Marvair CoolLinks NextGen User manual

1
NG-IOM-ATT Release 1.2 July 12, 2019
NextGen CoolLinks™ HVAC Controller
Installation & Operations Manual
This product manual describes the steps to install and operate the Marvair®NextGen CoolLinks™ HVAC controller. The
information contained in this manual is to be used as a guide only. This manual does not supersede or circumvent any
applicable national or local codes.
If you are installing the controller, scan the entire manual before starting work. The HVAC units should be installed before
the NextGen CoolLinks™ controller. For the installation instructions for the Marvair units, please contact Marvair. The
latest versions of all literature including the manuals can be downloaded from the Marvair customer portal on the Airxcel
website at www.airxcel.com.
Marvair®, Division of Airxcel™, Inc.
156 Seedling Dr. Cordle, GA. 31015
(229) 273-3636

2
NG-IOM-ATT Release 1.2 July 12, 2019
Table of Contents
Chapter 1 Materials Required for Installation…………………………………………………….4
Chapter 2 CoolLinks Overview…………………………………………………………………………....4
2.1 Equipment Architecture
2.2 Cooling Control
2.3 Heating Control
2.4 DAC/WAC Standalone Operation
2.5 System Interlocks
Chapter 3 Mechanical Installation……………………………………………………………………….8
3.1 Control Enclosure
3.2 Inside Temperature & Humidity Sensor
Chapter 4 Electrical Installation…………………………………………………………………………10
4.1 Electrical Connection Overview
4.2 Control Power (48 VDC)
4.3 Inside Temperature & Humidity Sensor
4.4 DAC/WAC unit
4.5 HVAC Units
4.6 Smoke Detector, Hydrogen Detector, Generator Running
4.7 RBS Alarms
4.8 Bonding
Chapter 5 Operator Interface……………………………………………………………………………..19
5.1 LCD Message Display
5.2 Wi-fi Hot Spot
5.3 Main Web Page
5.4 Cooling & Heating Set Points
5.5 DAC/WAC Unit Control
5.6 DX Menu
5.7 DX Unit Control
5.8 Blower Settings
5.9 Sensor Info
5.10 Alarms
5.11 Event Log
5.12 System Config
5.13 System Info
5.14 Extended System Config Options
Chapter 6 Functional Test Procedure…………………………………………………………………..33
6.1 Pre-Test Checklist
6.2 DAC/WAC
6.3 HVAC Mechanical Cooling
6.4 HVAC Mechanical Heating
6.5 Smoke Alarm
6.6 Generator Running
6.7 Hydrogen Alarm
6.8 RBS HVAC1 Fail Alarm
6.9 RBS HVAC2 Fail Alarm
6.10 RBS Temp High Alarm
6.11 RBS Temp Low Alarm
6.12 Standalone Operation (CoolLinks™ Interface Only)
Marvair Contact Information………………………………………………………………………………………37

3
NG-IOM-ATT Release 1.2 July 12, 2019
Important Safety Information
1. Use Care when Lifting or Transporting the controller
2. Turn Electrical Power OFF at the breaker or fuse box BEFORE installing or working on the controller. LINE
VOLTAGES ARE HAZARDOUS or LETHAL.
3. OBSERVE and COMPLY with ALL applicable ELECTRICAL AND BUILDING CODES and ORDINACES.
4. INSTALLATION and SERVICE should be performed ONLY by QUALIFIED and EXPERIENCED PEOPLE.
5. USE COMMON SENSE and BE SAFETY CONSCIOUS.
This is the safety alert symbol . When you see this symbol in the manual, be alert to the potential for personnel
injury or equipment damage. Understand the signal words DANGER, WARNING and CAUTION. These words are used to
identify levels of the seriousness of the hazard.
Failure to comply WILL result in death or severe personal injury or death.
Failure to comply COULD result in death or severe personal injury or death.
Failure to comply COULD result in minor personal injury and/or property damage.
IMPORTANT is used to point out helpful suggestions that will result in an improved installation, reliability or operation.
Confidentiality:
This document and the information contained herein are confidential and are the property of Marvair®. It may not in any
way be disclosed, copied or used by anyone except as expressly authorized by Marvair®. The document should always be
kept in a secure place and should be destroyed or returned to Marvair®when it is no longer needed. Not for use or
disclosure, except under written agreement. © 2019 Marvair®Proprietary. All rights reserved.
!
!DANGER!
!WARNING!
!CAUTION!

4
NG-IOM-ATT Release 1.2 July 12, 2019
Chapter 1 Materials Required for Installation
The following materials are provided in the NextGen CoolLinks™ HVAC controller package:
•NextGen CoolLinks™ controller enclosure
•Inside temperature sensor with 40 ft. sensor cable
•One, 50 ft. Cat5e Ethernet cables
•Alarm Punch Down Block with pre-wired and pigtail cables
•NextGen CoolLinks™ Installation and Operations Manual (this manual).
The following materials should be provided by the installer:
•Electrical conduit (3/4” and 1”), conduit fittings, mounting straps
•Mechanical installation hand tools (hammer drill, drill bits)
•Label maker & label tags
Chapter 2 NextGen CoolLinks™ Overview
The NextGen CoolLinks™ controller monitors internal and external shelter temperatures and controls the operation of the
Door Mount (DAC) or Wall Mount (WAC) DC Free-Air unit to provide cooling for the shelter equipment. The controller
also operates up to two mechanical-only cooling HVAC units that provide comfort cooling for technicians and serve as a
backup in the event of failure of the DAC/WAC unit. The primary goal of the CoolLinks™ controller is to maximize the
energy efficiency of the environmental control system while maintaining a consistent internal shelter temperature.
2.1 Equipment Architecture
Each telecommunications shelter is equipped with an externally mounted Marvair®DAC/WAC DC Free-Air unit and up to
two wall mount mechanical-only cooling HVAC units connected to the NextGen CoolLinks™ controller. A two-line
message display on the front of the controller provides inside and outside temperature and relative humidity indication
together with alarm notification. The controller also includes a Wi-fi hotspot through which technicians can connect with
a smart phone or laptop to determine the status of the system, manually control equipment, review the alarm
information, review and upload event logs, and download software updates.
The DAC/WAC is powered by 48 VDC from the DC plant and consists of a door mount (DAC) or a wall mount (WAC) air
handler unit coupled to an exhaust air damper unit mounted at the opposite end of the shelter from the DAC/WAC. A
CoolLinks™ board inside the DAC/WAC air handler controls an outside air damper and variable speed fan. The exhaust
air damper automatically opens whenever the DAC/WAC variable speed fan is running. When commanded by the
NextGen controller, the DAC/WAC opens its outside air damper and regulates the DC fan speed to introduce outside air
into the shelter to maintain the cooling temperature set point. The NextGen controller communicates over Ethernet to
the DAC/WAC unit.
The mechanical-only cooling DX HVAC units are powered by 208/240 VAC from the shelter Integrated Load Center (ILC).
These units only operate when commanded by a technician to provide temporary comfort cooling, or when the DAC/WAC
is unable to maintain the desired cooling temperature set point, or if the DAC/WAC fails. In addition to cooling, the HVAC
units, if equipped, provide shelter heating. The NextGen controller communicates to the HVAC units via either a
hardwired (thermostat) interface, or over Ethernet if a CoolLinks™ boards is installed in the HVAC unit. The CoolLinks™
interface provides enhanced control features and alarm notification.

5
NG-IOM-ATT Release 1.2 July 12, 2019
Figure 1: NextGen CoolLinks™ Architecture
Unit%2%DX
HVAC
NextGen
CoolLinks™%
Controller
Smart%Phone
Interface
Remote
Interface
Ethernet
Unit%1
DAC/WAC
Hardwired%or%Ethernet
Exhaust
Damper
Unit%3%DX
HVAC%
Optional%(Hardwired%or%Ethernet)
Hardwired

6
NG-IOM-ATT Release 1.2 July 12, 2019
2.2 Cooling Control
The DAC/WAC unit provides the primary shelter cooling. The secondary HVAC mechanical-only cooling units operate in
the event that internal temperatures exceed a threshold or failure of the DAC/WAC unit. When commanded to run, the
DAC/WAC unit fully opens the its internal damper and the remote exhaust damper then regulates the blower speed
dependent on internal shelter temperature.
DAC/WAC Cooling:
PARAMETER
THRESHOLD
DAC/WAC
INSIDE TEMP
< 55°F (13°C)
BLOWER OFF
INSIDE TEMP
>= 55°F (13°C)
BLOWER SPEED 5%
INSIDE TEMP
> 77°F (25°C)
BLOWER SPEED 5%-100%
INSIDE TEMP
> 90°F (32°C)
BLOWER SPEED 100%
INSIDE TEMP
>= 104°F (40°C)
BLOWER OFF
INSIDE TEMP
>= 109°F (43°C)
See note
Table 1: DAC/WAC Cooling Stages
HVAC Cooling:
PARAMETER
THRESHOLD
MECHANICAL
INSIDE TEMP
>= 104°F (40°C)
HVAC ON
INSIDE TEMP
<= 89°F (32°C)
HVAC OFF
INSIDE TEMP
>= 109°F (32°C)
See note
Table 2: HVAC Cooling Stages
Note:
For a DAC/WAC with one HVAC unit, if HVAC cooling is active and the indoor temperature rises above the local high
temperature alarm set point then the HVAC unit is disabled and the DAC/WAC assumes cooling responsibility. For a
DAC/WAC with two HVAC units, if HVAC cooling is active and the indoor temperature rises above the local high
temperature alarm set point then the lead HVAC unit is disabled and the lag HVAC unit assumes cooling responsibility. If
both lead and lag HVAC units are unavailable the DAC/WAC assumes cooling responsibility. Three consecutive events of
this type will set the HVAC Fail alarm for the HVAC unit.
2.3 Heating Control
The HVAC units exclusively provide shelter heating; the DAC/WAC unit does not run if heating is required. Note that if
the cooling and heating temperature set points overlap, the system will only allow cooling to be active.
DAC/WAC Heating:
PARAMETER
THRESHOLD
DAC/WAC
INSIDE TEMP
< 55°F (13°C)
BLOWER OFF
Table 3: DAC/WAC Heating Stages
HVAC Heating:
PARAMETER
THRESHOLD
MECHANICAL
INSIDE TEMP
< 45°F (7°C)
HVAC HEATING ELEMENTS ON
INSIDE TEMP
>= 55°F (13°C)
HVAC HEATING ELEMENTS OFF
Table 4: HVAC Heating Stages

7
NG-IOM-ATT Release 1.2 July 12, 2019
2.4 DAC/WAC Standalone Operation
If the control board in the DAC/WAC unit is unable to communicate with CoolLinks™ controller for a period of sixty
seconds, the DAC/WAC unit will select standalone mode. Here, the unit will run its blower at 100% and both the
DAC/WAC and exhaust dampers will be fully opened. When communications with the controller is restored, the DAC/WAC
will automatically drop out of standalone mode and return to CoolLinks™-controlled operation.
2.5 System Interlocks
Smoke Detector (optional):
If the smoke sensor input to the CoolLinks™ system is active, the blower motor on the DAC/WAC will be shut down and
the DAC/WAC and exhaust dampers will be fully closed. If any HVAC units are running, the compressor, evaporator
blower motor, and heater will be turned off on all units. This is to halt the flow of air within the shelter.
Hydrogen Detector (optional):
If the hydrogen sensor input to the CoolLinks™ system is active, the blower motor on the DAC/WAC will be commanded
to run at 100% and the DAC/WAC and exhaust dampers will be fully opened. Any running HVAC units will continue to do
so and, if not running, their evaporator blower(s) will be commanded to run. The intention here is to expel noxious gases
and to introduce the maximum volume of outside air into the shelter.
Generator Running (optional):
If the generator running input to the CoolLinks™ system is active, only the DAC/WAC unit will be permitted to run even if
the temperature conditions require the HVAC unit(s) to run.

8
NG-IOM-ATT Release 1.2 July 12, 2019
Chapter 3 Mechanical Installation
3.1 Control Enclosure
The NextGen CoolLinks™ enclosure can be mounted directly on the wall in any suitable location on the inside of the
shelter; the enclosure does not have to be mounted on the same wall as the DAC/WAC or HVAC units. However, there
are some physical constraints that should first be considered prior to mounting:
!
•DAC/WAC Unit: one, 50ft. Ethernet cable is provided for connection to the DAC/WAC unit. The enclosure
should be mounted to ensure that the distance from the electrical box inside each DAC/WAC unit to the
enclosure does not exceed 50ft. including all necessary conduit routing.
•Inside Sensor: one, 40ft. communications cable is provided for connection to the inside sensor. The
distance between the enclosure and the sensor should not exceed the length of the communications
cable, which must also be run in conduit.
•The two-line LCD message display provides the local interface to the system and should be installed at a
height where a technician can comfortably see the system while standing in front of the enclosure.
Ideally this would be at a height of 5ft. from the floor.
•The enclosure has a depth of just over 5 inches. It is important to ensure that the enclosure does not
extend into a walkway and does not impede access to other shelter equipment.
The enclosure is mounted to the shelter wall with four brackets attached the back of the enclosure. At a minimum,
screws should be 1¼” x ¼” wall anchors and must be installed in each hole to fully support the 20lbs weight of the
enclosure. If necessary, washers may be installed behind the heads of the screws. All cables or wires entering or leaving
the control enclosure should be installed in either fixed or flexible conduit. For this purpose two conduit knockouts are
provided on the top and one conduit knockout each on the bottom and sides of the enclosure.
3.2 Inside Temperature & Humidity Sensor
The inside temperature sensor measures the internal shelter temperature which in turn is used to operate the cooling and
heating functions of the controller. The sensor mounts on a standard 4” x 2” Handy box and can be installed anywhere
within 40ft. of the controller (including conduit routing). The ideal location is on the wall adjacent to the exhaust damper,
provided that this location is not behind any equipment or a grounding bar. The sensor requires a nominal flow of air
over the sensor element but should not be placed directly in front of the supply air vents or adjacent to the shelter entry
door. The sensor should also not be installed behind equipment racks or close to local heat sources such as rectifiers,
radio cabinets, or battery chargers.

9
NG-IOM-ATT Release 1.2 July 12, 2019
Figure 2: NextGen CoolLinks™ Enclosure Dimensions and Mounting Locations
Figure 3: Inside Sensor Mounting Location

10
NG-IOM-ATT Release 1.2 July 12, 2019
Chapter 4 Electrical Installation
4.1 Electrical Connection Overview
Turn each of the four captive screws one quarter-turn, counter-clockwise to remove the front cover from the NextGen
CoolLinks™ controller. The principal electrical connections and the corresponding section of the manual that describes
the details of these connections are shown below. All of these connections should be completed prior to commissioning
the cooling equipment.
Figure 4: NextGen CoolLinks™ Enclosure Principal Electrical Connections
!WARNING
ELECTRICAL SHOCK HAZARD
Failure to follow safety warnings exactly could result in serious injury, death, and/or
property damage.
Turn off electric power at the service panel or fuse box BEFORE making any electrical
connections and ensure a proper ground connection is made.
Control Power
(section 4.2)
Inside Sensor
(section 4.3)
Smoke,
Hydrogen,
Generator
(section 4.6)
Hardwired DX HVAC
(section 4.5.1)
DAC/WAC, DX HVAC
(section 4.4, 4.5.2)

11
NG-IOM-ATT Release 1.2 July 12, 2019
4.2 Control Power (48 VDC)
The NextGen CoolLinks™ controller requires a two-conductor, 5A, 48VDC feed from the shelter DC plant. The wire type
must be per AT&T policy document
ATT-002-290-701, Cell Site DC Power Wiring Requirements
. All wire connections in
the DC plant must use two-hole compression lugs sized for the wire gauge. The use of single-hole lugs is prohibited
unless the DC plant cannot accommodate two-hole lugs. The required wires sizes are shown below:
!
Equipment Type
DC Plant Breaker (A)
Cable Length (ft)
Wire Gauge (AWG)
DAC or WAC
20
0 - 30
12
30 - 50
10
50 - 80
8
NextGen CoolLinks™ Controller
5
< 100
14
Table 5: Equipment 48 VDC Power Connections
Notes:
1. Cable length represents the total end-to-end length including all conduit and cable tray routing.
2. Refer to ATT-TP-76300 for details of cable routing requirements.
3. TelcoFlex®III or KS24194®L3 for 14AWG through 10AWG.
4. TelcoFlex®IV or KS24194®L4 for gauges larger than 10AWG.
5. Always use the correct wire gauge. DO NOT reduce wire size by removing strands from larger gauge wire.
6. Designed voltage drop less than 4% based on load, wire gauge, and cable length.
After installing the correct cable between the DC plant and the controller, terminate the cable on the appropriate
terminals inside the DC plant. Connect TelcoFlex cable from DC Plant to one of the +48VDC terminals and one of the
RTN terminals of the five-position terminal block (note that the terminal block can be removed for ease of termination).
Figure 5: 48VDC Power Connections and Fuse
Install the 5A breaker in the DC plant with the breaker in the off position. Verify that the 48VDC polarity is correct. The
controller has polarity protection and will not power-up if the polarity is reversed. Turn on the breaker and the circuit
boards in the controller should now power-up. If the DC plant polarity is correct and the controller does not power-up,
turn the breaker off and swap the wires on the terminal block in the controller.Turn the breaker on and the unit should
now power-up. If the controller still fails to power-up, turn the breaker off then test and replace the 2A fuse if necessary.

12
NG-IOM-ATT Release 1.2 July 12, 2019
4.3 Inside Temperature & Humidity Sensor
This sensor provides the main control input for the controller. There are two possible sensors, the Air Test EE10 and
Prism Systems Temperature & Humidity sensor. Both sensors provide a temperature range of 32°F - 122°F and a relative
humidity range of 0% - 100%. The four-conductor communications wire connections for the sensors are as follows:
Terminal Block
Wire Color
Air Test EE10 Sensor
Prism T&H Sensor
+24V
Red
+V
+24VDC
RTN
Green
GND
COM
HUM
Black
RH
RH
TMP
White
T
TMP
Table 6: Inside Sensor Wiring Connections
The sensor must be connected to terminal block labeled TB1, Sensor 1 T&H_A1 as shown below (note that the terminal
block can be removed for ease of termination). The remaining temperature and humidity sensor terminal blocks are
reserved for future use.
Figure 6: Inside Sensor Terminal Block Connection
!!

13
NG-IOM-ATT Release 1.2 July 12, 2019
!
4.4 DAC/WAC Unit
The NextGen CoolLinks™ controller contains a five-port Ethernet router as shown below. All Ethernet devices in the
system connect through this router. The right-most port connects to the main processor circuit board. The Ethernet
cable from the DAC/WAC connects to any open port (the ports on the router are not dedicated) and to the RJ45 plug on
the CoolLinks™ board as shown below. The router supports auto negotiation of transmission speeds as well as auto
MDI/MDI-X crossover to allow either crossover or patch cable connections for any third-party Ethernet devices.
! ! !
Figure 7: CoolLinks™ DAC/WAC Unit Ethernet Connections
The NetAddr DIP-switch selects the last octet of the IP address of the CoolLinks™ board. The factory default setting for
all DAC/WAC units is all four switches in the down or off position corresponding to IP address 192.168.0.201. Note that it
is necessary to cycle power to the board for the changes to take effect however the switches on the DAC/WAC
CoolLinks™ board should NOT be changed from the factory setting.
!
!
Figure 8: CoolLinks™ DAC/WAC Unit Ethernet Address Settings
!!

14
NG-IOM-ATT Release 1.2 July 12, 2019
!
4.5 HVAC Unit
4.5.1 Hardwired Interface (Default)
The hardwired interface provides control for the mechanical cooling and heating functions of the HVAC unit. At a
minimum, a five-wire thermostat cable (not supplied) is required for control of the compressor, evaporator blower, and
heating element. If required, an additional two-wire input for monitoring the HVAC pressure lockout relay can be
connected. Note that the controller requires a normally closed lockout contact from the HVAC unit. The wire connections
for the terminal blocks labeled HVAC #1 and HVAC #2 are as follows:
Terminal Block
Wire Color
HVAC Unit
R
Red
24VAC Power
C
Black or Blue
24VAC Neutral
Y1
Yellow
Call for Cooling
G
Green
Call for Blower
W
White
Call for Heating
COM
Lockout Relay Common
NC
Lockout Relay NC Contact
Table 7: DX Unit Wiring Connections
!!!
Figure 9: HVAC Unit Wiring Connections (HVAC #1 Shown)
Hardwired Unit 2 DX HVAC (see figure 1) must ALWAYS be connected to terminal blocks labeled for HVAC #1. Hardwired
Unit 3 DX HVAC (see figure 1) must ALWAYS be connected to terminal blocks labeled for HVAC #2. The HVAC unit must
only be connected to those terminals identified in the wiring connections table. The unused terminals for HVAC #1 and
HVAC #2 are reserved for future use.

15
NG-IOM-ATT Release 1.2 July 12, 2019
4.5.2 CoolLinks™ Interface
The CoolLinks™ interface provides enhanced control and diagnostics for the mechanical cooling and heating functions of
the HVAC unit. The Ethernet cable from the CoolLinks™-equipped HVAC unit connects to any open port on the router
and to the RJ45 plug on the CoolLinks™ board as shown below.
! ! ! !
Figure 10: CoolLinks™ HVAC Unit Ethernet Connections
The NetAddr DIP-switch selects the last octet of the IP address of the CoolLinks™ board. CoolLinks™ Unit 2 DX HVAC
(see figure 1) should have its switch settings as shown in figure 11 (switch 1 up or on, all other switches down or off)
corresponding to IP address 192.198.0.202. CoolLinks™ Unit 3 DX HVAC (see figure 1) should have its switch settings as
shown in figure 12 (switch 2 up or on, all other switches down or off) corresponding to IP address 192.198.0.203. Note
that it is necessary to cycle power to the board for the changes to take effect.
!
Figure 11: CoolLinks™ HVAC Unit 2 Address Settings
!
Figure 12: CoolLinks™ HVAC Unit 3 Address Settings

16
NG-IOM-ATT Release 1.2 July 12, 2019
DC control power for the CoolLinks™ board in the DX unit can be sourced from the controller from any one of the four
48VDC terminal blocks. Ensure that the slider switch (1) is in the left position (green power LED (3) off).On the two-
position terminal block (2) connect +48VDC to the R terminal (5) and RTN to the C terminal (6) on CoolLinks board. Turn
the slider switch (1) to the right. Verify that the green power LED in the controller (3) and on the CoolLinks™ board (7)
are both On. If both power LEDs are off, turn the breaker off then test and replace the 2A fuse if necessary.
Figure 13: CoolLinks™ HVAC Unit Power Connections
4.6 Smoke Detector, Hydrogen Detector, Generator Running
Smoke Detector:
!
Figure 14: Wiring Connections With or Without Smoke Detector
2
3
1
4
5
6
7

17
NG-IOM-ATT Release 1.2 July 12, 2019
Hydrogen Detector:
Figure 15: Wiring Connections With or Without Hydrogen Detector
Generator Running:
Figure 16: Wiring Connections With or Without Generator Running Feedback

18
NG-IOM-ATT Release 1.2 July 12, 2019
4.7 RBS Alarms
A dedicated 66-block provides all controller hardwired alarms. Normally-open and normally-closed contacts are available
for each of the eight possible RBS alarms. For installations with limited interior space, a 25-pair pigtail is provided rather
than the dedicated 66-block to allow the alarms to be wired directly to the main shelter alarm block.
Figure 17: RBS Alarm Punch Down Block
4.8 Bonding
All of the electrical components within the NextGen CoolLinks™ controller are grounded to the back panel and this back
panel is in turn grounded to the enclosure. The outside of this enclosure should be grounded to the shelter halo with a
green 6 AWG stranded wire using a two-hole compression lug on the case and a C-tap at the halo. Two pre-drilled
bonding locations are provided on the top left hand and top right hand sides of the enclosure.

19
NG-IOM-ATT Release 1.2 July 12, 2019
Chapter 5 Operator Interface
5.1 LCD Message Display
The two-line LCD display provides basic status information for the NextGen CoolLinks™ controller. The contents of each
line is dependent on the controller conditions and are determined as follows:
Upper Line
Alternates every five seconds between the current indoor temperature and
relative humidity and the average temperature and relative humidity over the last
24 hours. A “??” indicates that the value from the sensor is bad and that either
the sensor is faulty or not connected properly.
Lower Line
(no active alarms)
Displays outdoor temperature and relative humidity. If the Wi-fi is Off and the
Wi-fi push button is pressed, displays “Wifi On”. If the Wi-fi is On and the Wi-fi
push button is pressed, reverts to outdoor temperature and relative humidity.
Lower Line
(active alarms)
Displays the Wi-fi connection status (“Wifi On” or “Wifi Off”) followed by “#
alarms” where # is the number of active alarms.
Table 8: LCD Message Display Line Definitions
Figure 18: Inside and Outside Temperature & Relative Humidity
Figure 19: Wi-fi Enabled and Active Alarm
5.2 Wi-fi Hot Spot
The NextGen CoolLinks™ controller is equipped with an integral Wi-fi hot spot, ngcl-wifi, that provides access to the
controller web page from a smart phone or laptop. By default the ngcl-wifi hot spot is disabled. To enable the hot spot for
a period of 30 minutes, press the Wi-fi enable push button on the bottom of the enclosure to the left of the 66-block
connector as shown below:!
Figure 20: Wi-fi Enable Push Button

20
NG-IOM-ATT Release 1.2 July 12, 2019
Wait for the LCD message display to indicate that the Wi-fi is On. From a smart phone or laptop choose the Wi-Fi
connection settings screen. Select the ngcl-wifi network and, when prompted, enter coollinks into the WPA2 password
field then select Join. The smart phone or laptop should now be connected to the controller:
Figure 21: Wi-fi Hot Spot Connection Sequence
Note that for NextGen controllers manufactured prior to November 2018 the WPA2 password is prismsystems rather than
coollinks. However, if these controllers are updated the password will change automatically when the software update is
complete. Entry of the password is only required for the first connection to the network. Subsequent connections will
use the cached password so that the technician only has to select the ngcl-wifi network to automatically connect.
Table of contents
Popular Controllers manuals by other brands
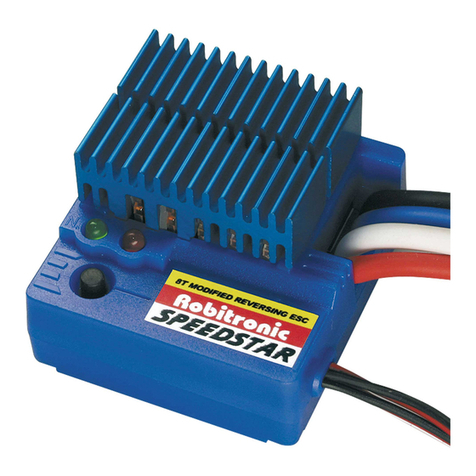
Robitronic
Robitronic Speedstar operating instructions

SEW-Eurodrive
SEW-Eurodrive MOVITRAC 07 manual

EST
EST CM1 installation manual
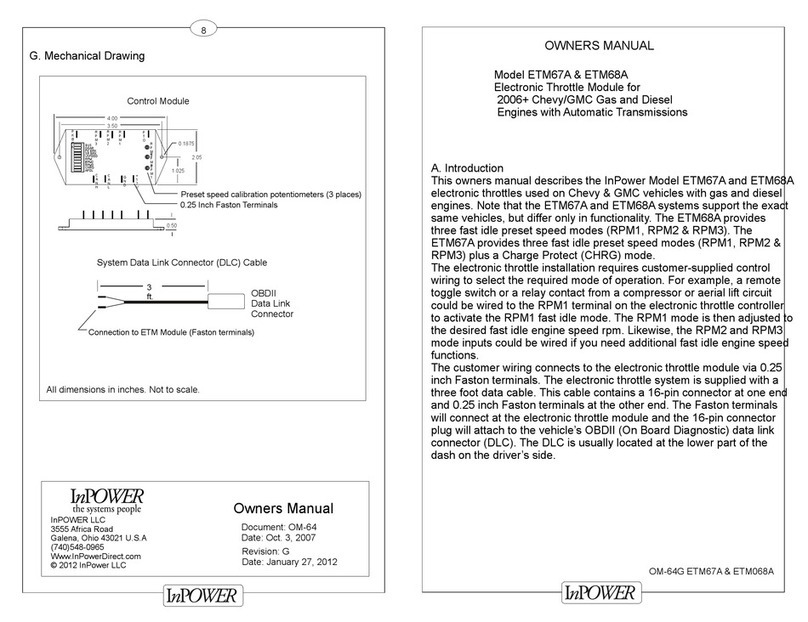
InPOWER
InPOWER ETM67A owner's manual
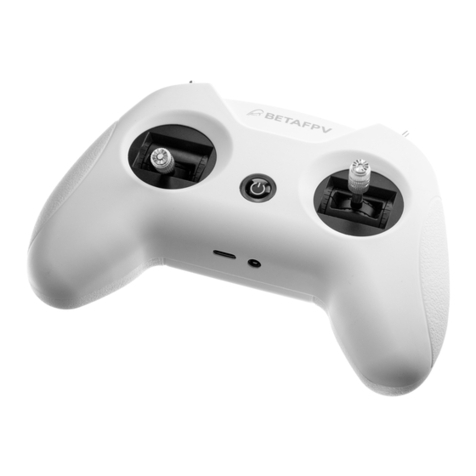
BETAFPV
BETAFPV LiteRadio 2 SE quick start guide
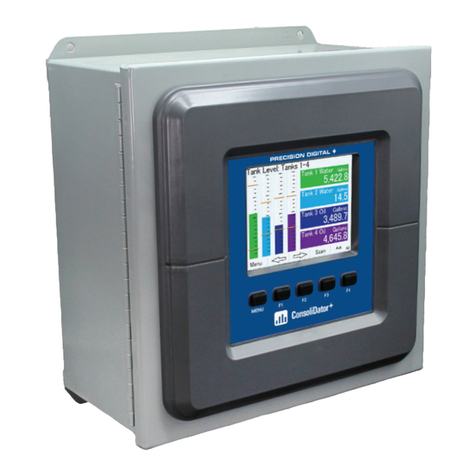
Precision Digital Corporation
Precision Digital Corporation ConsoliDator Plus PD9000 instruction manual