Kia G6DB-3.3 User manual

Engine Mechanical
System
GENERAL
ENGINE AND TRANSAXLE ASSEMBLY
TIMING SYSTEM
TIMING CHAIN
CYLINDER HEAD ASSEMBLY
ENGINE BLOCK
COOLING SYSTEM
LUBRICATION SYSTEM
INTAKE AND EXHAUST SYSTEM
INTAKE MANIFOLD
EXHAUST MANIFOLD
EXHAUST PIPE
www.CarGarage.ir
www.CarGarage.ir
www.CarGarage.ir

EMA -2 ENGINE MECHANICAL SYSTEM
GENERAL
SPECIFICATION EE6CF939
Specifications
Description G6DB - 3.3 G6DA - 3.8 Limit
General
Type V-type, DOHC
Number of cylinders 6
Bore 92mm (3.6220in) 96mm (3.7795in)
Stroke 83.8mm (3.2992in) 87.0 mm(3.4252in)
Total displacement 3,342cc (203.86cu.in) 3.778cc
(230.55cu.in)
Compression ratio 10.4
Firing order 1-2-3-4-5-6
Valve timing
Opens(ATDC) 14˚10
Intake
Closes(ABDC) 66˚66
Opens(BBDC) 52˚52
Exhaust
Closes(ATDC) 0˚0
Cylinder head
Flatness of gasket surface Less than 0.05mm (0.0019in)
[Less than 0.02mm (0.0008in) / 150x150]
Intake Less than 0.1mm(0.0039in)
[Less than 0.03mm(0.001in)/110x110]
Flatness of manifold
mounting
Exhaust Less than 0.1mm(0.0039in)
[Less than 0.03mm(0.001in)/110x110]
Camshaft
Intake 46.3mm (1.8228in) 46.8mm (1.8425in)LH
Camshaft Exhaust 45.8mm (1.8031in)
Intake 46.3mm (1.8228in) 46.8mm(1.8425in)
Cam height
RH
Camshaft Exhaust 45.8mm (1.8031in)
Intake No.1: 27.964 ~ 27.978mm (1.1009 ~ 1.1015in)
No.2,3,4: 23.954 ~ 23.970mm (0.9430
~ 0.9437in)
Journal outer
diameter LH ,RH
Camshaft
Exhaust No.1: 27.964 ~ 27.978mm
(1.1009 ~ 1.1015in)
No.2,3,4: 23.954 ~ 23.970mm
(0.9430 ~ 0.9437in)
Intake No.1: 0.027 ~ 0.057mm (0.0011 ~ 0.0022in)
No.2,3,4: 0.030~0.067mm(0.0012~0.0026in)
Bearing oil clearance LH ,RH
Camshaft
Exhaust No.1: 0.027 ~ 0.057mm (0.0011 ~ 0.0022in)
No.2,3,4: 0.030~0.067mm(0.0012~0.0026in)
www.CarGarage.ir
www.CarGarage.ir
www.CarGarage.ir

GENERAL EMA -3
Specifications
Description G6DB - 3.3 G6DA - 3.8 Limit
End play →0.02 ~ 0.18mm
(0.0008 ~ 0.0071in)
Valve
Intake 105.27mm(4.1445in)Valve length
Exhaust 105.50mm (4.1535in)
Intake 5.465 ~ 5.480mm (0.2151 ~ 0.2157in)Stem outer diameter
Exhaust 5.458 ~ 5.470mm (0.2149 ~ 0.2153in)
Face angle 45.25 ~ 45.75
Intake 1.56 ~ 1.86mm
(0.06142 ~ 0.07323in)
Thickness of
valvehead(margin)
Exhaust 1.73 ~ 2.03mm
(0.06811 ~ 0.07992in)
Intake 0.020 ~ 0.047mm (0.00078 ~ 0.00185in) 0.07mm
(0.00275in)
Valvestemtovalve
guide clearance
Exhaust 0.030 ~ 0.054mm (0.00118 ~ 0.00212in) 0.09mm
(0.00354in)
Valve guide
Intake 5.500 ~ 5.512mm (0.2165 ~ 0.2170in)Inner diameter
Exhaust 5.500 ~ 5.512mm (0.2165 ~ 0.2170in)
Intake 41.8 ~ 42.2mm (1.6457 ~ 1.6614in)Length
Exhaust 41.8 ~ 42.2mm (1.6457 ~ 1.6614in)
Valve seat
Intake 1.15 ~ 1.45mm (0.05118 ~ 0.05709in)Width of seat contact
Exhaust 1.35 ~ 1.65mm (0.05315 ~ 0.06496in)
Intake 44.75 ~ 45.20
Seat angle
Exhaust 44.75 ~ 45.20
Valve spring
Free length 43.86mm (1.7267in)
19.3±0.8kg/34.0mm (42.7±1.8 lb/1.3386in)
Load 42.3±1.3kg/24.2mm (93.3±2.9 lb/0.9527in)
Out of squareness Less than 1.5
MLA
Intake 34.964 ~ 34.980mm (1.3765 ~ 1.3772in)MLA outer diameter
Exhaust 34.964 ~ 34.980mm (1.3765 ~ 1.3772in)
Intake 35.000 ~ 35.025mm (1.3779 ~ 1.3789in)Cylinder head tappet
bore inner diameter Exhaust 35.000 ~ 35.025mm (1.3779 ~ 1.3789in)
Intake 0.020 ~ 0.061mm (0.0008 ~ 0.0024in) 0.07mm(0.0027in)MLA to tappet bore
clearance Exhaust 0.020 ~ 0.061mm (0.0008 ~ 0.0024in) 0.07mm(0.0027in)
Valve clearance
www.CarGarage.ir
www.CarGarage.ir
www.CarGarage.ir

EMA -4 ENGINE MECHANICAL SYSTEM
Specifications
Description G6DB - 3.3 G6DA - 3.8 Limit
Intake 0.17 ~ 0.23mm (0.0067 ~ 0.0090in) 0.10 ~ 0.30mm
(0.0039 ~ 0.0118in)
Exhaust 0.27 ~ 0.33mm (0.0106 ~ 0.0129in) 0.20 ~ 0.40mm
(0.0078 ~ 0.0157in)
Cylinder block
Cylinder bore 92.00 ~ 92.03mm
(3.6220 ~ 3.6232in) 96.00 ~ 96.03mm
(3.7795 ~ 3.7807in)
Flatness of gasket surface Less than 0.05mm (0.0019in)
[Less than 0.02mm (0.0008in) / 150x150]
Piston
Piston outer diameter 91.96 ~ 92.00mm
(3.6205 ~ 3.6220in) 95.96 ~ 95.99mm
(3.7779 ~ 3.7791in)
Piston to cylinder clearance →0.03 ~ 0.05mm
(0.0012 ~ 0.0020in)
No. 1 ring groove →1.22 ~ 1.24
(0.0480 ~ 0.0488in) 1.26mm (0.0496in)
No. 2 ring groove 1.22 ~ 1.24mm (0.0480 ~ 0.0488in) 1.26mm (0.0496in)
Ring groove width
Oil ring groove 2.01 ~ 2.03mm (0.0791 ~ 0.0799in) 2.05mm (0.0807in)
Piston ring
No. 1 ring →0.03 ~ 0.07mm
(0.0012 ~ 0.0027in) 0.1mm (0.004in)
No. 2 ring 0.03 ~ 0.07mm (0.0012 ~ 0.0027in) 0.1mm (0.004in)
Side clearance
Oil ring 0.06 ~ 0.15mm (0.0024 ~ 0.0059in) 0.2mm (0.008in)
No. 1 ring 0.17 ~ 0.32mm (0.0067 ~ 0.0126in) 0.6mm (0.0236in)
No. 2 ring 0.32 ~ 0.47mm (0.0126 ~ 0.0185in) 0.7mm (0.0275in)
End gap
Oil ring 0.20 ~ 0.70mm (0.0078 ~ 0.0275in) 0.8mm (0.0315in)
Piston pin
Piston pin outer diameter →23.001 ~ 23.006mm
(0.9055 ~ 0.9057in)
Piston pin hole inner diameter →23.016 ~ 23.021mm
(0.9061 ~ 0.9063in)
Piston pin hole clearance →0.01 ~ 0.02mm
(0.0039 ~ 0.0078in)
Connecting rod small end inner diameter 22.974 ~ 22.985mm (0.9045 ~ 0.9049in)
Connecting rod
Connecting rod big end innerdiameter 58.000 ~ 58.018mm(2.2834 ~2.2842in)
Connecting rod bearing oil clearance →0.038 ~ 0.056mm
(0.0015 ~ 0.0022in)
Side clearance 0.1 ~ 0.25mm (0.0039 ~ 0.0098in)
Crankshaft
Main journal outer diameter 68.942 ~ 68.960mm (2.7142 ~ 2.7149in)
Pin journal outer diameter 54.954 ~ 54.972mm (2.1635 ~ 2.1642in)
www.CarGarage.ir
www.CarGarage.ir
www.CarGarage.ir

GENERAL EMA -5
Specifications
Description G6DB - 3.3 G6DA - 3.8 Limit
Main bearing oil clearance 0.022 ~ 0.040mm (0.0008 ~ 0.0016in)
End play0.10 ~ 0.28mm (0.0039 ~ 0.0110in)
Oil pump
Relief valve opening pressure 450 ~ 550kPa
(4.59 ~ 5.61kgf/cm²,65.28 ~ 79.79psi)
Engine oil
Oil quantity (Oil pan) 4.5 ~ 5.5L(4.76 ~ 5.81U.S.qus, 3.96
~ 4.84lmp.qts)
Oil quantity (Oil filter) 0.4L(0.42U.S.qus,0.35lmp.qts)
Oil quantity (Drain and refill) 5.2L(5.49U.S.qus, 4.58lmp.qts)
Oil quality Above SJ or SL
Oil pressure 130kPa(1.32kgf/cm²,18.77psi)
[at 1000rpm,110 C(230 F)]
Cooling system
Cooling method Forced circulation with electrical fan
Coolant quantity 9.0L(9.40U.S.qus,7.83lmp.qts)
Type Wax pellet type
Opening temperature 82±2 C (179.6±35.6 F)
Fully opened
temperature 95 C(203F)
Thermostat
Full lift more than 10mm (0.3937in)
Main valve opening
pressure 93.16 ~ 122.58kpa
(0.95 ~ 1.25kg/cm², 13.51 ~ 17.78psi)
Radiator cap
Vacuum valve opening
pressure 0.98 ~ 4.90 kpa
(0.01 ~ 0.05kg/cm², 0.14 ~ 0.71 psi)
Water temperature sensor
Type Thermister type
20 C(68F) 2.31 ~ 2.59kΩ
Resistance
80 C(176 F) 0.3222 kΩ
www.CarGarage.ir
www.CarGarage.ir
www.CarGarage.ir

EMA -6 ENGINE MECHANICAL SYSTEM
TIGHTENING TORQUE
Item Quantity Nm kgf.m lb.ft
Crankshaft pulley bolt 1284.2 ~ 303.8 29.0 ~ 31.0 209.76 ~ 224.22
Timing chain cover bolt B 17 18.62 ~ 21.56 1.9 ~ 2.2 13.74 ~ 15.91
Timing chain cover bolt C 49.80 ~ 11.76 1.0 ~ 1.2 7.23 ~ 8.68
Timing chain cover bolt D 158.80 ~ 68.80 6.0 ~ 7.0 43.40 ~ 50.63
Timing chain cover bolt E 158.80 ~ 68.80 6.0 ~ 7.0 43.40 ~ 50.63
Timing chain cover bolt F 224.50 ~ 26.46 2.5 ~ 2.7 18.08 ~ 19.53
Timing chain cover bolt G 421.56 ~ 23.52 2.2 ~ 2.4 15.91 ~ 17.36
Timing chain cover bolt H 19.80 ~ 11.76 1.0 ~ 1.2 7.23 ~ 8.68
Timing chain cover bolt I 19.80 ~ 11.76 1.0 ~ 1.2 7.23 ~ 8.68
Timing chain cover bolt J 19.80 ~ 11.76 1.0 ~ 1.2 7.23 ~ 8.68
Cam to cam guide bolt 49.80 ~ 11.76 1.0 ~ 1.2 7.23 ~ 8.68
Timing chain auto tensioner bolt 29.80 ~ 11.76 1.0 ~ 1.2 7.23 ~ 8.68
Timing chain auto tensioner nut 29.80 ~ 11.76 1.0 ~ 1.2 7.23 ~ 8.68
Timing chain guide bolt 419.60 ~ 24.50 2.0 ~ 2.5 14.17 ~ 18.08
Oil pump chain cover bolt 39.80 ~ 11.76 1.0 ~ 1.2 7.23 ~ 8.68
Oil pump chain tensioner bolt 19.80 ~ 11.76 1.0 ~ 1.2 7.23 ~ 8.68
Oil pump chain guide bolt 29.80 ~ 11.76 1.0 ~ 1.2 7.23 ~ 8.68
Oil pump chain sprocket bolt 118.62 ~ 21.56 1.9 ~ 2.2 13.74 ~ 15.91
Lower oil pan bolt 13 9.80 ~ 11.76 1.0 ~ 1.2 7.23 ~ 8.68
Drive belt auto tensioner bolt(M12) 181.4 ~ 85.3 8.3 ~ 8.7 60.0 ~ 62.9
Drive belt auto tensioner bolt(M8) 129.4 ~ 33.3 3.0 ~ 3.4 21.7 ~ 24.6
Drive belt idler bolt 153.90 ~ 57.82 5.5 ~ 5.9 39.78 ~ 42.67
OCV(oil control valve) bolt 29.80 ~ 11.76 1.0 ~ 1.2 7.23 ~ 8.68
Cylinder head bolt 16 39.2 + 120˚+90˚4.0 + 120˚+90˚28.93+ 120˚+
90˚
Cylinder head bolt 118.62 ~ 23.52 1.9 ~ 2.4 13.74 ~ 17.36
CVVT &exhaust cam sprocket bolt 464.68 ~ 76.44 6.6 ~ 7.8 47.74 ~ 56.42
Camshaft bearing cap bolt 32 9.80 ~ 11.76 1.0 ~ 1.2 7.23 ~ 8.68
Cylinder head cover bolt 38 9.80 ~ 11.76 1.0 ~ 1.2 7.23 ~ 8.68
Connecting rod bearing bolt 12 19.60 + 90˚2.0 + 90˚14.46 + 90˚
Main bearing cap inner bolt(M11) 849.00 + 90˚5.0 + 90˚36.16 + 90˚
Main bearing cap outer bolt(M8) 819.60 + 120˚2.0 + 120˚14.46 + 120˚
Main bearing cap side bolt(M8) 629.40 ~ 31.36 3.0 ~ 3.2 21.70 ~ 23.14
Oil drain cover bolt 69.80 ~ 11.76 1.0 ~ 1.2 7.23 ~ 8.68
Rear oil seal case bolt 69.80 ~ 11.76 1.0 ~ 1.2 7.23 ~ 8.68
Baffle plate bolt 12 9.80 ~ 11.76 1.0 ~ 1.2 7.23 ~ 8.68
Upper oil pan bolt 16 9.80 ~ 11.76 1.0 ~ 1.2 7.23 ~ 8.68
www.CarGarage.ir
www.CarGarage.ir
www.CarGarage.ir

GENERAL EMA -7
Item Quantity Nm kgf.m lb.ft
Knock sensor bolt 215.68 ~ 23.52 1.6 ~ 2.4 11.57 ~ 17.36
Drive plate bolt 871.54 ~ 75.46 7.3 ~ 7.7 52.80 ~ 55.69
Oil filter cap 124.50 2.5 18.08
Oil drain bolt 134.30 ~ 44.10 3.5 ~ 4.5 25.31 ~ 32.55
Oil pump bolt 319.60 ~ 23.52 2.0 ~ 2.4 14.47 ~ 17.36
Oil filter body bolt 10 9.80 ~ 11.76 1.0 ~ 1.2 7.23 ~ 8.68
Oil filter body cover bolt 11 9.80 ~ 11.76 1.0 ~ 1.2 7.23 ~ 8.68
Water vent hose bolt 29.80 ~ 11.76 1.0 ~ 1.2 7.23 ~ 8.68
Water pump bolt(Timing chain
cover bolt L) 121.56 ~ 26.46 2.2 ~ 2.7 15.91 ~ 19.53
Water pump bolt(Timing chain
coverboltK) 49.80 ~ 11.76 1.0 ~ 1.2 7.23 ~ 8.68
Water pump pulley bolt 47.84 ~ 9.80 0.8 ~ 1.0 5.78 ~ 7.23
Water temp. control nut 419.6 ~ 23.52 2.0 ~ 2.4 14.5 ~ 17.36
Water temp. control bolt 219.6 ~ 23.52 2.0 ~ 2.4 14.5 ~ 17.36
Water inlet pipe bolt 316.66 ~ 19.60 1.7 ~ 2.0 12.30 ~ 14.47
Air vent pipe bolt 29.80 ~ 11.76 1.0 ~ 1.2 7.23 ~ 8.68
Intake manifold bolt 626.5 ~ 31.4 2.7 ~ 3.2 19.5 ~ 23.1
Intake manifold nut 218.62 ~ 23.52 1.9 ~ 2.4 13.74 ~ 17.36
Surge tank bolt 19.80 ~ 11.76 1.0 ~ 1.2 7.23 ~ 8.68
Surge tank nut 218.6 ~ 23.5 1.9 ~ 2.4 13.7 ~ 17.4
Exhaust manifold stay bolt 452.0 ~ 56.9 5.3 ~ 5.8 38.3 ~ 42.0
Surge tank bolt 318.6 ~ 23.5 1.9 ~ 2.4 13.7 ~ 17.4
Breather pipe bolt 29.80 ~ 11.76 1.0 ~ 1.2 7.23 ~ 8.68
Surge tank bracket bolt 227.44 ~ 31.36 2.8 ~ 3.2 20.25 ~ 23.14
ETC bracket bolt 215.68 ~ 25.48 1.6 ~ 2.6 11.57 ~ 18.80
Exhaust manifold nut 16 39.20 ~ 44.10 4.0 ~ 4.5 28.93 ~ 32.55
Heat protector bolt 69.8 ~ 11.8 1.0 ~ 1.2 7.2 ~ 8.7
Front muffler 239.20 ~ 58.80 4.0 ~ 6.0 28.93 ~ 43.40
www.CarGarage.ir
www.CarGarage.ir
www.CarGarage.ir

EMA -8 ENGINE MECHANICAL SYSTEM
INSPECTION ECE1FCC3
COMPRESSION PRESSURE
NOTE
If there is lack of power, excessive oil consumption or
poor fuel economy, measure the compression pres-
sure.
1. Warm up and stop engine.
Allow the engine to warm up to normal operating tem-
perature.
2. Remove ignition coils. (Refer to Ignition in FL Group)
3. Remove spark plugs.
Usinga16mmplugwrench,removethe6sparkplugs.
4. Check cylinder compression pressure.
a. Insert a compression gauge into the spark plug
hole.
b. Fully open the throttle.
c. After 7times of cranking the engine, measure the
compression pressure.
NOTE
Always use a fully charged battery to obtain engine
speed of 200 rpm or more.
d. Repeat steps (a) through (c) for each cylinder.
NOTE
This measurementmust be done in as short a time as
possible.
Compressionpressure:
1,225kPa (12.5kgf/cm², 177psi) - 200 ~ 250rpm
Minimum pressure :
1,078kPa (11.0kgf/cm², 156psi)
e. If the cylinder compression in 1 or morecylinders
is low, pour a small amount of engine oil into the
cylinder through the spark plug hole and repeat
steps (a) through (c) for cylinders with low com-
pression.
• If adding oil helps thecompression, it is likely
that the piston rings and/or cylinder bore are
worn or damaged.
• If pressure stays low, a valve may be stick-
ing or seating is improper, or there may be
leakage past the gasket.
5. Reinstall spark plugs.
6. Install ignition coils. (See EE group - ignition)
VALVE CLEARANCE INSPECTION AND
ADJUSTMENT
NOTE
Inspect and adjust the valve clearance when the en-
gine is cold (Engine coolant temperature : 20 C) and
cylinder head is installed on the cylinder block.
1. Remove the engine cover(A).
A
SBLM16001L
2. Remove the engine room resonator(A).
A
SBLM16003L
www.CarGarage.ir
www.CarGarage.ir
www.CarGarage.ir

GENERAL EMA -9
3. AfterdisconnectingtheMAFsensor connector(A)and
the breather hose(B), remove the air cleaner assem-
bly(C).
C
AB
SBLM16002L
4. Disconnect the other breather hose(A), the Purge
Control Solenoid Valve(PCSV) hose, the Positive
Crankcase Ventilation (PCV) hose(C) and the Elec-
tronic Throttle Control(ETC) cooling hoses(D) and
connector(E).
DE
C
SBLM16208L
A
SBLM16005L
5. Removethewiringoverthesurgetank.
1) Disconnect the injection harness connector(A).
2) Disconnect the camshaft position sensor(CMP)
harness connector(B).
3) Disconnect the ground line(C).
4) Disconnect the ignition coil harness connec-
tor(D).
5) Disconnect the condensor connector(E).
6) Disconnect the variable induction system(VIS)
solenoid valve connector(G).
7) Disconnect the oil control valve(OCV) harness
connector(F).
8) Disconnect the injector wiring(H) and ignition coil
wiring(I).
D
B
A
E
C
F
SBLM16006L
H
G
I
SBLM16206L
www.CarGarage.ir
www.CarGarage.ir
www.CarGarage.ir

EMA -10 ENGINE MECHANICAL SYSTEM
6. Disconnect the fuel hose tube(A).
A
SBLM16015L
7. Remove heater hose(A) and disconnect the brake
vaccume hose(B).
A
B
SBLM16017L
8. Disconnect the surge tank stay.
9. Remove the surge tank.
10. Loosenthecylinderheadcoverboltsand thenremove
the cover(A) and gasket.
A
SBLM16007L
11. Set No.1 cylinder to TDC/compression.
a. Turn the crankshaft pulley and align its groove
with the timing mark "T" of the lower timing chain
cover.
KDRF108A
www.CarGarage.ir
www.CarGarage.ir
www.CarGarage.ir

GENERAL EMA -11
b. Check that the mark(A) of the camshaft timing
sprockets are in straight line on the cylinder head
surface as shown in the illustration.
If not, turn the crankshaft one revolution (360 )
NOTE
Do not rotate engine counterclockwise
A
KDRF113A
12. Inspect the valve clearance.
a. Check only the valve indicated as shown. [No. 1
cylinder : TDC/Compression] measure the valve
clearance.
RH EXHAUST
LH EXHAUST
INTAKE
Timing mark
EDRF021A
· Using a thickness gauge, measure the clear-
ance between the tappet and the base circle of
camshaft.
· Record the out-of-specification valve clearance
measurements. They will be used later to deter-
mine the required replacement adjusting tappet.
Valve clearance
Specification
Engine coolant temperature : 20 C[68F]
Limit
Intake : 0.17 ~ 0.23mm (0.0067 ~ 0.0090in.)
Exhaust : 0.27 ~ 0.33mm (0.0106 ~ 0.0129in.)
b. Turn the crankshaft pulley one revolution (360 )
and align the groove with timing mark "T" of the
lower timing chain cover.
NOTE
Do not rotate engine counterclockwise
c. Check only valves indicated as shown. [NO. 4
cylinder : TDC/compression]. Measure the valve
clearance.
RH EXHAUST
LH EXHAUST
INTAKE
Timing mark
Timing mark
EDRF022A
13. Adjust the intake and exhaust valve clearance.
a. Set the No.1 cylinder to the TDC/compression.
b. Markonthetimingchainonthebasisofthemark-
ingonsprocketandCVVT.
c. Remove the timing chain.
d. Remove the camshaft bearing caps(A).
A
KDRF196A
www.CarGarage.ir
www.CarGarage.ir
www.CarGarage.ir

EMA -12 ENGINE MECHANICAL SYSTEM
e. Remove the camshaft assembly(A).
A
KDRF197A
f. Remove MLAs.
g. Measure the thickness of the removed tappet us-
ing a micrometer.
EDKE889D
h. Calculate the thickness of a new tappet so that
the valve clearance comes within the specified
value.
Valve clearance(Engine coolant tempera-
ture: 20 C[68 F])
T : Thickness of removed tappet
A : Measured valve clearance
N : Thickness of new tappet
Intake : N = T + [A - 0.20mm(0.0079in.)]
Exhaust : N = T + [A - 0.30mm (0.0118in.)]
i. Select a new tappet with a thickness as close as
possible to the calculated value.
NOTE
Tappets are available in 41size increments of
0.015mm (0.0006in.) from 3.00mm (0.118in.) to
3.600mm (0.1417in.)
j. Place a new tappet on the cylinder head.
NOTE
Appling engine oil at the selected tappet on the pe-
riphery and top surface.
k. Install the intake and exhaust camshaft.
l. Install the bearing caps.
m. Install the timing chain.
n. Turn the crankshaft two turns in the operat-
ing direction(clockwise) and realign crankshaft
sprocket and camshaft sprocket timing marks.
o. Recheck the valve clearance.
Valve clearance (Engine coolant tempera-
ture: 20 C[68 F])
[Specification]
Intake : 0.17 ~ 0.23mm (0.0067 ~ 0.0090in.)
Exhaust : 0.27 ~ 0.33mm (0.0106 ~ 0.0129in.)
www.CarGarage.ir
www.CarGarage.ir
www.CarGarage.ir

GENERAL EMA -13
TROUBLESHOOTING EB9DDED8
Symptom Suspect area Remedy
Worn crankshaft bearings.
Loose or improperly installed
engine drive plate.
Replace the crankshaft and bearings
as required.
Repair or replace the drive plate
as required.
Worn piston rings.
(Oil consumption may or may not
cause the engine to misfire.)
Inspect the cylinder for a loss of
compression.
Repair or replace as required.
Engine misfire with abnormal
internal lower engine noises.
Worn crankshaft thrust bearings Replace the crankshaft and bearings
as required.
Stuck valves.
(Carbon buildup on the valve stem) Repair or replace as required.
Excessive worn or mis-aligned
timing chain. Replace the timing chain and sprocket
as required.
Engine misfire with abnormal
valve train noise.
Worn camshaft lobes. Replace the camshaft and valve lifters.
Engine misfire with coolant
consumption. •Faulty cylinder head gasket and/or
cranking or other damage to
the cylinder head and engine
block cooling system.
•Coolant consumption may or may
not cause the engine to overheat.
•Inspect the cylinder head and engine
block for damage to the coolant
passages and/or a faulty head gasket.
•Repair or replace as required.
Worn valves, guides and/or valve
stem oil seals. Repair or replace as required.Engine misfire with excessive
oil consumption.
Worn piston rings.
(Oil consumption may or may not
cause the engine to misfire)
•Inspect the cylinder for a loss
of compression.
•Repair or replace as required.
Incorrect oil viscosity. •Drain the oil.
•Install the correct viscosity oil.
Engine noise on start-up, but
only lasting a few seconds.
Worn crankshaft thrust bearing. •Inspect the thrust bearing and
crankshaft.
•Repair or replace as required.
www.CarGarage.ir
www.CarGarage.ir
www.CarGarage.ir

EMA -14 ENGINE MECHANICAL SYSTEM
SymptomSuspectarea Remedy
Low oil pressure. Repair or replace as required.
Broken valve spring. Replacethevalvespring.
Worn or dirty valve lifters. Replace the valve lifters.
Stretched or broken timing chain and/or
damaged sprocket teeth. Replace the timing chain and sprockets.
Worn timing chain tensioner, if
applicable. Replace the timing chain tensioner
as required.
Worn camshaft lobes. •Inspect the camshaft lobes.
•Replace the timing camshaft and
valve lifters as required.
Worn valve guides or valve stems. Inspect the valves and valve guides,then
repair as required.
Stuck valves. (Carbon on the valve
stem or valve seat may cause the
valvetostayopen.
Inspect the valves and valve guides,
then repair as required.
Upper engine noise,regard-
less of engine speed.
Worn drive belt, idler, tensioner
and bearing. Replace as required.
Low oil pressure. Repair or required.
Loose or damaged drive plate. Repair or replace the drive plate.
Damaged oil pan, contacting the
oil pump screen. •Inspect the oil pan.
•Inspect the oil pump screen.
•Repair or replace as required.
Oil pump screen loose, damaged
or restricted. •Inspect the oil pump screen.
•Repair or replace as required.
Excessive piston-to-cylinder bore
clearance. •Inspect the piston, piston pin
and cylinder bore.
•Repair as required.
Excessive piston pin-to-piston
clearance. •Inspect the piston, piston pin and
the connecting rod.
•Repair or replace as required.
Excessive connecting rod bearing
clearance Inspect the following components
and repair as required.
•The connecting rod bearings.
•The connecting rods.
•The crankshaft pin journals.
Excessive crankshaft bearing clearance. Inspect the following components,
and repair as required.
•The crankshaft bearings.
•The crankshaft main journals.
•The cylinder block.
Lower engine noise,regard-
less of engine speed.
Incorrect piston, piston pin and
connecting rod installation •Verify the piston pins and connecting
rods are installed correctly.
•Repair as required.
www.CarGarage.ir
www.CarGarage.ir
www.CarGarage.ir

GENERAL EMA -15
SymptomSuspectarea Remedy
Low oil pressure Repair or replace as required.
Excessive connecting rod bearing
clearance . Inspect the following components
andrepair as required :
•The connecting rod bearings.
•The connecting rods.
•The crankshaft.
Engine noise under load.
Excessive crankshaft bearing clearance. Inspect the following components,
andrepair as required.
•The crankshaft bearings.
•The crankshaft main journals.
•The cylinder block.
Hydraulically locked cylinder.
•Coolant/antifreeze in cylinder.
•Oil in cylinder.
•Fuel in cylinder.
1. Remove spark plugs and check
for fluid.
2. Inspect for broken head gasket.
3. Inspect for cracked engine block
or cylinder head.
4. Inspect for a sticking fuel injector
and/or leaking fuel regulator.
Broken timing chain and/or timing chain
and/or timing chain gears. 1. Inspect timing chain and gears.
2. Repair as required.
Material in cylinder.
•Broken valve
•Piston material
•Foreign material
1. Inspect cylinder for damaged
components and/or foreign materials.
2. Repair or replace as required.
Seized crankshaft or connecting
rod bearings. 1. Inspect crankshaft and connecting
rod bearing.
2. Repair as required.
Bent or broken connecting rod. 1. Inspect connecting rods.
2. Repair as required.
Engine will not
crank-crankshaft will not
rotate.
Broken crankshaft. 1. Inspect crankshaft.
2. Repair as required.
www.CarGarage.ir
www.CarGarage.ir
www.CarGarage.ir

EMA -16 ENGINE MECHANICAL SYSTEM
SPECIAL SERVICE TOOLS E787872C
Tool (Number and name) Illustration Use
Crankshaft front oil seal installer
(09231-3C100)
KDRF233A
Installation of the front oil seal
Flywheel stopper
(09231-3C300)
KCRF030D
Removal and installation of the flywheel
and crankshaft pulley.
Torque angle adapter
(09221-4A000)
LCAC030A
Installation of bolts & nuts needing
an angular method
Valve stem seal remover
(09222-29000)
KDRF232A
Remover of the valve stem seal
Valve stem seal remover
(09222-3C100)
LCAC030D
Installation of the valve stem seal
www.CarGarage.ir
www.CarGarage.ir
www.CarGarage.ir

GENERAL EMA -17
Tool (Number and name) Illustration Use
Valve spring compressor
&holder
(09222-3K000)
(09222-3C300)
A
A
B
ECRF003A
Removal and installation of the intake
or exhaust valve
A : 09222-3K000
B : 09222-3C300 (holder)
Crankshaft rear oil seal installer
(09231-3C200)
(09231-H1100)
A
B
ACRF003A
Installation of the crankshaft rear oil seal
A : 09231-3C200
B : 09231-H1100
Oil pan remover
(09215-3C000)
KDRF219A
Removal of oil pan
Oil filter wrench
(09263-3C100)
B6327000
Removal and installation of the oil filter
www.CarGarage.ir
www.CarGarage.ir
www.CarGarage.ir

EMA -18 ENGINE MECHANICAL SYSTEM
ENGINE AND TRANSAXLE
ASSEMBLY
REMOVAL E31DBAFC
CAUTION
•Use fender covers to avoid damaging painted
surfaces.
•To avoid damage, unplug the wiring connec-
tors carefully while holding the connector
portion.
NOTE
•Mark all wiring and hoses to avoid misconnec-
tion.
•Turn the crankshaft pulley so that the No.1 piston
is at top dead center.
1. Removetheenginecover(A).
A
SBLM16001L
2. Recover refrigerant by opening the high &low pres-
sure pipe caps and connecting the refrigerant sta-
tion(Refer to Air conditioning system in HA Group).
3. Remove the under cover(A).
A
SBLM16016L
4. Drain engine oil, transaxle fluid and engine coolant.
5. Disconnect the neagative terminal from the battery
and remove the battery(A).
6. Remove the intake air hose and aircleaner assembly.
1) Disconnect the MAF connector(A).
2) Disconnect the breather hose(B) from air cleaner
hose.
3) Remove the intake air hose and air cleaner as-
sembly(C) with the resonator(D).
D
CAB
SBLM16113L
www.CarGarage.ir
www.CarGarage.ir
www.CarGarage.ir

ENGINE AND TRANSAXLE ASSEMBLY EMA -19
7. Disconnect the PCM connectors(A).
A
SBLM16009L
8. Remove the battery tray while recovering refrigerant.
9. Disconnect the high and low pressure pipes from the
radiator or the compressor.(Refer to Air conditioning
system in HA Group).
10. Remove the radiator.(Refer to Radiator in this Group).
11. Disconnect the engine wiring harness connectors.
1) Disconnect the oil control valve(OCV) harness
connector(A) and the knock sensor(LH) harness
connector(B)
A
B
SBLM16010L
2) DisconnecttheMAP(A),ETC(B),ignition coilhar-
nessconnector(C)andtheinjectionharnesscon-
nector(D).
BD
C
A
SBLM16011L
3) Disconnect the battery connector(A), the power
steering switch connector(B) and the knock sen-
sor(RH) harness connector(C).
C
B
A
SBLM16012L
4) Disconnect the oxygen sensors(A), CMP(B),
CKP(C), VIV(D) and the condensor harness
connector(E).
A
A
B
CE
D
SBLM16013L
www.CarGarage.ir
www.CarGarage.ir
www.CarGarage.ir

EMA -20 ENGINE MECHANICAL SYSTEM
5) Disconnector the water temperature sen-
sor(WTS) harness connector(A), the oil temper-
ature sensor(OTS) harness connector(B) and
the purge control solenoid valve(PCSV) harness
connector(C).
C
AB
SBLM16014L
12. Disconnect the transaxle wire harness connector and
remove the transaxle assembly.(Refer to Transaxle
system in AT Group).
13. Disconnect the fuel hose tube(A).
A
SBLM16015L
14. Disconnect the front exhaust muffler with the exhaust
manifolds.
15. Remove the front wheels and tires.(Refer to Suspen-
sion system in SS Group).
16. Remove heater hose(A) and disconnect the brake
vaccume hose(B).
A
B
SBLM16017L
17. Remove the exhaust and intake manifold covers.(Re-
fer to Intake and exhaust system in this Group).
18. Remove the power steering pump assembly.(Refer to
Power steering pump in ST Group).
19. Remove the hood assembly.(Refer to Hood in BD
Group).
20. Install a jack for supporting the engine assembly.
21. Remove the engine mounting brackets(A).
A
SBLM16018L
22. Jack up the engine assembly in order to remove the
engine from the vehicle.
www.CarGarage.ir
www.CarGarage.ir
www.CarGarage.ir
This manual suits for next models
1
Table of contents
Other Kia Engine manuals
Popular Engine manuals by other brands
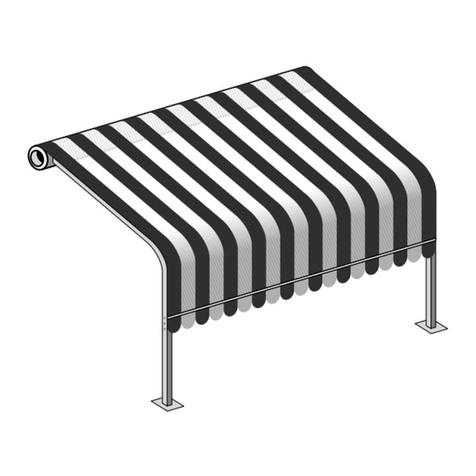
Nice
Nice To-Max T Series Instructions and warnings for installation and use
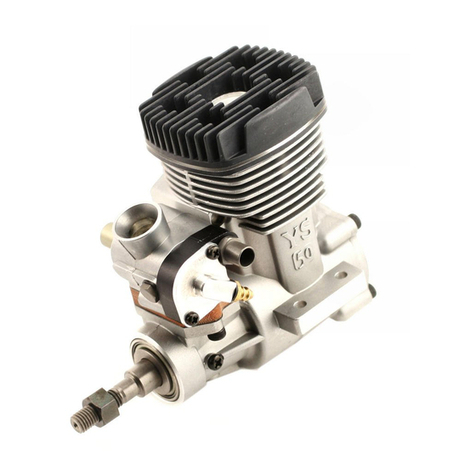
YS
YS 50ST Operator's manual

Roto
Roto 130 FSI operating instructions
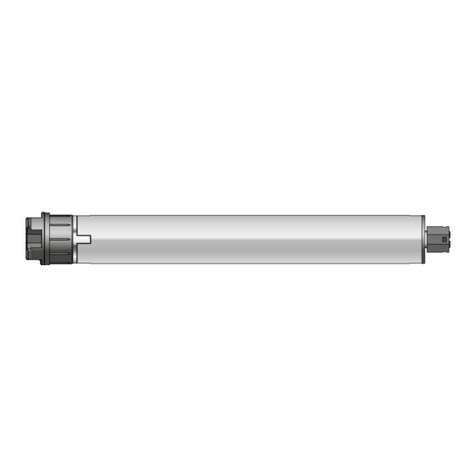
GEIGER
GEIGER GB45R Series Original assembly and operating instructions
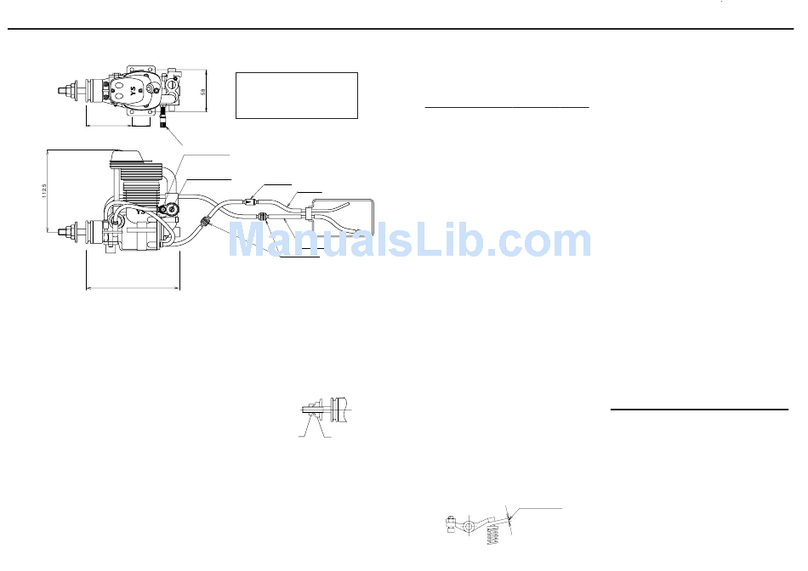
YS
YS 140LIMITED Operator's manual
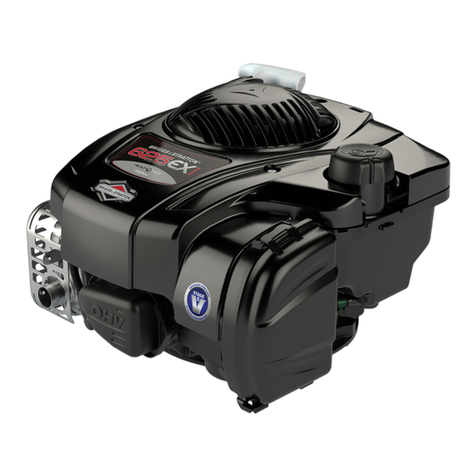
Briggs & Stratton
Briggs & Stratton 090000 Operator's manual

Vexta
Vexta SMK Series operating manual
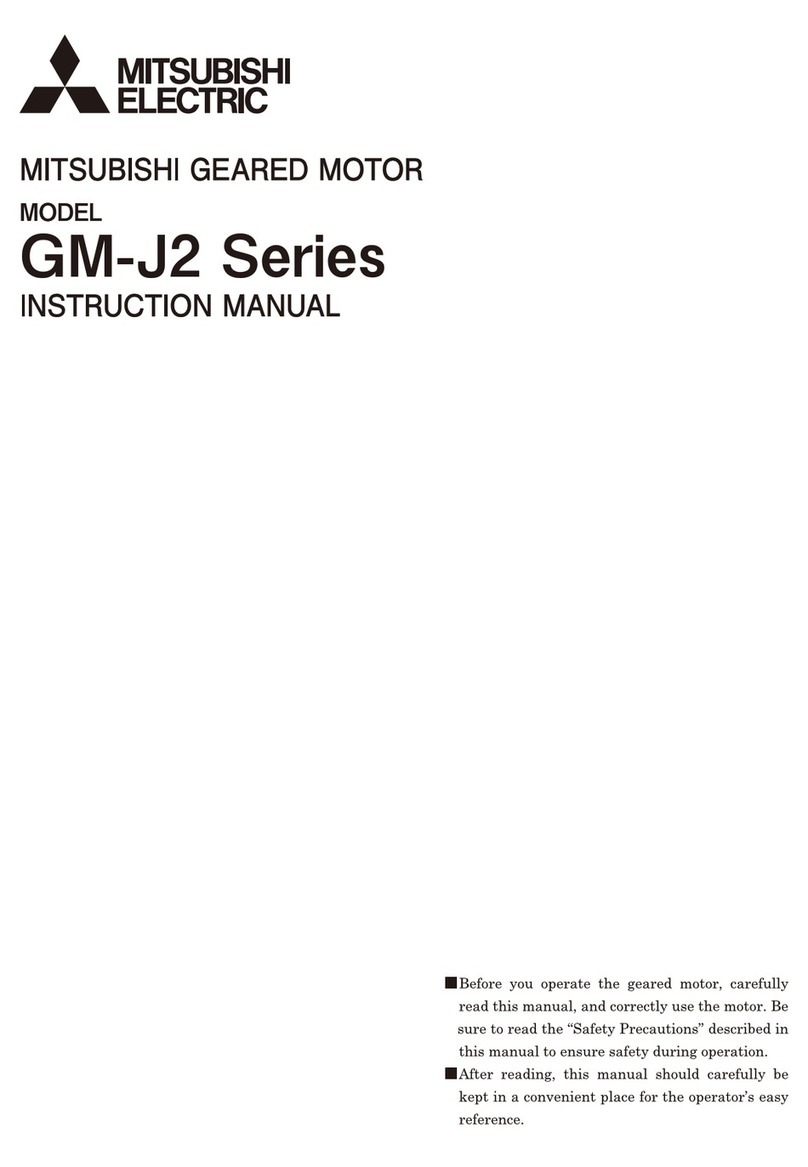
Mitsubishi Electric
Mitsubishi Electric GM-J2 Series instruction manual
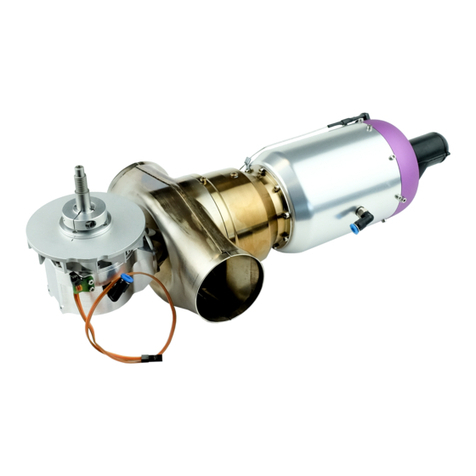
JetCat
JetCat SPH5 instruction manual

Perkins
Perkins 854E-E34TA Systems operation testing and adjusting

Tecumseh
Tecumseh HSK840 Technician's handbook

RADEMACHER
RADEMACHER RolloTube Basic 2160 20 90 installation instructions