Kato Engineering Standard AC Generator User manual

Page 1 Copyright © 2012 Kato Engineering, Inc. All rights reserved
Instruction Manual
Installation • Operation • Maintenance
Standard AC generator
Single or two-bearing
Drive-end air discharge
Publication 350-01001-00, 01/19/2016
Please read this manual and all included manuals in its entirety
before unpacking, installing, and operating your generator. If your
manual came on a CD, read all the files included on the CD.
Kato EngineeringP.O. Box 8447Mankato, MN USA 56002-8447Tel: 507-625-4011
Copyright © 2015 Kato Engineering, Inc. All rights reserved

Page 2
Copyright © 2012 Kato Engineering, Inc. All rights reserved
Table of Contents
Introduction.........................................................4
Foreword............................................................................4
Safety instructions..............................................................4
Ratings/description............................................................4
Construction and Operating Principles............5
Stator................................................................................. 5
Rotor..................................................................................5
Bearings.............................................................................5
Connection boxes..............................................................6
Excitation system...............................................................6
Optional PMG system........................................................7
Other options.....................................................................7
Installation...........................................................8
Receiving inspection..........................................................8
Unpacking and moving......................................................8
Location.............................................................................8
Base design.......................................................................8
Assemble to prime mover, alignment................................ 8
Two-bearing close-coupled alignment.....................9
Two-bearing alignment...........................................14
Single-bearing alignment........................................18
Foot deflection.................................................................23
Doweling..........................................................................23
Electrical connections......................................................23
Space heaters................................................................. 23
Inspection before startup.................................................23
Operation...........................................................25
Initial startup: generators w/auto & manual control..........25
Initial startup: generators w/auto control only...................25
Restoring residual magnetism/field flashing.....................26
Continuous operation.......................................................27
Idling.................................................................................27
Parallel operation..............................................................27
Notice: Because of rapid changes in
designs and processes and the variability of
Kato Engineering’s products, information in
this manual must not be regarded as binding
and is subject to change without notice.
The image on the front cover is representa-
tive only. Several variations are available
within the range of generators covered
within this manual.

Page 3 Copyright © 2012 Kato Engineering, Inc. All rights reserved
Maintenance.......................................................30
Schedules........................................................................30
Maintenance procedures.................................................32
Visual inspection methods of windings..................33
Cleaning................................................................ 35
Insulation resistance tests at low voltage..............35
Dry out procedures............................................... 36
Bearing lubrication................................................ 36
Rectifier tests........................................................ 37
Disassembly.....................................................................39
Overall disassembly...............................................39
Exciter armature and PMG removal......................40
Bearing removal.................................................... 42
Assembly..........................................................................43
Bearing installation................................................43
Overall assembly...................................................43
Exciter armature and PMG installation..................43
Storage............................................................................45
Torque chart..................................................46-47
Troubleshooting Guide.....................................48
Main part location.............................................................51
List of equipment required for installation
and maintenance............................................................. 52

Page 4
Copyright © 2012 Kato Engineering, Inc. All rights reserved
Introduction
Foreword
This manual contains instructions for installing, operating and
maintaining Kato Engineering AC brushless revolving field generators.
These generators are manufactured in many sizes and ratings and with
various options.
Lubrication information, electrical connection drawings, dimensional
drawings and parts listings for your model are contained in the manual
package as supplementary information and are the specific source of
information for making connections and ordering replacement parts.
Information about optional components of your generator may also be
contained as a supplement.
Please read this manual and all included manuals in its entirety before
unpacking, installing, and operating your generator. If your manual
came on a CD, read all the files included on the CD.
Safety instructions
In order to prevent injury or equipment damage, everyone involved in
installation, operating and maintenance of the generator described in this
manual must be qualified and trained in the current safety standards that
govern his or her work.
While “common-sense” prevention of injury or equipment damage
cannot be completely defined by any manual (nor built into any piece of
equipment), the following paragraphs define warnings, cautions, Notices
and Important as they are used in this manual:
WARNING: Warnings identify an installation, operating or
maintenance procedure, practice, condition, or statement that, if not
strictly followed, could result in death or serious injury to personnel.
CAUTION: Cautions identify a hazardous situation that if not
avoided could result in minor or moderate injury.
NOTICE: Notices identify an installation, operating or maintenance
procedure, practice, condition, or statement that, if not strictly followed,
could result in destruction of or damage to equipment or serious
impairment of system operation.
IMPORTANT: Important messages are informational only.
Ratings/description
Nameplates, which are located on the side of the generator, include
serial and model number as well as rating information and bearing and
lubrication information.
NOTICE: For specific lubrication
instructions, always refer to the bearing
lubrication sheet that came with your
manual or the lube plate on the generator.
Unauthorized lubricants may result in a
bearing failure.
WARNING: Shock hazard - Do not
service the generator or other electrical
machinery without de-energizing and
tagging the circuits as out of service.
Dangerous voltages are present, which
could cause serious or fatal shock.

Page 5 Copyright © 2012 Kato Engineering, Inc. All rights reserved
Construction and Operating Principles
Stator
The stator consists of the supporting frame, core, and armature windings.
The stator core is made from laminations, thin sheets of electrical steel,
which are stacked and held in place by steel endrings and support
bars. The rings and bars are welded to or are part of the steel frame.
Base mounting plates are welded to the bottom of the frame. The base
mounting plates allow the assembly to be mounted on the genset base.
The windings (coils) are constructed of layered and insulated copper
wire. The coils are inserted in the core slots, connected together, and
the entire assembly is vacuum-pressure impregnated with resin. Stator
leads terminate in standard connection lug or strap terminals for ease of
connection to the load.
Rotor
The main rotor assembly is the revolving field. It consists of windings
in a core, which is in turn mounted on a steel shaft. The exciter armature
assembly and optional permanent magnet generator (PMG) rotor are also
mounted on the shaft as are the fan(s) and other optional accessories.
The core consists of laminations, thin sheets of electrical steel, which are
stacked together. The core makes the salient poles (four, six, eight or 10).
With six or more poles, the poles are typically attached to a center hub.
The rotor windings consists of insulated magnet wire wound around
each pole. V-blocks between each pole keep the rotor windings in place.
Damper windings consist of copper or aluminum rods that are inserted
through each pole surface and are brazed to copper or aluminum damper
end plates at each end of the lamination stack. The end plates are brazed
to adjacent poles to form a continuous damper winding. The ends of the
windings are supported with bars or aluminum pole shoes. The rotor
either has resin applied during the winding process or is vacuum-pressure
impregnated with resin.
The shaft is made from high-strength rolled or forged steel and machined
to accommodate all the rotating generator components. Keyways in
the shaft ensure precise positioning of the rotor, exciter armature, and
optional PMG rotor as well as drive couplings. On the exciter side, the
shaft has a slot or hole in its centerline for running the revolving field
leads to the rectifier.
Bearings
The generator may contain either one or two bearings. Bearings are
typically ball or roller type and are regreaseable bearings, which contain
fill and drain ports for easy lubrication. Sleeve bearings are optional
on some designs. A supplementary instruction will be included in
NOTICE: For specific lubrication
instructions, always refer to the bearing
lubrication sheet that came with your
manual or the lube plate on the generator.
Unauthorized lubricants may result in a
bearing failure.
NOTICE: Generators equipped with sleeve
oil bearings must have oil added to the
bearing prior to rotation. Failure to comply
will result in bearing damage. See the
bearing manual.

Page 6
Copyright © 2012 Kato Engineering, Inc. All rights reserved
the manual package for sleeve bearings if they are applicable to this
generator. Some smaller generators may use heavy duty double shielded
bearings, which are typically used on smaller generators and are greased
for life.
Connection boxes
The main lead connection box houses the load lead terminals. In
addition, the generator may have auxiliary connection boxes for
connecting temperature detector outputs, space heater connectors, and
sensing outputs.
Excitation system
The excitation system consists of the exciter stator assembly and the
exciter armature assembly:
The exciter stator assembly consists of windings in a core. The core is
made from steel laminations that are stacked and welded together. The
main exciter stator coils are placed in slots in the core and form alternate
north and south poles. The entire assembly is either mounted to the end
bracket or mounted in a frame, which is mounted to the end bracket. The
stator is a stationary field, which is powered by the voltage regulator.
The assembly consists of two subassemblies: the exciter armature and
the rotating rectifier. The exciter armature assembly contains steel
laminations that are stacked and keyed on the shaft or on to a sleeve,
which is keyed to the generator shaft. A three-phase winding is inserted
into slots in the laminations. The coils are held in place by insulating
wedges. The coil extensions are braced with tape. Output leads from the
winding are connected to the rotating rectifier assembly.
The rotating rectifier is a three-phase full wave bridge rectifier,
converting the AC from the exciter armature to DC, which is transferred
to the revolving field windings. Two aluminum steel plates, each
containing three rotating rectifier diodes, are mounted on each side of
an insulating hub to form the negative and positive terminals. The plates
also act as heat sinks for the diodes.
Excitation system functional overview: Exciter field control is
established by the strength of the exciter field current developed by
the voltage regulator system. The DC voltage and current levels of the
exciter field signal from the voltage regulator varies depending upon the
generator output voltage and the loading of the output lines (see Figure
1).

Page 7 Copyright © 2012 Kato Engineering, Inc. All rights reserved
Optional PMG system
The permanent magnet generator (PMG) system consists of the PMG
stator and PMG rotor:
The PMG stator is a stationary armature and is located within the stator
assembly that also contains the exciter stator or is a separate stator
mounted next to the exciter stator. The PMG stator consists of steel
laminations. The laminations are held in place by steel compression rings
and are welded to the frame bars of the exciter-PMG frame. The PMG
windings are placed in slots in the laminations. Insulating wedges are
inserted at the top of each slot to hold the coils in position.
The PMG rotor consists of rectangular permanent magnets and cast pole
tips secured to a steel hub with nonmagnetic stainless steel bolts. The
PMG rotor is keyed to the shaft and secured with a nut and lock washer.
PMG system overview: The PMG system functions as a pilot exciter,
providing power to the automatic voltage regulator power supply. The
PMG is an AC generator that uses permanent magnets in the rotor instead
of electromagnets to provide the magnetic field (see Figure 1).
Other options
Other options include, but are not limited to, space heaters, filters, and
temperature sensing devices.
Figure 1: Overview of excitation system
(with an optional PMG)
Output leads
Voltage
regulator
Exciter stator
(field)
Main stator
(armature)
Shaft
Main rotor (DC)
Rectifier
Exciter
armature (AC)
PMG stator
(armature)
PMG rotor
(field)
Prime mover
Power input

Page 8
Copyright © 2012 Kato Engineering, Inc. All rights reserved
Installation
Receiving inspection
Before accepting a shipment, examine the packaging for any sign of
damage that might have occurred during transit. Report any damage to
the transportation company and Kato Engineering.
Unpacking and moving
If the generator is received during cold weather, reduce condensation on
cold surfaces and failure due to wet windings by allowing the generator
to reach room temperature before removing the protective packing.
Unpack the generator carefully to avoid scratching painted surfaces. Do
not remove the protecting lubricant from the shaft end or drive plates.
Inspect for loosely mounted components and the presence of moisture.
Inspect to make certain foreign material, such as crating nails, loose
bolts or packing material, which may have fallen into the machine during
unpacking, is removed. If damage is Noticed, determine the extent of
damage and immediately notify the transportation company claims office
and Kato Engineering. Be sure to give complete and accurate details
when reporting damage.
Move the generator by attaching an overhead hoist to the eyebolts
installed on the generator frame or by lifting the generator from
underneath the skid with a forklift.
Single-bearing generators are shipped with the exciter rotor assembly
removed from the shaft and a support mounted across the drive discs to
support the rotor.
Location
Install the generator in an area so it complies with all local and industrial
regulations. Locate it in a clean, dry, well-vented area or area that is
suitable for the generator enclosure. Make sure it is easily accessible for
inspection and maintenance.
Check winding insulation resistance before placing the generator in
operation (see the maintenance section).
Protect generators operating intermittently in very damp locations with
space heaters. Slowly warm generators placed in operation after being
subjected to very low temperatures to prevent excessive condensation.
Base design
The type of base to be used will depend upon the nature of the
installation site. However, the generator base must be rigid, level, and
free from vibration. Mounting holes must be larger than the fasteners to
allow for alignment.
WARNING: Electric shocks can occur
from faulty ground connections on portable
electrical equipment and failure to ground
stationary equipment which may result in
death or injury. Be alert at all times when
installing, operating and maintaining the
generator.Avoid contact with the uninsulated
metal parts of the generator. Test all portable
devices frequently to prove that a solid
electrical circuit exits from the metal frame
though the grounding conductor, in the
electrical cord, to the grounding contact in
the attachment plug. Do not use electrical
equipment with frayed, burned or damaged
cords.
Always take extreme care when moving the
generator. Be careful to not strike objects or
personnel.
WARNING: Apply lifting force to
structural points specifically provided for
lifting. Do not use the enclosure lifting holes
to lift the whole unit. Use lifting means
adequate for the weight. Observe lifting
notices attached to the generator. Failure
to observe these instructions can result in
injury, death and damage to the generator.
NOTICE: Do not attempt to transport a
single-bearing generator without maintaining
proper rotor support and with the exciter
rotor assembly removed. Failure to observe
this warning can result in equipment
damage.
NOTICE: Blocking or restriction of normal air
flow into or out of the generator may cause
damage to the electrical windings.

Page 9 Copyright © 2012 Kato Engineering, Inc. All rights reserved
Assemble to prime mover, alignment
Follow either the two-bearing alignment (if your generator model has
two bearings but no adapter to bolt to an engine flywheel housing),
two-bearing close-coupled alignment (if your generator model has two
bearings and an adapter for bolting to a flywheel housing), or single-
bearing alignment (if your generator has one bearing and drive plates).
Consult the factory for belt or gear drive alignment).
Two-bearing close-coupled alignment
Check the engine flywheel housing pilot’s radial and face runout by
mounting a dial indicator and measuring the flywheel to the flywheel
housing as shown in Figure 2. See Table 1 for maximum allowable
runout.
NOTICES:
Mounting of the indicators must allow
complete rotation of the prime mover.
Use dial indicators that are rigid so indicator
sag won’t be a factor. Using the shortest
offset distance of the indicator bracket will
reduce the effects of indicator droop or sag.
During alignment, you may also need to
compensate for engine expansion due to
heating. Generator expansion is generally
not considered a factor.
If the genset is moved to a different
location, check alignment before startup.
WARNING: Do not pry on the
generator fan blades. The blades can
weaken, which could result in serious injury
or death from flying debris.
Figure 2: Flywheel housing check
Shaft
Flywheel
Flywheel housing
Dial indicator
pointer for radial
runout
Dial indicator pointer for
face runout

Page 10
Copyright © 2012 Kato Engineering, Inc. All rights reserved
Check the engine flywheel’s radial and face runout by mounting a dial
indicator and measuring the flywheel housing to the flywheel as shown
in Figure 3. The maximum allowable flywheel runout is .0005” per inch
of radius with a maximum of .010”.
NOTICE: TIR = Total indicated runout
NOTICE: Compensation for engine
thermal growth must be taken into
account on this measurement.
SAE housing
number
6
5
4
3
2
1
0.5
0
00
10.500
12.375
14.250
16.125
17.625
20.125
23.000
25.500
31.000
Housing inside
dia.
Table 1: Maximum allowable
flywheel housing runout (inches)
Figure 3: Flywheel check
Shaft
Flywheel
Flywheel housing
Dial indicator pointer
for radial runout
Dial indicator
pointer for face
runout
0.002
0.003
0.003
0.004
0.004
0.005
0.005
0.006
0.007
Allowable
runout (TIR)

Page 11 Copyright © 2012 Kato Engineering, Inc. All rights reserved
Check the generator adapter’s radial and face runout by mounting a
dial indicator on the generator shaft or coupling as shown in Figure 4.
The maximum radial and face runout on the generator adaptor must not
exceed 0.010 inch.
NOTICES: Mounting of the indicators must
allow complete rotation of the prime mover.
Use dial indicators that are rigid so indicator
sag won’t be a factor. Using the shortest
offset distance of the indicator bracket will
reduce the effects of indicator droop or sag.
During alignment, you may also need to
compensate for engine expansion due to
heating. Generator expansion is generally
not considered a factor.
If the genset is moved to a different
location, check alignment before startup.
WARNING: Do not pry on the
generator fan blades. Blades can weaken
which could result in serious injury or death
from flying debris.
NOTICE: Generators equipped with sleeve
oil bearings must have oil added to the
bearing prior to rotation. Failure to comply
will result in bearing damage. See the
bearing manual.
Figure 4: Generator adapter check
Shaft
Adapter
Dial indicator pointer
for radial runout
Dial indicator
pointer for face
runout
Check the generator coupling’s radial and face runout by mounting
a dial indicator to the generator adapter as shown in Figure 5. The
maximum radial and face runout on the coupling must not exceed 0.003
inch.
Figure 5: Generator coupling check
Shaft
Adapter
Dial indicator
pointer for radial
runout
Dial indicator
pointer for face
runout

Page 12
Copyright © 2012 Kato Engineering, Inc. All rights reserved
Install the portion of the coupling that fits into the engine flywheel
following the manufacturer’s recommended procedures and in accor-
dance with engine manufacturer’s specifications. Check the coupling’s
radial and face runout by mounting a dial indicator to the engine
flywheel housing as shown in Figure 6. The maximum radial and face
runout on the coupling must not exceed 0.004 inch.
Measure and record the engine crank shaft endplay Set the engine
endplay at a position of one half of the measured distance.
Measure the generator endplay. Compare the measured endplay to the
factory recorded endplay located on the Generator Warranty/Test Tag.
Once this is verified, thrust the generator shaft all the way to the engine,
then back off that location .020”, or .508mm. This will allow for the
thermal growth of the shaft.
Mount the generator on the skid, and move the generator to within 0.010
inch of the engine. Place two 0.010-inch shims in the horizontal
(9 o’clock and 3 o’clock) positions between the generator adapter
and the engine flywheel housing. Raising the rear, exciter end of the
generator as necessary, place two 0.010-inch shims in the vertical (6
o’clock and 12 o’clock) positions between the generator adapter and
the engine flywheel housing. This will give a good starting point for
alignment. Remove the vertical shims at this time. (If necessary, mark
holes to be drilled on the base, and remove the generator at this time.)
Mount a dial indicator on the generator shaft or half coupling to the
flywheel radial surface for parallel alignment as shown in Figure 7.
IMPORTANT: The maximum allowable
flywheel runout is .0005” per inch of radius
with a maximum of .010”.
Shaft
Flywheel
Flywheel housing
Dial indicator pointer
for radial runout
Dial indicator
pointer for face
runout
Figure 6: Engine coupling check

Page 13 Copyright © 2012 Kato Engineering, Inc. All rights reserved
Mount a dial indicator on the flywheel coupling to the face of the
generator half coupling for angular alignment as shown in Figure 7.
Align the engine by rotating the prime mover in 90-degree increments
and measuring total indicator runout. Tighten the generator to the base
before taking each set of readings. Raise or lower the generator by
adding or removing shims under the machined feet.
Following the final generator adjustment and runout check, remove
the horizontal shims from the adaptor flywheel housing, and move the
generator all the way to the adaptor. Then tighten the fasteners.
Recheck alignment. Make sure angularity (face) total indicated runout
does not exceed 0.005 inch per inch of generator coupling diameter and
parallel (radial) total indicated runout does not exceed 0.005” TIR.
Torque the fasteners to the value shown in Table 3.
Shaft
Flywheel housing
Dial indicator pointer
for angular alignment
Dial indicator pointer
for parallel alignment
Flywheel
Figure 7: Alignment check
IMPORTANT: Clearances between the
adaptor pilot and the flywheel housing
recess are designed to meet the tolerance
of 0.001 to 0.015 inches.

Page 14
Copyright © 2012 Kato Engineering, Inc. All rights reserved
Install the portion of the coupling that fits into the engine flywheel
following the manufacturer’s recommended procedures and in accor-
dance with engine manufacturer’s specifications. Check the coupling’s
radial and face runout by mounting a dial indicator to the engine
flywheel housing as shown in Figure 9. The maximum radial and face
runout on the coupling must not exceed 0.004 inch. Measure and record
the engine crank shaft endplay Set the engine endplay at a position of
one half of the measured distance.
Measure the generator endplay. Compare the measured endplay to the
factory recorded endplay located on the Generator Warranty/Test Tag.
Once this is verified, thrust the generator shaft all the way to the engine,
then back off that location .020”, or .508mm. This will allow for the
thermal growth of the shaft.
If the generator has “floating bearings”, align the face of the outer seat
with the groove in the shaft (electrical center).
Two-bearing alignment
Follow the tolerances specified by the coupling manufacturer when they
are less than described in this manual.
Use shims, if necessary, between the mounting pad and the base to
properly level and align the generator to the prime mover.
Install the coupling(s) on the generator and engine drive shafts in
accordance with coupling manufacturer installation procedures. Check
the generator coupling’s radial and face runout by mounting a dial
indicator to the generator adapter as shown in Figure 8. The maximum
radial and face runout on the coupling must not exceed 0.003 inch.
Figure 8: Generator coupling check
Shaft
Adapter
Dial indicator
pointer for radial
runout
Dial indicator
pointer for face
runout

Page 15 Copyright © 2012 Kato Engineering, Inc. All rights reserved
Use a straight edge and a thickness gauge for rough alignment as shown
in Figure 10. Check for angular and parallel alignment as follows:
Figure 10: Rough alignment
Straight edge
Thickness gauge
Shaft
Flywheel
Flywheel housing
Dial indicator pointer
for radial runout
Dial indicator
pointer for face
runout
Figure 9: Engine coupling check

Page 16
Copyright © 2012 Kato Engineering, Inc. All rights reserved
Angular alignment: Fasten a dial indicator to one of the coupling halves,
and scribe the position of the dial button on the face of the opposite
coupling half as shown in Figure 11. Rotate both shafts simultaneously,
keeping the finger or button on the indicator at the reference mark on the
coupling hub. Notice the reading on the indicator dial at each one quarter
revolution.
A variation of readings at different positions will indicate how the
machine needs to be adjusted to obtain a maximum misalignment of
0.005 inch for each inch of the coupling hub’s radius, total indicator
runout. Place or remove slotted shims from under the front or rear engine
or generator mounting pads and/or shift the front or back half of one
component from side to side until the components are properly aligned.
Tighten the mounting bolts, and recheck alignment.
Parallel alignment: Fasten a dial indicator to one of the coupling halves,
and scribe the position of the dial button on the top of the opposite
coupling half as shown in Figure 12. Rotate both shafts simultaneously,
keeping the finger or button on the indicator at the reference mark on the
coupling hub. Notice the reading on the indicator dial at each one quarter
revolution. A variation of readings at different positions will indicate how
the machine needs to be adjusted to obtain a maximum misalignment of
0.005 TIR. Compensation for engine thermal growth must be taken into
account on this measurement. Place or remove slotted shims from under
all of the engine or generator mounting pads and/or shift one component
from side to side until the components are properly aligned. Tighten the
mounting bolts, and recheck alignment.
Dial indicator
Figure 11: Angular alignment

Page 17 Copyright © 2012 Kato Engineering, Inc. All rights reserved
Dial indicator
Figure 12: Parallel alignment

Page 18
Copyright © 2012 Kato Engineering, Inc. All rights reserved
Single-bearing alignment
Before assembling the generator to the prime mover, remove the exciter
cover and adapter cover. Remove the blocking holding the drive discs to
the adapter. Also make sure the generator bearing end clearance is not
less than the total engine crankshaft axial movement plus 1/16 inch. The
generator is shipped from the factory with 1/8-inch minimum bearing
end clearance. (This dimension is recorded on the Factory Recorded
Dimensions sheet, packaged with the generator.)
Measure the distance from the end of the exciter shaft extension to the
bearing housing on the endbracket (dimension A in Figure 13). This
dimension is recorded on the Factory Recorded Dimensions sheet,
packaged with the generator. If the dimensions do not match, move the
rotor axially relative to the stator until the dimensions are equal.
Check the engine flywheel housing pilots’s radial and face runout by
mounting a dial indicator and measuring the flywheel to the flywheel
housing as shown in Figure 5. See Table 1 for maximum allowable
runout.
Check the engine flywheel’s radial and face runout by mounting a dial
indicator and measuring the flywheel housing to the flywheel as shown
in Figure 3. See Table 2 for maximum allowable runout.
Measure the generator drive plate diameter (dimension S of Figure 14)
and flywheel bore diameter (dimension B of Figure 15). Drive plate
diameter must not be greater than the flywheel bore diameter. Also check
to make sure the hole centers match (dimension W of Figure 14 and
dimension C of Figure 15).
NOTICES: Mounting of the indicators must
allow complete rotation of the prime mover.
Use dial indicators that are rigid so indicator
sag won’t be a factor. Using the shortest
offset distance of the indicator bracket will
reduce the effects of indicator droop or sag.
During alignment, you may also need to
compensate for engine expansion due to
heating.
If the genset is moved to a different
location, check alignment before startup.
WARNING: Do not pry on the
generator fan blades. Blades can weaken
which could result in serious injury or death
from flying debris.
Figure 13: Generator coupling check
Bearing
Endbracket
Exciter field
Shaft extension
A

Page 19 Copyright © 2012 Kato Engineering, Inc. All rights reserved
Measure the axial distance from the surface on the generator adapter
to the outside surface on the drive disc coupling plates (dimension Y
in Figure 14). This dimension is recorded on the Factory Recorded
Dimensions sheet, which was packaged with the generator. If the
dimensions do not match, move the rotor axially relative to the stator
until the dimensions are equal.
Measure the axial distance from the machined surface on the engine
flywheel housing the bottom of the flywheel drive disc recess
(dimension G in Figure 15). Make sure the difference between
dimensions Y (of Figure 14) and G are less than 1/32 inch. If G is
more than Y, install additional spacers between the drive discs and the
generator hub. If Y is more than G, remove spacers between the drive
discs and generator hub.
Figure 14: Single bearing generator drive plate
and adaptor
S
Y
WA
Adaptor
Bolt holes
Drive
plates
Fan
Shaft
WARNING: Never grind the OD
of drive discs or attempt to drill out the
holes. If the dive discs do not fit properly,
use different discs or a different flywheel.
The number and thickness of drive discs
are specified for torque requirements. Do
not remove drive discs to compensate
for spacing Drive disc modifications may
result in drive disc failure and debris
ejected from the generator.

Page 20
Copyright © 2012 Kato Engineering, Inc. All rights reserved
Install the generator to the engine. Make sure the drive discs seat in
the recess of the flywheel housing. Secure the generator to the engine
(drive discs to flywheel, adapter to flywheel housing), and the base. Use
lock washers on all bolts. Torque the adapter and drive discs in a criss-
cross pattern to the values in Table 3.
Ensure that the bolts in the flywheel do not bottom out. If they are too
long or cannot be tightened with a socket or box wrench, use 1/4 to 3/8-
inch long spacers inserted in the bolts as shown in Figure 16 to increase
the clearance between the bolt head and the flywheel.
Occasionally, there is insufficient clearance to install the bolts that
fasten the drive discs to the engine flywheel, and the fan will have to be
temporarily moved to accommodate this. This situation will typically
occur with several types of generators:
• With the three-frame units that have an aluminum fan, loosen the fan
hub bolts to move the fan. After installing the drive disc-to-flywheel
bolts, move the fan back so the rotor-side edge is flush with the air
opening and the minimum distance between the windings and the
fan is 3/8 inch. Torque the fan hub bolts to 75 ft-lbs.
• With sheet metal fans with cast hubs that are in turn mounted on the
drive hub, mark the drive hub as closes as possible to the fan hub.
Loosen the two set screws, the fan clamping bolt, and the fan bolts.
Wedge the fan open, and move it out of the way (See Figure 17).
After attaching the drive discs-to-fly wheel bolts, align the fan hub
to the mark to move the fan back to its original position. Ensure
the key is fully in place under the fan hub and positioned so the set
screw will press on the key. Tighten the fan hub clamping bolt and
the set screws. Install the fan bolts and torque them according to
Table 3.
B
C
G
Tapped
bolt holes
Flywheel
Figure 15: SAE flywheel and adapter
Table of contents
Popular Portable Generator manuals by other brands
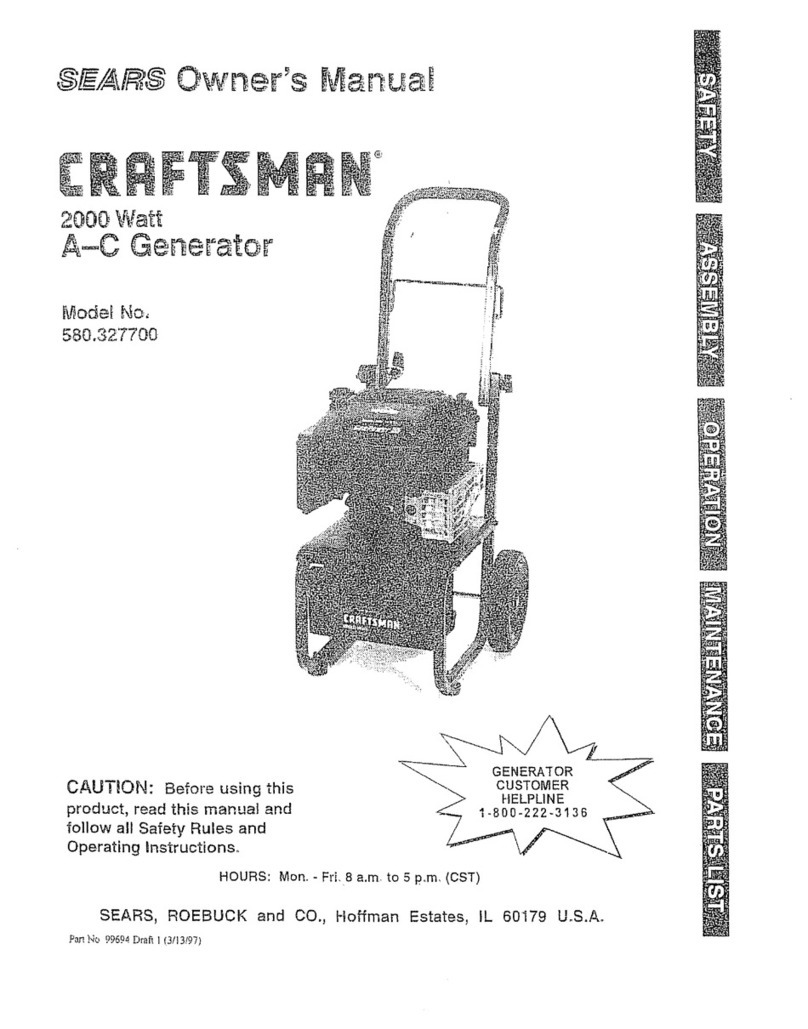
Craftsman
Craftsman 580.327700 owner's manual
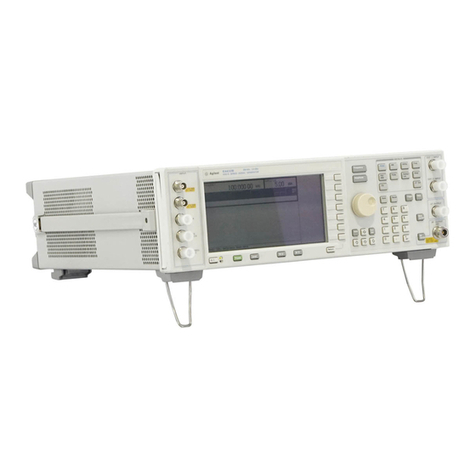
Agilent Technologies
Agilent Technologies ESG-D Series Manual supplement

Woodward
Woodward EGCP-2 Communications manual
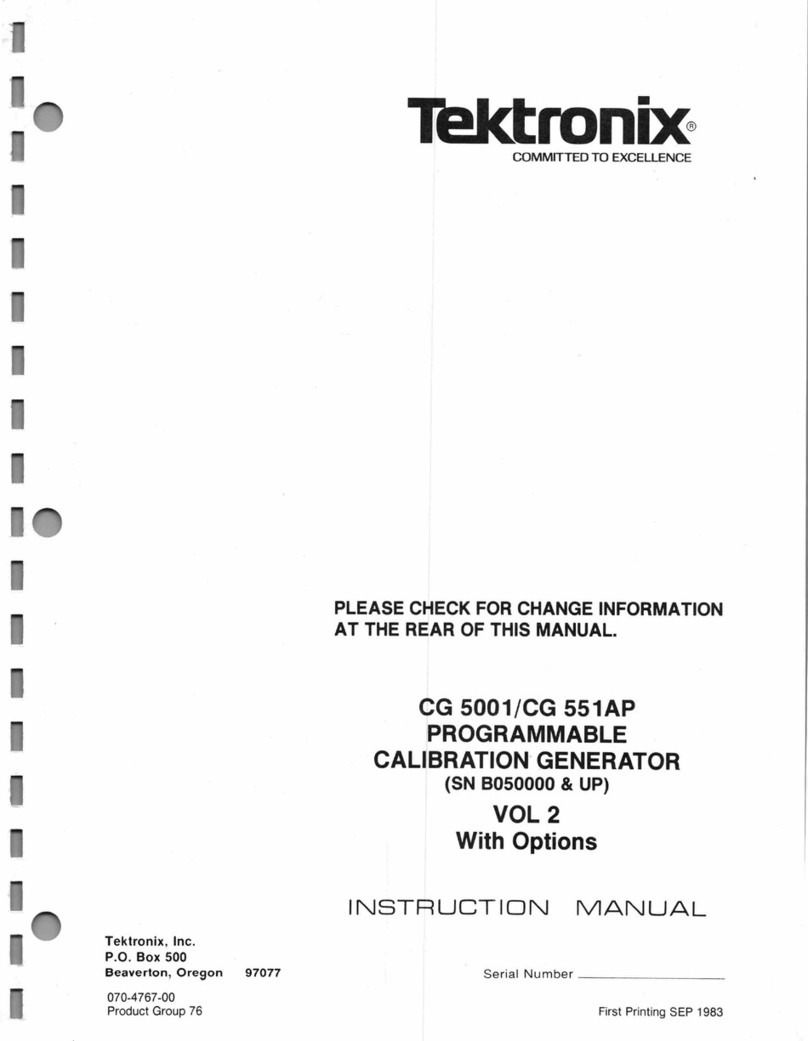
Tektronix
Tektronix CG 5001 instruction manual
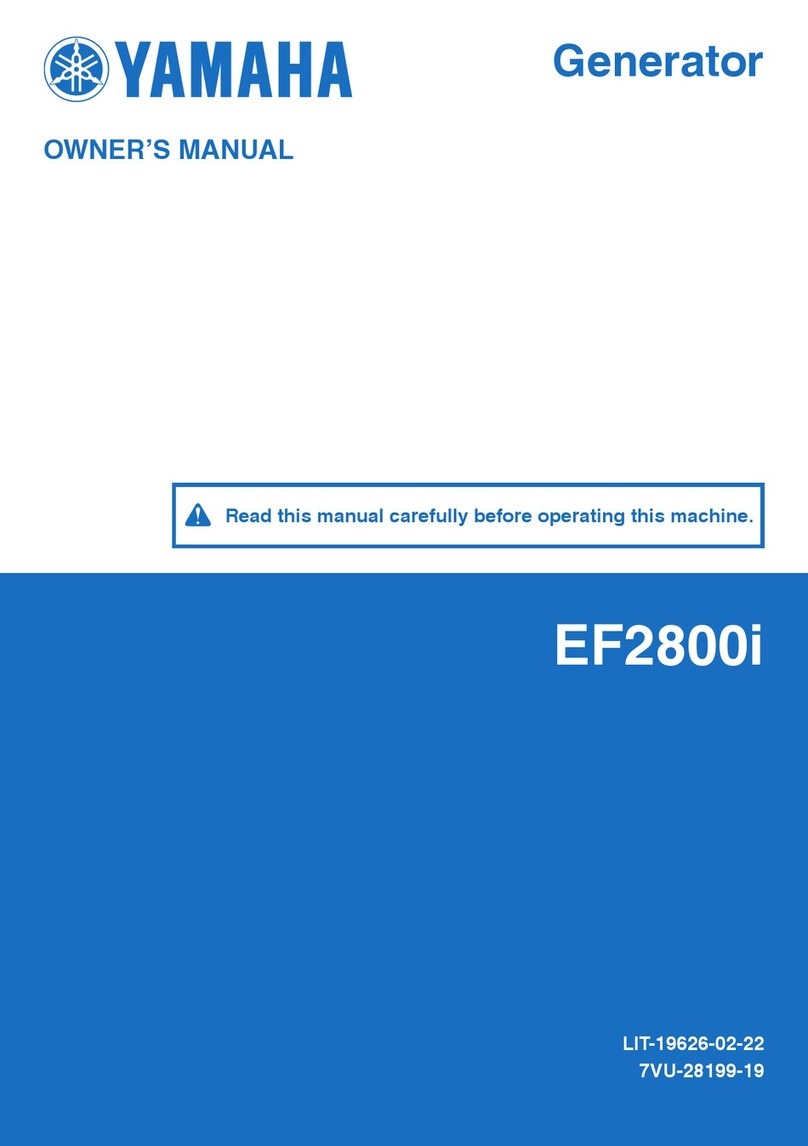
Yamaha
Yamaha EF2800i - Inverter Generator owner's manual
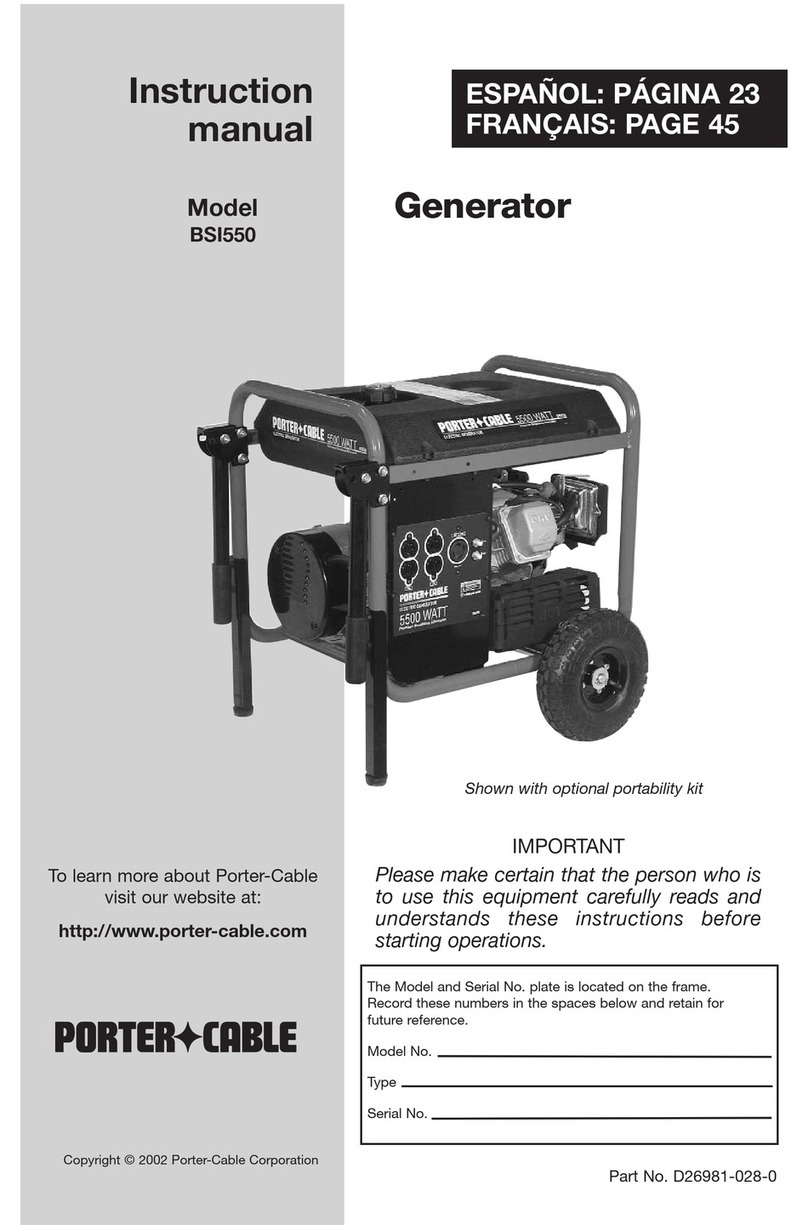
Porter-Cable
Porter-Cable D26981-028-0 instruction manual