Jarvis PFI-1 User manual

PRODUCTS CORPORATION
33 ANDERSON ROAD, MIDDLETOWN, CONNECTICUT 06457--4926
TEL. 860--347--7271 FAX. 860--347--6978 WWW.jarvisproducts.com
TABLE OF
CONTENTS Page.........................
PFI--1 4311002.......................
Balancer 1350147....................
•Safety Messages to Employer and Safety
Director 2.........................
•Safety Messages to Operators
Maintenance and Cleanup Personnel 3
•Parts Diagram and List 4............
•Specifications 5....................
•Installation Instructions 5............
•Operation Instructions 5.............
•Maintenance Instructions 6..........
PFI--1
PICKING FINGER INSTALLER
EQUIPMENT
SELECTION Ordering No.
..........
®
JARVIS
6223015::.

safety messages to employer
and safety director
page 2 of 8
Model PFI--1
PRODUCTS CORPORATION
33 ANDERSON ROAD, MIDDLETOWN, CONNECTICUT 06457--4926
TEL. 860--347--7271 FAX. 860--347--6978 WWW.jarvisproducts.com
®
JARVIS
6223015::.
1. Ensure that all employees who use this tool are trained in the proper use of this tool and are aware of
the dangers that may arise if they do not follow procedures outlined in this brochure.
2. Enclosed are four (4) copies of “NOTICE TO OPERATORS, MAINTENANCE AND CLEANUP PER-
SONNEL.” Post one copy on the employees’ bulletin board; give one copy to the operator(s); give one
copy to the maintenance foreman; and give one copy to the sub--contract cleanup / internal cleanup fore-
man. Additional copies will be provided upon request.
3. The tool is designed and intended to be powerful. This fact should be obvious to your employees, but
you must emphasize it to them.
4. Ensure that proper procedures are established (in accordance with OSHA’s lockout/tagout procedures
29 CFR 1910.147) to prevent accidental startup or release of stored energy.
5. Remove and repair any tool that malfunctions. All personnel must be instructed to remove any mal-
functioning equipment.
6. Never make modifications or alterations to the tool. Replace any missing or illegible labels.
7. Follow our installation and maintenance instructions for proper installation and care of the tool.
8. Avoid injury. Do not permit the tool to be misused.
9. If you resell or distribute a Jarvis product, you must provide the purchaser with the appropriate safety
sheets and tool brochure. Additional copies of safety sheets and tool brochures will be provided upon
request.
SAFETY MESSAGES TO EMPLOYER AND SAFETY DIRECTOR
AVOID INJURY

safety messages to operators,
maintenance and cleanup personnel
page 3 of 8 Model PFI--1
PRODUCTS CORPORATION
33 ANDERSON ROAD, MIDDLETOWN, CONNECTICUT 06457--4926
TEL. 860--347--7271 FAX. 860--347--6978 WWW.jarvisproducts.com
®
JARVIS
6223015:.
1. Disconnect the air hose in accordance with OSHA’s lockout/tagout procedures (29 CFR 1910.147) be-
fore performing any repair or maintenance.
2. Disconnect the air hose -- or have the air hose disconnected -- in accordance with OSHA’s lockout/tag-
out procedures (29 CFR 1910.147) before performing any cleanup.
3. Disconnect the air hose when the tool is not being used.
4. Never put fingers, hands or other parts of the body in the path of the moving claws while tool is connec-
ted to the air supply.
5. Test the tool prior to use or daily. Depress trigger and the claws should move into the frame. Release
the trigger and the claws should move out of the frame. If the tool malfunctions, remove it from service
and report or repair it immediately.
6. Never depress the trigger unless you want to use the tool.
7. Never make modifications or alterations to the tool. Replace any missing or illegible labels.
SAFETY MESSAGES TO OPERATORS, MAINTENANCE AND CLEANUP
PERSONNEL
REMOVE ANY MALFUNCTIONING TOOL FROM SERVICE
REPORT ANY PROBLEMS TO YOUR SUPERVISOR

parts diagram and list
page 4 of 8
Model PFI--1
PRODUCTS CORPORATION
33 ANDERSON ROAD, MIDDLETOWN, CONNECTICUT 06457--4926
TEL. 860--347--7271 FAX. 860--347--6978 WWW.jarvisproducts.com
®
JARVIS
6223015::.
ITEM PART NO. PART NAME QTY
1 1323011** Hose Assy (incls. item 2) 1
2 1324078** Quick Connect Socket 1
3 1324117 Quick Connect Plug 1
4 1347020 Handle 1
5 1301135 Fillister Head Screw 4
6 1301134 Set Screw 1
7 1301133 Set Screw 1
8 1336029 Compression Spring 1
9 1035336 O--ring (package of 5) 1
10 3345001* Trigger and Valve Assembly 1
(includes item 9 ) 1
11 1301138 Pan Head Screw 8
12 1304121 Guard Plate 2
13 1343061 O--ring 2
14 1343071 Rectangular Gasket 1
15 1302027 Hex Lock Nut 2
16 1303104 Plain Washer 2
17 1330059 Frame and Cyl. Housing. 1
18 1316068 Spacer 4
19 1311035 Cam Roller 2
20 1343058 U--cup Seal 1
21 1343060 O--ring 1
22 1312060 Piston Rod and Yoke 1
23 1336028 Extension Spring 1
ITEM PART NO. PART NAME QTY
24 1327128 Pivot Pin 2
25 1338030 Bushing 4
26 1349002 Double Claw (left side) 1
27 1317028+ Retaining Ring 2
28 1327147 Cotter Pin 2
29 1349003 Single Claw (right side) 1
30 1301137 Socket Head Screw 2
31 1017325 Danger Label 1
32 1301116 Eye Bolt 1
33 1338029 Bushing 1
34 1305044 Piston 1
35 1302033 Hex Jam Nut 1
36 1343057 U--cup Seal 2
37 1343059 O--ring 1
38 1322009 End Cap 1
39 1317027 Retaining Ring 1
40 1301136 Hex Screw 1
8330024* Special Tool (not shown) 1
Figure A
Picking Finger
Insertion Tool
Assembly
If any part of trigger and valve assembly needs replacing,
the whole assembly must be replaced. A special tool,
Jarvis part number 8330024, is required for trigger valve
sleeve removal and installation.
*
+Not used in current tools
** Available as spare part only, not included with tool.
+
** **
*

specifications, installation
and operation instructions
page 5 of 8 Model PFI--1
PRODUCTS CORPORATION
33 ANDERSON ROAD, MIDDLETOWN, CONNECTICUT 06457--4926
TEL. 860--347--7271 FAX. 860--347--6978 WWW.jarvisproducts.com
®
JARVIS
6223015:.
SPECIFICATIONS
Model PFI--1
Operating Pressure 90 psi 6.2 bar
Air Consumption
Per Cycle at 90 psi 0.091 ft3
Per Cycle at 6.2 bar 2.58 L
Overall Length 12.3 in 312 mm
Overall Width 4.0 in 102 mm
Opening Dimension (expanded)
widthxheight 1x1in 25.4x25.4mm
depth 4.75 in 120.7 mm
Weight 5.9 lbs 2.7 kg
INSTALLATION INSTRUCTIONS
1 Install the PFI--1 above the work area from a balanc-
er, if applicable. Jarvis part number 1350147 is
available.
1.1 The PFI--1 should have sufficient travel to allow
the operator to reach the entire work area.
2 Make the necessary air connection.
2.1 The minimum required compressed air supply is
0.091 ft3/ cycle at 90 psi (2.58 L / cycle at 6.2
bar).
2.2 An air filter/regulator/lubricator must be in-
stalled in the air supply line. Jarvis part number
3346001 is available. Keep the lubricator filled
at all times.
OPERATION INSTRUCTIONS
ALWAYS DISCONNECT THE AIR HOSE IN ACCOR-
DANCE WITH OSHA’S LOCKOUT/TAGOUT PROCE-
DURES (29 CFR 1910.147) BEFORE PERFORMING
ANY MAINTENANCE OR REPAIRS.
Refer to Figure A on page 4 for referenced items.
1 Connect air hose.
2Each day, before you begin operation, go through the
following checklist:
2.1 Make sure that the compressed air supply is at
the proper pressure and that the lubricator is up
to the full mark. (Use Jarvis Air Mist Lubrica-
tor Oil; if using a conventional air mist lubrica-
tor: set the feed rate at 8--10 drops per minute; if
using a micro fog air mist lubricator*: set the
feed rate at 100 drops per minute). *Almost all
air mist lubricators are micro fog air mist lubri-
cators.
2.2 Make sure the tool is working correctly. Depress
the trigger and the claws should move into the
frame. Release the trigger and the claws should
move out of the frame. If the tool malfunctions,
remove it from service and report the problem
to your supervisor immediately.
2.3 Make sure that the PFI--1 moves freely on the ba-
lancer, if applicable.
3 Inserting the fingers. Refer to Figure 1 as a guide.
THE PFI- 1 IS NOT INTENDED FOR REMOVAL OF
FINGERS. MISUSE OF THE TOOL CAN CAUSE IN-
JURY AND DAMAGE THE TOOL.
3.1 Insert rubber finger by hand through the hole in
barrel drum or plate.
3.1.1 Pull finger by hand firmly against barrel
drum or plate so that the finger will stay in
place for the PFI--1 to grasp. Note: Keep the
finger dry. Do not use any oil or water as a
lubricant on the finger.
3.2 Place opened claws over entire rubber finger and
press tool against barrel drum or plate, as appli-
cable.
3.3 Press trigger to grasp and pull the finger.
3.3.1 Use the PFI--1 to grasp and pull the finger
through the barrel drum or plate until groove
of rubber finger seats into the hole of the
barrel drum or plate. Repeat this step if nec-
essary.
3.4 Release the trigger and remove the PFI--1.

maintenance instructions
page 6 of 8
Model PFI--1
PRODUCTS CORPORATION
33 ANDERSON ROAD, MIDDLETOWN, CONNECTICUT 06457--4926
TEL. 860--347--7271 FAX. 860--347--6978 WWW.jarvisproducts.com
®
JARVIS
6223015::.
Double Claw
Figure 1
Finger Insertion
Single Claw
Barrel Drum
Fingers
Place PFI--1
against barrel
drum or plate.
Figure above depicts PFI--1 with barrel drum con-
taining round fingers. The PFI--1 can also be used
for plates and rectangular fingers. Note: Rectan-
gular fingers can only be installed one way. Check
holes for proper orientation.
Activate PFI--1 to
grasp and pull fin-
ger outward away
from barrel drum or
plate.
Groove
MAINTENANCE INSTRUCTIONS
ALWAYS DISCONNECT THE AIR HOSE IN ACCOR-
DANCE WITH OSHA’S LOCKOUT/TAGOUT PROCE-
DURES (29 CFR 1910.147) BEFORE PERFORMING
ANY MAINTENANCE OR REPAIRS.
DISSIPATE STORED ENERGY BEFORE PERFORM-
ING ANY MAINTENANCE OR REPAIRS.
Refer to Figure A on page 4 for referenced items.
1 DAILY: Each day, before you begin operation, go
through the following checklist:
1.1 Make sure the control trigger is working correct-
ly. Depress the trigger and the claws should
move into the frame. Release the trigger and the
claws should move out of the frame. If the tool
malfunctions, repair or remove it from service
immediately.
Connect the air hose to perform this operation
only.
1.2 Inspect all screws, nuts and fasteners and tighten
or replace as necessary.
1.3 Inspect air hose and fittings for leaks and tighten
or replace as necessary.
2 AS NECESSARY:
2.1 Disassemble, clean and inspect the PFI--1. Refer
to sections 3 through 12 as a procedural guide.
3 CAM ROLLER REMOVAL:
3.1 Remove hex nuts (item 15), washers (item 16)
and socket head screws (item 30).
3.2 Remove spacers (item 18) and cam rollers (item
19).
3.3 Clean and inspect all parts for wear and replace
them if necessary.
4 CAM ROLLER ASSEMBLY:
4.1 Reverse steps and procedures outlined in section
3.
5 SINGLE AND DOUBLE CLAW REMOVAL:
5.1 Remove pan head screws (item 11) and guard
plates (item 12) from both sides of frame and
cylinder housing (item 17).
5.2 Remove cam rollers (item 19). Refer to steps
and procedures outlined in section 3.
5.3 Extend the piston rod and yoke (item 22) so that
retaining rings (item 27) or cotter pins (item 28)
and pivot pins (item 24) are aligned with top and
bottom holes of frame and cylinder housing
(item 17).

maintenance instructions
page 7 of 8 Model PFI--1
PRODUCTS CORPORATION
33 ANDERSON ROAD, MIDDLETOWN, CONNECTICUT 06457--4926
TEL. 860--347--7271 FAX. 860--347--6978 WWW.jarvisproducts.com
®
JARVIS
6223015:.
5.4 Remove retaining rings (item 27) or cotter pins
(item 28) and pivot pins (item 24). Use a pin
punch to drive pivot pins out through holes in
frame and cylinder housing (item 17).
5.5 Slide the single and double claws (items 29 and
26) and bushings (item 25) out from piston rod
and yoke (item 22).
5.5.1 Remove the single and double claws and
bushings out from either side of the frame
and cylinder housing (item 17).
5.5.1.1 Remove the claws with the extension
spring (item 23) still attached to both
claws.
5.6 Remove extension spring (item 23).
5.7 Remove bushings (item 25) from single and
double claws (items 29 and 26).
5.8 Clean and inspect all parts for wear and replace
them if necessary.
6 SINGLE AND DOUBLE CLAW INSTALLA-
TION:
6.1 Reverse steps and procedures outlined in section
5. See notes below.Refer to Figure 2 as a guide.
6.1.1 Align holes in piston rod and yoke (item 22),
bushings (item 25), and single and double
claws (items 29 and 26) with the top and bot-
tom holes of frame and cylinder housing
(item 17) to install retaining rings (item 27)
or cotter pins (item 28) and pivot pins (item
24).
6.1.1.1 Slide pivot pins (item 24) through the
holes using a drive pin to hold pivot pins
in place while securing the retaining
rings (item 27) or cotter pins (item 28)
to them.
6.1.1.2 Use a 1/4 inch nut driver to push retain-
ing rings (item 27) securely onto pivot
pins (item 24) or push cotter pins (item
28) with a flat screw driver blade.
7 PISTON AND SEAL REMOVAL:
DISSIPATE STORED ENERGY FROM CYLINDER
HOUSING BEFORE PERFORMING ANY MAINTE-
NANCE OR REPAIRS.
Retaining Ring
Drive Pin
Pivot Pin
Retaining Ring
Pivot Pin
Nut Driver (1/4 inch)
Figure 2
Single and Double Claw
Installation
Push retaining rings
onto pivot pins.
Hold pivot pins in
place with drive pin
Double
Claw
Piston Rod
and Yoke
7.1 Disconnect hose from quick connect plug (item
3).
7.2 Slide piston rod and yoke (item 22) into frame
and cylinder housing so that piston assembly
(items 34 and 36) is all the way to the back end
of the frame and cylinder housing (item 17).
7.3 Remove retaining ring (item 39) and end cap
(item 38).
7.4 Remove o--ring (item 37), if necessary.
7.5 Remove hex nut (item 35).
7.6 Remove piston (item 34) and U--cup seals (item
36).
7.7 Clean and inspect all parts for wear and replace
them if necessary.

maintenance instructions
page 8 of 8
Model PFI--1
PRODUCTS CORPORATION
33 ANDERSON ROAD, MIDDLETOWN, CONNECTICUT 06457--4926
TEL. 860--347--7271 FAX. 860--347--6978 WWW.jarvisproducts.com
®
JARVIS
6223015::.
8 PISTON AND SEAL ASSEMBLY:
8.1 Reverse steps and procedures outlined in section
7. See notes below.
8.2 Apply a generous amount of Jarvis 1315 White
Grease to U--cup seals (item 36) before instal-
ling back into frame and cylinder housing (item
17).
8.3 Make sure that the flat surface of U--cup seals
(item 36) are facing each other.
8.4 Apply Loctite 262 to threads of hex nut (item 35)
before tightening.
8.5 Make sure retaining ring (item 39) is seated
properly into groove of frame and cylinder hous-
ing (item 17).
9 PISTON ROD AND SEAL REMOVAL:
9.1 Remove cam rollers (item 19). Refer to steps
and procedures outlined in section 3.
9.2 Remove single and double claws (items 29 and
26). Refer to steps and procedures outlined in
section 5.
9.3 Remove piston and U--cup seals (items 34 and
36). Refer to steps and procedures outlined in
section 7.
9.4 Slide piston rod and yoke (item 22) out from the
front end of frame and cylinder housing (item
17).
9.5 Remove U--cup seal (item 20) from inside the
front end of frame and cylinder housing (item
17).
9.6 Remove o--ring (item 21), if necessary.
9.7 Clean and inspect all parts for wear and replace
them if necessary.
10 PISTON ROD AND SEAL ASSEMBLY:
10.1 Reverse steps and procedures outlined in section
7. See notes below.
10.2 Apply a generous amount of Jarvis 1315 White
Grease to U--cup seal (item 20) before installing
into frame and cylinder housing (item 17).
10.3 Make sure flat surface of U--cup seal (item 20)
is facing toward the front end of frame and cylin-
der housing (item 17).
10.4 Follow steps and procedures outlined in section
8.
10.5 Follow steps and procedures outlined in section
6.
11 TRIGGER VALVE ASSEMBLY REMOVAL:
11.1 Remove set screw (item 6) from handle (item 4).
11.2 Remove trigger and valve assembly (item 10)
from handle.
11.3 Remove compression spring (item 8).
11.4 Remove set screw (item 7) from handle (item 4).
11.5 Remove valve bushing from handle (item 4).
Use Jarvis special tool (part number 8330024)
to remove and install valve bushing.
11.6 Clean and inspect all parts for wear and replace
them if necessary. NOTE: If any part of trigger
valve assembly needs to be replaced, the whole
valve assembly must be replaced. Do not mix old
and new parts.
12 TRIGGER VALVE ASSEMBLY INSTALLA-
TION:
12.1 Reverse steps and procedures outlined in section
9. See notes below.
12.2 Keep trigger and valve assembly (item 10) and
handle (item 4) clean from any dust or dirt.
12.3 Make sure trigger and valve assembly is
installed as a set. Do not mix old and new parts.
12.4 Apply a light coat of of Jarvis 1315 White
Grease to trigger and trigger valve sleeve before
installing into handle.
12.5 Make sure o--rings (item 9) are set properly in
grooves of trigger valve sleeve when installing
into handle.
12.5.1 Apply a light coat of grease around o--rings
to help keep them in place and to help slide
trigger valve sleeve into handle, if neces-
sary.
12.6 Use Jarvis special tool (part number 8330024)
to align trigger valve sleeve into handle (item 4).
See note below.
12.6.1 Align air passage holes (facing upward) of
trigger valve sleeve with air passage holes of
handle. Make sure indent (spot face) in
valve sleeve aligns with set screw (item 7).
Table of contents
Other Jarvis Power Tools manuals
Popular Power Tools manuals by other brands
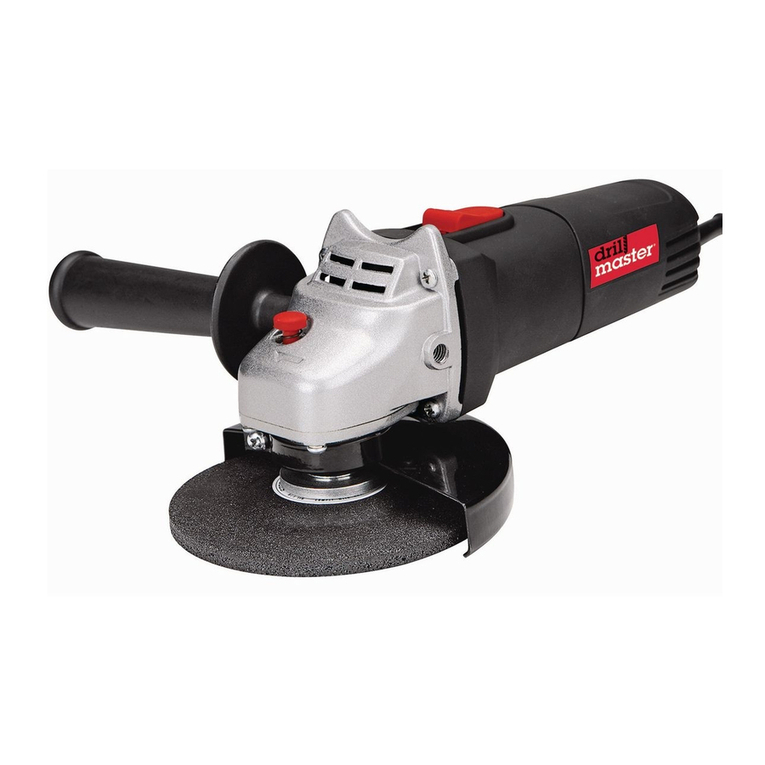
Drill Master
Drill Master 95578 Assembly and operating instructions
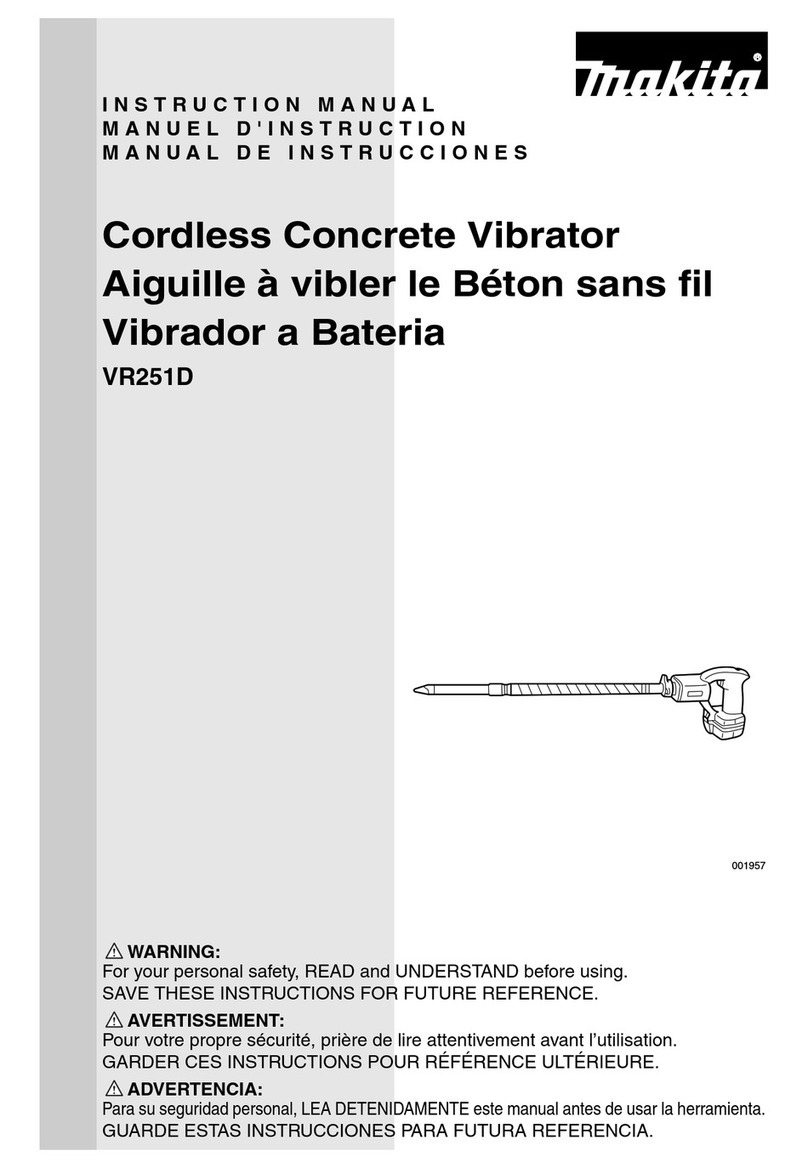
Makita
Makita VR251D instruction manual
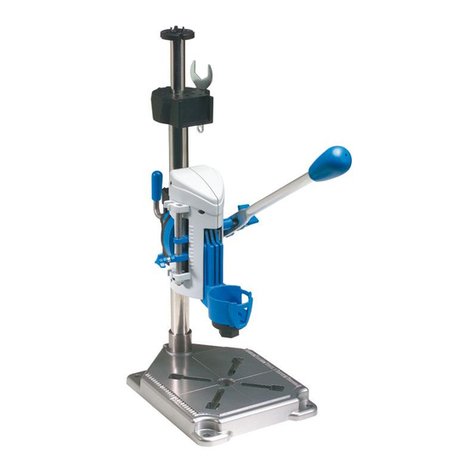
Dremel
Dremel WorkStation 220 Original instructions
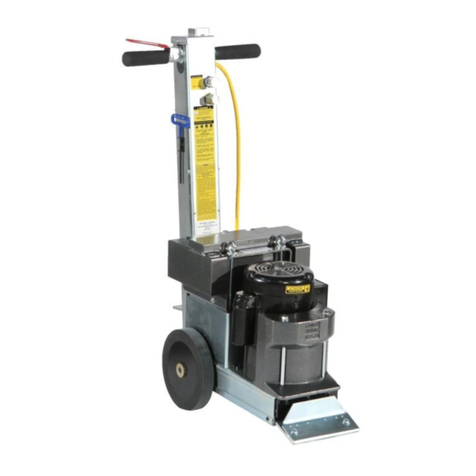
National Flooring Equipment
National Flooring Equipment 5280 Series instruction manual
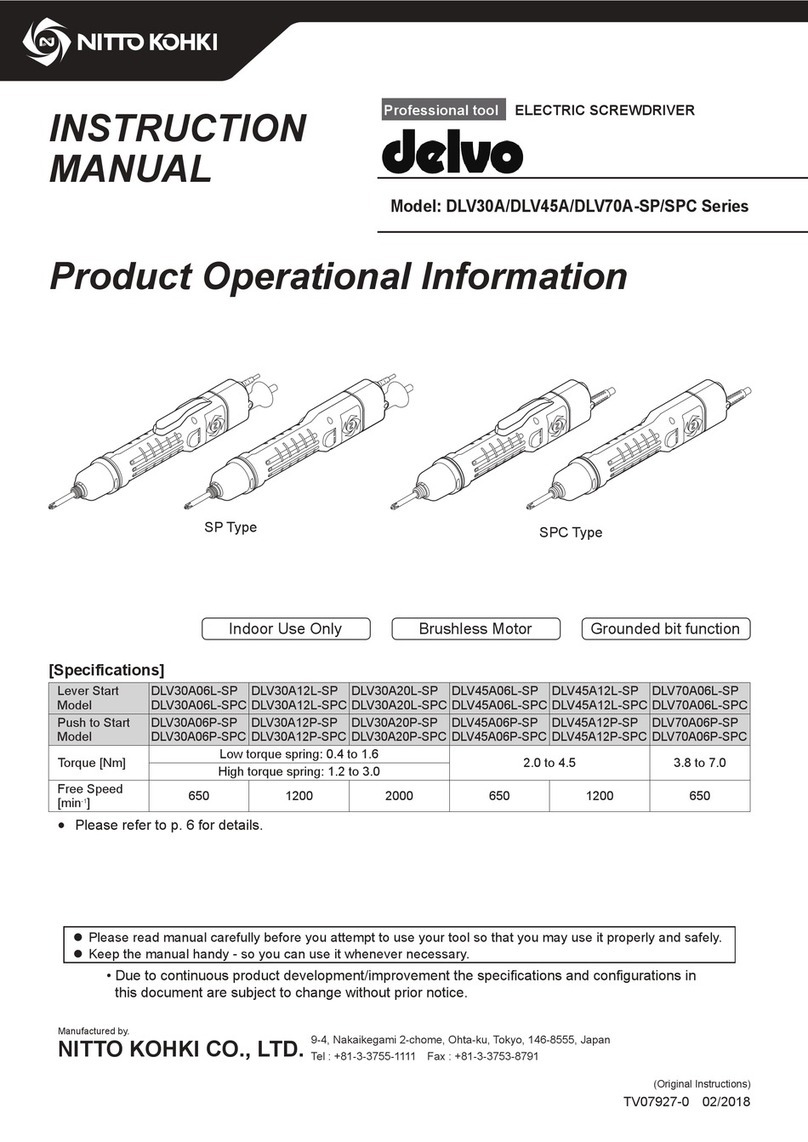
Nitto Kohki
Nitto Kohki DLV30A06L-SP instruction manual
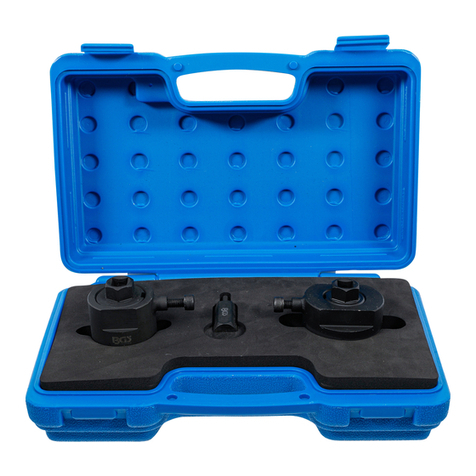
BGS technic
BGS technic 8759 instruction manual