HST WFS-1545 User manual

1
WFS 1545
Operations Manual
ORIGINAL
INSTRUCTIONS
Installation and Operation
Water Filtration System
WFS 1545
WFS-1545 6F
Serial Number: _________
HST Spindles, LLC.
1357 Route 3A
Bow, NH 33 4 USA
www.highspeedtechnologies.com

2
WFS 1545
Operations Manual
TABLE OF CONTENTS
Nomenclature Page 3
Images and Illustrations Page 3
Application Page 3
SECTION I OVERVIEW
1. Overview Page 4
2. Specifications Page 6
3. Setup and Requirements Page 7
4. Components Page 14
a. Pumps Page 14
b. Filtration Page 15
c. Chiller Page 15
d. Temperature Controllers Page 16
e. Float Valve Page 16
f. Control Cabinet Page 16
g. Optional Instrumentation and Alarms Page 18
SECTION II COMMISIONING
1. Commissioning Prerequisites Page 23
2. Filling the Reservoir Page 23
3. Recirculating Circuit Page 24
4. Process Supply Circuit Page 25
5. Starting the Chiller Page 26
6. Relief Valve Pressure Setting Page 26
7. Pressure Regulating Valve Page 27
SECTION III NORMAL OPERATION
1. Start-Up Check List Page 27
2. Power-Up Page 27
3. Pump and Chiller Start-Up Page 27
4. Shut Down Page 28
5. Filter Pressure Gages Page 28
6. Bypass Valve Page 28
TROUBLE SHOOTING Page 3
DESIGN DATA LINKS Page 31
SCHEMATIC PLUMBING Page 32
SCHEMATIC ELECTRICAL Page 33

3
WFS 1545
Operations Manual
Nomenclature
NOTE: This message highlights a feature, function or procedure that may be helpful.
CAUTION: This message warns of a condition that may have unintended negative
action or consequences. It indicates a need for heightened diligence.
WARNING: This message warns of a condition or procedure that has potential for
physical injury or death. Often it is applied to a procedure that requires special
equipment or qualified personnel.
This symbol warns of a potential shock hazard that may cause
injury or death.
Images and Illustrations
Each unit is hand built to order and may have slight variations from the
images depicted in this manual. Additionally, some images used are of a
generic assembly and may not depict certain optional equipment that is
included on any particular unit.
Application
This manual is for use with WFS 1545 and WFS 1545 6F Variant. The
procedures described herein are for a generic installation and
commissioning. The conditions vary from one facility to another and
procedures outlined herein may require modification to accommodate
specific facility requirements.

4
WFS 1545
Operations Manual
SECTION I OVERVIEW

5
WFS 1545
Operations Manual
1. OVERVIEW
The WFS 1545 standard filtration system and the WFS 1545 6F variant were specifically engineered
to provide clean, temperature-controlled water for wafer dicing and similar processes. The system
permits re-use of the process water used for dicing or grinding semiconductor wafers.
Although specifically designed for the semiconductor industry the unit can be applied to any process
that requires refrigerated, and filtered water.
The WFS 1545 provides economies in two ways:
• Significantly reduces water consumption by reconditioning and reusing the water.
• Eliminates or reduces contaminated or hazardous liquid waste disposal by filtering out
contaminates into a removable cartridge. The cartridge can be dried and the waste material
can then be handled as solid waste.
The WFS1545 system consists of an Internal Circulating Loop and a Process Loop all on a self-
contained skid. The Process Loop includes an off-skid Lift Station typically installed near the process
machinery for collecting used water and returning it back to the WFS1545 skid. The WFS1545
system also includes a two chambered reservoir, chiller unit and two filtration loops.
a. PROCESS LOOP
The Process Loop recirculates temperature controlled, filtered and cooled water for dicing and
grinding. The process pump draws water from the clean side of the reservoir and pumps it
through two final filters and then to the process machine. The Lift Station collects the water
from the process machine and returns it to the dirty side of the reservoir.
NOTE: The 6F variant provides three (3) final filters.

6
WFS 1545
Operations Manual
b. INTERNAL RECIRCULATING LOOP
This loop constantly recirculates process water returned from the lift station through filters and
cooling
c. LIFT STATION
The lift station returns contaminated water from the dicing process to the WFS.
2. SPECIFICATIONS
a. PROCESS WATER
b. CHILLER

7
WFS 1545
Operations Manual
c. LIFT STATION
d. RESERVOIR
The reservoir is made from polypropylene and divided into two chambers that are referred to as
the Dirty Side and the Clean Side. Water continuously circulates from the Dirty Side through a
cascade of three filters and a chiller unit and then back to the Clean Side of the reservoir. The
clean water cascades over a weir and back into the dirty side. This is a continuous process and
maintains clean, refrigerated water ready for process use.
3. SETUP AND REQUIREMENTS
a. FLOOR SPACE
Prior to installation consider the space required for proper servicing. Figure 2 provides
recommended clearances for servicing the various components on the WFS 1545.

8
WFS 1545
Operations Manual
b. UNCRATING
NOTE: Inspect “Tip and Tell” and shock indicators mounted on the outside of the crates for indication of
mishandling and potential damage during shipment.
The WFS 1545 is shipped in two crates. Inspect both crates and report any damage to the carrier
and the OEM before proceeding. The larger crate contains the base skid with filters and pump.
The electrical control panel is strapped to the chiller support structure and ships with the base
skid. A smaller crate contains the chiller unit.
The outside of the crates should be inspected for damage prior to uncrating. Additionally, “Tip and
Tell” and shock indicators are attached to the exterior. They should be inspected prior to
uncrating. If these indicators are missing or indicate that the crate has been subjected to
damaging shock loads or tipped, you should notify your carrier prior to uncrating.
Figure 3 shows the minimum door height clearance required to accommodate passage of the main
WFS platform prior to assembly.
FIGURE 2
NOTE: If necessary this side of the WFS can go
against a wall and filters accessed from the front.

9
WFS 1545
Operations Manual
c. ELECTRICAL POWER REQUIREMENTS
WFS 1545 requires the following:
3 phase 3 amp circuit
23 VAC 5 hz or 22 VAC 6 hz
The Lift Station requires the following:
115 VAC 5 /6 hz
7.5 Amps
See manufactures design data in appendix
d. LEVELING THE BASE
Once the unit is properly situated the base must be leveled and supported at four (4) points. Figure
4 shows the leveler location. A standard spirit or bubble level will provide sufficient accuracy for
leveling the unit.
FIGURE
3

1
WFS 1545
Operations Manual
Before verifying that the platform is level, insure all four of the
leveling legs are firmly on the floor. If any leg is not touching the
floor, adjust by loosening the leveler lock nut and winding this ½ - 13
nut in a clockwise direction. Once the leg is firmly on the floor, wind
the upper locknut (above the underside of the equipment base) in a
clockwise direction until tight. Complete by winding the exposed ½-
13 locknut ‘up’ in a counter-clockwise direction until tight. Next,
using a bubble level or similar leveling tool, measure the level of the
equipment base. Place the
level-tool
in an unobstructed surface of
the equipment base. If the equipment is off-level by less than ¼
bubble, no adjustment is necessary. However, if more than ¼ adjust
the respective legs accordingly. Ensure all leg locknuts are tight.
e. CHILLER ASSEMBLY
WARNING: Avoid personal injury. Installing the chiller and attaching the control panel requires lifting and
maneuvering heavy and bulky items. Use proper equipment and have adequate unobstructed room for
safe installation
After uncrating move the WFS base to an area where the chiller can be safely installed.
Remove the shrink wrap holding the control panel on the chiller support frame and carefully
support the control panel off to the side next to the Base frame.
1
CAUTION: Use care not to damage the flexible conduit going to the motors or other cables.
1
For units with optional sensors the cables can be unplugged from the sensor to allow easier handling of the control
cabinet.
Remove shrink wrap
from control panel and
set down on side next
to the base.
FIGURE
4
FIGURE
5

11
WFS 1545
Operations Manual
The installation requires lifting the chiller unit and placing it on the drip pan such that the two (2)
unions line up with the mating parts on the base unit. See Figure 5. Check to make sure that the O-
ring for each union is in place. Carefully move the chiller until the all of the union faces are in
contact with the corresponding face on the base unit. Use caution when tightening the union nut
to avoid “cross threading”. Do not over tighten. Check for leaks during commissioning of the
system. See Figure 6
Units provided in seismically active areas
2
have provisions for bolting the chiller to the frame.
Install the four (4) tie down bolts with spacers through the corner tabs of the chiller and bolt the
chiller to the frame
f. CONTROL CABINET INSTALLATION
Once the chiller is properly mounted the control panel can be attached to the chiller frame. The
chiller frame comes with four (4) “Spring Nuts” in the strut channel along with mounting bolts.
2
These areas include Western North America, Southern Europe and Pacific Rim Countries.
5/16
-
18 Bolt with hex nut
Spacer
OPTIONAL SEISMIC PACKAGE
Verify that O-rings are
in place .Line up
unions. Use care not
to “cross
-
thread”
FIGURE
6

12
WFS 1545
Operations Manual
WARNING: The control panel is heavy and awkward. Use proper equipment and caution when
lifting.
Remove the bolts from the top two spring nuts.
Loosen the bolts on the bottom spring nuts about
5/16”. Do not remove them. The bottom spring
nuts should be 14” apart with the rightmost nut
near the right end of the strut channel.
Lift the control cabinet over the lower bolts and
slide the bottom mounting tabs over the bolts. Let
the bottom bolts support the weight and bolt the
top tabs to the top spring nuts. Tighten all four
bolts.
Connect the yellow power cord to the round receptacle
on the bottom of the Control Panel.
Note: Connect any sensor cables that may
have been unplugged.
g. ELECTRICAL CONNECTION
WARNING!:
• Accidental contact with electrically live components can cause serious injury or death.
• Always disconnect electrical power from source and lock out/tag out when working inside
the Control Panel
• Only trained and qualified personnel may open the Control Panel
CAUTION: Installation wiring must comply with local and national electrical codes.
The unit requires three (3) phase 22 VAC 6 Hz 3 Amp or 23 VAC 5 Hz 3 Amp power with
grounding wire.
Connect yellow power cord from
chiller to the Control Panel
Slide bottom tabs over bolts

13
WFS 1545
Operations Manual
The power wires attach to the three lugs provided on the top of the distribution bus bar. The
ground wire must be attached to the grounding terminal to the left of the bus bar. See Figure 8.
h. PLUMBING CONNECTIONS
There are three (3) facility plumbing connections to the WFS Unit.
• Make-up Water 1” NPT
• Process Cooling Supply 1” NPT
• Process Cooling Return 1-1/4” NPT
The connection for the Process Cooling Supply is 1” NPT. This provides
water filtered and cooled by refrigeration to cool the cutting, grinding
or dicing process. This process is normally “open-loop”. Therefore,
a separate “Lift Station” is required to return the water back to
the WFS. The customer is responsible to collect and direct the
process water to the lift station pump.
The connection for the Process Cooling Return is 1-1/4” NPT. This
connection directs return water from the Lift Station back to the
reservoir.
The connection for the Make-Up Water is 1” NPT. The water source can
be provided from clean ordinary tap water.
i. LIFT STATION INSTALLATION
The inlet to the Lift Station (LS) is gravity fed from used process water and therefore must be
mounted at a lower elevation than the process water collection point
The LS has two available inlet ports: one on top and the other on the side. Either can be used
and the unused one plugged. The port is a 2” NPT.
A True Union check valve is provided with the LS. This should be installed on the discharge line
as close to the unit as possible. The check valve arrow should be pointing up.
NOTE:
Leave enough wire in the event that two legs
need to be switched. If motor rotation is in wrong
direction switch wires here or at source.
DO NOT switch leads after the circuit breakers

14
WFS 1545
Operations Manual
The unit has a small integral reservoir with a float switch. The Lift Station pump turns on when
the reservoir level triggers the float switch. It is normal for the lift station to cycle on and off
during normal operation.
WARNING!
• Accidental contact with electrically live components can cause serious injury or death.
• Use appropriate GFI circuit protection
4. COMPONENTS
a. PUMPS
The system has three pumps with the Internal Circulating Loop and a Process Loop each having their
own pump mounted on the main base. A third pump is built into the remote lift station. The system
is designed to provide a nominal 15 GPM (57 LPM) at 45 PSI ( .31 MPa)
The Internal Circulating pump pulls water from the Dirty Side of the reservoir and pumps it through a
cascade of three (3) filters, a chiller and returns the water back to the clean side of the reservoir.
The Process Loop pump pulls clean, refrigerated water from the Clean Side of the reservoir. Pumps it
through a final cascade of two filters (3 filters for the F6 variant) and then out to the process.
The Lift Station pump returns used water back to the Dirty Side of the reservoir.
Internal Recirculating Pump
Gould # 3HM 4N 5T6PBQE
Nominal performance
• .75 hp
• 15 gpm
• 4 psi

15
WFS 1545
Operations Manual
Process Pump
Nominal Performance
USA ONLY
Gould 3HM 7N11T6PBQE
• 1.5hp
• 15gpm
• 75 psi max.)
EU ONLY Gould
3HM1 N151T6PBQE
• 2. HP
• 15gpm
• 75 psi
NOTE: See link to Manufacturer’s Information in appendix
b. FILTRATION
The WFS uses Pall or FSI X1 filters that use disposable filter cartridges for filtration of the process
water. The filters are arranged in two cascading sets, one set of three filters for the Internal
Recirculating Loop and one set of two filters
3
for the Process Loop. We recommend having
increasingly finer filtration as the water cascades through the filters.
i. Filter Housings
The filter housings are manufactured from talc filled polypropylene and rated for 1 psi
maximum pressure and 11
o
F degrees maximum temperature.
ii. Filter Elements
Each filter housing is designed to hold three cartridge type filter elements. The housings
accept filter cartridges of various composition and filtration rating. The customer must
determine the type of filter element to best satisfy their requirements.
iii. Gauges
Each filter housing has a pressure gauge mounted directly on top. WFS. These gauges
provide indication of the filter condition. The filter elements should be changed when the
gages indicate a pressure increase in excess of 2 PSI.
NOTE: For detailed information concerning the filter housing see the link to manufacturer’s design data in
the appendix.
c. CHILLER
WFS 1545 chiller unit is specifically designed and built for use with processing semiconductors.
However, it can be applied to any process that requires refrigerated and filtered water. The chiller
3
F6 Variant uses 3 filters on the process side

16
WFS 1545
Operations Manual
uses a Tecumseh AWA452 3XNXC condensing unit with a custom made evaporator. It requires 2 8
-22 VAC 5 -6 hz electrical power.
The evaporator uses custom made titanium coils enclosed in schedule 8 PVC housing. The wetted
surfaces are PVC and titanium making the heat exchangers impervious to the effects of DI water.
NOTE: The condensing section of unit should be periodically cleaned. Use clean dry compressed air to blow
dust out from cooling fins. For specific detailed information concerning the Tecumseh condensing unit see
the design data page in the appendix.
d. TEMPERATURE CONTROLLER
The water temperature for the Process Circuit is controlled by a RANCO ETC111 2 Electronic
Temperature Controllers. This is mounted on the side of the main control cabinet. Water
temperature can be increased or decreased by use of the up or down arrows on the face of the
RANCO unit.
NOTE: For additional information see the Design Data section in the appendix.
e. FLOAT VALVE
A Hudson Float Valve is installed at a fixed position in the reservoir to maintain proper level and
compensate for evaporation and minor leaks. It is recommended that a separate supply source be
available for initial commissioning.
f. CONTROL CABINET

17
WFS 1545
Operations Manual
WARNING!
• Accidental contact with electrically live components can cause serious injury or death.
• Always disconnect electrical power from source and lock out/tag out when working inside
the Control Panel
• Only trained and qualified personnel may open the Control Panel
Controls and power distribution components are mounted in a NEMA 12 enclosure. The enclosure is
mounted on the side of the Chiller. All selector switches, push buttons and indicating lights required
to operate the unit are mounted on the front of the control panel.
i. Audible Alarm (Optional)
This lights up and may sound an audible alarm if a fault condition is detected. See ALARMS
section 4.h
ii. E-Stop Push Button
The E-Stop push button stops all pumps and the chiller. It is detented. After it has been
depressed it must be physically pulled out to permit resetting the controls.
iii. Power Selector Switch
This switch activates the control power. When it is first turned to the on position the red
Alarm indicating light will illuminate. If the Alarm light does not illuminate verify that the E-
Stop button has been pulled out.
iv. Reset Push Button
This button “resets” the control system after a fault is detected by an optional sensor or an
E-Stop. It will clear the fault display if the fault condition no longer exists. It is also required
when first turning on the power.

18
WFS 1545
Operations Manual
With the power on and the E-Stop button pulled out the blue Control Power indicating light
will illuminate when the Reset push button is depressed. The pumps and chillers can now be
started.
v. Pump 1 Start / Stop Push Buttons
These buttons start and stop the Internal Recirculating Pump
vi. Pump 2 Start / Stop Push Buttons
These buttons start and stop the Process Water Pump
vii. Chiller On / Off Push Buttons
These buttons start and stop the Chiller
CAUTION: To avoid ice damage do not run the chiller for more than 3 seconds without the Recirculating
Pump running.
viii. Indicating Lights
These illuminate when the corresponding pump or chiller is running.
ix. Beacon (Optional)
This illuminates when there is an alarm fault. As a reminder, it will also flash for 3 seconds
once every minute if Alarm Override is active. See Section XXX ALARMS
g. OPTIONAL INSTRUMENTATION AND ALARMS
A variety of sensors and displays can be added to monitor process conditions and provide
additional protection for pumps and equipment. This equipment may initiate alarms if process
conditions exceed or fail to reach preset limits; a condition referred to as “out of window”. See
Section 4.h ALARMS.
i. Water Temperature
This panel meter (PM-1) displays the water temperature that is going out to the process.
The sensor is installed just before the Process Supply Ball Valve. The panel meter is set to
trigger an alarm in the water temperature exceeds 8
o
F and may indicate a fault with the
chiller.

19
WFS 1545
Operations Manual
ii. Circulating Pressure
This panel meter (PM-2) displays the pressure at the circulating pump. The sensor is
mounted in a tee just after the pump output. It measures the accumulative back pressure
for all three recirculating filters. It is set to trigger an alarm if the pressure exceeds 7 PSI
and may indicate a need to replace filter cartridges.
iii. Process Pressure
This panel meter (PM-3) displays the pressure at the process pump. The sensor is
mounted in a tee just after the pump output. It measures the accumulative back pressure
for all process filters. It is set to trigger an alarm if the pressure exceeds 7 PSI and may
indicate a need to replace filter cartridges.
iv. Water Level Sensors
Two water level sensors mounted in the reservoir monitor the water level; one in the Dirty
Side and one in the Clean Side. These will trigger an alarm if the water level is below their
set point.
v. Leak Detector
A leak detecting strip is installed around the base of the WFS unit. A leak detecting relay
(LD-1) is mounted inside the control cabinet that monitors the condition of the sensing
strip. If it detects wetness it triggers an alarm. The trip point is adjustable with a small
knob on the relay.
vi. HMI Touch Screen Display Panel
The HMI is set up with three different pages and these are accessed by selecting one of
the “F” buttons, F1, F3, F5.
• F1 ALM displays an Alarm Silence button
• F2 MSG displays what fault is detected
• F3 OVR Allows for Alarm Override
See Section 4.h ALARMS
h. ALARMS (Optional)
The system responds in two different ways depending on the nature of the fault that triggered
the alarm. The faults are designated as a Class 1 Alarm or a Class 2 Alarm.
It is necessary to press the “RESET” button to clear any alarms. Alarms will only clear if the fault
no longer exists and the Reset button has been pressed.
i. Class 1 Alarm
This type of alarm indicates that there is a potentially damaging condition.
•
••
• Illuminates the beacon
•
••
• Illuminates the panel mounted alarm indicating light.
•
••
• Sounds the audible alarm tone
•
••
• Stops the pumps and chiller
ii. Class 2 Alarm

2
WFS 1545
Operations Manual
This type of alarm indicate that some corrective action may need to be taken. But there is
not imminent likelihood of damage.
• Illuminates the beacon
• Illuminates the panel mounted alarm indicating light.
• Sounds the audible alarm tone
• Does not stop the pumps and chiller
iii. Class 1 Triggers
• Leak
A leak has been detected and may indicate a serious problem.
• Low Water Level
The water level in either the Dirty Side or the Clean Side has been below the sensors
for more than 6 seconds. This can result in pump damage.
NOTE: A low water fault will not clear unless the water level has been above the sensors for more than 3
seconds.
iv. Class 2 Triggers
• High Water Temperature
The temperature of the Process Water exceed 8
o
F. This may indicate a problem with
the chiller.
• High Recirculating Pressure
Total head pressure at the recirculating pump exceeds 7 PSI. This may indicate the
need to change out the filter cartridges in one or more filters.
• High Process Pressure
Total head pressure at the process pump exceeds 7 PSI. This may indicate the need
to change out the filter cartridges in one or more of the filters. It may also indicate an
obstruction to flow someplace in the line such as a partially closed valve.
b. HMI Touch Screen
The HMI has three different screens where different information can be displayed or different
functions can be accessed. The different screens and functions can be selected using the F
buttons.
i. F1 ALM (Alarm Silence)
Pressing the F1 button on the screen will call up the Alarm Silence screen. Touching the
ALARM SILENCE button will stop the audible tone for 6 seconds. The button image will
change indicating that the silence mode has been selected. The beacon and panel light will
remain illuminated. The alarm message on the F3 screen will remain displayed and the fault
will not clear until the Reset Button is pressed.
This manual suits for next models
1
Table of contents
Other HST Water Filtration System manuals
Popular Water Filtration System manuals by other brands
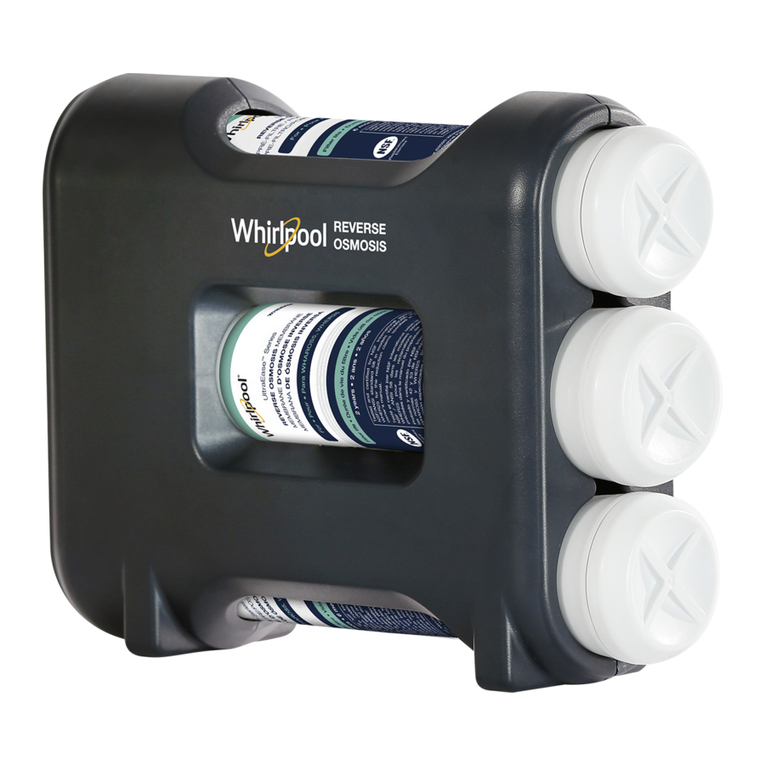
Whirlpool
Whirlpool WHAROS5 user manual
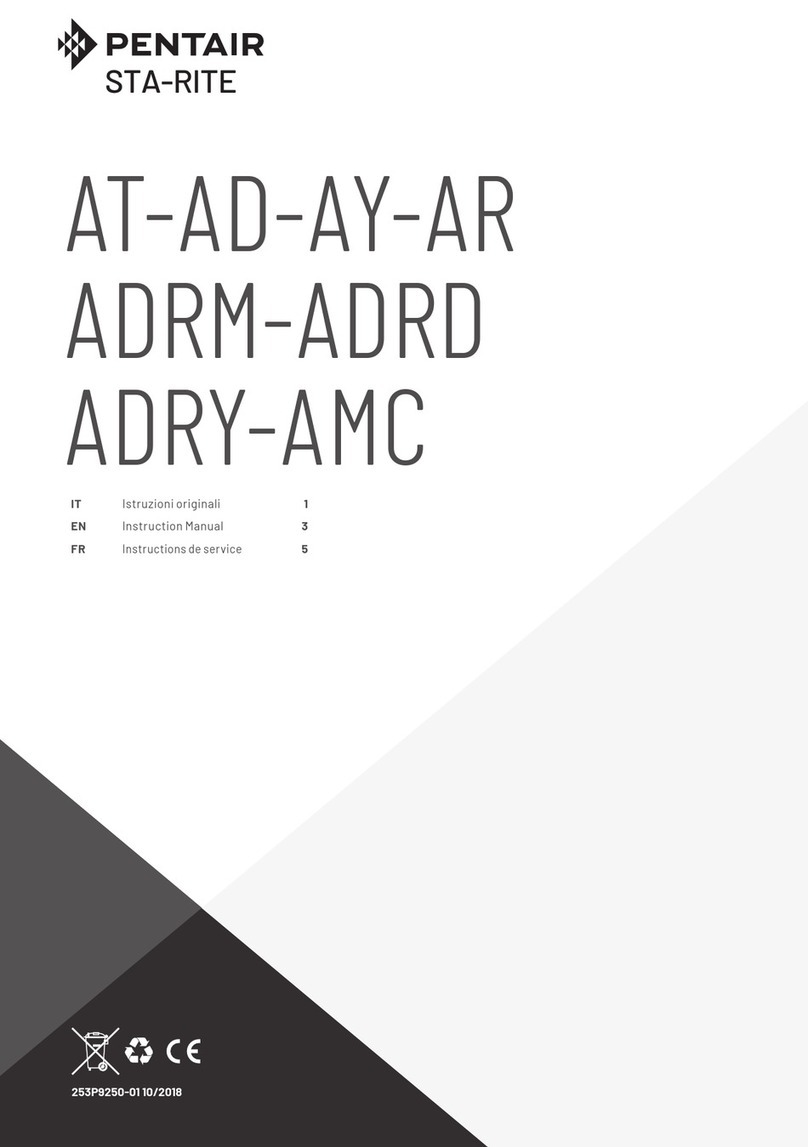
Pentair
Pentair STA-RITE AT 10 1-1,6A instruction manual
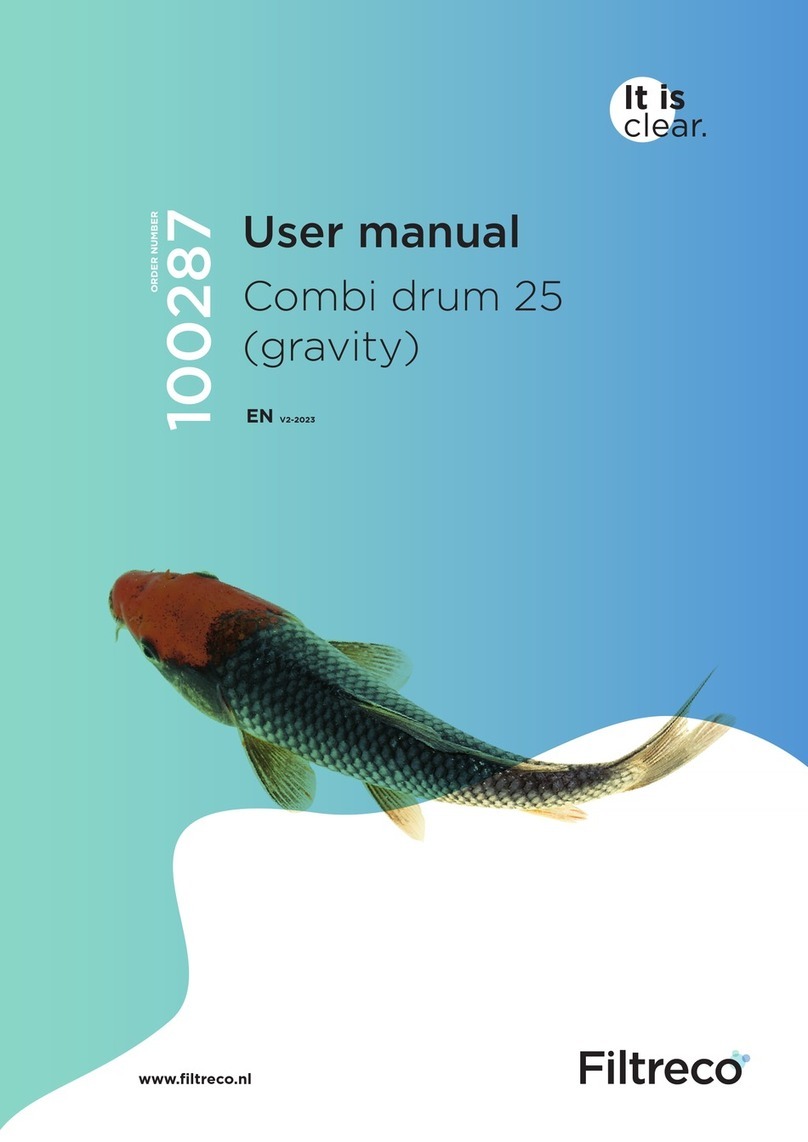
Filtreco
Filtreco Basic combi drum 25 user manual
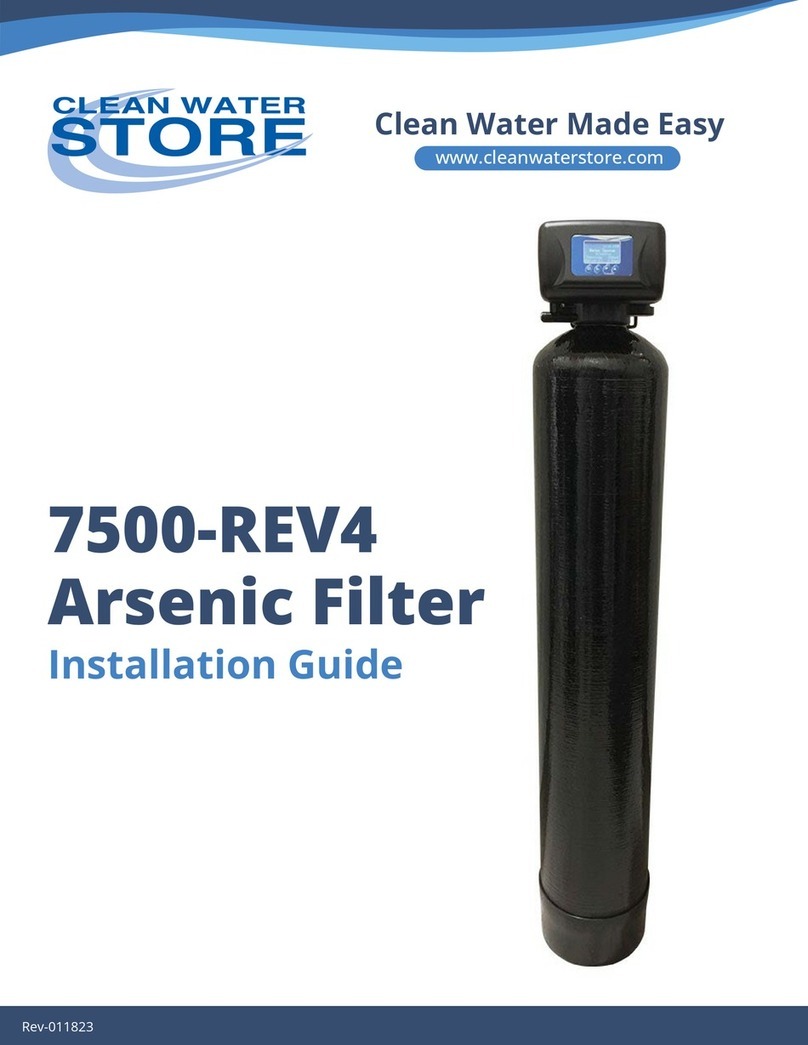
Clean Water
Clean Water 7500-REV4 installation guide
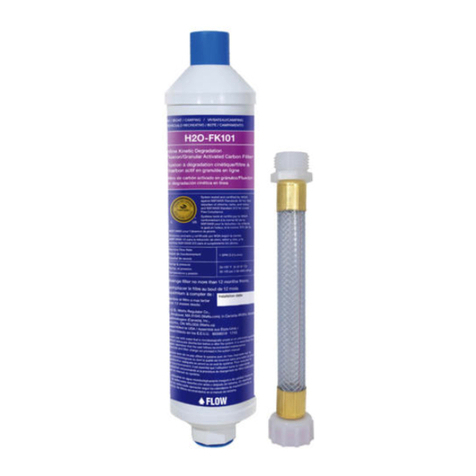
Watts
Watts pure H2O H2O-FK101 Installation, operation and maintenance manual
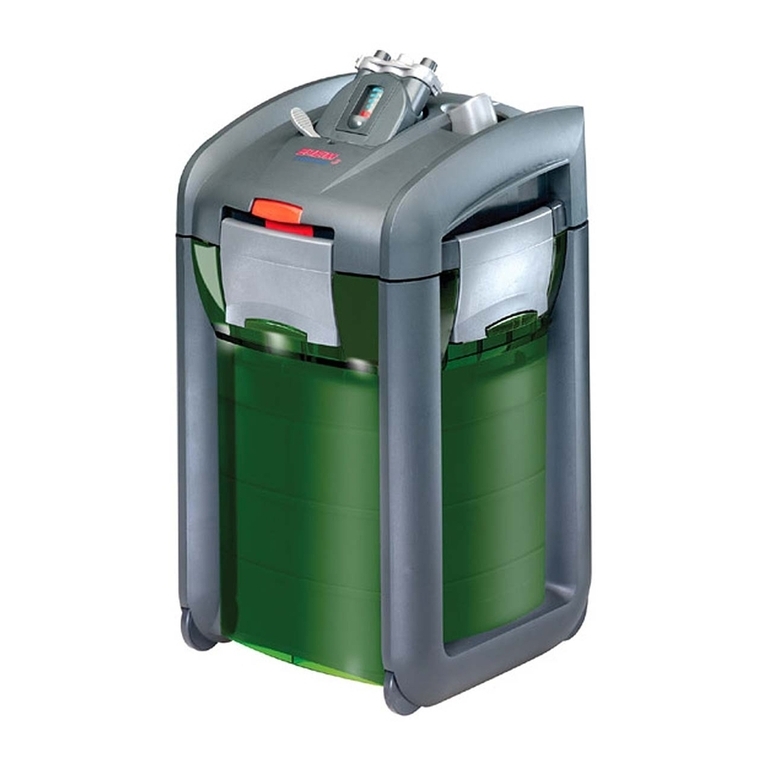
EHEIM
EHEIM Professionel-3 2080 operating instructions