Kitz SGE User manual

Document No.: KE-2032-01
Operation Manual
For
SGE Type Butterfly Valves
Thank you for choosing KITZ products.
For safe and trouble-free function and performance of the product, make sure
to read and understand all of the items included in this manual before valve
mounting and operation. Keep this manual in a convenient place and accessible
to the valve operating personnel.

Document No.: KE-2032-01
This manual applies to the KITZ SGE type butterfly valves.
For electric or pneumatic valve operation, refer to the operation manual prepared by the manufactures of
the relevant valve actuators.
SAFETY CAUTIONS
For the safe use of the product, read all of the safety precautions in this manual before handling the product.
The safety precautions in this manual are determined to ensure safe and proper use of the product and to
prevent personal injury and property damage. This manual uses two terms, Warning and Caution,
according to the hazard level, to clearly indicate the extent and severity of the risk.
Both Warning and Caution indicate important safety instructions. Please be sure to follow them.
Indicates an imminently hazardous situation that, if not avoided, may
result in serious injury or death.
Indicates a potentially hazardous situation that, if not avoided, may result
in minor or moderate injury and product damage.
Indicates a careful attention.
Indicates a prohibited action that must not be carried out.
Indicates a mandatory action that must be carried out.
NOTES TO USERS
This manual is designed to show an appropriate usage of the products for transportation, storage,
installation, operation and maintenance. Be sure to read through this manual before handling the
products.
This manual does not cover the whole scope of conceivable usage of the products for transportation,
storage, installation, operation and maintenance. If technical assistance beyond the scope of this
manual is required, contact KITZ Corporation or its distributors.
The specifications have been determined with safety consideration. Do not use products beyond the
specifications.
The illustrations given in this manual do not show all the details. If more detailed information is required,
refer to our relevant valve assembly drawings.
*Any information provided in this operation manual is subject to change without prior notice.

Document No.: KE-2032-01
Contents
I. Construction and Design Features
1. Construction and Function・・・・・・・・・・・・・・・・・・・・・・・・・・・・・・・・・・2
2. Product Coding ・・・・・・・・・・・・・・・・・・・・・・・・・・・・・・・・・・・・・・・・・・・・3
3. Design Features・・・・・・・・・・・・・・・・・・・・・・・・・・・・・・・・・・・・・・・・・・・・3
4. Specifications・・・・・・・・・・・・・・・・・・・・・・・・・・・・・・・・・・・・・・・・・・・・・・4
5. Piping Couplings・・・・・・・・・・・・・・・・・・・・・・・・・・・・・・・・・・・・・・・・・・・・4
II. Transportation and Storage
1. Precautions・・・・・・・・・・・・・・・・・・・・・・・・・・・・・・・・・・・・・・・・・・・・・・・・6
2. Transportation ・・・・・・・・・・・・・・・・・・・・・・・・・・・・・・・・・・・・・・・・・・・・・7
3. Storage・・・・・・・・・・・・・・・・・・・・・・・・・・・・・・・・・・・・・・・・・・・・・・・・・・・・7
III. Valve Installation
1. Precautions・・・・・・・・・・・・・・・・・・・・・・・・・・・・・・・・・・・・・・・・・・・・・・・・9
2. Before Installation ・・・・・・・・・・・・・・・・・・・・・・・・・・・・・・・・・・・・・・・・・・10
IV. Valve Operation
1. Precautions・・・・・・・・・・・・・・・・・・・・・・・・・・・・・・・・・・・・・・・・・・・・・・・・12
2. Lever Handle Type ・・・・・・・・・・・・・・・・・・・・・・・・・・・・・・・・・・・・・・・・・13
3. Gear Type ・・・・・・・・・・・・・・・・・・・・・・・・・・・・・・・・・・・・・・・・・・・・・・・・・14
4. Daily Inspection ・・・・・・・・・・・・・・・・・・・・・・・・・・・・・・・・・・・・・・・・・・・・15
V. Periodic Inspection
1. Precautions・・・・・・・・・・・・・・・・・・・・・・・・・・・・・・・・・・・・・・・・・・・・・・・・17
2. Inspections ・・・・・・・・・・・・・・・・・・・・・・・・・・・・・・・・・・・・・・・・・・・・・・・・18

Document No.: KE-2032-01 1/18
I. Construction and Design Features

Document No.: KE-2032-01 2/18
O ring
(EPDM/NBR)
Disc
(DUCTILE IRON+EPDM/NBR)
Body
(DUCTILE IRON+NYLON)
Disc
(DUCTILE IRON+EPDM/NBR)
O ring
(EPDM/NBR)
Bearing
(METAL BACKED PTFE)
Bottom stem
(SUS420J2Q)
End plate
(CARBON STEEL)
Bearing
(METAL BACKED PTFE)
Body
(DUCTILE IRON+NYLON)
Bottom stem
(SUS410/SUS420J2)
Plug
(ZDC2)
I. Construction and Design Features
1. Construction and Function
1.1The valve construction and the part names are as shown below.
1.2 Rotation of the stem by 90°opens or closes the valve.
1.3 Designed for use in fully open position, fully closed position, or half-open position. *
1.4 A center drive mechanism is provided.
1.5 Bi-directional flow is possible.
* Cavitation may occur if the valve is used with the slightly open position.
Contact KITZ if the valve is required to be used in the slightly open position.
Nominal size 50 to 200A
Bearing
(POLYACETAL)
Stem
(SUS410
/SUS420J2Q)
Bush
(STAINLESS STEEL)
Stem
(SUS420J2Q)
Gland plate
(CARBON STEEL)
Nominal size 250 to 300A

Document No.: KE-2032-01 3/18
I. Construction and Design Features
2. Product Coding
N: NBR
Operator No indication: hand lever, G: worm gear
Nominal pressre: 300psi
CE 100 Nominal size (mm)
G-300SGE
Seat material CE: Chlorine resistant EPDM
Type: SGE Type
3. Design Features
3.1 The external surface and the wetted surface of the body are nylon-lined to prevent corrosion.
3.2 A rubber lined disk is installed.
3.3 The face-to-face dimensions comply with MSS SP-67.
3.4 The actuator mounting flanges comply with ISO 5211.
3.5 The stem is designed to be blow-out proof so that the stem does not protrude even the operator is
removed.
3.6 Double sealing is provided to the stem section to prevent external leakage.
3.7 Long neck design for easier installation of 50 mm insulation.
3.8 Grooved dimensions comply with AWWA C606-15.
3.9 Chlorine resistant EPDM is used for the longer life time of the valve. (Only SGECE: EPDM Seat)

Document No.: KE-2032-01 4/18
I. Construction and Design Features
4. Specifications
4.1 Maximum service pressure : 2.1 MPa (300 psi)
4.2 Temperature range of service fluid
EPDM Seat : -20℃ to +110℃
(Continuous service temperature range : 0℃ to +100℃)
NBR Seat : 0℃ to +70℃
4.3 Pressure ‐Temperature rating
Pressure-Temperature Rating
Pressure [MPa]
2.1 SGECE
SGEN
-20 1100Temperature [℃]
70
5. Piping Couplings
Use conformable couplings with AWWA C606-15.

Document No.: KE-2032-01 5/18
II. Transportation and Storage

Document No.: KE-2032-01 6/18
II. Transportation and Storage
1. Precautions
(1) Do not come close to the valve lifting area.
(2) Use a hanging bolt or hold the valve neck section securely for lifting. Using the lever
handle or handwheel for lifting may damage the product by falling down.
(3) Do not give any impact to the valve by dropping, throwing or dragging.
(4) Do not pile up valves for storage. Unstable piling may
damage the valves or cause personal injury.
(5) Do not store the valve with the carton boxkept open. The valve function may be impaired due to the
intrusion of foreign objects.
(6) Do not expose packaged valves to rainwater, etc. High humidity may
deteriorate the package.
(7) Store valves in a dry and well-ventilated indoor place.

Document No.: KE-2032-01 7/18
II. Transportation and Storage
2. Transportation
2.1 Keep valves in the original packages during transportation and until just before installation.
2.2 High humidity may damage the strength of carton cases. Care shall be taken when handling such
deteriorated carton cases.
2.3 Take care not to damage painted valve surfaces during transportation. Repair the damaged surface to
prevent corrosion.
3. Storage
3.1 Place the packaged valves on the pallet, etc., for storage. Placing packaged valves directly on the ground
or concrete floor must be avoided.
3.2 Do not store valves in a corrosive environment. It may cause corrosion on the threaded areas, leading to
a malfunction of valve.
3.3 Do not place any objects on valves, or do not step on them. Overloading may damage the valve.

Document No.: KE-2032-01 8/18
III. Valve Installation

Document No.: KE-2032-01 9/18
III. Valve Installation
1. Precautions
(1) Check the valve specifications with the identification plate or the tag as well as the
relevant product catalog and ensure that the exact valve specified in the piping
arrangement plan is provided. The service fluid, pressure, temperature, etc., determine
the compatibility of the disc and seat materials. Incorrect application of valve could
cause accidents such as internal leakage.
(2) Do not attach butterfly valves directly to check valves or pumps. Contact of the disc
of the butterfly valve during operation may damage the valve.
(3) Do not install the valve close to the downstream side of an elbow pipe, a reducer, a
flow-regulation valve because the flow rate of these devices may quickly change.
Contact KITZ if such installation is required.
(4) When installing the valve to the outlet of a pumping system, align the operator position
as shown below. Incorrect orientation may damage the valve due to the differential of the
flow rate in the pipes.
(5) Where the piping system turns, ensure to mount the valve as shown below. Please
contact KITZ for details.
(6) Clean the EPDM seats with synthetic detergent to make them oil-free. Otherwise,
the EPDM seats may deteriorate and cause leakage.
Pump shaft Vortex pump
Lon
g
itudinal axis
Pump shaft
Vortex pump
Horizontal axis
Pump shaft
Vortex flow pump

Document No.: KE-2032-01 10/18
III. Valve Installation
(7) Install or remove the valve with the disc properly positioned within the
face-to-face dimension. If the valve is installed or removed when the valve is in the
open position, sealing section of the disc may be damaged resulting in leakage.
(8) When performing a pressure test with pressure higher than its maximum allowable
service pressure, the valve shall be in the fully open position. If a pressure test is
performed with the valve in the fully closed position, the valve may be damaged.
2. Before Installation
2.1 Allow sufficient room for operation, installation, disassembly and subsequent maintenance work with
consideration for the valve size and the stem direction.
2.2 Take appropriate measures for valves which are required to be installed in a confined space.
2.3 Keep a secure footing when removing and installing valves.
2.4 Provide adequate lighting for valve operation.
2.5 Provide appropriate piping supports to avoid excessive load on the pipes.
2.6 Do not install valves where vibration or other forces may hamper the valve function.

Document No.: KE-2032-01 11/18
IV. Valve Operation

Document No.: KE-2032-01 12/18
IV. Valve Operation
1. Precautions
(1) Do not loosen the bolts on the piping section and the operating section while the
valve is under operation and pressurized. Otherwise, it may cause an accident
resulting in injury or death.
(2) If an actuator is mounted on the valve, make sure to thoroughly read the
instruction manual of the actuator before operating the valve.
(3) Do not touch the stopper bolt on the gear operator carelessly. Positional
displacement of the valve closed position may cause seat leakage.
(4) When using the valve in the slightly open position, it may cause cavitation
resulting in vibration, noise or valve damage. Contact KITZ for technical advice.
(5) Valves equipped with manual operator such as a lever handle, or a handwheel must
be manually operated. Application of an excessive force may result in malfunction of the
valve and the manual operator.
(6) Wear protective gear such as goggles, gloves and safety footwear when
performing operations.
(7) Take safety measures against toxic, flammable or corrosive fluids.

Document No.: KE-2032-01 13/18
IV. Valve Operation
2. Lever Handle Type
Operate the lever handle after releasing the clutch by gripping the stop lever.
Operate the lever handle clockwise to close the valve and counterclockwise to open the valve as shown
below.
When fully closed or fully open operation is required, turn the lever handle with the stop lever gripped until
the lever handle contact with the index plate. The maximum operating angle of the lever handle from the fully
open position to the fully closed position is 90 degrees.
Make sure that the clutch on the stop lever is properly hooked in the groove on the index plate.
C
l
utc
h
[Open]
[Close]
Lever handle
Index plate
Flow direction
Stop lever
90°

Document No.: KE-2032-01 14/18
IV. Valve Operation
3. Gear Type
The valve is operated by turning the handwheel according to the indication, such as an arrow or letters,
namely rotating the handwheel clockwise to close or counterclockwise to open the valve.
Note)
1. The gear operator is a device to transfer a large torque to the valve stem by converting the torque from
the drive shaft by means of the speed reduction gearing mechanism.
2. The handwheel operating torques vary with a number of factors, such as the valve opening position, valve
sizes and working pressures.
Open Close

Document No.: KE-2032-01 15/18
IV. Valve Operation
4. Daily Inspection
Carry out daily maintenance and inspections on the valves in use.
Inspection items are as shown below.
Problems Areas to be inspected Inspection
method Remedies
Pipe connections Visual check
Soap water Retighten the bolts and nuts.
External leakage
Valve surface Visual check
Soap water Replace the valve.
Valve body Auditory check Consult a piping engineer.
Bolted sections
(looseness) Auditory check Retighten the bolts and nuts.
Abnormal noise
Pipes (vibration) Auditory check Consult a piping engineer.
Loosening of bolts
and nuts Bolted sections Visual check
Tactile check Retighten the bolts and nuts.
Seat leakage - - Remove foreign objects from the valve.
Disassemble and inspect the valve.
Replace the valve seats.
Valve
open/closed position Visual check Make sure that the valve is in the
predetermined operating position.
Operational
failure
Lever handle or
Handwheel of gear
operator
Tactile check
Auditory check Disassemble and inspect the valve.
Replace the valve.

Document No.: KE-2032-01 16/18
V. Periodic Inspection

Document No.: KE-2032-01 17/18
V. Periodic Inspection
1. Precautions
(1) Do not loosen the bolts on the piping section and the operating section while the
valve is under operation and pressurized. Otherwise, it may cause an accident
resulting in injury or death.
(2) Do not touch the dismounted valve used for toxic or explosive fluid service.
Adequate safety measures shall be taken when dismounting and disassembling valves.
Safety measures shall be also taken when storing or disposing of valves used for toxic
or explosive fluid service. They shall be kept away from unauthorized personnel.
(3) Keep off the valve lifting area to prevent personal injury when transporting valves.
(4) Carry out periodic inspections on the valves in operation by referring to the
appropriate section in the operation manual.
(5) Wear protective gear such as goggles, gloves and safety footwear.
(6) Keep a secure footing when removing and installing valves.
(7) When dismounting or mounting the valve, use appropriate piping supports to avoid
displacement of the pipes.
Table of contents
Other Kitz Control Unit manuals
Popular Control Unit manuals by other brands
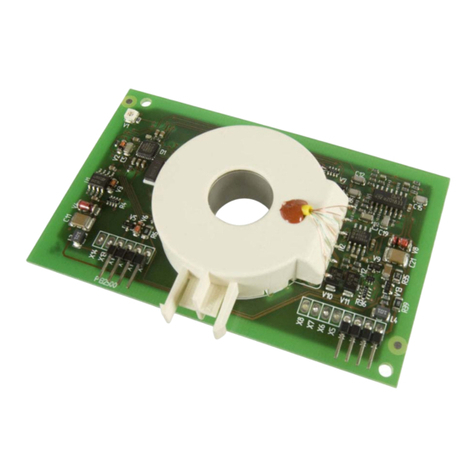
Bender
Bender RCMB103 operating manual
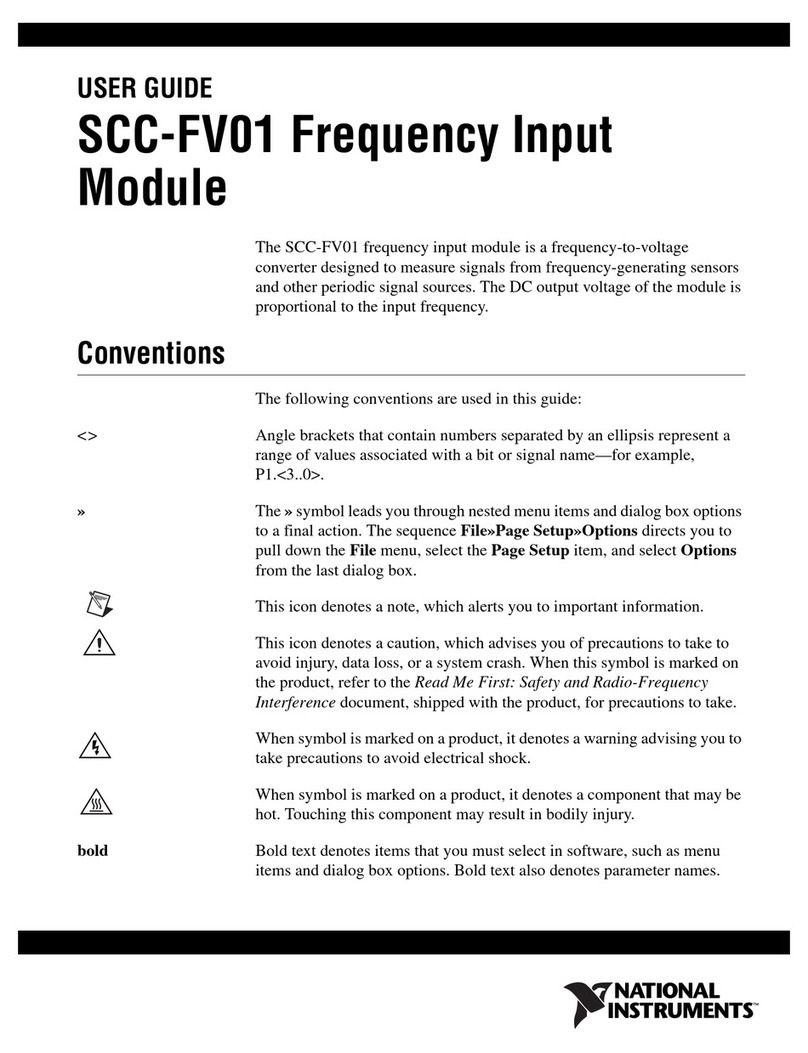
National Instruments
National Instruments SCC-FV01 user guide
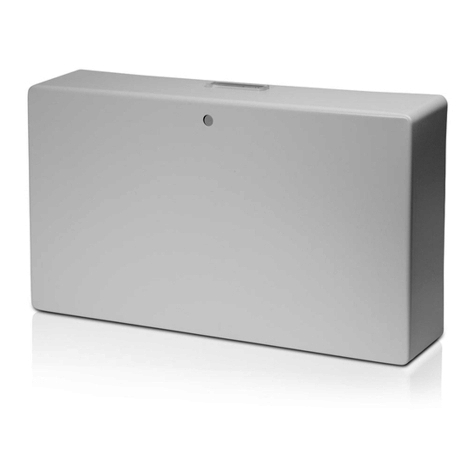
Feig Electronic
Feig Electronic ID ISC.ANT.U500/270 installation manual
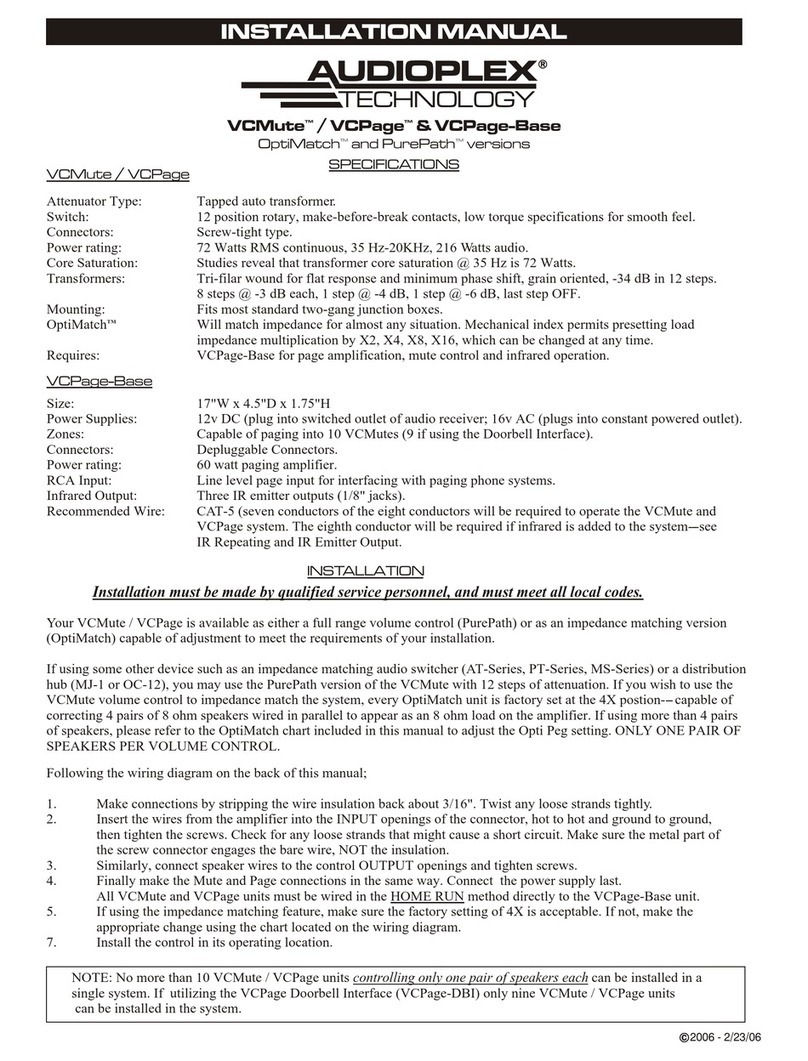
Audioplex
Audioplex VCMute installation manual
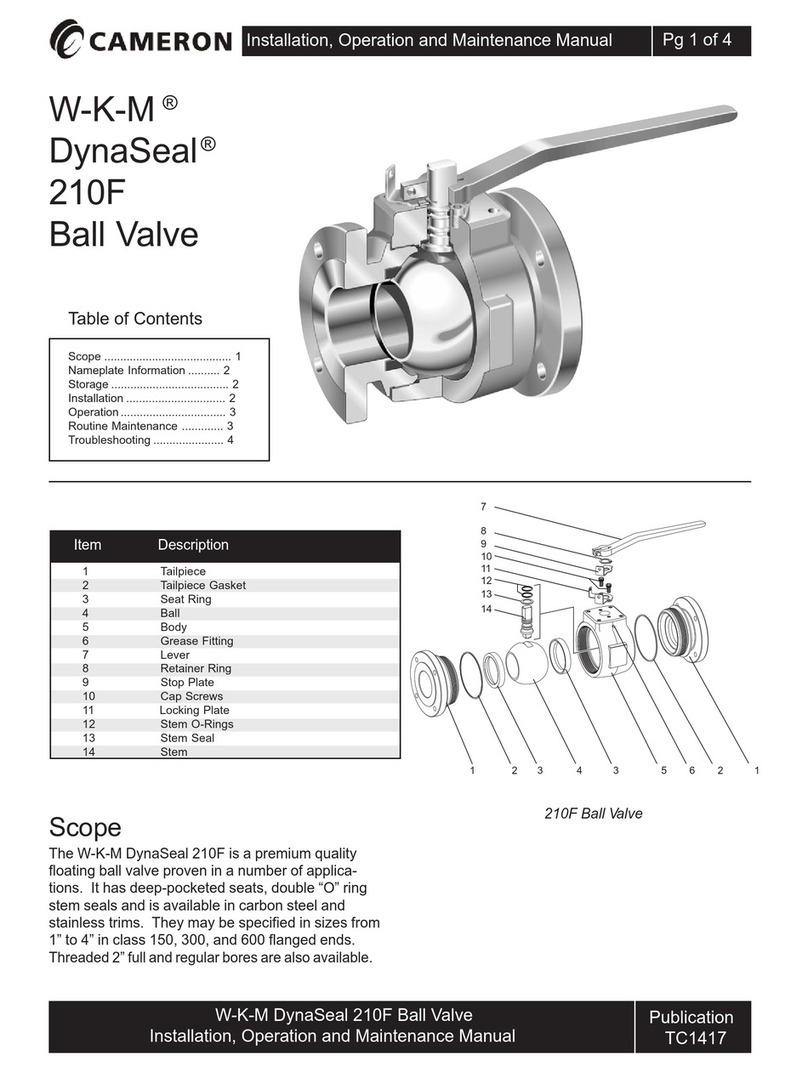
Cameron
Cameron W-K-M DynaSeal 210F Installation, operation and maintenance manual
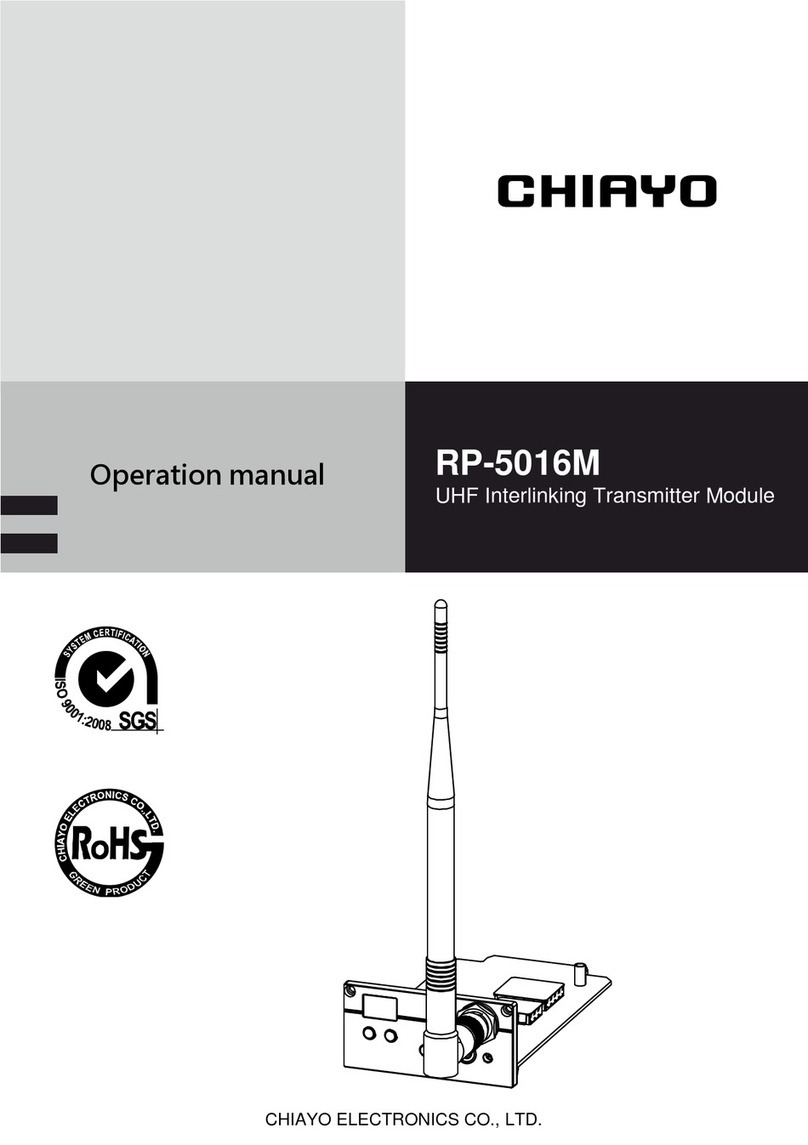
Chiayo
Chiayo RP-5016M Operation manual