Jafar 2904 User manual

OPERATION AND MAINTENANCE MANUAL 03-2016
Operation and maintenance
manual for
ONE-WAY
KNIFE
GATE VALVES
WITH RIVE ACTUATOR
P/N
2904
Approved for use by
President of Factory, JAFAR S.A.
Failure to comply with the guidelines and instructions in this Operation and
Maintenance Manual releases the manufacturer from all obligations, liability and guarantee.
Due to continuous business development, we reserve the right to introduce
modifications and structural changes to the presented product.

OPERATION AND MAINTENANCE MANUAL 03-2016
2
CONTENTS
1 TECHNICAL DESCRIPTION ........................................................................................................................... 3
1.1 PRODUCT DESIGNATION AND IDENTIFICATION ......................................................................... 3
1.2 USE............................................................................................................................................................... 3
1.3 TECHNICAL SPECIFICATION.............................................................................................................. 3
2 DESIGN............................................................................................................................................................... 3
2.1 DESCRIPTION OF THE VALVE DESIGN............................................................................................ 3
2.2 MATERIALS .............................................................................................................................................. 4
2.3 DIMENSIONS............................................................................................................................................. 5
2.4 REFERENCE STANDARDS..................................................................................................................... 6
2.5 ORDERING INFORMATION.................................................................................................................. 6
2.6 PRODUCTION AND ACCEPTANCE ..................................................................................................... 7
2.7 MARKINGS................................................................................................................................................ 7
3 PROTECTION, STORAGE & TRANSPORT.................................................................................................... 7
3.1 PROTECTIVE COATINGS...................................................................................................................... 7
3.2 PACKAGING.............................................................................................................................................. 7
3.3 STORAGE................................................................................................................................................... 7
3.4 TRANSPORT.............................................................................................................................................. 8
4.1 ASSEMBLY GUIDELINES....................................................................................................................... 8
4.2 ASSEMBLY INSTRUCTIONS.................................................................................................................. 9
4.3 OPERATION ............................................................................................................................................ 11
4.4 OCCUPATIONAL HEALTH AND SAFETY........................................................................................ 11
5 WARRANTY TERMS AND CONDITIONS.................................................................................................... 11

OPERATION AND MAINTENANCE MANUAL 03-2016
3
1 TECHNICAL DESCRIPTION
1.1 PRODUCT DESIGNATION AND IDENTIFICATION
The subject of this Operation and Maintenance Manual is:
Type 2904 one-way flange-to-flange knife gate valve with drive actuator
- full bore design
- stainless steel knife (closer)
- available with rising or stationary spindle
- soft gland seal of the closer and the body
1.2 USE
The Type 2904 one-way flange-to-flange knife gate valves are intended for water supply systems, and
especially sewage systems, and industrial processing systems. The valves can be operated both in
underground (non-flooded sewers) and overground installations as installed in vertical or horizontal
pipelines.
1.3 TECHNICAL SPECIFICATION
The Type 2904 flange-to-flange knife gate valves are intended for transfer of potable water, process water
and sewage, as well as other liquids as approved by the manufacturer.
- Temperature: 0°C to +70°C
- Nominal diameter (dimension) range: DN50 to DN700 [mm]
- Maximum medium flow rate: - liquid: max. 4 [m/s]
- gas: max. 30 [m/s]
- The driving torque at opening start and closing end is as listed below:
DN
[mm] 50 65 80 100 125 150 200 250 300 350 400 450 500 600 700
Mmax
[Nm]
20 25 30 30 50 60 70 80 90 105 120 160 180 210 250
Valve control mode: the standard version of gate valve has the
clockwise closing sense of rotation.
The closing sense of rotation can be opposite on special order.
- The knife valves are designed for installation between flange end faces
acc. to PN-EN 1092-2: 1999 with bolt holes for the pressure rating of PN10.
Installation length: per the technical file, see Table 2 for sizes.
- Nominal pressure PN values: - per size:
DN50 to DN250 - 1 MPa
DN300 to DN450 - 0.7 MPa
DN500 to DN600 - 0.4 MPa
DN700 - 0.25 MPa
2 DESIGN
2.1 DESCRIPTION OF THE VALVE DESIGN
The Type 2904 one-way flange-to-flange knife gate valves supplied by F.A. „JAFAR”S.A. feature a full
bore body, a stationary spindle (in the standard version) and an L-gasket closure seal embedded in a metal
enclosure. The body seal of the knife is a multi-layered packing compressed by a gland with bolts. The gland on
the delivered valve is loose and must be tightened before installation. The knife gate valve body is a monolithic

OPERATION AND MAINTENANCE MANUAL 03-2016
4
panel design. The valve knife clears the body driven by the electric actuator (available from DN50) which drives
the nut-seated threaded spindle from the outside. The one-way design means that the flow may only be admitted
from one direction only to keep the valve leak-tight. The holes for flange-to-flange connection are tapped in the
top valve body section and through in the bottom valve body section (see the bolt table). Table 4 shows the bolt
sizing for flange ends (PN10 bolt hole layout).
2.2 MATERIALS
Table 1 lists the structural materials of the Type 2904 flange-to-flange knife gate valves.
Item Part designation Material Reference standard
1Body Grey cast-iron, EN-GJL-250
Spheroidal cast-iron, EN-GJS-400-15
Steel grade 1.4301
PN-EN 1561: 2012
PN-EN 1563: 2012
PN-EN 10088-1: 2014
2Seal Package: Asbestos-free sealant +
NBR Manufacturer's catalogue
PN-EN 1629: 2005
3Knife Steel grade 1.4301 PN-EN 10088-1: 2014
4Spindle Steel grade 1.4021 PN-EN 10088-1:2014
5Stem Steel grade 1.0038 PN-EN 10025-2:2007
6Drive coupling Cast-iron, EN-GJS-400-15 PN-EN 1563: 2012
7 Bolt Stainless steel, A2 PN-EN ISO 4014: 2011
8 Safety ring Steel grade 1.4301 PN-EN 10088-1:2014
9Cap Polypropylene PN-EN ISO 1873: 2000
10 Shielding tube Steel, R45 PN-89/H-84023.07
11 Pressure plate Silumin, AlSi PN-EN 1706: 2011
12, 13 Gasket Rubber NBR PN-EN 1629: 2005
14 Electric drive actuator Manufacturer's catalogue

OPERATION AND MAINTENANCE MANUAL 03-2016
5
2.3 DIMENSIONS
Table 2
DN PN PS
Thread type No. of turns
K l
x
n A B D H
Mass
[mm] [mm] [n] [kg]
50 14 125 283 556 27
65 17 145 308 581 29
80 21 160 333 606 30
100 26 180 378 651 31
125 32 210 423 696 37
150 39 240 474 747 41
200 41 295 593 866 58
250 51 350 685 958 72
300 61 400 792 1118 86
350 59 460 23x16 96 900 1282 138
400 68 515 28x16 100 978 1441 168
450 76 565 28x20 106 1105 1587 234
500 84 620 28x20 1215 1809 269
600 102 725 31x20 1418 2060 313
700 2 SA 14.6 Tr 50x8 LH 103 840 31x24 1640 400 2372 480
[bar]
10
16
10
4
7
10
Flangedrive type
SA 07.2
(F7) F7
SA 14.2
(F14) F14
F7 / F10
SA 10.2
(F10)
SA 07.6
(F7 / F10)
F10
[mm]
40
50
60
83
93
19x4
19x8
23x8
Tr 20x4 LH
Tr 25x5 LH
Tr 35x6 LH
108
290
110
7023x12

OPERATION AND MAINTENANCE MANUAL 03-2016
6
2.4 REFERENCE STANDARDS
PN-EN 1074-1: 2002 Valves for water supply. Fitness for purpose requirements and appropriate
verification tests. General requirements
PN-EN 1074-2: 2002 Valves for water supply. Fitness for purpose requirements and appropriate
verification tests. Isolating valves.
PN-89/H-02650 Valves and pipelines. Pressure and temperature ratings.
PN-EN 1092-2: 1999 Flanges and their joints. Circular flanges for pipes,
valves, fittings and accessories, PN designated. Cast iron flanges.
PN-EN19: 2005 Industrial valves. Marking of metallic valves
PN-EN 12266-1: 2012 Industrial valves. Testing of metallic valves. Pressure tests, test procedures
and acceptance criteria. Mandatory requirements.
PN-EN ISO 5210: 2011 Industrial valves. Multi-turn valve actuator attachments.
PN-EN ISO 6708: 1998 Pipework components. Definition and selection of DN (nominal size).
PN-EN 1559-1: 2011 Founding. Technical conditions of delivery. General.
PN-EN 1561: 2012 Founding. Grey cast irons.
PN-EN 1563: 2012 Founding. Spheroidal graphite cast irons.
PN-EN 1370: 2012 Founding. Surface roughness inspection by
visual tactile comparators.
PN-EN 10088-1: 2014 Stainless steels. List of stainless steels.
PN-89/H-84023.05 Specific application steel. Improved quality low-carbon, low-alloy and alloy
steels. Grades.
PN-EN 10025-2:2007 Hot-rolled products of structural steel grades – Part 2: Technical
condictions for supply of non-alloy structural steel.
PN-EN 1982: 2010 Copper and copper alloys. Ingots and castings.
PN-EN 12420: 2002 Copper and copper alloys. Forgings.
PN-EN 1706: 2011 Aluminium and aluminium alloys. Castings. Chemical composition
and mechanical properties.
PN-ISO 965-1: 2001 General purpose ISO metric threads. Tolerances. Principles and basic data.
PN-ISO 2903: 1996 Trapezoid ISO metric threads. Tolerances.
PN-EN ISO 4017: 2011 Hexagon head screws. Product grades A and B.
PN-EN ISO 4027: 2006 Hexagon socket set screws with cone point.
PN-ISO 1629: 2005 Rubbers and latices. Nomenclature.
PN-EN ISO 1873-1: 2000 Plastics. Polypropylene (PP) moulding and extrusion materials. Designation
system and basis for specifications.
PN-EN ISO 12944-5: 2009 Paints and varnishes. Corrosion protection of steel structures by protective
paint systems. Protective painting systems.
2.5 ORDERING INFORMATION
Water supply system valves are specific purpose industrial valves, therefore orders must include:
- part number (P/N, equal to the product type);
- intended use, e.g. for water supply systems,
and:
- nominal diameter, acc. to PN-EN ISO 6708: 1998
- nominal pressure, acc. to PN-89/H-02650;
- type of body material — acc. to PN-EN 1561: 2012, PN-EN 1563: 2012
or PN-EN 10088-1: 2014
- maximum operating temperature, acc. to PN-89/H-02650.

OPERATION AND MAINTENANCE MANUAL 03-2016
7
2.6 PRODUCTION AND ACCEPTANCE
The Type 2904 flange-to-flange knife gate valves are accepted and produced in accordance with PN-EN
1074-2: 2002 (Valves for water supply. Fitness for purpose requirements and appropriate verification tests.
Isolating valves) and PN-EN 12266-1: 2012 (Industrial valves. Testing of metallic valves. Pressure tests, test
procedures and acceptance criteria. Mandatory requirements). All valves (100%) are subject to tightness testing.
The tests include external body tightness and closing tightness.
2.7 MARKINGS
The valve marking is regulated by the following standards: PN-EN-19: 2005, PN-EN-1074-1: 2002.
The valve bodies feature markings on the front and back walls of the body chamber. The marking contains
the following data:
- valve type (defined by the product reference standard number)
- nominal diameter
- nominal pressure
- body material type
- manufacturer trademark
The location on the valve specified in the documentation features the nameplate which contains the
following data: - manufacturer's company name and logo
- serial number
- sealing temperature rating
- construction mark "B" and/or mark "CE" (as applicable)
- product type.
3 PROTECTION, STORAGE & TRANSPORT
3.1 PROTECTIVE COATINGS
All inner and outer cast-iron and steel surfaces are protected with electro-deposited epoxy coat. The coat has
been approved for contact with foodstuffs.
The anti-corrosion coating layer minimum thickness is 250µm.
The casting surface is pre-treated for epoxy coating in accordance with the relevant technical documentation and
PN-EN ISO 12944-5: 2009.
The stem to body and to nut mount fastening bolts are made of stainless steel (A2).
3.2 PACKAGING
The Type 2904 knife gate valves are packed on EURO pallets (1200x800) and protected with heat-shrunk
film.
3.3 STORAGE
Store the Type 2904 knife gate valves in sheltered rooms.

OPERATION AND MAINTENANCE MANUAL 03-2016
8
3.4 TRANSPORT
Transport the Type 2904 knife gate valves on sheltered vehicles.
The manufacturer recommends slings for transport and installation of valve sizes from DN50 to DN700.
4 ASSEMBLY AND INSTALLATION
4.1 ASSEMBLY GUIDELINES
The Type 2904 flange-to-flange knife gate valves can be installed in underground or overground pipelines
both in horizontal or vertical orientation. The knife gate valves are designed for mounting between flange ends of
the pipelines sized for the PN10 bolt hole layout acc. to PN-EN 1092-2: 1999. Note that the system must not
expose the (gate) valve to bending or tensile stress from loading with the weight of unsupported pipeline sections.
Assemble with consideration to pressure and temperature compensation of the pipeline.
The knife gate valve allow adjusting the gland (by retightening) to eliminate all leaks through the valve.
Reseal the gland by tightening the nuts diagonally to the torque value appropriate for the nut size (see the table
below). Once installed and adjusted as above, the gate valve is ready for commissioning.
Any other work related to disassembly of the valve components (except for the gland) may result in loss of
seal and warranty rights.
CAUTION!
If the gate valve terminates a pipeline (system), bolt it between flanges on both ends.
Table 3

OPERATION AND MAINTENANCE MANUAL 03-2016
9
Bolt
thread
size
Bolt tightening torque
Bolt strength class
6.9 8.8 10.9
[Nm]
M4 2.7 3 4.3
M5 5 6 8.5
M6 9 11 15
M8 20 25 35
M10 42 51 70
M12 73 87 120
M14 115 135 195
M16 180 210 300
M18 245 290 410
M20 350 410 580
M22 470 560 780
M24 560 710 1000
M27 900 1050 1480
M30 1200
1430 2010
M33 1630
1940 2700
M36 2100
2490 3500
M39 2720
3220 4550
Table of maximum tightening torques for individual bolts for tightening the knife gate valve gland.
4.2 ASSEMBLY INSTRUCTIONS
Before attempting to install the valve, check the technical and commercial documents delivered with the
product to verify that the media and pipeline operating parameters comply with the manufacturer's declaration.
Any change in the operating conditions must be consulted with the valve manufacturer beforehand.
Before attempting to assemble the valve, remove the main bore plugs, check the inner surfaces of the valve and
thoroughly flush with water, if necessary.
Lubricate the spindle nut via the grease nipple in the nut holder and keep the nut clean.
CAUTION! If the product is damaged mechanically, do not install it in the pipeline.
CAUTION! In the horizontal orientation of installation, supports must be used to relief the strain on the
valve.

OPERATION AND MAINTENANCE MANUAL 03-2016
10
The figure below shows the assembly method of the gate valve and the valve orientation diagrams:
1. - Knife gate; 2. - Pipeline flange end; 3. - Assembly bolt; 4. - Seal; 5. - Nut; 6. - Washer
Use of bolts for the knife gate valve P/N 2904.
Recommended Permitted
Not permitted

OPERATION AND MAINTENANCE MANUAL 03-2016
11
Table 4
DN [mm] 50 65 80 100 125 150 200 250 300 350 400 450 500 600 700
D [mm] 165 185 200 220 250 285 340 395 445 505 565 615 670 780 895
K [mm] 125 145 160 180 210 240 295 350 400 460 515 565 620 725 840
Lxn 4x18
4x18
8x18
8x18
8x18
8x22
8x22
12x2
2 12x2
2 16x2
2 16x2
2 20x2
6 20x2
6 20x3
0 24x3
0
Thread-in
bolts
(l x M x
length)
8
M16
x25
8
M16
x25
8
M16
x30
8
M16
x30
8
M16
x30
8
M20
x35
8
M20
x35
16
M20
x40
16
M20
x40
20
M20
x45
20
M24
x50
28
M24
x55
28
M24
x55
28
M27
x55
32
M27
Z [mm] 8 8 9 9 9 10 12 12 12 19 20 24 24 24 -
Bolts with
nuts
(l x M x
length)
- - 4
M16
x120
4
M16
x120
4
M16
x120
4
M20
x130
4
M20
x140
4
M20
x150
4
M20
x150
6
M20
x180
6
M24
x190
6
M24
x200
6
M24
x200
6
M27
x200
8
M27
x210
4.3 OPERATION
The type 2904 knife gate valve shall be operated according to all relevant requirements for cut-off valves,
i.e. either in fully open or fully closed positions. Leaving the gate valve partially opened (or closed) may result in
seal failure. In order to guarantee full operating fitness, switch the gate valve periodically (at least every 6
months) (from fully open to fully closed) with the installation on line to self-clean the valve. At the same time
visually inspect the gland assembly. If leaks are found, repair it by following Section 4.1.
Exceeding the operating limits of the valve may result in damage that will not covered by the suretyship
granted by the manufacturer.
4.4 OCCUPATIONAL HEALTH AND SAFETY
The Type 2904 knife gate valves are eligible for the OHS guidelines and recommendation concerning
installation of pipelines and devices for water supply stations, heat power plants, water treatment plants, sewage
treatment plants, pumping stations and other facilities, and eligible for the Polish Regulation concerning general
OHS laws (use of personal protective equipment for hands, legs and head, and safety garment), especially at
work with low or high temperature hazard.
Misuse of this product is prohibited.
5 WARRANTY TERMS AND CONDITIONS
The product assembled, installed and operated in compliance with this Manual is covered by a commercial
warranty from the manufacturer.
The warranty terms, conditions and period are specified in the relevant
Warranty Sheet.
Table of contents
Popular Controllers manuals by other brands

Shinko
Shinko DCL-33A instruction manual
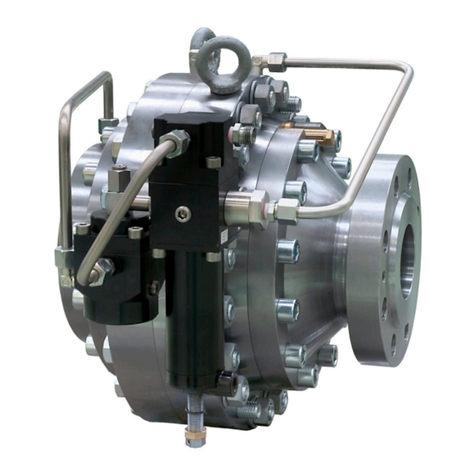
PIETRO FIORENTINI
PIETRO FIORENTINI ASX 176 TRANSLATION OF ORIGINAL INSTRUCTIONS
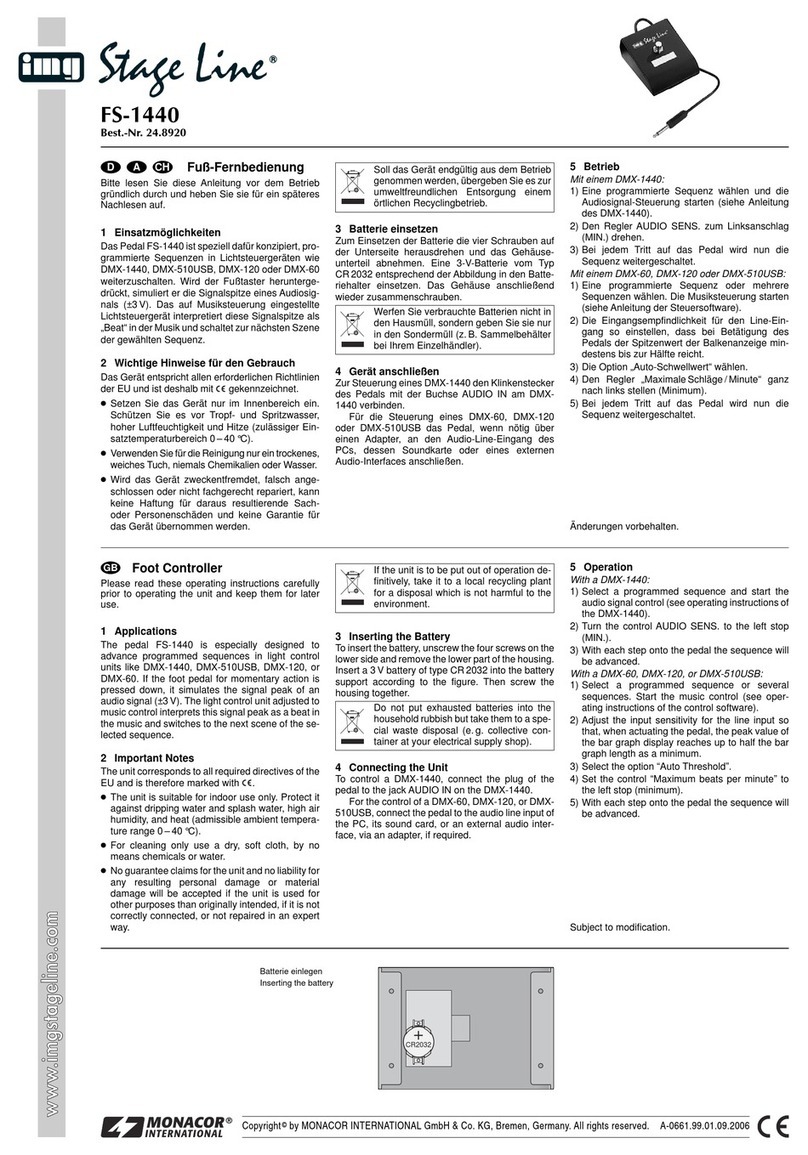
Monacor
Monacor IMG Stageline FS-1440 quick guide
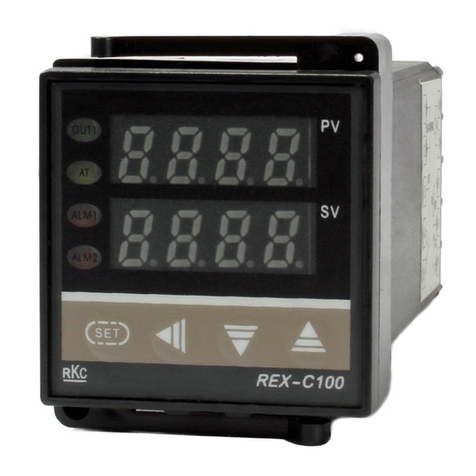
RKC INSTRUMENT
RKC INSTRUMENT REX - C100 INITIAL SETTING MANUAL
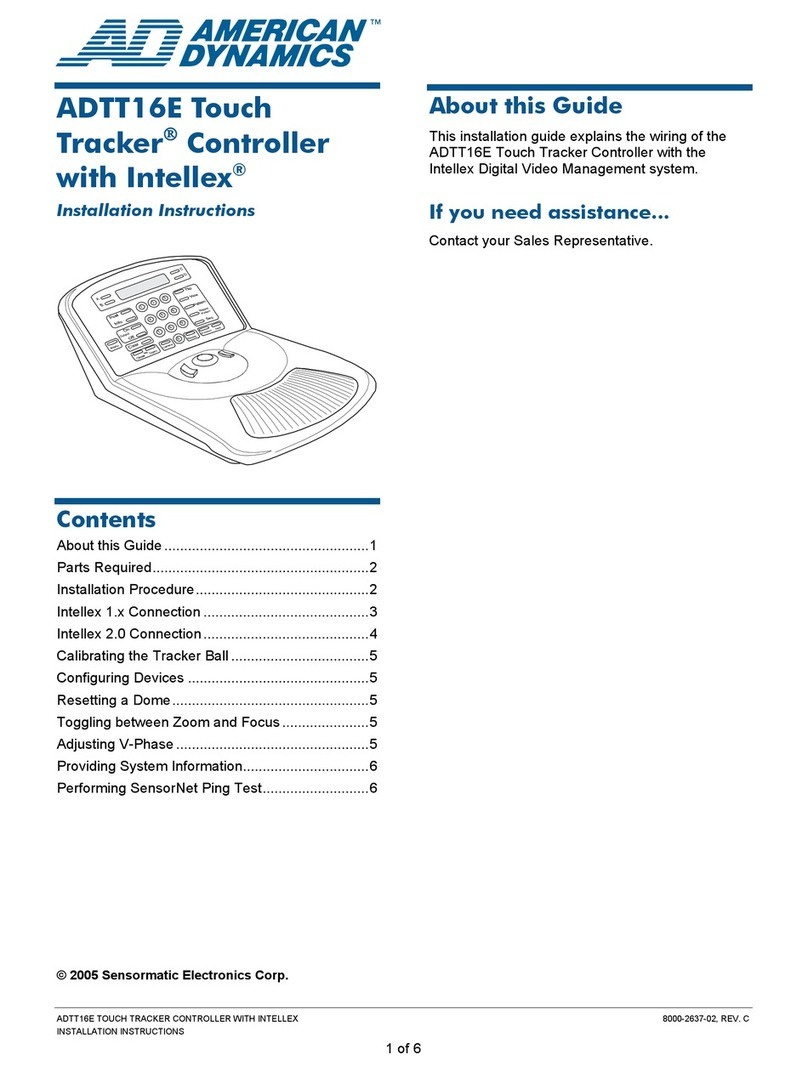
American Dynamics
American Dynamics ADTT16E Touch Tracker installation instructions
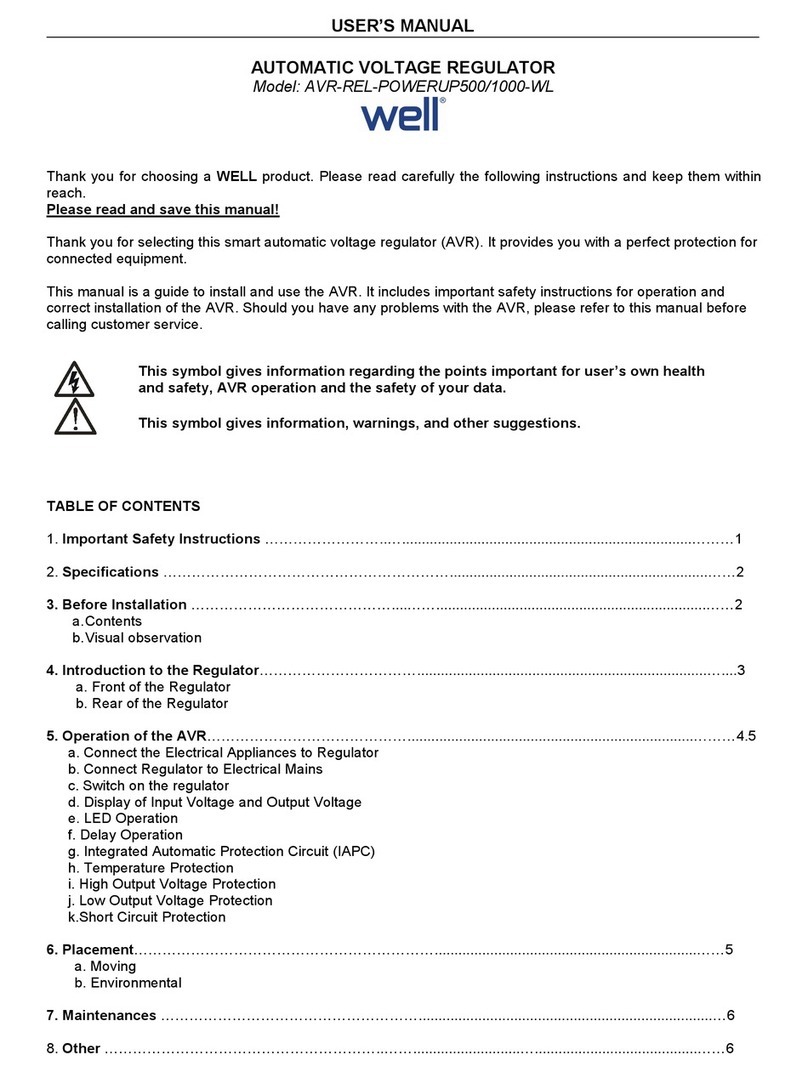
Well
Well AVR-REL-POWERUP500-WL user manual