Flomotion Systems BE6200 User manual

BE6200
Ultrasonic Flow Meter

BE6200 Ultrasonic Flow Meter O&M Manual
Page 2 Flomotion Systems, Inc ~ FlomotionSystems.com

BE6200 Ultrasonic Flow Meter O&M Manual
Flomotion Systems, Inc ~ FlomotionSystems.com Page 3
Installation and Operation Manual
BE6200
Ultrasonic Transit-Time Flow Meter
JUNE 2012
V18
Flomotion Systems, Inc.
165 Creekside Drive, Suite 112
Buffalo, NY 14228-2103
Toll Free (800) 909-3569
Tel: (716) 691-3941
Fax: (716) 691-1253
www.FlomotionSystems.com

BE6200 Ultrasonic Flow Meter O&M Manual
Page 4 Flomotion Systems, Inc ~ FlomotionSystems.com
Table of Contents
I. Introduction ................................................................................................................7
1. Preface ..............................................................................................................................................................................7
2. Characteristics ..............................................................................................................................................................7
3. Operation Principles .................................................................................................................................................8
4. Typical Applications .................................................................................................................................................9
5. Packing List ....................................................................................................................................................................9
6. Technical Specifications .......................................................................................................................................10
(1) DB6200 Version Updates……………………………...……………………………………………….……………...10
7. Power Connection ....................................................................................................................................................11
8. Cables .............................................................................................................................................................................11
(1) Power Cable ...........................................................................................................................................................11
(2) Output Signal Cable ............................................................................................................................................11
(3) Cable Between Transducer And Processor ..............................................................................................11
9. Wire Connections .....................................................................................................................................................12
(1) Wall Mount .............................................................................................................................................................12
II. Installation and Operation................................................................................. 13
1. Selecting the Measurement Point ...................................................................................................................13
2. Setting the Parameters ......................................................................................................................................... 13
3. Rapid Setup Procedure ………………………………………………………………………………………………14-15
. …(1) Preprograming…………………………………………………………………………...………………………………...14
. ((2) BE6200 Keypad & Display…………………..…………………………….……………………………………..........14
(3) Rapid Programing Setup……………………….……………………………..………………………………………..15
4. Transducer Mounting Distance ………………………………………………………………………………………15
5. Transducer Mounting Methods ........................................................................................................................16
(1) Signal Strength & Quality (M90) ...................................................................................................................17
(2) Total Travel Time and Time Difference (M93) .......................................................................................17
(3) Time Rate (TOM/TOS* 100, M91) ................................................................................................................17

BE6200 Ultrasonic Flow Meter O&M Manual
Flomotion Systems, Inc ~ FlomotionSystems.com Page 5
6. Selecting a Location for Transducer Mounting ....................................................................................... 18
Preparing the Pipe Surface ....................................................................................................................................18
7. Optional Data Logger Setup
(1) Logger Program Setup / Logger Status…………………………………………………………………………..19
(2) Logger Cable Connection / SD Connection ...............................................................................................19
III. Display Windows ................................................................................................. 20
1. Summary .......................................................................................................................................................................20
2. Descriptions ................................................................................................................................................................21
(1) Flow/Totalizer Displays ............................................................................................................................ 21-23
(2) Initial Setup ..................................................................................................................................................... 24-29
(3) Flow Unit Setup……………………………………………………………………………………………………….30-32
(4) Option Setup Menu…………………………………………………………………………………………………..33-35
(5) Output/Input Setup Menu………………………………………………………………………………………..36-45
(6) Energy Meter Setup Menu………………………………………………………………………………………..46-48
(7) Diagnostics Setup Menu…………………………………………………………………………………………...49-50
(8) Other Options Setup Menu……………………………………………………………………………………….51-53
III. Trouble Shooting ................................................................................................. 54
1. Power-On self-test information, Causes and Solutions........................................................................54
2. Error Code Causes and Solutions ....................................................................................................................55
3. 4-20 mA Output Calibration ...............................................................................................................................56
Appendix 1. Sound Velocity and Viscosity of Liquids.................................... 57
Appendix 2. Sound Velocity for Various Common Materials..................... 58
1. Pipe Material ...............................................................................................................................................................58
2. Liner Material .............................................................................................................................................................58
Appendix 3. Sound Velocity in Water (1 ATM) at different temperatures
.......................................................................................................................................... 59

BE6200 Ultrasonic Flow Meter O&M Manual
Page 6 Flomotion Systems, Inc ~ FlomotionSystems.com
Appendix 4. Pipe Dimensions and Weights ..................................................... 60
Ductile Iron Pipe.............................................................................................................................................................62
Cast Iron Pipe ...................................................................................................................................................................62

BE6200 Ultrasonic Flow Meter O&M Manual
Flomotion Systems, Inc ~ FlomotionSystems.com Page 7
I. Introduction
1. Preface
Welcome to BE6200 series ultrasonic flow meter. Please read this instruction manual thoroughly before
installation and operation.
BE6200 ultrasonic flow meter is a time-difference type ultrasonic flow meter, whose transducers are mounted by
being clamped to the external surface of a pipe. It measures clean, well-distributed flows of liquids in which the
content of suspended particles is minimal.
The system is configured as below;
• Sensor Set: A pair of ultrasonic transducers mounted on the external surface on a pipe.
• Processor: The processor and the transducers are connected by two double shield high frequency
cables. The processor can be monitored and controlled remotely through a PC connected via Internet. The
following illustrates the configuration of the processor unit and the transducer sets;
2. Characteristics
BE6200 ultrasonic flow meter is based on single-board technology featuring high accuracy, reliability and
repeatability.
Additional advantages:
Transducers are not intrusive. Therefore there’s no pressure drop. They are mounted on the outside wall
of the pipe.
Advanced intelligent instrumentation, processing and printing (logging) according to user requirements.
Almost all common flow units are used. It uses normal power, built-in battery or DC
power, etc.
It uses the most advanced direct time measurement method with the resolution of 0.2 ns. Coupled with
the advanced data processing functions, it provides high level of linearity.
Various output options available including analog current output, frequency output, relay output, etc.

BE6200 Ultrasonic Flow Meter O&M Manual
Page 8 Flomotion Systems, Inc ~ FlomotionSystems.com
3. Operation Principle
This time-of-travel (transit-time) meter has a pair of transducers mounted on each side of the pipe. The
configuration is such that the sound waves traveling between the devices are at a 45-degree angle to the direction
of liquid flow. The speed of the sound signal traveling between the transducers increases or decreases depending
upon the direction of transmission and the velocity of the liquid being measured. A time-differential relationship
proportional to the flow can be obtained by transmitting the signal alternately in both directions.
As per equation (1) and (2) above, the velocity of flow is
calculated as below;
The ultrasonic transit-time method is suitable for measuring single-phase, pure liquids without entrained air
bubbles. In industrial sites, the liquids may contain a certain level of impurities and flow conditions are often not
very uniform, thereby negatively affecting the performance of the ultrasonic flow meters. But our BE6200
ultrasonic flow meter adopts the most advanced direct time measuring method that considers the influence of
temperature and crude inside pipe situation in order to increase the accuracy and the reliability of the result. With
the use of the zero setting function, the meter renders 0.5% accuracy.
Where
M - travel times
V - velocity
D - inner diameter of the pipe
θ- transmission angle
C0 - sound velocity in a static fluid
TUP - upstream travel time (reverse flow
direction)
DOWN - downstream travel
time (flow direction)
ΔT - difference of travel time between
downstream and upstream

BE6200 Ultrasonic Flow Meter O&M Manual
Flomotion Systems, Inc ~ FlomotionSystems.com Page 9
4. Typical Applications
Water supply, drainage, water purification facility
Oil field and petrochemical plants
Power plants(thermal and hydro power plants)
Steel factory and mining industries
Food and beverage plants
Paper mills
HVAC
Etc.
5. Packing List
Items included are as follows;
1 processor
1 set of transducers(2 each)
1 transducer mounting bands
1 couplant
1 instruction manual
1 USB 2G memory (optional)

BE6200 Ultrasonic Flow Meter O&M Manual
Page 10 Flomotion Systems, Inc ~ FlomotionSystems.com
6. Technical Specifications
CLASSIFICATION
PERFORMANCE/PARAMETER
Pipe
Materials
Steel, Stainless Steel, Cast Iron. Plastics, Concrete,
etc.
Inner Diameter
0.5 to 236 in. (15 ~ 6000mm)
Straight Pipe Section
Requirement
10D upstream, 5D downstream (required length may
be longer depending on site conditions)
Fluid
Types
Clean, sonically conductive
Tubidity
Smaller than 10,000ppm(mg/l) with a low level of air
bubble content
Temperature
-4° F to 140° F (-20° C to 60° C)
Flow Velocity
-53 to +53 ft/s (-16 to +16 m/s)
Transducer
Pipe Size Range
S: 0.5 to 4 in. (15 ~100mm)
M: 2 to 40 in. (50 ~ 1000mm)
L: 12 to 236 in. (300 ~ 6000mm)
Mounting Method
‘V’ method: Suitable for pipe sizes 16 in. (400mm) or
smaller
‘Z’ method: Suitable for pipe size 10 in. (250mm) or
larger
Cable Length
16 ft (5m) Std. ( longer lengths available)
Flow Computer
Display
Alphanumeric
Keyboard
4x4 keypad
Mounting
Wall Mount or optional Panel Mount
Output
4-20mA or 0-20mA analog output, frequency output
(12-9999Hz), relay, serial output
Power
Wall Mount: 120VAC & 24VAC
Panel Type: 120VAC
Dimension
Wall Mount: 9.9 x 3.6 x 3.2 in. (251 x 92 x 80mm)
Weight
7 lbs. (3kg) Wall Mount
Operating Condition
Temperature
Flow Computer: -4 to158°F (-20 to 70°C)
Transducers: -4 to 140°F (-20 to 60°C)
Humidity
Flow Computer: 85% RH at 104°F (40°C)
Transducers: 98% RH at 104°F(40°C) (water
submersible up to 3 m)
Performance
Accuracy
±1.0% of reading above ±1 ft/s
Repeatability
±0.2% at 1 to 53 ft/s (0.3 ~16m/s)
Linearity
0.5%
(1) BE6200 Version Updated to Version 18
Differences Listed:
PREVEOUS VERSION 7
VERSION 18
Output : RS232 and 4-20mA
Output: RS 485 and 4-20mA
None have SD card
Optional SD card for the data logger
Add temperature transmitter test heat
Add PT100 can test the heat
None MUDBUS and M-BUS protocol
with MODBUS ,M-BUS protocol

BE6200 Ultrasonic Flow Meter O&M Manual
Flomotion Systems, Inc ~ FlomotionSystems.com Page 11
7. Power Connection
The meter can use standard 120VAC or 24VDC power supply. By default, the meter is provided with the
standard 120VAC power type. Therefore, should the user want 24VDC model, such should be indicated
when ordering.
8. Cables
Cables should never be spliced or cut. This may cause damage to the unit and void the warranty.
Attention: Meter can be badly damaged if a different power from
what was specified is supplied. Careful attention is advised.

BE6200 Ultrasonic Flow Meter O&M Manual
Page 12 Flomotion Systems, Inc ~ FlomotionSystems.com
9. Wire Connections
(1) Wall Mount

BE6200 Ultrasonic Flow Meter O&M Manual
Flomotion Systems, Inc ~ FlomotionSystems.com Page 13
II. Installation and Operation
The clamp-on type ultrasonic flow meter allows for the simplest and the easiest installation of all types of
flowmeters, though careful attention in selecting the measurement point, inputting pipe parameters, fixing the
transducers onto pipe, etc. in order to ensure accurate and reliable measurement of flow is needed. In this
chapter, you’ll be introduced to how to select the measurement point, input parameters, select mounting method,
etc.
1. Selecting the Measurement Point
Selecting the right measurement point is the most important factor for ensuring the accuracy and should be
done according to the following steps;
1) Make sure the pipe to be measured is full.
2) Select a location where it allows for straight pipe run of 10D upstream and 5D downstream. In case
there’s a pump or a bending section in the upstream, increase the upstream run to 30D in order to allow
the flow to fully develop into stable flow profile.
3) Ensure the temperature at the measuring point is within the specified range.
4) Avoid sections where the inner wall of the pipe is scaled or rusted that can negatively affect the
performance of the meter.
2. Setting the Parameters
In order to get the correct transducer mounting distance (the distance between the front edges of both
transducers) verify and set the following parameters;
1) Pipe outer diameter
2) Pipe inner diameter
3) Pipe material
4) Liner
5) Fluid type
6) Transducer type
7) Transducer mounting method type
When the above parameters are properly set, the correct transducer mounting distance is calculated and
displayed in the M25 window. Then the machine searches for proper amplifier gain. After S1, S2, S3 and S4 steps,
the machine enters into the normal operation state.

BE6200 Ultrasonic Flow Meter O&M Manual
Page 14 Flomotion Systems, Inc ~ FlomotionSystems.com
3. Rapid Setup Procedure
(1) Preprograming
Each BE6200 is preprogramed with the following values to help reduce setup time.
MENU
SELECTED VALUE
77 BEEPER SETUP
25. Disable Beeper
30 MEASURE UNITS IN
1. ENGLISH
31 FLOW RATE UNITS
US Gallon/min ( g/m)
32 TOTALIZER UNITS
US Gallon
34 NET TOTALIZER
OFF
35 POS TOTALIZER
ON
36 NEG TOTALIZER
ON
40 DAMPENING
10 SEC
41 LOW CUTOFF VALUE
0.2 FT/S
57 CL 20MA OUTPUT VALUE
1000
60 TIME, DATE (int. time std.)
YY-MM-DD HH:MM:SS
23 TRANSDUCER TYPE
Based upon order S1,M1 or L1
(2) BE6200 Keypad & Display

BE6200 Ultrasonic Flow Meter O&M Manual
Flomotion Systems, Inc ~ FlomotionSystems.com Page 15
The user can enter into specific windows using the key followed by a 2-digit code. So, for example, in order
to go to M13 window, this is the window for inputting the inner diameter of the pipe, press
.
(3) Rapid Programing Setup
1) Press to enter M11 window, input pipe outer diameter, press .
2) Press to enter M12 window, input wall thickness and press .
3) Press to enter M14 window and press or to scroll select pipe material, and
press .
4) Press to enter M16 window and or to scroll select liner material, and press .
5) Press to enter M20 window and or to scroll select fluid type, and press .
6) Press to enter M23 window and or to scroll select the transducer type, and press
.
7) Press to enter M24 window and or to scroll select the transducer mounting
method,and press .
8) Press to enter M25 window, which will display the correct
transducer spacing (the distance between the front edges of the transducers).
9) Press , the flow rate and the velocity of the flow will be displayed upon completion
of the gain adjusting process.
4. Transducer Spacing
The distance is measured between the front edges of both transducers. After all the parameters have been set,
the distance is shown in window no. M25.

BE6200 Ultrasonic Flow Meter O&M Manual
Page 16 Flomotion Systems, Inc ~ FlomotionSystems.com
5. Transducer Mounting Methods
Clamp-on Sensors
There are two mounting methods, ‘V’ and ‘Z’. Usually V method is used as standard because it provides longer
signal path and therefore more accurate measurement of flow velocity. It is recommended for pipes sizes
between 0.5~16” (15~400mm). Special attention should be given when mounting transducers to ensure that
sensors are aligned in direct line and along the center of the pipe and the transducer mounting line should be
aligned.
Z method is recommended for >10”(250mm) pipes or when the flow condition is bad because of scale built up
inside the pipe, entrained air bubbles, too thick liner, etc. which can induce a lot of noise into signal. Using this
method, the signal is dispersed in a straight path reducing the possibility of noise induction.
The user can verify whether the mounting is done correctly or not by checking the received signal strength,
total travel time, time difference and rate of travel time, which are described one the next page;

BE6200 Ultrasonic Flow Meter O&M Manual
Flomotion Systems, Inc ~ FlomotionSystems.com Page 17
(1) Signal Strength & Quality
The signal strength is indicated by a number between 0.00 ~ 99.9. 0.00 means no signal received and 99.9
means the signal strength is at the maximum. It should be larger than 60.0 for normal operation. The signal
quality Q is indicated by a number between 0.00 ~ 99.9. 0.00 indicates that the signal is at its lowest level
and 99.9 the highest. It should be at least 60.00 for normal operation.
(2) Total Travel Time and Delta Time
The measurement is taken based on the total travel time and the time difference. Under normal working
conditions the Delta time should not fluctuate beyond +-20%. If continuous violent fluctuation or fluctuations over
+- 20% occur stability has been compromised and adjustments must be made. Review and adjust the transducer
installation and the initial setup parameters M10 - M29.
(3) Time Rate (TOM/TOS* 100)
This is used to confirm whether the transducers are located with the correct interval. This should indicate 100
±3%.

BE6200 Ultrasonic Flow Meter O&M Manual
Page 18 Flomotion Systems, Inc ~ FlomotionSystems.com
6. Selecting a Location for Transducer Mounting
1. Locate the transducers downstream from the center of the longest available straight run. A location ten
pipe diameters or greater downstream from the nearest bend will provide the best flow profile
conditions.
2. Do not install the transducers downstream from a throttling valve, a mixing tank, the discharge of a
positive displacement pump or any other equipment that could possibly aerate the liquid. The best
location will be as free as possible from flow disturbances, vibration, sources of heat, noise, or radiated
energy.
3. Avoid mounting the transducers on a section of pipe with any external scale. Remove all scale, rust,
loose paint etc., from the location. Do not mount the transducers on a surface aberration (e.g., pipe
seam, etc.).
4. Do not mount transducers from different ultrasonic flow meters on the same pipe. Also, do not run
the transducer cables in common bundles with cables from communication equipment, other
electronic systems or any type of ultrasonic equipment. You can run these cables through a common
conduit ONLY if they originate at the same flowmeter.
5. Never mount transducers under water, unless you order submersible units and you install them in
accordance with factory instructions.
6. Avoid mounting transducers on the top or bottom of a pipe. The ideal placement is either the nine
o’clock or three o’clock position for Reflect Mode, or one transducer at nine o’clock and the other at
three o’clock for Direct Mode. Mounting on a vertical pipe is recommended only if flow is in the
upward direction.
Preparing the Pipe Surface
1. Pick a mounting location with the longest straight run. You must have easy access to at least one side of
your pipe. The mounting location must remain full, even at zero flow.
2. Decide on your mounting mode (Z or V). Use V Mode whenever possible.
3. After receiving the spacing dimensions from the Installation Menu, prepare the pipe surface. Degrease
the surface, if necessary, and remove any grit, corrosion, rust, loose paint, etc. Use abrasive material
provided to create a clean contact surface for the transducers.
4. Refer to the next sections for illustrated instructions on how to locate each area to be cleaned and how to
use each mounting option.
5. Install transducers in accordance with instructions in the manual and the appropriate installation
drawings.
6. Apply a 1/4” wide bead of couplant edge-to-edge down the
center of the emitting surface of the transducers.
7. Follow the instructions in the manual for installing the
transducers.
8. For permanent applications allow the RTV type couplant to
cure. It cures at room temperature upon exposure to
moisture in the air. During the cure, it releases acetic acid
Please note that the instructions show vertical mounting for clarity
purposes only. Do not install transducers on the top of a pipe. NOTE: In
the following paragraphs, references to the 9 o’clock position indicate
the section of the pipe that is closest to you.

BE6200 Ultrasonic Flow Meter O&M Manual
Flomotion Systems, Inc ~ FlomotionSystems.com Page 19
(vinegar like odor). It reaches full cure within 24 hours.
7. Optional Data Logger Setup
Logger Includes: SD card Interface, 2G SD Memory Card, Connection Cable, SD USB Memory Card Reader
(1) Logger Program Setup / Logger Status
1. Enter menu 50 to enable data logger and then select desired records to store.
2. Set Start Time, Interval and Log Times enter menu 51. By setting the Start Time to **:**:**, the
instrument will start logging instantly. If you set it to 22:00:00, it will start log time at 22:00:00. The
minimum logging interval is 1 second and the maximum is 24 hours. Set the Log Times to 1-9998 to limit
the amount of logs or set it to 9999 (equal to infinity), this will set the BE6200 to continual recording data.
3. Enter menu 52 select 0. Internal SerBus.
4. Check LED Status for normal operation and for saving data. The red LED on the interface will flash
according to diagram below. If the logger’s data status is normal the log file (print.txt) will be created and
accessible through the SD card.
LOGGGER LED STATUS
LOGGER DATA STATUS
LED will blink ON for .2 sec then OFF for .8 sec
Normal Operation
ON for 1 Second
Saving Data
Always ON, Check To Make Sure SD Card Is Formatted For
FAT32 Also Log Interval Could Be Set For 1 Sec
Possible Error
Always OFF,Check To Make Sure SD Card Is Inserted
Correctly, Read/View bellow. Also Check Power.
Error
(2) Logger Cable Connection / SD Connection
HOW TO INSERT SD CARD
Slide 2G SD Card in to the Interface pin side down.
Card is secure once clicked in place.
HOW TO REMOVE SD CARD
Push and release SD card; once you hear a click
the SD card will back out of the interface for removal.
PIN
DESCRIPTION
1
3.6 v
2
GROUND
3
NOT CONNECTED
4
DATA INPUT
SD DATA LOGGER
LED

BE6200 Ultrasonic Flow Meter O&M Manual
Page 20 Flomotion Systems, Inc ~ FlomotionSystems.com
III. Display Windows
1. Summary
All display windows of BE6200 and their descriptions will be discussed in this chapter. The user can enter
display windows following the instruction given in Chapter II, i.e. to realize the communication
between the user and the machine. The followings are the display menus, which are defined by 2 numbers on the
left column.
MENU
FLOW TOTALIZER/DISPLAY
MENU
OPTION SETUP
MENU
ENERGY METER MENU
00
Flow Rate/Net Totalizer
40
Damping
80
Batch Trigger Select
01
Flow Rate/Velocity
41
Low Flow Cutoff Val.
81
Flow Batch Controller
02
Flow Rate/POS Totalizer
42
Set Zero
82
Date Totalizer
03
Flow Rate/NEG Totalizer
43
Reset Zero
83
Automatic Amending
04
Date Time/Flow Rate
44
Manual Zero Point
84
Energy Unit Select
05
Energy Flow Rate/Energy Totalizer
45
Scale Factor
85
Temperature Select
06
AI1, AI2 (Analog Inputs)
46
Network IDN
86
Specific Heat
07
AI3, AI4 (Analog Inputs)
47
System Lock
87
Energy Totler ON/OFF
08
48
Entry to Calib. Data
88
Energy Multiplier
09
Net Flow Today
49
Serial Port Traffic
89
Temperature Diff.
MENU
INITIAL SETUP
MENU
OUTPUT/INPUT SETUP
8.
Heat Meter is On
10
Pipe Outer Perimeter
50
Data Logger Option
MENU
DIAGNOSTICS
11
Pipe Outer Diameter
51
Data Logger Setup
90
Strength + Quality
12
Pipe Wall Thickness
52
Send Log- Data To
91
TOM/TOS*100
13
Pipe Inner Diameter
53
Analog Input AI5
92
Fluid Sound Velocity
14
Pipe Material
54
OCT Pulse Width
93
Total Time, Delta Time
15
Pipe Sound Velocity
55
CL Mode Select
94
Reynolds No, Profile
16
Liner Material
56
CL 4mA Output Value
95
ETP ETN
17
Liner Sound Velocity
57
CL 20mA Output Value
MENU
OTHERS
18
Liner Thickness
58
CL Checkup (mA)
+0
Power ON/OFF Time
19
Inside ABS Thickness
59
CL Current Output
+1
Total Work Time
20
Fluid Type
60
Date and Time
+2
Last Power Off Time
21
Fluid Sound Velocity
61
Software Version and ESN
+3
Last Flow Rate
22
Fluid Viscosity
62
RS-485/RS-232 Setup
+4
ON/OFF Times
23
Transducer Type
63
Select Comm Protocol
+5
Calculator :input X=
24
Transducer Mounting
64
AI3 Value Range
+6
Media Vel. Threshold
25
Transducer Spacing
65
AI4 Value Range
+7
Total Flow for Month
26
Default Settings
66
AI5 Value Range
+8
Total Flow This Year
27
Save/Load Parameters
67
FO Frequency Range
+9
No-Ready Timer
28
Holding for Poor Signal
68
Low FO Flow Rate
29
Empty Pipe Setup
69
High FO Flow Rate
MENU
FLOW UNIT SETUP
70
LCD Backlight Option
30
Measurement Unit in
71
LCD Contrast
31
Flow Rate Unit
72
Working Timer
32
Totalizer Unit
73
#1 Alarm Low Value
33
Totalizer Multiplier
74
#1 Alarm High Value
34
NET Totalizer
75
2# Alarm Low Value
35
POS Totalizer
76
2# Alarm High Value
36
NEG Totalizer
77
77 Beeper Setup
37
Totalizer Reset
78
OCT Output Setup
38
Manual Totalizer
79
Relay Output Setup
39
Language Selection
3.
Segmental LCD
#
#
Table of contents
Other Flomotion Systems Measuring Instrument manuals
Popular Measuring Instrument manuals by other brands
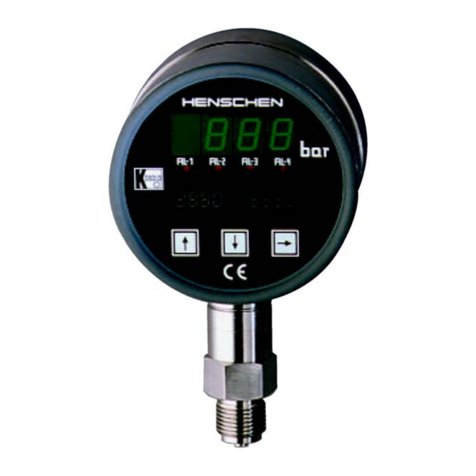
Kobold
Kobold Henschen MAN-SF Series operating instructions
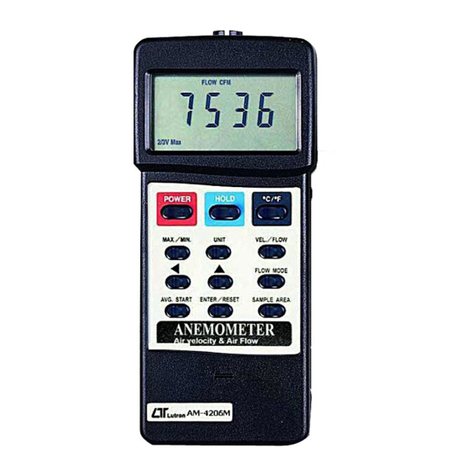
Lutron Electronics
Lutron Electronics AM-4206M Operation manual
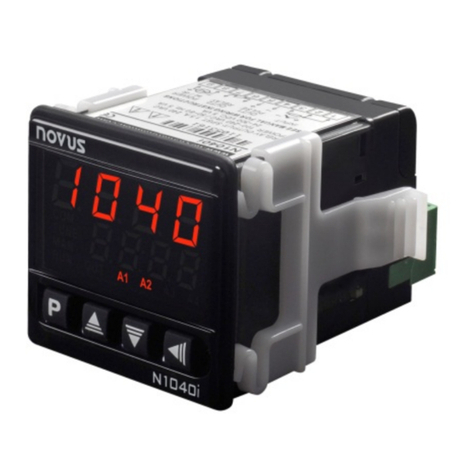
Novus
Novus N1040i user manual
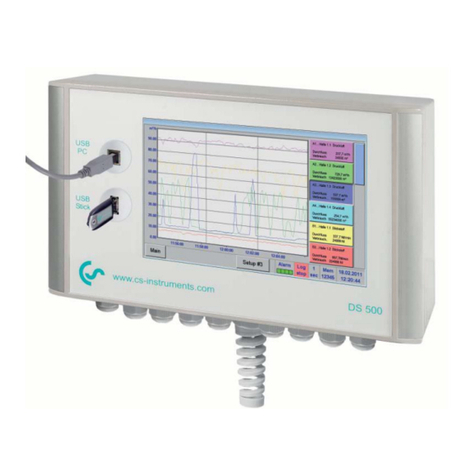
CS Instruments
CS Instruments DS 500 Modbus Installation and operating instructions
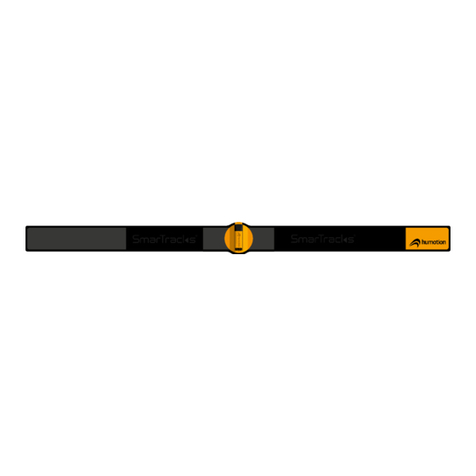
humotion
humotion SmarTracks Diagnostics v.3.16 Installation guide & user manual
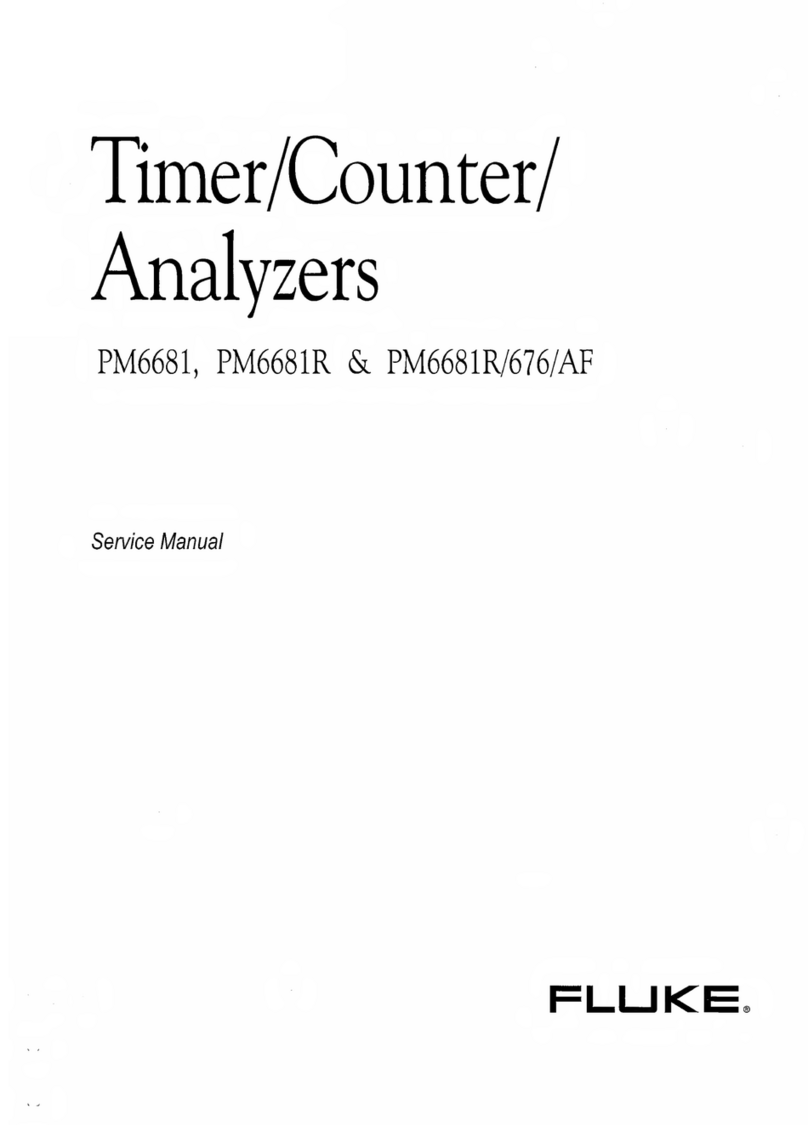
Fluke
Fluke PM6681 Service manual