MPC UC006 User manual

Operating manual
Unichiller in Desktop Housing
14.12.2009
Valid for following versions:
with natural refrigerant, Advanced models, for
models with heating
Valid for:
minichiller, minichiller w
UC006
UC007, UC010
UC012, UC012w
UC015, UC015w
UC022, UC022w
UC023w
UC025, UC025w
UC006Tw, UC009Tw


2
Contents V1.5/12.09
Foreword ............................................................................................................4
Chapter 1: Safety ................................................................................................5
Description of Safety and Information symbols ........................................................6
Intended Use and General Safety Instructions..........................................................7
Description .........................................................................................................8
Duties of responsible person .................................................................................9
Operator requirements ..........................................................................................9
Machine operator duties .......................................................................................9
Work area ...........................................................................................................9
Safety Devices to DIN12876............................................................................... 10
Environmental Conditions.................................................................................... 11
Operating conditions .......................................................................................... 12
Location ........................................................................................................... 13
Thermofluids ..................................................................................................... 14
Chapter 2 : Electronics and operation ...................................................................15
Display and operation ......................................................................................... 16
Advanced Functionality ...................................................................................... 16
Chapter 3: Connect the machine, fill and prepare fort he required application ............17
Power connection .............................................................................................. 18
Safety instructions ............................................................................................. 18
Start up ............................................................................................................ 18
Freezing protection (only valid for temperature control units with the option freezing
protection) ........................................................................................................ 18
Water-cooling (valid for units with water cooling) .................................................. 19
Connecting an externally closed application........................................................... 20
Switching on the temperature control unit ............................................................ 20
Setting the over-temperature switch..................................................................... 21
Entering a set point ............................................................................................ 21
Starting temperature control................................................................................ 21
Ending temperature control ................................................................................. 21
Filling and air purging an externally closed system ................................................. 22
Draining the machine and an externally closed application....................................... 23
Changing heat transfer fluid / internal cleaning ...................................................... 23
Chapter 4: Interface and software update ............................................................. 24
Data Communication .......................................................................................... 25
Chapter 5: First aid for a fault condition................................................................ 29
Display Error Messages....................................................................................... 30
Alarms and Warnings ......................................................................................... 30
Maintenance ..................................................................................................... 31
Decontamination / Repair .................................................................................... 32
Cleaning the surfaces ......................................................................................... 32
Plug contacts .................................................................................................... 32

3
Chapter 6: Taking the machine out of service........................................................ 33
Decommissioning............................................................................................... 34
Transport.......................................................................................................... 35
Disposal ........................................................................................................... 35

4
Foreword
Dear Customer,
The Huber team would like to thank you for ordering this product. You have made a
good choice. We thank you for your trust!
Please read and understand the instruction manual thoroughly before operating the unit.
All instructions and safety information must be complied with.
Please read this manual before transporting, commissioning, operating, maintaining,
repairing, storing or disposing of this unit.
Failure to comply with the instructions within this manual may invalidate any warranty
for this unit.

5
Chapter 1: Safety
In this chapter is to be found the following sections:
-Description of safety and information symbols
-Intended use and General Safety Information
-Description
-Duties of the responsible person
-Operator requirements
-Machine operator duties
-Work area
-Safety Devices to DIN 12876 (applicable for units with heating)
-Additional Protection Devices (if provided)
-Environmental conditions
-Operating conditions
-Location
-Thermofluids

6
Description of Safety and Information symbols
Safety information is shown with a pictogram and keyword.
The keyword indicates the level of the corresponding danger.
Danger!
Immediate risk to the life and health of
personnel (Serious injury or death).
Warning!
Possible risk to the life and health of
personnel (Serious injury or death).
Caution!
Possible dangerous situation (possible injury
to personnel or damage to property).
Information!
User-tips and other useful information.
Requirement!
Requirement to carry out a specific
method, or action, for safe machine
operation.

7
Intended Use and General Safety Instructions
Danger!
Non-intended use can result in considerable personal injuries and material damage.
No third persons are authorized to make any changes to the machine. The device
declaration becomes void, if any modification is carried out without manufacturers
consent. Only personnel trained by the manufacturer may carry out modifications,
repairs or maintenance work.
The following must be observed:
Always use the machine in a perfect working condition!
Only expert personnel may initially start-up and repair the device!
Do not bypass, bridge-over, dismantle or switch off the safety mechanisms!
The manufacturer is not liable for damages caused by technical changes
to the temperature control device, inappropriate handling and / or use of the
temperature control device without regard to the operating instructions.
The temperature control device is manufactured for commercial use only and may only
be used to maintain the temperature within the internal bath (does not apply for chillers)
and to maintain the temperature of reactors or other professionally expedient objects in
laboratories and industry. Suitable thermal fluids are used throughout the entire system.
The refrigerating or heating capacity is provided at the pump connections and in the
bath itself (does not apply for chillers). The technical specifications of the temperature
control device are determined in the data sheet. Operation must be prepared and carried
out according to the operating instructions. Any non-observance of the operating
instructions is considered as non-intended use.
The temperature control device corresponds to the state-of-the-art and the recognized
safety-related regulations. Safety devices are built into your temperature control device.
The device is NOT approved for use as a medical product!
This temperature control unit is NOT built as explosion-proof and is NOT
suitable for use in "ATEX" areas!
Foreseeable non-intended use:
-Activate the brakes for machines with rollers or roller support.

8
Description
Chillers are temperature control devices that ideally are used for carrying away of
process heat and as economic alternative for cooling water (drinking water) i.e. for a
reflux condenser, condensers, tools,…
Due to high refrigeration performance a very short cooling time can be achieved.
A pump is responsible for a good circulation of the thermal fluid.
For Chillers with a pump that can build pressure up to 3 bar, supply line pressure can be
set by means of a VPC-Bypass and thus can be adapted for the required application.
The pressure of the supply line is indicated via a manometer display.
Temperatures can be easily red via the LED-display screen.
An easy keypad (set point, arrow up and arrow down key) is used to set a set point.
Thermostats uses an over-temperature protection in accordance with DIN EN 61010-2-
010, which is independent of the actual control circuits (only valid for units with
heating)

9
Duties of responsible person
The operating instruction is to be kept easily accessible and in immediate vicinity of the
unit. Only suitably qualified personnel should operate this unit. Personnel should be
properly trained before operating the unit. Make sure that the operators have read and
understood the instruction manual. Supply appropriate Personal Protective Equipment as
required.
Operator requirements
Only authorised personnel should operate this unit. Personnel should be properly trained
before operating the unit. The minimum age for operators is 18 years. Personnel under
18 years should only operate the unit under the direct supervision of qualified
personnel. The operator is responsible for third parties within the working area.
Machine operator duties
Make sure that the operators have read and understood the instruction manual. Please
observe the safety instructions. Appropriate Personal Protective Equipment (e.g. safety
goggles, safety gloves) should be worn when operating the unit.
Work area
Work area is defined as the area in front of the machines control panel. Work area is
determined by the peripheral equipment connected by the operator.
It is the customer’s responsibility to ensure a clear, safe working area around the
temperature control unit. The arrangement of the work area should be made after
considering access to, and risk assessment of, the area and application.

10
Safety Devices to DIN12876
-Low level switch
-Adjustable over-temperature switch (also valid for units with heating)
Classification of Laboratory Thermostats and Baths
Your temperature control unit is designated a Class III FL.
Mechanical Over-temperature Switch
This temperature control unit is equipped with a mechanical over-temperature switch.
For setting the over-temperature protection refer to chapter setting the over-
temperature switch.
Classification Thermal Fluid Technical requirement Designation d
I non-flammable
aOver-temperature cut-off
cNFL
II Adjustable over-temperature cut-off
flammable b FL
III Adjustable over-temperature cut-off
and extra low-level switch
aNormally water; other fluids only when they are non-flammable in the event of a single
failure.
b The thermal fluid must have a flame point ≥65 °C, this means that ethanol can only
be used under constant supervision.
c The over-temperature protection can for example be provided by a fluid sensor or
a suitable over temperature switch.
dDetermined by the manufacturer.

11
Environmental Conditions
This unit, and operations, will comply with DIN EN 61010-1:2001, only when it is
located in suitable environmental conditions.
- for indoor use only;
- installation site ≤2000 m altitude;
- installed on a level, even, non flammable surface;
- maintain a clearance above and around the unit of 10 cm for water-cooled units,
and 20cm for air-cooled units, to allow air to circulate around the unit;
- for ambient temperature conditions please refer to the technical data sheet;
remaining within these ambient conditions is imperative in ensuring accurate
operation;
- maximum relative humidity of 80% up to 32°C, decreasing linearly to 50%
relative humidity at 40°C
- use only as long a power cord as necessary;
- the unit should be located so as not to restrict access to the mains power
switch;
- mains voltage should be ±10% of the rated value;
- avoid voltage spikes;
- transient voltage surges as they occur normally in the supply grid;
- clean rating 2;
- overvoltage category II

12
Operating conditions
Please make sure that the application and system performance is dependent upon the
temperature range, viscosity, and flow rate of the thermal fluid:
-Please ensure that the power supply connections are correctly dimensioned.
-The temperature control device should be located so, that sufficient fresh air
is available even when working with water cooled units.
-Please note that hose connections should be compatible with the thermal
fluid used and the working conditions.
-When choosing the thermal fluid, not only minimal and maximum
temperatures have to be complied with but also have to be suitable regarding
burn point, viscosity and / or freezing. Furthermore the thermal fluid has to be
compatible with all the materials used in the unit.
-Pressure changes with the length of hoses (keep as short as possible).
Choose as large a diameter of hoses as possible (the width of the pump
connections are considered as a point of reference) and may negatively affect
temperature control results. Flow restrictions may occur if a too narrow
connector is selected for corrugated hoses.
-The use of unsuitable hoses or hose connections may cause thermal and
toxic injury to personal and environment. Temperature control hoses and their
connections have to be insulated / secured against contact / mechanical
damage.
-Non-suitable thermal fluids can negatively affect temperature control and be
the cause of negative temperature results and damages. Therefore only use
the thermal fluids recommended by the manufacturer and only in the intended
temperature and pressure range. The application should be located on
approximately the same level or lower than the temperature control device, if
temperature control is to be carried out near to the boiling temperature of the
thermal fluid. The thermal fluid should have room temperature when filling.
Fill in the thermal fluid slowly, carefully and steadily. At the same time make
sure that no thermal fluid overflows (back pressure); it is thereby necessary
to wear personal protective equipment, e.g. safety goggles, thermally and
chemically resistant gloves, etc.
-After filling and setting all necessary parameters the thermoregulation circuit
has to be degassed. This is a requirement for proper operation of the device
and thus its application.
-In the case of pressure-sensitive applications, e.g. glass reactors, observe the
maximum inlet pressure of the temperature control device for cross section
reduction or shut-off (see data sheet). Take suitable precautions (e.g.
pressure limitation for temperature control devices with pressure control,
bypass).
-In order to avoid danger of overpressure in the system, which could damage
the temperature control device or the application, the thermal fluid must
always be adapted at room temperature before turning off and a possibly
available shut-off valve must be left open (pressure compensation).
-Temperature and dynamics within the reactor are determined by the outlet
temperature. A differential temperature is created (delta T) between outlet
temperature and the temperature within the reactor. This difference in

13
temperature has to be adapted, depending upon type of glass application. As
the differential temperature may exceed the admissible limit values and bursts
may occur. Delta T value has to be adapted to the corresponding application.
Therefore please see chapter Comfort menu.
-Do not kink the hoses.
-Check hoses in regular intervals for material fatigue (e.g. cracks).
With water cooled units please pay special attention to the maximum operating
temperature and differential pressure requirements for the cooling water. Therefore
please refer to the technical data sheet.
Danger!
If the cooling water contains high levels of minerals, e.g. chloride, bromide then suitable
water treatment chemicals should be used. Use only recommended materials to
maintain the unit warranty. Further information on corrosion, (appearance and
avoidance) can be found on our website www.huber-online.com under "Download /
Safety data sheets thermofluids / Characteristics of water".
Please refer to the sections on Intended use and general safety instructions.
Location
Caution!
-Transport the unit upright.
-The unit should be mounted in an upright and secure position, on a solid, stable
surface.
-Place on a non flammable surface.
-Keep the area around the unit clean, to avoid slip and trip hazards.
-Set the brakes on the castors once the unit is in position.
-Place suitable absorbent material under the unit to catch any condensate and
thermal fluid spills.
-Any spillage of thermal fluid should be immediately cleaned up.
-For large units, check the weight / load capacity for the flooring

14
Thermofluids
We recommend the thermal fluid shown in our catalogue. The name of a thermal fluid is
derived from the working temperature range and the viscosity at 25 °C.
Examples of thermal fluids in our catalogue:
M40.165.10:
•Lower working limit -40 °C
•Upper working limit 165 °C
•Viscosity at 25 °C: 10 mm2/s
The data sheet for the thermal fluid used is of utmost importance, and must be read
before use. This data sheet should be followed.
•Please note the classification of your machine according to DIN 12876
•The chosen thermal fluid must be compatible with stainless steel 1.4301 (V2A)
and FKM!
•The maximum viscosity of the thermal fluid may not exceed 50 mm²/s at the
lowest temperature reached!
•The maximum density of the thermal fluid may not exceed 1kg / dm³
•For chillers we recommend as thermal fluid a mixture of water and glycol (a
mixture is recommended that permits a temperature down to -25°C).
Information on water quality can be found on our website (www.huber-
online.com) under "Download / Safety data sheets thermofluids / Characteristics
of water".

15
Chapter 2 : Electronics and operation
The following sections are to be found in this chapter:
-Information displays and operation
-Advanced functionality

16
Display and operation
As a standard, internal temperature (e.g. temperature of the bath for thermoregulation
units and outlet temperature for chillers) is displayed. By pressing the SET-Key a
switchover to the actual set point temperature takes place. Keep the SET-Key pressed
to change of the set point. Via the two arrow-keys you may select the set point. To
START / STOP thermoregulation press the key ON / OFF. LEDs (Heating, Cooling and
Pump) give information on the actual operating status (e.g. Pump is working and
Cooling or Heating is on)
Advanced Functionality
Advanced Models contain, in comparison to standard models, of following possibilites:
1. Possibility of sensor relocation via an external sensor connection (Pt100)
2. An RS232 interface for controlling the machine.
Sensor relocation:
Keep the external Pt100 in a safe place!
A sensor relocation permits to control the temperature according to an external Pt100.
To activate this function, switch off the temperature control unit and connect the
external Pt100 to the designated Pt100 socket. Switch on the temperature control unit.
No switch over will take place (sensor relocation) when connecting the Pt100 if the
machine is operating. Please note, that within the internal and external sensor there is a
simple delta-T limit. This delta-T limit complies with the actual set point and the internal
sensor value. The internal sensor value lies always within a band of 5 K to the actual
set point.
RS232 interface:
Therefore, please see description on chapter 4.
Setting-Keys Set-Point Key On
/
Off
Display LEDs

17
Chapter 3: Connect the machine, fill and prepare fort he
required application
-Power connection
-Start up
-Connecting an externally closed application
-Switching on the temperature control unit
-Setting the over-temperature switch
-Setting set point limits
-Entering a set point
-Starting temperature control
-Ending temperature control
-Filling and air purging an externally closed application
-Draining an externally closed application
-Thermofluid change / internal cleaning

18
Power connection
. Danger!
Check to make sure that the line voltage matches the supply voltage specified on the
identification plate or data sheet.
We disclaim all liability for damage caused by incorrect line voltages!
Safety instructions
Start up
General
All models must be moved and installed in an upright position. Provide for a stable
installation and make sure that the thermostat cannot tilt. Ensure that sufficient fresh
air is available for the circulation pump and compressors at the installation site. The
warm exhaust air must be able to escape unhindered upwards.
Freezing protection (only valid for temperature control units with the option
freezing protection)
Temperature control devices (especially unichillers) with the option freezing protection
are capable of using water as thermal fluid. An additional freezing protection may be
activated for temperature control devices with the option freezing protection under the
main menu point Protection functions / Freezing protection to avoid critical situations
such as temperatures < 5°C at the internal heat exchanger and the risk of freezing of
the heat exchanger. A green flashing ice crystal indicates the activated freezing
protection under the main menu Display modes / Large display.
Danger! Only connect the unit to a power socket
with earthing contact (PE – protective earth)!
Caution! Do not move the unit from its location while
it is running.
Danger! Never operate equipment with damaged
mains power cables.

19
Water-cooling (valid for units with water cooling)
A cooling water controller is used in Huber tempering devices with water cooling, in
order to reduce the cooling water consumption. This only allows as much cooling water
to flow as is required by the current load situation of the tempering device. Only little
cooling water is consumed, if the required refrigerating capacity is low. No cooling
water flows in the OFF state. Only use pressure-resistant hoses in the cooling water
circuit.
Connection diagram:
water inlet water outlet
draining / water
Caution!
Depending upon mode of operation and available cooling water pressure, a cooling
water pressure of > 2 bar can build up in the cooling water supply line. In order to
avoid flooding of the premises, check the leak tightness and quality of the hoses, hose
connections in regular intervals, and if necessary take appropriate measures
(Replacement). Close down the cooling water supply to the tempering device even
during shorter shutdowns (e.g. over night).
Reinforced hoses must be used for increased safety requirements.
Preparation of devices with water-cooling:
Establish the hose connections for the cooling water. The filter screen has to be
inserted into the cooling water inlet. Please infer the position of the cooling water
connections from the connection diagram in the appendix. Cooling water connectors
Drainage with seal cap held closed and /or close. Open all stop valves. Please infer the
minimum / maximum differential pressure in the cooling water circuit and the
recommended cooling water inlet temperature from the data sheet.
Information on water quality can be found on our website (www.huber-online.com)
under "Download / Safety data sheets thermofluids / Characteristics of water".
This manual suits for next models
13
Table of contents
Popular Chiller manuals by other brands
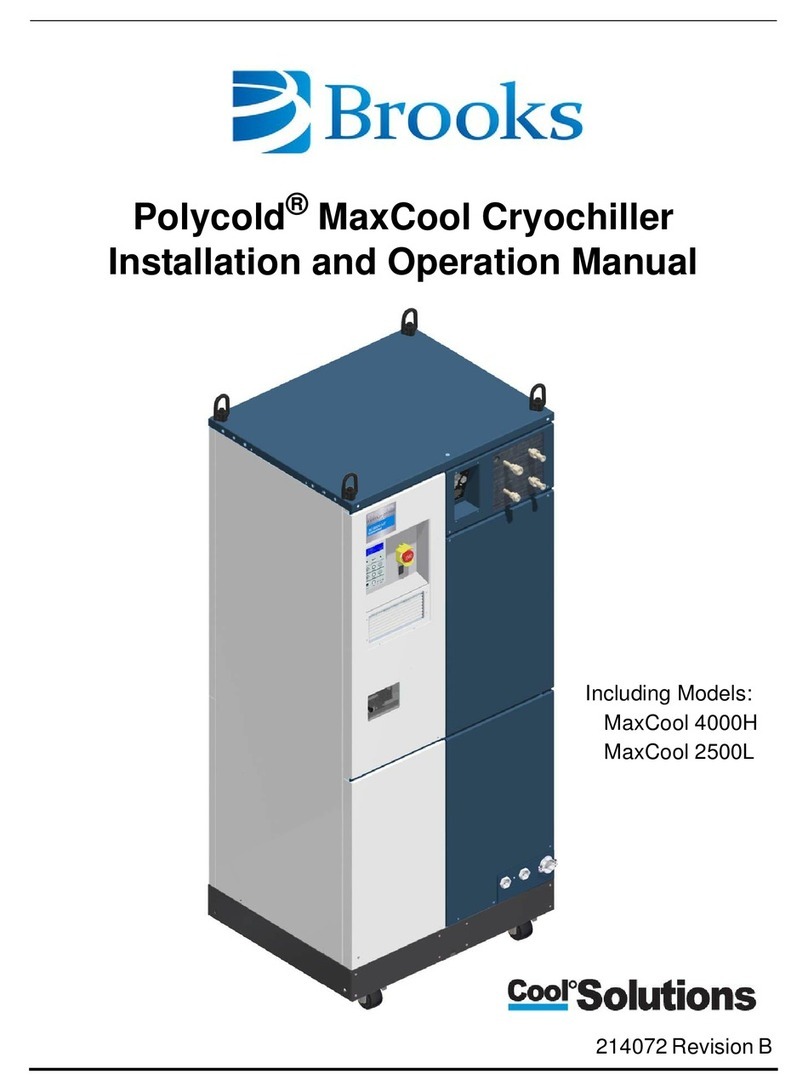
Brooks
Brooks Polycold MaxCool Series Installation and operation manual

Thermo Scientific
Thermo Scientific ThermoFlex900 Installation, operation and maintenance manual

Carrier
Carrier AquaEdge 19DV series Start-up, operation and maintenance instructions
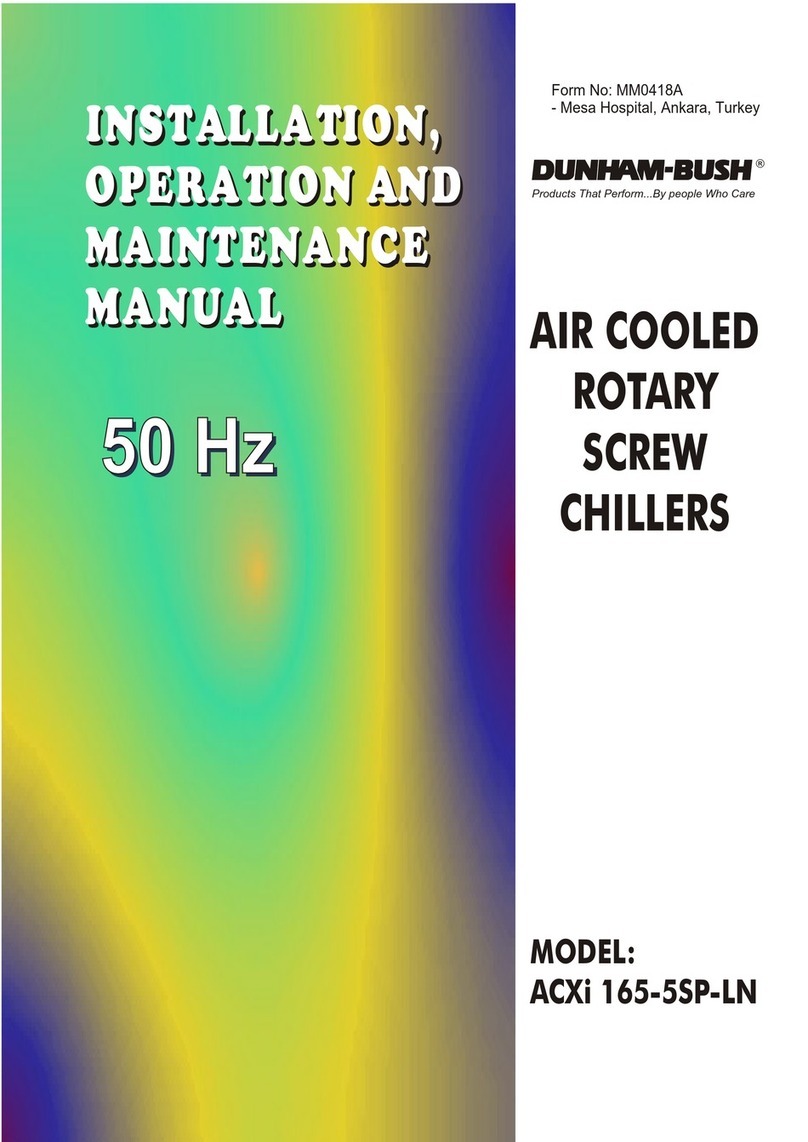
Dunham-Bush
Dunham-Bush ACXi 165-5SP-LN Installation, operation and maintenance manual

Cleveland
Cleveland P-TC-220 Specification sheet
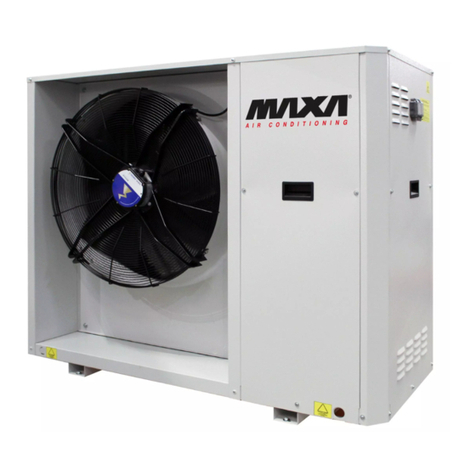
MAXA
MAXA i-32V5C MIDI 0121 installation manual