HST WFS - 101545 User manual

1
WFS
101545 Operations Manual
ORIGINAL
INSTRUCTIONS
Installation and Operation
Water Filtration System
WFS – 101545
Serial Number: _________
HST Spindles, LLC.
1357 Route 3A
Bow, NH 03304 USA
www.highspeedtechnologies.com

2
WFS
101545 Operations Manual
TABLE OF CONTENTS
SECTION I OVERVIEW
1. NOMENCLATURE Page 4
2. GENERAL DESCRIPTION Page 4
a. Process Loop Page 6
b. Spindle Loop Page 6
c. Internal Recirculating Loop Page 7
d. Lift Station Page 7
3. SPECIFICATIONS Page 8
a. Pump 1 Recirculating Water Page 8
b. Pump 2 Process Water Page 8
c. Pump 3 Spindle Water Page 8
d. Chiller Page 8
e. Lift Station Page 9
f. Filtration Page 10
g. Reservoir Page 10
4. SETUP PAGE 11
a. Floor Space Page 11
b. Uncrating Page 11
c. Electrical Power Requirements Page 12
d. Leveling the Base Page 12
e. Assembly Page 13
f. Facility Interface Page 16
5. OPERATOR CONTROLS Page 19
a. Power On-Off Selector Switch Page 19
b. E-Stop Push Button Page 19
c. Power on Pilot Light Page 19
d. Audible Alarm Page 20
e. Touch Screen Page 20
f. Resitivity Sensors Page 26
6. FILTER HOUSING AND ELEMENT CHANGE OUT Page 26
a. Filter Element Installation Page 28
b. Configuration Page 29
c. Air Bleed Valves Page 30
d. Leak Detector Page 30
e. Nuisance Tripping Page 31
f. Resin Tanks Page 31
g. Resin Tank Gages Page 32
h. Resin Tank Change-Out Page 32

3
WFS
101545 Operations Manual
SECTION II COMMISIONING Page 32
1. COMMISSIONING PREREQUISITES Page 32
2. FILLING THE RESERVOIR Page 33
3. FILLING THE RECIRCULATING FILTER HOUSINGS Page 34
4. FILLING THE PROCESS FILTER HOUSINGS Page 35
5. STARTING THE SPINDLE CIRCUIT Page 35
6. STARTING THE CHILLER Page 36
7. RESERVOIR PROCESS FLOW Page 36
8 PRESSURE SETTINGS Page 36
APPENDIX Page 38
ELECTRICAL SCHEMATICS
Sheet 1 Page 39
Sheet 2 Page 40
Sheet 3 Page 41
Sheet 4 Page 42
Sheet 5 Page 43
Sheet 6 Page 44
Sheet 7 Page 45
SCHEMATIC PLUMBING
Sheet 1 Page 46
TROUBLE SHOOTING Page 47
DESIGN DATA LINKS Page 48

4
WFS
101545 Operations Manual
SECTION I OVERVIEW
1) NOMENCLATURE
NOTE: This message highlights a feature, function or procedure that may be helpful.
CAUTION: This message warns of a condition that may have unintended negative action or
consequences. It indicates a need for heightened diligence.
WARNING: This message warns of a condition or procedure that has potential for physical
injury or death. Often it is applied to a procedure that requires special equipment or qualified
personnel.
This symbol warns of a potential shock hazard that may cause injury or death.
Images and Illustrations
Each unit is hand built to order and may have slight variations from the images depicted in this
manual. Additionally, some images used are of a generic assembly and may not depict certain
optional equipment that is included on any particular unit.
Application
This manual is for use with WFS 101545 with serial numbers 210610 and higher. The
procedures described herein are for a generic installation and commissioning. The conditions
vary from one facility to another and procedures outlined herein may require modification to
accommodate specific facility requirements.
2) GENERAL DESCRIPTION
The WFS 101545 filtration system was specifically engineered to provide temperature-
controlled water for wafer dicing and similar processes. The system permits re-use of process
and cooling water used for dicing or grinding semiconductor wafers. The WFS 101545 provides
complete water conditioning packaged on a compact rigid skid. The valving and redundant
features allow for change out of filter elements and resin beds without process interruption.
The unit provides the following water conditioning:
Cooling by refrigeration
Filtration
Deionization1
Although specifically designed for the semiconductor industry the unit can be applied to any
process that requires refrigerated, filtered and deionized water.
1 Deionization is accomplished by customer supplied resin beds. The unit provides valving and space for three 14”
diameter resin beds.

5
WFS
101545 Operations Manual
The WFS 101545 provides economies in two ways:
Significantly reduces DI water consumption by reconditioning and reusing the water.
Eliminates or reduces contaminated or hazardous liquid waste disposal by filtering out
contaminates into a removable cartridge. The cartridge can be dried and the waste
material can then be handled as solid waste.
The unit uses standard 2.5 x 20” filter elements. These come in a wide variety of
configurations. They are available from numerous commercial sources so the end user is
free to source them from their preferred vendor. The end user is not forced to go to the
OEM to purchase consumables.

6
WFS
101545 Operations Manual
The system provides two (2) separate cooling circuits. One is specifically for cooling the dicing
or sawing process. The other provides cooling water to the spindle or drive motors. Used
process water is cooled by refrigeration, filtered and deionized. Used spindle cooling water is
cooled by refrigeration in a separate circulating loop.
In addition to the built-in filtering and refrigeration capabilities, the WFS has provisions to accept three
(3) customer supplied 2.5 cubic foot (70.8 liter) resin tanks for additional filtering and/ or deionization.
The system has three water circulating loops:
Process Loop
Spindle Loop
Internal Recirculating Loop.
Additionally, a separate Lift Station pump is provided to return process water back to the WFS.
a. Process Loop
The Process Loop recirculates temperature controlled, filtered and deionized water for
dicing and grinding. It is rated to provide 15 GPM at 45 PSI.
b. Spindle Loop
This loop recirculates water cooled by refrigeration for the dicing spindle motors.
SIMPLIFIED SCHEMATIC OF THE PROCESS LOOP
CLEAN
SIDE
DIRTY
SIDE
PROCESS
GRAVITY
FEED
WFS 101545
ION
EXCHANGE
RESIN
ACTIVATED
CARBON
FINAL
FILTER
LIFT
STATION

7
WFS
101545 Operations Manual
The spindle coolant loop is rated at 10 GPM at 45 PSI
c. Internal recirculating Loop
This loop constantly recirculates process water returned from the lift station through filters
and cooling.
d. Lift Station
The lift station returns contaminated water from the dicing process to the WFS.
SIMPLIFIED SCHEMATIC OF THE
SPINDLE
CHILLER
SPINDLE COOLANT
CHAMBER
SPINDLE
MOTORS
WFS 101545
SIMPLIFIED SCHEMATIC OF THE
INTERNAL RECIRCULATING LOOP
DIRTY CLEAN
FILTER CHILLER
WEIR

8
WFS
101545 Operations Manual
3) SPECIFICATIONS
a. Pump 1
Recirculating water
Gould # 5HM04N11T6PBQE
25gpm
45psi
b. Pump 2
Process Water
USA ONLY
Gould 3HM07N11T6PBQE
1.5hp
15gpm
75 psi max
EU ONLY Gould
3HM10N151T6PBQE
2.0 HP
15gpm
75 psi
c. Pump 3
Spindle Water
Gould # 3HM04N05T6PBQE
1 hp
10gpm
50psi
d. Chiller
The chiller operates two zones; Zone 1 Process and Zone 2 Spindle. Each zone has
approximately 1/2 of the total chiller capacity.
WFS 101545 chiller unit is specifically designed and built for use with processing
semiconductors. However, it can be applied to any process that requires refrigerated and
SPINDLE WATER
PRESSURE FLOW
PSI Mpa GPM LPM
45 0.31 10 38
PSI Mpa GPM LPM
45 0.31 30 114
PRESSURE
FLOW
RECIRCULATING WATER

9
WFS
101545 Operations Manual
filtered water. The chiller uses a Copeland FFAP-03OZ condensing unit with a two custom
made evaporator units. It requires 208 -220 VAC 50-60 hz three phase electrical power.
The evaporators use custom made titanium evaporation coils enclosed in schedule 80 PVC
housing. The wetted surfaces are PVC and titanium making the heat exchangers impervious
to the effects of DI water.
Copeland FFAP-03OZ
e. Lift Station
This is a self contained pumping system with internal reservoir and float switch. It is
designed to collect water from the open-loop process and return it to the WFS. It utilizes a
Liberty 405 Sump Pum with associated check valve

10
WFS
101545 Operations Manual
f. Filtration
The WFS uses proprietary stainless-steel housings that require three 20” disposable filter
cartridges for filtration of the process water. The filters housings are arranged in two
parallel sets of two. One set of two filters for the Internal Recirculating Loop and one set of
two filters for the Process Loop.
Valving is provided to isolate any single filter housing to permit filter element change out
without process interruption.
i. Filter Housings
The filter housings are manufactured from 304 stainless steel and rated for 100 psi
maximum pressure and 110o F degrees maximum temperature. 316 stainless is
available at special order.
ii. Filter Elements
Each filter housing is designed to hold three cartridge type filter elements 20in x
2.5in. The housings accept filter cartridges of various composition and filtration
rating. The customer must determine the type of filter element to best satisfy their
requirements. Filter elements are customer supplied and can be sourced from a
variety of providers.
iii. Gauges
Each filter housing has a pressure gauge remote mounted and displayed facing the
control panel. These gauges provide indication of the filter condition. The filter
elements should be changed when the gages indicate a pressure increase in excess
of 15 PSI or in accordance with the filter element specifications.
g. Reservoir
The reservoir is made from polypropylene and divided into three chambers referred to as
the Dirty Side, the Clean Side and Spindle. The reservoir allows return water accumulation
to prevent pump cavitation. It also provides a certain amount of dwell time to allow heavy
particulate to settle out.
Two independent float valves maintain the proper fill levels in Dirty Side and the Spindle
chambers. These valves compensate for minor losses due to evaporation or small leaks and
splashing resulting from the process.
CHAMBER BRIM FULL NOMINAL
ALL 51 35
CLEAN SIDE 8.5 8.5
DIRTY SIDE 13 10.5
SPINDLE 20.6 16
RESERVOIR CAPACITY GALLONS

11
WFS
101545 Operations Manual
4) SETUP
a. Floor Space
Prior to installation consider the space required for proper servicing. Figure 4-1 provides
recommended clearances for servicing the various components on the WFS 101545.
b. Uncrating
NOTE: Inspect “Tip and Tell” and shock indicators mounted on the outside of the crates for
indication of mishandling and potential damage during shipment.
The outside of the crate should be inspected for damage prior to uncrating. Additionally,
“Tip and Tell” and shock indicators are attached to the exterior. They should be inspected
prior to uncrating. If these indicators are missing or indicate that the crate has been
subjected to damaging shock loads or tipped, you should notify your carrier prior to
uncrating.
The refrigeration unit is shipped in the smaller crate. The WFS base assembly and the
Isolation Valve Sub-Assembly are both contained in the larger crate.
Inspect both crates and report any damage to the carrier and the OEM before proceeding.
AREA FOR SERVICING
FILTERS
AREA FOR SERVICING RESIN
TANKS
AREA
FOR
FACILITY
PLUMBI
NG
AREA
FOR
SERVICIN
G
RECOMMENDED FLOOR SPACE FOR SERVICING THE WFS 101545
36”
914m
39”
1000m
m
39”
1000m
m
39”
1000m
FIGURE
4
-
1
84”
2134m
m
39”
1000m

12
WFS
101545 Operations Manual
Figure 4-2 shows the minimum door height clearance required to accommodate passage of
the main WFS platform prior to assembly.
c. Electrical Power Requirements
WFS requires the following:
3 phase 40 amp circuit
230 VAC 50 hz or 220 VAC 60 hz
The Lift Station requires the following:
115 VAC 50/60 hz
7.5 Amps
See manufactures design data in appendix
d. Leveling Base
Prior to assembly the base must be properly leveled and supported at six (6) points. Figure
4-3 shows the leveler location. A standard spirit or bubble level will provide sufficient
accuracy for leveling the unit.
FIGURE
4
-
2

13
WFS
101545 Operations Manual
Before verifying that the platform is level,
insure all six of the leveling legs are firmly
on the floor. If any leg is not touching the
floor, adjust by loosening the [visible]
copper plated leg lock nut and winding this
½ - 13 nut in a clockwise direction. Once
the leg is firmly on the floor, wind the
upper locknut (above the underside of the
equipment base) in a clockwise direction
until tight. Complete by winding the
exposed ½-13 (copper plated) locknut ‘up’
in a counter-clockwise direction until tight.
Next, using a bubble level or similar
leveling tool, measure the level of the
equipment base. Place the level-tool in an
unobstructed surface of the equipment base. If the equipment is off-level by less than ¼
bubble, no adjustment is necessary. However, if more than ¼ adjust the respective legs
accordingly. Ensure all leg locknuts are tight.
e. Assembly
The Isolation Valves Sub-Assembly (IVSA) and the Chiller must be installed on site. Figure 4-
4 The chiller unit is shipped in a separate crate and the Isolation Valves Sub-Assembly is
shipped in the same crate as the main unit.
i. Isolation Valve Sub Assembly Installation (ISVA)
CAUTION: Use care to not damage the Resitivity Sensor wires when removing the
retaining straps that secure the IVSA during shipment and when installing the IVSA.
CAUTION: Use care when connecting the IVSA unions. Make sure the O-Rings are
properly seated. Do not cross thread parts. Do not over tighten.
NOTE: The connector for the pressure transducer is keyed. One tab is slightly larger
than the other.
NOTE: Check for leaks during commissioning
Support the IVSA as the retaining straps are removed. Lift and place the unit on the
associated unions and clamp to the vertical strut channel. Verify that the O-rings are
properly seated and tighten the unions.
FIGURE 4
-
3

14
WFS
101545 Operations Manual
Install the connector on cable CBL-PT2 on the pressure transducer. Tight the center
screw.
ii. Preparing The Chiller for Installation
Remove the chiller from its crate and inspect for damage.
Remove the drip pan and the four carriage bolts from the Chiller Support
Frame.
Install the carriage bolts into the four slots on the chiller base.
Install the Drip Pan
Thread the Power Cord and Solenoid Control Cord through the Drip Pan
See Figure 4-5
FIGURE 4
-
4

15
WFS
101545 Operations Manual
iii. Installing The Chiller
CAUTION: The Chiller is heavy and awkward. Use proper equipment and personnel
for installation.
CAUTION: Ther may be sharp edges on some of the metal parts use proper Personal
Protective Equipment (PPE)
CAUTION: Use care when connecting the chiller unions. Make sure the O-Rings are
properly seated. Do not cross thread parts. Do not over tighten.
NOTE: Check for leaks during commissioning
Carefully place the prepared chiller on the Chiller Support Frame so the four carriage
bolts fall into the slots on the Support Frame.
FIGURE 4
-
5

16
WFS
101545 Operations Manual
Ease the chiller into a position where all four unions line up with the mating parts.
The union faces must be “flat” to one another. Verify that the O-rings are in place.
Tighten the union.
Install washers and nuts on the carriage bolts and tighten.
Connect the Power Cord and the Solenoid Control Cord to the round receptacles on
the bottom of the Control Panel. See Figure 4-6
f. Facility Interface
i. Plumbing Connections
There are six (6) facility plumbing connections to the WFS Unit.
Make-up Water for the Spindle Coolant Circuit
Make-up Water for the process Cooling circuit
FIGURE 4
-
6

17
WFS
101545 Operations Manual
Spindle Cooling Supply
Spindle Cooling Return
Process Cooling Supply
Process Cooling Return
Figure 4-7 shows the approximate location of the plumbing connections.
The connection for the for the Spindle
Coolant Make-Up Water is 1” NPT. The
water source can be provided from clean
ordinary tap water.
The connection for the for the Process
Coolant Make-Up Water is 1” NPT. This
water source can be from water deionized
by another source or from clean ordinary
tap water.
The connection for the Spindle Cooling
Supply is 1-1/4” NPT. This provides water
cooled by refrigeration to cool the spindle
motors. This is a “closed-circuit” loop circuit
and does not require a lift station.
The connection for the Spindle Cooling
Return is 1” NPT. This connection directs
return water from the spindle cooling loop
back to the reservoir.
The connection for the Process Cooling Supply is 1-1/4” NPT. This provides water
filtered, de-ionized2 and cooled by refrigeration to cool the cutting, grinding or
dicing process. This process is normally “open-loop”. Therefore, a separate “Lift
Station” is required to return the water back to the WFS. The customer is
responsible to collect and direct the process water to the lift station pump.
The connection for the Process Cooling Return is 1-1/4” NPT. This connection directs
return water from the Lift Station back to the reservoir.
ii. Electrical Hook-Up
The unit requires three (3) phase 220 VAC 60 Hz 40 Amp or 230 VAC 50 Hz 40 Amp
power with grounding wire.
2 Deionization is accomplished by customer supplied resin tanks.
FIGURE 4
-
7

18
WFS
101545 Operations Manual
The power wires attach to the three lugs provided on the top of the distribution bus
bar. The ground wire must be attached to the grounding terminal to the left of the
bus bar. See Figure 4-8.
CAUTION: Installation wiring must comply with local and national electrical codes.
WARNING: Only qualified and licensed personnel should install facility wiring.
WARNING: Electrical Shock hazard
NOTE: All pumps and the chiller have been “phased” together. If pump rotation is
not correct during commissioning change wire phase ONLY AT FACILITY
CONNECTION.
FIGURE 4
-
8

19
WFS
101545 Operations Manual
5) OPERATOR CONTROLS
Other than the mechanical ON/OFF switch and the E-Stop push button all controls are through
a touch screen HMI. See Figure 5-1
WARNING!
The Control cabinet
contains High Voltage
electrical connections.
Accidental contact with
electrically live
components can cause
serious injury or death.
Always disconnect
electrical power from
source and lock out/tag
out when working inside
the Control Panel
Only trained and qualified
personnel may open the
Control Panel
Operator controls consist of four components
Power ON-OFF selector switch
Power On Pilot Light
E-Stop detented push button
Touch Screen HMI
a. Power ON-Off Selector Switch
This switch activates the control power. This turns control power on.
WARNING: This switch DOES NOT turn off AC power within the control cabinet. High Voltage
AC current is still on inside the cabinet even when this switch is in the OFF position.
Disconnect power from outside source before opening the control cabinet.
b. E-Stop Push Button
The E-Stop push button stops all pumps and the chiller. It is detented. After it has been
depressed it must be physically pulled out to permit resetting the controls.
NOTE: Control Power remains on even with this switch depressed.
c. Power On Pilot Light
FIGURE 5
-
1

20
WFS
101545 Operations Manual
This is illuminated when electrical power is on to the control system.
d. Audible Alarm (Optional)
An audible alarm is sounded if a fault condition is detected. See ALARMS section 5.e.vi
e. Touch Screen HMI Display Panel
All functions other than Power ON-OFF or E-Stop are controlled or displayed through the
Touch Screen HMI. These include the following:
Pump and Chiller Start-Stop
Temperature Set-Points
Alarm Set Points
Alarm On-Off
System Status
The Touch Screen can display four (5) different pages:
Home
Water Temperature
Status
Set Points
Alarms
Each page provides certain specific information and provides control or settings.
i. Page Selection
Each page displays the five different page selections at the bottom. An operator can go
to any page at any time.
Two pages are used to program the various set points: WATER TEMP and SET
POINTS.
One page is used to start the pumps and provide alarm condition: HOME PAGE
One Page displays the data from all the transducers such as pressures: STATUS
One page displays specific alarms: ALARMS
ii. Home
On initial start up the HOME pages is displayed. This page provides the following
control, information or access. See Figure 5-3
Page Selection
Pump / Chiller On-Off push Buttons
Pump / Chiller On-Off Indicating Lights
Alarm Status and Control
E-Stop Depress notification
Pump Requirement Notification
FIGURE 5
-
2
Table of contents
Other HST Water Filtration System manuals
Popular Water Filtration System manuals by other brands

Sterling
Sterling IM Series Installation instructions & owner's manual

Breville
Breville Chill Control BWC200 Instruction booklet
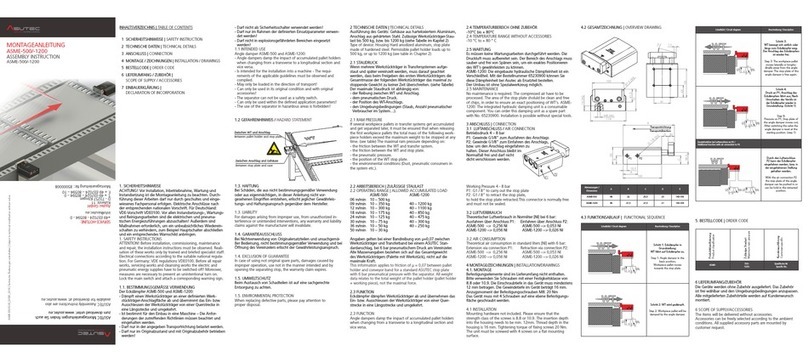
Asutec
Asutec ASME-500 Assembly instruction
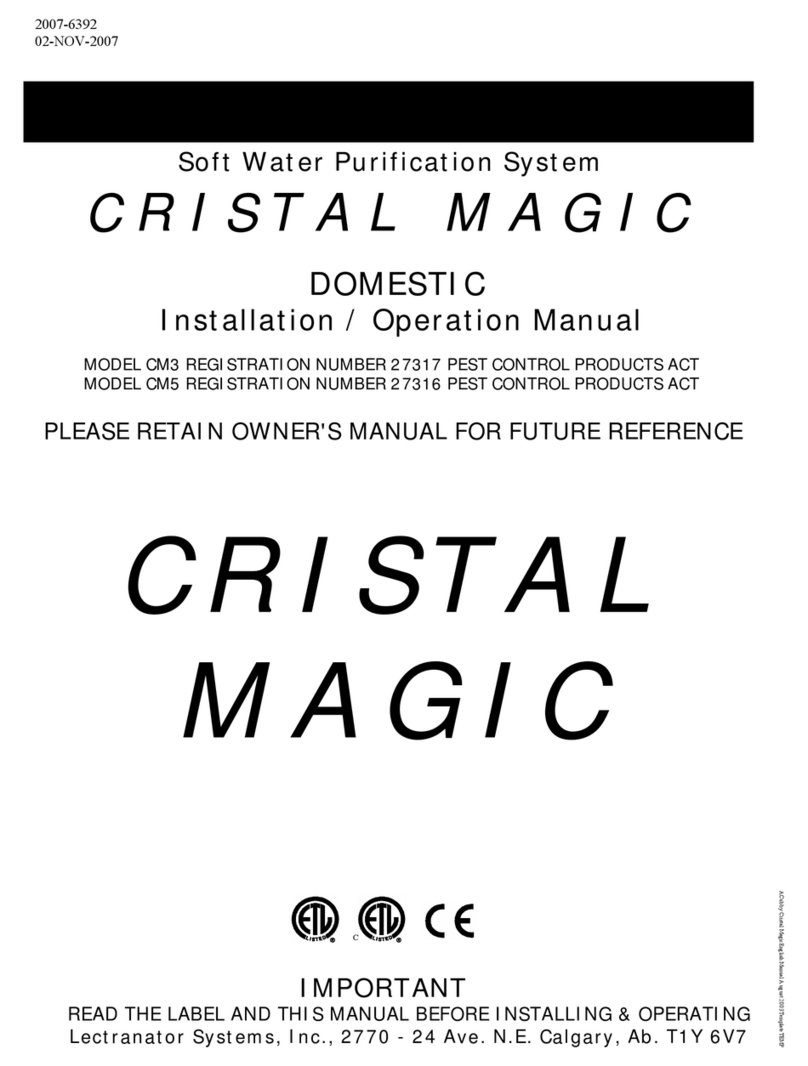
Lectranator Systems
Lectranator Systems CRISTAL MAGIC CM3-1 Installation & operation manual

GCTek
GCTek AlphaONE instructions
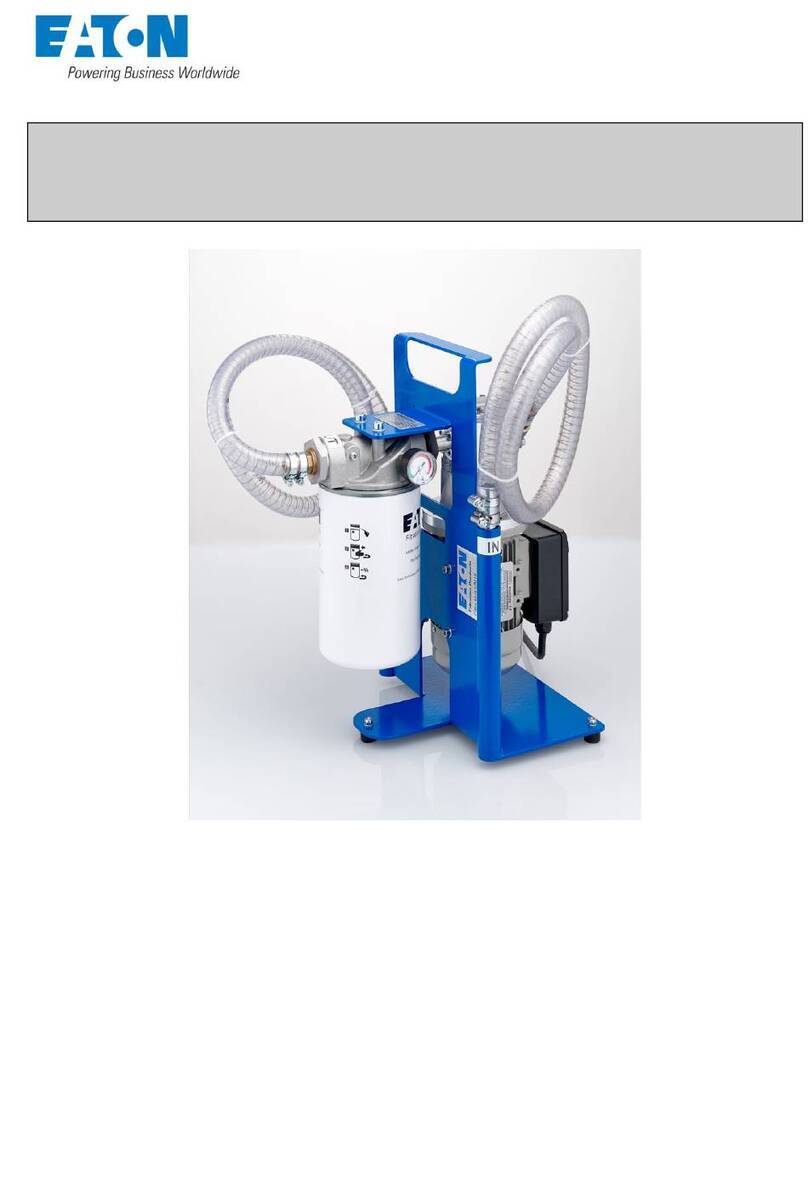
Eaton
Eaton UM15 operating instructions
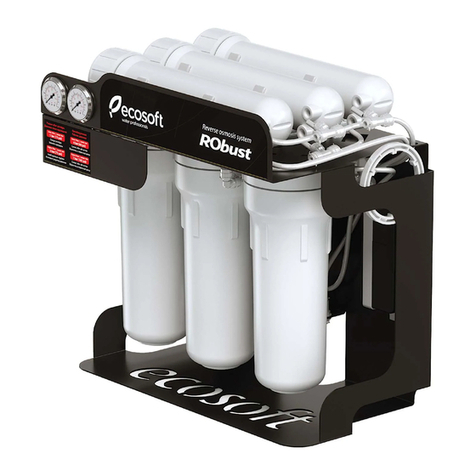
Ecosoft
Ecosoft Robust Installation and operation manual

AOX
AOX 2000NU user manual
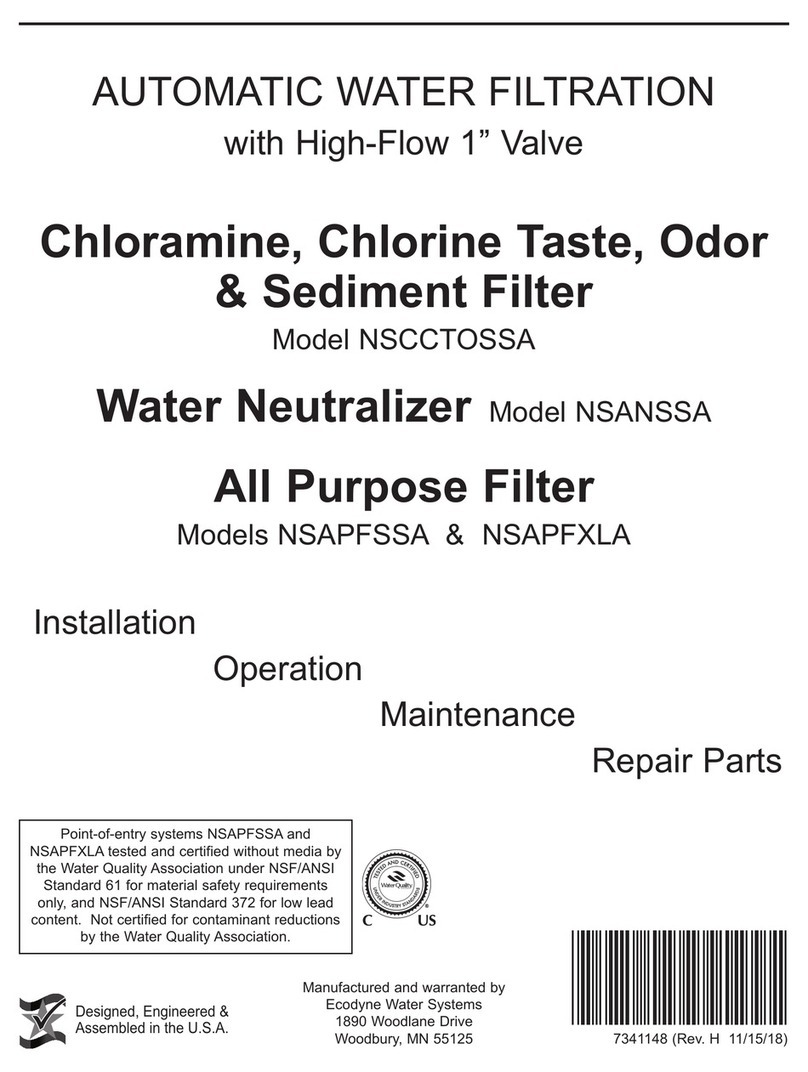
Ecodyne Water Systems
Ecodyne Water Systems HPF Installation, operation, maintenance & repair parts
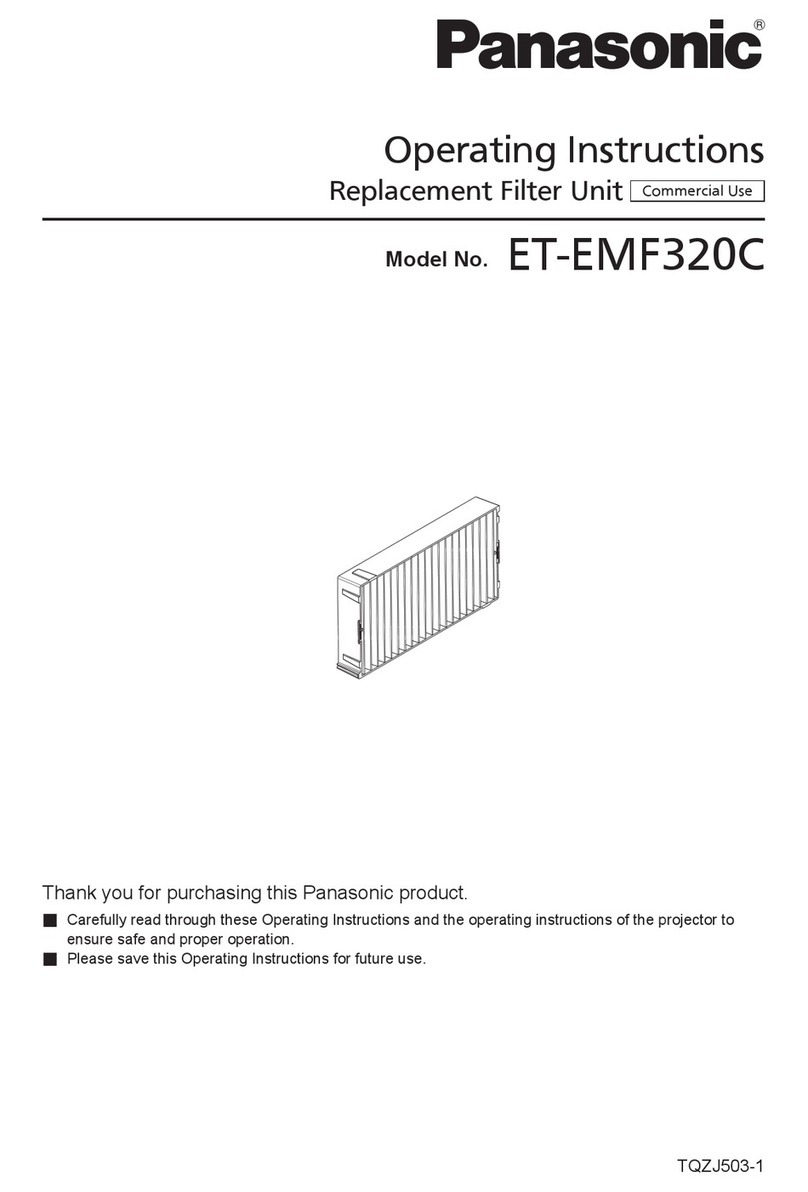
Panasonic
Panasonic ET-EMF320C operating instructions
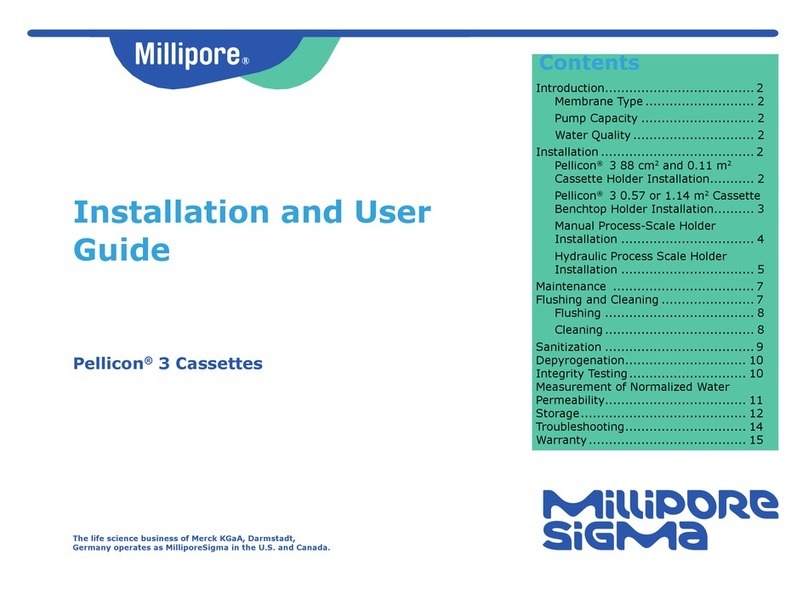
Millipore Sigma
Millipore Sigma Pellicon 3 Cassettes Installation and user guide
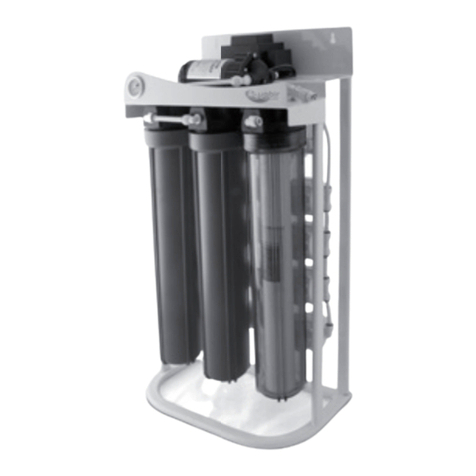
A.O. Smith
A.O. Smith OPAL NW Series user manual