Keyvalve KP-28 Installation and operation manual

Operating & Maintenance Manual
Two Way Pneumatic Actuated Globe Control Valve
Model: KP-28

Two Way Pneumatic Actuated Globe Control Valve
Introduction
KP-28, a two way pneumatic actuated globe control valve manufactured under license of
Keyvalve Company Limited. Pneumatic actuator conducts the opening and closing functions of
the valve efficiently. By using an electro-pneumatic (E/P) or pneumatic-pneumatic (P/P) positioner,
it regulates the flow pass through the valve gradually by means of changing its Kv value. Mechanical
switches or inductive sensors are mounted for effective stroke monitoring.
1) Specifications
1.1 Type: Two way globe control valve
1.2 Actuator: Diaphragm pneumatic actuator
1.3 Connection: Flange end
1.4 Trim material: Stainless steel 304
1.5 Plug type: Parabolic, V-form, perforated type with cage, PTFE soft seal plug
1.6 Plug and seat sealing: Metal to metal sealing (hardened), PTFE soft sealing
1.7 Stem sealing: Bellows with graphite packing, pure graphite, PTFE V-ring
1.8 Seat type: Screwed, welded
1.8 Pressure rating: PN10 to PN160, CL150 to CL600
1.9 Body material: Carbon steel SA216WCB, Stainless steel SA351CF8
2) Standards
2.1 Design standard: DIN2501, ASME 16.34, GB12235
2.2 Face to face standard: DIN3202, ASME B16.10, GB/T12221
2.3 Flange standard: EN1092-2, ASME B16.5
2.4 Inspection and testing standard: API598
3) Testing
Pressure rating PN10~PN160
CL150~CL600 Body test pressure 1.5 x PN/CL
Sealing test pressure 1.1 x PN/CL Air supply pressure Max. 6.0 bar
Operating temperature -20~425 ℃(WCB)
-20~500 ℃(CF8) Operating media Water, steam, oil, gas

Two Way Pneumatic Actuated Globe Control Valve
4) Installation
4.1 Before installing the globe control valve, please check the nameplate whether is matching
the requirements of the application.
4.2 Inspect the valve internal parts and sealing surfaces to ensure no blockage or dirt attached.
4.3 Inspect the bolts and nuts to ensure these parts are safely tightened.
4.4 Install the valve in accordance to arrow direction shown on valve body with actuator is
facing upwards.
5) Maintenance
5.1 Globe control valve shall be kept in dry and ventilated area. Sealing parts such as plug, seat
and stem sealing shall be taken extra care.
5.2 Globe control valve which has been kept for long time need to be inspected and
cleaned periodically.
5.3 After installation, globe control valve need to be inspected from time to time. Areas that need
for inspection as below:
a. Sealing surfaces erosion condition (plug and seat).
b. Visual check on foreign particles which might be attached to the plug and seat.
c. Actuator’s shaft movement condition when closing or opening the valve.
5.4 After installation, globe control valve shall go through sealing performance test. The test data
shall be documented for future reference.
6) Repair & Troubleshooting
6.1 This product’s malfunction might be due to two factors:
a. Stem sealing worn out which cause a leakage
b. Valve internal leakage due to erosion at the plug and seat surfaces.
6.2 Repair solution:
6.2.1 Follow sequence to open part no.4, no. 7, then no. 6. After that, part no. 5 can be taken out.
Replace part no. 5, PTFE or pure graphite packing (repair the leakage at stem). Please check
with Keyvalve engineer if bellows with graphite packing replacement is needed..
6.2.2 Dismantle in sequence for part no.3 and no.2 for replacing part no.2 parabolic, V-form,
PTFE soft seal or perforated plug.
6.2.3 Followed by hard alloy seat welding or replacement to part no.1 valve seat ring in order
to repair internal leakage.
Note: Please refer to diagram 7.1 for part number indication.

Two Way Pneumatic Actuated Globe Control Valve
7) Structure Diagram
7.1 Part Indication

Operating & Maintenance Manual
Two Way Electric Actuated Globe Control Valve
Model: KT-28

Two Way Electric Actuated Globe Control Valve
Introduction
KT-28, a two way electric actuated globe control valve manufactured under license of
Keyvalve Company Limited. Electric actuator conducts the opening and closing functions of
the valve efficiently. By using electronic positioner with potentiometer, it regulates the flow
pass through the valve gradually by means of changing its Kv value. Limit switches and
position transmitter are applicable when effective position monitoring is needed.
1) Specifications
1.0 Type: Two way globe control valve
1.1 Actuator: DC motorized electric actuator
1.2 Connection: Flange end
1.3 Trim material: Stainless steel 304
1.4 Plug type: Parabolic, V-form, perforated type with cage, PTFE soft seal plug
1.5 Plug and seat sealing: Metal to metal sealing (hardened), PTFE soft sealing
1.6 Stem sealing: Bellows with graphite packing, pure graphite, PTFE V-ring
1.7 Seat type: Screwed, welded
1.8 Pressure rating: PN10 to PN160, CL150 to CL600
1.9 Body material: Carbon steel SA216WCB, Stainless steel SA351CF8
2) Standards
2.1 Design standard: DIN2501, ASME 16.34, GB12235
2.2 Face to face standard: DIN3202, ASME B16.10, GB/T12221
2.3 Flange standard: EN1092-2, ASME B16.5
2.4 Inspection and testing standard: API598
3) Testing
Pressure rating PN10~PN160
CL150~CL600 Body test pressure 1.5 x PN/CL
Sealing test pressure 1.1 x PN/CL Power supply 24VDC, 110V/220VAC
Operating temperature -20~425 ℃(WCB)
-20~500 ℃(CF8) Operating media Water, steam, oil, gas

Two Way Electric Actuated Globe Control Valve
4) Installation
4.1 Before installing the globe control valve, please check the nameplate whether is matching
the requirements of the application.
4.2 Inspect the valve internal parts and sealing surfaces to ensure no blockage or dirt attached.
4.3 Inspect the bolts and nuts to ensure these parts are safely tightened.
4.4 Install the valve in accordance to arrow direction shown on valve body with actuator is
facing upwards.
5) Maintenance
5.1 Globe control valve shall be kept in dry and ventilated area. Sealing parts such as plug, seat
and stem sealing shall be taken extra care.
5.2 Globe control valve which has been kept for long time need to be inspected and
cleaned periodically.
5.3 After installation, globe control valve need to be inspected from time to time. Areas that need
for inspection as below:
a. Sealing surfaces erosion condition (plug and seat).
b. Visual check on foreign particles which might be attached to the plug and seat.
c. Actuator’s shaft movement condition when closing or opening the valve.
5.4 After installation, globe control valve shall go through sealing performance test. The test data
shall be documented for future reference.
6) Repair & Troubleshooting
6.1 This product’s malfunction might be due to two factors:
a. Stem sealing worn out which cause a leakage
b. Valve internal leakage due to erosion at the plug and seat surfaces.
6.2 Repair solution:
6.2.1 Follow sequence to open part no.4, no. 7, then no. 6. After that, part no. 5 can be taken out.
Replace part no. 5, PTFE or pure graphite packing (repair the leakage at stem). Please check
with Keyvalve engineer if bellows with graphite packing replacement is needed..
6.2.2 Dismantle in sequence for part no.3 and no.2 for replacing part no.2 parabolic, V-form,
PTFE soft seal or perforated plug.
6.2.3 Followed by hard alloy seat welding or replacement to part no.1 valve seat ring in order
to repair internal leakage.
Note: Please refer to diagram 7.1 for part number indication.

Two Way Electric Actuated Globe Control Valve
7) Structure Diagram
7.1 Part Indication

Keyvalve Co., Ltd.
7F, 22-28 Cheung Tat Road, Tsing Yi, Hong Kong.
Tel: +852-39796898 Fax: +852-39745305
Email: enquiry@keyvalveltd.com
Website: www.keyvalveltd.com
Version KT-28-OM/2015-8/EN, subjected to further changes without prior notice.
Copyright by Keyvalve Co., Ltd. All rights reserved.
Popular Control Unit manuals by other brands

Krom Schroder
Krom Schroder LSV operating instructions
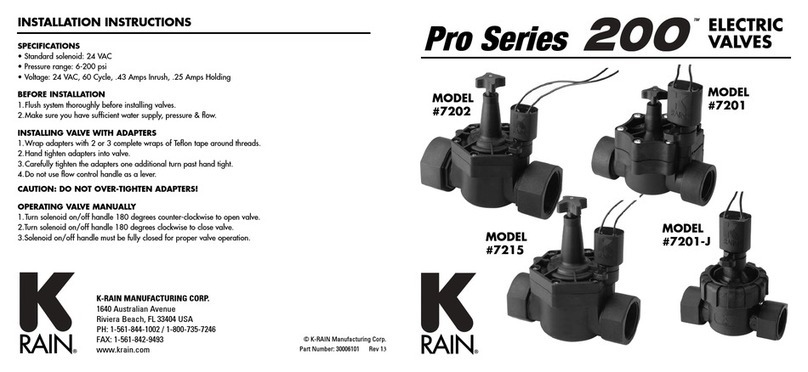
K-Rain
K-Rain 7202 installation instructions
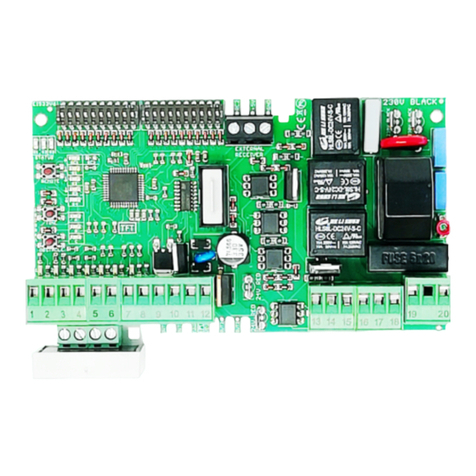
Tecnoautomazione
Tecnoautomazione T182A user manual

ProLite
ProLite E32-A user manual

HydroQuip
HydroQuip Baja Sportub ECO-5/6100 Series troubleshooting guide
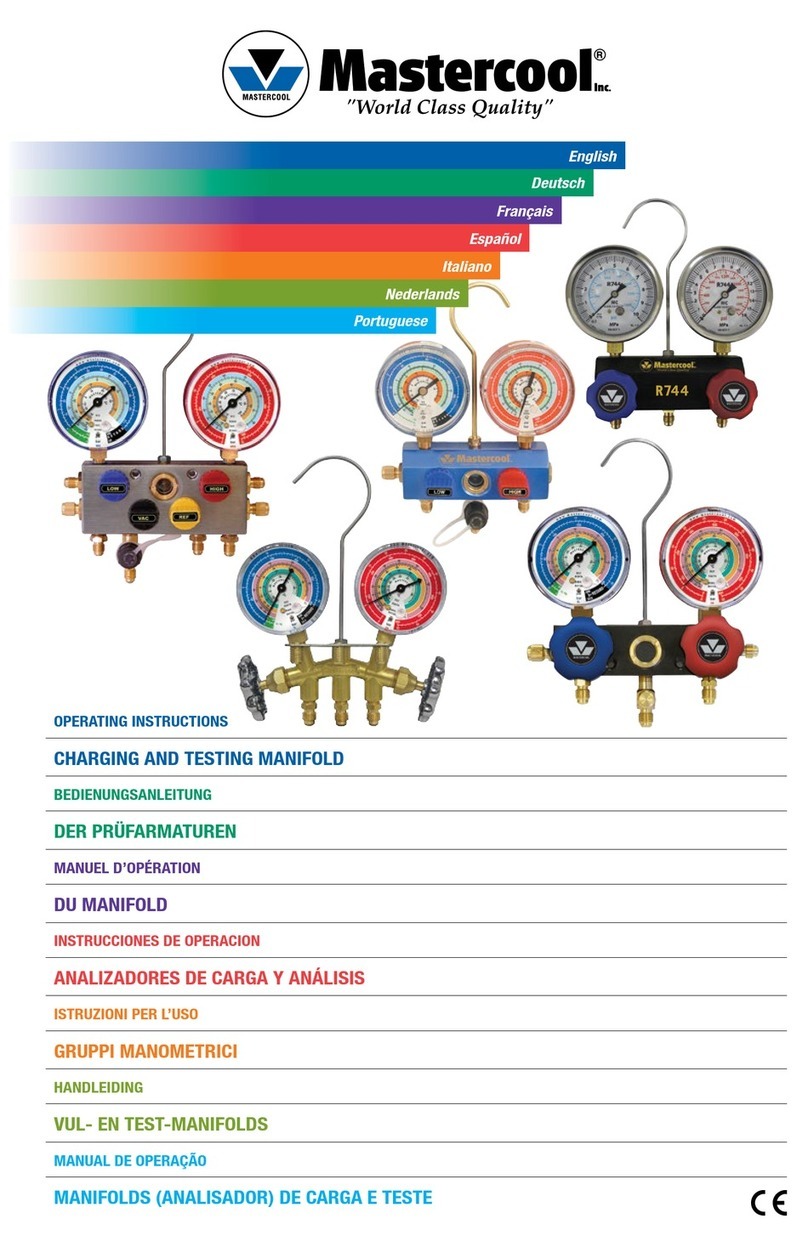
Master cool
Master cool 93103 operating instructions