King-Gage Multi-Point User guide

Page 1
Multi-Point Process Switch EX-1711Effective: September 2006 (Replaces October 2002) EX-1711
Multi-Point™ Process Switch
Single-Channel Analog
Start-Up/Operation
Instructions
KING-GAGE
®
4-20 mA Process Control

Page 2
Multi-Point Process Switch EX-1711
© 1989/1995 King Engineering Corporation. All rights
reserved.
The information contained in this manual was accurate at
the time of release. Specifications are subject to change
without notice.
Warranty—All King Engineering products are guaranteed
to be free from defects in material and workmanship for
one year from the date of purchase. Any product or part
found to be defective under normal use within one year of
purchase will be repaired or replaced at no charge if returned
to the company at Ann Arbor, Michigan within ten days
of discovery of the defect. No other warranties, whether
expressed, implied or statutory, including the warranties
of fitness for a particular purpose or merchantability, are
given by this agreement.
The exclusive remedy for nonconformity of these goods
shall be repair and/or replacement of the nonconforming
goods or parts.
Seller will not be liable for consequential damages resulting
from breach of this agreement. The term “consequential
damages” shall include but shall not be limited to damage
to all machines, equipment and goods other than the goods
sold hereby, interruption of production, loss of profits,
delays of any kind, administrative expense and overhead.
Revisions:
(A) October, 1989—Original Release.
(B) December, 1989—Revised Deadband Range
(C) April, 1995—Revised/Redrawn per ECR No. 3397
(D) October, 2002—Logo w/ web address (cover)
(E) September, 2006—Heading (cover), logo (back)

Page 3
Multi-Point Process Switch EX-1711
Contents
Specifications
Specification Data, Dimensions ............................................................................. 4
AC Power Requirements
Power Terminal Connections ................................................................................. 5
Internal Fuse Replacement .................................................................................... 6
4-20 mA Process Loop
Typical Process Loop Diagram................................................................................ 7
Input Current Limiting (PTC Resistor).....................................................................7
Set-Points/Output Relays
Front Panel—LED Status Indicators........................................................................8
3.0 Amp SPDT Relays ............................................................................................ 8
Set-Point Adjustments .......................................................................................... 9
Deadband Adjustment .......................................................................................... 10
Troubleshooting
Symptoms and Possible Causes ............................................................................. 11

Page 4
Multi-Point Process Switch EX-1711
Specifications
Power Requirements
nominal 115 Vac/60 Hz (unregulated)
3.45 W/0.03 A - fused @ 1/2 A
Temperature Range (Environmental)
32° F to 158° F / 0° C to 70° C operating
(-40° F to 158° F / -40° C to 70° C storage)
Input
dc current: 4-20 milliamperes
Current Limiting (Overload)
70 mAdc maximum; automatic trip/reset using
PTC resistor (positive temperature coefficient)
circuit
Input Impedance
132 ohm resistance (3 Vdc drop @ 20 mAdc)
Set-Points
(4) four independent user set-points; continuously
adjustable over full input range. Front panel LED
status indicator gives visual confirmation when set-
point value has been exceeded.
Sensitivity (Adjustment)
Set-points can be adjusted to better than
0.05% FS/0.008 mAdc
Repeatability
Set-point settings are repeatable to better than
0.05% FS
(Long-Term Repeatability: better than 0.1% FS)
Deadband
Single deadband potentiometer controls all four set-
point settings. Deadband adjustable from 1.0% -
12.5% FS. (Factory preset to 1% FS.)
Output
(4) independent SPDT (form-C) relays; maximum
3.0 A @ 115 Vac. Rated for minimum 100,000 cycle/
life at rated load.
Size/Weight
7.125"H × 2"W × 6.125"D
(181mm × 51mm × 155mm)
22 oz/624 g
®
KING-GAGE
S
E
T
1
S
E
T
2
S
E
T
3
S
E
T
4
MULTI-POINT
Process Switch
1
2
3
4
Coarse Adj.
Fine Adj.
Coarse Adj.
Fine Adj.
Coarse Adj.
Fine Adj.
Coarse Adj.
Fine Adj.
2 in
51 mm
6 in
152 mm
7-1/8 in.
181 mm
6-1/2 in.
165 mm
POWER Hot
Gnd
Neu
C
N.O.
N.C.
C
N.O.
N.C.
C
N.O.
N.C.
C
N.O.
N.C.
+
-
INPUT
4-20 mA
AC
115 V
S
E
T
1
S
E
T
2
S
E
T
3
S
E
T
4
9/32 in.
7 mm, qty. 4
1-1/16 in.
27 mm

Page 5
Multi-Point Process Switch EX-1711
Terminal Connections
Electrical Power
The Process Switch requires nominal 115 Vac/60 Hz. (single-
phase) power for operation. Connections should be made
using approved 3-conductor, source grounded cabling.
Proper polarity must be maintained for optimum
performance of the unit. See illustration that details the
terminal connections located at the top of the housing.
Plug Type Connectors
Terminal blocks plug into a mating socket on the Process
Switch housing. Three (3) individual terminal blocks are
provided...
1. 3-terminal AC Power block
2. 12-terminal Relay Contact block
3. 2-terminal Signal Input block
Hot
Gnd
Neu
C
N.O.
N.C.
C
N.O.
N.C.
C
N.O.
N.C.
C
N.O.
N.C.
+
-
INPUT
4-20 mA
AC
115 V
S
E
T
1
S
E
T
2
S
E
T
3
S
E
T
4
AC
Power
Relay
Contact
Signal
Input
Connections Detail
Plug Type Connectors
®
KING-GAGE
POWER

Page 6
Multi-Point Process Switch EX-1711
Internal Fuse
The AC Power input of the Process Switch is internally fused
using a 0.5 Amp/250 Volt non-time delay fuse. To replace
this fuse, remove the side panel from the housing. This is
held in place by four (4) phillips-head
screws.
CAUTION: Disconnect AC power prior to opening
housing or replacing fuse assembly!
Replacement Fuse - Order No. 7469-21-0, 1/2 Amp FAST-
BLO, 5-pack (Equivalent to BUSS AGC 1/2)
Internal Fuse

Page 7
Multi-Point Process Switch EX-1711
4-20 mA Input Signal
The Multi-Point Process Switch is a single channel analog
set-point control. It provides continuous monitoring of a
typical process loop with four (4) independent set-points
that are user adjustable over the full input range. The
Process Switch accepts any proportional, externally-powered
two-wire 4-20 mAdc current loop from any typical process
transmitter (level, pressure or temperature).
Unit must be wired in series with transmitter to
maintain proper polarity at the + and - terminals.
See Diagram.
Internal input resistance of the Process Switch is 132
ohms (nominal) during normal operation.
Input Current Limiting
A positive temperature coefficient (PTC) resistor circuit is
incorporated into the Process Switch for protection against
overcurrent situations. This thermal resistor undergoes
increased orders of magnitude in resistance when an input
current ≥ 70.0 mAdc heats it above a certain point. In the
switched state, a latched high-resistance limits current to
no more than a few milliamps.
The resistor circuit resets automatically, permitting normal
current flow once the input drops below 70 mAdc. (NOTE:
Protective resistor circuit is rated for 30 trip/cycles max.)
32 ohms
nominal
100
ohms
V
COM
-
+ +-
Process
Transmitter
Process
Switch +VA
Diagram of Typical Process Loop
Voltage supply ( +VA ) provides power to process trans-
mitter which outputs 4-20 mA signal through the loop.
Process Switch is wired into loop to receive signal.
Internal PTC resistor provides overcurrent protection by
limiting input through high-resistance.
(See “Input Current Limiting”)

Page 8
Multi-Point Process Switch EX-1711
®
KING-GAGE
S
E
T
1
S
E
T
2
S
E
T
3
S
E
T
4
MULTI-POINT
Process Switch
1
2
3
4
Coarse Adj.
Fine Adj.
Coarse Adj.
Fine Adj.
Coarse Adj.
Fine Adj.
Coarse Adj.
Fine Adj.
POWER
LED Status
Indicators
User
Set-Points
C
NO
NC
SPTD
(Form-C)
Not Energized
LED not
illuminated
C
NO
NC
SPTD
(Form-C)
Energized
LED
illuminated
Adjustable Set-Points
The Process Switch has four (4) user set-points that can be
adjusted to control continuous process operations, provide
fail-safe limiting or alarm functions.
Front Panel - LED Status Indicators are located on the
front panel of the Process Switch. Each of the four (4) LEDs
correspond to “SET1, SET2, SET3, SET4" adjustments and
output relays. When illuminated, the LED indicates that
the set-point has been reached and
corresponding relay energized.
SPDT (Form-C) Output Relays
Four (4) independent SPDT (single-pole/double-throw) relays
are provided on the Process Switch. Form-C configuration
includes normally-open (N.O.), normally-closed (N.C.) and
common (C) relay contacts. Rated for 3.0 Amps maximum
@ nominal 115 Vac.
Relay is energized when corresponding set-point milliamp
value is exceeded.

Page 9
Multi-Point Process Switch EX-1711
Set-Points/Deadband Adjustments
Set-Points
The Process Switch has four (4) user set-points which are
continuously adjustable over the full 4-20 mAdc input
range. Each set-point can be adjusted to within 0.008
mAdc (or 0.05% FS).
Coarse Adjustment—20-turn potentiometer/each
complete turn yields approximately 1.0 mA change.
Fine Adjustment—20-turn potentiometer/each
complete turn yields approximately 0.005 mA
change.
Deadband
A master deadband adjustment controls all four set-points.
The deadband adjustment range is 1.0% -12.5% FS. (Process
Switch is factory-preset with a nominal 1.0% FS deadband.)
Deadband can be used to eliminate cycling due to
fluctuations within the 4-20 mA input signal. Resetting the
deadband will also shift the set-point accordingly. Refer to
diagrams below:
10.00 mA
9.84 mA
Set Point
1% FS
Deadband
Relay
Remains
Energized
Relay off
Relay is
triggered
mA
mA
10.00 mA
10.04 mA
9.84 mA
9.80 mA
Original
Set Point
Increased
Deadband
Relay
Remaining
Energized
Relay off
Relay is
triggered
mA
mA
16.00 mA
15.68 mA
Set Point
2% FS
Deadband
Relay
Remains
Energized
Relay off
Relay is
triggered
mA
mA
15.96 mA
16.00 mA
15.72 mA
15.68 mA
Original
Set Point
Decreased
Deadband
Relay Remaining
Energized
Relay off
Relay is
triggered
mA
mA
Decreased Deadband Effect on Set-Point
Increased Deadband Effect on Set-Point

Page 10
Multi-Point Process Switch EX-1711
Adjustment Procedure
The LED status indicators are used when adjusting the
individual set-points. When illuminated, they indicate
the set-point has been reached and corresponding relay
energized.
One method of adjusting set-points is to input a simulated
4-20 mA signal. By slowly varying the milliamp signal, the
precise value of the existing setting (including deadband)
can be determined prior to making any adjustments. This
procedure requires a very high
precision meter and milliamp source.
Generally, however, set-points are adjusted in-process.
Assuming the Process Switch is receiving the desired milliamp
(mAdc) input signal from the transmitter . . .
1. If the LED status indicator is not illuminated, turn the
Coarse potentiometer clockwise (CW). As soon as the
LED is illuminated, slowly turn in the opposite direction
until it goes out. Very slowly turn potentiometer
clockwise but not so much as to trigger LED. (It may
be necessary to repeat this procedure to acheive the
“coarse” adjustment.)
If the LED status indicator is illuminated, turn the Coarse
potentiometer counter-clockwise (CCW) until it goes
off. Very slowly turn potentiometer clockwise but not so
much as to trigger LED. (It may be necessary to repeat
this procedure to achieve the “coarse” adjustment.)
2. Turn FINE potentiometer clockwise (CW) very slowly
and stopping immediately as soon as LED is illuminated.
Warning!
If deadband is adjusted, all existing set-points will shift
accordingly. This will generally require re-adjustment of all
set-points. The deadband adjustment controls all set-points.
Deadband Adjustment
The MULTI-POINT Process Switch has been factory-adjusted
with a 1% FS deadband (0.16 mA). This represents the
range through which the input signal can be varied without
initiating a response at the output relays.
Deadband is adjustable up to 12.5% FS for applications
when greater tolerance of input fluctuation is required.
When deadband is adjusted, set-points will shift accordingly.
Note—Deadband should be adjusted only by a skilled
technician. High-precision meters and signal generators
are required to accurately adjust the deadband setting.
Deadband Potentiometer
The adjustment pot for deadband settings is located inside
of the housing. See below.
Deadband
Potentiometer

Page 11
Multi-Point Process Switch EX-1711
Preliminary Troubleshooting
Relay does not energize . . . LED indicator is not
illuminated
Disconnect 115 Vac power from MULTI-POINT Process
Switch and check internal fuse. If fuse is blown, replace
(see Page 6).
Check that 115 Vac power is properly connected to input
terminals and power circuit is “on”.
Relay remains energized . . . LED indicator does not
turn off
Relays and LEDs remain energized whenever input signal
(mAdc) is greater than the set-point value. If a low level
set-point is required to actuate a pump or to close a
valve, re-wire circuit at relay using the N.C. (normally-
closed) switch contact.
Unusually high load resistance (RL) at Process Switch
Possible short-circuit in signal loop. If signal current
exceeds 70 mAdc, an overcurrent-limiting PTC (PTC—
positive temperature coefficient) resistor restricts current
levels through the entire loop to only a few milliamps.
Relay remains energized too long
Deadband is adjustable over an extremely wide bandwidth
(1.0%–12.5% FS). An adjustment to the deadband may
create a situation where the relays will remain energized
much longer than desired. (See Page 9)

CORPORATION
ENGINEERING
KING
3201 South State St, Ann Arbor, Michigan 48108-1625 U.S.A.
PO Box 1228, Ann Arbor, Michigan 48106-1228 U.S.A.
Phone: (734) 662-5691 • FAX: (734) 662-6652
www.king-gage.com
®
Since 1937
Table of contents
Popular Switch manuals by other brands
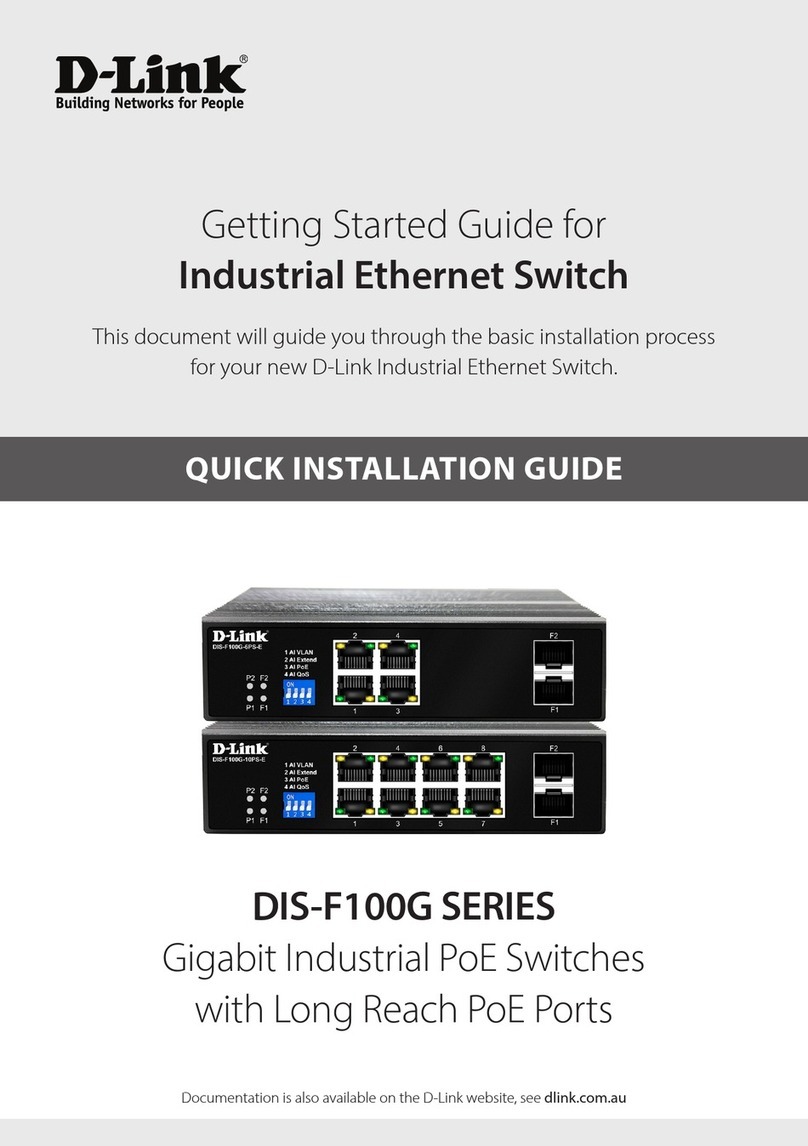
D-Link
D-Link DIS-F100G Series Quick installation guide
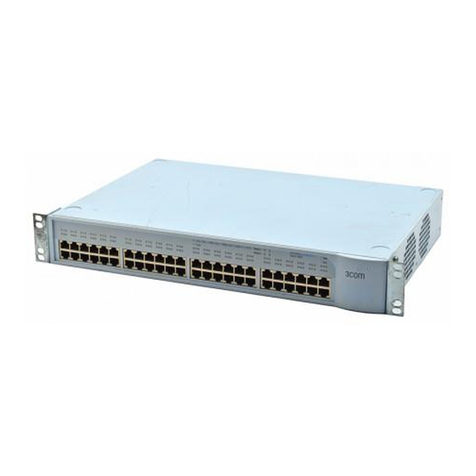
3Com
3Com SuperStack 3 4300 Getting started guide
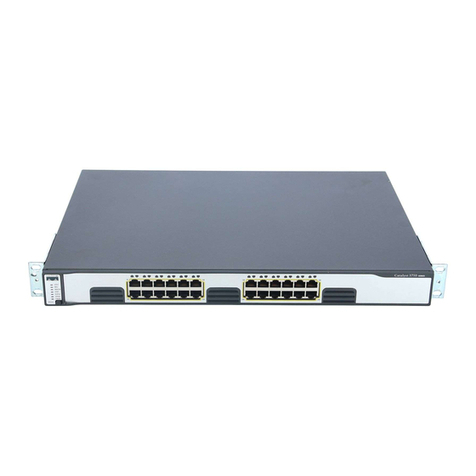
Cisco
Cisco 3750 - Catalyst EMI Switch Message guide
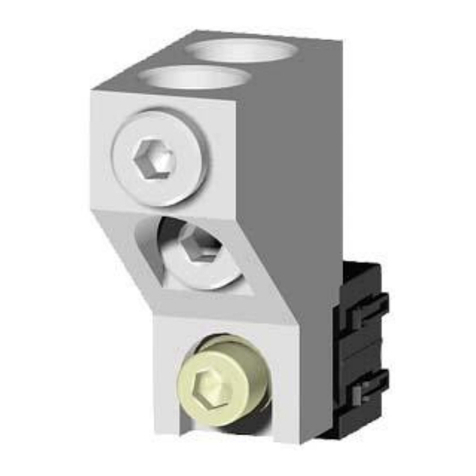
Siemens
Siemens 3VT9324-4TF30 operating instructions
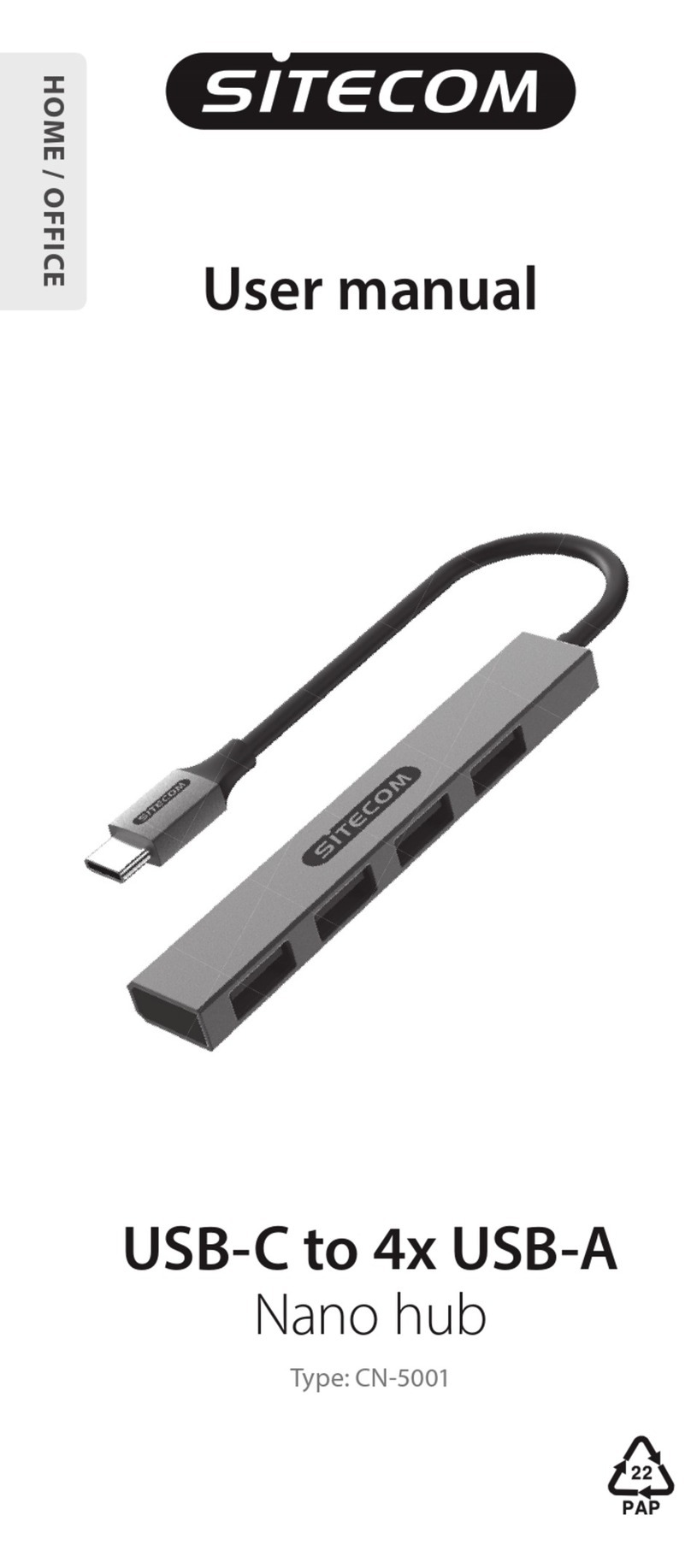
Sitecom
Sitecom CN-5001 user manual
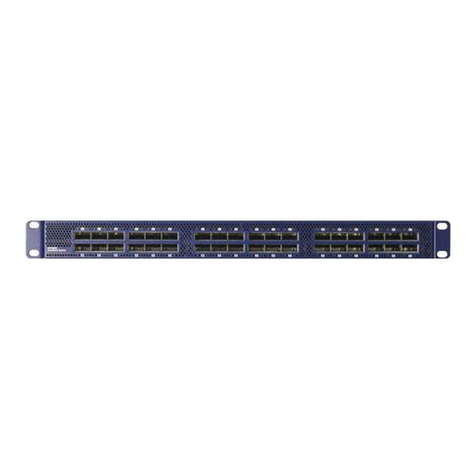
Mellanox Technologies
Mellanox Technologies InfiniScale MTS3600Q-1BNC user manual