HP D2846 User manual

SERVICE MANUAL
CHASSIS
SPECIFICATIONS
N3
D2846
US Model
Canadian Model
AEP Model
Chassis No. SCC-L04G-A
HP
COLOR GRAPHIC DISPLAY

– 2 –
D2846
SAFETY CHECK-OUT
(US Model only)
LEAKAGE TEST
The AC leakage from any exposed metal part to earth ground
and from all exposed metal parts to any exposed metal part
having a return to chassis, must not exceed 0.5 mA (500
microampers).
Leakage current can be measured by any one of three meth-
ods.
1. A commercial leakage tester, such as the Simpson 229 or
RCA WT-540A. Follow the manufacturers’ instructions to
use these instruments.
2. A battery-operated AC milliammeter. The Data Precision 245
digital multimeter is suitable for this job.
3. Measuring the voltage drop across a resistor by means of a
VOM or battery-operated AC voltmeter. The “limit” indica-
tion is 0.75 V, so analog meters must have an accurate low-
voltage scale. The Simpson 250 and Sanwa SH-63Trd are ex-
amples of a passive VOMs that are suitable. Nearly all battery
operated digital multimeters that have a 2 V AC range are suit-
able. (See Fig. A)
WARNING!!
NEVER TURN ON THE POWER IN A CONDITION IN
WHICH THE DEGAUSS COIL HAS BEEN REMOVED.
SAFETY-RELATED COMPONENT WARNING!!
COMPONENTS IDENTIFIED BY SHADING AND MARK
¡ON THE SCHEMATIC DIAGRAMS, EXPLODED
VIEWS AND IN THE PARTS LIST ARE CRITICAL FOR
SAFE OPERATION. REPLACE THESE COMPONENTS
WITH SONY PARTS WHOSE PART NUMBERS AP-
PEAR AS SHOWN IN THIS MANUAL OR IN SUPPLE-
MENTS PUBLISHED BY SONY. CIRCUIT ADJUST-
MENTS THAT ARE CRITICAL FOR SAFE OPERATION
ARE IDENTIFIED IN THIS MANUAL. FOLLOW THESE
PROCEDURES WHENEVER CRITICAL COMPO-
NENTS ARE REPLACED OR IMPROPER OPERATION
IS SUSPECTED.
AVERTISSEMENT!!
NE JAMAIS METTRE SOUS TENSION QUAND LA
BOBINE DE DEMAGNETISATION EST ENLEVÉE.
ATTENTION AUX COMPOSANTS RELATIFS À LA
SÉCURITÉ!!
LES COMPOSANTS IDENTIFIÉS PAR UNE TRAME ET
UNE MARQUE ¡SONT CRITIQUES POUR LA
SÉCURITÉ. NE LES REMPLACER QUE PAR UNE PIÈCE
PORTANT LE NUMÉRO SPECIFIÉ. LES RÉGLAGES DE
CIRCUIT DONT L’IMPORTANCE EST CRITIQUE POUR
LA SÉCURITÉ DU FONCTIONNEMENT SONT
IDENTIFIÉS DANS LE PRÉSENT MANUEL. SUIVRE CES
PROCÉDURES LORS DE CHAQUE REMPLACEMENT
DE COMPOSANTS CRITIQUES, OU LORSQU’UN
MAUVAIS FONCTIONNE-MENT EST SUSPECTÉ.
After correcting the original service problem, perform the fol-
lowing safety checks before releasing the set to the customer:
1. Check the area of your repair for unsoldered or poorly-sol-
dered connections. Check the entire board surface for solder
splashes and bridges.
2. Check the interboard wiring to ensure that no wires are
“pinched” or contact high-wattage resistors.
3. Check that all control knobs, shields, covers, ground straps,
and mounting hardware have been replaced. Be absolutely
certain that you have replaced all the insulators.
4. Look for unauthorized replacement parts, particularly transis-
tors, that were installed during a previous repair. Point them
out to the customer and recommend their replacement.
5. Look for parts which, though functioning, show obvious signs
of deterioration. Point them out to the customer and recom-
mend their replacement.
6. Check the line cords for cracks and abrasion. Recommend the
replacement of any such line cord to the customer.
7. Check the B+ and HV to see if they are specified values. Make
sure your instruments are accurate; be suspicious of your HV
meter if sets always have low HV.
8. Check the antenna terminals, metal trim, “metallized” knobs,
screws, and all other exposed metal parts for AC Leakage.
Check leakage as described below.
Fig. A. Using an AC voltmeter to check AC leakage.
1.5 k
Ω
0.15
µ
FAC
Voltmete
r
(0.75 V)
To Exposed Metal
Parts on Set
Earth Ground

– 3 –
D2846
MODE AT PRODUCTION
MODE 1 MODE 2 MODE 3 MODE 4 MODE 5 MODE 6 MODE 7 MODE 8 MODE 9 MODE 10
RESOLUTION
640 X 400 640 X 480 800 X 600 1024 X 768 1024 X 768 1280 X 10241280 X 10241280 X 10241600 X 12001600 X 1200
CLOCK
25.175 MHz 36.000 MHz 56.250 MHz 78.750 MHz 94.500 MHz 135.000 MHz 135.000 MHz 157.500 MHz 202.500 MHz 229.500 MHz
—HORIZONTAL—
H-FREQ
31.469 kHz 43.269 kHz 53.674 kHz 60.023 kHz 68.677 kHz 78.125 kHz 79.976 kHz 91.146 kHz 93.750 kHz 106.250 kHz
usec usec usec usec usec usec usec usec usec usec
H. TOTAL 31.778 23.111 18.631 16.660 14.561 12.800 12.504 10.971 10.667 9.412
H. BLK 6.356 5.333 4.409 3.657 3.725 3.319 3.022 2.844 2.765 2.44
H. FP 0.636 1.556 0.569 0.203 0.508 0.474 0.119 0.406 0.316 0.279
H. SYNC 3.813 1.556 1.138 1.219 1.016 1.422 1.067 1.016 0.948 0.837
H. BP 1.907 2.222 2.702 2.235 2.201 1.422 1.837 1.422 1.501 1.325
H. ACTIV 25.422 17.778 14.222 13.003 10.836 9.481 9.481 8.127 7.901 6.972
— VERTICAL —
V. FREQ(HZ) 69.931 Hz 85.008 Hz 85.061 Hz 75.029 Hz 84.997 Hz 72.005 Hz 75.025 Hz 85.024 Hz 75.000 Hz 85.000 Hz
lines lines lines lines lines lines lines lines lines lines
V. TOTAL 450 509 631 800 808 1085 1066 1072 1250 1250
V. BLK 50 29 31 32 40 61 42 48 50 50
V.FP 12111131111
V. SYNC 2333333333
V. BP 36 25 27 28 36 55 38 44 46 46
V. ACTIV 400 480 600 768 768 1024 1024 1024 1200 1200
— SYNC —
INT(G) NO NO NO NO NO YES NO NO NO NO
EXT(H/V)/POLARITY
YES N/P YES N/N YES P/P YES P/P YES P/P NO YES P/P YESP/P YES P/P YES P/P
EXT(CS)/POLARITY
NO NO NO NO NO NO NO NO NO NO
INT/NON INT NON INT NON INT NON INT NON INT NON INT NON INT NON INT NON INT NON INT NON INT
97.9.19 VER.
POWER SAVING FUNCTION
DIAGNOSIS
Failre
+B failure
Horizontal / Vertical Deflection failure,
Thermal protector
ABL protector
HV failure
Aging / Self Test
Power LED
Yellow →Off
(0.5 sec) (0.5 sec)
Yellow →Off
(1.5 sec) (0.5 sec)
Yellow →Off
(0.5 sec) (1.5 sec)
Yellow →Off →Yellow →Off
(0.25 sec) (0.5 sec) (0.25 sec) (1.25 sec)
Yellow →Off →Green →Off
(0.5 sec) (0.5 sec) (0.5 sec) (0.5 sec)
Aging Mode (Video Aging) : During Power Save, press “MENU” key for longer than 2 second.
Self Test (OSD Color Bar) : During Power Save, press “CONTRAST” + (>) key for longer than 2 second.
Reliability Check Mode : During Power Save, press “CONTRAST” – (.) key for longer than 2 second.
TIMING SPECIFICATION

– 4 –
D2846
Note: Hand degauss must be used on stand-by or power-off condition.
This model has an automatic earth magnetism correction function by using an earth
magnetism sensor and a LCC coil. When using a hand degauss while monitor (LCC
coil) is being operated, it sometimes gets magnetized, and the system may not work
properly as a result.
TABLE OF CONTENTS
Section Title Page
1. GENERAL................................................................... 5
2. DISASSEMBLY
2-1. Cabinet Removal .................................................. 13
2-2. D Board Removal ................................................ 13
2-3. G Board Removal ................................................ 14
2-4. A Board Removal ................................................ 14
2-5. L Board Removal ................................................. 15
2-6. I/O Terminal Board Removal ............................... 15
2-7. Service Position .................................................... 16
2-8. H and J Boards Removal ..................................... 16
2-9. Picture Tube Removal ......................................... 17
3. SAFETY RELATED ADJUSTMENT ............ 18
4. ADJUSTMENTS ...................................................... 19
5. DIAGRAMS
5-1. Block Diagrams .................................................... 21
5-2. Frame Shcematic Diagram.................................... 27
5-3. Circuit Boards Location........................................ 29
5-4. Schematic Diagrams and Printed Wiring Boards..... 29
(1) Schematic Diagram of D Board ........................... 33
(2) Schematic Diagrams of G, GA, H, J,
L and U3 Boards .................................................. 37
(3) Schematic Diagram of A Board ........................... 44
5-5. Semiconductors .................................................... 49
6. EXPLODED VIEWS
6-1. Chassis ................................................................. 51
6-2. Picture Tube ......................................................... 52
6-3. Packing Materials ................................................ 53
7. ELECTRICAL PARTS LIST ............................ 54

– 5 –
SECTION 1
GENERAL
The operating instructions mentioned here are partial abstracts
from the Operating Instruction Manual. The page numbers of
the Operating Instruction Manual remain as in the manual.

– 6 –

– 7 –

– 8 –

– 9 –

– 10 –

– 11 –

– 12 –

– 13 –
D2846
SECTION 2
DISASSEMBLY
2-1. CABINET REMOVAL
Top cover
Four screws
(+ BVTT 4 x 8)
Four screws
(+ BVTT 4 x 8)
Video shield
4
5
6
8
Screw cover
Cabinet
3
Four screws
(+ BVTP 4 x 16)
2
1
Two claws
Screw cover
7
2-2. D BOARD REMOVAL
Two screws
(+ BVTT 4 x 8)
Two screws
(+ BVTP 3 x 10)
D board
Screw
(+ P 3.5 x 20)
Open the D block in the direction
of the arrow . and remove of
the arrow .
Three hooks
6
A
B
A
B
Screw
(+ BVTT 4 x 8)
1
2
3
4 5

– 14 –
D2846
2-3. G BOARD REMOVAL
2-4. A BOARD REMOVAL
A borad Two screws
(+BVTT 4 x 8)
12
Two screws
(+ BVTT 4 x 8)
Three hooks
Two screws
(+BVTP 3 x 10)
G shield
G board
Open the G block in the direction
of the arrow . and remove of
the arrow .A
BTwo printed circuit board holders
A
B
1
7
Screw
(+ BVTT 4 x 8)
3
2
4
5
6

– 15 –
D2846
2-5. L BOARD REMOVAL
L board
Four printed circuit board holders
1
2
CN5001
CN5002 CN5004
CN5003
2-6. I/O TERMINAL BOARD REMOVAL
Three screws
(+ BVTT 3 x 8)
1
I/O terminal
2
CN511 CN401
CN402

– 16 –
D2846
2-7. SERVICE POSITION
2-8. H AND J BOARDS REMOVAL
D board (Refer to 2-2.)
Rear shield
D,G boards
A board (Refer to 2-4.)
G board
(Refer to 2-3.)
CAUTION : SHORT
If the claw is hooked,
opening and closing
the board is impossible.
Do not tr
y
to do it b
y
force.
If the claw is hooked,
opening and closing
the board is impossible.
Do not try to do it by force.
*
*
Four screws
(Tapping screw 5)
CN801
H board Two screws
(+ BVWHTP 3 x 12)
Bezel
1
2
3
4
Claw
J board
7
CN891
Shaft Claw
Claw
5
6

– 17 –
D2846
3When one side of the rubber cap is
separated from the anode button, the
anode-cap can be removed by turning
up the rubber cap and pulling up it in the
direction of the arrow c.
• HOW TO HANDLE AN ANODE-CAP
1Don’t hurt the surface of anode-caps with shartp shaped material!
2Don’t press the rubber hardly not to hurt inside of anode-caps!
A material fitting called as shatter-hook terminal is built in the
rubber.
3Don’t turn the foot of rubber over hardly!
The shatter-hook terminal will stick out or hurt the rubber.
• REMOVAL OF ANODE-CAP
NOTE: Short circuit the anode of the picture tube and the anode cap to the metal chassis, CRT shield or carbon painted on the CRT, after
removing the anode.
• REMOVING PROCEDURES
1Turn up one side of the rubber cap in
the direction indicated by the arrow a.2Using a thumb pull up the rubber cap
firmly in the direction indicated by the
arrow b.
2-9. PICTURE TUBE REMOVAL
a
b
Open the D block
(Refer 2-2.)
GND (DY)
6P (DY)
10P (DY)
Four screws
(+ BVTT 4 x 8)
A board
Open the G block
(Refer 2-3.)
Neck assy
Deflection yoke
Picture tube
Three connectors
Anode cap
1
2
3
4
5
6
8
9
7
c
Anode Button

– 18 –
D2846
SECTION 3
SAFETY RELATED ADJUSTMENT
When replacing or repairing the shown below table, the
following operational checks must be performed as a
safety precaution against X-rays emissions from the unit.
a) HV Regulator Circuit Check
1) Confirm that the voltage of the pin 2of CN901 on D
board is within the voltage range shown below.
Standard: 9.00 ± 0.065 VDC
b) HV Protector Circuit Check
1) Confirm that the HV protector circuit works and TV
Raster disappears when apply the voltage as shown
below between pin 3of CN901 on D board and
GND using an external DC power supply.
Check Condition: Less than 34.10 VDC
c) Beam Current Protector Circuit Check-1
1) Measure HV voltage and record that value.
2) Shorted between pin 1and pin 4of CN901 on D
board.
3) Connect to the Constant Current Jig (A) between pin
1of CN901 on D board and GND, confirm that the
Beam Current Protector Circuit works and HV go
down more than 1.25 kV from the value of (1).
Check Condition: 1.50 mA
d) Beam Current Protector Circuit Check-2
1) Connect to the Constant Current Jig (B) between pin
1of CN901 on D board and GND, confirm that the
Beam Current Protector Circuit works and TV Raster
disappears.
Check Condition: 1.59 mA
e) Voltage of 3rd winding of FBT
1) Confirm that the voltage of pin 3of CN901 on D
board is within the voltage range shown below.
Standard: more than 28.0 VDC
HV Regulator
Circuit Check
HV Protector
Circuit Check
Beam Current
Protector Circuit
Check
Part Replaced (])
D Board IC901, T902
• Mounted D board
D Board Q660, Q661, D916,
D935, C924, R665,
R667, R940, R980,
T902
• Mounted D board
G Board PH680, Q680, Q683,
D680, R680, R685,
R686, R687, R688,
R689
• Mounted G board
D Board IC901, D904, D907,
D908, R011, R908,
R909, R921, R925,
R926, R929, R930,
T902
• Mounted D board
Check Condition
Input voltage : 100 ~ 240 VAC
Input signal : White Cross Hatch at 107 kHz
Beam control : BRT and CONT →Minimum
B+ voltage : 195 ~ 205 VDC

D2846
– 19 –
SECTION 4
ADJUSTMENTS
•Landing Rough Adjustment
1. Enter the full white signal. (or the full black dots signal).
2. Adjust the contrast to the maximum.
3. Make the screen monogreen.
Note: Off the outputs from R ch and B ch of SG.
4. Reverse the DY, and adjust coarsely the purity magnet so that
a green raster positions in the center of screen.
5. Adjust the tilt of DY, and fix lightly with a clamp.
Note: “TILT” shall be set at 0.
•Landing Fine Adjustment
1. Put the set inside the Helmholtz coil. (“LCC SW” = “12”)
2. Input the single green signal and set the CONT control to
MAX.
Note: After the W/B adjustment with 9300K, measure an average
of SIk when a full white signal is entered in the CONT
MAX/BRT CENT status. Then make adjustment so that the
specified screen can be attained after aging for 2 hours with
Ik equivalent to 30% of the average value.
3. Demagnetize the metal part of the chassis with the hand de-
gausser and coil degausser, and the CRT surface with the
hand degausser.
Input AC 230V to AC IN, turn on and off the power to per-
form auto degaussing. (Perform auto degaussing by setting
“MON CON REG2”=152. Return to the original value after
use.)
Demagnetize the CRT surface with the hand degausser again.
Note:
(1) Hand degauss must be used on stand-by or power-off condi-
tion.
This model has an automatic earth magnetism correction
function by using an earth magnetism sensor and a LCC coil.
When using a hand degauss while monitor (LCC coil) is being
operated, it sometimes gets magnetized, and the system may
not work properly as a result.
(2) Adjust in a non-magnetic field. BV=45uT.
(3) If adjusting in a magnetic fields, add the shift from the non-
magnetic field in your estimation.
4. Attach the wobbling coil to the designated part of the CRT
neck.
5. Attach the sensor of the landing adjustment unit on the CRT
surface.
6. Adjust the DY position and purity, and the DY tilt, and land-
ing of the center and 4 corners with the landing checker.
After adjustment, set “LCC SW” to “13”.
•Write terrestrial magnetism sensor reading VX and VY to
“LCC VX” and LCC VY” respectively. Adjust the landing
by moving “LCC NS”, “LCC LT”, “LCC LB”, “LCC RT”
and “LCC RB”. However, the register adjustment must be
limited within the following range.
“LCC NS” 128 ± 15
“LCC LT”, “LCC LB”, “LCC RT”, “LCC RB”
128 ± 40
Save the service data.
A difference between red and blue
must be within the specification
given right.
* Adjustment and measurement should be made at the points one
inch inside the fluorescent screen.
± 6 ± 6 ± 6
± 6 ± 4 ± 6
± 6 ± 6 ± 6
<Specifications>
Adjust so that the green is within
the specification given right.
4 corner adjust target : within ± 1
The red and blue must be within
the specification given right with
respect to the green.
0 ± 3 0 ± 7.5 0 ± 3
0 ± 5 0 ± 5 0 ± 5
0 ± 3 0 ± 7.5 0 ± 3
(µm)
(µm)
10 10 10
10 7 10
10 10 10
(µm)
7. For the up/down swing, swing the DY and insert a wedge so
that the up and down pins are equal at the top and bottom.
Adjust the DY TLV VR so that the horizontal trapezoid is
equal at the left and right. Insert the wedge firmly so that the
DY does not shake.
8. Check the landing of each corner, and if it does not satisfy the
specification, adjust the landing of four corners using “LCC
LT“, “LCC LB”, “LCC RT” and “LCC RB”.
However, the register adjustment must be limited within the
following range.
“LCC NS” 128 ± 15
“LCC LT”, “LCC LB”, “LCC RT”, “LCC RB” 128 ± 40
After adjustment, save the service data.
9. Remove the sensor and wobbling coil.
10. Switch the signal to R.G.B., and check that each color is pure.
11. Check that the DY is not tilting.

D2846
– 20 –
Connect the communication cable of the computer to the connector located on the D board on the monitor. Run the service software and
then follow the instruction.
XBV XCV
R
B
B
RR
B
B
R
BBR
H. AMP
H. TILT (TLH) YBHYCH
R B
R B
R
IBM AT Computer
as a Jig
1-690-391-21
1A-1500-819-A
Interface Unit
2
*The parts above ( ) are necessary for DAS adjustment.
13
D-sub
(9 Pin [female]) mini Din
(8Pin) 4 Pin
3-702-691-01
Connector Attachment
3
To BUS CONNECTOR
4 Pin 4 Pin
•Convergence Rough Adjustment
(1) Receive an image of the white crosshatch signals (white lines
on black).
(2) Place the protrusions of the 6-fold poles magnet attached to
the CRT neck upon each other. (Fig. 1)
(3) Make rough adjustment of the H and V direction convergence
by using 4-fold poles magnet.
(4) Make a rough adjustment of the V direction convergence by
using “V. STAT”.
Protrusions
60°
Fig. 1
Fig. 3 Fig. 2
TLV
YCH
YBH
XBV
XCV
APH
*
* Set so that the protruding parts of
the 2 magnet rings agree with each
other.
*
•Convergence Specification
•White Balance Adjustment Specification
(1) 9300K
x = 0.281 ± 0.005
y = 0.311 ± 0.005
(All White)
(2) 6500K
x = 0.313 ± 0.005
y = 0.329 ± 0.005
(All White)
•Vertical and Horizontal Position and Size
Specification
•Focus adjustment
Adjust the focus volume 1 and 2 (HDK 1 and 2) for the
optimum focus.
B
a
a 3.2 mm
b 3.2 mm
a
b
b
A
MODE
A
B
1-5, 9-10
388 mm
291 mm
6-8
364 mm
291 mm
B
AMODE
A
B
1, 2
0.24 mm
0.24 mm
3-14
0.24 mm
0.32 mm
FBT
HDK1 (V)
HDK2 (H)
Table of contents
Other HP Monitor manuals

HP
HP 70004A User manual
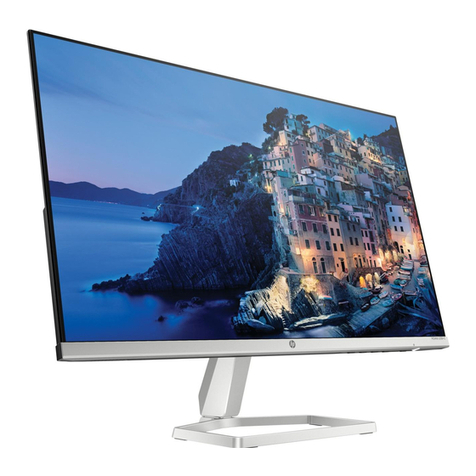
HP
HP M24FD Specification sheet

HP
HP Pavilion f1904 User manual

HP
HP S1932 User manual

HP
HP 2310mfa User manual
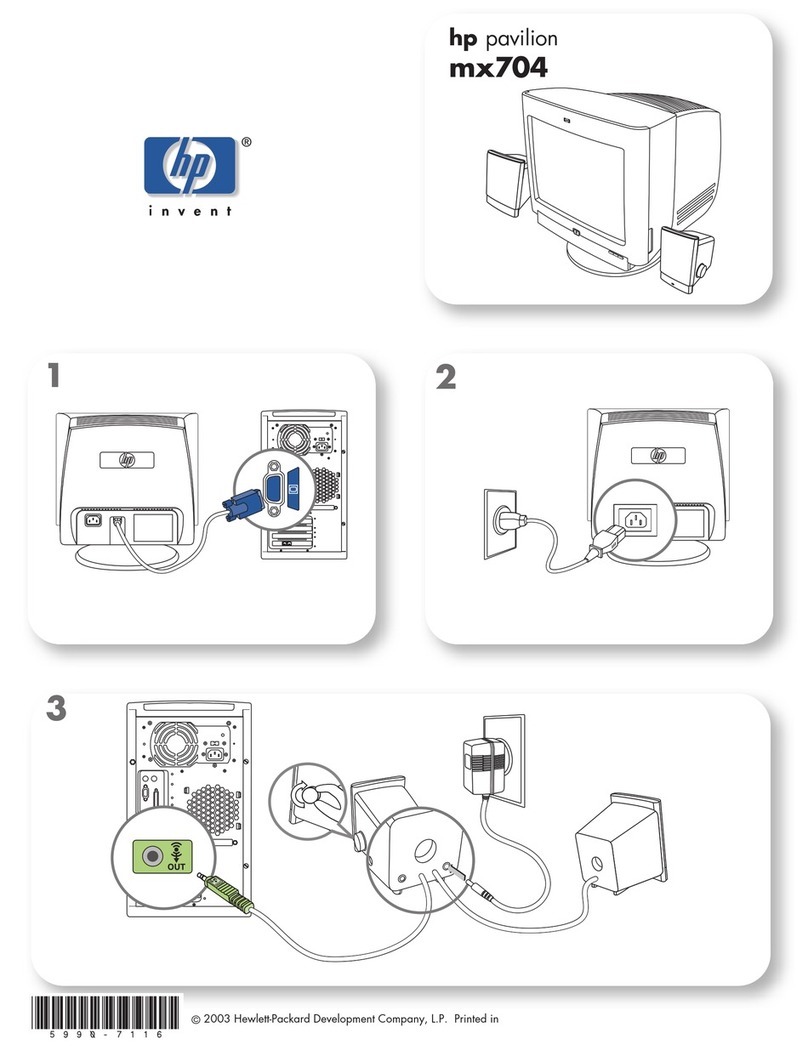
HP
HP Pavilion MX704 Specification sheet
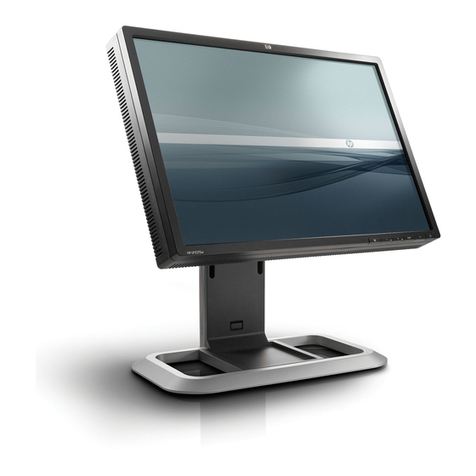
HP
HP LP2275w - 22" LCD Monitor User manual
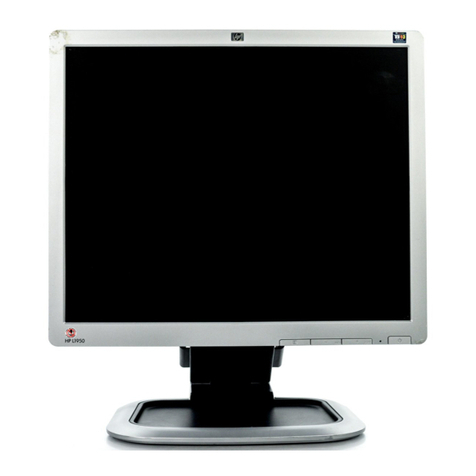
HP
HP L1950 User manual
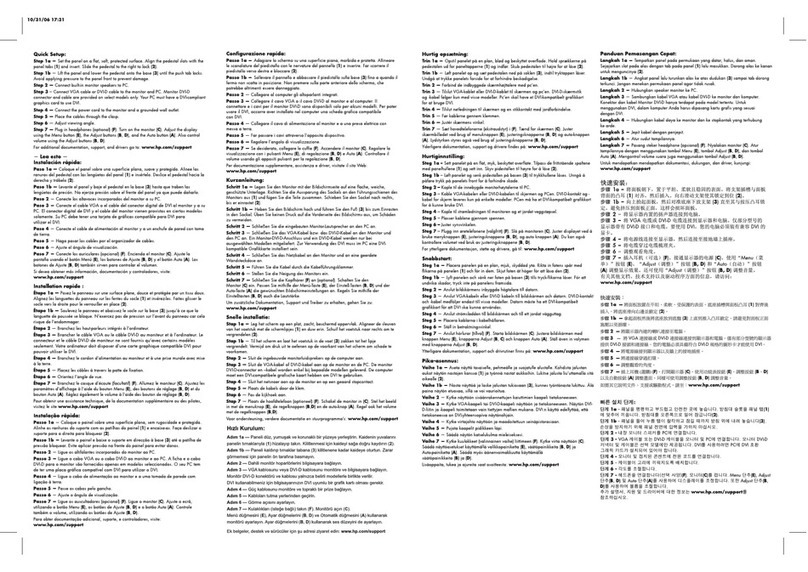
HP
HP W1907 Specification sheet
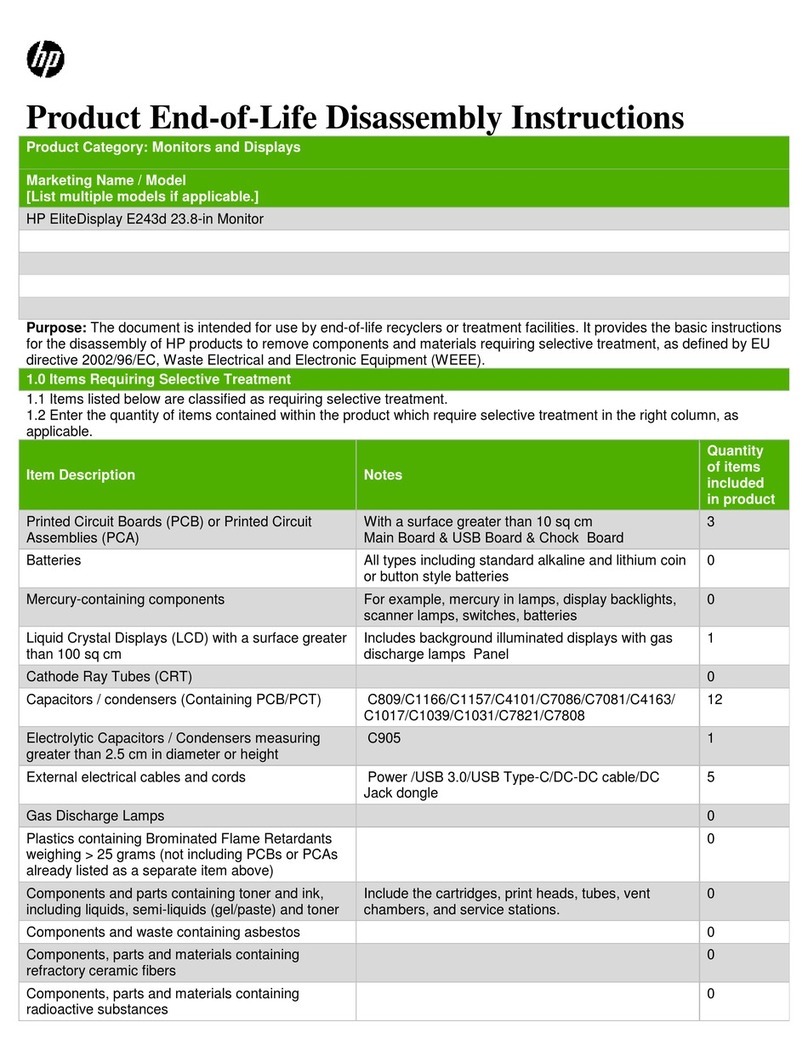
HP
HP EliteDisplay E243d Installation instructions