ISOMET RFA741 Series User manual

Jan 18
Acousto-Optic Modulator Driver
Including: Modulator Alignment
AOM740-H
Instruction Manual
RFA741 Series
Digital Modulation, Dual Frequency
Remote Power Level Control
Models -
RFA741 : 40MHz / 50.7MHz, 180W output
Options –xxx, combinations possible.
- BR : Brass water cooled heatsink
ISOMET CORP, 5263 Port Royal Rd, Springfield, VA 22151, USA.
Tel: (703) 321 8301, Fax: (703) 321 8546, e-mail: isomet@isomet.com
www.ISOMET.com
ISOMET (UK) Ltd, 18 Llantarnam Park, Cwmbran, Torfaen, NP44 3AX, UK.
Tel: +44 1633-872721, Fax: +44 1633 874678, e-mail: isomet@isomet.co.uk
ISOMET

2
ISOMET
1. GENERAL
Key Features:
•24Vdc, water cooled high power amplifier
•RF output >150W at 40.00MHz, and >150W at 50.67MHz
•RF rise/fall time < 400/100nsec at 150W
•High Speed Digital ON:OFF modulation
•Modulation ON level is defined by two methods for each frequency
- Digitally programmed potentiometer stack
- Manual adjustment potentiometer.
•Digital potentiometers programmed via buffered I2C interface
•Opto-isolated PLC compatible inputs on POT select and RF enable inputs.
(Response time < 1msec)
•Tri colour LED status indicator
•High VSWR shut-down protection
The RFA741 Combined Driver and Power Amplifier is a fixed dual frequency RF power source
specifically designed to operate with the AOM740- series of acousto-optic high power modulators
A block diagram of the driver is shown in Figure 3. The center frequencies are determined by free-
running quartz-crystal oscillator. The frequency is accurate to within ±25ppm and the stability is
better than ±25ppm. A high-frequency, diode ring modulator provides high speed amplitude
modulation of the RF carrier. The peak RF power level for each frequency is set by a multi-turn
manual potentiometer or by digitally controlled potentiometers.
The prime frequency of 40MHz provides the active “ON” laser output beam. The dummy frequency of
50.67MHz is applied in the “OFF” condition and is used to provide a constant thermal load to the
AOM.

3
ISOMET
2, CONTROL
Two inputs directly control the RF output;Gate and Freq Modulation.
The Gate response time (tgm, fig1) is approximately 1msec
The RF Frequency Modulation response time is < 50nsec
The relationship between the driver control inputs, the RF waveform and AO response is shown
below.
Time
FREQ
MODULATION
Input
FREQ
Modulated
RF Output
Zero Order
Max Laser O/P
0 W
Ton
Minimum
(not 0)
Maximum
Maximum
(= Laser O/P)
First Order
Control Range
0 W
Minimum
50MHz "Dummy" FIRST ORDER
ZERO ORDER
RF
tgm
GATE
TTL High
Low
POT Set Level
RF OUTPUT
AOM OUTPUTS (Bragg adjusted for 40MHz)
DRIVER INPUTS
40MHz "Active" FIRST ORDER
40MHz "Active" 50MHz "Dummy"
Figure 1: Typical Digital Modulation Waveforms

4
ISOMET
Gate (active high enables the RF amplifier)
PLC compatible opto-isolated input
Default condition is RF Off.
A high level (5V < V < 24V) will gate the RF ON.
A low level (0V < V < 4V), or not connected will gate the RF OFF.
Digital Modulation (active high )
Provides high speed frequency selection of the RF output.
A TTL high level will select 40.00MHz ( Main 1st order beam “ON”) .
A TTL low level will select 50.67MHz (Main 1st order beam “OFF”) .
The amplitude level for either frequency is defined by the selected RF power adjustment POT.
RF Power Adjustment (POT set level)
The maximum RF power limit is set by one of two methods. The method is selectable by the user.
a) A manual adjust multi-turn potentiometer ‘PWR ADJ’ for each frequency.
Maximum RF power = fully clockwise
or
b) A quad 256 step digital potentiometer configured to give independent power control for 40
and 51.7MHz levels with common variable end limits
All 4 channels are used for power level control. RDAC0, RDAC1, RDAC2 and RDAC3
(see AD5254 data sheet). Levels are set remotely via an I2C compatible serial connection.
The slave address for the digital I2C potentiometer is at 0101100.(AD0 = AD1 = 0)
DC Power
A low impedance DC power supply is required. The operating voltage is +24Vdc only at a current
drain of approximately < 18A. The external power source should be regulated to ±2% and the power
supply ripple voltage should be less than 200mV for best results. Higher RF output power is achieved
at 28Vdc.

5
ISOMET
2.1 Thermal Interlocks
The AOM and Driver are fitted with thermostatic switches which will switch open circuit if a
predetermined temperature is exceeded. These thermal interlocks will reset once the AO device and /
or RF driver are cooled below this temperature.
- The driver thermal switch over-temperature threshold is 50deg C
- The AOM740-H series thermal switch over-temperature threshold is 32deg C
The hysterisis of the thermal switches is 7-10deg C.
Once in a fault state the coolant temperature may need to be reduced to reset the thermal switches.
Precautions
TTL digital input levels must not exceed 7 volts
PLC logic input levels must not exceed 24 volts
Water cooling is mandatory.
The heatsink temperature must not exceed 70°C.
Corrosion inhibitor should be added to the cooling water
SERIOUS DAMAGE TO THE AMPLIFIER MAY RESULT IF THE TEMPERATURE EXCEEDS 70°C.
SERIOUS DAMAGE TO THE AMPLIFIER MAY ALSO RESULT IF THE RF OUTPUT CONNECTOR
IS OPERATED OPEN-CIRCUITED OR SHORT-CIRCUITED.

6
ISOMET
2.2 LED Indicator and Monitor outputs
The front panel tri-colour LED indicates the operating state.
(RF PWR ADJ) 51MHz 40MHz LED
RED
The top LED will illuminate RED when there is a poor VSWR load (High reflected RF power fault).
Normal condition is OFF
A fault signal is triggered when the reflected RF power exceeds approximately 50% of the average
forward power for more than 1 second. This fault is latching and the driver is disabled (RF power will
go to zero). This fault can occur if the RF connection between the AOM and driver is broken.
Resetting
Once the fault condition is corrected, it will be necessary to reset the driver.
1) Turn the DC power OFF and ON
or
2) Press momentary RESET button on driver located to right to the D-type
YELLOW
The middle LED will illuminate YELLOW, when the RF outputs are live and provided that
a) the Gate duty cycle is more than 20% (approx).
b) the RF average power is > 30W (approx)
Normal condition is ON, but may be OFF if the above conditions are not met
GREEN
The lower LED will illuminate GREEN when the following signal are all true:
1) RF DC power is applied and
2) Interlocks are valid and
3) GATE input is high.
Normal condition is ON

7
ISOMET
LEDS Off
The GREEN and/or YELLOW LED’s will not illuminate if :
a) the internal driver thermal interlock switch is open (Over temperature fault)
b) the AOM thermal interlocks switch is open (Over temperature fault)
c) the AOM thermal interlock is not connected to the driver interlock input
d) the DC supply is off.
The RED LED should be OFF
Monitor Outputs
The status of the YELLOW and GREEN LEDS is available at the D-type connector
These outputs are opto-isolated .
+12V
+5V
+5V
15 way D-Type
8
15
7
14
6
13
5
12
4
11
3
10
2
9
1
3 1
2
560
YELLOW GREEN
-Interlock
INT
Rtn-
Control
Connector
EN Imon+
Interlock
Connector
RF mon+
MONITOR OUTPUTS
Rmon
Imon
“Enabled” = low impedance between pins 2 and 10 = Green LED ON
“RF Active” = low impedance between pins 3 and 10 = Yellow LED ON

8
ISOMET
3. INSTALLATION AND ADJUSTMENT
The basic set-up below is described using the manual RF power limit adjustment.
The remote power adjustment is described from 3.15 onwards. The driver will default to
manual adjustment unless the remote power adjustment is selected,
3.1 Connect cooling water to the RFA741 at a minimum flow of 2.0 litres/minute at < 20 deg.C.
Refer to Figure 2. Use of a Corrosion inhibitor is strongly advised.
Connect cooling water to the AO device.
Due to the high RF power dissipated in the AO modulator, it is paramount that the device is
operated only when water cooling is circulating.
For optimum AO performance ensure the flow rate is more than 2 litres/minute at < 20 deg.C
3.2 With no DC power applied, connect the + 24V DC in to the screw terminals of the filtered
terminal. DO NOT APPLY POWER.
3.2 Connect the TNC output RF connector to the acousto-optic modulator TNC RF input.
(or a 50ΩRF load, if it is desired to measure the RF output power).
3.4 Connect the Interlock of the acousto-optic modulator (mini 3-pin snap connector) to the RF
driver “INT” input (mini 3-pin snap connector).Connect pin 1 to pin 1 and pin 2to pin 2.
If the temperature of the modulator exceeds 32ºC or the internal driver temperature exceeds
50ºC then the interlock connection becomes open circuit, disabling the RF output. An LED
indicator illuminates when the Interlocks are closed and the RF is enabled. In addition, a open
drain ‘interlock valid’ signal output is provided on pin 2 of the D-type connector for remote
monitoring purposes.
3.5 Adjustment of the RF output power is best done with amplifier connected to the acousto-optic
modulator. When shipped, the Amplifier maximum output power is set to approx 100W
selecting the manual PWR ADJ pot and 120W for the digital pots.
The optimum RF power level required for the modulator to produce maximum first order
intensity depends on the laser wavelength and AOM aperture height. This value is called
“Psat”. Applying RF power in excess of this optimum level will cause a decrease in first
order intensity, increase thermal dissipation and make accurate Bragg alignment
difficult. It is therefore recommended that initial alignment be performed at a low RF power
level.

9
ISOMET
A typical relationship between RF drive and efficiency for a correctly aligned AOM740-H at
10.6um is illustrated below.
10%
20%
30%
40%
50%
60%
70%
80%
90%
100%
010 20 30 40 50 60 70 80 90 100 110 120 130 140 150 160
RF Pow er (W)
Efficiency
3.6 Locate the PWR ADJ access holes on the driver end plate.
The 40MHz RF Power adjuster is closest to the LED stack
3.7 With an insulated alignment tool or screwdriver rotate both PWR ADJ potentiometers fully
anti-clockwise (CCW) i.e. OFF, then clockwise (CW) approx 5 turns.
3.8 Apply DC to the amplifier.
3.9 Apply a constant TTL high signal to the Freq Modulation input on the D-type connector of the
RFA741. Connect pin 7 of ‘D’ to the TTL signal and pin 14 of ‘D’ to the signal return (0V).
3.10 Apply a constant PLC high level (typically 12V or 24V) to the digital gate input on the D-type
connector. Connect pin 8 of the ‘D’ to the Signal and pin 15 of the ‘D’ to the signal return.
3.11 Apply a constant PLC low level (less than 2V) to the POT SELECT input (S0) on the D-type.
Connect pin 1 of the ‘D’ to the Signal and pin 9 of the ‘D’ to the signal return.
A low level will enable power adjustment using the Manual pots.

10
ISOMET
Input the laser beam toward the centre of either aperture of the AOM. Ensure the polarization is
horizontal with respect to the base and the beam height does not exceed the active aperture height of
the AOM. Start with the laser beam normal to the input optical face of the AOM and very slowly rotate
the AOM (either direction). See Figure 4 for one possible configuration.
RF
AO crystal
Acoustic Wave
Active Aperture H
Laser Beam
Cover Aperture
Y
X
Input Beam Location
Y axis : Centre beam in active aperture height H
X axis : Not critical but avoid clipping device cover
3.12 Observe the diffracted first-order output from the acousto-optic modulator and the undeflected
zeroth order beam. Adjust the Bragg angle (rotate the modulator) to maximise first order
beam intensity with the 40MHz Frequency selected.
3.13 After Bragg angle has been optimized, slowly increase the RF power by turning PWR ADJ
clockwise until maximum first order intensity is obtained.
3.14 The modulator and driver are now ready for use.
When the 50.67MHz is selected, the 40MHz beam will be OFF. A significant proportion of the
laser beam will now be diffracted into the 50,67MHz beam location. This will be further from
the zero order beam
3.15 Remote RF Power Adjust
The RF power can be adjusted remotely using an I2C compatible interface. The control circuit
is based on the Analog Devices non-volatile 256 step digital potentiometer AD5254.
The accompanying data sheet describes the communication protocol.

11
ISOMET
The slave address for the digital I2C potentiometer is at 0101100. (AD0 = AD1 = 0)
Maximum resistance equates to maximum RF power.
The digital potentiometer value is non-volatile and will recall the last saved value on power-
up.
5V
+5V
24V
10T Pot (40MHz)
1
3
2
10k
560
R39
470
P82B715TD
1
2
67
8
4
3
5nc1
Lx
SyLy
Vcc
Gnd
Sx
nc
560
R38
470
47k
AD5254 BRU10
5
8
43
2
7
6
10
11
12
13
14
16
17
9
20
15
1
18
19
-WP
A1
AD0 A0
B0
B1
W1
Vss
A2
B2
W2
SCL
AD1
A3
SDA
Vdd
GNDd
W0
B3
W3
10T Pot (50MHz)
1
3
2
1213
1
14
2
4
5
11
10 6
7
8
9
3
VddGnd
A0
A1
enS1
S2
S3
S4 D
nc
nc1
nc2
Vss
15 way D-Type
8
15
7
14
6
13
5
12
4
11
3
10
2
9
1
560
10k
560
-
+
6
74
3
2
R_W-B = D/256
S0
LCL
GND
Control
Connector
(Inverts)
I2C Buffer
LDA
S0
POT SELECT
INPUT RF Level
Freq MOD
NC
S1
40MHz 50MHz
DO NOT exceed +5V on the I2C Inputs, LDA (data IO) and LCL (clock)
The I2C signals are buffered using the bus extender chip P82B715 from NXP
To enable remote RF power control, connect pin 1 (S0) of the 15way D-type control driver connector
to a PLC compatible logic port and apply a high signal.

12
ISOMET
5V
W0
13
2
W3
13
2
47k
W1
13
2
W2
13
2
RDAC3 = 255
W3 = 10Kohm
RDAC0 = 255
W0 = 0 ohm
RDAC2 = 0 - 255
V50_Control = 50,67MHz Pow er
RDAC1 = 0 - 255
V40_Control = 40.0MHz Power
VH
VL
The four digital pots are configured into a potential divider.
The main power control pots W1 and W2 are in parallel and equate to 5Kohm resistance.
The upper and lower limit adjustment Pots W3 and W0 apply to both 40MHz and 50MHz powers.
AD5254 configuration
RDAC2 defines the 50 MHz power control factor
V50_Control VL + (VH-VL) x W2/255
where W2= 8-bit value programmed into RDAC2
RDAC1 defines the 40 MHz power control factor
V40_Control = VL + (VH-VL) x W1/255
where W1= 8-bit value programmed into RDAC1
RDAC0 defines the lower limit pot
Lower pot resistance R_W0 = (255-W0)/255 x 10Kohm
Lower limit voltage VL = (R_W0) / (47K+R_W3+5K+R_W0)
RDAC3 defines the upper limit pot
Upper pot resistance R_W3 = (W3)/255 x 10Kohm
Upper limit voltage VH = (R_W0+5K) / (47K+R_W3+5K+R_W0)

13
ISOMET
The full range power adjustment is shown below.
Settings: RDAC3 = 0 (R_W3=0k) and RDAC0 = 255 (R_W0=0k).
The V_Control scale equates to 0 – 255 adjustment range on RDAC1 (W1) or RDAC2 (W2)
Digital Pot RF Control
0
10
20
30
40
50
60
70
80
90
100
110
120
130
140
150
160
170
0.0 0.1 0.2 0.3 0.4 0.5 0.6 0.7 0.8 0.9 1.0
V_Control (Volts)
RF Power W
By adjusting the values of RDAC0 and RDAC3 it is possible to increase the adjustment resolution of
the 8-bit power level control at 40.0 MHz (RDAC1) and 50.7MHz.(RDAC2) over a defined range.
A typical Digital Power curve is shown below. In this case settings are: RDAC3 = 255 (R_W3=10k)
and RDAC0 =t 200 (R_W0=2K)
Digital Pot RFControl
20
30
40
50
60
70
80
90
100
110
120
016 32 48 64 80 96 112 128 144 160 176 192 208 224 240 256
Digital Value (dec)
RF Power W

14
ISOMET
4. MAINTENANCE
4.1 Cleaning
It is of utmost importance that the optical apertures of the deflector optical head be kept clean and
free of contamination. When the device is not in use, the apertures may be protected by a covering of
masking tape. When in use, frequently clean the apertures with a pressurized jet of filtered, dry air.
It will probably be necessary in time to wipe the coated window surfaces of atmospherically deposited
films. Although the coatings are hard and durable, care must be taken to avoid gouging of the surface
and leaving residues. It is suggested that the coatings be wiped with a soft ball of brushed (short
fibres removed) cotton, slightly moistened with clean alcohol. Before the alcohol has had time to dry
on the surface, wipe again with dry cotton in a smooth, continuous stroke. Examine the surface for
residue and, if necessary, repeat the cleaning.
4.2 Troubleshooting
No troubleshooting procedures are proposed other than a check of alignment and operating
procedure. If difficulties arise, take note of the symptoms and contact the manufacturer.
4.3 Repairs
In the event of deflector malfunction, discontinue operation and immediately contact the manufacturer
or his representative. Due to the high sensitive of tuning procedures and the possible damage which
may result, no user repairs are allowed. Evidence that an attempt has been made to open the optical
head will void the manufacturer's warranty.

15
ISOMET
RFA741 Connection Summary
1.0 15 way ‘D’ Type Control Connection
Signal (see notes) Type Pin out connection
NECESSARY
Digital Gate (slow)** Input Signal pin 8
PLC high (5v<V<24v) = ON Return pin 15
PLC low (0.0v<V<4v) or NC = OFF
Frequency Modulation (fast)* Input Signal pin 7
TTL high (2.7v<V<6.0v) = 40.0MHz Return pin 14
TTL low (0.0v<V<0.8v) = 50.67MHz
Interlock *** Input Connect to AOM “INT”
Normally closed
OPTIONAL
‘Enabled’ monitor Output Signal pin 2
(Open collector logic, Low = OK) Return pin 10
Maximum applied voltage
(via external pull up resistor) = 24V
Maximum current = 20mA
‘RF Status’ monitor Output Signal pin 3
(Open collector logic, Low = OK) Return pin 10
Maximum applied voltage
(via external pull up resistor) = 24V
Maximum current = 20mA
I2C Clock Input Signal pin 5
(0.0v<V<5.0v) Return pin 13
I2C Data IO In/Out Signal pin 6
(0.0v<V<5.0v) Return pin 13
POT Select Control, S0 Input Signal pin 1
PLC high (5v<V<24v) = Digital Pot Return pin 9
PLC low (0.0v<V<4v) or NC = Manual Adjust

16
ISOMET
RF Out INT
RF Output
TNC 15-way male
D-type
G1/8" Thread with
Legris Push-in Water Fittings
LF3101-08-10
240
5230
2080 71
120
Mounting Holes (4 places)
M5 Thread Water cooled Heatsink
Must not exceed 50deg C
Use Corrosion Inhibitor in coolant
Driver Amplifier Outline
Dimensions : mm
1" = 25.4mm
220
Underside View
PWR
ADJ
+24V 0V
CTRL
RF DRIVER
MODEL :
S/N :
ISOMET
INTERLOCK Input
Binder 719 Series
Male Socket
50.6MHz 40.0MHz
RF PWR ADJ POT
Modulation and Gate Input connections
31
2
J1 1
2
15way
8
15
7
14
6
13
5
12
4
11
3
10
2
9
1
J2
1
2
31
2
AOMThermal Interlock Plug
(OK = connected contacts 1-2)
J2 = FREQ MODinput
TTL compatible
Logic HIGH (3V < V < 5V) = 40.0 MHz
Logic LOW (0V < V < 2V) = 50.67MHz
J1 = GATEinput
PLCcompatible
Logic HIGH (5V < V < 24V) = ON
Logic LOW (0V < V < 4V) = OFF
RF Driver INT Plug
(OK = connected contacts 1-2)
RF Driver D-Type
Notes:
*** The interlock signal must be connected. Contacts closed for normal operation.
2.0 Mounting Holes
4 x M5
Figure 2: Driver Installation

17
ISOMET
+Vcc
+24Vdc
+Vcc
+Vset
+
o
Gnd
En
Out
Vcc
13
2
1 3
2
Gnd
En
Out
Vcc
PWR
Adj
Mixer
Oscillator
S0 = 1 =Dig Pot
S0 = 0 =Man Adj
Pot
Select
FREQ
Modulation
Input
PATransistor
4 Channel Digital Pot
RF
Output
RF
SET
Pre-Amp
I2C
GATE
Input
PWR
Adj
Oscillator
Osc
Select
Figure 3: Driver Block Diagram

18
ISOMET
Modulation,
Gate,
I2C,
Pot Select Inputs
RF INT
First Order (-1)
Zero Order
Input Laser Beam
AOM740-H series
RFA741
Separation
Angle
Separation Angles at : 9.4 / 10.6um
40MHz main beam :68.4 / 77 mrad
51MHz dummy beam :86.5 / 97 mrad
Coolant circuit not shown for clarity.
Flow rate >2 liter / min at less than 20deg C
DC supply : 24Vdc / < 14A
1
23
Interlock Connector
Normally Closed Contacts : Pins 1 , 2
Not connected : Pin 3
Bragg Angle at 40MHz
9.4um = 34.2mrad
10.6um = 38.5mrad
Bragg
Angle
(-2)
(+1)
Main Beam
Dummy Beam
First Order (+1)
Zero Order
Input Laser Beam
AOM740-H series
Separation
Angle
Bragg
Angle
(+1)
Dummy Beam
Main Beam
+(2)
(-1)
(or)
Either optical face can be used for input.
Thus with reference to the above diagram, the input laser beam can also be from the right to left.
Figure 4: Typical Configurations using RFA741 series.
.

19
ISOMET
Basic AO Modulator Parameters
Driver
RF
Intensity
Modulation
Input Laser Beam
1st Order Deflected Beam
0th Order
θ
θ
BRAGG
SEP
The input Bragg angle, relative to a normal to the optical surface and in the plane of deflection is:
θ BRAGG = λ.fc
2.v
The separation angle between the Zeroth order and the First order is:
θ SEP = λ.fc
v
Optical rise time for a Gaussian input beam is approximately:
tr = 0.65.d
v
where: λ = wavelength
fc = centre frequency = 40MHz / 50.67MHz
v = acoustic velocity of interaction material = 5.5mm/usec (Ge)
d = 1/e2beam diameter
Figure 5. Modulation System
Table of contents
Other ISOMET DC Drive manuals
Popular DC Drive manuals by other brands
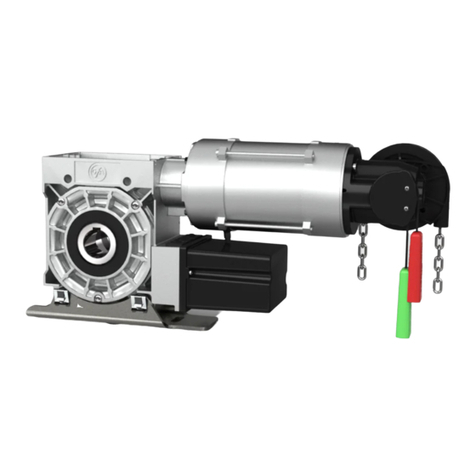
GFA
GFA ELEKTROMAT SI 40.10-40,00 installation instructions

Rockwell Automation
Rockwell Automation RELIANCE ELECTRIC DC3N Series user guide
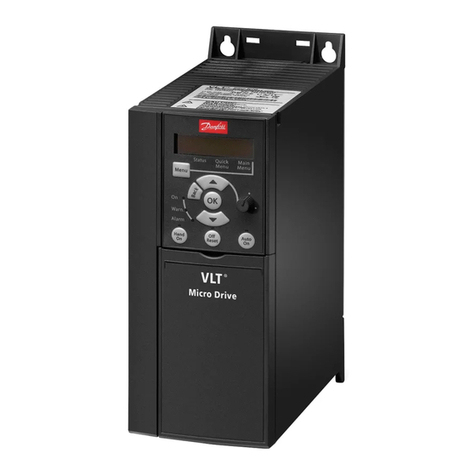
Danfoss
Danfoss VLT Micro Drive FC 51 Series Design guide
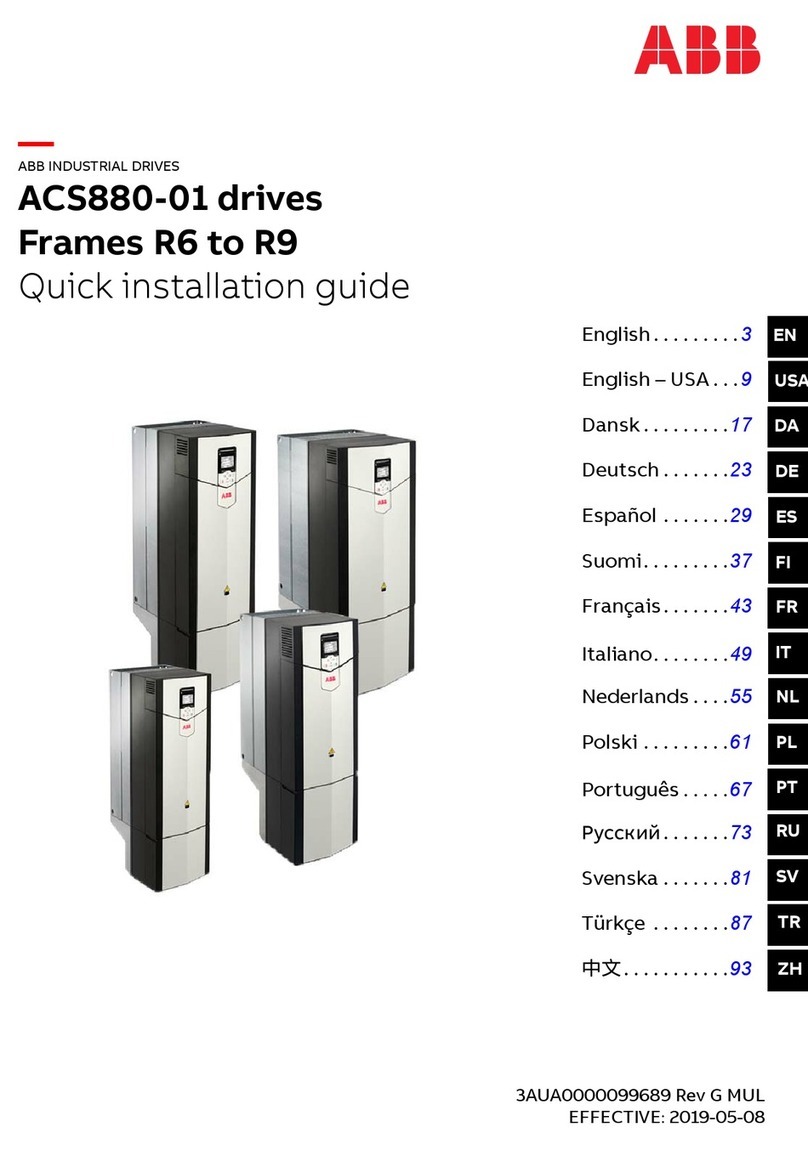
ABB
ABB ACS880-01 Series Quick installation guide
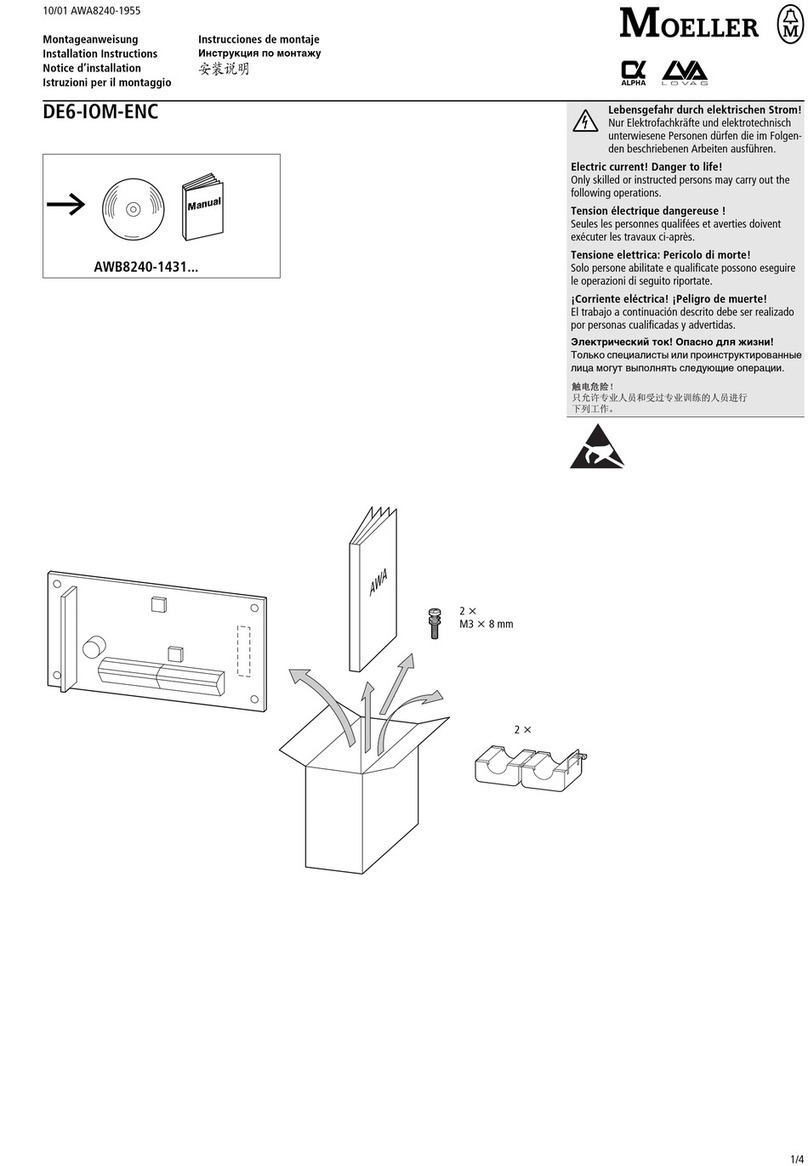
Moeller
Moeller DE6-IOM-ENC installation instructions
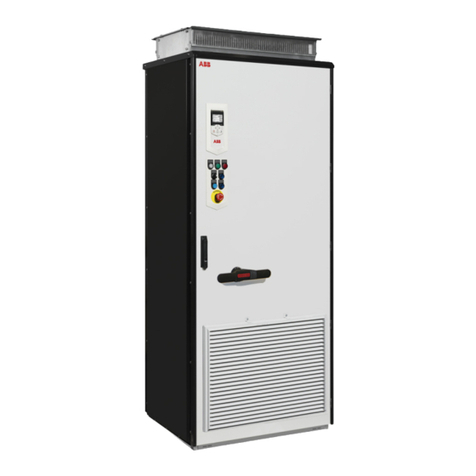
ABB
ABB ACS880-07 user manual