MiniMax FORMULA T1 User manual

FORMULAT1
TOUPIE
SPINDLE MOULDER
TOUPIE
TISCHFRÄSE
TOUPI
USO E MANUTENZIONE
OPERATION AND MAINTENANCE
FONCTIONNEMENT ET ENTRETIEN
BETRIEBS- UND WARTUNGSANLEITUNG
USOY MANTENIMIENTO
❑❑❑
ENGLISH
0000502377G/2

GENERAL
T1 1.1
1
MINI MAX is not responsible for damages caused by the wrong use and not correct maintenance of
the machine as well as by not permitted modifications.
For any technical problem concerning the machine apply to the dealer:
Pagine totali compresa copertina e retro: vedi paragrafi Diviso libretto CE e
NON CE, Profilatrice e
Tenonatrice
B9421 2
CF3 C.I. LIBRETTO USO E MANUTENZIONE
T1
INGLESE
NON CE
07/02/97
Unificato libretto per
macchine CEe e non
CE
B9390 1
N° Bolla B9357 22/11/95
Data 19/07/95
Modifica N° Bolla
Firma
SIT/RB/03 N° 0000502377G/2 Data

GENERAL
1.2 T1 BF-NGB1
SYMBOLS USEDSYMBOLS USED
SYMBOLS USEDSYMBOLS USED
SYMBOLS USED
Machines not in accordance with 89/392/CEE directive
Machines in accordance with CANADIAN AND USA prescriptions
Basic machine version
OPTIONAL: ..................... devices indicated in price list available only upon request
( for ...) optional device for .....
NOTE:
This handbook includes all machines T1 model therefore you have to consider the notes as well as
symbols which identify the versions.
All parts not identified by notes and/or symbols are valid for each version.

GENERAL
T1 1.3
1
GENERALGENERAL
GENERALGENERAL
GENERAL ..............................................................................................................................................................................................................
..............................................................................................................................................................................................................
....................................................................................................... SECTION 1SECTION 1
SECTION 1SECTION 1
SECTION 1
Page
1-1 Mail contact ................................................................................................................................. 1.5
1-2 Notes for the user ....................................................................................................................... 1.5
1-3 Machine identification ............................................................................................................... 1.6
1-4 Conditions foreseen for the use and prohibitions ................................................................. 1.6
1-4A Operator’s training .......................................................................................................... 1.8
1-5 Specifications............................................................................................................................... 1.9
1-6 Noise level ................................................................................................................................. 1.10
1-7 Safety rules ................................................................................................................................ 1.11
1-8 Optionals.................................................................................................................................... 1.13
1-9 Overall dimensions .................................................................................................................. 1.14
1-10 Safe working procedure .......................................................................................................... 1.16
INSTINST
INSTINST
INSTALLAALLA
ALLAALLA
ALLATIONTION
TIONTION
TION ........................................................................................................................................................................................
........................................................................................................................................................................................
............................................................................................ SECTION 2SECTION 2
SECTION 2SECTION 2
SECTION 2
Page
2-1 Unloading the machine ............................................................................................................. 2.2
2-2 Fitting the demounted parts ..................................................................................................... 2.4
2-2.1 Fitting the additional tables............................................................................................ 2.4
2-3 Electric connection ..................................................................................................................... 2.6
2-4 Connection to the suction system ............................................................................................ 2.8
2-5 Safety devices.............................................................................................................................. 2.9
MACHINE SETTING AND USEMACHINE SETTING AND USE
MACHINE SETTING AND USEMACHINE SETTING AND USE
MACHINE SETTING AND USE................................................................................................................................
................................................................................................................................
................................................................ SECTION 3SECTION 3
SECTION 3SECTION 3
SECTION 3
Page
3-1 Control board .............................................................................................................................. 3.2
3-2 Machine start............................................................................................................................... 3.6

GENERAL
1.4 T1 BF-NGB1
MOULDER FUNCTIONMOULDER FUNCTION
MOULDER FUNCTIONMOULDER FUNCTION
MOULDER FUNCTION..............................................................................................................................................................
..............................................................................................................................................................
............................................................................... SECTION 7SECTION 7
SECTION 7SECTION 7
SECTION 7
Page
7-1 Interchangeable spindle ............................................................................................................ 7.2
7-2 Fitting the tool............................................................................................................................. 7.2
7-3 Vertical adjustment of the spindle........................................................................................... 7.4
7-4 Spindle speed selection ............................................................................................................. 7.6
7-5 Spindle speed change and belt stretching .............................................................................. 7.8
7-6 Belt replacement ......................................................................................................................... 7.8
7-7 Fitting the adjustable hood-fence unit .................................................................................. 7.10
7-8 Fence adjusting for profiling with aligned fence halves .................................................... 7.12
7-9 Fence adjusting for milling with not aligned fence halves ................................................ 7.14
7-10 Vertical pressers........................................................................................................................ 7.20
MAINTENANCEMAINTENANCE
MAINTENANCEMAINTENANCE
MAINTENANCE ..................................................................................................................................................................................
..................................................................................................................................................................................
......................................................................................... SECTION 20SECTION 20
SECTION 20SECTION 20
SECTION 20
Page
20-1 Periodical machine cleaning ................................................................................................... 20.2
20-2 Periodical lubrication............................................................................................................... 20.2
20-3 Checking the safety devices.................................................................................................... 20.2
20-4 Machine removal - storage - demolition............................................................................... 20.3
20-5 Emergency conditions ............................................................................................................. 20.4
20-6 Troubles - Causes - What to do .............................................................................................. 20.3

GENERAL
T1 1.5
1
1-11-1
1-11-1
1-1 MAILMAIL
MAILMAIL
MAIL CONTCONT
CONTCONT
CONTACTACT
ACTACT
ACT
Writing or telephoning to the dealer or to MINIMAX for any reason concerning your machine,
always specify the following information:
1) Machine model
2) Serial number
3) Voltage and frequency
4) Purchase date
5) Name of the dealer where the machine was bought
6) Detailed informatin about the trouble
7) Detailed information about the working to be carried out
8) Period of use - number of working hours
SCM
Divisione Minimax Samco
Via Casale, 450
47827 - VILLA VERUCCHIO - ITALIA
Tel.0541-677208-679580-679578 - Fax.0541-678781
1-21-2
1-21-2
1-2 NOTES FOR THE USERNOTES FOR THE USER
NOTES FOR THE USERNOTES FOR THE USER
NOTES FOR THE USER
The handbook desribes all operations required for the normal maintenance of the machine.
Do not carry out any operations not described in the handbook.
Alloperationswhich require the demounting of machine as well as maintenance operations shall be
carried out only by authorized technicians.
Keep the safety regulations as well the general industrial medicine prescriptions.
NOTES:NOTES:
NOTES:NOTES:
NOTES:
- Use only original MINIMAX spare parts. The machine manufacturer is not responsible for
damages caused by the use of not original parts.
- For imformation concerning the electric system always specify the data indicated on the plate
(fig.1.1) arranged in the inside of the door for access to the electric housing.
FORNIT. Company that carried out the electric system
DATA Date of power unit manufacturing
CODICE DISTINTA Number of electric components bill
N. Wiring diagram number
VOLT RETE Mains voltage for machine supply (V)
VOLT AUX Voltage for auxiliary circuits supply (V)
VOLT FRENO Voltage for motor brake supply (V)
Hz Frequency (Hz)
kW Absorbed power
MACCH. Machine type1.1

GENERAL
1.6 T1 BF-NGB1
1-31-3
1-31-3
1-3 MACHINE IDENTIFICAMACHINE IDENTIFICA
MACHINE IDENTIFICAMACHINE IDENTIFICA
MACHINE IDENTIFICATIONTION
TIONTION
TION
Machine data are punched on the metallic plate applied to the side of the machine frame.
Mod. Machine model
N. Serial number
Ref. Internal reference
Volt Voltage (V)
- Phase number
Hz Frequency (Hz)
kW Installed power
kg Gross weight
A Electric input (Ampere)
1-41-4
1-41-4
1-4 CONDITIONS FORESEEN FOR THE USE AND PROHIBITIONSCONDITIONS FORESEEN FOR THE USE AND PROHIBITIONS
CONDITIONS FORESEEN FOR THE USE AND PROHIBITIONSCONDITIONS FORESEEN FOR THE USE AND PROHIBITIONS
CONDITIONS FORESEEN FOR THE USE AND PROHIBITIONS
Working permitted: profiling, not-through profiling, shaping.
Material which may be processed:solid wood, plywood, chipboards, fiber panels; the panels may
be coated with laminate or finishing material and eventually strips are glued to their edges.
DIMENSION OF WORKPIECE TO BE MILLEDDIMENSION OF WORKPIECE TO BE MILLED
DIMENSION OF WORKPIECE TO BE MILLEDDIMENSION OF WORKPIECE TO BE MILLED
DIMENSION OF WORKPIECE TO BE MILLED
Min. piece size for profiling operation:
Thickness 8mm - Width 8 mm - Length 220 mm
Max. size of solid wood piece for profiling operation:
Thickness 250 mm - Width 250 mm - Length 1000 mm
in case of longer pieces use rest tables
TOOLS WHICH MAY BE USEDTOOLS WHICH MAY BE USED
TOOLS WHICH MAY BE USEDTOOLS WHICH MAY BE USED
TOOLS WHICH MAY BE USED
The machine has been designed to use only tools in accordance with prEN 847-1 norm, suitable for
the material and for manual feed.
Bymanualfeedwemeannotonlytheguideofthepiecebyhandbutalsobyaslidingtableorafeeder.
Features of tools for manual feed:
- max. chip thickness 1,1 mm
- tool shape round
- chip exhaust space narrow
The relation between tool and rotation speed is explained in cap. 7-4.

GENERAL
T1 1.7
1
ENVIRONMENTENVIRONMENT
ENVIRONMENTENVIRONMENT
ENVIRONMENT
The machine can work under these conditions:
- Max. humidity: 90%
- Temperature : min. + 1°C - max. + 40°C.
- max.altitudeoversealevel:1000m(incaseofhigheraltitudeapplytothemachinemanufacturer).
Always connect the machine to the suction system see par. 2-4.
The machine may not be used in the open air.
The machine may not run in explosive rooms.
PROHIBITIONSPROHIBITIONS
PROHIBITIONSPROHIBITIONS
PROHIBITIONS
- a different use of the machine is not permitted.
- the machine may not work without the proper guards foreseen
for that working; never remove parts of the guards!.
- never machine pieces of material and dimensions different from the ones mentioned above.
- Tools not in accordance with prEN 847-1 prescription or tools of dimensions not proper for the
spindle diameter may not be used: see cap. 7-4.
The user is responsible for the damages caused by the wrong use of the machine.
RESIDUAL RISKSRESIDUAL RISKS
RESIDUAL RISKSRESIDUAL RISKS
RESIDUAL RISKS
Evenifyoukeepallsafety rules and use the machineintheproperway,thefollowing risks may rise:
- Contact with the tool
- Contact with the spindle in rotation
- Contact with the rotating parts (belts, pulleys)
- Danger due to the dust in case of working without suction.

GENERAL
1.8 T1 BF-NGB1
1-4A1-4A
1-4A1-4A
1-4A OPERAOPERA
OPERAOPERA
OPERATOR’S TRAININGTOR’S TRAINING
TOR’S TRAININGTOR’S TRAINING
TOR’S TRAINING
The machine operator is to be trained for the use, adjustment and operation of the machine.
In particular the training shall include:
a) the priciples for the right use and operation of the machine and fence adjustment.
b) the correct use of the pieces during the working.
The operator is to be informed about the dangers due to the machine operation and about the
precautionstobetaken;besidestheoperatorshallbeabletocarryoutperiodicaltestsonguardsand
safety devices.

GENERAL
T1 1.9
1
1-51-5
1-51-5
1-5 SPECIFICASPECIFICA
SPECIFICASPECIFICA
SPECIFICATIONSTIONS
TIONSTIONS
TIONS
Worktable size....................................................................................................................... 1200x730 mm
Worktable height from the floor .................................................................................................. 915 mm
Working spindle height................................................................................................................. 180 mm
Max. tool diameter:
- profiling operation................................................................................................................... 250 mm
Vertical spindle adjusting ............................................................................................................. 260 mm
Vertical spindle adjusting ............................................................................................................. 140 mm
Spindle speed .......................................................................................3000-4500-6000-7000-10000 Upm
Max. size of the tool disappearing under the table ............................................................. 320x90 mm
Suction hoods diameter ................................................................................................................. 120 mm
Number of rings on the table.................................................................................................................... 5
Internal diameter of rings on the table..............................................................72 - 117 - 152 - 260 mm
Main motor power............................................................................................................................. 5,5kW
Standard machine weight ................................................................................................................475 kg
Working voltage and frequency.................................................... see plate of machine identification
STANDARD ACCESSORIESSTANDARD ACCESSORIES
STANDARD ACCESSORIESSTANDARD ACCESSORIES
STANDARD ACCESSORIES
Mechanic spindle locking for tool change
* Fence with wood fence halves, micrometric adjustment,
suction hood with 120 mm diameter
Set of distance rings for moulding spindle
Set of wrenches
* Accessory supplied to be used according to the working.

GENERAL
1.10 T1 BF-NGB1
1-61-6
1-61-6
1-6 NOISE LEVELNOISE LEVEL
NOISE LEVELNOISE LEVEL
NOISE LEVEL
MOULDER Type: T1
Operating conditions: Profiling
Reference norm: ISO 3744 + ISO/DIS 7690-D
Idle working
without suction In
operation
Sound power
level dB W (A) [mW
(A)] LW 88.8 [ 0.8 ] 92.9 [ 1.9 ]
Sound pressure level
at operator
station
dB (A) [dB max]
79.2 84.6 [< 130]
K Costant = 2 [dB] according to pr EN 848-1
The values refer to the "free field" conditions in accordance with the test
modalities foreseen by the reference norm.
ATTENTION:
The noise levels which have been measured are emission levels and not levels of safe working.
The relation between emission levels and exposure levels may not be used to determine whether
further precautions are required.
Factors which influence the real exposure level for the operator include the exposure time, the room
features, further sound sources (as for example number of the adjacent working machines).
Also the exposure levels permitted are not the same for all countries.
Thank to this information the operator to evaluate the risks and the dangers.
Here are some factors which reduce the exposure to the noise:
- right tool selection
- right rotation speed selection
- machine and tool maintenance
- proper use of ear protective means.

GENERAL
T1 1.11
1
1-71-7
1-71-7
1-7 SAFETY RULESSAFETY RULES
SAFETY RULESSAFETY RULES
SAFETY RULES
Carefully read this manual before starting the machine.
In the proper Section concerning the adjustments the relative guards and their use are described.
This machine has been built to ensure the highest safety degree
as well the best perfomance.
The manufacturer is not responsible for the damages due to modifications carried out on the
machine.
Final safety depends on you.
Any machine tool may be be potentionaly dangerous: do not forget it!
PERSONAL SAFETYPERSONAL SAFETY
PERSONAL SAFETYPERSONAL SAFETY
PERSONAL SAFETY
1- Experience teaches that there are various objects on a person that can cause injuries; take off
rings,watches,bracelets;buttonyoursleevestightlyaroundyourwrists,takeofftiesthatcould
be caught in tight places, keep hair gathered underneath aproper nets (cap, elastics, hair pins).
Use prescribed footwear usually recommended by all countries.
2- Always use glasses, protective shields for your eyes.
3- Use proper means for ear protection (plugs etc.)
MACHINE SAFETYMACHINE SAFETY
MACHINE SAFETYMACHINE SAFETY
MACHINE SAFETY
1- Be extremely careful when starting any working cycle
2- Never start the machine without having properly installed the covers for the spindle, the belts,
chains etc.
3- Before starting the machine make sure that the worktable is free from parts which do not relate
to the working
4- Work only when all guards are in place.
5- Do not machine workpieces too smal or too big for the machine.
6- Before fitting the spindle make sure that each support surface is clean, free from dents and
perfectly flat.
7- Make sure that the cutters are perfectly balanced, sharp and well clamped.
Not sharp tools reduce not only the quality of the finished piece but they increase the piece
kickback danger.
8- Neverusedeformedcuttersanddonotexceedthespeedlimitindicatedonthemandprescribed
by tool manufacturer or by MINI MAX.
9- Use only tools in accordance with prEN 847-1 and suitable for manual feed.
10- The use of circular saw blades is not permitted
11- Thetoolshallbeadjustedwiththemachineoffandwithproperinstruments(gauge,comparator).
12- It is necessary to connect all suction hoods to the suction system.
By taking proper measures make sure that when you start the motor the suction system is
switched on at the same time.

GENERAL
1.12 T1 BF-NGB1
13- Test working to check the tool adjustment may not be carried out without the guards required.
14- The working area shall have a good lighting and a sufficient room so that the operator is always
out of a dangerous area and so that no slipping danger may rise.
15- Start the working only when the tool has reached the right working speed.
16- Inallmillingoperations,inwhichthepiecekickbackispossibleparticularyincaseofinterrupted
milling, you shall use antikickback devices.
In case of short pieces use template to guide the piece against the cutter.
17- When possible use a feeder.
MAINTENANCE SAFETY
1- When you stop the machine for carrying out adjustments or demounting any machine member,
turn main switch to zero and indicate it by a sign, then lock the main switch .
Make sure that the electric system of the machine is swichted off.
2- Completelystopthemachinebeforecleaningorremovingtheguardsformaintenanceoperations.
3- Thegeneralcleaningofthe machine (inparticulartheworktable)and of thefloorisan important
safety factor.
4- Use proper gloves for handling the tools.
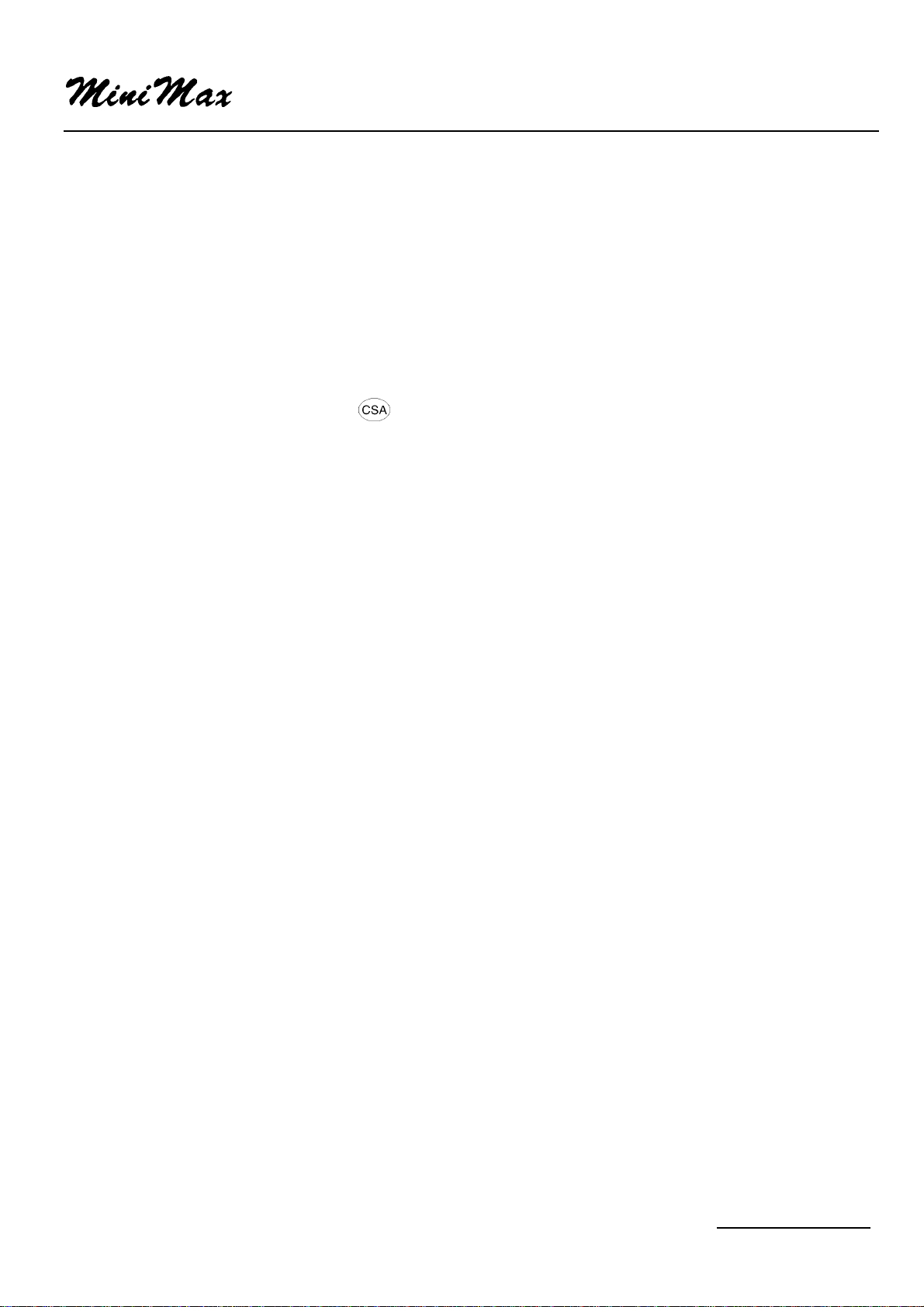
GENERAL
T1 1.13
1
1-81-8
1-81-8
1-8 OPTIONALSOPTIONALS
OPTIONALSOPTIONALS
OPTIONALS
1) TABLE WITH 2 EXTENSIONS FOR PROFILING
Extensions at inlet and outlet side of the machine table useful for profiling long pieces.
2) INTERCHANGEABLE SPINDLE MK5
It can be totally removed to use cutters with diffeternt bores.
3) 4 HP SINGLE PHASE MOTOR
NOTE:These optionals may be requested only when you order the machine.

GENERAL
1.14 T1 BF-NGB1
POSIZIONE OPERATORE
OPERATOR POSITION
POSITION OPERATEUR
STELLUNG DES BEDIENUNNGSMANNES
POSICION OPERADOR
1-91-9
1-91-9
1-9 OVERALLDIMENSIONSOVERALLDIMENSIONS
OVERALLDIMENSIONSOVERALLDIMENSIONS
OVERALLDIMENSIONS

GENERAL
T1 1.15
1
The measures indicated above are to be considered as the free space of the working area.

GENERAL
1.16 T1 BF-NGB1
1-101-10
1-101-10
1-10 SAFE WORKING PROCEDURESSAFE WORKING PROCEDURES
SAFE WORKING PROCEDURESSAFE WORKING PROCEDURES
SAFE WORKING PROCEDURES
C.1C.1
C.1C.1
C.1GENERALGENERAL
GENERALGENERAL
GENERAL
These notes are given as examples for the safe operation of the machine.
C.2C.2
C.2C.2
C.2OPERATOR TRAININGOPERATOR TRAINING
OPERATOR TRAININGOPERATOR TRAINING
OPERATOR TRAINING
It is necessary that all operators of vertical spindle moulding machines are properly trained in the
use, adjustment and operation of the machine, in particular:
a) The principles of the correct operation and use of the machine, adjustment of the fence,
safeguards as well as the use of devices for special working.
b) The right selection of tools for each working.
c) The safe handling of the workpiece during milling operations.
d) The position of the hands relative to the cutter before, during and after working.
C.3C.3
C.3C.3
C.3STABILITYSTABILITY
STABILITYSTABILITY
STABILITY
To ensure the correct and safe operation of the machine, it shall be stable and and securely fixed to
the floor (see par. 2-1.)
C.4C.4
C.4C.4
C.4MACHINE SET UPMACHINE SET UP
MACHINE SET UPMACHINE SET UP
MACHINE SET UP
a) The machine shall be isolated from the power source before carrying out any adjustment.
b) For clamping and setting the tools refer to the tool manufacturer’s instructions.
The force applied for locking the tips shall be the same force specified by the tool manufacturer.
c) For safe and efficient operation use balanced tools and supports.
C.5C.5
C.5C.5
C.5PIECE GUIDANCEPIECE GUIDANCE
PIECE GUIDANCEPIECE GUIDANCE
PIECE GUIDANCE
It is important to use:
a) the fence to ensure during the milling the proper piece guidance.
b) when possible a proper element joining the fence halves in order to minimise the gap between
the cutters and the fence halves.
c) a pusher for the manual piece feed or when possible a feeder which may be switched off when
it shall not be used.
d) roller tables or table extensions shall be used to support long pieces.

GENERAL
T1 1.17
1
C.6C.6
C.6C.6
C.6DIRECTION OF ROTATION AND ROTATION SPEED SELECTIONDIRECTION OF ROTATION AND ROTATION SPEED SELECTION
DIRECTION OF ROTATION AND ROTATION SPEED SELECTIONDIRECTION OF ROTATION AND ROTATION SPEED SELECTION
DIRECTION OF ROTATION AND ROTATION SPEED SELECTION
C.6.1C.6.1
C.6.1C.6.1
C.6.1 DIRECTION OF ROTATIONDIRECTION OF ROTATION
DIRECTION OF ROTATIONDIRECTION OF ROTATION
DIRECTION OF ROTATION
It is very important that the tool rotates in the correct direction.and that the piece feed occurs in the
direction contrary to direction of the spindle rotation.
C.6.2C.6.2
C.6.2C.6.2
C.6.2 SPEED SELECTIONSPEED SELECTION
SPEED SELECTIONSPEED SELECTION
SPEED SELECTION
The operator must ensure that the right rotation speed has been selected and that the speed selected
is proper for the tool fitted to the spindle.
C.7C.7
C.7C.7
C.7MACHINE OPERATION, GUARD SELECTION AND ADJUSTMENTMACHINE OPERATION, GUARD SELECTION AND ADJUSTMENT
MACHINE OPERATION, GUARD SELECTION AND ADJUSTMENTMACHINE OPERATION, GUARD SELECTION AND ADJUSTMENT
MACHINE OPERATION, GUARD SELECTION AND ADJUSTMENT
Because of the variety of workings which can be carried out on vertical spindle moulding machines
by using different spindles, toolholders and cutters, no safeguard can be considered effective for all
conditions.
Each working should be considered separately and the best practicable safeguard selected for that
particolar job.
The cutter type, the tips projection and the height at which the cutter is set, will determine the
minimum diameter of the hole on the table.
Thismaybeobtainedbyusingthereducingringssupplied,thusreducingtheriskthattheworkpiece
oscillates or fits into the cutters.
The guard shall enclose the cutters to the greatest extent according to the working.
The distance between the fence halves shall be so large only to permit the cutter rotation without
contact.
If you use a removable feeder on the machine with straight fence, it can be used to cover the cutters
to the greatest extent possible and often represents the best method of guarding on these machines.
Such feeders shall be easly adjustable to suit different size of workpiece and should not create a
trapping hazard.
If no feeder is used, pressers forming a tunnel, through which the workpiece can be fed, may be
properly used; they fit for working at the fence on the entire piece length if they are used with an
element joining the fence halves or other means to close the gap between fence halves.
C.8C.8
C.8C.8
C.8MILLING AT THE FENCE, WORKING ON THE ENTIRE PIECE LENGTHMILLING AT THE FENCE, WORKING ON THE ENTIRE PIECE LENGTH
MILLING AT THE FENCE, WORKING ON THE ENTIRE PIECE LENGTHMILLING AT THE FENCE, WORKING ON THE ENTIRE PIECE LENGTH
MILLING AT THE FENCE, WORKING ON THE ENTIRE PIECE LENGTH
Tohindertheaccesstothetoolduring the milling at the fence, it is necessarytousetogetherwiththe
fencearemovalefeederorguardsequippedwithproperpressersaccordingtothepiecedimensions.
Thefollowingpiecemaybeusedtopush the previous one; the last piece is milledattheendwiththe
aid of a pusher.
In case of thin pieces only the vertical presser may be used if its thickness is proper.

GENERAL
1.18 T1 BF-NGB1
C.9C.9
C.9C.9
C.9INTERRUPTED MILLINGINTERRUPTED MILLING
INTERRUPTED MILLINGINTERRUPTED MILLING
INTERRUPTED MILLING
To hinder the access to the tool during the not-through milling (interrupted milling) it is necessary
tousetogetherwiththefencearemovablefeederorguardsequippedwithproperpressersaccording
to the piece dimensions.
To hinder kickback of the piece use front and rear stops which are fastened to the fence, to the table
or to the table extension.
We recommend to use a clamping template unless the piece may be hold in a safe way by the hands.
For clamping the piece use fast locking devices which operate with levers or cams.
C.10C.10
C.10C.10
C.10 MILLING AT THE SPINDLEMILLING AT THE SPINDLE
MILLING AT THE SPINDLEMILLING AT THE SPINDLE
MILLING AT THE SPINDLE
Tohindertheaccesstothetoolduringthemillingatthespindleusetheproperguardandaclamping
template.
C.11C.11
C.11C.11
C.11 CHAMFERINGCHAMFERING
CHAMFERINGCHAMFERING
CHAMFERING
To hinder the access to the tool during the oblique milling, besides the fence use a special template
or an auxiliary stop.
C.12C.12
C.12C.12
C.12 CLIMB MILLINGCLIMB MILLING
CLIMB MILLINGCLIMB MILLING
CLIMB MILLING
When possible it is necessary to avoid the clim milling.

T1 2.1
2
SECTION 2SECTION 2
SECTION 2SECTION 2
SECTION 2
INSTINST
INSTINST
INSTALLAALLA
ALLAALLA
ALLATIONTION
TIONTION
TION
PagePage
PagePage
Page
2-1 Unloading the machine ................................................................................................................ 2.2
2-2 Fitting the demounted parts ........................................................................................................ 2.4
2-2.1 Fitting the additional tables ( )............................................................................. 2.4
2-3 Electric connection ........................................................................................................................ 2.6
2-4 Connection to the suction system ............................................................................................... 2.8
2-5 Safety devices................................................................................................................................. 2.9
Table of contents
Other MiniMax Lathe manuals