MrCool HVLS User manual

Please read this manual carefully before installation and keep it for future reference.
Please keep this manual where the operator can easily find it. Inside, you
will find helpful hints on how to use and maintain your unit properly.
For more info visit www.mrcool.com
Installation Manual
Cool Blade ~ Because We Blow More™
Industrial HVLS Fan

Contents
Page 1 mrcool.com
Safety Precautions .....................................................................................................2
Product Summary ......................................................................................................3
Installation Preparation ........................................................................................4
Installation - Transition Fittings ...................................................................... 6
Installation - Motor .................................................................................................... 7
Installation - Fan Blades ......................................................................................... 8
Installation - Arc Plates ........................................................................................... 9
Installation - Lock Wire Rope ..............................................................................10
Installation - Sling Wire Rope ..............................................................................11
Installation - Control Box .......................................................................................12
Control Box Summary ............................................................................................ 13
Fault Codes .....................................................................................................................14
!
1
2
3
4
5
6
7
8
9
10
11

Page 2
Safety Precautions
mrcool.com
Read Before Using
Incorrect usage may cause serious damage or injury.
The seriousness of potential damage or injuries is classified as either a WARNING or CAUTION.
WARNING
CAUTION
WARNING
• Read and follow these detailed rules carefully before installing or using this product. Failure to do so can
bring serious harm to yourself and others.
• Dedicated personnel must be assigned the responsibility for starting and stopping the fan and performing
scheduled maintenance.
• Before starting the fan, make sure that there are no persons or obstacles within the operating range of
the fan that could affect the operation of the product.
• After the power is turned off, the operator must wait for the fan blades to completely stop before leaving.
• Repair or automation adjustments can only be performed by a qualified installation engineer.
• During maintenance work, surround the area with a safety barrier that is 20 feet (6m) radius from the fan
center.
• Before performing maintenance, be sure to lock the fan controller and disconnect the power supply.
• Maintenance personnel is responsible for taking corresponding protective measures according to local
laws and regulations; necessary risk assessment should be performed and appropriate safety gear worn.
DO NOT perform any maintenance work when the fan is running or powered on.
DO NOT perform any maintenance work on the controller when it is powered on, except for
reprogramming or viewing error codes.
DO NOT store flammable or explosive materials in the vicinity of the fan controller to avoid danger.
DO NOT keep the control device within children’s reach to avoid accidental operation.
This symbol indicates that ignoring instructions may cause death or serious injury.
This symbol indicates that ignoring instructions may cause moderate injury
to your person, damage to your unit, or other property.
This symbol indicates that you should NEVER perform the indicated action.
!
Safety Precautions
CAUTION
• MRCOOL will not be responsible for any damage caused by incorrect use or when using not as specified.
• MRCOOL will not be responsible for the safety or operation of the automatic systems if alternate parts or
configurations are used.
• The installation engineer shall explain to the end user correct operating procedures and important
matters needing attention before use.

Installation Summary
Page 3 mrcool.com
1
Product Summary
• The unique blade design creates greater air volume than many other industrial fans with similar blade
diameter
• Quiet and efficient
• Minimal maintenance required
• Inexpensive operation
• Consumes less power than the average hair dryer
• Reduces “recovery time” when there is constant air flow throughout a space
• Provides a constant, even temperature throughout the space eliminating cold or hot spots
(From floor to ceiling and wall to wall)
• Minimizes the need for expensive duct work in new construction for both heating and cooling systems
• Increases productivity and decreases absenteeism by providing a comfortable workplace environment
INSTALLATION FLOW CHART
PRODUCT FEATURES
PREPARATION
ELECTRICAL
WIRING
WIRING +
COMMISSIONING
MATERIAL
INSPECTION
INSTALLING
TRANSITION
FITTINGS
INSTALLING
MOTOR
COMPONENTS
INSTALLING
LOCK
WIRE ROPES
INSTALLING
FAN
BLADES
INSTALLING
ARC BINDER
PLATES
INSTALLING
CONTROL
BOX
INSTALLING
SLING
WIRE ROPES
NOTE
Illustrations in this manual are for explanatory purposes only and are not drawn to scale.

Installation Preparation
Page 4mrcool.com
2
Assessment Of Installation Site
Prior to the installation of industrial fans, the project personnel must assess and communicate any civil construction or
installation conditions, ground facilities, locations of on-site power supplies, on-site voltage, wiring distances, and the
installation locations of control boxes and fans with installation engineers.
Parts Inspection
In order to ensure that the installation process goes smoothly, it is necessary for the project team to make an inventory of
provided materials in combination with a list of required tools (not included), while checking the quantity and quality of each one.
Part Name Quantity Looks Like Quality Requirement
Transition
Fittings
No bad spray-coating, paint
chips, severe scratches, etc.
No loosened fasteners
No shipping damage present
No bad aluminum alloys,
damaged plastic parts
1
1 Set
1 Set
1 Set
1 Set
1
1
5
Motor
Components
Fan Blade
Components
Locks & Tiger
Claw Package
Arc
Compression
Package
Installing Plate
Package
Set of Screws
Control Box
0

Installation Preparation
Page 5 mrcool.com
Preparation Of Tools And Equipment
Other Preparations
Standard Tools Standard Equipment
Specific tools and equipment are required to safely complete installation.
The project leader and installation engineer must assess staffing needs, work schedules, and the
estimated installation time in addition to the quantity and site of installations when preparing for
installation.
• Pistol drill
• Saw
• Screwdrivers
• Allen wrenches
• Other wrenches
• Sockets
• Scaffolds
• Forklift
• Crane
• Ladder Truck
• Other tools not listed
• Safety Belt
NOTE
Tools will need to be selected according to site requirements. Some sites may require the use of
tools and/or equipment not listed here.
CAUTION
The following pages in this manual illustrate the HVLS installation procedures. These steps must be
followed in sequential order to ensure safe and effective fan operation. A qualified engineer must use
the proper tools and equipment necessary to perform the fan installation.

Installation - Transition Fittings
Page 6mrcool.com
3
Transition
Fittings
Building
Structure
Hexagon Bolts
Installing The Binder Plate
Installing The Base Plate
Steel Structure of Building
Installing The Base
Hex Nuts
According to the diagram, install the transition
fitting on the steel I-beam, and then lock the
fastening screws to complete the installation.
NOTE
• Illustrations are for explanatory purposes only and are not drawn to scale.
• If you are installing the fan to a building structure other than I-Beam, you may need to purchase an
additional installation bracket. Examples requiring a separate installation kit include: Z-Purlins, Solid
Beam, and Angled I-Beam.
• Extensions brackets are available to drop the fan height lower. They are available in 20 inches (500mm),
32 inches (800mm), and 48 inches (1200mm) sizes.
After confirming the installation location and ensuring all parts,
tools, and equipment are received, the next step is installing the
transition fittings. The process could be different according to
your building structure.
I-Beam Installation
STEP 1

Installation - Motor 4
Page 7 mrcool.com
Motor
Components
After installing the transition fitting, attach
the motor component to the bottom plate
using hex nuts and hexagon screws. Tighten
the screws to complete installation.
Hexagon
Screws
Motor
Component
Transition
Fitting
Steel
Beam
Hex Nuts
After installing the transition fittings to the building structure,
the next step is to install the motor component. See the
following diagram that shows how to attach the motor
component using hex nuts and hexagon screws.
STEP 2

Page 8
mrcool.com
Refrigerant Piping Connection 5
Installation - Fan Blades
M10X100 Hexagon Screws and
Flat/Spring Washers
Fan Blade Components
Aluminum
Safety Plate
M10 Nuts
M10 Bolts
Aluminum Safety
Plate
Fan Blade
Components
Fan Base
According to the diagram, use the
aluminum fan base and safety plate to
clamp the fan blade components to
the middle position, and then pass
through the screws to secure them.
After installing the transition fittings and motor components, the next step is to install the fan blades.
Our HVLS Industrial fan includes aluminum safety plates that connect the blades to the fan chassis
forming a safe, stable, and secure design. See the following diagram that illustrates proper fan blade
alignment and installation.
STEP 3

Page 9 mrcool.com
Refrigerant Piping Connection 6
Installation - Arc Plate
Arc Plates
Bolts, Flat Washers, &
Spring Washers
Overlap the arc plates, lining up the holes for the bolts. Tighten
the bolts to lock the arc plate onto the safety plate.
M8 Bolts
Aluminum
Safety Plate
Arc
Plate
The Arc Plates are installed next to form an additional layer of protection to secure the fan blades to the
structure. This step helps to reduce vibration and noise. See the diagram below for proper alignment and
installation illustration.
STEP 4

Installation - Lock Wire Rope
Page 10mrcool.com
7
Wire Rope
Tiger Claw
According to the diagram,
wind the wire rope through
the steel-I-beam, and
secure it with the tiger claw
to lock it in place.
STEP 5
The next step in the installation process includes using the
provided wire rope to form an additional safety feature ensuring
the fan is secure in the event the fan becomes unsteady due to
natural disaster or building structural age. Use the supplied tiger
claws to secure the wire rope to the beam. See the diagram
below that illustrates proper rope placement.

Installation - Sling Wire Rope 8
Page 11 mrcool.com
Wire Rope 02 LockLock Catch
Tiger Claw
Install the wire rope, locks, tiger claws, and
lock catches according to the diagram below
C-Shaped
Purlines
Tiger
Claw
Wire
Rope
02 Lock
02 Lock
Lock
Catch
Lock
Catch
STEP 6
The next step in the installation process includes using the provided wire rope, locks, and tiger claws to
stabilize and secure the fan to the building structure. See the diagram below for proper placement using
the supplied fan parts identified below.

Page 12
mrcool.com
Refrigerant Piping Connection 9
Installation - Control Box
Attach the Control
Box to the wall
using the side
holes as seen in
this illustration
After the fan has been installed and secured
to the structure, the final step in the process
is to install the Honeywell Control Box to the
wall and wire it to the fan motor. Make sure
to choose a location that is not accessible to
children. The control box is used to operate
the HVLS fan, change the fan speed, or
change the direction of the fan blades. See
the diagrams below and the included
Honeywell User Manual for proper installation
and wiring procedures.
Please see the following connection
diagrams for power and control wiring.
Please refer to the Honeywell User
Manual for specific guidelines.
STEP 7
Connection Diagram
IP20 & IP66 Non°Switched Units
IP66 Switched Units
M
D
Key
AProtective Earth (PE) Connection
BIncoming Power Connection
CFuse / Circuit Breaker Selection
DOptional Input Choke
EOptional External EMC Filter
FInternal Disconnect / Isolator
GOptional Brake Resistor
HMotor Connection
IAnalog Output
JRelay Output
KUsing the REV/0/FWD Selector Switch
(Switched Version Only)
LAnalog Inputs
MDigital Inputs

Page 13 mrcool.com
Refrigerant Piping Connection 10
Control Box Summary
NAVIGATE
START
RESET/STOP
UP
DOWN
Used to display real-time
information, to access
and exit parameter edit
mode and to store
parameter changes.
Used to reset a
tripped drive.
When in Keypad
mode is used to Stop
a running drive.
When in keypad mode,
used to Start a stopped
drive or to reverse the
direction of rotation if
bi-directional keypad
mode is enabled.
Used to increase speed in
real-time mode or to
increase parameter values in
parameter edit mode.
Used to decrease speed in
real-time mode or to
decrease parameter values
in parameter edit mode.
Use the control box to operate the fan’s speed using the UP or DOWN keys on the control panel. Any
commissioning or fault codes will appear in the display window on the control panel.
Fan Rotation
The fan blades should rotate counterclockwise as viewed from below the fan. To maximize the energy savings
for supplemental heating and cooling systems, operate the fan year-round. The most effective method is listed
below.
Heating Season
Set the fan on the slowest speed setting to push the
hot air back down from the ceiling without causing a
draft. Additionally, lower your thermostat setting by a
few degrees to create a comfortable environment while
still saving energy costs.
Cooling Season
The fan speed can be adjusted to a higher setting to
provide a continuous breeze and constant air
movement. By increasing the thermostat’s setting by
2-7°and running the fan only when people are
present in the building, you can reduce energy costs.
0
NOTE
Please refer to chapter 5 in the Honeywell Control Box User Manual that is
included with your fan for detailed Control Box operation instructions.

Page 14
mrcool.com
Refrigerant Piping Connection 11
Control Panel Codes
Fault Code No. Description Suggested Remedy
00 No Fault Not required.
Check external brake resistor condition and connection wiring.
The drive has tripped to prevent damage to the brake resistor.
The drive has tripped after delivering >100% of value in P-08 for a period of time to
prevent damage to the motor.
Check the supply voltage is within the allowed tolerance for the drive. If the fault
occurs on deceleration or stopping, increase the deceleration time in P-04 or install
a suitable brake resistor and activate the dynamic braking function with P-34.
The incoming supply voltage is too low. This trip occurs routinely when power is
removed from the drive. If it occurs during running, check the incoming power
supply voltage and all components in the power feed line to the drive.
The drive is too hot. Check the ambient temperature around the drive is within the
drive specification. Ensure sufficient cooling air is free to circulate around the drive.
Trip occurs when ambient temperature is less than -10°C. Temperature must be
raised over -10°C in order to start the drive.
E-trip requested on digital input 3. Normally closed contact has opened for some
reason. If motor thermistor is connected check if the motor is too hot.
Check communication link between drive and external devices. Make sure each
drive in the network has its unique address.
Check incoming supply phases are all present and balanced.
Check incoming power supply phases are present and balanced.
Press the stop key. If the fault persists, consult you supplier.
Check the analog input connection(s).
Press the stop key. If the fault persists, consult you supplier.
Connected motor thermistor over temperature, check wiring connections and motor.
Check / replace the cooling fan.
Drive ambient temperature too high, check adequate cooling air is provided.
Indicates a fault on the output of the drive, such as one phase missing, motor phase
currents not balanced. Check the motor and connections.
The motor parameters measured through the autotune are not correct. Check the
motor cable and connections for continuity. Check all three phases of the motor are
present and balanced.
Check the incoming Modbus RTU connection cable.
Check that at least one register is being polled cyclically within the timeout limit set in
P-36 Index 3.
Check the incoming CAN connection cable. Check that cyclic communications take
place within the timeout limit set in P-36 Index 3.
Check for short circuits on the motor and connection cable.
NOTE Following a trip, the drive cannot be immediately reset. A delay time is inbuilt,
which allows the power components of the drive time to recover to avoid damage.
Instantaneous Over current on the drive output. Excess load or shock load on the
motor.
NOTE Following a trip, the drive cannot be immediately reset. A delay time is inbuilt,
which allows the power components of the drive time to recover to avoid damage.
Brake channel over current
Brake resistor overload
Output Over Current
Motor Thermal Overload (I2t)
Over voltage on DC bus
Under voltage on DC bus
Heatsink over temperature
Under temperature
Factory Default parameters loaded
External trip
Optibus comms loss
DC bus ripple too high
Input phase loss trip
Output Over Current
Faulty thermistor on heatsink
Internal memory fault (IO)
4-20mA Signal Lost
Internal memory fault (DSP)
Motor PTC thermistor trip
Cooling Fan Fault (IP66 only)
Drive internal temperature too high
Output Fault
Autotune Fault
Modbus comms loss fault
CAN comms loss trip
01
02
03
04
06
07
08
09
10
11
12
13
14
15
16
17
18
19
21
22
23
26
41
50
51
no-FLT
01-b
0l-br
0-1
1‒t-trP
0-volt
U-Volt
0-t
U-t
P-dEf
E-trip
SC-06s
FLt-dc
P-LOSS
h 0-1
th-Flt
dAtA-F
4-20 F
dAtA-E
F-Ptc
FAn-F
0-hEAt
OUt-F
AtF-02
SC-F01
SC-F02
Note: Following an over current or overload trip (3, 4, 5, 15), the drive may not be reset until the reset time delay has elapsed
to prevent damage to the drive.

The design and specifications of this product and/or manual are subject to change without prior notice.
Consult with the sales agency or manufacturer for details.
Cool Blade ~ Because We Blow More™
Industrial HVLS Fan
Table of contents
Other MrCool Fan manuals
Popular Fan manuals by other brands

CARNES
CARNES HXBG Installation, operation and maintenance manual
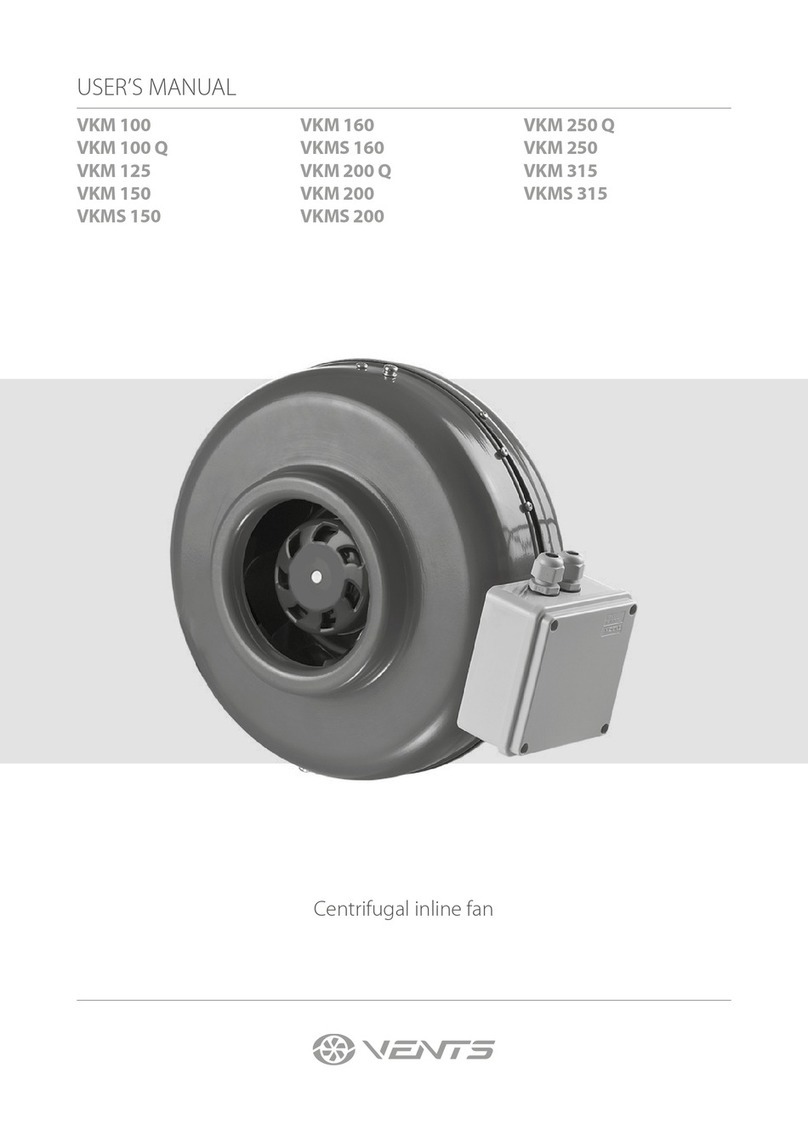
Vents
Vents VKM 100 user manual

Vectaire
Vectaire ELP2204 Installation and operating instructions
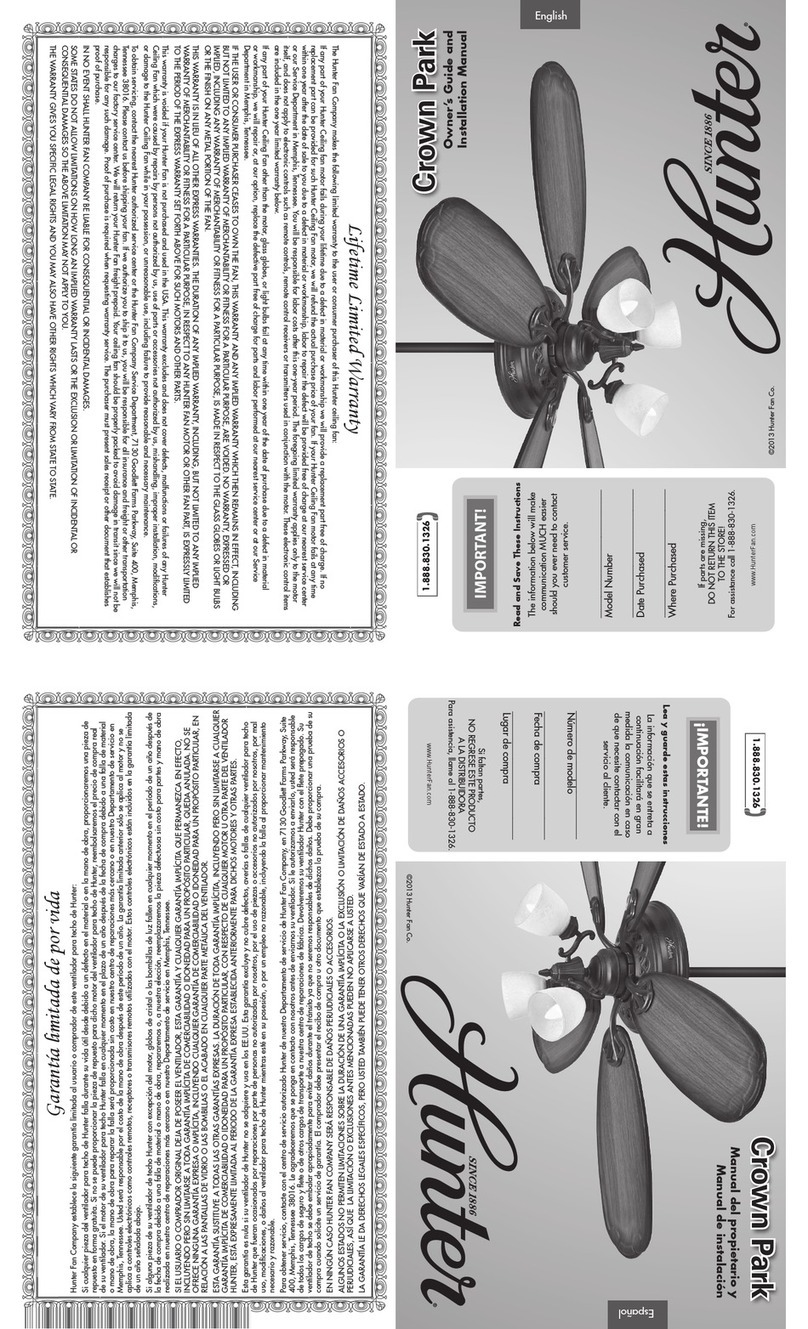
Hunter
Hunter Crown Park Owner's guide and installation manual
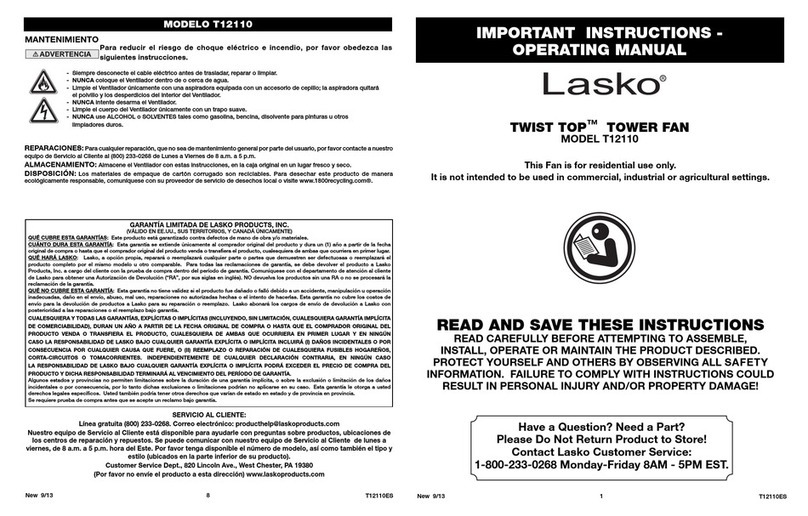
Lasko
Lasko TWIST TOP T12110 Important instructions & operating manual
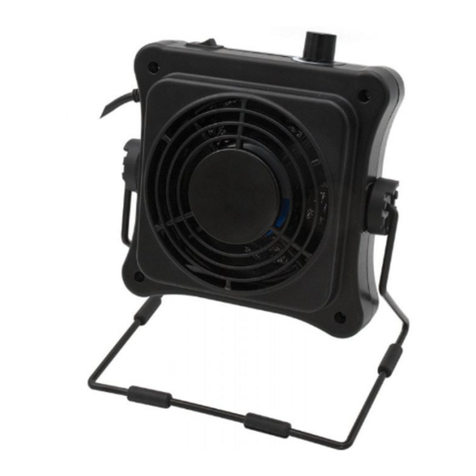
ELCART
ELCART 07/00708-00 user manual
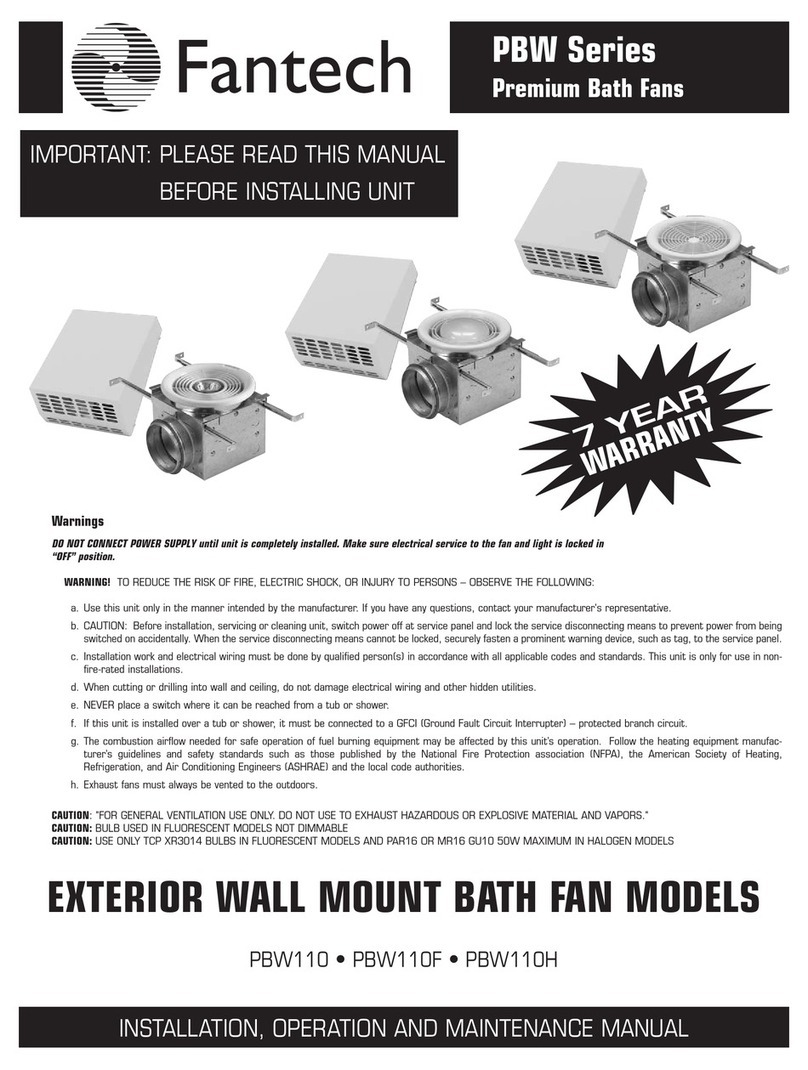
Fantech
Fantech PBW110 Installation, operation and maintenance manual

Siegenia
Siegenia AEROVITAL Original operating instructions

BLAUBERG
BLAUBERG TwinBox EC 150 user manual
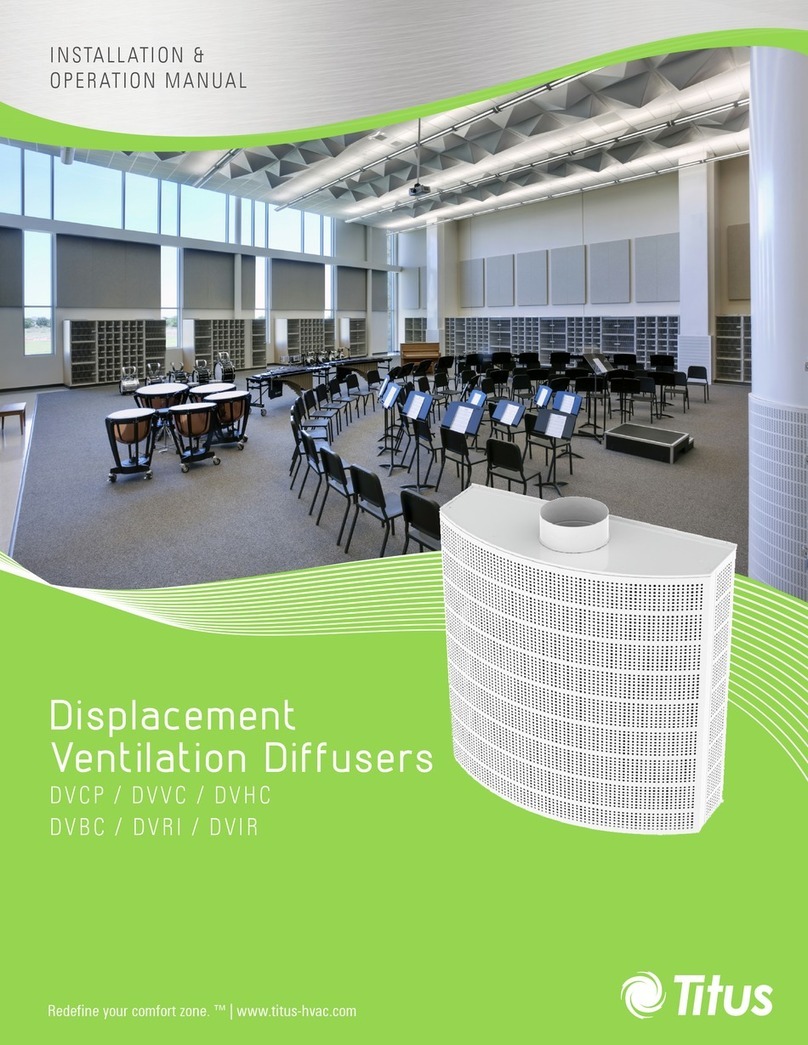
Titus
Titus DVCP Installation and operation manual
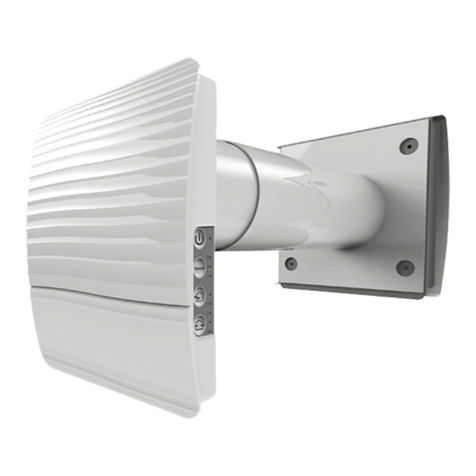
Vents
Vents TwinFresh Expert RW-30 V.2 user manual
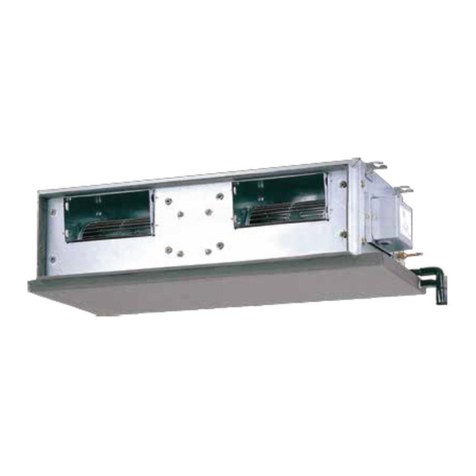
Daikin
Daikin C-Series installation manual