Hydraram MK Series User manual

Hydraram B.V.
Meander 7, 9231DB, Surhuisterveen Holland
www.hydraram.com
11-2021 Certified company
Operation and maintenance manual
MULTI-PROCESSOR - MK SERIES


Table of contents
1. Introduction 1
1.1. Purpose of the user and maintenance instruction manual 1
1.2. Safekeeping of the instruction manual 2
1.3. Updating the instruction manual 2
1.4. Who is this manual intended for? 2
1.5. Glossary and symbols 2
1.6. Copyright 4
2. General information 5
2.1. Manufacturer’s identification data 5
2.2. Attachment identification data and plate 5
2.3. Safety regulations 5
2.4. Set-up procedures to be carried out by customer
technician 6
2.5. General warranty conditions 6
3. Safety 8
3.1.General precautions 8
3.2.Intended use 10
3.3.Unforeseen improper use 10
3.4.Safety indications relating to use of the attachment 11
3.5.Safety indications relating to maintenance of the
attachment 11
3.6. Operator’s position 12
3.7.Accident prevention plates and labels 13
3.8.Safety pictograms 14
3.9.Residual risks 15
3.10.Placement of accident prevention plates and labels 15
3.11. Lighting 15
3.12. Vibration 16
3.13.Noise emissions 16
4. Description of the attachment 16
4.1.Description of the attachment 16
4.2. Permitted enviromental conditions 16
4.3. Attachment technical data 17
5. Installation 21
5.1.Moving and handling 21
5.2. Storage 22
5.3. Coupling check 22
5.4.Mounting the attachment 23
5.5.Use on construction cranes 24
5.6.Hydraulic connections 24
5.7. Stopping and disassembly 26
6. Using the attachment 27
6.1. Putting into operation 27
6.2. Kit replacement 27
6.2.1. Kit removal for models with mechanical coupling 27
6.2.2. Coupling procedure 29
6.3. Operating cycle 30
6.4. Stopping the attachment 30
6.5. Temporary decommissioning 30
6.6. Waste disposal 30
6.7. Dismantling 31
7. Maintenance 31
7.1. De-energising the attachment 31
7.2. General information 31
7.3. Regular maintenance 32
7.4. Scheduled maintenance 32
7.5. Extraordinary Maintenance 33
7.5.1. Checking and replacing the interchangeable
teeth 34
7.5.2. Adjusting and replacing the blades 35
7.5.3. Lubrication 37
7.5.4.Table of lubricants 38
7.5.5. Tightening the screws 39
7.5.6. Anti-wear material 40
7.6. Diagnostics and troubleshooting 41
8. Spare parts 43
8.1.Assistance 43
8.2. Spare parts 43

- 1 -
1. Introduction
1.1. Purpose of the user and maintenance instruction manual
This manual forms an integral part of the attachment and is intended to provide all the information
necessary to:
• Inform operators correctly regarding safety issues;
• Handle, pack and unpack the attachment safely;
• Install the attachment safely;
• Ensure users are fully aware of its operating features and limits;
• Ensure the attachment is used correctly and safely;
• Ensure maintenance operations are carried out correctly and safely;
• Dismantle the attachment safely and in accordance with the standards and regulations regarding
health and safety in the workplace and environmental protection.
IMPORTANT!
Under current law, the personnel responsible for using and operating this attachment are obliged
to read the contents of this document carefully and to ensure the operators and maintenance
technicians have read the parts relating to their specific duties. The time spent doing this this will
ensure correct and safe operation of the attachment.
This document assumes that the applicable laws on safety and occupational hygiene are adhered to where
the attachment is to be used. The instructions, drawings and documentation contained in this manual are of
a confidential, technical nature and may not be reproduced in whole or in part.
This manual is subject to the following limitations:
• It may never take the place of an adequately experienced user;
• For particularly demanding operations, the manual can only provide a summary of the main steps.
The manual should be regarded as an integral part of the attachment and must be kept for future reference
until the attachment is dismantled for disposal. The manual must be stored correctly and kept where it may
be readily consulted when using the attachment with the operating machine.
The company Hydraram may not be held liable in the following cases:
• Improper use of the attachment;
• Use contrary to specific national law;
• Incorrect installation (in the case where the attachment was installed by unauthorised personnel);
• Power supply defects;
• Serious failures to perform the required maintenance;
• Unauthorised modifications and operations;
• Use of replacement parts or materials not specific to the model;
• A total or partial failure to follow the instructions provided;
• Use of the attachment with an incompatible machine;
• Exceptional events.

- 2 -
1.2. Safekeeping of the instruction manual
The manual must be stored carefully and kept together with the attachment whenever the latter changes
hands throughout its working life. The manual will last longer if it is handled carefully with clean hands and
not placed on dirty surfaces.
No parts of the manual should removed, torn out or modified arbitrarily. This manual should be stored in
a cool, dry place near to the attachment it refers to. The manufacturer can supply additional copies of the
manual upon request.
1.3. Updating the instruction manual
The manufacturer reserves the right to change the design of, and make improvements to, the attachment
without notifying customers and without updating manuals that have already been delivered to the user.
Moreover, if the manufacturer makes changes to the attachment already in use at the customer’s premises
that require changes to one or more chapters of the manual, the manufacturer shall be responsible for
sending the manual holder the chapters aected by the change, together with a copy of the new manual
revision list.
1.4. Who is this manual intended for?
This manual is intended for: Installation personnel, Operators and Technicians qualified to carry out
maintenance on the attachment.
OPERATOR refers to the person assigned to operate, adjust, clean and perform regular maintenance
on the attachment.
QUALIFIED PERSONNEL or QUALIFIED OPERATOR, refers to those persons who have attended
specialisation and training courses etc. and who have experience in the installation, operation and
maintenance, repair or transport of the attachment.
EXPOSED PERSON refers to any person located inside an area inside and/or near an operating
machine where their presence may be hazardous to their safety, health or well-being.
The attachment is intended for industrial use and, thus, professional and not general use. As a result, it
may only be operated by qualified persons and persons who specifically:
• are adults;
• are physically and mentally able to perform work of particular technical diculty;
• have been adequately instructed in the use and maintenance of the attachment;
• have been judged suitable by the employer to perform the work entrusted to them;
• are capable of understanding and interpreting the manual and the safety instructions;
• are familiar with the emergency procedures and how to implement them;
• are able to operate the specific type of attachment;
• are familiar with the regulations in force;
• have understood the operating procedures defined by the manufacturer of the attachment.
1.5. Glossary and symbols
This section defines the abbreviations used and the meaning of the symbols used to indicate the operator
qualification level and the status of the attachment. Their use allows for information regarding the correct
and safe use of the attachment to be communicated quickly and clearly.

- 3 -
OPERATOR AREA
The area where the operator must work during
normal use of the attachment.
DANGER ZONE
An area inside and/or near the attachment where
the presence of an exposed person is a risk to the
health of that person.
EXPOSED PERSON
Any person wholly or partially located inside a
danger zone.
MAN-OPERATING MACHINE INTERACTION:
Any situation where an operator interacts with the
attachment during any of the operational phases at
any time during its life cycle.
OPERATOR QUALIFICATION LEVEL
Minimum skill level that the operator must have to
perform the operation described.
NUMBER OF OPERATORS
The number of operators required to perform the
operation described. This number is derived from a
careful analysis by the manufacturer, meaning that
the presence of a dierent number of personnel
could prevent the expected result from being
achieved or expose the personnel to danger.
STATUS OF THE OPERATING MACHINE
The status of the operating machine includes
its operating mode, for example, automatic, jog,
stopped, etc., the condition of the safety devices
on the operating machine, such as safety devices
enabled, safety devices disabled, emergency stop
button pressed, power source insulation type, etc.
RESIDUAL HAZARD
A hazard that it has not been possible to eliminate
or reduce suciently during the design stage, and
against which the existing safety device are not
(or are not completely) eective. Information on
the presence of such hazards is provided in the
manual, as well as instructions and precautions on
how to avoid it.
SAFETY COMPONENT
This is a component used to guarantee a given
safety function and whose failure or poor operation
may have a negative impact on the safety and/
or health of exposed persons: its specific function
is to guarantee safety and is ancillary to the main
function of the machine.
P.P.E.
Acronym for Personal Protective Equipment.
KIT or JAW
Refers to the operating part of the multiprocessor,
consisting of two jaws, one of which is
operated by a hydraulic cylinder. This part is
available in various dierent versions,
which can be interchanged on the same body and
are used for dierent tasks.
WARNING!
Descriptions preceded by this symbol contain very important information/instructions regarding
safety. Failure to observe them may:
• Endanger the well-being of the operators;
• Render the warranty null and void;
• Result in the manufacturer not accepting liability.
IMPORTANT!
This symbol is used to indicate particularly important information regarding the use of the
attachment that the operator must make sure to read and understand thoroughly.

- 4 -
1.6. Copyright
The copyright of this manual is the property of Hydraram. This manual is intended for use by operating and
maintenance personnel. It contains instructions and technical diagrams that may not be copied, in whole or
in part, distributed or examined by unauthorised persons for competitive purposes or divulged to any other
third party.
SYMBOLS RELATING TO OPERATOR QUALIFICATION LEVELS
General labourer: an operator with no specific skills who is qualified only to carry out simple
tasks as directed by qualified technicians.
Lifting and handling equipment operators: an operator qualified to use vehicles and
equipment for lifting and handling materials and machinery (in strict accordance with the
manufacturer’s instructions), subject to the legislation in force in the country where the
machinery is in use.
Operator: person able to install and operate the attachment.
Maintenance mechanic: a qualified technician, who is able to assemble and disassemble the
attachment and adjust, service and repair its mechanical parts, as necessary. Typically, such
personnel are not qualified to work on live electrical systems.
Manufacturer’s technician: a technician provided by the manufacturer to perform complex
operations under unusual or special circumstances or when in agreed with the user.
Depending on the situation, such personnel must possess the appropriate skills and
qualifications for the work to be carried out.

- 5 -
2. General information
2.1. Manufacturer’s identification data
Hydraram B.V.
Meander 7 9231DB Surhuisterveen - The Netherlands
AFTER-SALES SERVICE / SPARE PARTS / CALL CENTRE
www.hydraram.com
2.2. Attachment identification data and plate
Each attachment is identified by a CE plate indelibly marked with all the relevant machine information
Always provide this information when contacting Hydraram or the customer service centre. The plate
is secured to the attachment in a protected position where it is easy to read. This position may vary
depending on the model.
2.3. Safety regulations
The attachment has been manufactured in conformity with the safety standards listed below:
UNI EN ISO 12100: Machine Safety - Fundamental concepts, general design principles -
Risk assessment and reduction.
UNI EN ISO 13857: Machine safety - Safety distances to prevent hazard zones from being reached
by upper and lower limbs.
UNI EN 349: Machine safety - Minimum distances to avoid crushing parts of the human body.
UNI EN 474-1: Earthmoving machines - Safety - General requirements.
UNI EN 474-5: Earthmoving machines - Safety - Requirements for hydraulic excavators.
The regulations mentioned in this manual may not apply to specific situations that may arise during various
work phase

- 6 -
2.4. Set-up procedures to be carried out by customer technician
Except where otherwise stipulated in the contract, the customer shall be responsible for:
• Preparing the working environment/area and operating equipment in conformity with the legally
applicable specific safety regulations in the country where the attachment is to be used;
• Checking that the attachment is coupled to the operating machine in compliance with the legally
applicable specific safety regulations in the country where the attachment is to be used;
• Providing the hydraulic supply system for the attachment, in conformity with the regulations
applicable in the country of use and the instructions in this manual.
WARNING!
It is the specific responsibility of the customer/user to integrate these instructions into the system/
plant user and maintenance manual and to provide any additional information the operator may
require.
2.5. General warranty conditions
Hydaram guarantees that all products are free from material or manufacturing defects. Under the terms of
this warranty, Hydraram’s responsibilities are limited to the repair or replacement with a similar part at the
company’s plant, on condition that the product is returned within 8 days of the date on which the defect is
detected, and provided the defect is correctly identified by photographs or the product is returned with all
shipping expenses prepaid.
The company will replace or repair, at its own discretion, any part that, after examination, is determined
to demonstrate material or manufacturing defects. In any event, Hydraram’s responsibility shall be limited
to the original purchase price of the product; any costs incurred in relation to the necessary inspections
or report generation are excluded. No repairs will be carried out on site; the warranty applies exclusively
when the product is returned to the company.
This warranty replaces any other warranties, expressed or implied, including, but not limited to, guarantees
of marketability and suitability, irrespective of purpose; furthermore, under the terms of this warranty
Hydrarm’s obligations and responsibilities shall not include any shipping or other expenses, i.e. installation
costs or liability for any direct, indirect or resultant damages or for delays caused by any such defect.
This warranty applies exclusively to new products manufactured by Hydraram. Products manufactured by
third parties are covered exclusively by warranties oered to Hydraram by the respective suppliers and will
be subjected to any inspections or checks as requested by such parties.
Products manufactured or welded by Hydraram as standard units are guaranteed for twelve (12) months
from the delivery date. This guarantee period is completely independent of the eective date the product
was put into operation.
If the customer tampers with the product or attempts to disassemble in any other location than the
supplier’s premises or repair workshop, and/or without notifying the manufacturer in advance, this warranty
shall be considered null and void. Hydraulic cylinders or components returned under the guarantee must
not be disassembled and must be returned intact to Hydraram. Any welding, modifications or repairs to

- 7 -
the attachment must be authorised in writing in advance by Hydraram; any service operations performed
without such authorisation shall result in this warranty being considered null and void. Hydraram may not
be held liable for any costs/charges deriving from the customer’s failure to meet these warranty conditions.
Hydraram reserves the right to make changes or modifications to the accessories, which, in the company’s
reasonable opinion, may improve the performance and eciency of the machine or improve production
techniques, at any time. Hydrarm is under no obligation to implement such changes or modifications
retroactively on any machines that are already in use. Any operations that are expressly forbidden, either
verbally or in any written document, or repairs or assembly procedures that are not recommended or
authorised by Hydraram shall result in the warranty being considered null and void.
The warranty does not include any parts that are subject to normal wear and tear, or any that are broken
or damaged due to improper use of the attachments supplied by Hydraram. In this case, the customer
shall arrange for delivery and collection at our factory at their own expense; if the customer requests
repairs at their own premises (assuming this is possible), they shall be required to pay for the seller’s travel
expenses. If, during the warranty period and as a result of customer negligence or any other factor out of
the control of Hydraram, the company is unable to intervene promptly in the aftermath of breakdown or
fault condition, the customer shall be responsible for any further deterioration or damages resulting from
the continued use of the Hydraram products. Any such additional damage is not included in the terms of
the warranty.
The company Hydraram may not be held liable for any expenses for repairs performed by, or requested by
the customer in workshops other than the authorised structures or in the event where such activities were
not authorised in advance. The customer may not claim compensation for any damages deriving from
machine downtime during the warranty period.
IMPORTANT!
This warranty is valid only if the product has been entirely paid for in conformity with the required
supply conditions and is returned within 2 weeks from the date of purchase. Failure to pay for the
products within the agreed terms shall result in the warranty being considered null and void, even if
the goods in question are entirely paid for at a later date.

- 8 -
3. Safety
3.1.General precautions
Operator safety is one of the manufacturer’s main concerns. When designing and manufacturing a new
attachment, we attempt to foresee all possible danger situations and, naturally, to adopt suitable safety
measures, paying particular attention to operations that are especially hazardous. The manufacturer may
not be held liable for the consequences of any failure to adhere to the safety and accident prevention
instructions set out in this manual.
IMPORTANT!
Before using the attachment, operators must read the instructions contained in this manual carefully
read and ensure they adhere to the instructions it contains.
The manufacturer has fitted the attachment with all the protection and safety devices considered
necessary and, in addition, has provided sucient information for its safe and correct use. To this end,
wherever necessary, each chapter contains the following information regarding every possible man-
attachment interaction:
• Minimum operator qualifications required;
• Number of operators necessary;
• Status of the attachment;
• Residual risks;
• Necessary or recommended personal protective equipment;
• Prevention of human errors;
• Prohibitions/obligations regarding reasonably foreseeable incorrect behaviour.
WARNING!
This information must be adhered to scrupulously.
The user may supplement the manufacturer’s information with additional instructions, provided that they
do not conflict with that set out in the manual, in order to contribute to the safe use of the attachment. All
personnel assigned to work on the attachment must ensure they are wearing appropriate clothing.
• Avoid the use of clothing that could become entangled with parts of the attachment;
• Avoid wearing ties or other loose items of clothing;
• Avoid wearing rings or bracelets that could cause hands to be trapped in the components of the
attachment.
Wherever necessary, the manual provides additional recommendations for preventive measures to taken
by the user, personal protective equipment, helpful information for avoiding human errors and instructions
designed to prevent reasonably foreseeable prohibited behaviours.

- 9 -
It is, however, extremely important to adhere scrupulously to the following instructions:
• It is strictly forbidden to operate the attachment with the fixed protection panels removed;
• It is strictly forbidden to inhibit or bypass the safety devices installed on the attachment;
• Washing must be performed with the hydraulic separation devices disconnected;
• Do not modify any parts of the attachment;
• The manufacturer may not be held responsible for malfunctions caused by failure to respect the
above instructions. In the event it is necessary to modify the attachment, we strongly recommend
contacting the manufacturer directly.
IMPORTANT!
The manufacturer may not be held liable for personal injury or damage caused by the attachment in
the case of:
• Use of the attachment by inadequately trained personnel;
• Improper use of the attachment;
• Defects in the hydraulic power supply;
• Incorrect installation;
• Lack of the required maintenance;
• Unauthorized service or modifications;
• Use of non-original or unsuitable spare parts;
• Total or partial failure to follow the instructions;
• Use contrary to specific national law;
• Disasters or exceptional events.
Control and checks
Checks must be performed by an expert; they must be visual and functional, with the purpose of
guaranteeing the safety of the attachment. They include:
• A check of all the load-bearing structures, which must be free from cracks, breakages, damage,
deformation, corrosion, wear or alteration with respect to their original specifications;
• A check of all the mechanical components;
• A check of all the safety devices installed on the attachment;
• A check of all connections with pins and screws;
• A functional check of the attachment;
• A check of the status of the attachment;
• A check to ensure that the hydraulic system is airtight and that it operates correctly.
WARNING!
If anomalies are found, they must be eliminated before putting the attachment back into operation.
If the person performing the check finds any dangerous cracks or faults, they must notify the manufacturer
of the attachment immediately. In the event of a malfunction, stop using the attachment immediately and
carry out the appropriate checks and/or repairs.

- 10 -
Make sure that there are no objects between the parts of the attachment. After any maintenance work,
check that there are no objects remaining between moving parts.
To guarantee maximum safety when transporting the attachment, it is FORBIDDEN:
• To tamper with any part of the attachment;
• To leave moving parts unattended;
• To use the attachment when it is not working at 100% eciency;
• To modify the attachment with respect to its intended use without explicit authorisation from the
manufacturer or without assuming full liability as per current legislation;
• To attempt to move the moving parts manually in the absence of power.
3.2.Intended use
The attachment described in this Manual was designed to be mounted and used on earthmoving
machines (consult the paragraph 4.3. for the type). The attachment must be used for crushing and
demolishing reinforced cement structures and cutting ferrous material with characteristics similar
to those described in paragraph 4.3. This attachment is intended exclusively for professional use.
3.3.Unforeseen improper use
It is strictly prohibited for anyone to use the attachment for any purpose other than that expressly permitted
and documented. Any improper use of the latter will absolve the manufacturer of all and any damage to
property and persons and render any guarantees null and void. The attachment must always be used in
the manner and at the times and places required by good practice and in conformity with the applicable
legislation, even if there are no laws regulating the sector in the country of use.
Specifically, the attachment must not be used:
• For any purpose other than those set out in paragraph 3.2, or for any other purpose not mentioned
in this manual;
• In an explosive or corrosive atmosphere or where there are high concentrations of dust or oily
substances suspended in the air;
• In an atmosphere where there is a risk of fire;
• With its safety devices disabled or not working.
• To lift or transport persons, animals or objects.
• To lift or extract parts stuck in the ground.
• To reach elevated positions by climbing onto the equipment.
• Depending on the structure to be cut, do not start working on the lower tips of the structure when
cutting as this could cause the upper part to collapse.
• To strike structures to be demolished.
• As a support point for moving the operating machine.
• To pull, push from the front or the side, strike or impact in any way.
WARNING!
The arm must be moved safely, with slow, accurate movements. Avoid abrupt movements.

- 11 -
3.4.Safety indications relating to use of the attachment
Overhead working may result in falling debris or blocks of material. Make sure that
the machine the attachment is installed on has the necessary protections for performing
this type of work and that the cab has falling object protective structures (FOPS).
• Before operating the attachment, the
operator must read this manual carefully and
have thorough knowledge of the operating
machine’s technical specifications and
controls.
• It is recommended that the operator be
trained to make best use of the attachment.
Unauthorized and/or unqualified personnel
may not use the attachment.
• Do not approach to within 20 metres of the
range of action of an operating machine
when working with an attachment.
• Before starting work with the attachment,
warn any persons in its vicinity.
• Wear personal protective equipment
whenever the attachment is in use.
• The attachment may only be operated
by a qualified operator who has read and
understood the contents of this manual.
• Do not allow unauthorized personnel to
operate the attachment or perform any type
of maintenance on it.
• The operator must quickly release their grip
on the attachment in the event of danger.
• Do not use the attachment if it is not working
properly.
• The attachment may only be used when it is
installed on the operating machine using the
upper bracket and the pins provided.
• Make sure that the floor can support the load
of the operating machine.
• Make sure in advance that the work area
contains no pipes with pressurised gas
or fluids that could be damaged during
demolition: risk of explosion.
• Ensure the operating machine remains at
a distance of at least 10 metres from live,
overhead electrical lines.
• To avoid generating and spreading dust
while working, it is necessary to dampen the
work area with water.
• In the event of a malfunction of the
attachment or damage to its components,
contact the maintenance manager without
attempting to repair it.
• Do not remove the safety devices or
protective guards.
3.5.Safety indications relating to maintenance of the attachment
• Maintenance must only be performed by qualified personnel. Unauthorized and/or unqualified
personnel may not adjust or repair the attachment.
• Use the most suitable tools for the tasks required.
• All adjustments, maintenance, repair or cleaning must be performed while the operating machine’s
engine is o, the attachment must be stably supported on the ground and there must be no residual
hydraulic pressure. Any residual hydraulic pressure must be released by opening and closing
the attachment several times while the engine is o and while depressurising the oil tank. All
maintenance operations must be marked on the card in the cabin.
• When cleaning, assembling, disassembling, performing maintenance and transporting, ensure that
the attachment is perfectly stable and lock it with the pins provided to prevent it rotating. All moving
parts must be secured by external constraints (such as slings or supports).
• All service operations on the rotation slew ring must be performed by a specialized technician
equipped with a torque wrench for tightening the screws.

- 12 -
• For the hydraulic connections, only use hydraulic hoses and fittings that conform to the SAEJ517 or
DIN20066 standards for the specified pressures. Failure to observe the above could compromise
the safety of the attachment.
• Always check the hoses are intact and that they have not been damaged in any way. If necessary,
ensure they are replaced immediately. Search for leaks using small pieces of paper or cardboard
and never with fingers to avoid injuries to the skin due by high pressure oil.
• The oil can reach very high temperatures. Before performing any service on external surfaces, wait
for them to completely cool.
• Never perform hasty or makeshift repairs that could compromise the correct operation of the
attachment. If in doubt, always request service by specialized personnel.
• It is forbidden to perform checks and/or replace parts during operation.
• All checks and maintenance that require the removal of the safety protections shall be performed
entirely at the user’s risk. Therefore, we recommend that such operations be performed exclusively
by specialised and authorised technicians.
• In the case of operations or repairs that need to be performed in positions that are not directly
accessible from the ground, use ladders or lifting devices that are safe and that conform to national
safety regulations.
• In the event of repairs near or below the attachment, make sure that there are no moving parts
that can start working and that parts that are unstable by nature are not positioned on or near the
attachment; always block them using adequate tools.
• Unless expressly specified by this manual, do not repair or adjust the attachment (or parts of it)
during operation, in order to avoid being hooked by moving parts.
• Wear personal protective equipment whenever the attachment is in use, or when working in its
vicinity.
• Only use original spare parts to replace worn parts.
• Do not make any adjustments or changes that the manufacturer has not previously agreed to and
approved in writing.
WARNING!
• These safety standards supplement and do not replace current local safety standards.
• Any tampering by the user shall absolve the manufacturer of all and any liability and shall render
the user solely responsible to the competent authorities for the prevention of accidents.
IMPORTANT!
Hydraram declines all liability for any accidents, injuries to personnel or damage to property
resulting from the failure to adhere to the general safety instructions and the standards set out in
this document.
3.6. Operator’s position
When the operating machine is working, the operator must pay particular attention to their own position in
other to avoid potential hazards to themselves and persons nearby. The area adjacent to the attachment is
divided into two areas:

- 13 -
Operator Areas:
These are the areas in which the operator must work during normal operation of the attachment. The
“operator areas” are considered potentially dangerous areas. In these areas, which are indicated on the
following diagram, the operator should pay the maximum attention while working to protect the well-being
of persons close by;
It is extremely important to follow all the accident prevention rules described up to this point.
Danger Zones:
These are the areas that unauthorised personnel must not approach while the attachment is in use.
(A) Control area
(B) Person in safe area
(C) Person in danger area
(D) Range of action of the machine
(E) Safe area limit
3.7.Accident prevention plates and labels
The accident prevention plates attached to the attachment include the main warnings and instructions that
should be borne in mind during use.
Symbol Description Symbol Description
“Read the manual”
Read this Use and Maintenance Manual
carefully.
“Safety distance”
Remain at a safe distance from the range
of operation of the operating machine.
“Burn hazard”
Surfaces that can reach high
temperatures resulting in burn hazards.
Wait for the attachment to cool before
carrying out any work on it.
“Danger of ejected material”
Remain at a safe distance from the range
of operation of the operating machine.
“Cutting hazard”
Do not approach the operating machine
during the work cycle. In the event of
maintenance, wear personal protective
equipment.
“Crushing hazard”
Do not approach the operating machine
during the work cycle. In the event of
maintenance, wear personal protective
equipment.

- 14 -
3.8.Safety pictograms
In the manual various pictogram may be used to indicate warnings regarding DANGER, PROHIBITION and
OBLIGATION.
The following pictograms indicate when it is obligatory to wear personal protective equipment (PPE)
Symbol Description Symbol Description
“Greasing points”
Indicates the points to be lubricated.
“Oil input”
Power/rotation oil inlet.
“Oil return”
Power/rotation oil outlet
“Rotation direction”
Direction in which the attachment must
rotate
“Drainage”
Overflow point for excess oil.
“Lifting points”
Use the indicated points when handling
and moving the attachment
Symbol Description Symbol Description
Danger of crushing upper limbs Danger of crushing limbs
Entanglement hazard Dragging hazard
Generic hazard Removal of safety devices prohibited
Cleaning, greasing, repairing or adjusting moving parts manually prohibited
Symbol Description Symbol Description
Protective goggles obligatory Work clothing obligatory
Ear defenders obligatory Protective gloves obligatory
Safety shoes obligatory Hard hat obligatory

- 15 -
3.9.Residual risks
A residual risk is a hazard that cannot be completely eliminated through design and protective techniques
or a potential hazard that is not obvious.
Hazard: crushing/cutting limbs
Possibility/location of hazard
When assembling disassembling or performing
maintenance on the attachment there is a risk of
the attachment or part of it falling, or of sudden
movement of part of the attachment.
Protections/precautions
Such operations must be carried out carefully by
trained personnel. Wear suitable P.P.E.
Hazard: ejected oil
Possibility/location of hazard
When assembling/disassembling or performing
maintenance on the hydraulic components of the
attachment there is a risk that oil may ejected as a
result of residual pressure.
Protections/precautions
De-pressurise the circuit fully as shown in this
manual. Such operations must be carried out
carefully by trained personnel. Wear eye protection.
3.10.Placement of accident prevention plates and labels
The position of the accident prevention plates may vary depending on the model of the attachment.
3.11. Lighting
Lighting in the work area must conform to applicable legislation law in the country where the attachment is
being used and must provide good visibility at every point, not create dangerous reflections and allow for
clear visibility of the controls and the entire work area up to the safety limits required for objects that may
be ejected. Since the attachment has no independent lighting, the environment must be provided with
general lighting of 250 to 400 lux at every point in the work area.

- 16 -
3.12. Vibration
No dangerous vibrations are generated provided the attachment is used in accordance with the correct
operating instructions.
3.13.Noise emissions
The attachment does not generate noise (sound pollution).
4. Description of the attachment
4.1.Description of the attachment
The MK Series Multiprocessorr is an attachment that has been designed and constructed by Hydraram. It
is a functional and versatile attachment designed to handle a variety of work (demolition, crushing, cutting
scrap and metal profiles). The attachment consists of a main body and the jaws. There are 6 types of jaws.
Pulverizer kit: used to reduce cement elements and separate the rebar from the cement.
Shear kit: used on job sites and in industrial demolition depots to cut ferrous materials such as profiles,
plates and pipes.
Combi kit: for demolitions of structures made of reinforced cement with a high percentage of ferrous
materials.
Universal Kit: for controlled demolition of concrete structures and for the immediate reduction of rod
armor during the crushing of the concrete.
Tankshear Kit: indicated in construction sites and in stores for the demolition industry for cutting ferrous
materials such as steel and tanks.
Demolition kit: Is designed for primary demolition phases of most precision, as indicated for the demolition
of concrete structures and the removal of materials at relevant heights.
Various types of jaws (kits) are available that can be interchanged on the same body. The body is fitted
with a slew ring for continuous hydraulic rotation, so as to reduce moving operations as much as possible
and provide the highest level of precision.
The closing force is produced by a hydraulic cylinder, which enables the device to demolish even the
most resistant materials. The body and various types of kits are made from wear-resistant steel with
high elasticity. This ensures excellent anti-abrasion characteristics together with exceptional mechanical
strength.
The hinges are made of thermally-treated steel alloy and rotate on hardened, ground bushings with
grooves for internal lubrication.
Kits with an interchangeable teeth and blade system ensures they can be replaced quickly and directly on
site, thus avoiding having to repair worn parts reducing maintenance costs and limiting machine downtime.
4.2. Permitted enviromental conditions
The attachment is suitable for operating in environments that are:
• At altitudes no higher than 3,000m above sea level;
• At temperatures between -20 °C and +50 °C with an average temperature of about 25°C;
• At relative humidity between 30% and 95%.

- 17 -
WARNING!
The attachment is NOT suitable for use in environments that are:
• Explosive.
• Corrosive.
• Subject to high fire risk.
4.3. Attachment technical data
Pulverizer kit Combi kit
Demolition kit Tankshear kitSteel kit
Universal kit
Base body
Table of contents
Popular Computer Hardware manuals by other brands
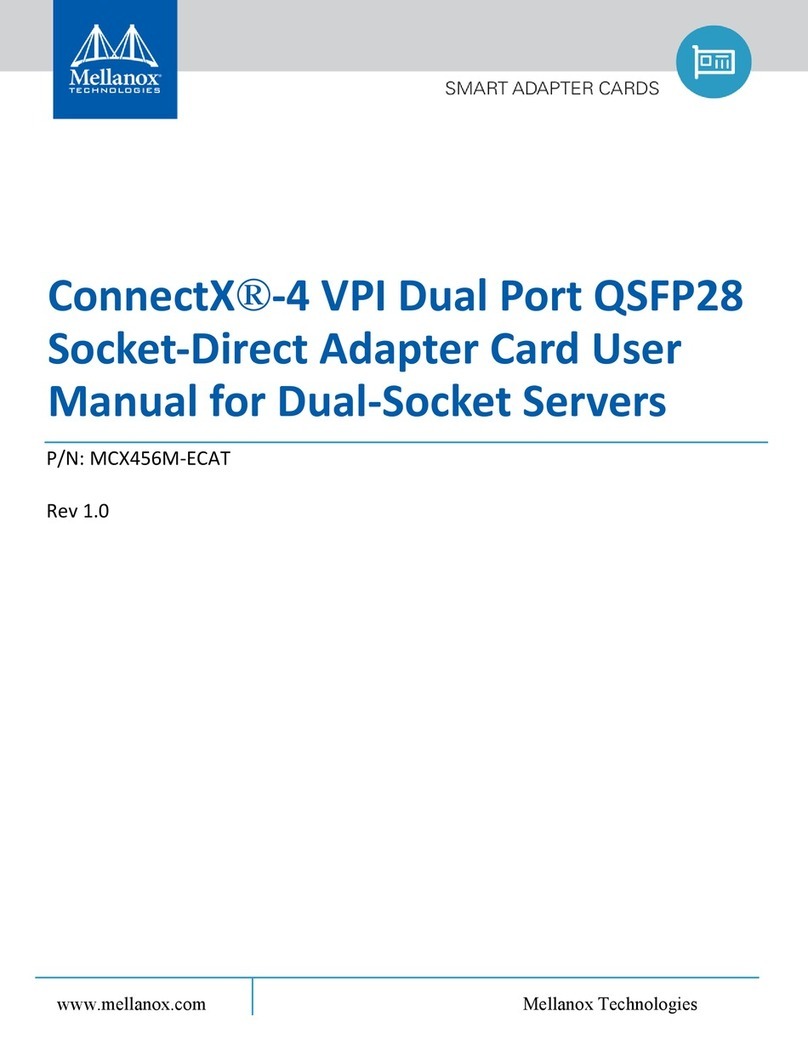
Mellanox Technologies
Mellanox Technologies MCX456M-ECAT user manual
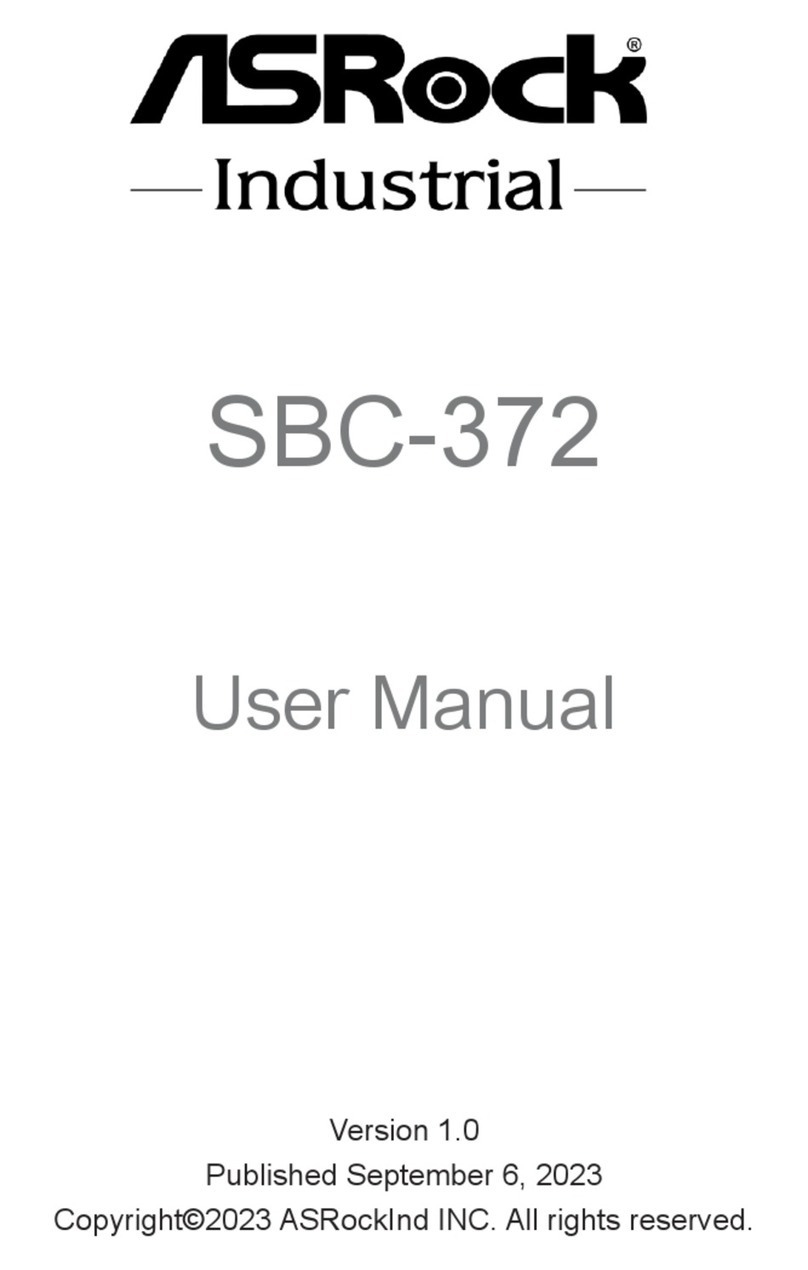
ASROCK
ASROCK SBC-372 user manual
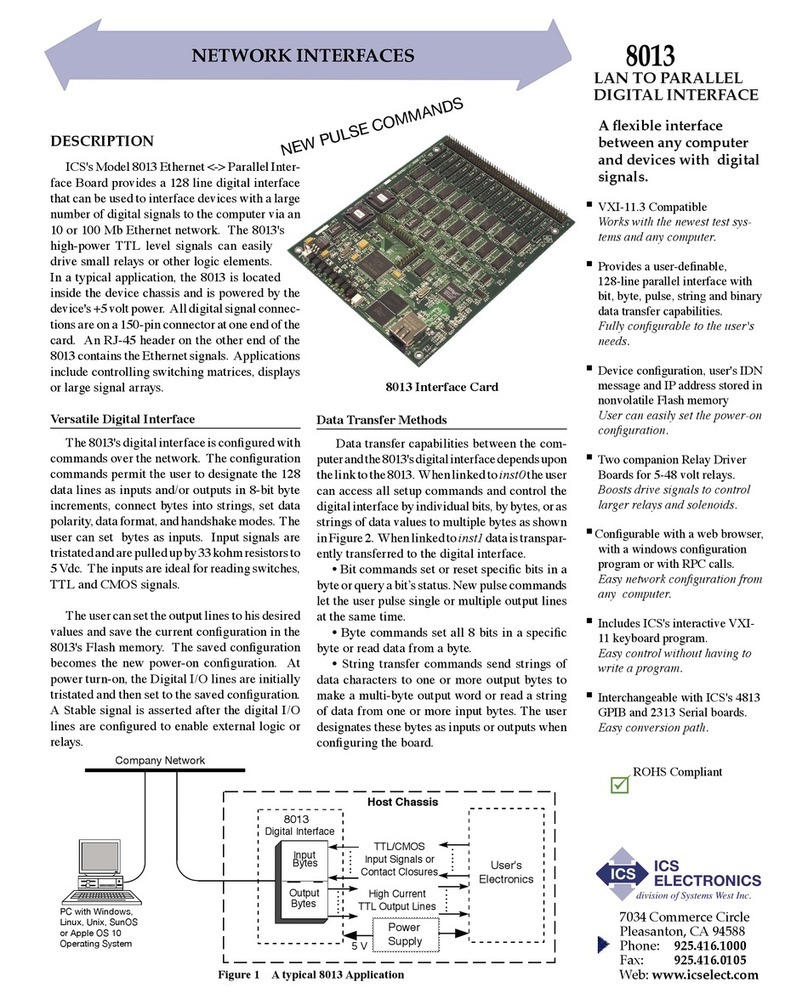
ICS ELECTRONICS
ICS ELECTRONICS 8013 manual
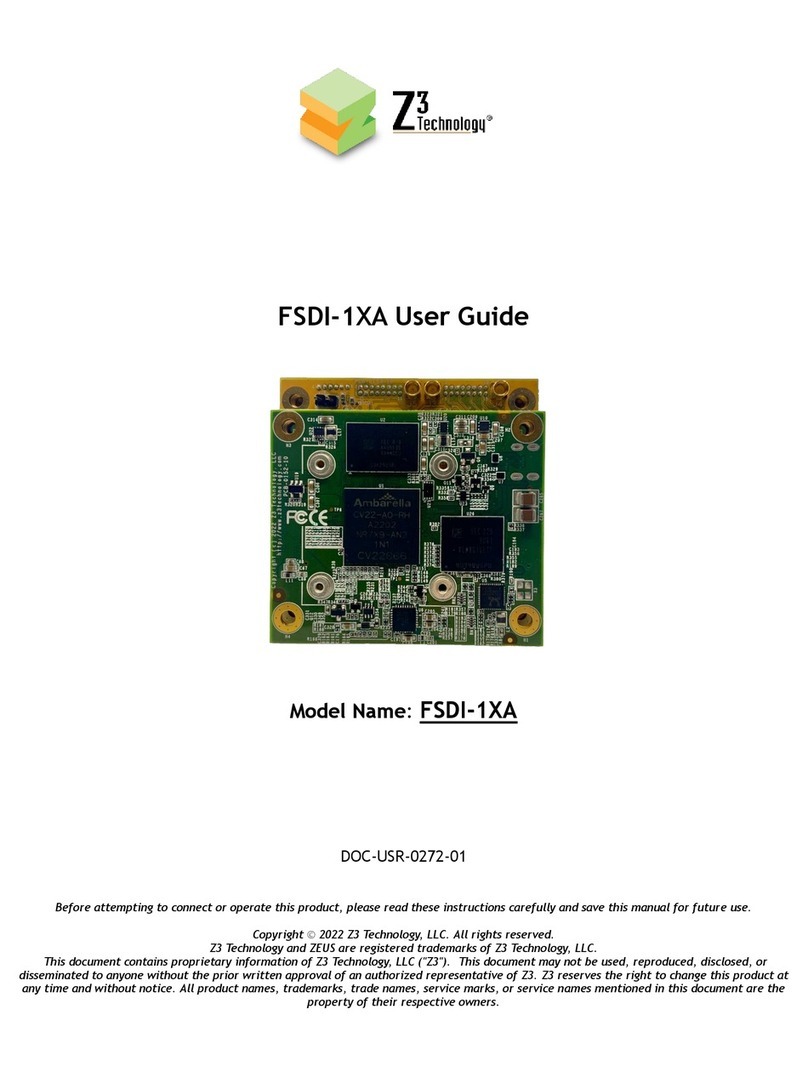
Z3 Technology
Z3 Technology FSDI-1XA user guide
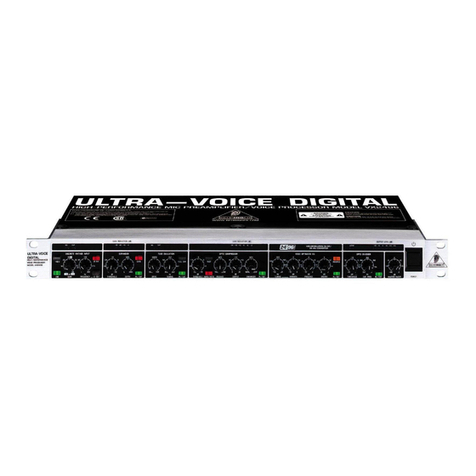
Behringer
Behringer Ultravoice Digital VX2496 Technical specifications
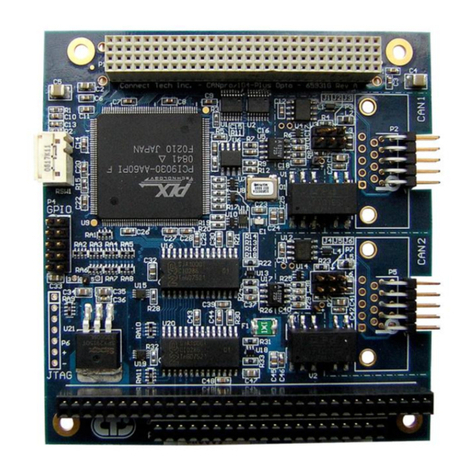
Connect Tech
Connect Tech CANpro/104-Plus Opto user manual