Midcontinent MD23-342 Technical Document

Manual Number
9019161
Revision C
August 18, 2023

Manual Number 9019161 Revision C, August 18, 2023 2
FOREWORD
This manual provides information intended for use by persons who, in accordance with current
regulatory requirements, are qualified to install this equipment. If further information is required,
please contact:
Mid-Continent Instruments and Avionics
Attn: Customer Service Dept.
9400 E. 34
th
St. N.
Wichita, KS 67226 USA
Phone 316-630-0101
Fax 316-630-0723
mcia@mcico.com
www.mcico.com
We welcome your comments concerning this manual. Although every effort has been made to keep
it free of errors, some may occur. When reporting a specific problem, please describe it briefly and
include the manual part number, the paragraph/figure/table number, and the page number. Send
your comments to:
Mid-Continent Instruments and Avionics
Attn: Customer Service Dept.
9400 E. 34
th
St. N.
Wichita, KS 67226 USA
Phone 316-630-0101
Fax 316-630-0723
mcia@mcico.com
© Copyright 2020
Mid-Continent Instrument Co., Inc.
Download the current
version of this installation
manual using your
smartphone or tablet.

Manual Number 9019161 Revision C, August 18, 2023 3
REVISION HISTORY
Rev Date Detail Approved
A 09/09/2020 Production release. BAW
B 10/18/2022
Added data for IMU (-3) configuration. Added NVIS
versions. Added a feature cross reference table by unit
version (1.3). Added QR code, page 2.
CAS
C 08/18/2023
Updated TSO compliance for addition of C6e.
Corrected multiple Table references.
Added note to clarify product version/’dash number’
references at bottom of page 6.
CAS

Manual Number 9019161 Revision C, August 18, 2023 4
TABLE OF CONTENTS
SECTION 1 GENERAL DESCRIPTION 5
1.1 Introduction 5
1.2 Technical Specifications 6
SECTION 2 PRE-INSTALLATION CONSIDERATIONS 8
2.1 Cooling 8
2.2 Equipment Location 8
2.3 Routing of Cables 8
2.4 Limitations 8
2.5 Modification 9
SECTION 3 INSTALLATION PROCEDURES 10
3.1 General Information 10
3.2 Parts List 10
3.3 Cable Harness 10
3.4 Pneumatic pressure Connections 15
3.5 Mounting 15
3.6 Installation Completion 16
SECTION 4 OPERATION 18
4.1 General Function 18
4.2 User Interface 19
4.3 Pre-Flight Mode 20
4.4 Flight Mode 21
4.5 Configuration Mode 24
SECTION 5 CONFORMANCE 30
5.1 Instructions for Continued Airworthiness 30
5.2 Environamental Qualification Statement 32

Manual Number 9019161 Revision C, August 18, 2023 5
SECTION 1 GENERAL DESCRIPTION
INTRODUCTION
The model MD23 series FLEX Custom Function Display (“CFD”) is a panel-mounted instrument
capable of displaying various inputs in a configurable graphical presentation. FLEX
is an off-the-
shelf solution that is FAA and EASA TSO-approved with Level A design assurance software
certification. The power of FLEX
is its ability to become exactly what your application requires
without the time and cost of a product development and certification effort. This unique new
breakthrough in avionics uses a Patent Pending software concept that allows it to be quickly
customized to your requirements by Mid-Continent Instruments and Avionics without re-certification.
With the ability to receive and send multiple types of inputs and outputs, allow user interface, and
display custom designed graphics, FLEX
is as flexible as it gets.
The MD23 is a general purpose CFD indicator in a standard 2-inch (2-¼”) rear-mounted form-factor
with a daylight readable color IPS-LCD display and a push-and-turn knob. The model series comes
in three hardware platforms, each with a 26-pin electrical connector, one with quick-disconnect pitot
and static pneumatic inputs, and one with integrated IMU sensing. A USB port is accessible behind
a cover on the rear of the unit for field-loadable software updates and installation of a Custom
Instrument Definition (CID) file.
The unique Multi-I/O (MIO) feature allows twelve of the unit’s electrical inputs to be configured per
the CID file to either accept or output various types of signals and information. MIO pins can be
defined to be an analog input, a discrete on/off input, an analog output, or a discrete output. In the
indicator version of the unit (non-pitot/static), the unit is also capable of accepting up to three
independent frequency inputs for tachometer or related use. There are two ARINC 429 serial inputs
and one output. The ARINC labels can be defined as needed for each application. The ARINC
output can combine both ARINC inputs, user selections, and translate MIO (analog/discrete) inputs
into a single ARINC data stream. The remaining interface options include a thermocouple input,
RS-232, RS-422, RS-485, an external dimming control, and 10-32VDC power.
An Inertial Measurement Unit (IMU) based on 6-axis of internal sensing gives FLEX the ability to
function as a standalone solution to a variety of traditional inertial instruments, such as an attitude
indicator, turn coordinator, g-meter, or AHRS data source. By combining internal IMU data with
external data such as magnetic heading, FLEX can be further configured to display navigational
information in a custom display that meets the unique needs of any aircraft.
The MD23 FLEX
can add a new function to your panel, combine multiple data sources into a single
display, or control external equipment. The FLEX
is a great tool for any panel upgrade, STC, or
forward-fit challenge. It brings a cost effective and certified product together with the flexibility to
configure it to your custom requirements, making it the perfect value and solution for your specific
cockpit display and control needs.

Manual Number 9019161 Revision C, August 18, 2023 6
TECHNICAL SPECIFICATIONS
Electrical Attributes
Input Voltage 10-32 VDC
Input Power 4 watts (0.14A @ 28VDC)
Lighting Input 5, 14, or 28VDC or automatic photocell control
Battery Backup (clock function only) Rechargeable coin cell (qty 1)
Table 1.1
Data Inputs and Outputs*
Analog Input (-1, -2)
Input (-3)
Output (-1, -2)
Output (-3)
0V to 28VDC, ±0.050V accuracy, impedance >50Kohms
-24V to 29VDC, ±0.050V accuracy, impedance >50Kohms
0V to 5VDC, ±0.050V accuracy,
-8V to 8VDC, ±0.050V accuracy,
Discrete Input
Output
Sensing of open or ground
Open, Ground, Pullup to 5V
Frequency Input (-1)
0.5-100VDC pk-pk, input impedance >50K ohms
10-20,000 Hz (3 input pairs; differential or single-ended)
ARINC 429 Input
Output
Low/High Speed input; 2 input channels
Low/High Speed output; 1 output channel
RS-232 Format per CID; 1 receive, 1 transmit
RS-422/485 (-3)
Format per CID; 2 channels / 4 wires, bidirectional
Thermocouple (-1, -2)
1 pair; cannot be grounded
Pressure Static (-2)
Pitot (-2)
0-15 psi absolute (TSO accurate -1,500 to +55,000 feet)
±15 psi differential (TSO accurate 20 to 500 knots)
Table 1.2
Available Features by Unit Version* -1 -21 -2 -22 -3 -23
Standard Display
NVIS Display
Analog / Discrete Multi-IO
ARINC 429
RS-232
RS-422 / RS-485
Pneumatic Inputs
Frequency / Tachometer Inputs
Inertial Sensors
Thermocouple Input
External Dimming Input
Table 1.3
* NOTE: All references to -X throughout the document also apply to -2X respectively. -2X versions
represent the NVIS display version of the respective -X version and are otherwise identical.

Manual Number 9019161 Revision C, August 18, 2023 7
Physical Attributes
Weight 0.4 pounds (0.17 kg)
Dimensions 2.43” x 2.43” x 1.0” (HxWxD)
Mating Connectors 26-pin D-Sub and backshell MCIA p/n 9019162-1
Pneumatic fittings MCIA p/n 9019162-2
Mounting Rear Panel Mount with (4) #6-32 screws;
2.25 inch round bezel
Table 1.4
IMU Performance Limits (-3)
Attitude (-3) Pitch Angle
Pitch Rate
Roll Angle
Roll Rate
No limits (360°)
500° per second max
No Limits (360°)
500° per second max
Table 1.5
Qualifications
Certifications FAA/EASA TSO-C2d (Type B), C3e, C4c, C6e, C8e, C10c,
C106, C113
b
, C201
(
A4H
4
T3
)
Environmental Qualification RTCA DO-160G (details listed in Section 5.2)
Software Qualification RTCA DO-178C, Design Assurance Level A
Lithium-ion Qualification UL 1642
NVIS Display (-21, -22, -23) Verified for installations requiring NVIS White compliance
with MIL-STD-3009 and RTCA/DO-275
Table 1.6
Exclusivity Rights
Rights U.S. Patent 11,038,389
Table 1.7

Manual Number 9019161 Revision C, August 18, 2023 8
SECTION 2 PRE-INSTALLATION CONSIDERATIONS
COOLING
No external cooling is required. The unit will generate some heat as a function of normal operation.
Installation in an area that is exposed to extreme heat or restricted airflow can reduce the expected
life of the product. Mounting the unit to a metal surface can help reduce the effects of temperature
on the unit but is not required.
EQUIPMENT LOCATION
The MD23 FLEX
is designed primarily to be installed in the instrument panel of the aircraft. The unit
has an extra-wide viewing angle allowing for flexible installation location. When selecting a panel
location for the MD23, be sure to consider appropriate field-of-view with regard to pilot and/or co-
pilot visibility and accessibility. Other locations may be acceptable if the environmental qualifications
are considered with respect to the installation approval.
Additionally, consider what equipment is behind the panel that could impede the installation.
Clearance for the unit as well as its electrical and pneumatic connections (if present) and routing
must be allowed.
ROUTING OF CABLES
Be aware of routing cables near other electronics or with other wire bundles that may be
susceptible to high energy flow. Avoid sharp bends in cabling and routing near aircraft control
cables. Also avoid proximity and contact with aircraft structures, avionics equipment, or other
obstructions that could chafe wires or hoses during flight and cause undesirable effects.
LIMITATIONS
The MD23 FLEX
series of CFDs is certified to multiple FAA TSOs with the following limitations
identified:
Deviations have been granted for the use of RTCA/DO-160G and RTCA/DO-178C rather
than the environmental and software standards specified in the TSOs.
Applicable TSOs:
Technical Standard Order Authorization to FAA TSO C113b applies to all versions of the MD23.
TSOs C2d, C8e, C10c, and C106 only apply to the version(s) of the MD23 with pneumatic inputs.
TSOs C3e, C4c, C6e, and C201 only apply to the version(s) of the MD23 with IMU capability.
Further, all TSOs are only applicable to customized configurations of the unit that represent the
major functions of each TSO.
The MD23 contains a rechargeable manganese lithium coin cell for the purpose of maintaining non-
volatile memory. Per RTCA/DO-311A, the cell is an Energy Category 1 (0.051Wh < 2 Wh) and is
certified to UL 1642, thus certification to RTCA/DO-311A is not required. Specific STC limitations or
ACO coordination is not required for product or installation qualification.
The conditions and tests for TSO approvals of this article are minimum performance standards.
Those installing this article, on or in a specific type or class of aircraft, must determine that the

Manual Number 9019161 Revision C, August 18, 2023 9
aircraft installation conditions are within the TSO standards, specification of the article, and
deviations as listed above. TSO articles must have separate approval for installation in an aircraft.
The article may be installed only according to 14 CFR part 43 or the applicable airworthiness
requirements.
MODIFICATION
This product has a nameplate that identifies the manufacturer, part number, description,
certification(s) and technical specifications of the unit. It also includes the “MOD” or modification
number representing notable changes in the hardware design of the unit.
Modification (MOD) 0 is the initial release of the product and is identified on the nameplate by the
lack of marking on the MOD numbers 1 through 9 (i.e. 1-9 are visible). All subsequent
modifications are identified on the nameplate by the marking/blacking out of that particular MOD
number (i.e. for MOD 1, the number 1 is not visible and 2-9 are visible - see Figure 2.1 for
examples). MODs do not have to be sequentially inclusive and may be applied independent of each
other.
For additional details regarding specific changes associated with each MOD status refer to the
product published Service Bulletins at www.mcico.com.
Figure 2.1 Nameplate and MOD Status Example
MOD 0
MOD 1
MOD 1 & MOD 2

Manual Number 9019161 Revision C, August 18, 2023 10
SECTION 3 INSTALLATION PROCEDURES
GENERAL INFORMATION
IMPORTANT: READ THIS ENTIRE SECTION PRIOR TO STARTING INSTALLATION!
This section contains interconnect diagrams, mounting dimensions and other information pertaining
to the installation of the MD23 FLEX
Custom Function Display. For specific pinout that uniquely
applies to each custom application, please refer to your custom User Guide, or to the CID
Requirements associated with your application.
PARTS LIST
When unpacking this equipment, make a visual inspection and notify the sender if there is any
evidence that damage may have incurred during shipment. The following parts are included:
Item Description MCIA Part Number
a. MD23 FLEX Custom Function Display 6420023-( )
b. Installation Manual 9019161
c. Electrical Connector Kit 9019162-1
i. 26-pin d-sub
ii. Size 22 contacts/sockets
iii. Backshell kit, quick-disconnect
iv. (4) #6-32 mounting screws
d. Pneumatic Connector Kit * 9019162-2
v. (2) Pneumatic Connectors, quick-disconnect
* pneumatic connector kit only included with the pitot/static version
Optional Equipment Available
a. Large Knob Kit 9019749-1
(0.57” dia x 0.67” long)
CABLE HARNESS
Construct the cable harness in accordance with the instructions below, including the Connector
Pinout shown in Figure 3.1, Table 3.2 or Table 3.3, and Harness Assembly per Figure 3.2. Installers
should follow industry-accepted practices regarding aircraft wiring and applicable regulatory
requirements and guidance. The instructions for constructing the cable harness as listed within this
manual were also used to construct the harness during environmental and electrical testing.
Alterations may invalidate environmental qualification and/or performance results.
Refer to Section 2.2 and 2.3 for planning unit location and cable routing guidelines.

Manual Number 9019161 Revision C, August 18, 2023 11
3.3.1 WIRE GAUGE SELECTION
Wire gauge should be 22 AWG. Use of PTFE, ETFE, TFE, Teflon, or Tefzel insulated wire is
recommended for aircraft use per MIL-DTL-16878 or equivalent. Additionally, for data
signals associated with ARINC 429 inputs and outputs, all MIO signals, and RS-
232/422/485, shielded twisted pair wiring per M27500 or equivalent is recommended (and
required to meet the qualifications associated with the product certification.)
3.3.2 CONNECTOR PINOUT
The supplied connector and backshell is required for proper installation and operation of the
unit. The functions associated with the 26-pin high density D-subminiature connector are
identified in Figure 3.1 and Table 3.2 or Table 3.3 below.
Note that for the -1 Indicator version of the unit (non-pitot/static), six of the MIO pins have
different capabilities. These are referred to as “Frequency Inputs” and are identified as three
separate pairs on pins 23/15, 24/25, and 17/26. Also described below as MIO #7/8, #9/10,
and #11/12. The functions of these pins are detailed further in Section 4.
Figure 3.1 View from Rear of Mating Connector
Contact Tooling Reference
Tool Positronic P/N
Daniels P/N
Mil P/N
Hand Crimp 9507-0-0-0
AFM8
M22520/2-01
Positioner 9502-3-0-0
K
-
41
M22520/2-06
Insert/Removal
4811-2-0-0
91067
-
1
M81969/1-04
Table 3.1 Contact Tooling Reference

Manual Number 9019161 Revision C, August 18, 2023 12
Connector Pinout (-1, -2)
Pin
Description Pin Description
1 Power Return 14 ARINC In #1 B
2 ARINC Out A 15 Multi I/O #8
3 ARINC Out B 16 ARINC In #2 B
4 Dim Input 17 Multi I/O #11
5 ARINC In #1 A 18 Thermocouple +
6 ARINC In #2 A 19 Power In (+10-32VDC)
7 RS 232 In 20 Multi I/O #2
8 RS 232 Out 21 Multi I/O #4
9 Thermocouple - 22 Multi I/O #6
10 Signal Return 23 Multi I/O #7
11 Multi I/O #1 24 Multi I/O #9
12 Multi I/O #3 25 Multi I/O #10
13 Multi I/O #5 26 Multi I/O #12
Table 3.2 Unit Connector Pin Identification (-1, -2)
Connector Pinout (-3)
Pin
Description Pin Description
1 Power Return 14 ARINC In #1 B
2 ARINC Out A 15 Multi I/O #8
3 ARINC Out B 16 ARINC In #2 B
4 Dim Input 17 RS485#2 A
5 ARINC In #1 A 18 RS485#1 A
6 ARINC In #2 A 19 Power In (+10-32VDC)
7 RS 232 In 20 Multi I/O #2
8 RS 232 Out 21 Multi I/O #4
9 RS485#1 B 22 Multi I/O #6
10 Signal return 23 Multi I/O #7
11 Multi I/O #1 24 Multi I/O #9
12 Multi I/O #3 25 Multi I/O #10
13 Multi I/O #5 26 RS485#2 B
Table 3.3 Unit Connector Pin Identification (-3)

Manual Number 9019161 Revision C, August 18, 2023 13
3.3.3 CABLE HARNESS ASSEMBLY
To assemble the aircraft cable harness, refer to the following instructions and Figure 3.2:
1) Install a pin/socket as supplied in the Connector Kit using an appropriate crimping tool for
each wire in the aircraft cable harness. Be sure to make the harness long enough to remove
the unit from the panel without stressing the harness.
a. Crimp and insertion/removal tool references can be found in Table 3.1.
2) Wire shields should be exposed and peeled back from the pin/socket termination
approximately 2”.
3) Insert the pins of the cable harness into the rear of the 26-pin D-Sub connector (Item 1, as
applicable, per Table 3.2 or Table 3.3 and Figure 3.1 using an appropriate pin insertion tool
per Table 3.1 or similar.
4) Select one (recommended), two or three locations for routing the wire harness bundle into the
Backshell (Item 2) and slide the Blanking Plates (Item 3) into the unused entry points.
5) Install the Backshell Spring Clip (Item 4) into the thin slot of the Backshell as shown.
6) Place the Backshell Slide Lock (Item 5) over the D-Sub connector.
7) Install the D-Sub connector with Slide Lock and cable harness attached into the Backshell and
secure with (2) screws (Item 6). Verify that the Backshell Leaf Spring is between the Slide
Lock and Backshell. Move the Slide Lock back and forth to verify free movement.
8) Bundle the exposed shields and wrap them around the harness for the length of the cable
clamp.
9) Add a grounding wire or braid to the bundled shields which can be attached to nearby aircraft
chassis ground.
10) Route the aircraft wire harness (with exposed shield bundle and chassis ground wire) between
the two halves of the Cable Strain Relief Clamp (Item 7).
11) Connect the two halves of the Cable Strain Relief Clamp with (2) screws (Item 8).
12) Place the Cable Strain Relief Clamp in the Backshell as shown.
13) Secure the Backshell Cover (Item 9) onto the Backshell using (4) Screws (Item 10).
14) The completed assembly should look as shown. Verify that the Slide Lock operates freely and
that no wires are pinched, nicked, or otherwise damaged.
15) Verify that power and ground signals are installed properly before connecting power.

Manual Number 9019161 Revision C, August 18, 2023 14
Figure 3.2 Mating Cable Harness Assembly
Cable Harness Kit Parts
Item
Qty
Description
1 1 DSub, 26pin HD, with #22 contacts
2 1 Backshell
3 2 Backshell blanking plate
4 1 Spring Clip
5 1 Slide Lock
6 2 Screw, Pan-head Phillips
7 2 Cable Clamp
8 2 Screw, Flat-head Phillips, Long
9 1 Backshell Cover
10 4 Screw, Flat-head Phillips, Short
1
8
9
3
5
2
7
4
6
10
Shield
(s)
Grounding Wire

Manual Number 9019161 Revision C, August 18, 2023 15
PNEUMATIC PRESSURE CONNECTIONS
For the MD23 versions with pneumatic inputs, the connector kit supplied with the unit contains two
(2) pneumatic quick disconnect fittings. These fittings are specific to the connections on the rear of
the unit and are required for proper operation. The two fittings are marked with “S” and “P” on the
case. The “S” fitting, or Static, is for absolute pressure. The “P” fitting, or Pitot, is for positive
pressure and provides a differential pressure in relation to the Static input.
Aircraft tubing that connects to the unit must be ¼” OD with an approximate 0.17” ID. When
determining tubing length, be sure to include sufficient service length for insertion and removal
without stressing the tubing.
NOTE: It is helpful to identify/label each tube (pitot or static) so that it can be connected to the
correct port on the back of the unit during installation and so they do not get switched during
maintenance or reconnection in the future.
WARNING: Engage the Lock by pressing the metal tab on the quick disconnect before connecting
to the unit to avoid damaging the o-rings. The connectors will ‘snap’/lock into place once they are
fully engaged.
MOUNTING
The MD23 FLEX
is designed primarily to be rear mounted in an aircraft instrument panel. Refer to
Section 2.2 for Equipment Location information. To install the unit in the instrument panel, follow the
instructions below and refer to Figure 3.3 and Figure 3.4.
Some applications that utilize the IMU feature (such as an attitude indicator) may require specific
mounting orientation. See the individual User Guide associated with each CID for more details.
Notes:
If using flat-head screws, minimum panel thickness is 0.050 inches (1.3mm). Thinner
panels require a pan-head screw, or a spacer/washer between the unit and the rear surface
of the panel to properly secure the unit.
If using screws other than those provided, ensure that they do not protrude more than ½-
inch into the unit.
Remove burrs around the cutout and holes to allow the unit to mount flush with the panel.
Electrical bonding between the aircraft and the unit chassis is NOT required.
1. Once a location is selected, cut the panel per the dimensions in Figure 3.4.
Either through-holes for pan-head or cap screws, or countersink holes for flat-head
screws can be used. The installation kit includes flat-head screws.
2. Route the prepared cable harness and pneumatic tubing (if applicable) behind the panel
and to the panel cutout.
3. VERIFY THAT AIRCRAFT POWER IS TURNED OFF.
4. Connect the cable harness and pneumatic fittings (if applicable) to the rear of the unit.
5. Insert the unit into the panel cutout and secure with four (4) #6-32 screws (provided).

Manual Number 9019161 Revision C, August 18, 2023 16
INSTALLATION COMPLETION
After installation of cabling and before installation of the equipment, ensure that power is applied
only to the pins specified in the interconnect diagram.
Prior to operating the unit in the aircraft, verify the basic operation of the unit and conduct a
standard leak check of the pitot/static system per the aircraft maintenance manual or industry
practice. Verify the proper CID number is installed for the application.
Figure 3.3 MD23 Outline Drawing
all dimensions apply to all versions
-1,-3
VERSIONS
-2 VERSION

Manual Number 9019161 Revision C, August 18, 2023 17
Figure 3.4 Panel Cutout

Manual Number 9019161 Revision C, August 18, 2023 18
SECTION 4 OPERATION
IMPORTANT: READ THIS ENTIRE SECTION PRIOR TO OPERATING THE UNIT IN FLIGHT!
The MD23 FLEX
Custom Function Display is a unique new type of avionics equipment with a Patent
Pending software concept. It utilizes a highly capable and certified hardware and software platform
that can be customized to receive, output, and display a wide array of information. Because FLEX
can become almost anything, this section is designed to explain the functional capabilities, standard
operation, and configurable defaults. Operational details of specific custom applications are
provided separately as a User Guide that serves as a compliment to this manual.
GENERAL FUNCTION
4.1.1 CUSTOM INSTRUMENT DEFINITION (CID)
The Custom Instrument Definition, or CID, is a data file that describes the definition of the
inputs, outputs, and graphical display for a specific application. The CID utilizes the certified
functions of the MD23 and provides settings and variables to parameterize them to meet the
requirements as requested.
The CID is provided as a single file that can be loaded onto the MD23 through the USB
Type A data port on the rear of the unit. Each unique CID file is assigned an identification
number and revision – typically in the format of 1###X, where # is a three-digit number and
X is the revision, starting with “A”. The currently loaded CID version can be found on the
startup screen during Pre-Flight Mode and in the Options Menu on the Info screen during
Flight Mode.
Contact Mid-Continent Instruments and Avionics to inquire about the purchase and creation
of a CID file to meet your specific application requirements.
4.1.2 SYSTEM NAVIGATION
All standard MD23 units have the same basic system structure. The system navigation map
in the figure below demonstrates the basic functions and relationships between the various
modes and menus. The user interface on how to maneuver between modes and menus is
described in Section 4.2. The details associated with each mode and menu can be found
further in Section 4.3, 4.4, and 4.5. (Figure 4.1)
4.1.3 USB FUNCTION
The MD23 CFD includes a USB Type-A Programming Port connector on the rear of the unit
that is used for loading unit software and CID files. This feature makes it easy and
convenient to perform updates with any standard USB flash drive. The Programming Port is
only accessible when not in flight and shall only be used by authorized personnel in
accordance with the instructions found within this manual.

Manual Number 9019161 Revision C, August 18, 2023 19
Figure 4.1 System Navigation Map
USER INTERFACE
The MD23 FLEX
CFD is designed for simple, intuitive operation for ease of use for all custom
applications. The Control Knob and Menu Operation are standard for all MD23 installations.
4.2.1 CONTROL KNOB
The central Control Knob is located at the bottom-center of the unit bezel. This is the only
user interface on the unit.
The Control Knob has two functions: push and turn.
The knob provides 16-detents per revolution and typically increments whatever element it is
controlling on the display one unit per detent. It can also be used to scroll between
controllable elements, menu options, or pages.
The push function is typically used to select the highlighted option in a menu, on the display,
and/or to enter and exit menus and control functions. The push function can also perform
certain operations with a push-and-hold action as described herein.
Hold
Knob
Introduction
Screen
Hold
Knob Options Menu
User Options
Menu*
Normal
Operation
Config
Menu
User Config
Menu*
YES NO
FLIGHT MODE CONFIG MODE
PRE-FLIGHT MODE
Power On

Manual Number 9019161 Revision C, August 18, 2023 20
4.2.2 MENU OPERATION
The menu parts are defined below:
Menu title
white text on a blue background at the top of each menu
Current item cursor
highlighted by a white box and green
background
Selectable items any selectable item on the menu is indicated with white text
Unavailable items
information only / unavailable options are indicated with gray text
Menu operation throughout the MD23 is simple and intuitive:
Turning the Control Knob will scroll the cursor over the available options within each menu.
For items that can be changed without opening another page, the currently set value is
displayed in gray directly to the right of each setting. Pressing the Control Knob for one of
these items will make its options available to the right. Scroll to the desired option and press
the Control Knob to select it. The green highlight will return to the menu options on the left
and the new value will be displayed in gray to the right.
After confirming any setting by selecting it, that setting will become immediately active and
be saved in memory, regardless of whether the EXIT command is selected or it times out
and automatically reverts to the active display.
PRE-FLIGHT MODE
In Pre-flight Mode, power is applied to the unit and the introduction screen appears during startup.
The startup screen will display the manufacturer’s logo, model name and number, unit software
version and CID version. It may also include additional graphics (such as a logo) or other
information specific to the custom application.
During Pre-flight Mode, the introduction screen will be displayed while the unit conducts an initial
power-up built-in test (PBIT) of the system to validate operational readiness. This includes, among
others, an internal test to verify software and memory, and a check that the loaded CID file is valid.
Inputs and outputs are not enabled during Pre-flight Mode.
The introduction screen will be displayed for approximately five (5) seconds and will transition to
Flight Mode when complete. (Figure 4.2)
Figure 4.2 Pre-Flight Mode
manufacturer’s logo
model number/name
software version CID version
customer info
(optional)
This manual suits for next models
1
Table of contents
Other Midcontinent Monitor manuals
Popular Monitor manuals by other brands
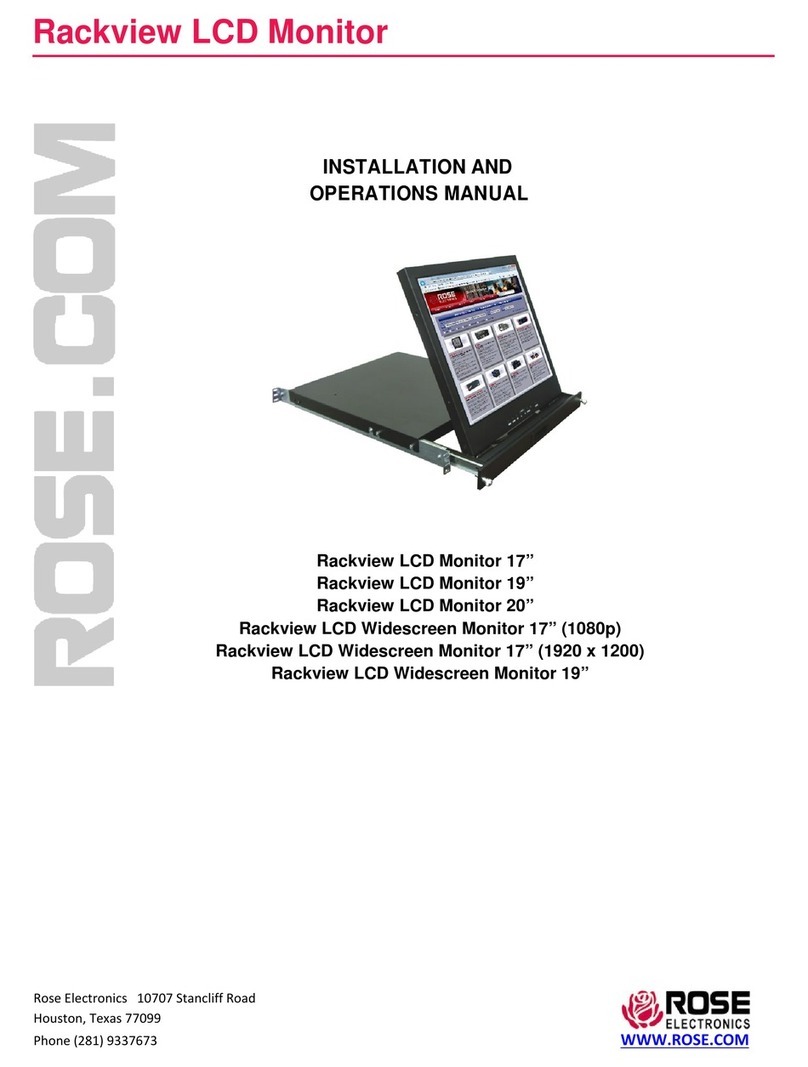
Rose electronics
Rose electronics Rackview LCD Panel Mount 19" Installation and operation manual

NEC
NEC P42XC10 - PlasmaSync - 42" Plasma Panel Specifications
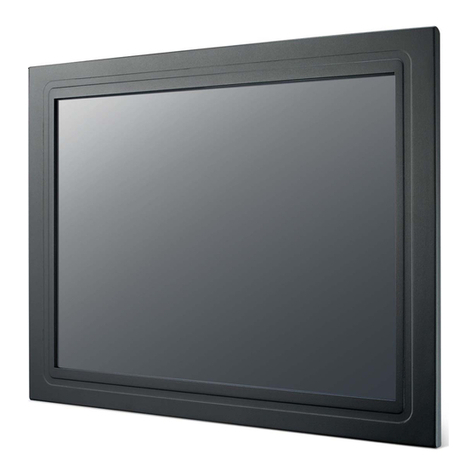
Advantech
Advantech IDS-3212 Series user manual
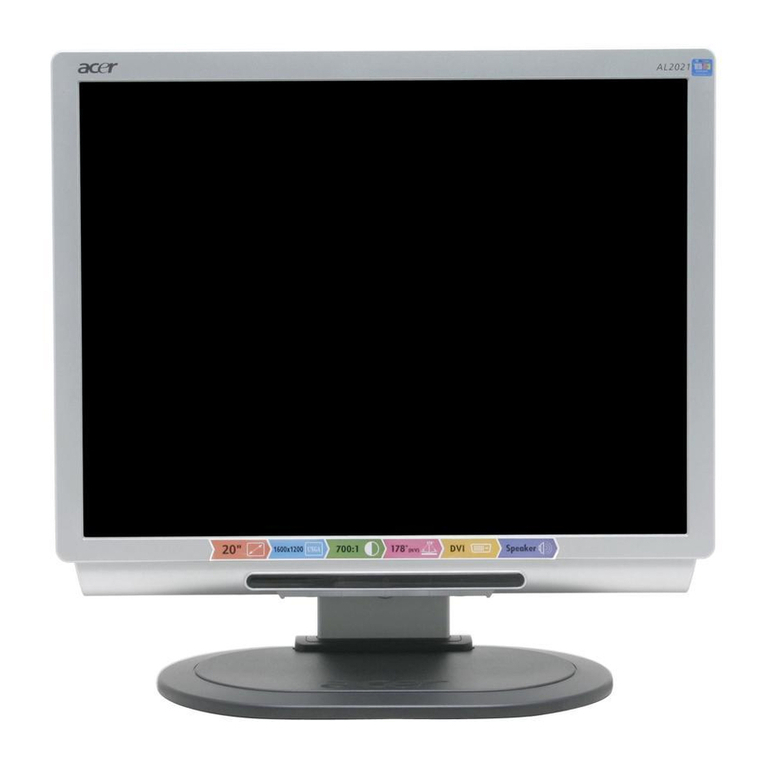
Acer
Acer AL2021 user manual

Dahua
Dahua Digital VTH Series quick start guide

X4-TECH
X4-TECH zelo M8 instruction manual