MAXIMATOR DLE 5 Setup guide

1
Operating, maintenance and repair
instructions for
MAXIMATOR
®
Compressors
DLE 5
MAXIMATOR GmbH
Walkenrieder Straße 15
37449 Zorge
Phone: +49-55 86-80 30
Fax: +49-55 86-8 03 40 E-Mail: Info@maximator.de
Homepage: www.maximator.de

2
1 Index
1Index _________________________________________________________ 2
2Mode of operation _______________________________________________ 3
3Safety instructions_______________________________________________ 4
3.1 Usage to the intended purpose _________________________________ 4
3.2 Emission___________________________________________________ 4
3.3 Safety hazards ______________________________________________ 4
3.4 Safety at the place of assembly _________________________________ 5
4Technical data__________________________________________________ 5
4.1 Dimension drawing___________________________________________ 5
5Mounting ______________________________________________________ 7
5.1 Assembly __________________________________________________ 7
5.2 Compressed air system _______________________________________ 7
5.2.1 Compressed air quality ____________________________________ 7
5.2.2 Compressed air oiler______________________________________ 7
5.2.3 Line cross-sections _______________________________________ 7
5.2.4 Direct pilot valve air_______________________________________ 8
5.3 High-pressure system ________________________________________ 8
5.3.1 Inlet___________________________________________________ 8
5.3.2 Pressure line____________________________________________ 8
5.3.3 Pumping medium ________________________________________ 8
5.4 Operation __________________________________________________ 8
6Maintenance ___________________________________________________ 9
7Warranty ______________________________________________________ 9
8Repair ________________________________________________________ 9
8.1 High-pressure sealing repair __________________________________ 10
8.1.1 Dismantling ____________________________________________ 10
8.1.2 HP piston assembly _____________________________________ 13
8.1.3 HP cylinder assembly ____________________________________ 16
8.2 Repair of air drive parts and pilot valves _________________________ 18
8.2.1 Dismantling ____________________________________________ 18
8.2.2 Assembly______________________________________________ 23
8.3 Repair of suction and delivery valves____________________________ 32
8.3.1 Dismantling ____________________________________________ 32
8.3.2 Assembly______________________________________________ 35
8.4 Spool valve________________________________________________ 39
8.4.1 Dismantling ____________________________________________ 39
8.4.2 Assembly______________________________________________ 41

3
2 Mode of operation
As a rule, the MAXIMATOR compressors operate according to the pressure
intensifier principle: large surface area with a low pressure (air piston(3)) small
surface area with a high pressure (HP piston(2)). A continual flow is attained by
continuous pulsation. This pulsation is achieved by an impulse-controlled 4/2-way
valve (servo-valve(4)). The servo-valve alternately impinges the top and bottom side
of the air pistons. The servo-valve is selected via two 2/2-way valves (pilot valves(7))
that are mechanically by the air piston in its end positions. The pilot valves ventilate
and vent the actuation chamber of the servo-valve. The drive air provides the
restoring force for the servo-valve. In the actuation chamber the servo-valve has a
larger effective surface area than in the control chamber that is permanently
impinged with compressed air. The HP piston generates the volume flow by means of
check valves (suction valve, delivery valve(1)). The HP section of the compressors
consists of two stages. The first stage has a low pressure ratio and conveys directly
into the second stage with a high pressure ratio. These two stages allow for the
generation of a high operating pressure with sufficient compressor capacity, even
with a low admission pressure. The initial pressure depends on the adjusted drive
pressure. The below formula:
ALB
P
i
i
PiP **
1
2
2
+=
is used to calculate the static final pressure. Upon reaching the final pressure the
compressor stops and ceases to consume air. Only a pressure drop at the high-
pressure side or a pressure increase at the drive side occasion the compressor to re-
start.
where:
P
B
: Operating pressure
PL : Drive pressure
PA : Admission pressure
i : Pressure ratio

4
3 Safety instructions
MAXIMATOR compressors are manufactured to the latest state of the art and are
safe to operate. However, there are potential hazards in case of inadvertent wrong
operation or wrong use:
• For the health and lives of persons.
• For the compressor and its accessory parts as well as other assets.
• For the life cycle and the performance capacity of the compressors and its
accessory parts.
Operation, maintenance and assembly of the compressor may only be carried by
personnel who are familiar with working on pneumatic systems and are familiar with
the hazards entailed by such systems. In addition, the operating instructions shall be
thoroughly studied and adhered to.
3.1 Usage to the intended purpose
The compressors may be exclusively used with those media for which they are
suitable according to our media endurance schedule. Any other media have to be
tested by us for compatibility with the compressor materials prior to being used. The
compressor drives are designed for compressed air up to 10 bar, other gases have to
be tested by us for compatibility with the compressor materials prior to being used.
Changes and modifications of the compressors are prohibited for safety reasons.
All maintenance, assembly and operating instructions specified in these operating
instructions must be adhered to in order to guarantee full functioning and safety.
3.2 Emission
Expanding compressed air is, depending on the specific application, prone to
generate a certain level of noise. Moreover, exhausting air from the silencer may be
fouled with water and oil (grease). It is also possible that small ice crystals form at the
silencer, become loose and fly around. This is why persons have to wear goggles
and, if need be, ear protection while in the vicinity of running compressors.
3.3 Safety hazards
During operation of the unit, both the drive part and the high-pressure part are under
pressure. Hence, it should be borne in mind that any gas that may leak due to a
defect or also during normal operation are highly pressurised and must not be
contained or deviated by objects or body parts. It must be ensured that in case of a
defect a compressor is immediately depressurised and repaired.
Maintenance and repair work may only be carried out at depressurised units.

5
3.4 Safety at the place of assembly
MAXIMATOR compressors must not be operated in closed containers, since the
discharged drive air may burst the container.
The high-pressure bolted connections at the suction and pressure sockets must not
be unscrewed, even if this would facilitate the erection of the compressor. The bolted
connections must be firmly tightened in order to avoid any leakages and damage.
The air drive has been designed in such manner that the compressors are safe to be
operated in areas that subject to explosion hazards.
The compressor should be installed in such a manner that the operating elements
and bolted connections are freely accessible at any time.
4 Technical data
Type Pressure ratio
Compression ratio
Admission pressure
Min. Max. Max.
operating pressure
Turn-of-
piston
volume Max.
stroke frequency
Threaded connection
Max. operating
temperature Weight
i bar bar cm31/min Inlet*Outlet*°C kg
(i1/i2) PAPB
DLE 5
1:5 1:15 2 50 50 746 110 BSP 1/2 BSP 1/2 60 20
4.1 Dimension drawing

6

7
5 Mounting
5.1 Assembly
The mounting position of the compressor is optional. It must be ensured that there is
no ingress of foreign matter into the connections of the compressor during assembly
(e.g. boring dust during wall mounting). Hence, the blind plugs in the connections of
the compressor should only be removed immediately before fastening the respective
connections.
5.2 Compressed air system
We recommend the use of one of our air control units for compressed air supply. The
units consist of a filter, water separator, shut-off valve, pressure controller, pressure
gauge and, where appropriate, a safety valve. If there is no maintenance unit
employed it must be ensured that the compressed air quality complies with our
specifications.
5.2.1 Compressed air quality
• Solid matter:
o Max. particle size: 5µm
o Max. particle concentration: 5mg/m³
• Dew point
o + 10°C = water content 9.4g/m³
up to +2°C = water content 5.6g/m³
5.2.2 Compressed air oiler
As a rule, a compressed air oiler is not required. All moving parts have been treated
with special grease during assembly.
The grease may become gummy when the compressor is operated for a longer
period of time with extremely dry air. It is recommended to replace the compressed
air oiler in such a case.
Caution! If the compressor has been operated with a compressed air oiler it must not
be later used without an oiler because the oil washes all grease out of the
compressor and thus prevents permanent lubrication. The remedy is re-lubrication
with MAXIMATOR grease.
If a compressed air oiler is used, the oil content of the air should be 1mg/m³ to
5mg/m³.
5.2.3 Line cross-sections
The air supply should not be dimensioned smaller than the threaded connection, a
reduction to a smaller threaded connection may result in performance losses and
malfunctions of the pump. Also excessively long supply lines may cause problems
due to the pressure drop in a small line.

8
5.2.4 Direct pilot valve air
The compressors are designed for operation with direct pilot valve air which should
be connected downstream of the pressure controller, if applicable. Thus, the pump
can reverse better with small drive pressures. The compressor does not operate
unless the direct pilot valve air is connected.
5.3 High-pressure system
The employed HP piping and accessory parts must be matched in their pressure and
cross-section to the compressor, otherwise the efficiency and safety of the
compressor may be impaired.
5.3.1 Inlet
In order to achieve economic compressor output capacities and the indicated end
pressures, the compressors have to be impinged with an admission pressure of the
gas to be compressed. Only compressors with a pressure ratio of 2 can operate
without admission pressure.
If there is no admission pressure available, an optimal compressor performance can
only be realised with an underpressure-tight suction line. Otherwise the conveyed
medium may be contaminated by ambient air. Cutting-ring bolted connections are not
suitable.
A filter with a mesh width of max. 10µm should be installed into the suction line to
avoid damage at the suction and delivery valves as well as at the HP sealing.
5.3.2 Pressure line
The pressure line and the respective accessories must withstand the max. initial
pressure of the compressor. It is recommended to install an appropriate safety valve
into the pressure line.
5.3.3 Pumping medium
The compressors shall be exclusively used with media that are suitable according to
our media endurance schedule. Any other media have to be tested by us for
compatibility with the compressor materials prior to being used.
5.4 Operation
The compressor starts to deliver as soon as drive air as well as direct pilot valve air
are available.
Escaping drive air is used in compressors with a higher pressure ratio to cool down
the HP parts. However, when a compressor is running in continuous operation with a
high stroke frequency, there may be considerable heating up of the compressor
despite cooling. This may result in increased wear of the sealings. It is recommended
to monitor the temperature of the compressed gas in order to avoid overheating.
Temperatures above 100°C at the compressor outlet should be avoided.

9
6 Maintenance
The air drives of all compressors have been pre-treated with heavy-duty grease and
do not require any other type of lubrication. Only during overhauling of the
compressor, the servo-valves and air pistons should be treated with acid- and silicon-
free Maximator grease.
7 Warranty
We grant a warranty for the material and manufacturing quality of our products of six
months commencing upon the shipping date of the unit.
Defects that may be caused by inappropriate handling or malfunctions, the use of
inadmissible liquids, foreign matter in drive or pumping media or be exceeding the
max. operating pressure are not subject to warranty. Wearing parts, such as
sealings, guide elements, etc., are exempted from our warranty.
8 Repair
All repair work is to be carried out be qualified skilled personnel under extremely
clean conditions. Even smallest impurification may cause serious damage at the
precision-machined pneumatic components.
All individual pump and compressor parts are available from MAXIMATOR as spare
parts. The respective purchase order numbers can be gathered from the drawings
attached to each compressor. Typically, there is more than one sealing defective or
worn out, hence, we have compiled different sealing kits. The compositions of sealing
kits can be gathered from the drawings, like the respective purchase order numbers.
Make sure to indicate the compressor serial number when ordering spare parts. The
serial number is located in the machine plate of the compressor and is also punched
into the compressor housing (as a 6-digit number).
It goes without saying that the most convenient approach for you is to ship a
defective unit to us. All repairs are carried out by qualified persons in our workshops,
where there are no metal-cutting activities and thus extreme cleanliness is ensured.
As a rule we acknowledge the receipt of the forwarded unit and send you a cost
estimate and, after your confirmation, repair your unit as quickly as possible and
return it to you.
Note: Via our Homepage, you can access detailed repair instructions and
drawings of the individual compressors that are to provide support to
you during repair work or in case of any problems.

10
8.1 High-pressure sealing repair
8.1.1 Dismantling
Loosen the four hexagon nuts from the stud
bolts.
Carefully separate the compressor head by
means of light taps with a plastic hammer
from the HP cylinder.
Loosen the HP cylinder by means of light taps
with a plastic hammer from the top cover.
Draw the HP cylinder from the HP piston.

11
Remove the retaining pin of the castle nut.
Loosen the castle nut. If the HP piston follows
to turn, it is recommended to use an impact
screwdriver to loosen the castle nut.
Remove the piston disk.
Remove the piston sealing ring and O ring from the HP piston.

12
Draw the HP piston from the piston rod.
Remove the O ring from the HP piston.
Remove the O rings of the HP head.
Dismantle the O ring that seals the HP
cylinder.

13
8.1.2 HP piston assembly
Clean all re-used components and inspect them for any damage.
Slightly grease all sealing and guide elements.
Use preferably MAXIMATOR grease Works No. 3610.1456.
Grease the top and bottom cover the O rings that seal the HP part and assemble the rings
(first and second stage).
Attach the HP piston to the piston rod.
Grease the O ring and insert it into the groove between HP piston and piston rod.

14
Grease the O ring and mount it into the HP piston.
Grease the HP cylinder.
Insert the piston sealing ring into the HP
cylinder and align the ring parallel ca. 13 mm
below the cylinder edge.
Push the HP cylinder over the HP piston until
the piston sealing ring fits close to the O ring.

15
Attach the piston disk.
Attach the spring lock washer and the castle
groove.
Tighten the castle groove with 25 Nm. The
piston sealing ring is pushed onto the O ring
during tightening.
Use the retaining pin to secure the castle nut
(appropriately bend the retaining pin with a
screwdriver).

16
8.1.3 HP cylinder assembly
Push the HP cylinder over the O ring of the
top cover till to the stopper.
Caution: Make sure not to damage the O ring.
Grease and mount the O rings that seal the HP head.

17
Push the compressor head over the stud bolts.
Make sure that the suction and pressure lines
can be mounted without any warping.
Attach the hexagon nuts and screw retainers
to the stud bolts. (Do not tighten!)

18
8.2 Repair of air drive parts and pilot valves
The HP parts have to be dismantled before the air drive parts can be disassembled.
8.2.1 Dismantling
8.2.1.1 Dismantling of the air drive
Remove the servo-valve and the air pipe, loosen the 4 socket head screws.
Remove the four hexagon nuts from the
hexagon bolts.
Draw the bottom cover from the air cylinder. Now also the pressure pipe can be dismantled.
Caution: The piston rod must not be withdrawn from the top cover because it may get jammed
in the end groove.

19
Withdraw the air cylinder from the top cover
and the air piston.
Pull the air piston slightly out of the top cover and remove the retaining pin and bolts.
Pull the piston rod out of the top cover into
the direction of the HP part.
Remove the O ring from the air piston.

20
8.2.1.2 Dismantling of top cover and bottom cover
Remove the locking ring.
Knock the bearing bush out of the top and bottom covers by means of a plastic mandrel.
Remove the O rings from the bearing bush.
Remove the sliding rings and O rings from the bearing bush.
Table of contents
Other MAXIMATOR Air Compressor manuals
Popular Air Compressor manuals by other brands

ABB
ABB HT606743 Operation manual
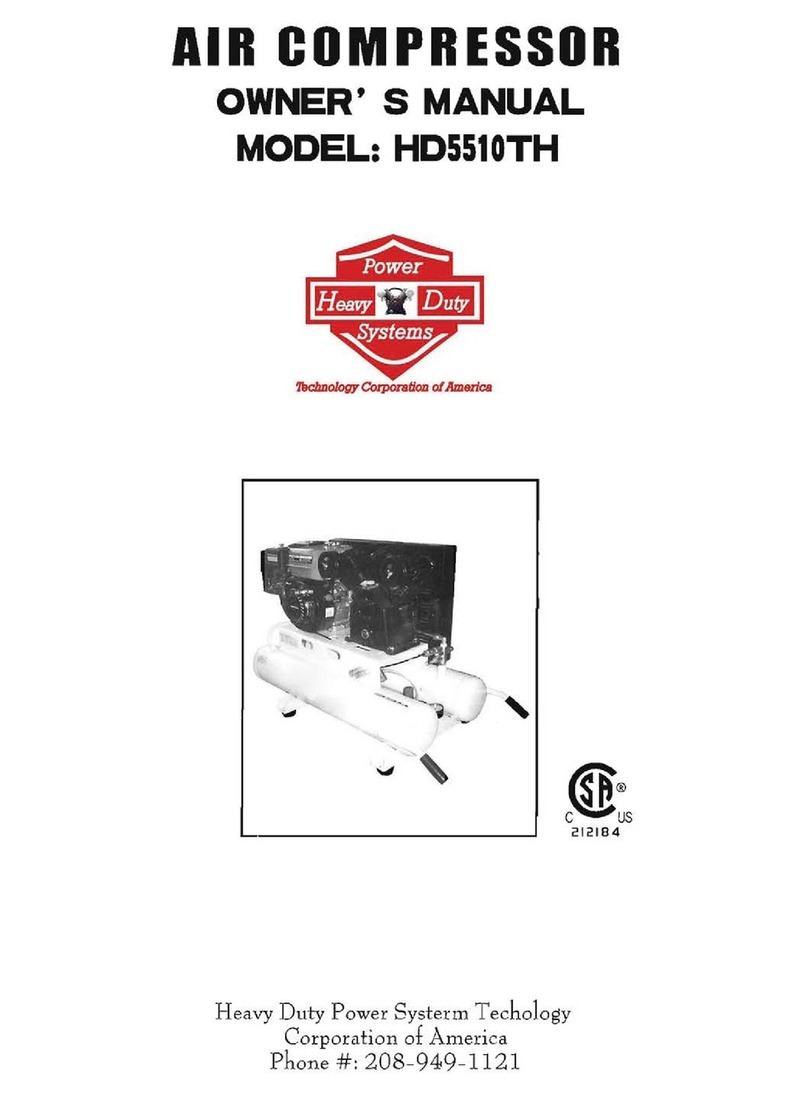
Heavy Duty Power Systems
Heavy Duty Power Systems HD5510TH owner's manual
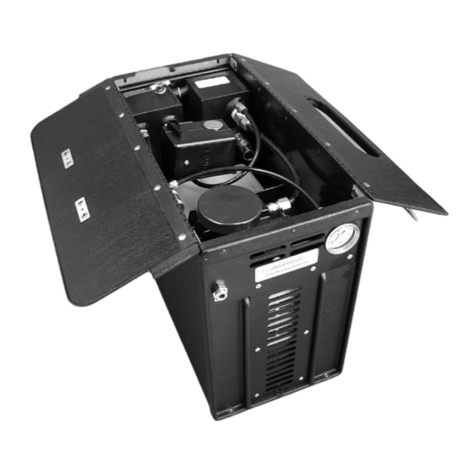
Aseptico
Aseptico AA-74 Installation, operation and maintenance instructions manual
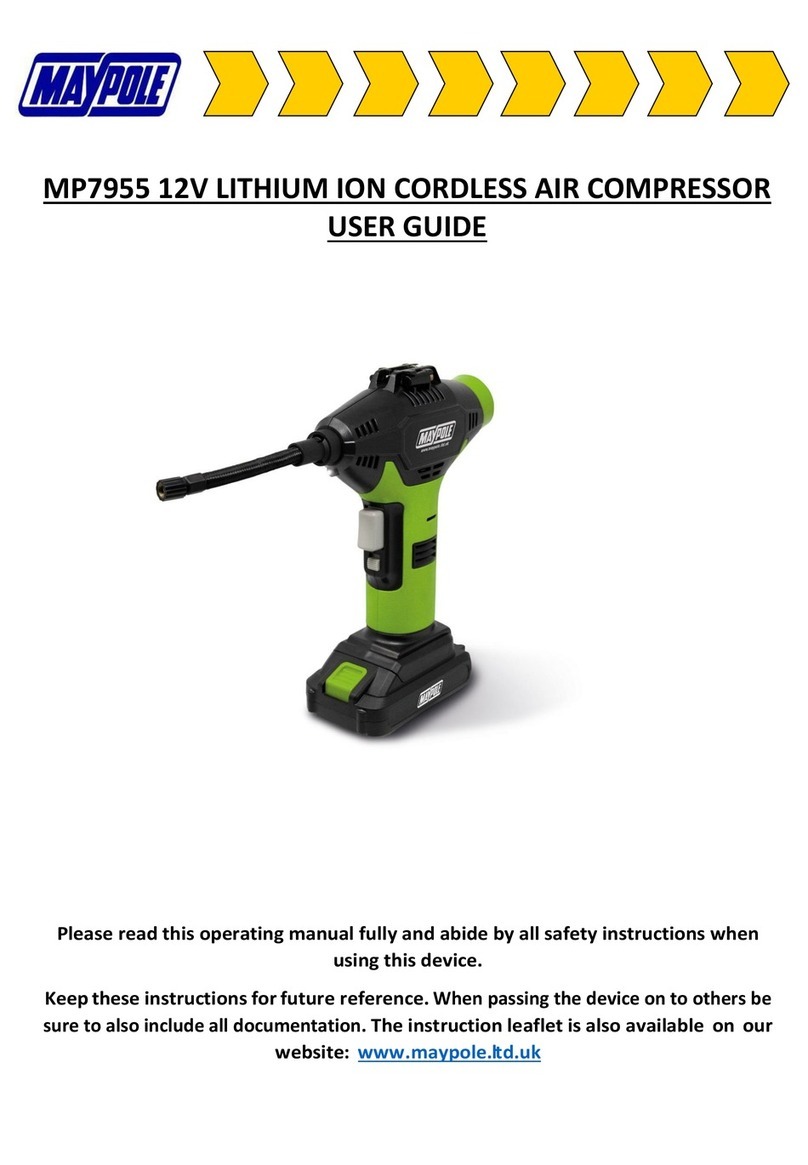
MayPole
MayPole MP7955 user guide
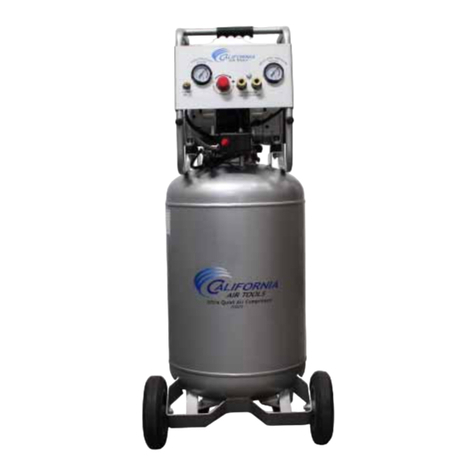
California Air Tools
California Air Tools 20020 owner's manual
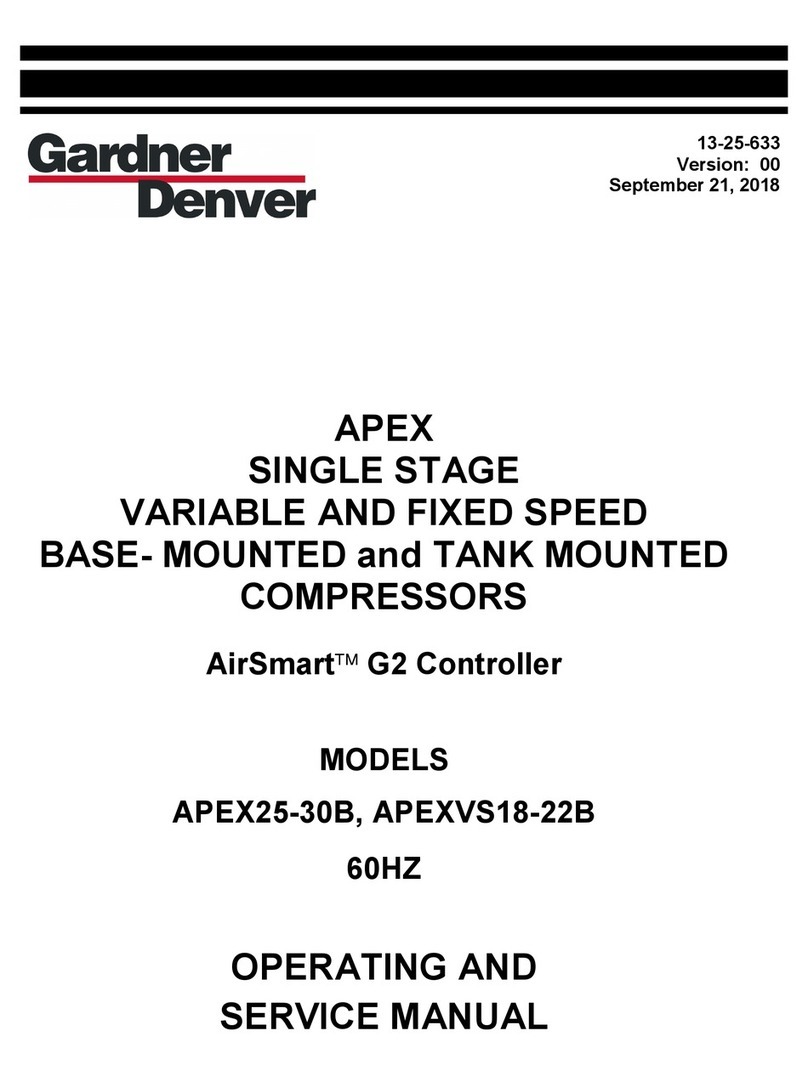
Gardner Denver
Gardner Denver APEX25-30B Operating and service manual
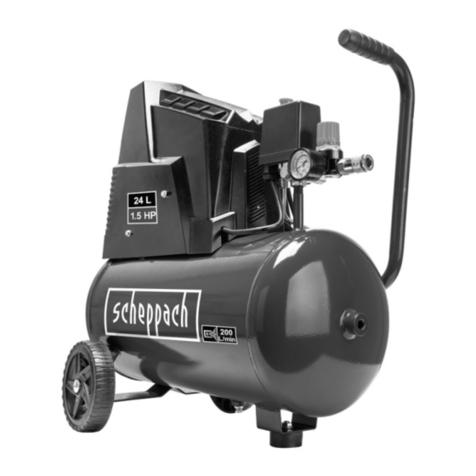
Scheppach
Scheppach HC30o Translation of original instruction manual
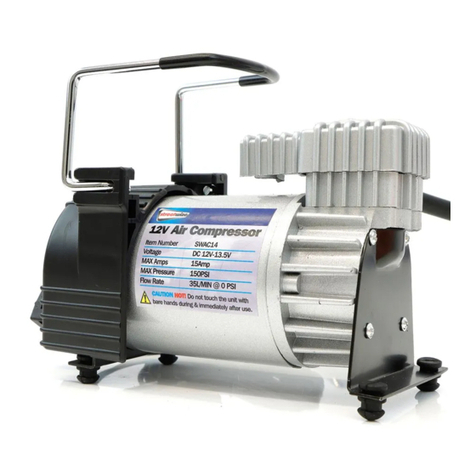
Streetwize
Streetwize S8AC14 quick start guide
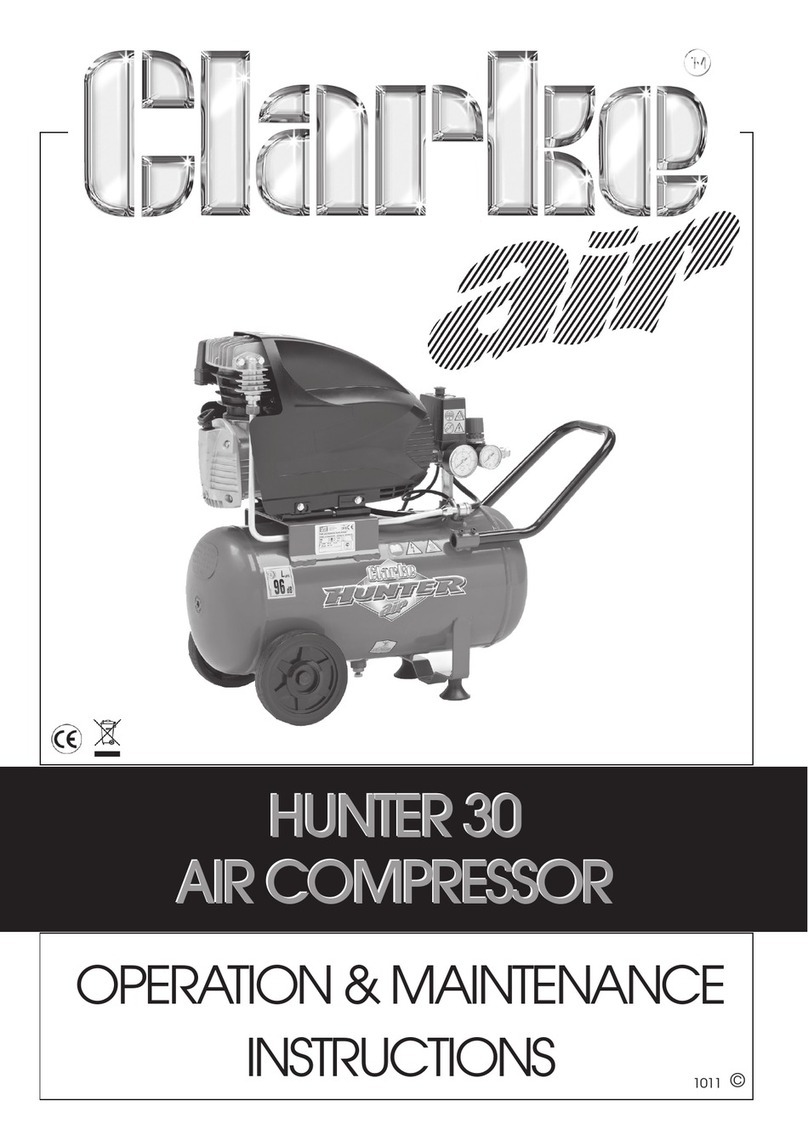
Clarke
Clarke HUNTER 30 Operation & maintenance instructions
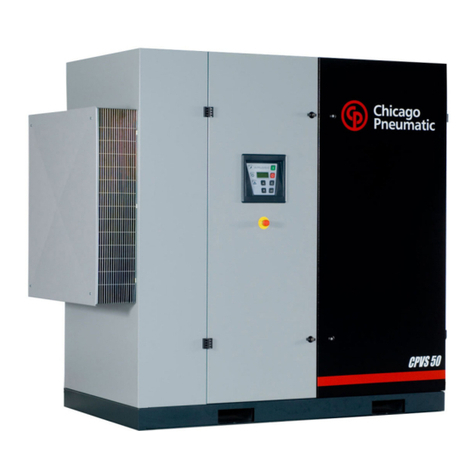
Chicago Pneumatic
Chicago Pneumatic CPVS 40 instruction manual
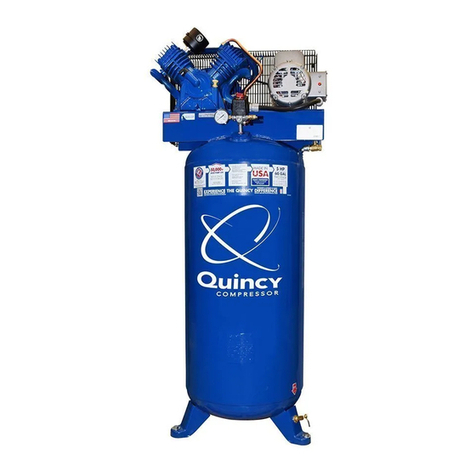
Quincy Compressor
Quincy Compressor Industrial Series instruction manual

Atlas Copco
Atlas Copco G 18 Instruction book