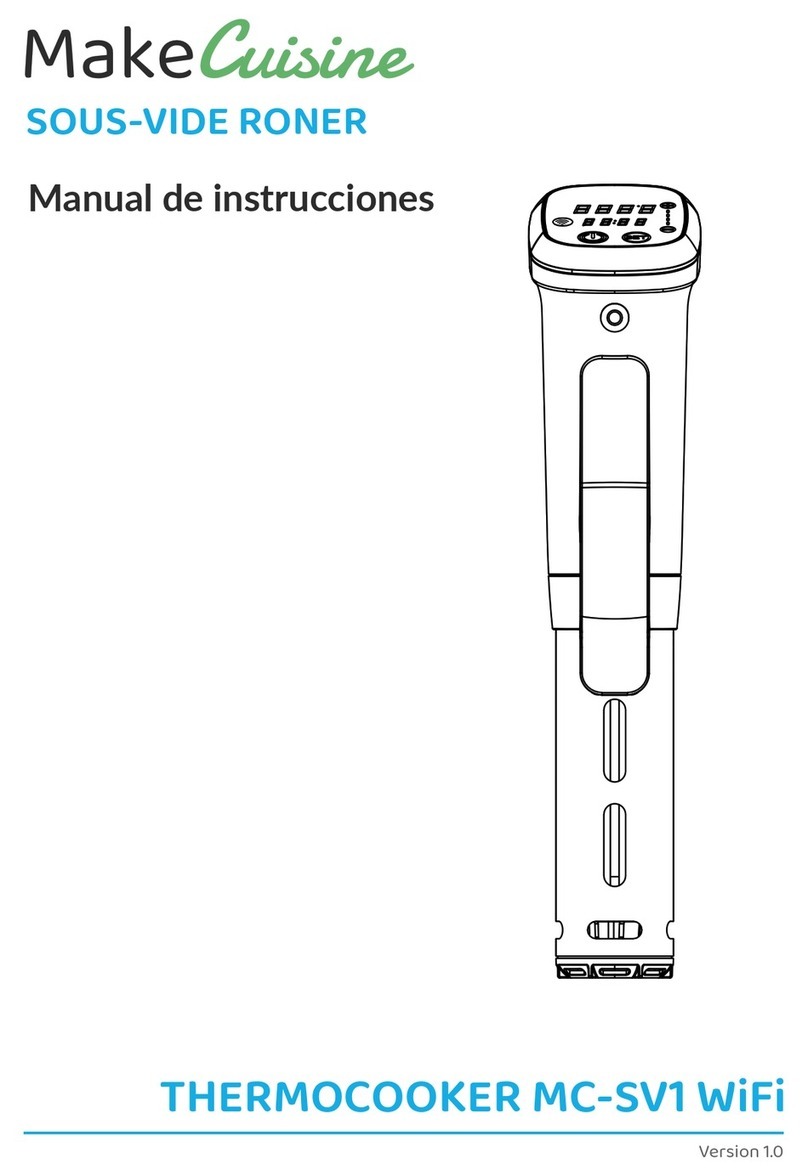
Make Cuisine
Make Cuisine MC-SV1 user manual

Lotus
Lotus TP-78G Installation and operating instructions
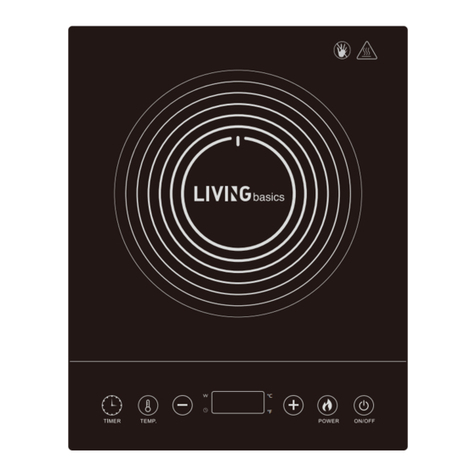
LIVING BASICS
LIVING BASICS LB-CI-C18D57 Operation manual
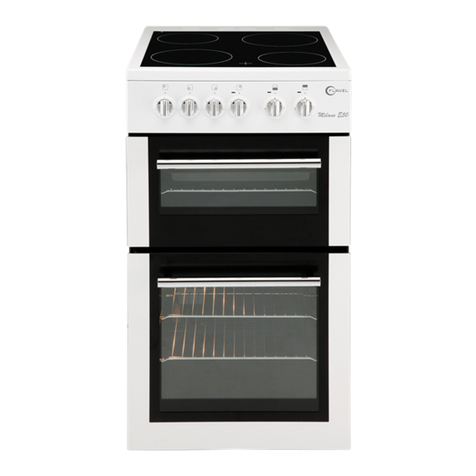
Flavel
Flavel ML5CDW User and installation guide
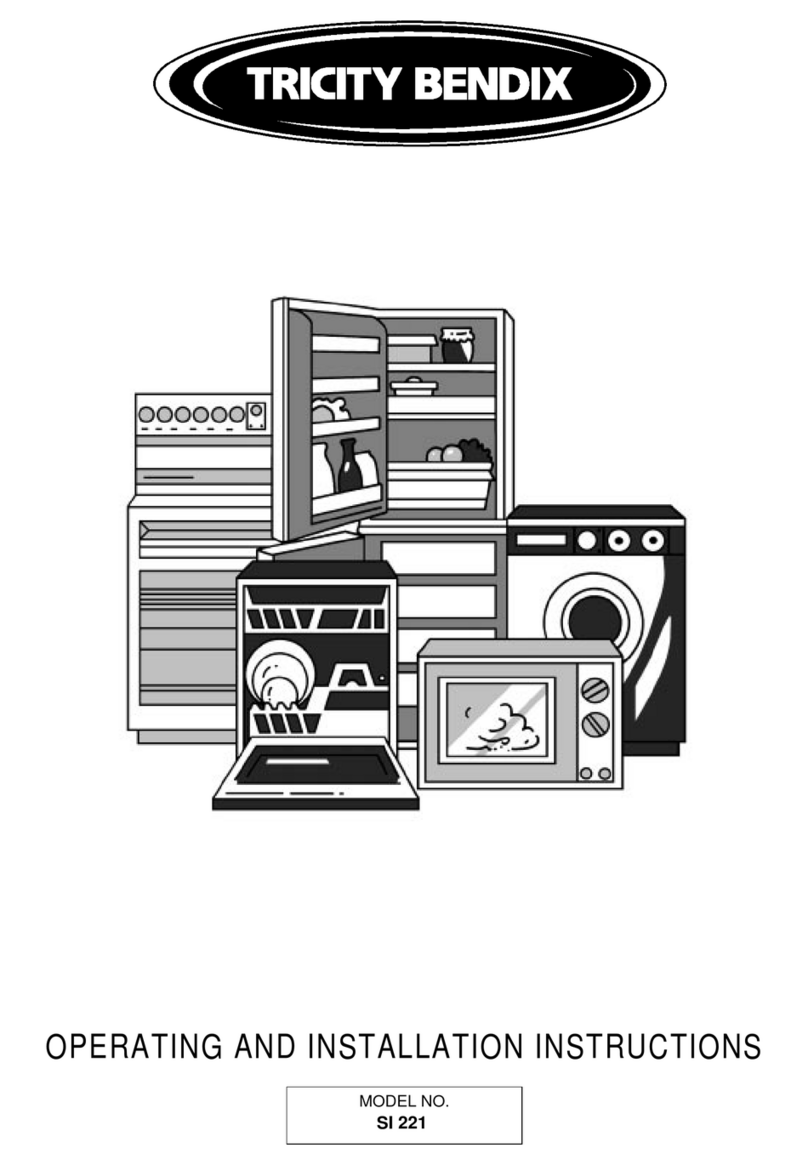
Tricity Bendix
Tricity Bendix SI 221 Operating and installation instructions
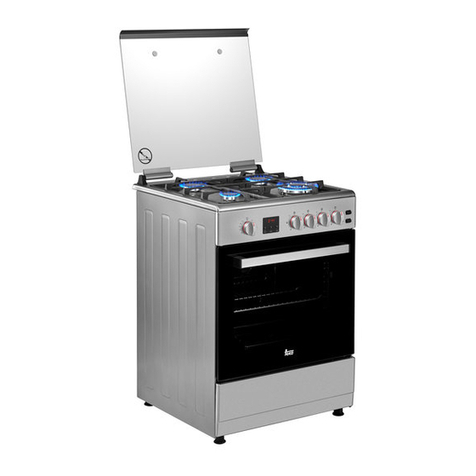
Teka
Teka FS 601 4GG SS LPG user manual

Rayburn
Rayburn Cookmaster 300K Installation & servicing instructions

arcelik
arcelik STO 810 DG quick start guide
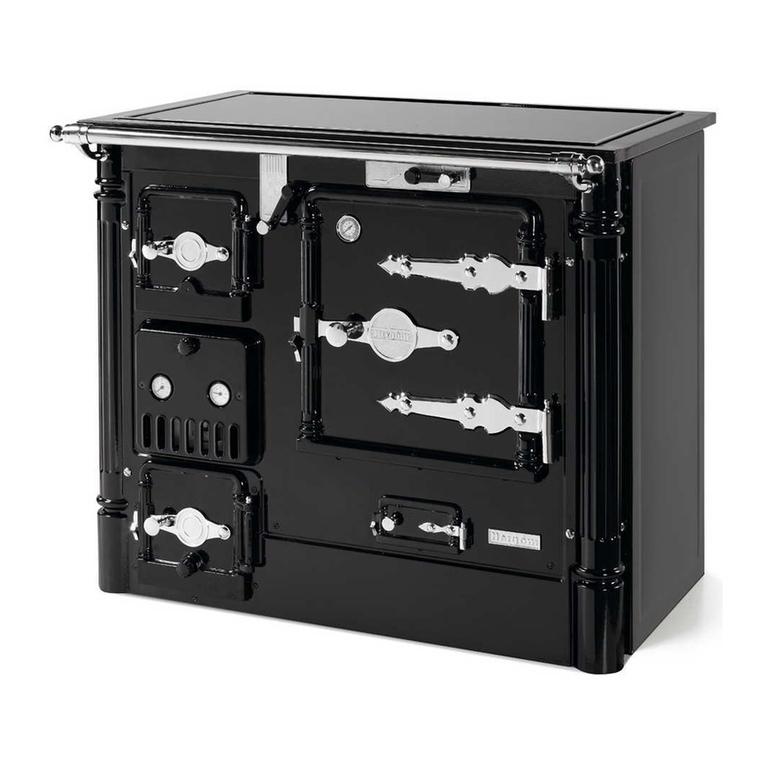
hergom
hergom L-08 CCE Installation, use and maintenance instructions

Bompani
Bompani BI540GAN Instructions for use and maintenance

Swift
Swift 500 Series quick start guide