ISOMET RFA21 0 Series User manual

July 22
Acousto-Optic Modulator Driver
Including: Basic Modulator Alignment
M1340
Instruction Manual
RFA21x0 Series
Models –
RFA2110-1-25-x, (was RFA2110) : 110MHz, > 25W output
RFA2110-1-15-x (was RFA2110-L) : 110MHz, > 15W output
RFA2120-1-25-x, (was RFA2120) : 120MHz, > 25W output
RFA2120-1-15-x (was RFA2120-L) : 120MHz, > 15W output
Options -x:
- L : active low gate
(no connection = RF disabled)
- V : 0-5V analog modulation range
- A : analog modulation only. No gate signal
- D : digital modulation only. No gate signal
- R : coolant fittings on rear face
ISOMET CORP, 10342 Battleview Parkway, Manassas, VA 20109, USA.
Tel: (703) 321 8301, Fax: (703) 321 8546, e-mail: isomet@isomet.com
www.ISOMET.com
ISOMET (UK) Ltd, 18 Llantarnam Park, Cwmbran, Torfaen, NP44 3AX, UK.
ISOMET

2
ISOMET
1. GENERAL
The RFA21x0 is a combined Analog Driver and Power Amplifier is a fixed frequency RF power source
specifically designed to operate with Isomet acousto-optic devices such as the M1340. The driver
accepts two independent control signals and provides a double-sideband amplitude modulated RF
output to the acousto-optic modulator. A summary of the driver specification is shown in the following
table:
Model Center Frequency Output Power
RFA2110-1-25 110MHz 25 Watts
RFA2120-1-15 120MHz 15 Watts
Figure 2 is a functional block diagram of the driver. The center frequency of the driver is determined
by the free-running quartz-crystal oscillator. This frequency and stability are accurate to within ±
25ppm. The oscillator is not temperature stabilized.
A high-frequency, diode ring modulator is used to amplitude-modulate the RF carrier. The single turn
potentiometer provides gain control for adjusting the peak RF power level when the modulation input
is at maximum.
A solid-state RF switch provides a high-speed gate function. A TTL equivalent high level will gate the
RF ON. The MMIC r-f pre-amplifier stage isolates the low-level modulation and control circuitry from
the power amplifier stage.
The rise and fall times for the amplifier from either the modulation or the Gate input is near identical.
Please refer to Table 1
The analog input level must not exceed 15 volts
The digital inputs must not exceed 7 volts
This amplifier is designed to operate at full rated power into a 50Ωload with 100% duty cycle.

3
ISOMET
Water cooling is mandatory. The case temperature must not exceed 50°C.
SERIOUS DAMAGE TO THE AMPLIFIER MAY RESULT IF THE TEMPERATURE EXCEEDS 70°C.
SERIOUS DAMAGE TO THE AMPLIFIER MAY ALSO RESULT IF THE RF OUTPUT CONNECTOR
IS OPERATED OPEN-CIRCUITED OR SHORT-CIRCUITED.
A low impedance DC supply is required. The operating voltage is +24V (+28Vdc MAX) at a current
drain of approximately 4A. Please refer to the model data sheet. The external power supply should
be regulated to ±2% and the power supply ripple voltage should be less than 200mV for best results.
Increased RF output power is achieved at 28Vdc.
The output power level is set by the power adjust potentiometer (PWR ADJ)
NOTE : Maximum power = fully clockwise
1.1 AO MODULATION OVERVIEW
To intensity modulate a laser beam in an acousto-optic modulator requires that the input RF carrier
voltage (power) be varied according to the video or baseband information. From the viewpoint of
intensity modulation, the deflection efficiency equation is normalized as:
i1= Sin2(kERF)
where i1 is the instantaneous intensity in the first order diffracted beam and ERF is the instantaneous
RF envelop voltage across the matched transducer.
In effect, the acousto-optic interaction demodulates the RF carrier, transforming the modulation
envelop (baseband signal) into intensity variation of the first order diffracted laser beam.
Figure 7 shows the key modulator parameters

4
ISOMET
2 LED INDICATORS
The LEDs [C] and [D] illuminate when the DC power is applied, and the Interlocks are valid.
•[A] Shows GREEN when the RF output is live PROVIDED:
a) the modulation duty cycle is more than 20% (approx).
b) the RF CW power is > 20% (approx) of the driver maximum power
•[B] Not applicable – for future options
•[C] shows RED when the DC power is applied
•[D] shows GREEN when the (thermal) Interlocks are enabled
Caution, the RF output may be live even if these LED’s are not illuminated.
LED Fault Conditions
The LEDs [C] and [D] will not illuminate if:
a) the internal driver thermal interlock switch is open (over temperature fault).
b) the AO thermal interlock switch is open (over temperature fault).
c) the AO thermal interlock is not connected to the driver interlock input.
d) the DC supply is off.
Standard over-temperature trip points
- RF driver: 50deg C
- AO device: 32deg C (Germanium) or 40degC (Quartz, Fused Silica).
The thermal interlocks will reset once the AO device and / or RF driver are cooled below the trip
temperature. The hysteresis of the thermal switches is 7-10deg C. Once in a fault state, the coolant
temperature may need to be reduced below the normal operating point to reset the thermal switches.
See AN1710 Resetting the AO Thermal Interlock (https://isomet.com/appnotes.html)

5
ISOMET
3. INSTALLATION AND ADJUSTMENT
3.1 Connect cooling water to the driver AND the AO device (e.g. M1340).
Use of a corrosion inhibitor is strongly advised.
Due to the high RF power dissipated in the AO modulators, it is paramount that the
device is operated only when water cooling is circulating.
For optimum AO performance ensure the flow rate is more than 1 litre/minute
at < 20 deg.C.
3.2 Connect the +24V (or +28V) and 0V DC supply to the feed-thru screw terminals as marked.
See figure 1. Older versions may have a solder pin for +V and screw terminal for 0V. (See
page 9). DO NOT turn on DC supply until step 3.10
3.3 Connect the RF output BNC jack to the acousto-optic modulator (or a high power 50ΩRF
load, if it is desired to measure the modulator RF output power).
3.4 Connect the Interlock of the acousto-optic modulator (SMA, SMC or ‘Binder719’ 3pin snap
connector) to the interlock inputs on the 9-pin D-type connector of the RFA. See page 8.
Connect pin 4 of ‘D’-type to INT+ and pin 5 to INT-
The interlock connection becomes open circuit disabling the RF output if the temperature
exceeds the trip point. The trip point depends on the modulator type*: Germanium 32ºC,
Quartz 40degC, or if the internal driver temperature exceeds 50ºC. An LED indicator
illuminates when the Interlocks are good (closed) and the RF is enabled (see Section 2). In
addition, a CMOS ‘interlock valid’ signal output is provided on pin 1 of the D-type connector
for remote monitoring purposes.
3.5 Adjustment of the RF output power is best done with amplifier connected to the acousto-optic
modulator. The amplifier output power is pre-set to approximately half maximum. (Refer to
the test data sheet).
The optimum RF power level required for the modulator to produce maximum first
order intensity will be different at various laser wavelengths. Applying RF power in
excess of this optimum level will cause a decrease in first order intensity (a false
indication of insufficient RF power) and make accurate Bragg alignment difficult. It is
therefore recommended that initial alignment be performed at a low RF power level.

6
ISOMET
3.6 Locate the PWR ADJ access on the driver end plate.
3.7 With an insulated alignment tool or screwdriver rotate the PWR ADJ potentiometer fully anti-
clockwise (CCW), then clockwise (CW) approx’ 1/4 turn.
3.8 Connect pin 8 of the D-type to the modulation signal source and pin 9 to the (0V) return.
Apply a constant ON modulation signal:
- Standard and Option -A models, the modulation is analog(A-mod): ON = 10V.
- For Option -D models, the modulation is digital (D-mod): ON = High = 5V.
3.9 Apply a constant TTL high level to the digital gate input on the D-type connector.
Connect pin 6 to the signal source and pin 7 to the (0V) return.
Alternatively connect to a 5V DC supply if not actively used.
(This input is not required for -A or -D variants)
3.10 Apply DC power to the driver.
Input the laser beam toward the centre of either aperture of the AOM. Ensure the polarization is
correct for the AO crystal type and the beam height does not exceed the active aperture height of the
AOM. Refer to Figures 4,5,6, and appendix-A for beam alignment.
Start with the laser beam normal to the input optical face of the AOM and very slowly rotate the AOM
(either direction).
3.11 Observe the diffracted first-order output from the acousto-optic modulator and the undeflected
zeroth order beam. Adjust the Bragg angle (rotate the modulator) to maximise first order
beam intensity.
3.12 After Bragg angle has been optimized, slowly increase the RF power (rotate PWR ADJ CW)
until maximum first order intensity is obtained.
3.13 The driver is now ready for use. Figures 3 and 4 illustrate typical modulation characteristics.
* Standard values. Check specific model test data sheet

7
ISOMET
4. MAINTENANCE
4.1 Cleaning
It is of utmost importance that the optical apertures of the deflector optical head be kept clean and
free of contamination. When the device is not in use, the apertures may be protected by a covering of
masking tape. When in use, frequently clean the apertures with a pressurized jet of filtered, dry air.
It will probably be necessary in time to wipe the coated window surfaces of atmospherically deposited
films. Although the coatings are hard and durable, care must be taken to avoid gouging of the surface
and leaving residues. It is suggested that the coatings be wiped with a soft ball of brushed (short
fibres removed) cotton, slightly moistened with clean alcohol. Before the alcohol has had time to dry
on the surface, wipe again with dry cotton in a smooth, continuous stroke. Examine the surface for
residue and, if necessary, repeat the cleaning.
4.2 Troubleshooting
No troubleshooting procedures are proposed other than a check of alignment and operating
procedure. If difficulties arise, take note of the symptoms and contact the manufacturer.
4.3 Repairs
In the event of deflector malfunction, discontinue operation and immediately contact the manufacturer
or his representative. Due to the high sensitive of tuning procedures and the possible damage which
may result, no user repairs are allowed. Evidence that an attempt has been made to open the optical
head will void the manufacturer's warranty.

8
ISOMET
Cable
3-way Binder719 Plug
1
2
3
P1
RFA 9-way D-ty pe
5
9
4
8
3
7
2
6
1
J2 1
2
J1 1
2
J1 = GATE input
5V Logic
J2 = MODULATION input
(A-mod / D-mod)
AO Thermal Interlock, Pin View
(OK = connected contacts 1-2)
Connection Summary: 9-way D-type
NC = Not Connected
SEE NOTE NEXT PAGE, minimum connections shown below:
Binder 719 connector pin assignment
*Either pin is permitted. Isolated thermostatic switch in AO.
Binder 719 3-way cable connector
(supplied)
Description
Model
Variant Signal Type
Signal
Pin
Return
Pin
Level Action
GATE
Standard 5V Logic Input 6 7
>1.7V
ON
<0.8V or NC
OFF
Option -L 5V Logic Input 6 7
<0.8V
ON
>2.5V or NC
OFF
MODULATION
Standard
Analog,
proportional
Input 8 9 10V Fully ON
Option -A
Analog,
proportional
Input 8 9 10V Fully ON
Option -V
Analog,
proportional
Input 8 9 5V Fully ON
Option -D
Digital,
5V logic
Input 8 9 >2.5V ON
ALL modulation
Input
8
9
0V
OFF
INTERLOCK All 15V Logic Input 4 5
Closed contact
ON
Open / NC
OFF
Monitor All 15V Logic Output 1 2
15V
OK
< 1V
Fault
Cable Connector
Binder719 – 3way
Driver
D-type 9way
Pin1
to
Pin5 (or Pin4*)
Pin2
to
Pin4 (or Pin5*)

9
ISOMET
PWR A DJ
+24V 0V
RF
Analog Mod'n nput
BNC
9-way male
D-type
240
230
2080 71
120
Mounting Holes (4 places)
M5 Thread
Water cooled Heatsink must not exceed 50deg C
Driver Amplifier Outline
Dimensions : mm
1" = 25.4mm
220
Underside View
CTRL
ISOMET
RF DRIVER
MODEL :
S/N :
DC Supply Input
Screw terminals
+Vdc
GND
G 1/8" Thread Water Fittings
Front placement : RFAXXX
Rear placements : RFAXXX-R
RF Output
BNC
+24Vdc
to centre pin
Note:
Unless stated, both Digital GATE and Analog Modulation signals need to be applied.
The interlock signal must be connected. Contacts closed for normal operation.
Legacy design, DC supply connection
Figure 1: Driver Installation, mounting holes: 4 x M5

10
ISOMET
+Vdc
+Vdc
Gnd
nc
En
Out
no
Vcc
o
+
BNC
RF
Output
Modulation Input
Oscillator
Pre-Amp
PA Transistor
Mixe r
Digital
(Gate) Input
PWR
Adj
Figure 2: Driver Block Diagram
Peak Level
set by driver
PWR ADJ
potentiometer
RFOutput
Power
Analog Input
Range = 0 - 10V
10V
0V
0W
Digital
Gate Input
Set W
t
ART
t
R
t
GRT
t
F
t
GFT
Figure 3: Typical RF Output Waveforms: Standard and Option -A models
The RF output waveform is a combination of the Modulation and Gate control inputs as illustrated
above. Analog modulation shown.

11
ISOMET
Description
Variant
Standard
-A
-D
tR
RF rise time resulting from large signal
modulation.
<150 ns <150 ns <150 ns
tF
RF fall time resulting from large signal
modulation.
<50 ns <50 ns <50 ns
tART
Latency delay between a change in
modulation level (A-Mod or D-mod) and RF
output.
60 ns 60 ns 60 ns
tGRT
Latency delay between a Gate High input
and RF output fully enabled.
200 ns NA NA
tGFT
Latency delay between a Gate Low input
and RF output fully disabled.
100 ns NA NA
Table 1: Timing spec’s:
Time
Analog
Modulation
Input
(0 - 10V)
AM Modulated
RF Output
Zero Order
Control Range
Max Laser O/P
0 W
Ton
Vmod
Minimum
(not 0)
Maximum
Maximum
(= Laser O/P)
First Order
Control Range
0 W
Minimum
FIRST ORDER
ZERO ORDER
RF
tgm
GATE
DRIVER INPUTS
POT Set Level
Figure 4: Illustration of Laser Beam Modulation and RF driver controls

12
ISOMET
1st
0th
Input
Orientation options
Input
Input
Input
1st
1st
1st
0th
0th
0th
Modulation Input
+
RF Gate Input
RF INT
First Order (-1)
Diffracted Beam
Zero Order
Input Laser Beam
AOM
RFA21x0
Separation
Angle
Coolant circuit not shown for clarity.
Flow rate > 1 liter / min at less than 20deg C
DC supply : 24Vdc / 4A
2
13
AO Interlock Connector 'INT' (Pin view)
Normally Closed Contacts : Pins 1 , 2
Not connected : Pin 3
Bragg
Angle
(-2)
(+1)
Figure 5: Typical Connection Configuration
Figure 6: Possible Input Bragg Angle Orientations

13
ISOMET
Basic AO Modulator Parameters
Driver
RF
Intensity
Modulation
Input Laser Beam
1st Order Deflected Beam
0th Order
θ
θ
BRAGG
SEP
The input Bragg angle, relative to a normal to the optical surface and in the plane of deflection is:
θ BRAGG = λ.fc
2.v
The separation angle between the Zeroth order and the First order is:
θ SEP = λ.fc
v
Optical rise time for a Gaussian input beam is approximately:
tr = 0.65.d
v
where: λ = wavelength
fc = centre frequency
v = acoustic velocity of interaction material = 5.7mm/usec (Quartz)
= 5.96mm/usec (Fused Silica)
d = 1/e2beam diameter
Figure 7. Modulation System

14
ISOMET
RF
Pulse
AO crystal
Acoustic Wave
Active
Aperture
Height
Laser Beam
Active Aperture
Centre Line
H mm
X mm
d mm
Absorber
Bragg Pivot Point
Transducer
(V)
Y mm
B
A
Appendix A: Beam Position
Timing Considerations for AO Devices in Pulsed Lasers Applications
When attempting to synchronize a pulsed laser beam with a pulsed RF acoustic wave in an AO
device, the designer must consider the transit time of the acoustic wave from the transducer to the
laser beam position. This is called the Pedestal delay.
Input Beam Location
Vertical axis: Place the laser beam at the centre of the active aperture at Y mm above the base.
Horizontal (Diffraction) axis: Place beam above the Bragg pivot point.
Timing considerations with respect to the RF modulation signal
An acousto-optic device is characterized by a travelling acoustic wave. This wave is launched from
the RF excited transducer and travels at velocity V across the laser beam and into the absorber.
It is important to consider this transit period when synchronizing a pulsed laser output with a pulsed
AOM/AOD driver signal.
Early/later refers to the laser trigger
timing relative to the RF driver
modulation signal

15
ISOMET
RF Driver input
modulation signal
RF Signal at AO
transducer
Acoustic Signal
at laser beam
position
Pedestal Delay Tp
A
B
Laser Beam, diameter d
Acoustic velocity, V mm/usec
Pedestal delay
The time taken for the acoustic wavefront to reach the laser beam centre (2).
Tp = beam position from transducer (X)
acoustic velocity (V)
Transit time
The time taken for the acoustic wavefront to cross the entire laser beam diameter.
where: Tt = beam diameter (d)
acoustic velocity (V)
This equates to the minimum RF pulse width.
Optical rise / fall switching time
For a Gaussian beam is approximately Tr = 0.65 x Tt
Total Sync Time
This represents the total delay time between the electronic modulation signal and the corresponding
acoustic signal at the laser beam centred over the Bragg Pivot Point. This is given by :
Tst= Pedestal delay + ½ pulse width duration
The minimum RF pulse width duration will depend on the beam diameter. See ‘Transit Time’
In the limiting case, pulse width duration = transit time.
Laser sync output
Please be aware, there may be an additional delay between the laser input trigger signal and the laser
output pulse. This delay should also be considered when synchronizing.
This manual suits for next models
6
Table of contents
Other ISOMET DC Drive manuals
Popular DC Drive manuals by other brands
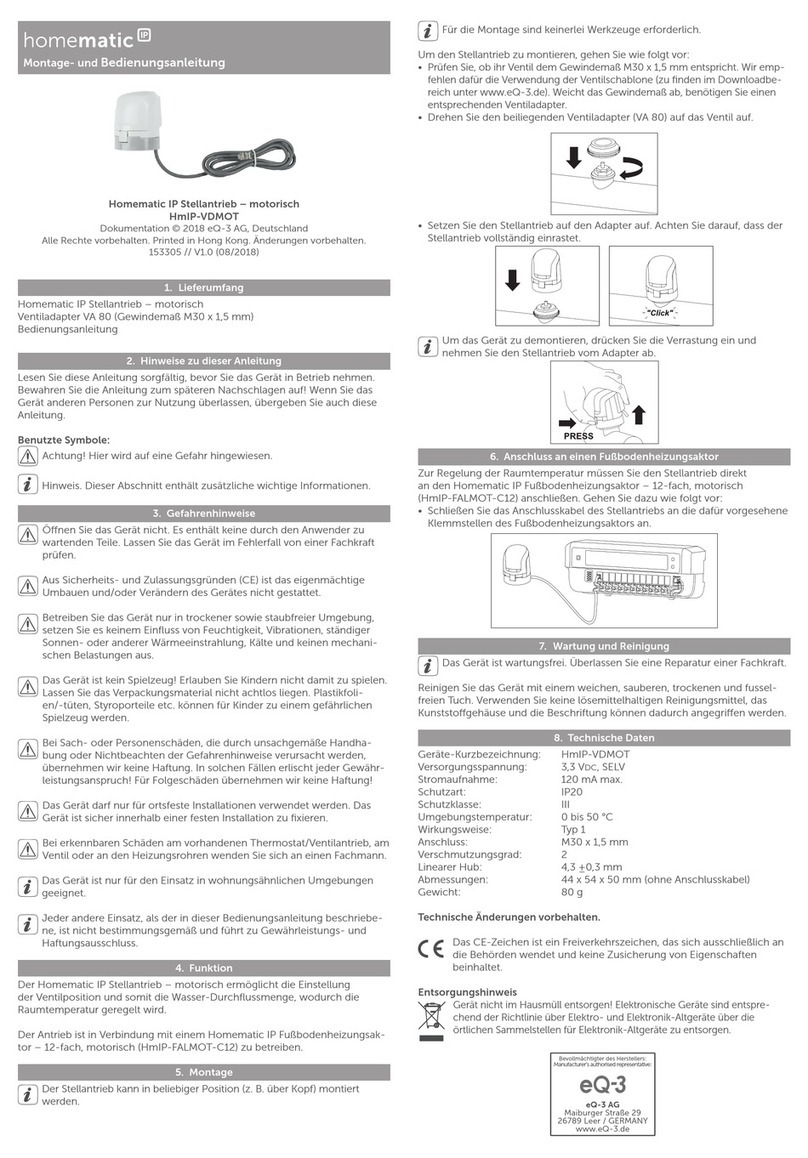
Homematic IP
Homematic IP HmIP-VDMOT Installation and operating manual
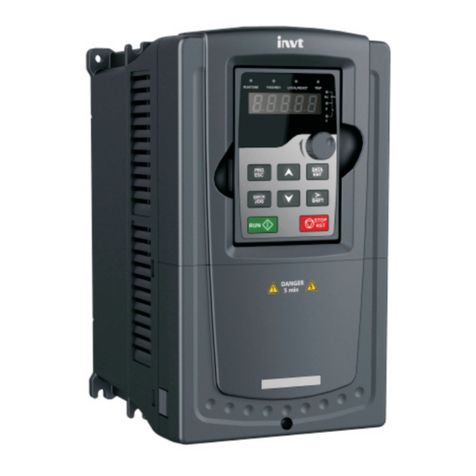
INVT
INVT Goodrive300 Series Operation manual
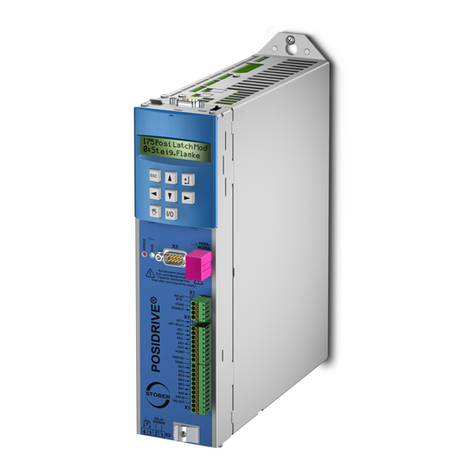
Stober
Stober POSIDRIVE MDS 5000 Operation manual
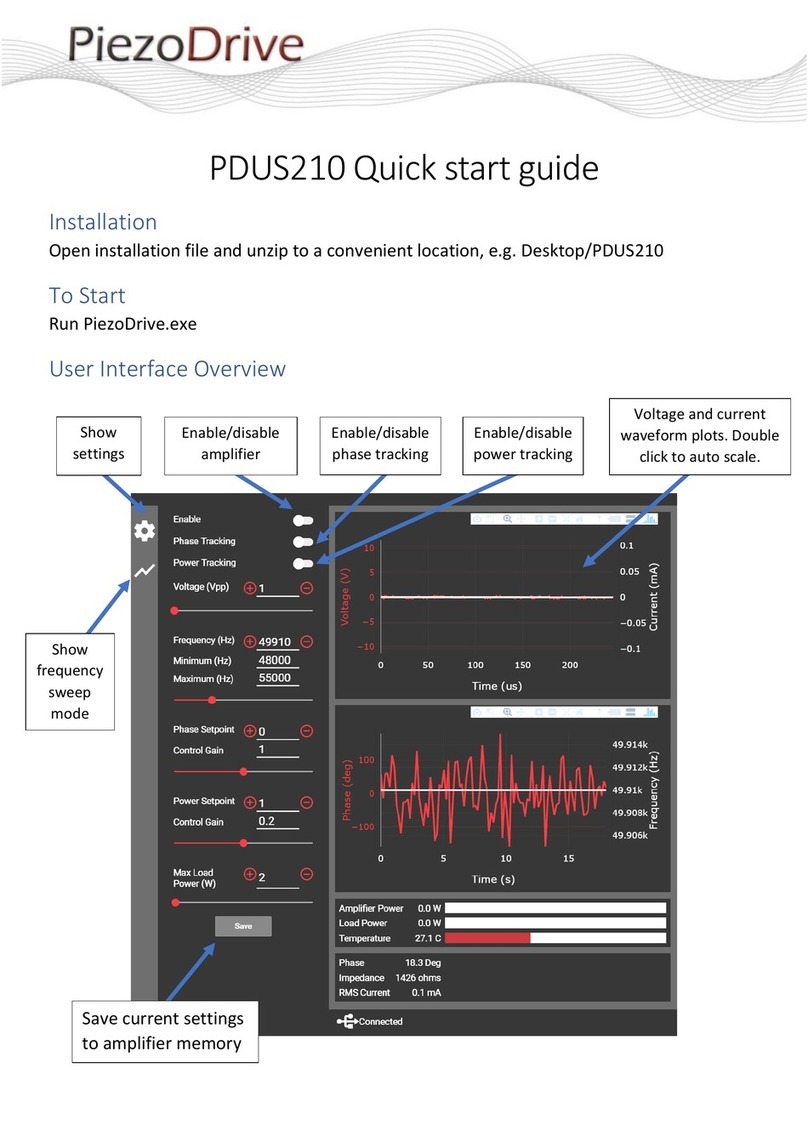
PiezoDrive
PiezoDrive PDUS210 quick start guide
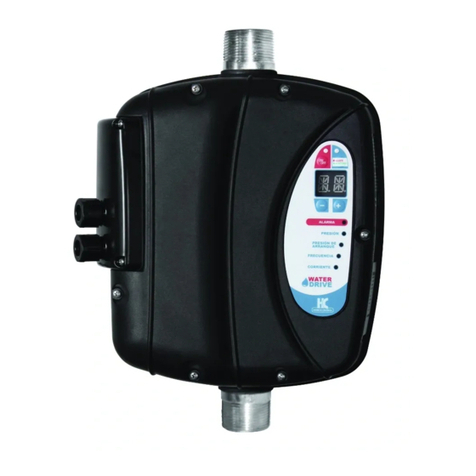
HIDROCONTROL
HIDROCONTROL WATER DRIVE W-Drive2M2M/08 user manual
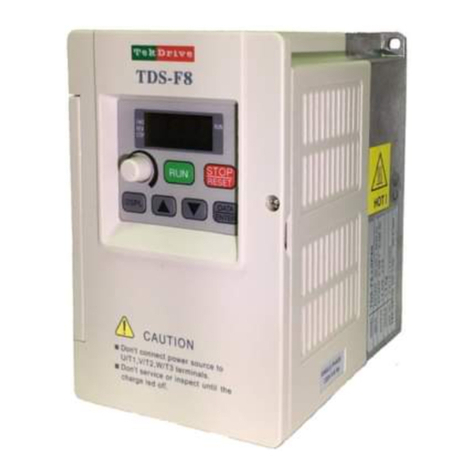
Tek Drive
Tek Drive TDS-F8 instruction manual