Mini Motor AM-AC Series User manual

Use and Maintenance Manual Rev5 – of 24/03/2020 0
TABLE OF CONTENTS
1. General Safety Information ...................................................... 1
1.1 Product Identification ....................................................... 2
1.2 Movement/Handling and Storage .................................... 2
1.3 Identification and notes on cURus and cCSAus products . 3
2 Preliminary operations ............................................................. 3
2.1 Pre-Installation Product Inspection .................................. 3
2.2 Electrical Connection ........................................................ 3
2.3 Instructions for Alternating Current Products .................. 4
2.4 Instructions for Permanent Magnet Direct Current
Products ........................................................................................ 5
2.5 Intended Uses and Limitations ......................................... 5
2.6 General Warranty Conditions ........................................... 6
3 Installation and Periodic Inspections ........................................ 6
3.1 Brake Inspection and Regulation ...................................... 6
4 Troubleshooting ........................................................................ 7
Use and Maintenance
Manual
For motors and gear motors of the following
series: AM-AC ACC PA PAC BC2000 BC2000-
24MP MC MCC PC PCC XC BS MCBS ACF PAF
MCF PCF XCF MCFBS AMSS PCFSS XCFSS
SXCFSS AMSSE

Use and Maintenance Manual for Product Series (*) rev 5 of 24/03/2020
1
(*) AM-AC ACC PA PAC BC2000 BC2000-24MP MC MCC PC PCC XC BS MCBS ACF PAF MCF PCF XCF MCFBS AMSS PCFSS XCFSS SXCFSS AMSSE
1. GENERAL SAFETY INFORMATION
This manual has been written by the manufacturer to provide authorised personnel
with all information required to safely perform the transport, movement and
handling, installation, testing and inspection, and repair of Mini Motor products.
This manual applies to the following product series: AM-AC ACC PA PAC BC2000
BC2000-24MP MC MCC PC PCC XC BS MCBS ACF PAF MCF PCF XCF MCFBS AMSS
PCFSS XCFSS SXCFSS AMSSE (see Mini Motor technical catalogue). This manual also
applies to the version with planetary gear stage (suffix “E” to product series code,
e.g. ACE).
The motors in question are electrical machinery, and as such should be considered
hazardous as they contain live parts and others which rotate.
Movement/handling, commissioning, use and any repairs required must be
performed by QUALIFIED PERSONNEL, and only after complying with the following
instructions:
The qualified personnel must be familiar with the procedures for the
installation, maintenance and use of the motor, and must have read this
use and maintenance manual.
The qualified personnel must know all technical data, specifications and
electrical connections for the motor to install.
In order to minimise actions which could lead to damage to the product and injury
to the operator and/or bystanders, the following instructions must be followed:
Check that the system is not live before making the electrical connection
to the motor.
Check that the electrical cables have not been damaged during
installation, that they are dressed properly away from moving parts, and
that they are not subject to mechanical stresses.
Close the cover of the terminal box before applying power to the motor.
The surfaces of the motor could reach or exceed a temperature of 100°C, therefore
do not position parts near the motor which could degrade or catch fire at these
temperatures.
Warning: Make the earth connection to the motor before any
application
Do not approach rotating parts with any part of the body.
Use appropriate personal protective equipment (PPE) when working in
the vicinity of the end of the shaft (presence of sharp edges in the key
seat).
Before testing the machine, provide for adequate protection around
rotating parts (joints etc.).
Check the tightness of the screws of the electrical terminals before
proceeding to test the motor.
The use of standard servomotors, gear units and gear motors is not allowed in the
following:
saline environments and those with high humidity levels;
corrosive environments with explosion risk (ATEX);
liquid or totally immersed environments, with the exception of the “SS”
series.

Use and Maintenance Manual for Product Series (*) rev 5 of 24/03/2020
2
(*) AM-AC ACC PA PAC BC2000 BC2000-24MP MC MCC PC PCC XC BS MCBS ACF PAF MCF PCF XCF MCFBS AMSS PCFSS XCFSS SXCFSS AMSSE
1.1 PRODUCT IDENTIFICATION
The product is fitted with a nameplate to allow rapid identification and to
comply with applicable regulations.
An example nameplate for single-phase, three-phase and direct current
motors/gear motors is given below.
For further details, see the technical catalogue which can be downloaded
from the website www.minimotor.com .
Figure 1 - Nameplate nomenclature for single-phase, three-phase and direct current
motors/gear motors
Figure 2 - Nameplate nomenclature for brushless motors/gear motors
Figure 3 - Nameplate nomenclature for “SS” series motors/gear motors
Every Mini Motor product has a unique serial number stamped on its
nameplate and inside the gearbox housing terminal compartment. Check
that the two serial numbers match.
1.2 MOVEMENT/HANDLING AND STORAGE
All products are packaged to prevent damage during shipping and handling.
It is nevertheless the user’s responsibility to check the integrity of the
product before installation.
Below are some precautions to follow for correct storage:
Store the product in an environment with temperatures of
between 0°C and +40°C, which should be covered, dry, clean and
free from vibrations.
Keep the product off the ground.
Place the product on a flat, stable surface.
For storage periods exceeding four months, protect the outer
machined parts in steel and the output shaft with rust preventive
oil or grease, and periodically check the condition (with the
exception of products equipped with optional stainless-steel
output shafts).
Perform a few turns of the slow shaft every four to five months.

Use and Maintenance Manual for Product Series (*) rev 5 of 24/03/2020
3
(*) AM-AC ACC PA PAC BC2000 BC2000-24MP MC MCC PC PCC XC BS MCBS ACF PAF MCF PCF XCF MCFBS AMSS PCFSS XCFSS SXCFSS AMSSE
1.3 IDENTIFICATION AND NOTES ON CURUS AND CCSAUS
PRODUCTS
- cURus UL recognized products for the US
and Canada can be identified from the
product mark directly on the product nameplate. All
information relating to acceptability conditions for the end
user can be viewed at the following link. The Product IQ site
requires user registration.
https://iq.ulprospector.com/info/
Searching for “MINI MOTOR” or the individual product
purchased will give access to the above information.
- cCSAus approved products are equivalent to the previous
ones, but approved by the CSA approval body. They are
identified by the cCSAus logo directly on the product
nameplate.
Information for the end user can be found at the
following address:
https://www.csagroup.org/testing-certification/product-
listing/
2 PRELIMINARY OPERATIONS
2.1 PRE-INSTALLATION PRODUCT INSPECTION
The following checks must be performed before installing the
product:
Check that the product corresponds to the purchase order.
Check product integrity after opening the packaging.
Check the data given on the nameplate.
Check that the supply voltage complies with that specified on the
nameplate.
Check that there are no lubricant leaks.
Check the tolerance of the couplings to the drive components.
Apply tolerances on the order of g7 / f7.
For products of construction type B3, check the flatness of the
mounting surface.
For products of construction type B5/B14, check that the mating
tolerance is F7.
Earthing of the product to the machine.
For worm screw gear motors, it is possible during running in that
the nameplate rpm and torque data will be below the nominal
values given.
There may be a film of dewatering fluid on the
products, which is required to protect the external
parts from corrosion.
2.2 ELECTRICAL CONNECTION

Use and Maintenance Manual for Product Series (*) rev 5 of 24/03/2020
4
(*) AM-AC ACC PA PAC BC2000 BC2000-24MP MC MCC PC PCC XC BS MCBS ACF PAF MCF PCF XCF MCFBS AMSS PCFSS XCFSS SXCFSS AMSSE
Always earth the motor before connecting it to the power
supply. The marked terminal is located inside the terminal box
(use a cable of sufficient cross-sectional area).
In the case of single-phase, three-phase and direct current
motors/gear motors, the diagram is located under the terminal
compartment cover.
To connect the product to the supply, the four retaining screws must be
removed and the cover removed as shown in the figure.
Figure 4 - Example of Connection Diagram
The type of terminals used allows ferrules and other types of wire terminals
to be avoided, as they ensure excellent electrical contact even in the
presence of strong vibration or high temperatures, while fully complying
with applicable regulations. Connection only requires 8 mm to be stripped
from the end of the cables, as specified on the yellow plate shown in Figure
4.
The cable gland used (M16x1.5 with strain relief) allows a cable of between
4 mm and 10 mm diameter to be used.
Make a preliminary check of the type of diagram to use.
Precisely follow the instructions given on the diagram; modifying the
connection diagram could compromise correct product operation.
In the case of products with thermal protection, this must always be
connected to ensure correct product operation.
In the event that the nameplate with the wiring diagram is lost, wiring
diagrams can be downloaded from www.minimotor.com .
In the case of special connection diagrams, contact Mini Motor directly.
For brushless servomotors, follow the diagrams available at
www.minimotor.com when connecting the motors; the following cables
must be used:
For the signals: the connecting cable must be of screened shielded
twisted-pair type.
For the power: the connecting cable must have outer shielding.
Use separate conduit for the power cables and signal cables.
Contact Mini Motor directly for the wiring and connection diagrams.
2.3 INSTRUCTIONS FOR ALTERNATING CURRENT PRODUCTS
If the motor is controlled via electromechanical contactors, it is
essential to use a protection system against the voltage surges
generated when the contacts of the individual contactors open.
Solution 1: RC Filter: Provides excellent protection against voltage
surges, drastically reducing electromagnetic emissions. The sizing
is independent of the supply voltage. This solution CANNOT be
used if the motor is driven by frequency converters (INVERTER).
Solution 2: Varistors: Provide good protection from voltage surges, and can
also be used on inverter-driven products. The varistors must have a rated
voltage of between 1.3 and 1.5 times the value of the supply voltage, and
a dissipation energy of at least 50J.
For example: Supply voltage 400 Vac; minimum rated voltage of the
varistor: 1.3 x 400 = 520 Vac; maximum rated voltage of the varistor: 1.5
x 400 = 600 Vac.

Use and Maintenance Manual for Product Series (*) rev 5 of 24/03/2020
5
(*) AM-AC ACC PA PAC BC2000 BC2000-24MP MC MCC PC PCC XC BS MCBS ACF PAF MCF PCF XCF MCFBS AMSS PCFSS XCFSS SXCFSS AMSSE
Both solutions must be connected in parallel to the motor phases downline
of the contactor (between the contactor and the motor).
These measures will ensure correct product operation. Mini Motor shall
not be held liable for malfunctions or burned out windings in the event
that these measures are not applied.
2.4 INSTRUCTIONS FOR PERMANENT MAGNET DIRECT
CURRENT PRODUCTS
It is essential that the peak inrush current draw is no more than three
times the rated current value.
Exceeding this value could cause demagnetisation of the stator and/or
damage to the product.
Brushed gear motors are not designed for continuous use, as the
continuous contact of the brushes would reduce the product lifespan.
During normal product operation, it is necessary to limit the maximum
power draw through calibration of the power supply equipment.
It is absolutely prohibited to supply the motors directly from batteries
without the use of suitable current limitation systems (e.g.: AC/DC or
DC/DC drives).
2.5 INTENDED USES AND LIMITATIONS
Each product has a potentially different use: ensure that the purchased
product can be used in the intended environment. As a general rule, unless
otherwise specified on the product itself, Mini Motor products must be:
Handled, installed, used and maintained in accordance with
this manual.
Handled, installed, used and maintained by qualified and
authorised staff.
Used within a temperature range of 0°C to +40°C.
Installed with adequate ventilation provided for.
For construction type B3 (with feet), ensure that the
mounting surface is flat.
For construction type B5 (with flange), fastening must be
performed with F7 mating tolerance.
Use the threaded holes on the end of the shafts for assembly;
avoid use of a hammer, as repeated impacts could
irreparably damage the bearings.
For THREE-PHASE motors/gear motors, whenever there is the possibility
of the output shaft jamming and/or persistent overload conditions, it is
advisable to use magneto-thermal protection (MCBs).
Single-phase motors/gear motors contain a thermal cut-out device inside
the winding which protects the motor by automatically cutting the power
supply when the winding temperature reaches 130°C ± 5%.
DC powered motors/gear motors require the use of dedicated current
limitation systems, and where necessary a thermal pellet fastened to the
radiator which will cut the power supply whenever there is a possibility
of the output shaft jamming.
Brushless servomotors have a PTC temperature sensor inside the motor
which is responsible for reporting motor overheating to the converter
control circuits. The PTC sensor is connected to the converter via the
resolver cable.
Ensure that the resolver cable has been correctly connected and the
converter setting has been performed correctly.
Mini Motor shall not be held liable for burned out windings, premature
wear of bearings and deterioration of lubricant oil due to the causes
outlined above. Premature wear of seal rings is not covered by warranty,
as they are exposed to weather and unknown environmental conditions.

Use and Maintenance Manual for Product Series (*) rev 5 of 24/03/2020
6
(*) AM-AC ACC PA PAC BC2000 BC2000-24MP MC MCC PC PCC XC BS MCBS ACF PAF MCF PCF XCF MCFBS AMSS PCFSS XCFSS SXCFSS AMSSE
2.6 GENERAL WARRANTY CONDITIONS
Mini Motor's warranty covers only manufacturing defects and is valid for
one year from product shipment, unless agreed otherwise. Mini Motor will
replace or repair defective parts under this warranty, but bears no liability
for direct or indirect damages of any nature. The warranty shall lapse in the
event that the provisions listed in the use and maintenance manual have
not been followed, and/or repairs or modifications have been made
without the company’s written authorisation.
3 INSTALLATION AND PERIODIC INSPECTIONS
Before placing the motor into service, check that the torque output
is lower than that specified on the nameplate.
The activities to be performed before installation are listed below,
along with the periodic inspection intervals:
Activity
Check for any lubricant leaks. Before installation
Check the coupling tolerances for matching of the product to the mating
component.
Check the individual model ordered in the Minimotor catalogue
(www.minimotor.com).
Before installation
For products of construction type B3, check the flatness of the
mounting surface. Before installation
For products of construction type B5/B14, check that the mating
tolerance is F7. Before installation
Periodic Inspections
(2000 hour intervals, and in any case at least once a year)
Check for any lubricant leaks
Clean fan cover
Check brake
Check the brushes and replace if necessary (for permanent magnet DC products)
3.1 BRAKE INSPECTION AND REGULATION
Permanent magnet brakes are single-disc devices in which the force of the
permanent magnet is used to produce a braking torque (safety system with
mechanical locking of the rotor with no current present).
To remove the braking force, the permanent magnetic field is cancelled out
by an opposing electromagnetic field.
Ensure that the motor, gear motor or servomotor is free (not
braked) before power is applied.
For self-braking motors/gear motors (products with the letters KA or KB
in the product code), whenever the braking action should be reduced due
to wear, the gap must be restored as follows:
1) Power the brake (causing it to release);
2) Slacken off the fan retaining screws on the motor shaft;
3) Move the fan away from the brake, without removing it, using a
suitable extractor;
4) Obtain a 0.20 mm spacer;
5) Position the spacer between the surface of the brake and the fan;
6) Move the fan up to the brake surface so that it takes on the spacer
measurement;
7) Tighten the fan retaining screws to a torque of 1.0 Nm using a
torque driver, and pull out the spacer.
Brushless servomotors (BSK and BSEK series) do not require maintenance
of the brake. Contact Mini Motor directly with any problems.

Use and Maintenance Manual for Product Series (*) rev 5 of 24/03/2020
7
(*) AM-AC ACC PA PAC BC2000 BC2000-24MP MC MCC PC PCC XC BS MCBS ACF PAF MCF PCF XCF MCFBS AMSS PCFSS XCFSS SXCFSS AMSSE
4 TROUBLESHOOTING
A series of potential issues are listed below. Follow the advice given before
taking any action.
Fault Possible Cause Solution
Leaking
lubricant
Excessive vibration of gear motor Check installation
Worn seal rings Contact Mini Motor
High
temperature
Electrical connection not made correctly Check connection
Contact Mini Motor
Insufficient ventilation Remove any foreign bodies
Load applied to product greater than nominal
nameplate value
Check applied load
Contact Mini Motor
Faulty capacitor
(single-phase motors/gear motors only)
Replace capacitor
Contact Mini
Motor
Excessive noise
Incorrect brake gap
(only KA and KB braked versions)
Restore gap
(Sec. 3.1)
Contact Mini Motor
Worn bearings Contact Mini Motor
Worn shaft/worm screw coupling
(VSF gear motors only) Contact Mini Motor
Foreign bodies in ventilation zone Check fan and fan cover condition
Product does
not operate
Incorrect electrical connection Check connection
Contact Mini Motor
Jam Check value of load and method of
application
Open circuit/fault on capacitor Replace capacitor
Contact Mini Motor
This manual suits for next models
23
Table of contents
Other Mini Motor Engine manuals
Popular Engine manuals by other brands

rollease acmeda
rollease acmeda AUTOMATE MT01-2101-069002 Operation guide
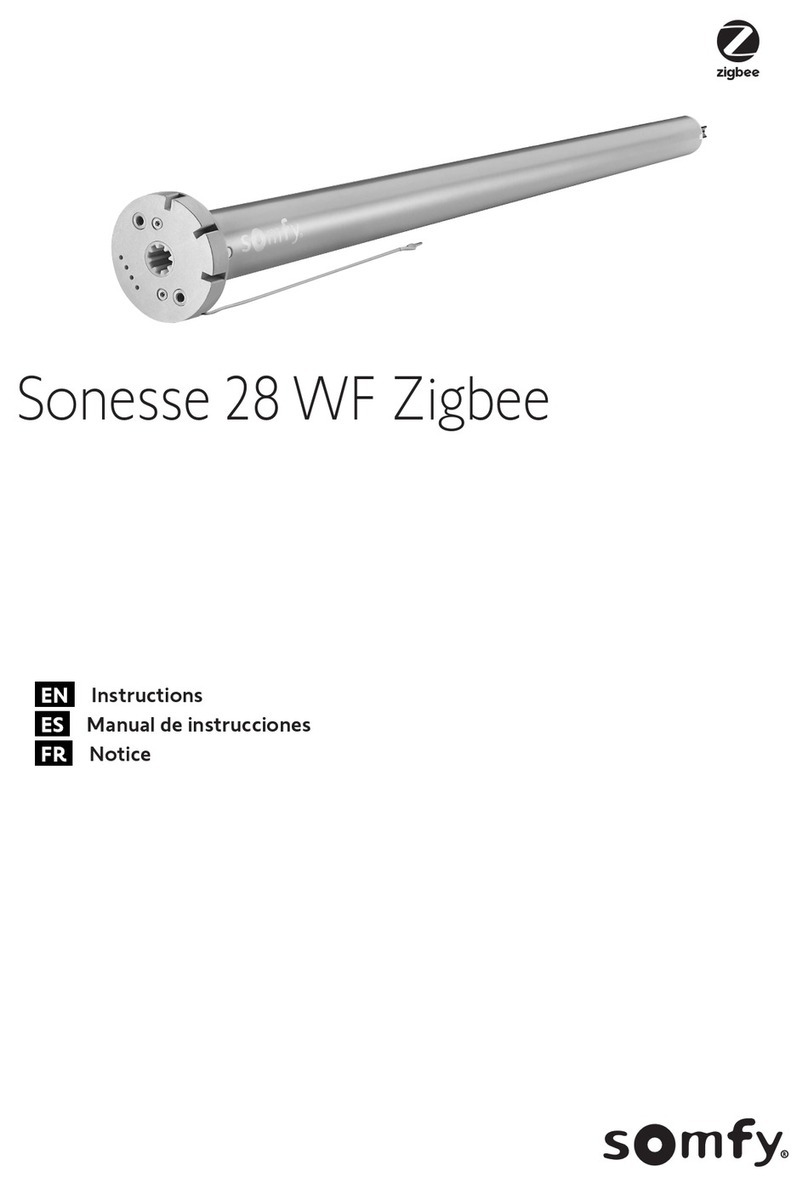
SOMFY
SOMFY Sonesse 28 WF Zigbee instructions
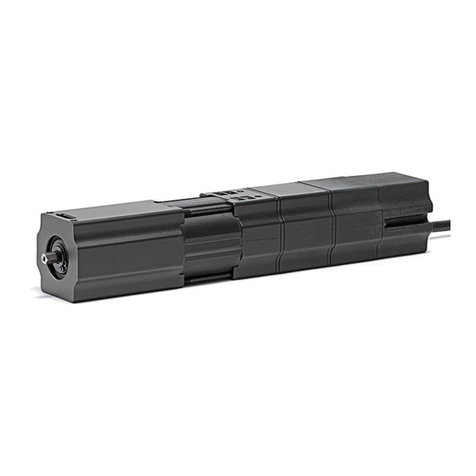
elero
elero JAR quick start guide

Briggs & Stratton
Briggs & Stratton 120000 Operator's manual
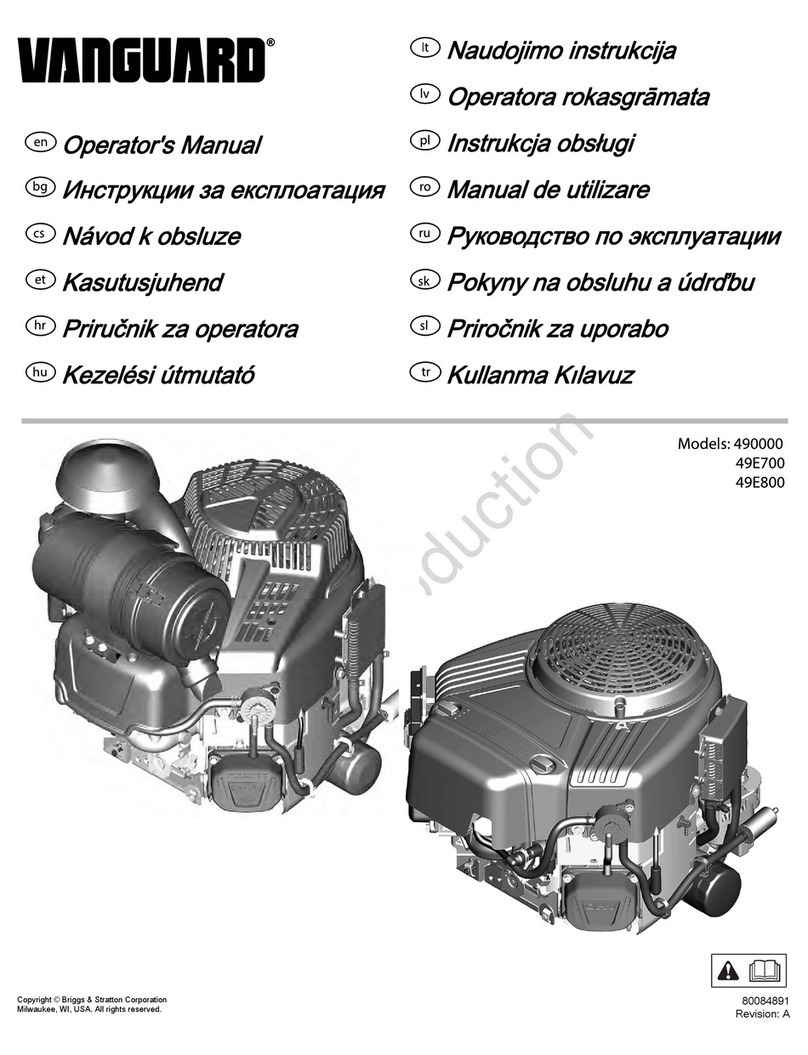
Briggs & Stratton
Briggs & Stratton Vanguard 490000 Operator's manual

EuroLite
EuroLite MD-2010 user manual