Kitz SCHBSL User manual

Document No.: KE-2033-00
Operation Manual
For
SCHBSL Type Butterfly Valves
【Lug Type】
Thank you for choosing KITZ products.
For safe and trouble-free function and performance of the product, make sure to
read and understand all items in this manual before handling the product.
Keep this manual accessible to all the valve operating personnel.

Document No.: KE-2033-00
This operation manual applies to the manually operated KITZ SCHBSL type butterfly valves (lug type).
For automated operation, refer to the operation manual prepared by the manufacture of the valve actuator.
SAFETY PRECAUTIONS
For the safe use of the product, read all of the safety precautions listed in this manual before handling the
product.
The safety precautions in this manual are determined to ensure safe and proper use of the product and to
prevent personal injury and property damage. This manual uses two terms, “Warning”and “Caution”,
according to the hazard level, to clearly indicate the extent and severity of the risk.
Both “Warning”and “Caution”indicate important safety instructions. Please be sure to follow them.
Indicates an imminently hazardous situation that, if not avoided, may
result in serious injury or death.
Indicates a potentially hazardous situation that, if not avoided, may result
in minor to moderate injuries or product damage.
Indicates a “prohibited”action that must not be carried out.
Indicatesa“mandatory”action that must be carried out.
NOTES TO USERS
This manual is designed to show an appropriate usage of the products for transportation, storage,
installation, operation and maintenance. Be sure to read through this manual before handling the products.
This manual does not cover the whole scope of conceivable usage of the products for transportation,
storage, installation, operation and maintenance. If technical assistance beyond the scope of this manual is
required, contact KITZ Corporation or its distributor.
The specifications have been determined with safety considerations. Do not use the products beyond the
specifications.
The illustrations given in this manual do not show all the details. If more detailed information is required,
refer to the relevant approved drawings.
*Any information provided in this operation manual is subject to change without prior notice.

Document No.: KE-2033-00
Contents
Ⅰ. Construction and Design Features ・・・・・・・・・・・・・・・・・・・・ 1
Ⅱ. Valve Operating Device ・・・・・・・・・・・・・・・・・・・・・・・・・・・・・・・・・・・7
Ⅲ. Transportation and Storage ・・・・・・・・・・・・・・・・・・・・・・・・・・・ 10
Ⅳ. Valve Installation ・・・・・・・・・・・・・・・・・・・・・・・・・・・・・・・・・・・・ 13
Ⅴ. Valve Operation ・・・・・・・・・・・・・・・・・・・・・・・・・・・・・・・・・・・ 18
Ⅵ. Periodic Inspection ・・・・・・・・・・・・・・・・・・・・・・・・・・・・・・・・・・・ 23
Ⅶ. Disassembly and Reassembly ・・・・・・・・・・・・・・・・・・・・・・・・・ 27

Document No.: KE-2033-00 1/33
Ⅰ. Construction and Design Features

Document No.: KE-2033-00 2/33
Ⅰ. Construction and Design Features
1. Construction and Function
1.1 A typical construction of the SCHBSL type butterfly valves (lug type) is as shown below.
1.2 Rotation of the stem by 90°opens and closes the valve.
1.3 Designed for use in the fully open, fully closed, or intermediate position for flow control.
1.4 Double offset structure is adopted for smooth opening and closing operation.
1.5 Both direct flow and reverse flow can be shut off. However, the flow from the retainer side is
recommended.
This illustration shows a typical construction.

Document No.: KE-2033-00 3/33
Ⅰ. Construction and Design Features
2. Features
2.1 Seat structure for both flows
Sheet structure for both flows to maintain stable sealing performance.
2.2 Long life RPTFE seat ring
Filler-containing fluororesin (RPTFE) which has long endurance performance as well as low friction and
wear coefficients is adopted as the seat material. The seats have high durability and they are available
for a variety of fluids. See the KITZ catalog for details.
2.3 Retightening of gland bolts
Gland bolts can be retightened quickly by directly applying a spanner to the gland bolts which are
located between the upper part of the valve and the operating lever or gear unit.
.
2.4 Face-to-face dimensions
The face-to-face dimensions comply with MSS SP-68(API609 Class300).
However, NPS 21/2B, 5B are the KITZ standard.
Retightening of gland bolt
Gland packing
Gland
Gland bolt

Document No.: KE-2033-00 4/33
Ⅰ. Construction and Design Features
2.5 Bidirectional flow
This valve can be used for shutting off both the direct flow and reverse flow. However, in order to avoid
the deterioration of the seat sealing performance, please use this valve to seal a recommended flow
direction.
3. Specifications and Pressure-Temperature Rating
3.1 Specifications
3.1.1 Maximum service pressure
5.1 MPa (740psi)
3.1.2 Temperature range of service fluid
For use in air conditioning ----- -29 〜 + 100℃ ( -20 〜 212 ℉)
For API PT ratings ----------- -29 〜 + 204℃ ( -20 〜 400 ℉)
* Refer to P-T rating chart for more details. (No freezing of fluid)
3.1.3 Applicable flange
ASME B16.5 Class 300
3.2 Pressure –Temperature Rating (P-T Rating)

Document No.: KE-2033-00 5/33
Ⅰ. Construction and Design Features
4. Size and Number of Piping Bolt and Nut (Hexagon Bolt)
The bolt length is the length when gasket and steel flange are used.
4.1 StudBolts&Nuts unit : mm (inch)
Flange ASME Class300
STUDS&NUTS (NOTE 1 )
valve Thread L1 L2
Length Length
size size qty mm inch
qty mm inch
21/2 3/4-10UNC 8 75 3 8 75 3
3 3/4-10UNC 8 80 3.25 8 80 3.25
4 3/4-10UNC 8 90 3.5 8 90 3.5
5 3/4-10UNC 8 95 3.75 8 90 3.5
6 3/4-10UNC 12 95 3.75 12 95 3.75
8 7/8- 9UNC 12 115 4.5 12 110 4.25
10 1- 8UNC 16 130 5 16 120 4.75
12 11/8- 8UN 16 140 5.5 16 130 5
Note 1) Nut: ASME B18.22 Heavy Hex Nut
4.2 Machine Bolts unit : mm (inch)
Flange ASME Class300
MACHINE BOLTS (NOTE 2 )
valve Thread L1 L2
Length length
size size qty mm inch
qty mm inch
21/2 3/4-10UNC 8 48 1.875 8 48 1.875
3 3/4-10UNC 8 50 2 8 50 2
4 3/4-10UNC 8 55 2.25 8 55 2.25
5 3/4-10UNC 8 65 2.625 8 60 2.375
6 3/4-10UNC 12 70 2.75 12 65 2.5
8 7/8- 9UNC 12 80 3.125 12 75 3
10 1- 8UNC 16 90 3. 5 16 85 3.375
12 11/8- 8UN 16 100 4 16 90 3.5
NOTE2) Bolt lengths are set based on the following conditions
・Gasket thickness of 1.6mm (0.06 inches).
・Minimum flange thickness of weld neck flanges per ASME B16.5

Document No.: KE-2033-00 6/33
Ⅰ. Construction and Design Features
5. Pipes for Piping
The pipes shown in the table below with a mark “〇”are applicable when the valve is installed to the
welded flanges. Or the flanges shall be larger than the minimum pipe inside diameter.
6. Gaskets for Piping
● Installation of gasket between the pipe flange and the valve is required. Use the gasket as
shown below.
【 Gasket Type 】
・Joint seat gasket made of non-asbestos materials
・Tetrafluoroethylene (filler-containing) resin seat gasket
・PTFE wrapping gasket
・Spiral wound gasket
【 Gasket Configuration 】
・Full face gasket for flat face or raised face flange
【 Dimension】
・Compliance with ASME
Thickness of seat gasket shall be 1.5 mm (0.06 inches) and above.
Minimum inside
diameter of pipe
Nominal valve Size
(NPS) Sch XS
mm inch
2-1/2 ○ 53 2.07
3 ○ 73.5 2.88
4 ○ 93 3.66
5 ○ 121 4.74
6 ○ 143 5.63
8 ○ 191 7.51
10 ○ 236 9.27
12 ○ 286 11.25

Document No.: KE-2033-00 7/33
Ⅱ. Valve Operating Device

Document No.: KE-2033-00 8/33
Ⅱ.Valve Operating Device
1. Lever Handle Type
1.1 A lever handle is directly mounted to the valve.
1.2 Turning the lever handle by 90 degrees clockwise will close the valve, and turning the lever handle by
90 degrees counterclockwise will open the valve.
Recommended flow directio
n
Recommended flow direction
Open
Close

Document No.: KE-2033-00 9/33
Ⅱ.Valve Operating Device
2. Gear Type
2.1 A gear operator (reduction gear) is mounted to the valve.
2.2 According to the letter or arrow on the handwheel, turning the handwheel clockwise will close the valve
and turning the handwheel counterclockwise will open the valve.
2.3 The handwheel operating torque varies between the fully closed position and fully open position and
with the valve size.
2.4 The gear operator is a device to transmit a large torque to the valve stem by converting the torque
from the drive shaft by means of the reduction gears.
Recommended flow direction
Open Close

Document No.: KE-2033-00 10/33
Ⅲ. Transportation and Storage

Document No.: KE-2033-00 11/33
Ⅲ. Transportation and Storage
1. Transportation
1.1 Precautions
● Keep off the valve lifting area to prevent personal injury when a valve is lifted for
removal or installation.
● Take care not to damage the painted surfaces of the valve. Repair the damaged
portions as required to prevent corrosion.
● Pay attention to handling and storage of carton-packaged products. High humidity may
damage the carton and the product.
1.2 Transportation
1.2.1 Keep valves in the original packages during transportation and until just before installation.
If the dustproof/protection cover comes off or it is lost during transportation, immediately take
measures for valve protection.
1.2.2 Never apply any excessive impact to the valve by throwing, dropping, or dragging it.

Document No.: KE-2033-00 12/33
Ⅲ. Transportation and Storage
2. Storage
2.1 Precautions
● DO NOT store the valve in a corrosive environment. It may cause corrosion in the
threaded portions of the valve.
● DO NOT remove the dustproof/protection cover until just before the installation. Take
measures to prevent dust from entering the valve and damaging the internal parts such
as seat ring.
● DO NOT apply any heavy load to the valve. Overloading may damage the valve
● DO NOT pile up the products carelessly. The products may be damaged and personal
injury may occur due to the collapse of cargo.
2.2 Storage
2.2.1 Store valves in a dust-free and well ventilated indoor area with low humidity, avoiding direct sunlight.
2.2.2 Store valves in box and put it on a pallet or rack. Storing valves directly on the ground or concrete
floor shall be avoided.
2.2.3 When valves are stored outdoors unavoidably, protect them from rain, direct sunlight or dust with a
waterproof sheet.

Document No.: KE-2033-00 13/33
Ⅳ. Valve Installation

Document No.: KE-2033-00 14/33
Ⅳ. Valve Installation
1. Precautions for Installation
● Check the valve specifications with the catalog and/or the attached nameplate. The
valve trim and seat materials determine the operating pressure, fluid and the
temperature range. When the valve is used beyond the specifications, it may result in
failure such as leakage.
● Keep a secure footing when removing and mounting a valve.
● Sufficient lighting shall be provided for valve installation.
● Use a support stand when the valve is heavy.
● DO NOT directly install the valve to a check valve or pump. The disc may hit against
the connecting device and cause damage to the disc.
1.1 Allow sufficient space for operation, installation, disassembly and subsequent maintenance of the valve.
1.2 For a smooth operation, inspection and maintenance, take appropriate measures for the valve installed in
a small space.
1.3 Valves shall not be installed in a place where valve functions may be hampered by the outer forces such
as vibrations.

Document No.: KE-2033-00 15/33
Ⅳ. Valve Installation
2. Precautions for Piping
● Install the valve after the flanges and pipe weld connections have been completely cooled
down.
● Edges of the flange welded areas shall be thoroughly chamfered to protect the valve surface.
● Remove any foreign objects such as sand, dust and weld spatter from the connecting piping.
● Flange surfaces shall have no damage, deformation or irregularities.
● Align the upstream side flanges and the downstream side flange accurately. Inaccurate
alignment may cause pipe leakage.
● Install the valve so that the arrow on the body show the flow direction as shown below.
In the case the valve is used for bidirectional flow service, the arrow shall show the flow
direction from the side with the higher differential pressure.
● Make sure to install a new gasket when installing a valve.
● Installation to stub end flanges (wrap joint, stainless steel pipe fittings with collared end) is not
allowed.
● Install or remove the valve with the valve in the fully closed position.
● Retighten the gland bolts properly so that the valve operating force does not become too
great. Tighten the gland bolts alternately with an even force to avoid over-tightening. If
leakage is observed from the gland section due to stress relaxation, retighten the gland bolts.
● If insulation of the valve is necessary, insulate the valve not to cover the gland section so that
the gland bolts can be retightened.
Low pressure (downstream)
side when valve is fully
closed
High pressure (upstream)
side when valve is fully
closed

Document No.: KE-2033-00 16/33
● Lug type butterfly valves are available to use the dead end service on following conditions.
a)Non-shock water
b)Lever or gear operated type(not automatic operated type)
c)Maxmum pressure;Full working pressure of the valve
d)To be locked on full closed position
e)Within 4 days(Note1)
Note1)It is recommended to use the blank flange for long period of time beyond 4 days.
If the valve is used beyond of these conditions,it may cause the external leakage.
● When leakage occurs near the retainer bolt in the dead-end service in the reverse flow
direction.
Retighten the retainer bolt with a hexagonal wrench using the tightening torque shown in the
table below.
If the leakage does not change even after retightening, replace the sheet after removing the
fluid from the piping.
Retainer Bolt Opposite side
dimension B Tightening torque
VALVE SIZE
(NPS) (nominal diameter) mm inch Nm lbf・in
21/2〜3 M4 3 0.118 3.5 31
4 M5 4 0.157 7 62
5-6 M6 5 0.197 12 106
8 M8 6 0.236 30 266
10-12 M10 8 0.315 55 487
Reverse pressure dead-ended service

Document No.: KE-2033-00 17/33
Ⅳ. Valve Installation
3. Installation
3.1 Set jack bolts, if required, to adjust the dimension between the pipe flanges. The dimension between the
pipe flanges shall be 6 to 10 mm (0.2 to 0.4 inch) wider than the face-to-face dimension of the valve.
3.2 [When sandwiching the valve between the flanges on both
sides]
Install the valve between the flanges. Set two bolts and nuts
in the lower section temporarily and insert a gasket to each
side of the valve. Then set two bolts and nuts in the upper
section temporarily.
[when mounting for each flange on one side]
Adjust the valve to the flange.Temporarily tighten the two
lower bolts, insert a gasket between the valve and the flange,
and temporarily tighten the two upper bolts.
3.3 Loosely tighten two upper bolts and two lower bolts. Adjust
the valve in the correct position.
3.4 Before tightening the bolts for piping, fully open the valve and
make sure that the disc does not hit against the inside of the
flanges.
3.5 Attach all of the remaining bolts and nuts.
3.6 Tighten the bolts evenly and alternately to avoid uneven
tightening.
3.7 Raise the line temperature and pressure gradually during the
test operation. Retighten the bolts as required.
sandwiching between the flanges
on both sides
mounting for each flange on one side
Table of contents
Other Kitz Control Unit manuals
Popular Control Unit manuals by other brands
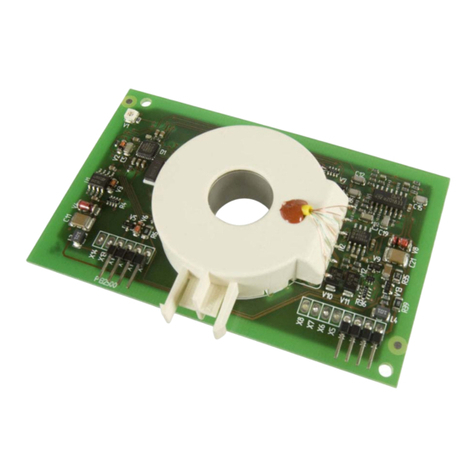
Bender
Bender RCMB103 operating manual
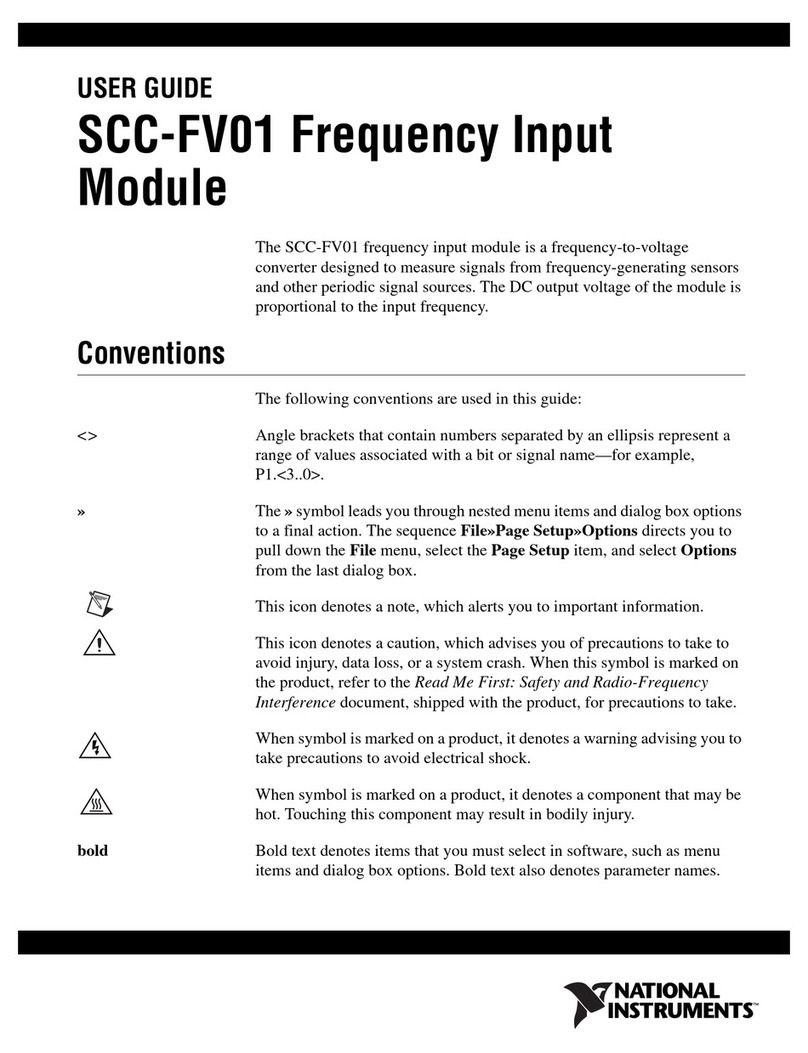
National Instruments
National Instruments SCC-FV01 user guide
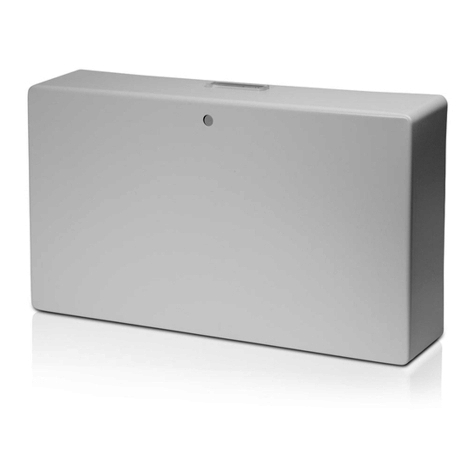
Feig Electronic
Feig Electronic ID ISC.ANT.U500/270 installation manual
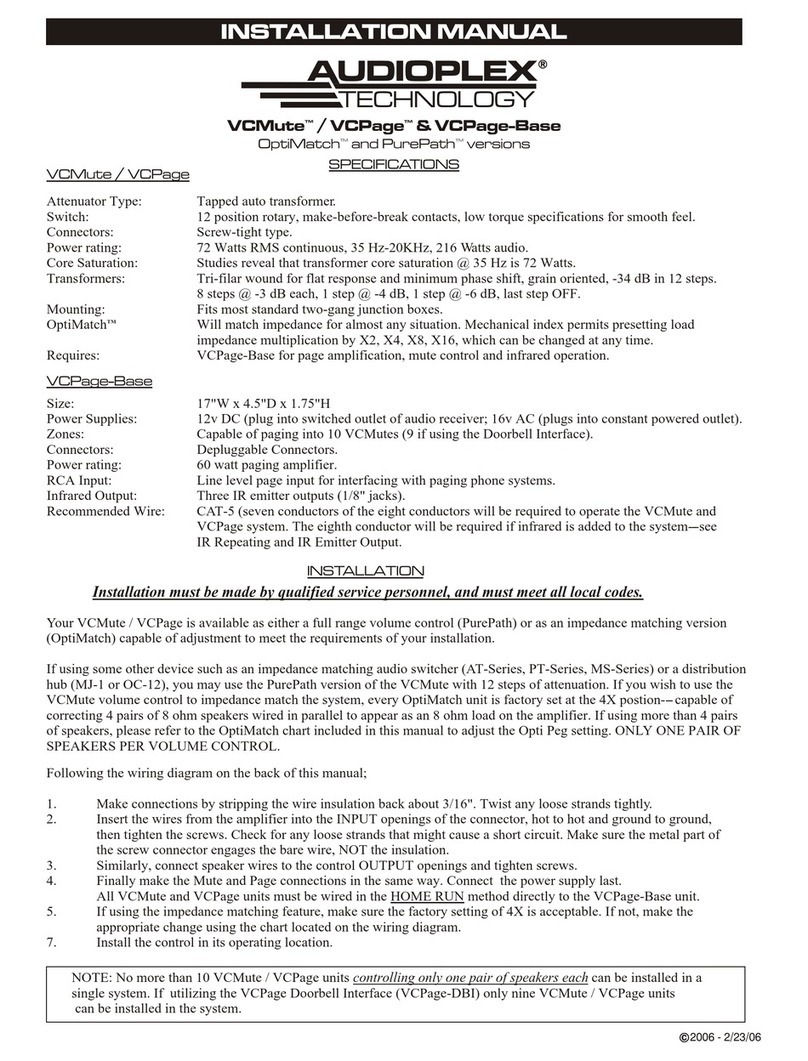
Audioplex
Audioplex VCMute installation manual
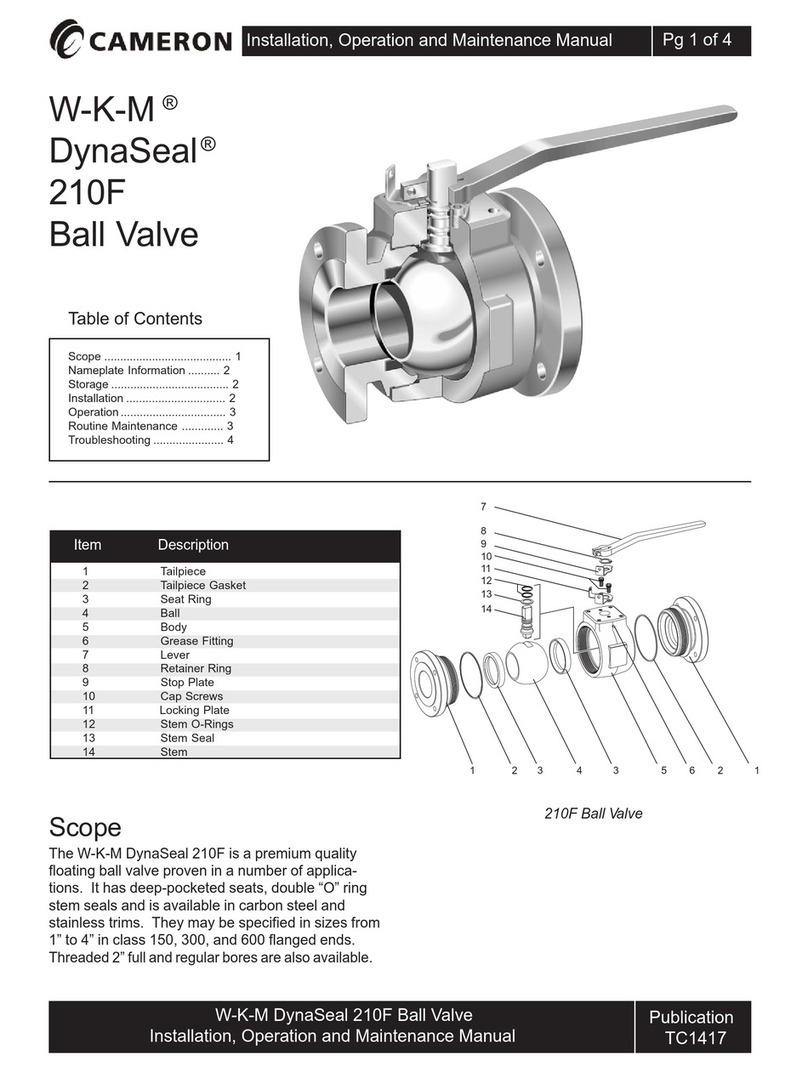
Cameron
Cameron W-K-M DynaSeal 210F Installation, operation and maintenance manual
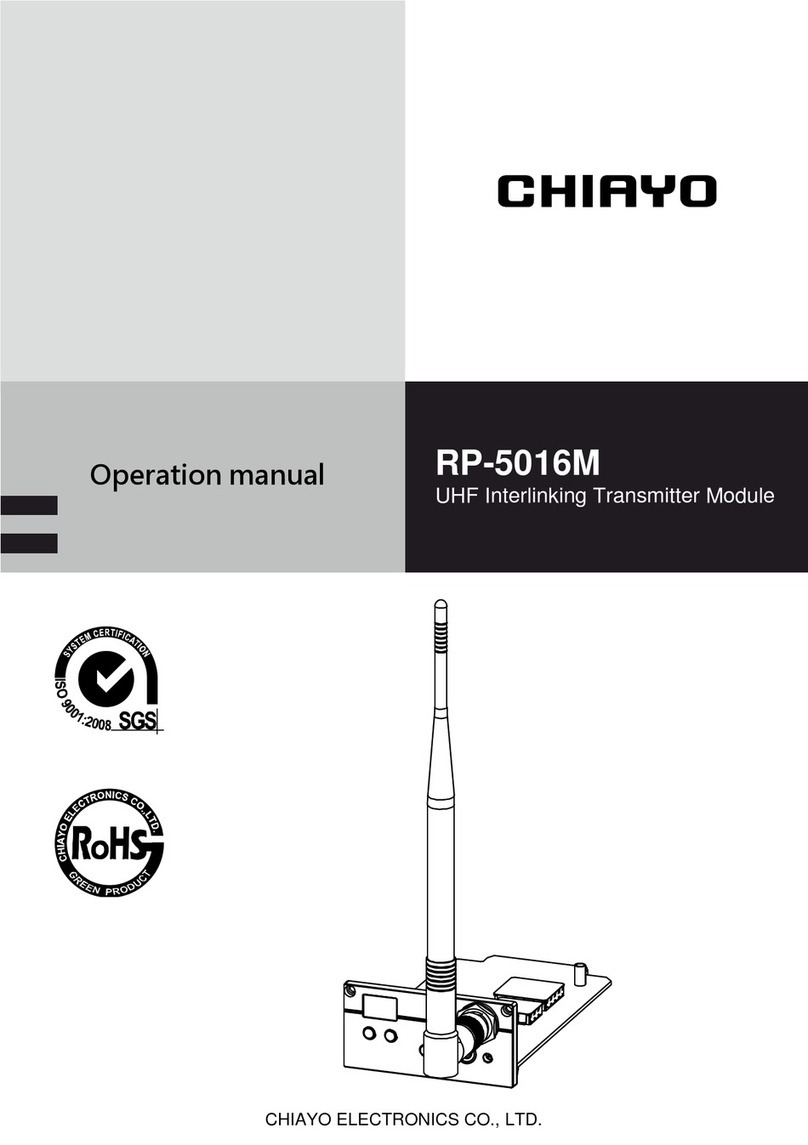
Chiayo
Chiayo RP-5016M Operation manual