Isel ICP 4030 iMC-P User manual

Assembly instructions for CNC basic
machines (incomplete machines)
Operating instructions for CNC machines
(complete machines)
Type/Model: ICP 4030 iMC-P
© isel Germany AG, January 2018, German

ICP 4030 iMC-P
1/71
January
2018
On these operating instructions
Abbreviations
MRL Machinery Directive 2006/42/EC
Symbols used
In this manual, you will find various symbols to draw your attention to important
information / facts and risks:
Warning!
Warning of hazards that may lead to adverse health effects,
physical injury or death.
Warning! Lethal voltage
Warning of danger from electrical current. Ignoring this may lead to
serious injury or death.
Attention!
This symbol highlights instructions, which if not followed may
result in damage or malfunction.
Information
This symbol highlights important information and notices.
Safety notice
Before you start up the CNC machine ICP 4030, work with the machine or make
additions or changes to the electrical installation of the machine / in the control
cabinet /5/ of the machine, please read carefully:
•the safety notices in these operating instructions (Section 3) and
•the safety instructions for electrical drives and controls in the operating
instructions manual Positioning module with CANopen interface /1.1/ or
/1.2/
These operating instructions must be kept close to the machine and be
accessible to the staff (operators, fitters, maintenance personnel) at all times.

ICP 4030 iMC-P
2/71
January
2018
Copyright
© isel Germany AG, 2018 all
rights reserved.
Despite the utmost care, printing errors and mistakes cannot be excluded. We
would be grateful for any suggested improvements or references to errors.
CE marking for (complete) CNC machines:
isel-CNC machines are CE compliant and marked accordingly. The CE
conformity declaration applies to these machines.
no CE marking for partly completed machinery:
Partly completed machinery (Definition as per Machinery Directive 2006/42/EC)
have no CE marking.
The declaration of incorporation applies to party completed machinery.
For all other machine parts and components, to which CE safety guidelines apply,
start-up is prohibited until all appropriate requirements are met.
The company isel Germany AG accepts no responsibility or liability if you make
changes to the machine without the manufacturer's consent, which affect the CE
conformity of the machine.
The EMC test is only valid for the original machine configuration delivered ex
works. Manufacturer:
isel Germany AG
Bürgermeister-Ebert-Str. 40,
D-36124 Eichenzell
Tel.: (06659) 981-700
Fax: (06659) 981-776
E-mail: automation@isel.com
http://www.isel.com
Art.-No. 970280 BD016 (Original operating instructions)
Review index
Date of
change
Reason for change
Changed
by
c
24.01.2018
Update ICP 4030
JT
b
25.03.2015
Description stop key 4.3.2
RL
a
03.12.2014
Serial number:
RL

ICP 4030 iMC-P
3/71
January
2018
Contents
1 Introduction......................................................................................................... 5
2 Intended use, foreseeable misuse..................................................................... 7
3 Safety notices.................................................................................................... 10
3.1 General safety notices.................................................................................10
3.2 Special safety notices..................................................................................12
4 Setting up and connecting the CNC machine................................................. 14
4.1 Scope of supply...........................................................................................14
4.2 Delivery status ex works (quality assurance) ..............................................14
4.3 Space required ............................................................................................15
4.4 Transporting the CNC machine ...................................................................16
4.5 Setting up the CNC machine .......................................................................16
4.6 Coordinate system and reference point .......................................................17
4.7 Processing machine ....................................................................................17
4.7.1 Protective cover with solenoid interlock 18
5 Design and operation ....................................................................................... 19
5.1 Safety notices..............................................................................................19
5.2 Overview .....................................................................................................20
5.3 Connections ................................................................................................21
5.3.1 Connections on the back 21
5.3.2 Front Panel Controls 22
5.3.3 Structure of the stepper motor control 23
5.4 Connections on the stepper motor controller ...............................................24
5.4.1 Safety notices 24
5.4.2 Access to the stepper motor controller and its components 24
5.4.3 Connections 25
5.5 Setting the stepper motor output stages ......................................................30
6 Installation and commissioning ...................................................................... 33
6.1 Safety notices..............................................................................................33
6.2 Preparation..................................................................................................33
6.3 Create connections......................................................................................33
6.4 Software installation ....................................................................................34
6.5 Mode AUTOmatik –Production on the CNC machine .................................36

ICP 4030 iMC-P
4/71
January
2018
6.5.1 Manufacture of operational readiness 36
6.5.2 Production: Processing / manufacturing a component 41
6.5.3 Ending the operational readiness 42
6.6 Operating modes.........................................................................................43
6.6.1 Use of the ICP 4030 in CNC operation 43
6.6.2 Use of the ICP 4030 in DNC operation 44
7 Cleaning, lubrication and maintenance........................................................... 45
7.1 Cleaning ......................................................................................................45
7.2 Lubrication...................................................................................................45
7.2.1 Basic lubrication 45
7.2.2 Re-lubrication 45
7.2.3 Lubrication points of the linear axes X, Y and Z 46
7.3 Maintenance intervals according to operating hours counter .......................48
7.4 Maintenance activities .................................................................................49
8 Returning used electrical and electronic equipment for disposal ................ 50
9 Remote diagnosis ............................................................................................. 51
10 Accessories ...................................................................................................... 52
11 Technical Data ................................................................................................ 53
11.1 Dimensions and weight................................................................................53
11.2 Electrical Data .............................................................................................53
12 Malfunctions...................................................................................................... 54
13 Declaration of conformity or declaration of incorporation ........................... 55
13.1 Declaration of Conformity for (complete) machine .......................................56
13.2 Declaration of incorporation for (partly completed) basic machines .............57
14 Exploded views / spare parts lists................................................................... 58
14.1 Structure axis systems.................................................................................60
15 Source directory ............................................................................................... 66
16 Index................................................................................................................ 66
17 Annex .............................................................................................................. 68
17.1 Service card ................................................................................................68

ICP 4030 iMC-P
5/71
January
2018
1 Introduction
All isel-CNC basic machines (pursuant to the Machinery Directive 2006/42/EC partly
completed machinery or partial machines) pr isel-CNC machines (pursuant to the
Machinery Directive 2006/42/EC Machinery, i.e. complete machines) of the type ICP
4030 are tried and tested CNC machines, which offer a wealth of possibilities for two or
three-dimensional machining of components.
The basis is formed by precisely tailored and variably mountable standard profiles and
drive units, which are fitted depending on the requirements of the machine type (the
so-called machine kinematics). The external appearance of the machine of one type is
always the same. The applications of the specific CNC machine in accordance with
the tool mounted (on the Z axis) can be quite diverse.
A common feature of all CNC basic machines / CNC machines of the type ICP 4030 is
the control and safety concept and the basic structure of the mechanics. Each machine
is configured before delivery, tested for many hours in depth, measured at the factory
and run in.
For each basic machine / machine delivered, a measurement and test report with the
customer's order number is kept at the manufacturer isel Germany AG, and can be
requested by you as a buyer. All basic machines / machines are measured with
circularity tester QC20 by Renishaw® in all three interpolation planes or laser
interferometer.
As a prerequisite for your work, you need basic knowledge in CNC technology and PC
application, and if possible, a basic knowledge of the terminology of the currently
applicable Machinery Directive (MRL):
- MRL 2006/42/EC since 29.12.2009 legally binding
Please follow these operating instructions so that you
•can work properly install / start up the CNC basic- / CNC machine
•and work it safely and effectively
•Keep hazards away from people and equipment
•and fully use the performance of the CNC machine.
The statements in these operating instructions are based on a standard scope of
delivery, with which the machine is ready for operation. You can skip statements (e.g.
regarding accessories and software), which do not affect your machine in your initial
study of these operating instructions.

ICP 4030 iMC-P
6/71
January
2018
The statements in these operating instructions apply to the following equipment /
technical level of the CNC machine control:
•all
motor output stages are
fitted with
Standstill monitoring
(from 01/07/2008)
•the operating software used is: ProNC /6/ / Remote /7/ from software version
V1.46.2.1
To install and set up software or the accessories, please also consult the other
manuals and instructions.
These are indicated in the source directory.
Example CNC basic machine ICP 4030:
•(partly completed machine)
•without tool, no clear definition of the intended purpose
•this CNC machine is delivered without a CE mark
•the declaration of incorporation applies to this CNC machine.
Fig 1: ICP 4030 EC CNC basic machine
Example CNC basic machine ICP 4030:
•Complete machine
•fitted with the tool cutter spindle, so suitable for drilling / cutting
•this CNC machine is delivered with a CE mark
•the declaration of conformity applies to this CNC machine.
Fig 2: JCP 4030 EC CNC machine

ICP 4030 iMC-P
7/71
January
2018
2 Intended use, foreseeable misuse
isel-CNC machines / isel-CNC basic machines are CNC controlled machines with
several linear axes or an optional rotating axis. The motor output stages are
controlled via a control core either independently (CNC operation) or PC-based
CNC control (DNC operation). The complete control and power electronics for all
axes is housed behind the back wall of the machine.
Difference between a CNC machine and a CNC basic machine:
isel-CNC machine:
In the Machinery Directive 2006/42/EG legally binding since 29.12.2009, the term
“Machine“ is defined as follows (quote from MD, Article 2, Letter a):
"Machine"
•
an assembly, fitted with or intended to be fitted with a drive system other than directly applied
human or animal effort, consisting of linked parts or components, at least one of which moves,
and which are joined together for a specific application;
Every isel-CNC machine, delivered with a tool (e.g. cutter or engraving spindle,
dosing unit, sensor like CCD camera or triangulation laser, water jet nozzle, plasma
burner or equiv.), is a machine pursuant to the Machinery Directive 2006/42/EC,
because it is manufactured and to be used for a specific purpose or for a specific
application and thus use.
The use results from the type of the tool (fitted on a movable axis), for example:
Tool = machining spindle
Application for cutting, drilling
Tool = engraving spindle
Application for engraving
Tool = dispensing unit
Application for sticking, dispensing
Tool = water jet nozzle
Application for water jet cutting
etc.
As the manufacturer, isel Germany AG can carry out the statutory required risk
assessment for CNC machines. CNC machines are supplied with housing.

ICP 4030 iMC-P
8/71
January
2018
isel-CNC basic machine:
In the new Machinery Directive 2006/42/EC legally binding since 29.12.2009, the
term “partly completed machines“ is defined as follows (quote from MD, Article
2, Letter g):
“partly completed machine“
•
an assembly which is almost machinery but which cannot in itself perform a specific
application. A drive system represents a partly completed machine. Partly completed
machinery is only intended incorporated into or assembled with other machinery or other
partly completed machinery or equipment, thereby forming machinery to which this
Directive applies;
Every isel-CNC basic machine delivered without a tool and therefore not for a
specific application, is partly completed machinery pursuant to the Machinery
Directive 2006/42/EC.
•The CNC machine / CNC basic machine is designed for use in dry rooms
(workshops, labs or similar rooms) and industrial companies (maximum ambient
temperature: 40°C)
•CNC machine:
o
The CNC machine (complete machine) must be used accordingly based on the type of the
tool fitted on the machine. This means, the concrete tool of the CNC machine determines
the proper use of the machine in accordance with the Machinery Directive (Annex I, Section
1.1.2). Under this premise, the CNC machine is suitable for milling, drilling, cutting,
engraving, dosing, measuring or water jet cutting. The CNC machine is not suitable for
graphite machining.
o
Suitable processing materials are light metals, plastics, wood, glass, circuit board materials
and the like.
o
Not permitted are materials that produce harmful gases when they are processed.
o
The CNC machine is prepared for an extraction device. This extraction is preferably suitable
for dry dust (wood dust, fibreglass / fibreglass-platinum dust and similar).
•The CNC basis machine (partly completed machine) may be supplemented
by you as the buyer of the basic machine with a wide range of suitable
processing tools for the CNC machine (complete machine) in compliance with
the requirements of the Machinery Directive. You are responsible for the CE
certification if you deploy / use or sell (market) the machine. The CE certification
also contains the statutory mandatory marking of the safe machine with the CE
mark.

ICP 4030 iMC-P
9/71
January
2018
•CNC machines for milling:
o
The CNC cutting machines are designed for cutting / drilling the following materials:
Aluminium, copper, brass, plastics (e.g. GRP/fibre glass), wood
o
Processing magnesium is prohibited due to the risk of fire.
o
In the processing of steel / stainless steel only engraving works or processing with low
cutting forces is possible.
o
Cutters and drills may be used up to a maximum shaft diameter of 7 mm.
o
In the case of the tools form cutters and counter-bores for the wood sector, the cutting
diameter shall not exceed 45mm and the shank diameter shall not exceed 7mm.
•The rapid traverse rates should, depending on the system size, not exceed the
value of 150 mm / sec to a maximum of 200mm / sec.
•The feed speed of the tools in the material must be determined technologically
and should always be less than the rapid traverse rate.
•The user is responsible for the secure clamping of the tools in the tool holder.
The (reasonably) foreseeable misuse includes the operation of the CNC machine by
two persons. It is prohibited for a person in the test mode (see Section 7.1 Operating
modes) to activate the acknowledgement button on the operating panel and the
other person to reach into the working area of the machine with opened door or
perform activities of any kind therein.
There must be no tampering with the lock of the protective cover (on the back).

ICP 4030 iMC-P
10 / 71
January
2018
3 Safety notices
Read this section of the Operating Instructions carefully before connecting and
operating the machine! As with all technical systems, faultless function and
operational safety can only be guaranteed with this machine if the general safety
precautions and the special safety instructions are observed during operation.
3.1 General safety notices
1.
The machine must only be installed and commissioned by authorised personnel
with the appropriate qualifications.
2.
The machine must only be used in accordance with these instructions. The
manufacturer excludes any liability for damages arising from use of the machine for
other applications.
3.
The CNC machine may only be operated to process suitable materials using tried
and tested components. The use of non-approved materials and accessories (e.g.
cutters) may cause damage to the machine or components. In this case, the
manufacturer excludes any liability.
4.
Before starting the machine, check that mains voltage specified on the rating plate
of the individual components mains voltage matches the mains voltage available.
The wrong mains voltage can destroy the machine and its components.
5.
To prevent electric shocks, do not put any objects into the machine; an exception
to this is the proper replacement of parts in accordance with these operating
instructions.
6.
Always isolate the machine from the mains before carrying out any maintenance
work.
7.
Never operate the machine in locations where there is a risk of water or other liquids
entering the control unit behind the rear cover or the front panel controls.
8.
The floor space of the machine must be sufficiently stable; please note the
permissible floor load.
9.
The opening of the machine housing and repairs to the machine must only be
performed by authorised service technicians.
10.
Please note that there may be risk of injury from a cutter clamped in the cutting
spindle.

ICP 4030 iMC-P
11/71
January
2018
11.
The cutting machine may only be operated with original accessories, or accessories
approved by the manufacturer. When replacing parts in accordance with these
operating instructions, only original parts may be used. No liability shall be accepted
for damages caused by the use of non-approved accessories or external parts.
12.
The cutting machine must not be used potentially explosive areas.
13.
When laying the mains line, make sure there are no risks of tripping or damage to
the lines.
14.
If, without the written consent of the manufacturer, a change to the CNC machine
or its components is made, the EC declaration of conformity issued shall become
invalid.
15.
When cleaning the machine, avoid breathing in any dust created.
16.
Clean the machine only with suitable cleaning agents (standard household, non-
abrasive cleaning agents).
17.
Mobile telephones should not be used in the vicinity of the machine. Interference
with the CNC control cannot be ruled out.

ICP 4030 iMC-P
12/71
January
2018
3.2 Special safety notices
•The CNC machine is surrounded by a housing enclosing the working area or a
protective cover.
The transparent panes fixed in the machine frame or the protective cover
ensure the safety of operating personnel. The panes must not be removed. The
material of these panes is:
- PETG = Polyethylene terephthalate with glycol or
- Polycarbonate, e.g. brand name Makrolon ®
The transparent panes ensure during the operation of the machine (during set up
or processing of the component) protection against moving machine parts and
any tool or component parts ejected from the working area due to a break in the
material.
The housing reduces the noise level and holds back chips created in a chipping
process. During processing, the protective hood is locked (bolt) and cannot be
opened. This safety device (door lock, the so-called Schmersal switch) must
not be removed or changed.
A CNC machine delivered with CE marking must not be started without a
full, intact housing including undamaged PETG or polycarbonate panes.
•The drill or cutting tools used on the CNC machine with processing spindle
must, in the case of the tool holder SK11, have a maximum shaft diameter of
7 mm (standard). If you are unsure or have any queries about the choice of tool,
please contact the application technology department at isel Germany AG.
•The CNC basic machine without a housing or protective hood is a complete
machine under the Machinery Directive 2006/42/EG and is supplied without CE
marking. The declaration of incorporation and assembly instructions applies. As
the operator of the CNC basic machine, you are responsible, based on your
risk assessment, for taking appropriate protective measures to meet the
safety requirements on the machine under the Machinery Directive
2006/42/EC.
•Always make sure the components are sitting tightly. The use of a suitable, i.e. safe
component clamping device for the specific processing is the task of the operator
of the CNC machine. Unsuitable, unsafe clamping devices can if the component
comes loose from the clamping device during processing and lead to serious
accidents resulting in death or personal injury or serious damage to the component,
the tool, the clamping device and other machine parts.

ICP 4030 iMC-P
13/71
January
2018
•For emergencies, you will find an emergency stop switch at the front. This interrupts
the power supply to the power electrics (motor output stages) and the frequency
converter for the main spindle drive. The shut-down takes place according to stop
category 1 (controlled stop and subsequent interruption of the power supply to the
drives).
•Only skilled and trained persons should handle the key switch on the control
elements because in test mode there is an increased risk of injury. Keep the
spare key locked away.
•Provide adequate ventilation for dust or gas, caused by the processing of the
materials.
•If the sound pressure level on the machine exceeds the value of 70dB(A),
appropriate ear protection must be worn by the operators.
•Work on and with the machine must be carried out by authorised, trained and
instructed staff. These staff must have received special training on possible risks
(in particular residual risk).
•Before changing the tool, the machine must be switched off by operating the
emergency stop switch.
•For cooling. no running water may be used, but only a cooling device (see
accessories), in which a water mist or air causes the cooling effect. No drops
must be allowed to form and flow under the clamping plate.
•ATTENTION! High leakage current (earth leakage current, protective
conductor current)!
Before connecting to the AC supply network, it is essential to connect an
additional protective conductor (cross-section, installation and terminal point in
the control cabinet are described in section 5.5 Connection to the AC supply
network).

ICP 4030 iMC-P
14/71
January
2018
4 Setting up and connecting the CNC machine
4.1 Scope of supply
The machine is delivered fully assembled on a pallet. In the scope of delivery of
the ICP 4030, Art no.: 280270 XXX
the following are contained:
▪
Machine housing including:
othree drive axes with ball screw spindle 16 x 10mm or 4mm, 2-phase
stepper motors and two limit switches
oProtective cover with solenoid interlock
▪
Stepper motor control behind the machine rear wall included:
oMains input filter with main switch and fuses
o2-phase stepper motor output stages for 4 axes with max. 4
A rated current
oConnection board with processor (core module)
oSafety circuit module (SK module)
o48V power supply unit and 24V power supply unit
oFunction keys and emergency stop on the front of the machine
▪
Triangular key for unlocking the cover switch
▪
Mains supply line, communication line
▪
Remote as software (optional: ProNC:
▪
Operating instructions
4.2 Delivery status ex works (quality assurance)
The ball-bar measuring system QC10 Renishaw is used to demonstrate / check the
machine accuracy of the CNC machines.
This system determines the precision of the axes of all CNC machines / CNC basic
machines produced before the delivery.
Ball-bar measuring system QC10
The assembly of the QC10 is possible on each tool machine and only takes a few
minutes. The ball-bar measurement is controlled via a simple, standardised CNC
programme. The data is identified in the diagnostic software, evaluated and the faults
displayed graphically/in a table with their size and the corresponding impact on the
overall accuracy.
The form of the circuits detected (in all three interpolation levels XY/XZ/YZ)
gives indications of possible machine faults:
•Tracking errors / position tolerance
•Straightness error / square
•Dimensional error / backlash
•Quadrant transition / circular deviation

ICP 4030 iMC-P
15/71
January
2018
The measurements are done based on the size of the axes to be measured with a
radius of 50mm, 100mm, 150mm and 300mm. The shortest axis must always be taken
into consideration.
Each CNC machine will not be delivered until all parameters are within the
prescribed limits. The results of measurements are stored either as machine- or
order-related and archived.
Figure: Circularity measurement with Renishaw's QC10 circular form measuring system
4.3 Space required
The machine's space requirement is limited to the external dimensions and sufficient
space in front of the machine to be able to operate and set it up. At the back you need
about 10 cm space for the connectors. The cover of the housing opens upwards.
Figure: Dimensions and space required

ICP 4030 iMC-P
16/71
January
2018
Always keep the triangular wrench especially when transporting outside
the machine.
When you set up your CNC machine, use only suitable,
, secure clamping tools (see
chapter Accessories).
Always make sure the components are sitting tightly.
When planning the installation space for the CNC machine, all-round
access for trained personnel during a maintenance or service phase must
be taken into account!
4.4 Transporting the CNC machine
Remove the transport locks. Use only appropriate lifting devices (forklifts, trucks).
Only lift the machine from the bottom.
On subsequent transport, make sure that the mains and connection lines are not
damaged.
Remove the mains plug before any transport
When transporting the machine, make sure it is not exposed to
heavy vibrations.Always keep the triangular wrench for manually
unlocking the door outside the machine.
4.5 Setting up the CNC machine
The clamping area / processing area of the CNC machine and all axes are factory set
exactly perpendicularly.
Never loosen the fastenings of the axes or the mounting angle at
which the transverse axis is mounted (X-axis). Otherwise the
machine must be re-measured by a technician of the manufacturer
isel Germany AG.
Set the machine up on a level and
firm surface. You can compensate for
any unevenness in the floor/table with
the height-adjustable feet.
To accurately align the machine, you
need a spirit level with accuracy of at
least 0.1 mm/m. Secure the height of the
machine feet with the locknut.

ICP 4030 iMC-P
17/71
January
2018
4.6 Coordinate system and reference point
The coordinate system of the machine is defined as shown in the illustration,
whereby you can freely select (move) the component zero point P0 via the software.
The reference point of the machine (machine zero point) is set in front (Y) at the factory on the
left (X) above (Z).
Stickers on the machine indicate the axes.
4.7 Processing machine
The standard machine tool (accessory, not included in
the scope of delivery) can accept different tools with a
maximum shaft diameter of 6.35 mm in the collet (4)
(standard 3 mm, other Ø see accessories).
Use two open-end wrenches SW 22 to change the collet
chuck. The power for the processing machine is
released via the software.
The speed of the machine can be set manually with the
wheel (1).
To disassemble the machine tool, turn off the main switch of the
ICP, remove the power cable from the distributor box, loosen the
clamping screw (2) and remove the machine tool from its bracket.
To disassemble the machine with the bracket, remove the power
cable, loosen the two outer screws (3) (only loosen, do not
unscrew completely) and remove the machine with the holder
and T-slot nuts out downwards.

ICP 4030 iMC-P
18/71
January
2018
You can also mount many other tools, measuring devices (laser) or other suitable
fixtures to the T-slot plate of the Z-axis with appropriate brackets.
For the electrical connection, please use the junction box on the Z-axis.
If you want to reassemble the machine tool or other tools, you must realign the
bracket parallel to the XY plane.
The machine tool is directly wired and can be switched by the software. Also other
optional switching outputs with which you can switch additional devices (see Technical
data). The machine tool can only be switched on if the POWER button lights up, the
hood is closed and locked, the rotary switch on the machine is set to ON and the
software responds to the machine.
4.7.1 Protective cover with solenoid interlock
In the CNC-compact machines of the type ICP, the housing is
homogeneous, i.e. not removable.
The transparent glass panes fixed in the machine frame or hood (material):
polycarbonate or PETG ensure during the operation of the machine (during set up
or processing of the component) protection against moving machine parts and any
tool or parts of tools ejected from the working area.
A CNC machine delivered with CE marking must not be started
without a full, intact housing including undamaged polycarbonate
panes

ICP 4030 iMC-P
19/71
January
2018
5 Design and operation
On delivery:
▪
all operating elements are already connected to the safety circuit of the control unit.
▪
the main spindle drive is (not speed controlled 230V/500-750W or speed
controlled 750W)
▪
additional actuators or sensors are connected according to
customer requirements.
5.1 Safety notices
All work on the electrical installation must only be carried out
by authorised and trained personnel. Any changes to the
electrical installation will void the warranty and CE conformity.
When adding to the machine (e. g. working spindle, inverters,
actuators, sensors, etc.), the operator is responsible for ensuring
that all safety regulations in accordance with EN 60204-1 are
complied with.
Observe the technical data of the machine and the pin
assignments.
Table of contents
Other Isel Power Tools manuals
Popular Power Tools manuals by other brands

AP Diving
AP Diving APV300 Maintenance manual

Dremel
Dremel MOTO-TOOL 275 owner's manual
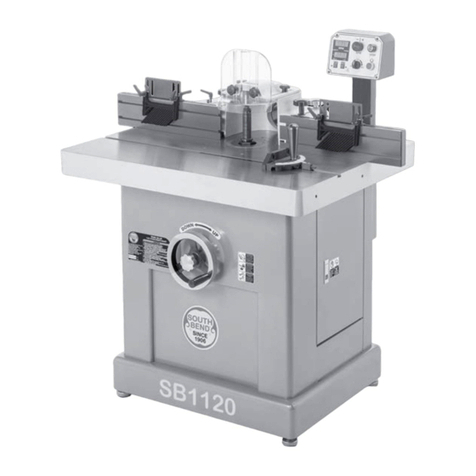
South Bend Tools
South Bend Tools SB1119 owner's manual

Omega Lift
Omega Lift MAGIC LIFT 29023 Operating instructions & parts manual
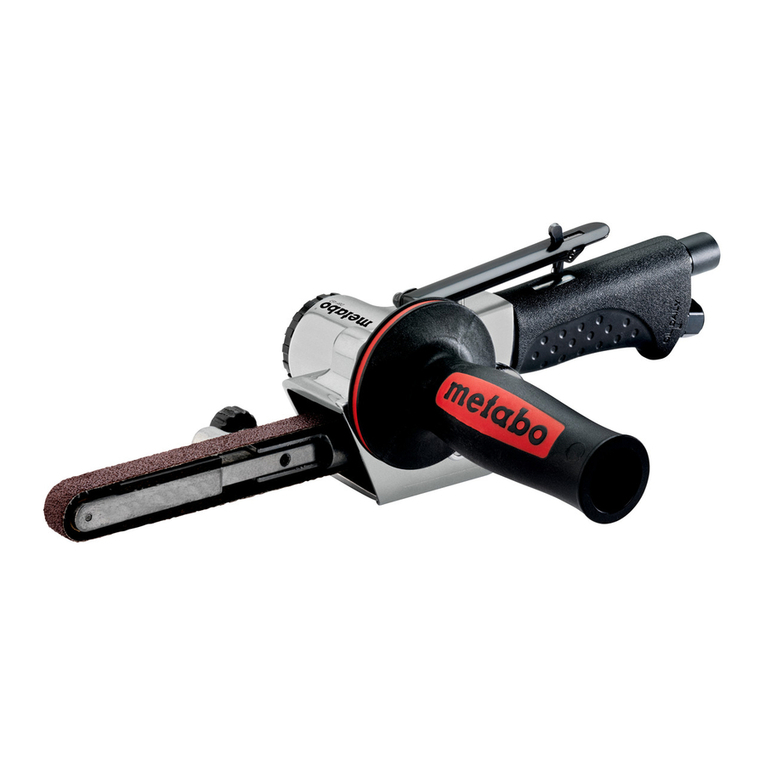
Metabo
Metabo DBF 457 Original instructions

Performax
Performax 240-3710 Operator's manual