Miura MP1-200 User manual

START-UP OPERATION
MANUAL
Multiple Installation Controller
Pressure Controller MP1-200
MI Terminal MT1-200
T519-998-9150

Date of preparation: May 2012

Introduction
Have the documents below available as well as this Start-up Operation Manual for the start-up operation
of the Pressure Controller MP1-200 (hereinafter called MP1-200)/MI Terminal MT1-200 (hereinafter
called MT1-200).
Document name Manual No. Usage
MP1-200/MT1-200
Installation Manual T519-998-9140
Required for installing the power supply wire and
earth leakage circuit breaker and for performing the
input/output wiring, communication wiring, and
steam pressure sensor wiring.
Also have the document below available according to the boiler to be connected.
Document name Manual No. Usage
Start-up operation
manuals for
equipment units used
-------- Required for setting and operating each equipment
unit.

i
Table of Contents
1. Before the Start-up Operation.............................................................................3
1.1. Checking Installation .............................................................................................................3
1.2. Model Configuration ..............................................................................................................4
1.3. Circuit Board Layout..............................................................................................................5
1.4. Supported Function List ........................................................................................................7
1.5. Display Control Panel............................................................................................................9
1.6. List of Display Items ............................................................................................................10
2. Related Equipment Setting/Start-up .................................................................11
2.1. Setting Boiler for MI Control ................................................................................................11
2.1.1. Setting boiler steam pressure .................................................................................. 11
3. Setting MP1-200..................................................................................................12
3.1. MP1-200 Basic Setting and Connection..............................................................................12
3.1.1. Setting switch (SW1) ............................................................................................... 13
3.1.2. Setting MI control (SW2 to SW4, VR1, and VR4).................................................... 14
3.2. Setting Others for MP1-200 ................................................................................................15
4. Setting MT1-200..................................................................................................16
4.1. MT1-200 Setting Switch Layout and Operation Method......................................................16
4.2. Setting MT1-200 Switch ......................................................................................................17
4.3. Setting MT1-200 Data .........................................................................................................18
4.4. Operating Clear for MT12-CPU Circuit Board (SW2) ..........................................................23
4.5. MT1-200 Setting Example...................................................................................................24
4.5.1. Rotation setting example ......................................................................................... 24
4.5.2. Timer setting example ............................................................................................. 25
5. Checking Operation ...........................................................................................27
5.1. Checking MI-NET Communication ......................................................................................27
5.2. Checking MT1-200..............................................................................................................27
5.2.1. Direct input monitor on MT1-200 Boiler Control Terminal........................................ 27
5.3. Checking MP1-200..............................................................................................................28
5.4. Checking MI Control Operation ...........................................................................................28
6. Handling MT1-200 Alarm (MT12-CPU Circuit Board).......................................30
7. Troubleshooting .................................................................................................34
7.1. There is a small difference between the MPI-200 header pressure display and header steam
pressure gauge. ..................................................................................................................34
7.2. MT1-200 indicator blinks. ....................................................................................................34
7.3. Boilers are controlled by the boiler steam pressure settings (boilers are in manual operation).
............................................................................................................................................34

ii
7.4. The boiler stops with the voltage lower than the control pressure setting (VR1).................34
7.5. “MI” LED turns off................................................................................................................34
7.6. “B.BLOW” and “S.BLOW” LEDs light regardless of 0 of each notification time setting........35
7.7. Input signal error indication is displayed. ............................................................................35
7.8. Communication error occurs. ..............................................................................................36
7.9. When the main power of MT1-200 is off for a long period, the priority order becomes “1”..38
7.10. When the main power of MT1-200 is off for a long period, “F02” alarm is displayed...........38
7.11. Rotation may not occur. Or priority order is duplicated. ......................................................38
8. Supplemental Explanation ................................................................................39
8.1. MP1-200 Input/Output Signal Operation Overview .............................................................39
8.2. MI Control Operation Overview...........................................................................................41
8.3. Priority.................................................................................................................................44
8.4. Backup control ....................................................................................................................45
8.5. Blowdown Timing Notification Function...............................................................................45
8.6. Boiler Maintenance Control Function ..................................................................................45
8.7. Low Load Operation Control ...............................................................................................46

2. Related Equipment Setting/Start-up
3
1. Before the Start-up Operation
1.1. Checking Installation
Before the start-up operation of MP1-200/MT1-200, check the following according to
“MP1-200/MT1-200 Installation Manual.”
a) Unit installation
Ensure that the unit is secured to an appropriate location.
See the section “5. Installation” in MP1-200/MT1-200 Installation Manual for details.
b) Installation of steam pressure sensor
Ensure that the MP1-200 steam pressure sensor is installed correctly to the steam header.
Also ensure that the MT1-200 steam pressure sensor (optional) is installed correctly if it is
used.
See the section “5. Installation” in MP1-200/MT1-200 Installation Manual for details.
c) Wiring
Ensure that the following wires 1) to 5) are correctly connected referring to the section “6.
Wiring” in MP1-200/MT1-200 Installation Manual.
1) Power supply wire and earth leakage circuit breaker installation
2) Input/output signal wire
3) Communication wire
4) Steam pressure sensor wire

2. Related Equipment Setting/Start-up
4
1.2. Model Configuration
MP1-200 and MT1-200 come in the following models depending on the power supply voltage,
available language, cover color, and others. For MT1-200, the model lineup has been renewed
with the adoption of a new internal board MT12-CPU and a wide-range power supply.
The following model is used in North America.
Table 1-1 MP1-200 Model in North America
Model MP1-200A
Steam pressure
specifications 20 K
Power supply 120 VAC
50 / 60 Hz, single phase
Available language English
Cover color Cream
Steam pressure unit PSI
Table 1-2 MT1-200 Model in North America (MT1-200-MAIN circuit board included)
Item MT1-200A
Power supply 120 VAC
50 / 60 Hz, single phase
Available language English
Cover color Cream
Country of destination North America
Steam pressure unit kgf/cm2
Table 1-3 MT1-200 Model in North America (MT12-CPU circuit board included)
Item MP1-200 CG
Power supply 100 to 220VAC
50 / 60 Hz, single phase
Available language English
Cover color Cream
Country of destination North America, Asia
Steam pressure unit kgf/cm2, MPa, PSI

2. Related Equipment Setting/Start-up
5
1.3. Circuit Board Layout
Figure 1-1 MP1-200 Internal Layout
Transformer
MP1-200
DISP
10
P
10
P
CN3 CN2
4P
3P
MP1-200
MP11-****
MP1-200-CPU
MP1-200
MP11-****
Program version indication

2. Related Equipment Setting/Start-up
6
Figure 1-2 MT1-200 Internal Layout (MT1-200-MAIN circuit board)
Figure 1-3 MT1-200 Internal Layout (MT12-CPU circuit board)
CN4CN3

2. Related Equipment Setting/Start-up
7
1.4. Supported Function List
Functions and specifications of MP1-200 and MT1-200 have been changed along with the
program version and circuit board change. The changes are listed below. See the descriptions
of functions for details.
The method of checking the program version depends on the model and circuit board type;
therefore check the program version according to Table 1-4.
Table 1-4 Program Version Checking Method
Model Checking method
MP1-200 Check the label on the ROM on the MP1-200-CPU circuit board.
(See Figure 1-1)
MT1-200
(MT1-200-MAIN)
Check the label on the ROM on the MT1-200-MAIN circuit board.
(See Figure 1-2)
MT1-200
(MT12-CPU) Check the display. The version number of four digits of “MT12 -
****”is displayed in the program version item in the DIP SW display.
(See Figure 1-6)
Table 1-5 List of Supported Functions along with MP1-200A Program Change
Program version
MP11-****
1015 or later
Emergency stop input
(See Table 8-1.)
Contact specification switching (SW1-2)
Supported
Low load operation control (SW1-1)
Supported
Steam pressure display unit switching PSI
Note) Contact our sales office for the program versions other than the above.

2. Related Equipment Setting/Start-up
8
Table 1-6 List of Function Changes along with MT1-200A Program Change
Program version MT11-**** MT12-****
1015 1000 or later
Circuit board type MT1-200-MAIN MT12-CPU
Operation method for optional steam
pressure sensor availability setting
On-display On-display
Optional steam pressure sensor 20-k
and 30-k support
Supported
Supported
Rotation time addition
Supported
Supported
Steam pressure unit switching
(MPa, kgf/cm2, PSI)
Unsupported
Supported
Note) Contact our sales office for the program versions other than the above.
Table 1-7 List of Function Changes along with MT1-200 Circuit Board Change
Circuit board type MT1-200-MAIN MT12-CPU
Internal layout diagram Figure 1-2 Figure 1-3
Circuit board layout MT1-200-MAIN
MT1-200-DSP
MT1-200-PW
MT12-CPU
MT1-200-DSP
Power supply voltage 120 VAC
100 to 220 VAC
Internal power supply Transformer Switching power supply
Steam pressure sensor
power supply
12 VDC 24 VDC
Memory backup
method
Battery implementation
on the board
Battery replacement
request to Electric
Manufacturing
Department is required.
Battery
replacement
available
(Connector type)
No battery
Backup for two weeks or
more available with parts
on the board
Program version
upgrade method
ROM replacement Flash rewrite
Program version
(See Table 1-4.)
MT11-**** MT12-****

2. Related Equipment Setting/Start-up
9
1.5. Display Control Panel
Figure 1-4 MP1-200 Control Panel
Figure 1-5 MT1-200 Control Panel
“DISPLAY CHANGE” Pressing the switch
changes the display in the order below.
Steam pressure
Control pressure setting
Control range setting
Pressure alarm L setting
Pressure alarm H setting
Display
It turns ON when the steam
pressure becomes the set value
of pressure alarm H or more. At
this time, the contact of pressure
alarm H output turns ON.
HIGH-PRESSURE LED
It turns ON when the steam
pressure becomes the set value
of pressure alarm L or less. At this
time, the contact of pressure
alarm L output turns ON.
LOW-PRESSURE LED
It turns ON when the circuit
between external control input
terminals 2 and 3 is shorted. At
this time, the boilers that are
under normal communication
conditions are stopped regardless
of pressure and manual/automatic
mode.
EMERGENCY STOP LED
It turns ON when the circuit
between external control input
terminals 7 and 8 (all stop) or
between 6 and 7 (all combustion)
is shorted.
LUMP OPERATION LED
It is used to change the display
items on the 4-digit LED.
When external output “alarm” is
ON, press it. The output turns
OFF.
DISPLAY CHANGE switch
It turns ON if any of the buzzers
for the boilers under MI control(*)
is activated.
At this time, the external output
“boiler trouble” turns ON.
BOILER TROUBLE LED
It turns ON if an abnormality of
pressure sensor is detected. At
this time, the external output
“sensor fail” turns ON.
SENSOR FAIL LED
It turns ON if the CPU is not
correctly operated due to voltage
fluctuation, circuit failure, etc.
CPU FAIL LED

2. Related Equipment Setting/Start-up
10
1.6. List of Display Items
Figure 1-6 MT1-200 List of Display Items
Note 1) Items added from MT12-CPU circuit board
The display items are changed by “SELECT”. Setting can be made by pressing “UP” and “DOWN” simultaneously.
Basic data display
It is shown by simultaneous pressing of “SELECT” and “B.BLOW”.
Priority and header steam pressure
The first two digits are the priority order.
The priority order can be set.
Boiler steam pressure
It is displayed when the optional pressure
sensor is installed.
It can be set.
Steam pressure setting (high)
(Only when the pressure sensor is nstalled)
It is combustion stop pressure in manual mode
Normal display
It is shown by simultaneous pressing of “SELECT” and “S.BLOW”.
DIP SW display
It is shown by simultaneous pressing of “SELECT” and “TIMER”.
The first digit represents the day of the week from Sunday to Saturday.
0
1 - 7
8
9
A to F
Current time (24 hour display) hour minute
hour, minute
The day of the week is represented by
number: 0as Sunday, 1 as Monday … 6 as
Saturday. It can be set.
Next ON/OFF time
0display: ON time
F display: OFF time
Cumulative combustion time (Hour)
It is used to determine the priority in rotation.
It can be set.
Input signal error
It is displayed when the input signal has an
error.
Under-judgment alarm
It is displayed when there is an under-
judgment alarm.
With/without pressure sensor
It is set to 1 when the optional pressure
sensor 1 is installed.
Pressure sensor specification (Only when the
pressure sensor is installed)
The settings vary depending on the pressure
specification.
01: 0.98 MPa (10 k)
02: 1.96 MPa (20 k)
03: 2.94 MPa (30 k)
It is for future optional parts.
Be sure to set to 0.
It is for future optional parts.
Be sure to set to 0.
Boiler No. display
It is the boiler number set by the boiler
number setting SW in the box.
It is only the display and cannot be changed
here.
Pressure display unit
The unit of steam pressure display and
pressure setting can be changed.
0: MPa
1: kgf/cm2
2: psi
Program version
The program version of the CPU board is
displayed.
Differential setting (high)
(Only when the pressure sensor is installed)
Steam pressure setting (low)
(Only when the pressure sensor is installed)
It is high fire stop pressure in manual mode
Differential setting (low)
(Only when the pressure sensor is installed)
Holding-pressure setting
(Only when the pressure sensor is installed)
It is the pressure obtained during automatic
standby. When 0.0 is set, pressure holding
combustion does not occur.
Differential setting (holding)
(Only when the pressure sensor is installed)
ON time on each day
It is the time to be ON with the timer.
OFF time on each day
It is the time to be OFF with the timer.
Decimal point is shown.
Post-fire time (second)
Low fire occurs for the set time or more
before stop.
Rotation time
(Only displayed on boiler No. 1.)
Time for rotation
Effective when the rotation flag is 1 to 7.
Rotation flag
The performances below are shown
according to the rotation flag value.
: No automatic rotation
: Constant time at intervals of 1 to 7 days
: When [B. Blow] is pressed
: Priority order is fixed
: Interval of 1 to 12 hours
(A to F is effective only when the pressure
sensor is installed.)
The rotation will be performed with the setting
of boiler No. 1 even when the 0~7 is set in the
boiler other than boiler No. 1.
Priority combustion time after complete
blowdown (second)
It is the time to bring forward the priority
temporarily after [B. Blow] is pressed.
Complete blowdown notification time (hour)
It is the time to notify complete blowdown.
Decimal point is shown (High fire
conversion)
Soot blow notification time (hour)
It is the time to notify soot blow. (High fire
conversion)
Display on boiler No.no setting
Displayed when the boiler No.is 0.
Input condition display
Continued pressing of [Select] for 7 seconds or
more shows MT1-200 signal input status.
Display on alarm evaluation (Note1)
It is displayed when an alarm has been
evaluated.

2. Related Equipment Setting/Start-up
11
2. Related Equipment Setting/Start-up
Before the setting and start-up operations of MP1-200/MT1-200, complete the setting and start-up
operations of all equipment units for MI control with MP1-200.
2.1. Setting Boiler for MI Control
Perform the steam pressure setting (the steam pressure sensor) for the boiler unit. Perform and
check the settings of equipment units for MI control as described below.
For details about how to set and operate these equipment units, refer to the start-up manuals of
appropriate models.
2.1.1. Setting boiler steam pressure
The boiler steam pressure setting (high) and boiler steam pressure setting (low) must be
set to satisfy the following conditions. This allows MP1-200 to provide smooth MI control.
・Boiler steam pressure setting (high) - boiler differential setting (high)
≥MI control upper limit pressure + pressure loss
・Boiler steam pressure setting (low) - boiler differential setting (low)
≥MI control upper limit pressure + pressure loss
・Boiler steam pressure setting (high) ≥boiler steam pressure setting (low)
Note 1) Set the boiler steam pressure setting (high) lower than the boiler backup steam
pressure switch setting. If the boiler steam pressure exceeds the boiler backup
steam pressure switch setting, the boiler will be forced into the standby state.
Note 2) The MI control upper limit pressure indicates the upper limit of the pressure
range where boilers are fired up under MI control.
Note 3) Set the “Boiler steam pressure setting (high) - boiler differential setting (high)”
and “Boiler steam pressure setting (low) - boiler differential setting (low)” higher
than the MI control upper limit pressure in consideration of pressure loss, sensor
errors, and other factors (about 0.1 MPa〔15PSI〕under standard pressure). If
these are set to around the MI control upper limit pressure, the combustion
standby may be continued due to pressure loss between the header and boiler
and steam pressure sensor errors.

3. Setting MP1-200
12
3. Setting MP1-200
3.1. MP1-200 Basic Setting and Connection
This setting is essential for using MP1-200.
Be sure to perform the settings in Sections 3.1.1 and 3.1.2 before use.
Figure 3-1 MP1 Internal Switch Layout
VR7: Zero adjustment 2
Usually, settings are not
required.
VR6: Zero adjustment
Use for Zero adjustment
of pressure sensor.
VR5: Gain
Use for gain adjustment
for pressure sensor.
VR4: Control range
Use for setting pressure
range for control.
VR3: Alarm L
Use for setting the
desired pressure for low
pressure alarm.
VR2: Alarm H
Use for setting the
desired pressure for
high pressure alarm.
VR1
: Control pressure
Use for setting
maximum pressure for
control.
Terminal block for
external control
Use for external control
such as all stop.
External switches are
connected to this
terminal block.
Terminal block for
external monitor
Output terminal block for
alarm and buzzers.
SW1
Set pressure
sensor type or
earthquake
detector contact.
SW2
Set the quantity of
boilers connected.
SW3
Set the desired
quantity of boilers
to give priority to
low fire.
SW4
Set the delay time of
combustion stop for
the boiler with the
first priority.

3. Setting MP1-200
13
3.1.1. Setting switch (SW1)
Set SW1 of MP1-200 according to Table 3-1.
Figure 3-2 MP1-200 Dip Switch Settings (Steam Pressure Sensor 20k Specifications)
Table 3-1 MP1-200 Switch (SW1) Settings
SW1 Functions
Corresponding
program version (Note
1)
(See Table 1-4.)
Remarks
SW1-1 Low load
operation control
*006 and
*011 or later
Set whether to use the low load operation control. Refer to page
46 for information including precautions about the low load
operation control.
ON: Under normal control
OFF: Under the low load operation control
SW1-2 Emergency stop
input setting *005 or later
Set the contact specifications of emergency stop input (See
Table 8-1.) (a contact (normally open) or b contact (normally
closed)).
ON: normally open
OFF: normally closed
SW1-3 Not used - OFF fixed
SW1-4
Communication
status output
setting
All
Set the output condition of the communication status (See Table
8-3.). Close the contact under the following conditions.
ON: When MP1-200 is normally communicating with any of
MT1-200 units.
OFF: When MP1-200 is not communicating with any of
MT1-200 units.
SW1-5
SW1-6
Steam pressure
sensor setting All
Perform the setting according to MP1-200 steam pressure
sensor.
SW1-5 SW1-6 Steam pressure sensor specifications
MPa (kgf/cm2)
OFF OFF 0.98 (10)
ON OFF 1.96 (20)
OFF ON No setting is allowed
ON ON 2.94 (30)
SW1-7 Not used - OFF fixed
SW1-8 Steam pressure
unit setting
See the description in
the right.
Set the steam pressure unit to be displayed on MP1-200. Set it
with the boiler display unit.
Fix SW1-8 to OFF because MP1-200A for North America
supports only PSI unit. (Note 1)
Model SW1-8 Steam pressure unit
MP1-200A
(For North America)
OFF
Fixed
PSI
Note 1) Usable functions depend on the last three digits of the program version number “MP11 - *ooo.”
*= 1 (MP1-200A for North America), *= 0 (destinations other than North America)

3. Setting MP1-200
14
3.1.2. Setting MI control (SW2 to SW4, VR1, and VR4)
Set SW2 to SW4, VR1, and VR4 of MP1-200 according to Table 3-2.
Figure 3-3 SW2 to SW4
Table 3-2 MP1-200 Switch (SW2 to SW4, VR1, and VR4) Settings
Item Setting item Setting range Initial value Unit of measure
SW2
Quantity of boilers 0 to 15 0 boilers
Set the quantity of boilers to be controlled. Characters A to F correspond to 10 to 15 boilers.
Boilers connected more than the quantity specified here will not be under MI control.
SW3
Quantity of standby units 0 to 15 0 boilers
Set the quantity of boilers that should be held at low fire conditions. Characters A to F correspond
to 10 to 15 boilers. Boilers of the quantity specified here are started hold the lowest possible fire;
therefore, if higher responsiveness to load fluctuation is required, adjust this setting close to the
quantity of boilers (SW2). In addition, this setting changes the priorities to fire the boilers. (Refer to
page 41.)
SW4
Delay time 0 to 55 0 sec.
Set the time to delay the actual boiler stop for load fluctuation even after the first-priority boiler
reaches the pressure to stop. Note that if the pressure increases in the delay time to the level
where the steam pressure setting (high) of the boiler is activated, the order of the subsequent
ignitions may be incorrect or the response may be delayed. See the following for the relation
between switch settings and delay time.
SW4 setting 0 1 2 3 4 5 6 7
Delay time
(second)
0 1 2 4 6 8 10 14
SW4 setting 8 9 A B C D E F
Delay time
(second)
18 22 26 30 35 40 45 55
VR1
Control pressure setting - - Steam pressure unit for SW1-8
Press the “DISPLAY CHANGE” switch to display the “Control steam
pressure setting”. Turn the internal potentiometer VR1 to set the
maximum steam pressure value. When the delay time is 0, the
boiler with the first priority with this steam pressure stops.
VR4
Control range setting - - Steam pressure unit for SW1-8
Press the “DISPLAY CHANGE” switch to display the “Control range
setting”. While checking the display, turn the internal volume VR4 to
set a control steam pressure range. Boilers are controlled within the
pressure range between the control pressure (VR1) and the value
obtained by subtracting the control range (VR4) from the control
pressure (VR1).

3. Setting MP1-200
15
3.2. Setting Others for MP1-200
Set items in Table 3-3 as needed.
Table 3-3 MP1-200 Other Settings
Item Setting item Setting range Initial value Unit
VR2
Pressure alarm H - - Steam pressure unit for
SW1-8
Set it when the header steam pressure upper limit is
monitored.
Install an indication lamp, buzzer, etc. to the pressure alarm
H output. (See Table 8-3.) Press the “DISPLAY CHANGE”
switch to display the “Pressure alarm H.” While checking the
display, turn the internal potentiometer VR2 to set the steam
pressure for the alarm.
VR3
Pressure alarm L - - Steam pressure unit for
SW1-8
Set it when the header steam pressure lower limit is
monitored.
Install an indication lamp, buzzer, etc. to the pressure alarm
L output. (See Table 8-3.) Press the “DISPLAY CHANGE”
switch to display the “Pressure alarm L.” While checking the
display, turn the internal potentiometer VR3 to set the steam
pressure for the alarm.
VR5
VR6
Steam pressure sensor
correction - - Pressure unit for SW1-8
Adjust the header steam pressure indicator if it is different from the actual pressure.
Press the “DISPLAY CHANGE” switch to display the “Steam pressure” and make the
adjustment in the order of 1) and 2).
1) Zero adjustment (VR6)
Remove the steam pressure sensor from the steam
piping to release pressure from the sensor. Adjust
VR6 to the point where the steam pressure value is
changed from “ . ” to “0.00” as shown in the figure on
the right.
2) Gain adjustment (VR5)
Install the steam pressure sensor to the steam piping to apply pressure on the
sensor. At this time, adjust VR5 to agree with the reading of the steam pressure
gauge.
Note 1) If zero adjustment is performed after gain adjustment, another gain
adjustment must be performed.

4. Setting MT1-200
16
4. Setting MT1-200
4.1. MT1-200 Setting Switch Layout and Operation Method
The MT1-200 setting method and switch layout are as follows.
- Setting method
1) For settable items, pressing the “UP” and “DOWN” switches simultaneously starts blinking
of the area that allows setting.
2) Press the “UP” or “DOWN” switch to change the value.
3) After changing the value, press the “SELECT” switch to finish the setting.
Figure 4-1 MT1-200 (MT1-200-MAIN) Internal Switch Layout
Figure 4-2 MT1-200 (MT12-CPU) Internal Switch Layout

4. Setting MT1-200
17
4.2. Setting MT1-200 Switch
Items (indicated with ) described in Table 4-1 must be set to useMT1-200. Set the switches
on the circuit board of MT1-200.
Table 4-1 MT1-200 Basic Settings
Note 1) The indication on the circuit board varies depending on the circuit board type.
MT12-CPU : SW1
MT1-200-MAIN : DSW
Note 2) The setting is required only for MT1-200-MAIN. The MT12-CPU circuit board does not
have this switch.
Item Setting item Setting range Initial value Unit
SW1
DSW
(Note 1)
Boiler No. setting 0 to 15 0 -
Remove the top cover of MT1-200 to set a boiler No. other than 0 with the switches
(DSW or SW1) on the circuit board. Alphabetical characters A to F correspond to the
boiler No.10 to 15. To avoid overlapping of the boiler No. of each MT1-200 unit, set
them with consecutive numbers starting from 1.
If the boiler No. is not set (the boiler No. is 0), the indicator blinks as shown in the
figure on the right and MI control cannot be performed; therefore, a number other than
0 must be set.
Boiler No. setting switch Indication when the boiler No. is not set.
SW2
(Note 2)
SW2 (MT1-200-MAIN) OFF-ON OFF -
The usage of SW2 on the MT1-200-MAIN circuit board depends on the program
version. Set SW2 to OFF for the program version MT11-0011 and later.
Program version
(See Table 1-4.)
Usage of SW2
MT11-*010 and earlier Set to ON temporarily only when
the steam pressure sensor is set
MT11-*011 and later OFF fixed
MT12-**** No switch
Other manuals for MP1-200
2
This manual suits for next models
1
Table of contents
Other Miura Controllers manuals
Popular Controllers manuals by other brands
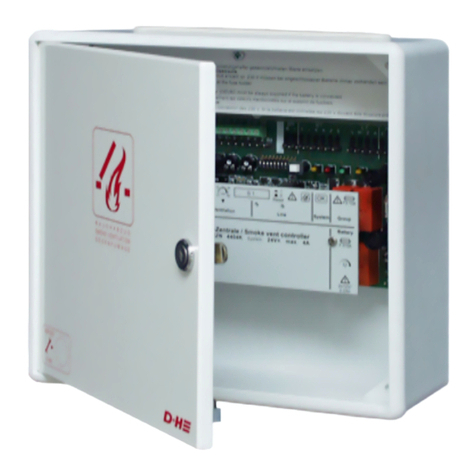
D+H
D+H RZN 4402-K V2 Original instructions
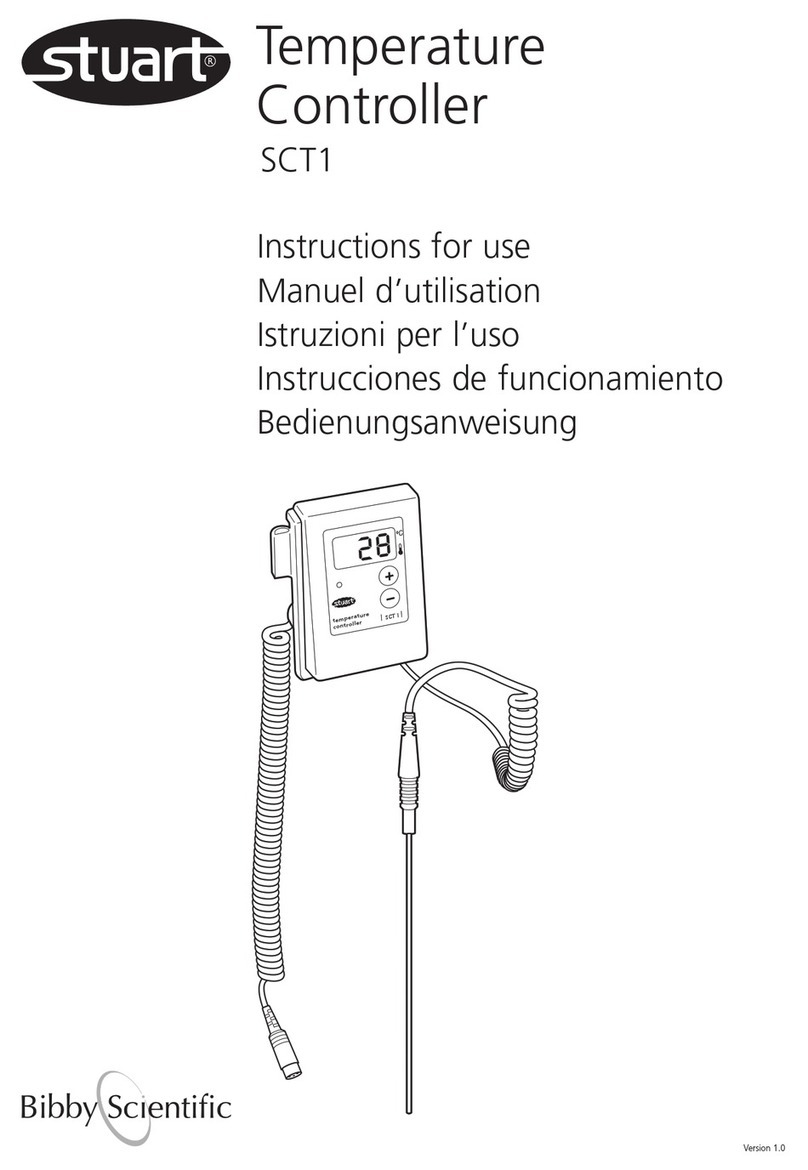
Bibby Sterilin
Bibby Sterilin Stuart SCT1 Instructions for use
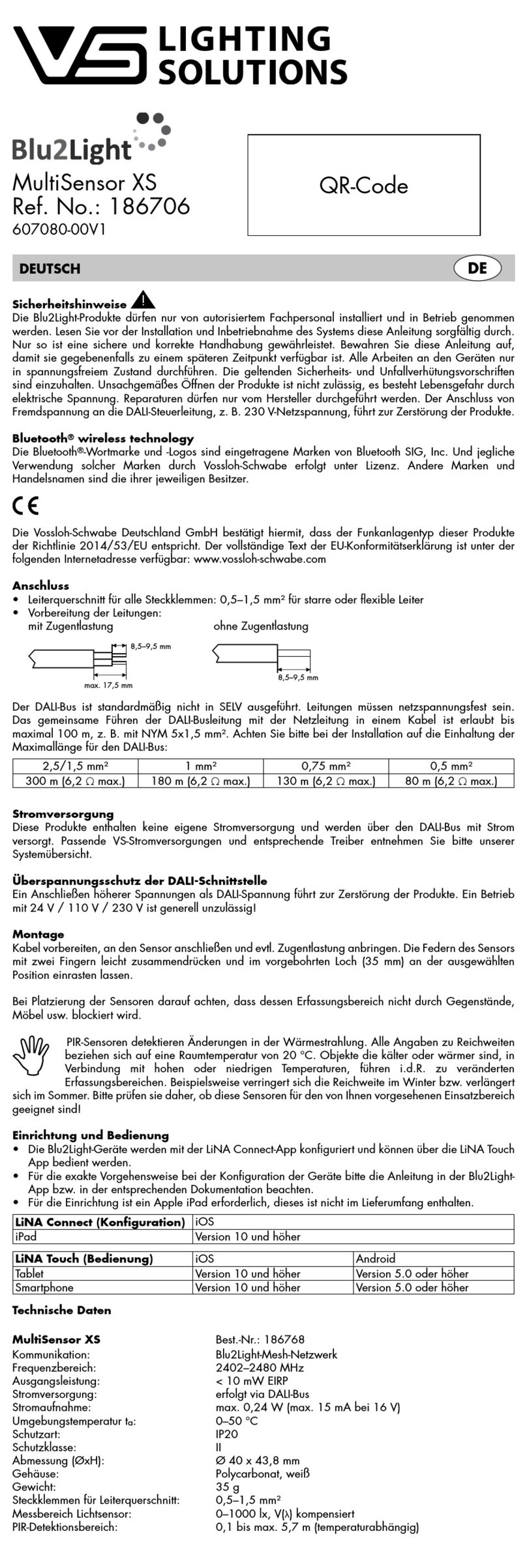
VS LIGHTING SOLUTIONS
VS LIGHTING SOLUTIONS Blu2Light MultiSensor XS manual
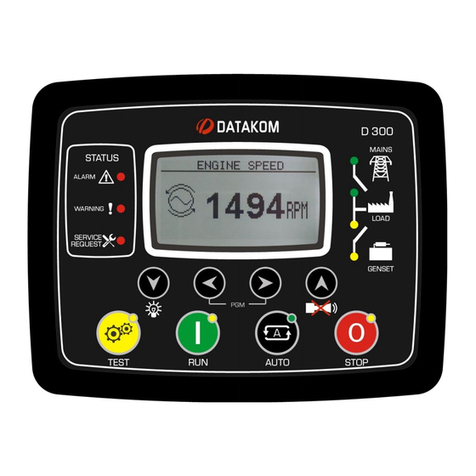
Datakom
Datakom D-300 MK2 user manual

Modellbau-Regler
Modellbau-Regler AS-12/15RW user manual
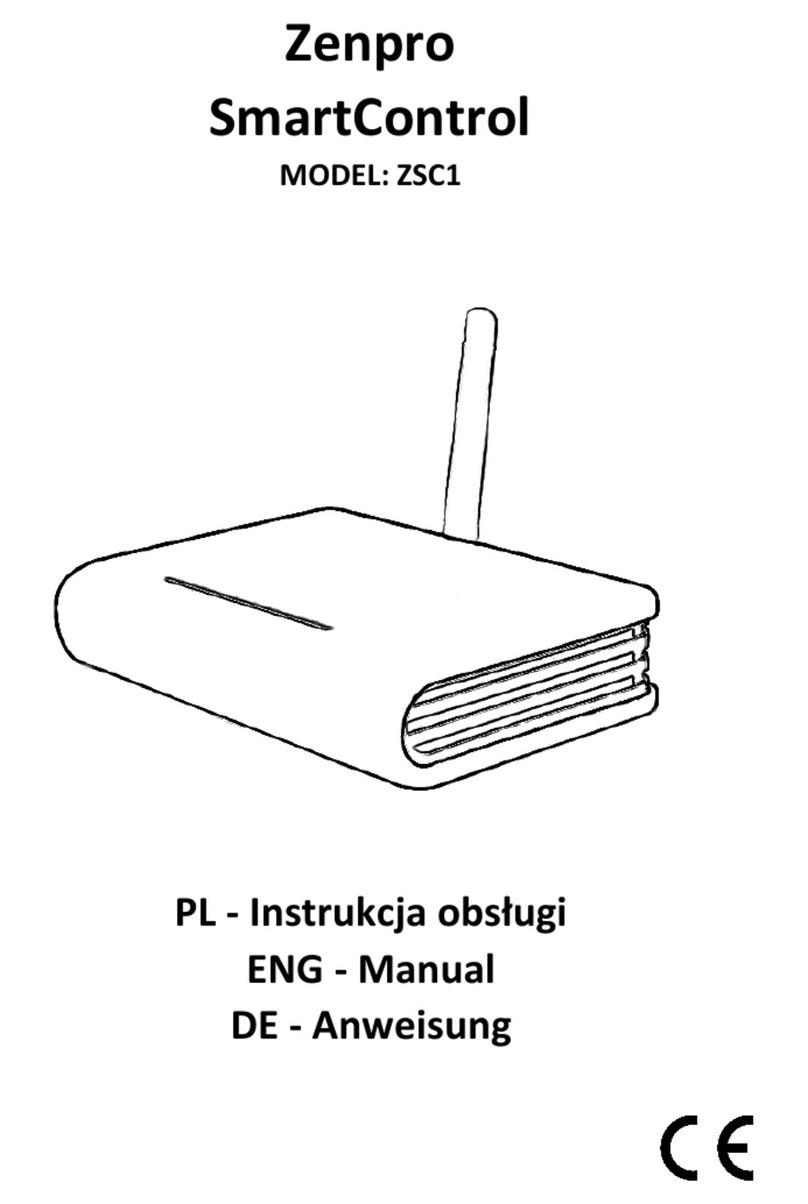
Zenpro
Zenpro SmartControl ZSC1 manual