IMT CAS440HU User manual

Printed on 22 August, 2016
Manual Part # 99901339
CAS440HU Air Compressor
Revised: August 22, 2016
IOWA MOLD TOOLING CO., INC.
PO Box 189
Garner, IA 50438
Tel: 641-923-3711 FAX: 641-923-2424
Website: http://www.imt.com
Copyright © 2016 Iowa Mold Tooling Co., Inc.
All rights reserved
No part of this publication may be reproduced, stored in a retrieval system, or transmitted in any
form or by any means, electronic, mechanical, photocopying, recording or otherwise without the
prior written permission of Iowa Mold Tooling Co., Inc.
Iowa Mold Tooling Co., Inc. is an Oshkosh Corporation Company.


i
Contents
Revisions ..................................................................................................................................................... ii
Compressor Introduction 3
Compressor Precautions ...............................................................................................................................5
Compressor Safety........................................................................................................................................6
Compressor Information Record...................................................................................................................7
CAS440HU Recommended Spare Parts.......................................................................................................8
CAS440HU Specifications 9
Installation 11
PTO & Pump Installation ...........................................................................................................................11
PTO Installation..........................................................................................................................................11
Driveline and Pump Installation .................................................................................................................13
Underdeck Compressor Installation............................................................................................................14
Oil Cooler (optional)...................................................................................................................................15
Operation 17
Operation ....................................................................................................................................................17
Shutdown....................................................................................................................................................18
Maintenance & Repair 19
Maintenance Schedule................................................................................................................................20
Compressor Hydraulic Oil..........................................................................................................................21
Hydraulic Fluid Deterioration.....................................................................................................................22
Compressor Hydraulic Oil Change.............................................................................................................23
Compressor Filter Element Replacement ...................................................................................................24
Drive Belt....................................................................................................................................................24
Compressor Hydraulic System Precautions................................................................................................25
Troubleshooting Guide...............................................................................................................................26
Parts 27
CAS440HU Compressor Parts (51720149)................................................................................................28
Thread Torque Charts.................................................................................................................................31

ii Contents
Revisions
DATE LOCATION DESCRIPTION
20070817
MAINTENANCE
SCHEDULE
REVISED COMPRESSOR OIL CHANGE SCHEDULE TO 6 MONTHS
AND 12 MONTHS
20071004
51720149
ECN 10523 - CHANGE ITEM #39 FROM 72065616 TO 72661642
20071127
MAINT.
SCHEDULE
ECN 10612 - CHANGED NOTE IN MAINTENANCE SCHEDULE TO 6
MONTHS
20090409
51720149
ADDED MOTOR CALLOUT, ADDED SPECIFICATIONS
20090722
51720149
ECN 11060 - PLUMBING CHANGES
20090914
51720149
ECN 11070 - CHANGED TO HOSES RATHER THAN HARD-TUBING
PLUMBING.
20110610
51720149
ECN 11448 - NEW PRESSURE RELIEF VALVE.
20140227
51720149
PER ENGINEERING MARKUP – IMAGES UPDATED
20160705
51720149
Replaced missing images/drawings.
20160707
51720149
ECN1239MADE SURE WASHER QTY WAS 12 FOR KIT51720597
20160822
Changed 12/ psi off/10 psi on to 12 bar off/ 10 bar on, in Specification
Table, pressure switch column.

3
This volume provides information on the installation, operation, and repair of IMT hydraulic air
compressors. In addition to reading the manual, it is your responsibility to become familiar with
government regulations, hazards, and the specific operation of your equipment. Use caution
and common sense while operating and maintaining the equipment and follow all safety
procedures and regulations. Treat this equipment with respect and service it regularly.
MODIFICATIONS
Modifications to your equipment must be performed with IMT approved accessories, parts and
optional equipment. If in doubt, contact IMT prior to making any modifications. DO NOT alter or
modify any safety device! All safety devices must be inspected, tested and maintained in proper
working condition.
Decals regarding safety and operation are considered safety equipment, and must be kept clean
and legible.
The equipment owner and/or designated employee is responsible for informing all operators,
maintenance personnel, and others involved in equipment operation about the safe operation
and maintenance of the equipment. If questions arise concerning safe operation, contact IMT or
your IMT distributor for clarification.
WARRANTY
Warranty of this unit will be void on any part of the unit subjected to misuse due to overloading,
abuse, lack of maintenance and unauthorized modifications. No warranty - verbal, written or
implied - other than the official, published IMT new machinery and equipment warranty will be
valid with this unit.
NOTICE TO THE OWNER / USER
If your equipment is involved in a property damage accident, contact your IMT distributor
immediately and provide them with the details of the accident and the serial number of the
equipment. If an accident involves personal injury, immediately notify your distributor and IMT
Technical Support at:
IOWA MOLD TOOLING CO., INC.
500 HWY 18 WEST
GARNER, IA 50438
641 - 923 - 3711
SECTION 1
Compressor Introduction

4 CAS440HU Air Compressor Manual Part # 99901339
WARNING
READ YOUR MANUAL!! FAILURE TO READ, UNDERSTAND AND FOLLOW ANY SAFETY
PROCEDURES APPLICABLE TO YOUR EQUIPMENT MAY RESULT IN EQUIPMENT
DAMAGE, SERIOUS INJURY, OR DEATH.
MANUAL STRUCTURE
Throughout this manual, three means are used to draw the attention of personnel. They are
NOTEs, CAUTIONs and WARNINGs and are defined as follows:
NOTE
A NOTE is used to either convey additional information or to provide further emphasis for a
previous point.
CAUTION
A CAUTION is used when there is the very strong possibility of damage to the equipment or
premature equipment failure.
WARNING
A WARNING is used when there is the potential for personal injury or death.

Section 1 Compressor Introduction 5
Compressor Precautions
Failure to follow operating and maintenance
procedures as outlined in this manual could result
in equipment damage, personal injury or death.
Follow all maintenance procedures and intervals.
Do not use air from this compressor for
breathing or food processing. Air from this
compressor will cause severe injury or death if
used for breathing or food processing.
Maintenance must be performed only by trained
and qualified personnel, using correct tools,
specified torques and approved replacement
parts.
Hot oil under pressure can cause severe injury
or death. Shut down, let cool and relieve
pressure in compressor before servicing.
All electrical components and cable wiring must
be installed and grounded in accordance with
NFPA, national electrical codes and applicable
state and local codes.
Do not overfill the compressor with oil. Use
correct quantity of manufacturer's lubricant.
Repair leaks and clean spills immediately.
Before removing guards or servicing the
compressor, disconnect all power supplies.
Display warning signs and lock out electrical
circuits.
Compressors generate high temperatures. Do
not touch or otherwise come in contact with hot
surfaces. Doing so can cause severe personal
injury.
All guards must be in position and secure before
and during operation.

6 CAS440HU Air Compressor Manual Part # 99901339
Compressor Safety
WARNING
AVOID PERSONAL INJURY OR PROPERTY DAMAGE! READ YOUR MANUAL! All units
are shipped with a detailed operators and parts manual which contains vital information for the
safe use and efficient operation of this unit.
AIR COMPRESSOR SAFETY PRECAUTIONS
Safety is basically common sense. While there are standard safety rules, each situation has its
own peculiarities that cannot always be covered by rules, and with your experience and common
sense, you are in a position to ensure your safety. Lack of attention to safety can result in death,
serious injury, accidents, and efficiency reductions. Watch for safety hazards and correct them
promptly. Use the following safety precautions as a general guide to safe operation:
Do not attempt to remove any compressor parts without first relieving the entire system of
pressure.
Do not attempt to service any part while the machine is operating.
WARNING
AVOID PERSONAL INJURY OR PROPERTY DAMAGE! Check the compressor sump oil
level only when the compressor is not operating and the system is completely relieved of
pressure. Open the service valve to ensure relief of system air pressure when performing
maintenance on compressor air/oil system.
Do not operate the compressor at pressure or speed in excess of its rating as indicated in
Compressor Specifications.
Periodically check all safety devices for proper operation.
Do not play with compressed air. Pressurized air can cause serious injury to personnel.
Exercise cleanliness during maintenance and when making repairs. Keep dirt away from
parts by covering parts and exposed openings.
Do not install a shut-off valve between the compressor and compressor oil sump.
DANGER
AVOID DEATH OR SERIOUS INJURY!
Do not use IMT compressor systems to provide breathing air. Such usage, whether supplied
immediately from the compressor source, or supplied to breathing tanks for subsequent use,
can cause serious bodily injury.

Section 1 Compressor Introduction 7
IMT disclaims any and all liabilities for damage for loss due to personal injuries, including
death, and/or property damage including consequential damages arising out of any IMT
compressors used to supply breathing air.
Do not disconnect or bypass safety circuit system.
Do not install safety devices other than authorized IMT replacement devices.
Close all openings and replace all covers and guards before operating compressor unit.
Do not leave tools, rags, or loose parts on the compressor or drive parts.
Do not use flammable solvents for cleaning parts.
Keep combustibles out of and away from the compressor and any associated enclosures.
The owner, lessor, or operator of the compressor are hereby notified and forewarned that any
failure to observe these safety precautions may result in damage or injury.
IMT expressly disclaims responsibility or liability for any injury or damage caused by failure to
observe these specified precautions or by failure to exercise that ordinary caution and due care
required when operating or handling the compressor, even though not expressly specified
above.
Compressor Information Record
TO BE COMPLETED BY DEALER
CHASSIS INFORMATION
TRANSMISSION MAKE:
MODEL:
PTO NUMBER:
PTO %:
COMPRESSOR AND HYDRAULIC PUMP INFORMATION
COMPRESSOR MODEL:
SERIAL NUMBER:
PUMP MAKE:
MODEL:
RESERVOIR CAPACITY:
ENGINE RPM:

8 CAS440HU Air Compressor Manual Part # 99901339
CAS440HU Recommended Spare Parts
Recommended Spare Parts for one-year for CAS440HU Under-deck Compressor:
NOTE: This spare parts list does not necessarily indicate that the items can be expected to fail in
the course of a year. It is intended to provide the user with a stock of parts sufficient to keep the
unit operating with the minimal down-time waiting for parts. There may be parts failures not
covered by this list. Parts not listed are considered as not being Critical or Normal Wear items
during the first year of operations and you need to contact the distributor or manufacturer for
availability.
PART NO.
DESCRIPTION
QTY
CODE
COMPRESSOR ASSEMBLY COMPONENTS (51720149)
73051614
HYDRAULIC MOTOR
1
W
73540449
RELIEF VALVE
1
W
73052091
RETURN FILTER
1
P
COMPRESSOR (70073051)
70073727
LP INTAKE VALVE
1
W
70073726
LP EXHAUST VALVE
1
W
70732447
HP INTAKE VALVE
1
W
73054340
HP EXHAUST VALVE
1
W
70073766
RING SET
1
W
70143298
RELEASE VALVE KIT
1
W
70732429
INTERCOOLER TUBE LH
1
W
70732430
INTERCOOLER TUBE RH
1
W
70732448
KIT - VALVE SET
1
P
76391490
SHAFT SEAL
1
W
73054339
POP-OFF, 70 psi
1
W
73054031
PILOT VALVE
1
C

9
CAS440HU
DELIVERY AT 175 PSI
46 cfm (1300 lpm)
FLUID CAPACITY
28 gal (106 l) (on IMT Predator)
FILTER - HYDRAULIC SUCTION
100 mesh
FILTER - HYDRAULIC RETURN
10 microns
PRESSURE SWITCH
175 psi off / 150 psi on (12 bar off/ 10
bar on)
COMPRESSOR PULLEY RPM
980 rpm (900 - 1000)
NORMAL OPERATING PRESSURE
1850 psi (130 bar)
MAXIMUM PRESSURE
2400 psi (165 bar)
GPM
16 gpm (60 lpm)
MOTOR PULLEY DIAMETER
10.75" (27 cm)
COMPRESSOR PULLEY
DIAMETER
18.88" (48 cm)
SECTION 2
CAS440HU Specifications


11
PTO & Pump Installation
In some cases the customer or his agent may have to install a compressor, PTO, and pump.
These instructions will provide general information to assist with installation. The pump may be
installed either directly on the PTO or may be driven by a driveline.
PTO Installation
A power take-off (PTO) must be properly matched to the vehicle’s transmission as well as the
requirements of the crane. In order to properly select a PTO the following information is needed:
1 Make and model of transmission in the carrier vehicle.
2 Power requirements of the crane being driven.
3 Necessary PTO speed.
4 Direction in which the PTO must turn.
5 PTO torque required.
If possible, use a hydraulic pump directly mounted to the PTO. This will eliminate an auxiliary
driveshaft and it is easier to install as it eliminates driveline angle and phasing errors. It is also
quieter and should require less maintenance since driveline lubrication will not be necessary.
PTO manufacturers provide specific installation instructions with their products. Their
instructions should be followed when installing the PTO. The following steps are provided as an
introduction to the installation.
NOTE
IT MAY BE NECESSARY TO REMOVE AND MODIFY EXHAUST COMPONENTS TO
PROVIDE SPACE FOR PTO CLEARANCE.
1 Chock the wheels of the vehicle.
2 Secure any part attached to or on the vehicle which could move or pose a hazard.
SECTION 3
Installation

12 CAS440HU Air Compressor Manual Part # 99901339
3 Run the engine and transmission in a well ventilated area. Listen for noises which indicate
any engine/transmission problems. The engine and transmission should be in good operating
condition before the installation of the PTO.
4 Become familiar with the PTO manufacturer’s installation instructions, warnings, and
precautions.
5 After the engine and transmission have cooled, drain the transmission fluid. Check the fluid
for signs of damage such as metal chips, etc.
6 With the vehicle engine “Off”, visually inspect the transmission for gear damage or foreign
particles lodged between gear teeth.
7 Remove the PTO from its shipping container. Inspect for foreign objects which may have
lodged in the PTO cavity.
8 Mount the PTO per manufacturer’s instructions.
9 Check backlash per manufacturer’s instructions.
10 Refill the transmission with manufacturer’s recommended lubricant to the proper level.
11 Install the shifter cable to suit conditions. Always allow a slight overshift on lever or knob to
make certain PTO is fully engaged.
CAUTION
AVOID SHARP BENDS IN THE SHIFTER CABLE. ALL BENDS SHOULD HAVE A
MINIMUM 6" RADIUS. TIGHTER BENDS CAUSE DIFFICULT OPERATION OF THE
SHIFTER CABLE.
12 Make sure the vehicle has all safety and operation decals.
13 Start the engine, engage the PTO and allow to run for 5 to 10 minutes. Check for leaks,
unusual noise and proper operation.
14 Check PTO mounting bolts for proper torque as specified by manufacturer.

Installation 13
Driveline and Pump Installation
The pump may be driven using a driveline rather than directly mounting to the PTO. The
following steps are a guide in this application.
NOTE
Before installing driveline, refer to instructions for proper driveline installation techniques.
1 Install the PTO (see instructions).
2 Loosely bolt the pump mounting bracket to the adjustable bracket.
3 Bolt the adjustable bracket to the frame at a point that will not exceed 48" (122cm) from the
PTO and will not cause a joint angle greater than 8°.
4 Check the pump rotation. Install pump, pump end yoke and PTO end yoke.
5 Size, cut and weld the driveline to the necessary length. Ensure driveline balance and run
out meet specification. Allow 1" (2.54 cm) extra for PTO end yoke.
6 Install driveline in phase with proper operating angle calculations. Lock set screws. Grease
U-joints and mating spline.
7 Ensure all mounting bolts are tight.
DANGER
70392891
Keep clear of rotating drive shaft.
Never work on or near an installed
power take-off or driveline with the
engine running.
CONTACT WITH A ROTATING DRIVELINE
WILL CAUSE
KEEP AWAY
DEATH OR SERIOUS INJURY
WARNING! AVOID DEATH OR SERIOUS INJURY! The driveline installer must inspect the
final position of the driveline to determine whether an operator or other personnel are
protected from rotating driveline hazards. If the protection is insufficient, a guard MUST be
installed. Contact IMT for information on installing a guard.

14 CAS440HU Air Compressor Manual Part # 99901339
Underdeck Compressor Installation
Use these instructions as a guide only, due to variations.
1 Position the compressor below the compressor compartment with the belt side to the rear of
the compartment.
2 Lift the compressor base into position so the base is flush with the bottom of the
compartment. Make sure there is clearance within the compartment and no interference is
present. Support the compressor in this position.
3 Using the base as a template, drill eight 17/32" diameter holes through the compartment.
4 Bolt the compressor base to the walls of the compartment using 1/2" grade 5 cap screws, flat
washers and lock nuts.
5 Connect the hydraulic hose from the pump to the relief valve connected to the hydraulic drive
motor on the compressor. See the compressor assembly drawing.
6 Connect the return line to the reservoir. See the compressor assembly drawing.
7 If the compressor is positioned properly, torque all mounting bolts per Torque Data Chart.
8 Connect the air hoses per the compressor assembly drawing.
9 Install the engine speed control as shown and connect hoses from compressor to speed
control.
10 Fill the oil reservoir and open the suction gate valve. Disconnect the pressure hose at the
hydraulic pump. Engage the PTO and turn the vehicle engine with the starter until oil flows
through the pressure side of the pump. Reconnect the pressure hose. Pull out the
compressor switch and open the gate valve to the air receiver. Disengage the PTO and start
the truck. Depress clutch and engage PTO. Release the clutch slowly. It may be necessary
to warm the truck engine so that it will pull at idle RPM. Push in the compressor switch. This
will close the control valve and start the compressor. Allow for warm-up time. Close the gate
valve on the air receiver. This will activate the speed control. Adjust the engine speed
control for proper operating RPM. Check for system leaks and proper operation.
11 Install compressor kill switch. See figure.
- +
BATTERY
IGNITION
SWITCH
NORMALLY
CLOSED
DOOR
SWITCH
COIL (GAS)
OR
FUEL SOL. (DIESEL)

Installation 15
Oil Cooler (optional)
Oil coolers vary in their installation dependent on available space and other considerations.
Install the oil cooler in front of the carrier vehicle's radiator, or, as an alternative, in a protective
structure which is cooled by an electric fan. See figure for general location within the hydraulic
system.
RELIEF
VALVE
COMPRESSOR
PULLEY
MOTOR
OIL
COOLER
RESERVOIR RETURN
FILTER CONTROL
VALVE
GATE
VALVE SUCTION
FILTER
PUMP


17
Operation
The compressor has an operating time limit of approximately three hours depending upon
ambient air temperature (outside air temperature), weather conditions and whether an oil cooler
has been installed. Oil coolers will extend the three hour limit.
CAUTION
THE HYDRAULIC OIL TEMPERATURE MUST NOT BE ALLOWED TO EXCEED 190°F
(88°C). IF THE OIL TEMPERATURE REACHES THIS LIMIT, THE SYSTEM MUST BE
SHUT DOWN AND ALLOWED TO COOL. OIL COOLERS WILL EXTEND THE THREE-
HOUR LIMIT.
To start the compressor:
1 Ensure the PTO is disengaged, control valve is open (pull the compressor switch out) and
the receiver drain cock is open.
2 Start the truck engine and allow it to idle until it reaches the proper operating temperature
(refer to the vehicle owner’s manual).
3 Depress the clutch, engage the PTO and carefully release the clutch pedal. Allow the
system to warm up for the time period as shown in chart.
COMPRESSOR WARM-UP TIME
AMBIENT AIR TEMPERATURE
(°°F) IDLING TIME (WARM-UP)
+40° OR ABOVE NONE
+20° TO +40° 2 - 5 MINUTES
0° TO +20° 5 - 10 MINUTES
-20° TO 0° 10 - 15 MINUTES
-40° TO -20° 15 - 20 MINUTES
BELOW -40° 20 MINUTES MINIMUM
4 When starting the compressor, the RPMs will automatically increase due to low volume of air
in the system.
SECTION 4
Operation

18 CAS440HU Air Compressor Manual Part # 99901339
CAUTION
1000 RPM MAXIMUM! Operating this unit in excess of 1000 RPM, measured at the
compressor flywheel, will void your warranty. Engine RPM may be different.
5 The flow required to the compressor is 16 GPM.
Shutdown
Shut down the compressor system as follows:
1 Allow the compressor to build to maximum pressure and the truck engine will automatically
idle down.
2 Place the compressor control valve in the open (off) position.
3 Depress the clutch pedal and disengage the PTO.
4 Open the receiver drain cock and discharge the air in the receiver.
WARNING
Federal law prohibits driving the carrier vehicle on public roads with the receiver filled with
compressed air. Always drain the receiver before moving the vehicle.
Table of contents
Other IMT Air Compressor manuals
Popular Air Compressor manuals by other brands

California Air Tools
California Air Tools 8010AAD owner's manual
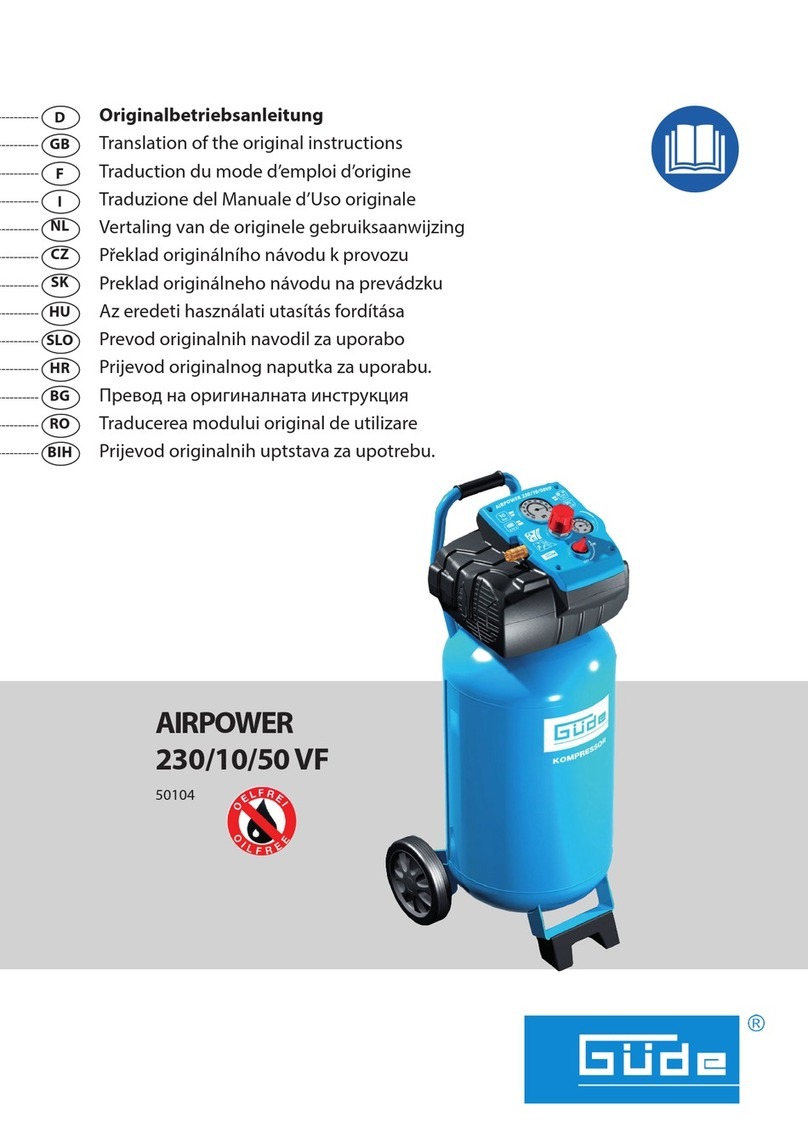
GÜDE
GÜDE AIRPOWER 230/10/50 VF Translation of the original instructions
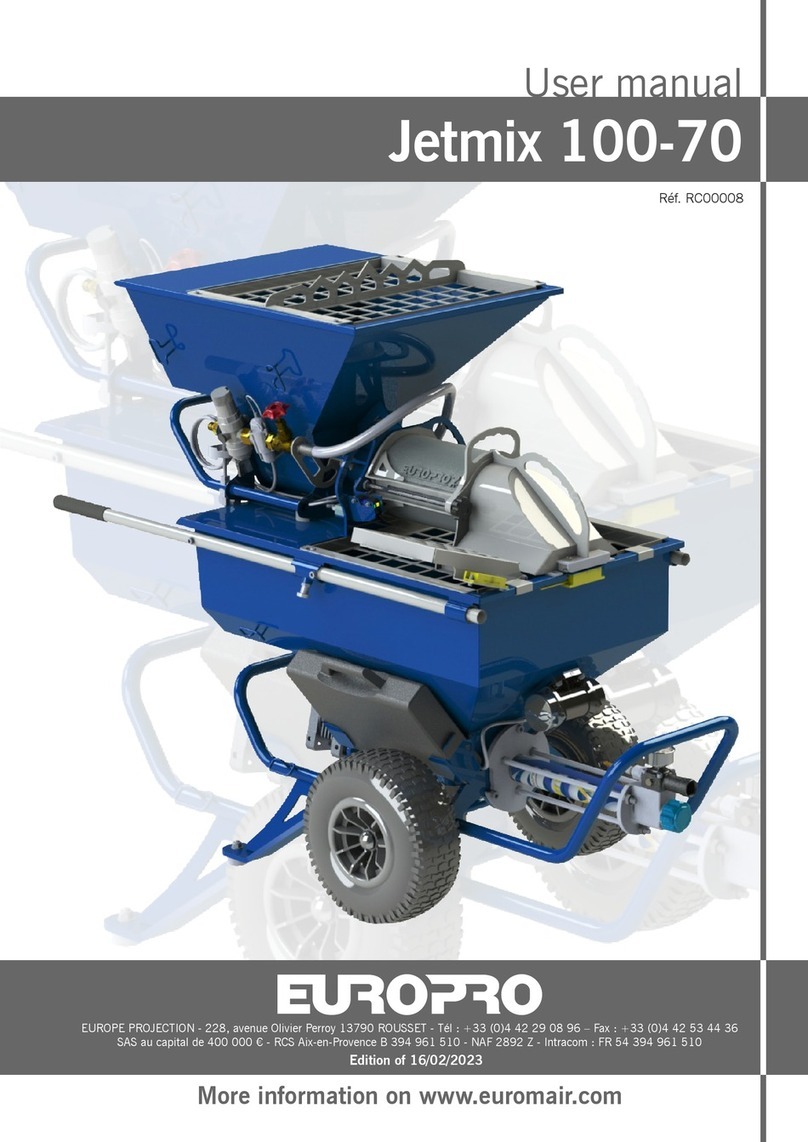
EUROPE PROJECTION
EUROPE PROJECTION Jetmix 100-70 user manual
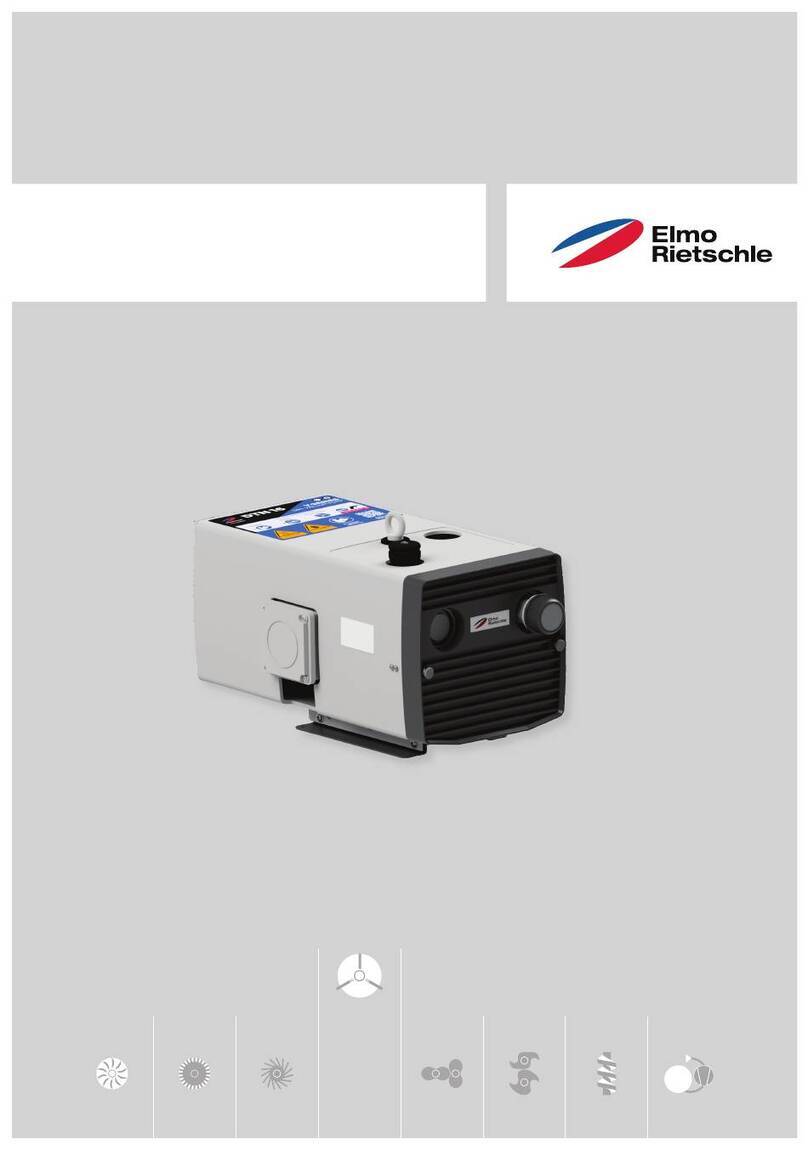
Elmo Rietschle
Elmo Rietschle V Series operating instructions

WilTec
WilTec AF18-2 Operation manual

Klutch
Klutch 52491 owner's manual