Maxcess Tidland D3 User manual

Tidland D3 Differential Air Shaft
Installation, Operation and Maintenance Manual
EN
For use with Tidland Serial Numbers 651931 and after
Includes Appendices for earlier shaft models
MI 638671 1 Q
TIDLAND WINDING SOLUTIONS

www.maxcessintl.com
Tidland D3 Differential Air Shaft
MI 638671 1 Q
Page 2
SAFETY INSTRUCTIONS
When using this Tidland product, basic safety precautions should always be followed to
reduce the risk of personal injury. Your company's safety instructions and procedures should
always be followed. When using this product with any other equipment or machinery, all
safety requirements stipulated by that equipment or machinery manufacturer must be
followed. Compliance with local, state, and federal safety requirements is your responsibility.
No part of these or the following instructions should be construed as conflicting with or
nullifying the instructions from other sources. Be familiar with the hazards and safety
requirements in your work environment and always work safely.
1. Read and understand all instructions and shaft design application limits before operation.
2. Never use this product for a purpose or in a machine that it was not specifically designed for. See
Product Safety Data Sheet (PSDS).
3. Do not exceed the operation loads for this shaft as noted on its PSDS, Product Safety Data Sheet.
4. Follow all warnings and instructions marked on the product and on the PSDS.
5. Inspect the shaft for wear and/or other safety and functional deficiencies daily, before each use.
6. Wear safety glasses or proper eye protection when inflating or deflating or otherwise operating the
air system.
7. Do not remove or otherwise alter any setscrews or fastening devices prior to using this product.
8. Do not operate this product if any setscrews or fastening devices are missing.
9. Do not lift shaft manually if it is beyond your capacity. Loads over 1/3 your body weight may be
prohibitive. Consult your company safety policy.
10. When lifting a shaft, use proper lifting techniques, keeping back straight and lifting with the legs.
11. Do not carry or lift this product over wet or slippery surfaces.
12. Use appropriate mechanical lifting devices, such as a hoist or shaft puller, for heavier shafts.
13. When performing maintenance or repair procedures, do not pressurize the shaft if journal
setscrews are loose or missing.
14. When performing maintenance procedures, do not pressurize the shaft if the journal is missing.
15. All replacement parts used on this product should be made to original Tidland specifications.
16. All maintenance and repair procedures performed on this product should be done to Tidland
specifications by qualified personnel.

www.maxcessintl.com
Tidland D3 Differential Air Shaft
MI 638671 1 Q
Page 3
TABLE OF CONTENTS
Safety Instructions.................................................................................................................2
Tidland Customer Service......................................................................................................4
Recommended Tools.............................................................................................................4
Nomenclature and Part Numbers...........................................................................................5
Shaft..................................................................................................................................5
Tray Assembly...................................................................................................................6
Pressure Control Valve System .........................................................................................7
How it Works......................................................................................................................7
Operation...............................................................................................................................8
Bleeder Valves...................................................................................................................8
Muffler............................................................................................................................8
Adjusting the Exhaust Bleeder Valve .............................................................................8
Inflation Sequence.............................................................................................................9
To Begin Winding ............................................................................................................ 10
When Winding is Complete..............................................................................................10
Maintenance........................................................................................................................11
General Information.........................................................................................................11
Maintenance Schedule.................................................................................................11
Shaft Care....................................................................................................................11
Polyurethane Bladders.................................................................................................11
Poron®Springs ............................................................................................................11
Wear Bars....................................................................................................................11
Exhaust Bleeder Valve.....................................................................................................12
Cleaning.......................................................................................................................12
Replacing.....................................................................................................................12
Tension Segment Tray.....................................................................................................13
Remove Tension Segment Tray from Shaft .................................................................13
Disassemble Tension Segment Tray............................................................................ 14
Shaft and Tray Maintenance........................................................................................ 15
Install Bladders................................................................................................................ 16
Core-Locking Element (Lower Bladder) .......................................................................16
Tension Segment Element (Upper Bladder).................................................................17
Install Tension Segment Strip.......................................................................................... 18
Install Tray in the Shaft Slot.............................................................................................19
Replace Wear Bars.......................................................................................................... 19
Troubleshooting...................................................................................................................20
Appendix A..........................................................................................................................22
Appendix B..........................................................................................................................23

www.maxcessintl.com
Tidland D3 Differential Air Shaft
MI 638671 1 Q
Page 4
CAUTION
Wear eye protection when using tools or compressed air.
TIDLAND CUSTOMER SERVICE
800.426.1000 www.maxcessintl.com
360.834.2345
Visit the Tidland Repair and Return Center online to review our return policies
or to submit an electronic Return Material Authorization Request at
www.maxcessintl.com/returns.
RECOMMENDED TOOLS
Clean non-lubricated air supply: 0-40 psi (0.0-2.8 bar) for proper operation.
Tidland Inflation Tool (P/N 128052)
Tidland Air Release Tool and (P/N 111630)
Tidland Hole Punch Tool (P/N 560345)
Hex drive wrenches: 2.5mm, 7/64"
LOCTITE® 242 (blue)
Parker Super O-Lube O-ring Lubricant (make no substitutions)
Small pliers
For more accessories to help with your winding processes, visit www.maxcessintl.com
NOTICE
Maximum operating air pressure = 40 psi (2.8 bar)
Maximum overspeed = 10%; recommend 5%

www.maxcessintl.com
Tidland D3 Differential Air Shaft
MI 638671 1 Q
Page 5
SOC HD CAPSCREW (2 PLCS EACH TRAY)
616740
TENSION SEGMENT TRAY ASSEMBLY
SHAFT BODY
O-RINGS (3 PLCS EACH SLOT)
126193
Earlier shaft models
have only 2 o-rings.
REQUIRED:
ROTARY AIR SUPPLY
INFLATES UPPER BLADDER
TO RAISE TENSION SEGMENTS
VALVE (LOCATION MAY VARY)
INFLATES LOWER BLADDER
TO LOCK CORE STOP SEGMENTS
CALL FOR PART NUMBER
WEAR BAR
SEE NOTE BELOW
NOMENCLATURE AND PART NUMBERS
Air valve locations vary for the Tidland Equalizer Model D3 Differential Air Shaft. See page 9
for complete instructions on inflation sequence and valve operation.
Shaft
For shaft serial numbers before 660659, see page 11 for information about wear bars.
TRAY RETAINING ROD
(2 PLCS EACH TRAY)
653041
WEAR BAR
652361
FOR SERIAL NUMBERS
660659 AND AFTER
EXHAUST BLEEDER VALVE OUTLET
(END OR SIDE LOCATION)
REGULATES UPPER BLADDER
TO RAISE TENSION SEGMENTS
639967
MUFFLER
665891
SOC HD CPSCR
VARIES BY CONFIGURATION
CALL FOR PART NUMBER

www.maxcessintl.com
Tidland D3 Differential Air Shaft
MI 638671 1 Q
Page 6
ASSEMBLY DIAGRAM AND PART NUMBERS
Tray Assembly
See Appendix B for shaft serial numbers up to and including 651018.
Spacer (UHMW) part profile changed with serial number XXXXXX, but it does not affect assembly.
Rotary Air End
Non-Rotary Air End

www.maxcessintl.com
Tidland D3 Differential Air Shaft
MI 638671 1 Q
Page 7
OPERATION
Pressure Control Valve System
Successful operation of the Tidland Differential Shaft series depends upon proper internal air
pressure. Each of the Differential Shaft models can be equipped with a pressure control
system comprising two bleeder valves. Used with your applied air pressure, these valves
allow the operator to adjust and maintain internal air pressure, which is critical in low-tension
winding applications where the required internal pressure is very low and the pressure range
is very small.
Variable pressure is required in order to control the air pressure on the tension segments as
the roll diameter increases. As the roll diameter grows, the required rate of pressure increase
will diminish due to the weight of the roll and friction between the roll and shaft. These
parameters will vary based on your application.
How it Works
As operating air pressure is applied to the shaft, the factory-set inlet valve causes a drop in
pressure as air enters the bladder. The exhaust bleeder valve controls the amount of that
pressure drop. The larger the exhaust opening, the greater the pressure drop, resulting in
lower internal bladder pressure. Reducing the exhaust opening increases the internal air
pressure.
If you are unable to achieve optimal tension control by adjusting your applied air pressure,
use the exhaust bleeder valve to improve the resolution of your tension controller.
For the D3 Differential Shaft, this Pressure Control Valve System affects only the
upper bladder that controls the tension segment height.
Note: The Pressure Control Valve System is installed in Tidland D3 shafts starting with serial
number 644698.
NOTICE
Before beginning the winding operation, please read and understand the
following.
CAUSES A PRESSURE DROP;
SHOULD NOT REQUIRE ADJUSTMENT
AFFECTS THE INTERNAL AIR PRESSURE; CONTROL
THE PRESSURE DROP BY ADJUSTING THE OUTLET
(EXHAUST BLEEDER VALVE, PAGE ERROR! BOOKMARK
NOT DEFINED.)

www.maxcessintl.com
Tidland D3 Differential Air Shaft
MI 638671 1 Q
Page 8
OPERATION
Bleeder Valves
As operating air pressure is applied to the shaft, the factory-set inlet valve causes a drop in
pressure as air enters the bladder. The exhaust bleeder valve controls the amount of that
pressure drop. The larger the exhaust opening, the greater the pressure drop, resulting in
lower internal bladder pressure. Reducing the exhaust opening increases the internal air
pressure.
Both valves are factory-set according to customer operating specifications: roll specs
(width, diameter and weight), and web tension (PLI).
If you are unable to achieve optimal tension control by adjusting your applied air
pressure, use the exhaust bleeder valve to improve the resolution of your tension
controller. For the majority of applications, no adjustment is required for the exhaust
bleeder valve. For higher internal pressure, adjust to a smaller opening in the valve. For
lower internal pressure, adjust to a larger opening. Adjustments are made with a 1/8" hex
key.
The restrictor valve at the inlet should not require adjustment.
Do not operate shaft with missing valves.
A muffler may be installed* on the exhaust bleeder valve outlet to reduce noise. A slight
hiss may be audible: this indicates that the Pressure Control Valve System is functioning,
allowing air to escape from the shaft as designed. The muffler must be removed (12 mm
socket) before attempting to adjust or remove the bleeder valve. (See Bleeder Valve
Maintenance, page 12.)
*Not available on all Differential shaft designs.
Adjusting the Exhaust Bleeder Valve
1. Stop winding operation and shaft rotation.
2. To adjust the internal air pressure, turn the valve in 1/8 turn
increments using a 1/8" hex drive wrench.
To increase the pressure, turn the valve clockwise.
To decrease the pressure, turn the valve
counterclockwise.
DO NOT adjust while shaft is spinning.
To clean or replace the valve, see page 12.
The purpose of this graph is to illustrate the
characteristics of bleeder valve function. The
tension values displayed are arbitrary.
Actual winding tension will differ by variables
such as bladder length, shaft speed, roll specs
(width, diameter and weight), and core material.
Exhaust Bleeder Valve Function
0.00
0.10
0.20
0.30
0.40
0.50
0.60
0.0 5.0 10.0 15.0 20.0 25.0 30.0 35.0 40.0
APPLIED AIR PRESSURE - PSI
WEB TENSION - PLI
1/8 TURN OPEN
VALVE CLOSED
1/4 TURN OPEN
CLOSE

www.maxcessintl.com
Tidland D3 Differential Air Shaft
MI 638671 1 Q
Page 9
OPERATION
Inflation Sequence
NOTICE
The core-locking feature may be disarmed if the
appropriate pressurization sequence is not followed.
Successful operation of the D3 differential shaft depends upon proper pressurization.
Tidland recommends the use of precision instrumentation to ensure that inflation specifications are
met.
Do not exceed maximum operating pressure as outlined in chart on page 10. Excessive pressure
may cause bladder to explode or premature wear of tension segments and wear bars.
Deflate the Bladders
The D3 shaft is equipped with two separate bladders.
The upper bladder, inflated through the rotary union
air supply, controls the pressure of the tension segments
against the cores.
The lower bladder, inflated through a side or end
valve, raises the core-locking bar that locks the
tension segments between the cores in a raised position.
1. Make sure both bladders are completely deflated.
2. Install cores on shaft.
At the Rotary Union Air Supply
3. Using clean, non-lubricated air, inflate the tension element
bladder with a constant air source at a pressure high enough
to raise the tension segments to their maximum height.
Recommended: 20-40 psi (1.4-2.8 bar)
At the Side Valve
4. Using clean, non-lubricated air, manually inflate the
lower core-locking bladder to raise the locking angle bar.
You may hear it "click" into place as it locks the tension
segments in their raised position.
Recommended: 40 psi (2.8 bar)
At the Rotary Union Air Supply
5. Deflate the upper bladder to 0 (zero) psi, which will lower
the tension segments under the cores.
The following conditions must be met or the shaft
will not work properly:
The tension segments between the cores must remain
raised at a height that prevents lateral movement of the
cores on the shaft.
The tension segments beneath the cores must be
fully retracted, and cores should turn by hand easily
on the shaft. If they do not, refer to Troubleshooting
on page 21.
TENSION
SEGMENT
UPPER
BLADDER
LOWER
BLADDER
CORE-LOCKING
BAR
TENSION
SEGMENT
TRAY
3.
4.
5.

www.maxcessintl.com
Tidland D3 Differential Air Shaft
MI 638671 1 Q
Page 10
OPERATION
To Begin Winding
Important! Low-tension winding requires very low pressure.
1. Begin winding between 0 –1 psi (0-0.1 bar).
Tidland recommends precision instrumentation to ensure proper air pressure.
2. Make sure that cores can slip on the shaft as the winding continues.
(If they do not, refer to Troubleshooting on page 21.)
3. Continue winding.
4. During winding, observe the tension controller readout and adjust the applied air pressure as
needed. Adjusting the exhaust bleeder valve may improve the effectiveness of the tension
controller. (See page 8.)
D3 Pressure/Overspeed Limits
(Maintaining Safe Temperature for Plastic Components 70° Ambient)
20
40
60
80
100
120
140
160
180
200
220
240
260
15 20 25 30 35 40 45 50
PRESSURE, psi
OVERSPEED, rpm
Overheating or seizing will occur
Recommended operation
When Winding is Complete
1. When the desired roll size is reached and winding has stopped, manually deflate the lower bladder
(side or end valve) using the Tidland air release tool. To ensure that all the air is exhausted from
the bladder, increase the air pressure in the tension segment bladder (rotary union valve) while
engaging the air release tool in the side/end valve. This forces the core-locking bar down and
squeezes the air out of the lower bladder.
2. Reduce tension segment pressure (rotary union valve) to zero psi.
3. Rolls are now ready to be repositioned or removed from shaft.

www.maxcessintl.com
Tidland D3 Differential Air Shaft
MI 638671 1 Q
Page 11
MAINTENANCE
General Information
Complete maintenance procedures begin on page 13.
Maintenance Schedule
During operation shifts, use compressed air to keep shaft free from dust and debris.
As needed, remove sticky residue. Use a soft cloth damp with a mild solvent, such as rubbing
alcohol.
Shaft Care
Clean shaft with a soft cloth.
Mild solvents may be used sparingly; make sure shaft slot and all parts are wiped
completely dry of solvents before beginning reassembly.
Avoid lubricants as they cause dust to accumulate, preventing the shaft from functioning
properly.
Polyurethane Bladders
Petroleum-based lubricants will damage polyurethane bladders and o-rings. Do not use.
To help ensure leak free operation when replacing bladders:
a. Measure the length carefully so that bladder will be secured under the element end
clamps.
b. Always cut the bladders square across the end; bladders cut at an angle are at risk for
leaks.
c. Ensure that the element end clamp screws are tightened to 30 in·lbs (3.4 Nm).
Use LOCTITE 242 on screw threads.
Poron®Springs
The Poron material attached to the tension segment strip is fragile –use care when
handling the strip.
A torn or broken strip can function, but such damage may result in the loss of tension
segments when the strip is outside of the tray.
Strips with missing tension segments will prevent proper shaft operation. Do not use.
Wear Bars
Inspect the UHMW wear bars for gouges and deep wear depressions. If they are evenly
worn, Tidland recommends replacing all wear bars at the same time.
Single replacements can be made in the event of a damaged wear bar.
Wear bar configurations vary.
For shaft serial numbers up to 653669, contact Tidland Customer Service for
replacement information. 1-800-426-1000
Shaft serial numbers 660659 and after, see page 19 for replacement instructions.

www.maxcessintl.com
Tidland D3 Differential Air Shaft
MI 638671 1 Q
Page 12
MAINTENANCE
Maintaining the Bleeder Valve
If maintaining low tension during winding becomes difficult, the bleeder valve may require
adjustment or cleaning.
Note:
The fine threads on the needle and the housing are easy to damage. Use care when
working with these components.
Do not attempt to remove the bleeder valve housing from the shaft. If repair is necessary,
return the shaft to Tidland. (www.tidland.com/returns)
Location of valve varies due to custom shaft configurations.
Do not operate the shaft if:
the valve is missing.
the orifice is otherwise plugged.
Cleaning the Exhaust Bleeder Valve
1. Stop the winding operation and shaft rotation.
2. Locate the bleeder valve at the end or on the side of the shaft.
3. Using a 12 mm socket, carefully remove muffler*, if installed.
4. Using a 1/8" hex drive, carefully back the needle valve all the
way out of its housing (counterclockwise).
5. Using compressed air, blow dust and debris out of the valve.
6. Carefully reinstall the needle valve in the housing.
7. Close the valve down until it just bottoms out in the housing,
and then adjust as required for your application.
8. Resume winding operation.
9. Adjust the bleeder valve incrementally to achieve required
internal pressure.
*Not available on all Differential shaft designs.
Replacing the Exhaust Bleeder Valve
1. Stop the winding operation and shaft rotation.
2. Locate the bleeder valve at the end or on the side of the shaft.
3. Using a 12 mm socket, carefully remove muffler, if installed.
4. Using a 1/8" hex drive, carefully back the needle all the way out of its housing
(counterclockwise).
5. Carefully reinstall the needle valve in the housing.
6. Close the valve down until it just bottoms out in the housing, and then adjust as required
for your application.
7. Resume winding operation.
8. Adjust the bleeder valve incrementally to achieve required internal pressure.
MUFFLER
VALVE

www.maxcessintl.com
Tidland D3 Differential Air Shaft
MI 638671 1 Q
Page 13
MAINTENANCE
Tension Segment Tray
For shaft serial numbers up to and including 651018, see Appendix A (page 22) for tray
removal instructions.
Remove Tension Segment Tray from Shaft
1. Remove the journal (or end cap) from the shaft. (Configurations vary.)
2. Remove the two plastic rods that hold the selected tray in place. Grasp the protruding end of the
rod with small pliers and pull it out.
3. Remove the socket head capscrews that secure the tray to the slot. (7/64" hex drive)
4. Lift the tray out of the shaft and set it on a workbench.
5. Ensure that three o-rings remain in the shaft body slot after the tray is removed. Earlier shaft
models have two o-rings: see page 23.
O-RING
O-RINGS
PLASTIC ROD (2 PER TENSION SEGMENT TRAY)

www.maxcessintl.com
Tidland D3 Differential Air Shaft
MI 638671 1 Q
Page 14
MAINTENANCE
Disassemble Tension Segment Tray
Tray configurations vary for earlier shafts. See Appendix B (page 23) for shaft serial numbers up to
and including 651018.
1. On the bottom side of the tray, remove the two
outermost screws at each end to remove the
upper bladder end clamps.
(2.5mm hex drive)
[21 in·lbs/2.37 Nm]
2. Push –and gently pull –on the tension segment
strip to slide it out of the tray. Use care not to tear
the fragile Poron spring material.
3. On the bottom side of the tray, remove the retainer
rings to release the bladder from the tray. Unseat
the air fittings and remove the bladder from the
tray. Unscrew the threaded bushing from the air
fitting and remove the air fitting from the bladder.
4. On the bottom side of the tray, remove two screws
that secure the lower bladder end clamp. (2.5mm
hex drive)
5. Slide the core-locking bar out of the tray.
RETAINER RING
THREADED BUSHING

www.maxcessintl.com
Tidland D3 Differential Air Shaft
MI 638671 1 Q
Page 15
MAINTENANCE
Disassemble Tension Segment Tray (continued)
1. On the bottom side of the tray, remove two
screws that secure the lower bladder end clamp
to the tray.
2. Unscrew the threaded bushing from the air fitting
to release the bladder from the tray.
3. Remove the air fitting from the bladder.
Note: Retain the o-ring that is seated in the threaded bushing.
If your shaft design does not have an o-ring on the bushing, wipe the external threads of
the air fitting with a small amount of LOCTITE 242 during reassembly.
Shaft and Tray Maintenance
1. After the tension segment tray has been removed, clean the shaft slot using a soft cloth. A mild
solvent, such as rubbing alcohol, may be used sparingly; make sure shaft slot is wiped
completely dry before beginning reassembly.
2. Ensure that there are three o-rings seated in the positions shown below in each slot.
Earlier shaft models have two o-rings: see page 23.
3. Apply a small amount of o-ring lubricant to each o-ring before beginning reassembly.
4. Clean the tension segment tray with a mild solvent, such as rubbing alcohol. Dry thoroughly
before beginning reassembly.
NOTICE
Petroleum-based lubricants will damage the bladders and o-rings. Do not use!
THREADED BUSHING
O-RING
O-RING
O-RING

www.maxcessintl.com
Tidland D3 Differential Air Shaft
MI 638671 1 Q
Page 16
MAINTENANCE
Install Bladders
Use a small amount of LOCTITE 242 on the
threads of all screws and tighten to torque
specifications noted in brackets.
Core-Locking Element (Lower Bladder)
1. Cut the end of the lower bladder square and install
it in the tray lined up just at the edges of the screw
holes, as shown.
2. On the bladder, mark the location of the center of
the air fitting and remove the bladder from the tray.
3. Using the Tidland Hole Punch Tool, punch a hole
in one wall only of the bladder and insert the air
fitting into the bladder.
4. Reinstall the bladder in the tray with the air fitting
extending through the hole in the tray.
5. Screw the threaded bushing (with o-ring installed)
onto the air fitting to secure it to the tray. Do not
over-tighten or the bladder will distort, which may
result in leaks.
Note: If your shaft does not use an o-ring on the
bushing, wipe the external threads of the air fitting
with a small amount of LOCTITE.
6. Install the element end clamp with two flathead
cap screws, securing the bladder underneath.
(2.5mm hex drive)
[21 in·lbs/2.37 Nm]
7. Mark the other end of the bladder at a point that
lines up just at the edges of the screw holes, as
shown, and cut the end of the bladder square.
8. Slide the core-locking bar into the tray.
9. Install the element end clamp with two flathead
cap screws, securing the bladder underneath.
(2.5mm hex drive)
[21 in·lbs/2.37 Nm]
AIR FITTING LOCATION
TRAY
BLADDER
0.130"
AIR FITTING
BLADDER
0.130"
TRAY
BLADDER
TRAY
CORE-LOCKING BAR
FLAT HD CPSCR (2 PLCS)
6mm LG
LOWER END CLAMP
0.435"
TRAY
AIR FITTING
BLADDER
O-RING
FLAT HD CPSCR (2 PLCS)
6mm LG
LOWER END CLAMP
THREADED BUSHING

www.maxcessintl.com
Tidland D3 Differential Air Shaft
MI 638671 1 Q
Page 17
MAINTENANCE
Before continuing reassembly, test the bladder for air leaks at 80 psi (5.5 bar). Spray soapy water
onto element end clamps and air fittings and watch for bubbles. When inflated, the bladder should
cause the core-locking bar to lift.
Tension Segment Element (Upper Bladder)
1. Cut the end of the upper bladder square and
install it in the tray (on top of the core-locking
bar) lined up just at the edges of the screw
holes, as shown.
2. On the bladder, mark the location of the center
of the air fitting and remove the bladder from
the tray.
3. Using the Tidland Hole Punch Tool, punch a
hole in one wall only of the bladder and insert
the air fitting into the bladder.
4. Reinstall the bladder in the tray with the air
fitting extending through the hole in the lower
element end clamp.
5. On the underside of the tray, install the
retainer ring to secure the air fitting.
6. Install plastic spacer as shown.
7. Install the upper element end clamp with two
flathead cap screws in the outermost holes of
the tray. (2.5mm hex drive)
[21 in·lbs/2.37 Nm]
8. Cut other end of the bladder square at a point
that lines up at the edges of the screw holes,
as shown.
9. Mark the location of the center of the air fitting
and remove the end of the bladder from the
tray.
10. Using the Tidland Hole Punch Tool, punch a
hole in one wall only of the bladder and insert
the air fitting into the bladder.
11. Return the end of the bladder to the tray with
the air fitting extending through the hole in the
tray.
12. Install the retainer ring to secure the air fitting
to the tray.
0.130"
AIR FITTING LOCATION
UPPER BLADDER
TRAY
.496"
AIR FITTING
BLADDER
RETAINER RING
AIR FITTING
UPPER BLADDER
CORE-LOCKING BAR
0.130"
AIR FITTING LOCATION
UPPER BLADDER
.496"
UPPER END CLAMP
FLAT HD CPSCR (2 PLCS)
12mm LG
CORE-LOCKING BAR
UPPER BLADDER
AIR FITTING
RETAINER RING
TRAY
SPACER

www.maxcessintl.com
Tidland D3 Differential Air Shaft
MI 638671 1 Q
Page 18
MAINTENANCE
Install Tension Segment Strip
1. Carefully feed the end of the tension segment strip into the open end of the tray.
2. Push –do not pull –the strip into the tray. The Poron spring material is fragile.
3. As the strip is installed, ensure that the bladder does not wrinkle underneath it.
Tip: Lay a small strip of thin plastic or sturdy paper across the air fitting and the end of the tray to
help start feeding the tension segment strip into the shaft. Be sure to remove the plastic strip before
installing the remaining element end clamp.
4. When the tension segment strip has been completely loaded into the tray, install the short plastic
spacer, in the direction shown below.
5. Install the remaining upper element end clamp with two flathead cap screws in the outermost
holes of the tray. (2.5mm hex drive) [21 in·lbs/2.37 Nm]
Before continuing reassembly, test the bladder for air leaks at 80 psi (5.5 bar) using
soapy water at end clamps and air fitting. When inflated, the bladder should cause the tension
segments to lift.
TRAY
TENSION SEGMENT STRIP
UPPER BLADDER
LOWER BLADDER
AIR FITTING
RETAINER RING
FLAT HD SOC SCR (2 PLCS)
6mm LG
UPPER END CLAMP
SPACER
TRAY
TENSION SEGMENTS
PORON SPRINGS
PLASTIC STRIP

www.maxcessintl.com
Tidland D3 Differential Air Shaft
MI 638671 1 Q
Page 19
MAINTENANCE
Install Tray in the Shaft Slot
1. Ensure that there are three o-rings in each slot of the shaft body. Use a small amount of o-ring
lubricant on each o-ring before installing the tray.
Note: Earlier shaft models have two o-rings: see page 23.
2. Insert the tray in the shaft slot, making sure that
fittings on the bottom of the tray align with holes in
shaft slot.
3. Apply LOCTITE 242 to the threads of the socket
head capscrews and install at each
end of the tray.
4. Tighten to 17 in·lbs (1.9 Nm).
5. Slide the plastic rods into the grooves in the shaft to retain the
tray. If they do not slide in easily, press down gently on the tray as
the rod goes into the shaft.
6. Install the shaft journal or end cap. (Shaft end cap configurations
vary.) Use LOCTITE 242 on bolt threads and tighten to
specifications for your shaft material.
Aluminum 5 ft·lbs (6.8 Nm)
Steel 9 ft·lbs (12.2 Nm)
Replace Wear Bars
1. Remove shaft journal or end cap.
2. Slide wear bar out of shaft.
3. Slide new wear bar into shaft and reinstall the
shaft journal or end cap. (Configurations vary.)
Use LOCTITE 242 on bolt threads and tighten to specifications for
your shaft material (see Step 6 above).
Note: If there is a valve in the wear bar slot, remove it before
attempting to slide the wear bar out. When reinstalling the valve,
do not use LOCTITE. Tighten valve to 8-10 in·lbs (0.9-1.1 Nm).
Aluminum Wear Bars are installed with button head screws. Use a
hex drive wrench (2.5mm) to remove. When reinstalling screws, apply
LOCTITE 242 to threads and tighten to 15 in·lbs (1.7 Nm).
O-RINGS
O-RING
WEAR BAR

www.maxcessintl.com
Tidland D3 Differential Air Shaft
MI 638671 1 Q
Page 20
TROUBLESHOOTING
Problem
Possible Cause
Recommended Solution
Tension segments do
not activate
Exhaust Bleeder Valve
missing or not adjusted
correctly –too much air
escaping from shaft.
Ensure bleeder valve is installed.
Carefully tighten bleeder valve until it seats in
its housing. Back off one-quarter turn (90°).
Make further adjustments 45° at a time.
Air Leak or obstruction in air
system.
Make sure element end clamps are tightened
to 21 in·lbs. Inflate bladders and use soapy
water at element end caps to locate leaks.
Replace bladders or air lines as needed.
Tension segments jammed
with core dust or debris
Remove cores; use compressed air to remove
dust and debris
Tensions segments
do not retract
Bladder(s) not deflated
properly
Use Tidland Air Release tool to deflate
bladder(s),
Tension segments jammed
with core dust or debris
Cut web and cores from shaft; use
compressed air to remove dust and debris.
Use care not to damage tension segment strip
when cutting cores.
Overheated shaft has
deformed the bladder(s).
Cut web and cores from shaft; replace
bladder(s).
Overheated shaft
Shaft spinning inside cores
after winding operation has
stopped
Stop shaft rotation when not in winding
operation.
Excessive friction caused by
dust or residue buildup on
shaft
Stop winding operation; remove cores and
clean shaft.
Use compressed air to remove dust. For
residue, use a rag damp with small amount of
mild solvent, such as rubbing alcohol.
Let shaft dry completely before reloading
cores.
Overspeed
Reduce winding speed:
10% max overspeed; recommend 5%
Oversized cores will not allow
core locking bar to engage;
tension segments will not
retract properly –rubbing on
cores.
Replace cores. *
Table of contents
Other Maxcess Measuring Instrument manuals
Popular Measuring Instrument manuals by other brands
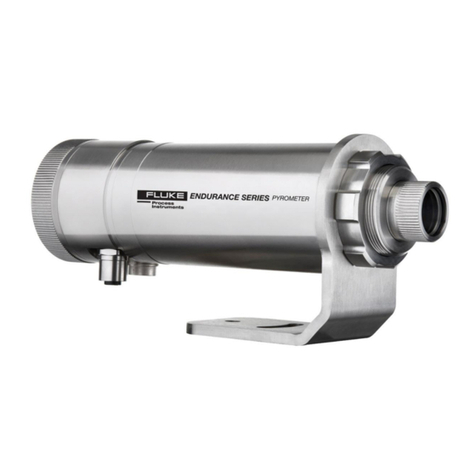
Fluke
Fluke endurance series user manual
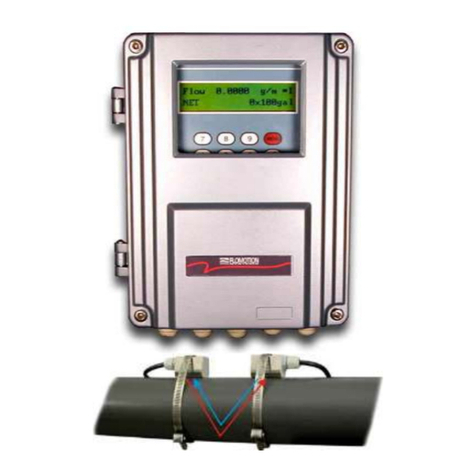
Flomotion Systems
Flomotion Systems BE6200 Installation and operation manual
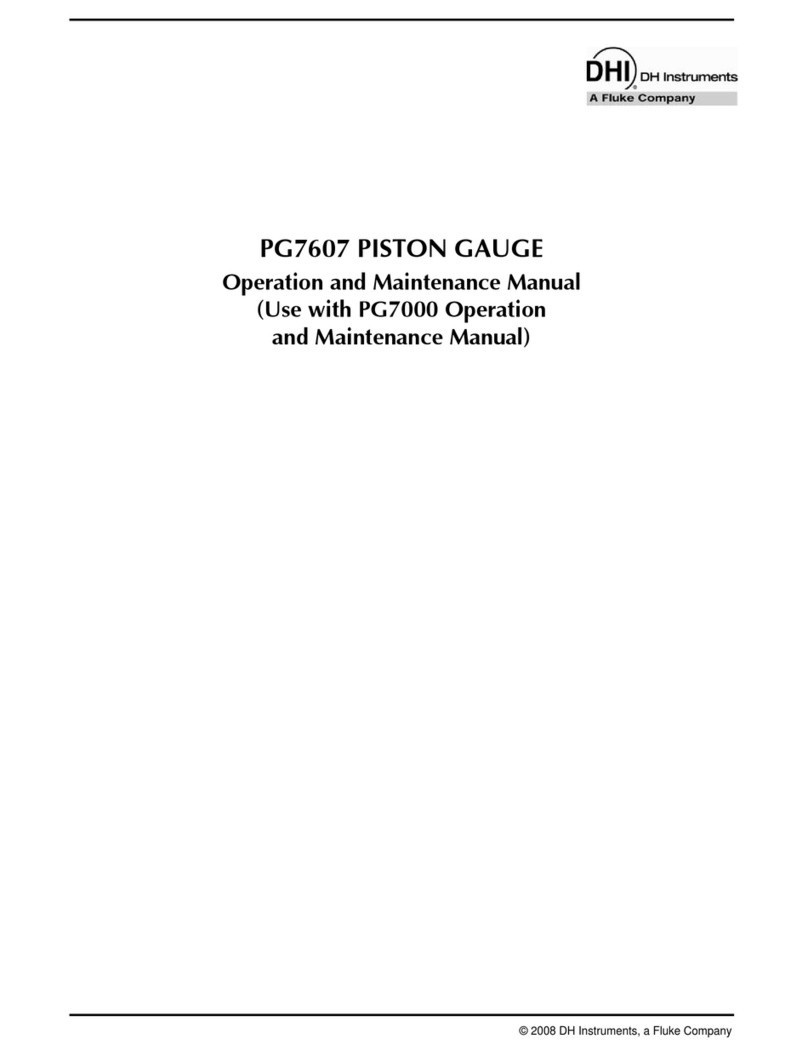
DH Instruments
DH Instruments PG7607 - 2008 Operation and maintenance manual
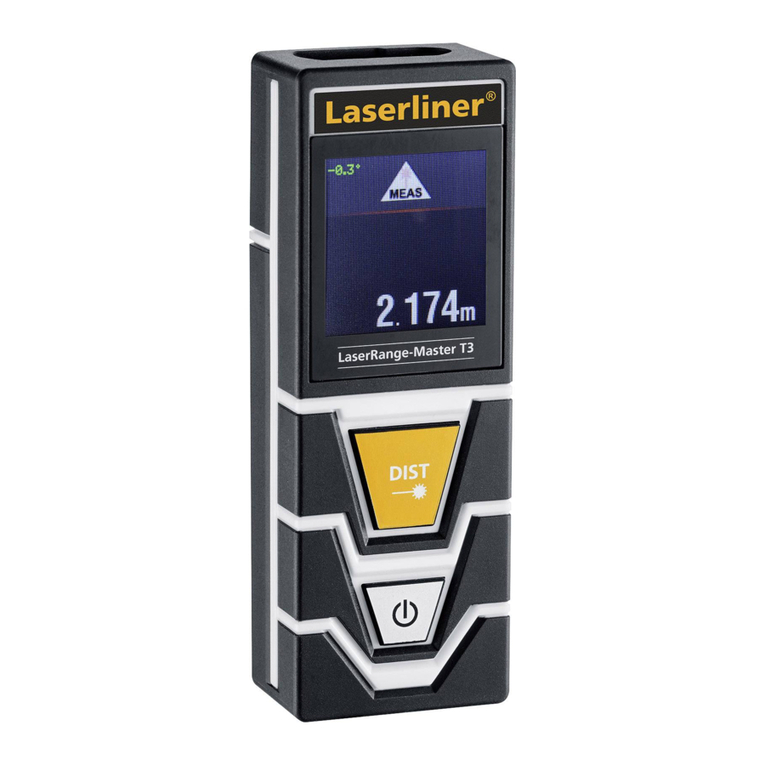
LaserLiner
LaserLiner LaserRange-Master T3 operating instructions
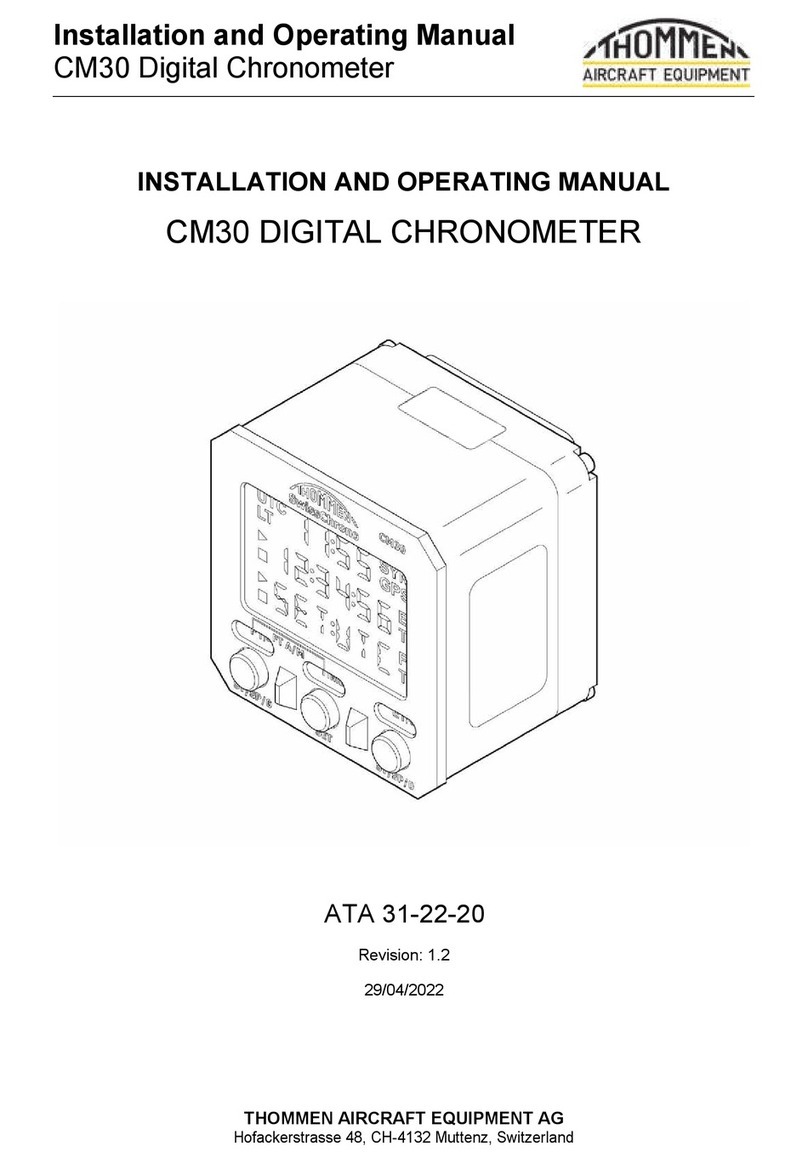
Thommen
Thommen CM30 Installation and operating manual

TechTest
TechTest RECOGNOIL user manual