NAMICAM DC2000A User manual

CYCLONE
DUST COLLECTORS
2.5HP
1.75HP
DC2000A
DC3000A
Operator's Manual

SAFETY SYMBOLS
IMPORTANT! Safety is the single most important consideration in the operation of this equipment. The following
instructions must be followed at all times. Failure to follow all instructions listed below may result in electric shock,
re, and/or serious personal injury.
There are certain applications for which this tool was designed. We strongly recommend that this tool not be modied
and/or used for any other application other than that for which it was designed. If you have any questions about its
application, do not use the tool until you have contacted us and we have advised you.
SAFETY INSTRUCTIONS
GENERAL SAFETY
KNOW YOUR POWER TOOL. Read the owner’s manual
carefully. Learn the tool’s applications, work capabilities,
and its specic potential hazards.
BEFORE USING YOUR MACHINE
To avoid serious injury and damage to the tool, read and
follow all of the Safety and Operating Instructions before
operating the machine.
1. Some dust created by using power tools
contains chemicals known to the State of California to
cause cancer, birth defects, or other reproductive harm.
Some examples of these chemicals are:
• Lead from lead-based paints.
• Crystalline silica from bricks, cement, and other
• masonry products.
• Arsenic and chromium from chemically treated lumber.
Your risk from these exposures varies, depending on how
often you do this type of work. To reduce your exposure to
these chemicals: work in a well ventilated area and work
with approved safety equipment, such as those dust masks
that are specially designed to lter out microscopic
particles.
2. READ the entire Owner’s Manual. LEARN how to use
the tool for its intended applications.
3. GROUND ALL TOOLS. If the tool is supplied with a 3
prong plug, it must be plugged into a 3-contact electrical
receptacle. The 3rd prong is used to ground the tool and
provide protection against accidental electric shock. DO
NOT remove the 3rd prong. See Grounding Instructions
on the following pages.
4. AVOID A DANGEROUS WORKING ENVIRONMENT.
DO NOT use electrical tools in a damp environment or
expose them to rain.
5. DO NOT use electrical tools in the presence of
ammable liquids or gases.
6. ALWAYS keep the work area clean, well lit, and
organized. DO NOT work in an environment with oor
surfaces that are slippery from debris, grease, and wax.
7. KEEP VISITORS AND CHILDREN AWAY. DO NOT
permit people to be in the immediate work area,
especially when the electrical tool is operating.
8. DO NOT FORCE THE TOOL to perform an operation
for which it was not designed. It will do a safer and
higher quality job by only performing operations for
which the tool was intended.
9. WEAR PROPER CLOTHING. DO NOT wear loose
clothing, gloves, neckties, or jewelry. These items can
get caught in the machine during operations and pull the
operator into the moving parts. The user must wear a
protective cover on their hair, if the hair is long, to
prevent it from contacting any moving parts.
10. CHILDPROOF THE WORKSHOP AREA by
removing switch keys, unplugging tools from the
electrical receptacles, and using padlocks.
11. ALWAYS UNPLUG THE TOOL FROM THE
ELECTRICAL RECEPTACLE when making adjust-
ments, changing parts or performing any maintenance.
SAFETY ALERT SYMBOL: Indicates DANGER, WARNING, or CAUTION. This symbol may be used
in conjunction with other symbols or pictographs.
Indicates an imminently hazardous situation, which, if not avoided, could result in death or
serious injury.
Indicates a potentially hazardous situation, which, if not avoided, could result in death or serious
injury.
Indicates a potentially hazardous situation, which, if not avoided, could result in minor or
moderate injury.
NOTICE: Shown without Safety Alert Symbol indicates a situation that may result in property damage.
2

SAFETY INSTRUCTIONS
16. NEVER LEAVE A RUNNING TOOL UNATTENDED.
Turn the power switch to the “OFF” position. DO NOT
leave the tool until it has come to a complete stop.
17. DO NOT STAND ON A TOOL. Serious injury could
result if the tool tips over, or you accidentally contact the
tool.
18. DO NOT store anything above or near the tool where
anyone might try to stand on the tool to reach it.
19. MAINTAIN YOUR BALANCE. DO NOT extend
yourself over the tool. Wear oil resistant rubber soled
shoes. Keep oor clear of debris, grease, and wax.
20. MAINTAIN TOOLS WITH CARE. Always keep tools
clean and in good working order. Keep all blades and tool
bits sharp, dress grinding wheels and change other
abrasive accessories when worn.
21. EACH AND EVERY TIME, CHECK FOR DAMAGED
PARTS PRIOR TO USING THE TOOL. Carefully check
all guards to see that they operate properly, are not dam-
aged, and perform their intended functions. Check for
alignment, binding or breaking of moving parts. A guard
or other part that is damaged should be immediately
repaired or replaced.
22. DO NOT OPERATE TOOL WHILE TIRED, OR
UNDER THE INFLUENCE OF DRUGS, MEDICATION
OR ALCOHOL.
23. SECURE ALL WORK. Use clamps or jigs to secure
the work piece. This is safer than attempting to hold the
work piece with your hands.
24. STAY ALERT, WATCH WHAT YOU ARE DOING,
AND USE COMMON SENSE WHEN OPERATING A
POWER TOOL.
A moment of inattention while operating power tools may
result in serious personal injury.
25. ALWAYS WEAR A DUST MASK TO PREVENT
INHALING DANGEROUS DUST OR AIRBORNE
PARTICLES, including wood dust, crystalline silica dust
and asbestos dust. Direct particles away from face and
body. Always operate tool in well ventilated area and
provide for proper dust removal. Use dust collection
system wherever possible. Exposure to the dust may
cause serious and permanent respiratory or other injury,
including silicosis (a serious lung disease), cancer, and
death. Avoid breathing the dust, and avoid prolonged
contact with dust. Allowing dust to get into your mouth
or eyes, or lay on your skin may promote absorption of
harmful material. Always use properly fitting NIOSH/OSHA
approved respiratory protection appropriate for the dust
exposure, and wash exposed areas with soap and water.
26. USE A PROPER EXTENSION CORD IN GOOD
CONDITION. When using an extension cord, be sure to
use one heavy enough to carry the current your product
will draw. The table on the following page shows the cor-
rect size to use depending on cord length and nameplate
amperage rating. If in doubt, use the next heavier gauge.
The smaller the gauge number, the larger diameter of the
extension cord. If in doubt of the proper size of an exten-
sion cord, use a shorter and thicker cord. An undersized
cord will cause a drop in line voltage resulting in a loss of
power and overheating.
USE ONLY A 3-WIRE EXTENSION CORD THAT HAS A
3-PRONG GROUNDING PLUG AND A 3-POLE
RECEPTACLE THAT ACCEPTS THE TOOL’S PLUG.
27. SAVE THESE INSTRUCTIONS. Refer to them
frequently and use them to instruct others.
12. KEEP PROTECTIVE GUARDS IN PLACE AND IN
WORKING ORDER.
13. AVOID ACCIDENTAL STARTING. Make sure that
the power switch is in the “OFF” position before plugging
in the power cord to the electrical receptacle.
14. REMOVE ALL MAINTENANCE TOOLS from the
immediate area prior to turning “ON” the machine.
15. USE ONLY RECOMMENDED ACCESSORIES. Use
of incorrect or improper accessories could cause serious
injury to the operator and cause damage to the tool. If in
doubt, check the instruction manual that comes with that
particular accessory.
3

SAFETY INSTRUCTIONS - DC2000A
4
COVER
RAILS
THE USE OF AN EXTENSION CORD
WITH THIS MACHINE IS NOT RECOMMENDED. For
best power and safety, plug the machine directly into a
dedicated, grounded electrical outlet that is within the
supplied cord length of the machine.
If an extension cord needs to be used, it should only be
for a limited operation of the machine. The extension
cord should be as short as possible in length, and have
a minimum gauge size of 14AWG.
Check extension cords before each
use. If damaged replace immediately. Never use a tool
with a damaged cord, since touching the damaged
area could cause electrical shock, resulting in serious
injury.
Use a proper extension cord. Only use cords listed by
Underwriters Laboratories (UL). Other extension cords can
cause a drop in line voltage, resulting in a loss of power
and overheating of tool. When operating a power tool out-
doors, use an outdoor extension cord marked “W-A” or “W”.
These cords are rated for outdoor use and reduce the risk
of electric shock.
DO NOT MODIFY ANY PLUG. If it will not t the electrical
receptacle, have the proper electrical receptacle installed
by a qualied electrician.
IMPROPER ELECTRICAL CONNECTION of the
equipment grounding conductor can result in risk of
electric shock. The conductor with the green insulation
(with or without yellow stripes) is the equipment ground-
ing conductor. DO NOT connect the equipment grounding
conductor to a live terminal if repair or replacement
of the electric cord or plug is necessary.
CHECK with a qualied electrician or service personnel if
you do not completely understand the grounding
instructions, or if you are not sure the tool is properly
grounded when installing or replacing a plug.
USE ONLY A 3-WIRE EXTENSION CORD THAT HAS
THE PROPER TYPE OF A 3-PRONG GROUNDING PLUG
THAT MATCHES THE MACHINE’S 3-PRONG PLUG AND
ALSO THE 3-POLE RECEPTACLE THAT ACCEPTS THE
TOOL’S PLUG. *
REPLACE A DAMAGED OR WORN CORD
IMMEDIATELY.
This tool is intended for use on a circuit that has an
electrical receptacle as shown in FIGURE A. It shows a
3-wire electrical plug and electrical receptacle that has
a grounding conductor. If a properly grounded electrical
receptacle is not available, an adapter as shown in
FIGURE B can be used to temporarily
connect this plug to a 2-contact ungrounded
receptacle. The adapter has a rigid lug
extending from it that MUST be connected
to a permanent earth ground, such as a
properly grounded receptacle box.
THIS ADAPTER IS PROHIBITED IN
CANADA.
IN THE EVENT OF A MALFUNCTION OR BREAKDOWN,
grounding provides the path of least resistance for electric
current and reduces the risk of electric shock. This tool
is equipped with an electric cord that has an equipment
grounding conductor and requires a grounding plug (not
included). The plug MUST be plugged into a matching elec-
trical receptacle that is properly installed and grounded in
accordance with ALL local codes and ordinances.
THIS TOOL MUST BE GROUNDED
WHILE IN USE TO PROTECT THE OPERATOR FROM
ELECTRIC SHOCK.
EXTENSION CORDS
Keep the extension cord clear of
the working area. Position the cord so that it will not
get caught on lumber, tools or other obstructions while
you are working with your power tool.
* Canadian electrical codes require extension cords
to be certied SJT type or better.
** The use of an adapter in Canada is not acceptable.
FIG. B
FIG. A
ELECTRICAL SAFETY

SAFETY INSTRUCTIONS - DC3000A
5
EXTENSION CORDS
USE OF AN EXTENSION CORD
WITH THIS MACHINE IS NOT RECOMMENDED. FOR
BEST POWER AND SAFETY, PLUG THE MACHINE
DIRECTLY INTO A DEDICATED GROUNDED ELECTRI-
CAL OUTLET THAT IS WITHIN THE SUPPLIED CORD
LENGTH OF THE MACHINE.
IF AN EXTENSION CORD NEEDS TO BE USED, IT
SHOULD ONLY BE FOR LIMITED OPERATION OF THE
MACHINE. THE EXTENSION CORD SHOULD BE AS
SHORT AS POSSIBLE IN LENGTH, AND HAVE A
MINIMUM GAUGE SIZE OF 14AWG.
USE ONLY A 3-WIRE EXTENSION CORD THAT HAS
THE PROPER TYPE OF A 3-PRONG GROUNDING PLUG
THAT MATCHES THE MACHINE'S 3-PRONG PLUG AND
ALSO THE 3-POLE RECEPTACLE THAT ACCEPTS THE
TOOL’S PLUG.
Check extension cords before each
use. If damaged replace immediately. Never use a tool
with a damaged cord, since touching the damaged
area could cause electrical shock, resulting in serious
injury.
Use a proper extension cord. Only use cords listed by
Underwriters Laboratories (UL). Other extension cords can
cause a drop in line voltage, resulting in a loss of power
and overheating of tool. When operating a power tool out-
doors, use an outdoor extension cord marked “W-A” or “W”.
These cords are rated for outdoor use and reduce the risk
of electric shock.
Keep the extension cord clear of
the working area. Position the cord so that it will not
get caught on lumber, tools or other obstructions while
you are working with a power tool.
DO NOT MODIFY ANY PLUG. If it will not t the electrical
receptacle, have the proper electrical receptacle installed
by a qualied electrician.
REPLACE A DAMAGED OR WORN CORD OR PLUG
IMMEDIATELY.
IMPROPER ELECTRICAL CONNECTION of the
equipment grounding conductor can result in risk of
electric shock. The conductor with the green insulation
(with or without yellow stripes) is the equipment grounding
conductor. DO NOT connect the equipment grounding
conductor to a live terminal if repair or replacement of the
electric cord or plug is necessary.
CHECK with a qualied electrician or service personnel if
you do not completely understand the grounding
instructions, or if you are not sure the tool is properly
grounded when installing or replacing a plug.
This tool is intended for use on a circuit that has a 230
volt electrical receptacle. FIGURE A shows the type of the
230V, 3-wire electrical plug and electrical receptacle that
has a grounding conductor that is required.
* Canadian electrical codes require extension cords to
be certied SJT type or better.
** The use of an adapter in Canada is not acceptable.
IN THE EVENT OF A MALFUNCTION OR BREAKDOWN,
grounding provides the path of least resistance for electric
current and reduces the risk of electric shock. This tool
is equipped with an electric cord that has an equipment
grounding conductor and requires a grounding plug (not
included). The plug MUST be plugged into a matching
electrical receptacle that is properly installed and grounded
in accordance with ALL local codes and ordinances.
ELECTRICAL SAFETY
THIS TOOL REQUIRES THE USE OF
A 230V PLUG (NOT INCLUDED), AND MUST BE
GROUNDED WHILE IN USE TO PROTECT THE
OPERATOR FROM ELECTRIC SHOCK.
Sample of 230 volt plug required for this machine.
Consult a qualied
electrician if the
distance of the
machine from the
electrical panel is
greater than 30 feet.
FIG. A

6
SPECIFIC SAFETY INSTRUCTIONS FOR DUST COLLECTORS
SAFETY INSTRUCTIONS
This machine is intended for the collection of chips, shavings and dust from the surfacing, cutting and sanding
of natural wood, plywood, plastics and other man-made wood based composites. It is for collecting DRY
materials only. Any other use not as specified, including modification of the machine or use of parts not tested
and approved by the equipment manufacturer, can cause unforeseen damage and invalidate the warranty.
ATTENTION: Use of this dust collector still presents risks that cannot be eliminated by the manufacturer.
Therefore, the user must be aware that wood working machines are dangerous if not used with care and all
safety precautions are adhered to.
This owner’s manual is not a teaching aid and is intended to show
assembly, adjustments, and general use.
1. Do not operate this machine until you have read all of the following instructions.
2. Do not attempt to operate this machine until it is completely assembled.
3. Do not turn ON this machine if any pieces are missing or damaged.
4. If you are not familiar with the operation of the machine, obtain assistance from a qualied person.
5. It is highly recommended that this machine be placed on a sturdy vertical surface.
6. This machine must be properly grounded.
7. Always wear approved protective eye, hearing and respiratory protection when operating this machine.
8. Always make sure the power switch is in the OFF position prior to plugging in the machine.
9. Always make sure the power switch is in the OFF position and the machine is unplugged when doing
any cleaning, assembly, setup operations, or when not in use.
10. DO NOT use the dust collector for collecting liquids, substances impregnated with liquids, metals,
gasoline or potentially flammable or combustible substances.
11. DO NOT use the dust collector to dissipate fumes or smoke. NEVER pick up any material that is
burning or smoking, such as cigarettes, matches or hot ashes.
12. DO NOT use the dust collector without a filter cansiter and dust collector bag securely in place.
13. DO NOT use the dust collector with unused intake ports uncapped. Always cover exposed intake ports.
14. Always wear a dust mask when cleaning or working near a dust collector.
15. Make sure all machine parts, hose connections and bags are securely tightened before operating the
machine. Periodically check bags and hoses for rips or tears. If present, repair or replace immediately.
16. The use of any accessories or attachments not recommended may cause injury to you and damage
your machine.
17. Never reach inside of a running machine. Always keep your hands, body parts and clothing clear of
openings and moving parts such as impellers, fans and hose intake openings.
18. Do not clear any hose blockage while the machine is running. Stop the machine, unplug it from the
power source, and then remove the blockage in the hose.
19. Do not expose the machine to rain or use in damp locations.
20. Keep these instructions for future reference.
CALIFORNIA PROPOSITION 65 WARNING
WARNING: Drilling, sawing, sanding or machining wood products can expose you to wood dust, a
substance known to the State of California to cause cancer. Avoid inhaling wood dust or use a dust mask
or other safeguards for personal protection. For more information go to www.P65Warnings.ca.gov/wood

7
DUST HAZARDS AND SAFETY
GROUNDING THE DUCT WORK
NOTE: For permanent dust collector set-ups, the following instructions are recommended. For the occasional
use of any dust collector, care must none-the-less be taken to keep the hose and bag clean.
The duct
To properly ground plastic duct work, simply run a small gauge bare copper wire through the ducting and have
it emerge from the hose at the dust collector and at each dust producing machine. The bare copper wire should
be bonded to the metal shell of each machine by means of a metal screw. The screw must be threaded into the
metal shell to ensure a good connection.
The grounding of metal duct work is similar
wire inside the ducting. It can be wrapped along the out side of the ducting and should be bonded to each
machine as described above.
EMPTYING & CLEANING THE DUST COLLECTOR
CAUTION: Make sure the dust collector is unplugged before cleaning or servicing.
Always wear a dust mask or respirator while emptying the collector bags or cleaning the dust collector. Please
refer to the California Proposition 65 warning on page 7 of this manual regarding hazards from exposure to
wood dust. For more detailed information visit www.P65Warnings.ca.gov/wood.
WIRING DIAGRAM

TROUBLESHOOTING
PROBLEM POSSIBLE CAUSE SOLUTION
Reduction of
dust collection
suction power
Loud or unusual
noises from
motor or fan
1. Malfunction of the lter cleaning system.
2. Plugged hose lines.
3. Retaining of dust in the collector due to low
density.
4. Wetting of lter.
5. Filter is dirty or permeability of the cloth
has increased.
1. Check all system components.
2. Check and clean inlets and hoses for
obstructions.
3. Clean or replace lter and check all
connections for leakage.
4. Control intake of moisture. Dry wet lter.
5. Clean or replace lter.
1. Motor, fan housing, base or parts of the
frame are loose.
2. Impeller fan is rubbing the housing.
3. Motor bearings are loud.
4. Impeller fan is loose, unbalanced, or
damaged.
1. Inspect and tighten all parts or replace as
needed.
2. Check position of the fan and adjust or
replace any loose/damaged parts.
3. Replace worn bearings.
4. Secure fan on motor shaft, and replace if
any damage is found.
1. Incorrect line voltage.
2. Motor capacitor has failed.
3. Extension cord is being used.
4. Impeller is clogged with debris.
1. Restricted air ow due to dirty lter or
blockage in the hoses.
2. Motor overloaded.
3. Extension cord is used.
4. Machine used for extended time.
5. Poor air ow in work area.
1. Have qualied electrician check circuit
for proper line voltage.
2. Replace motor capacitor.
3. Do not use an extension cord. Plug the
collector directly into an outlet.
4. Clean debris from blocked impeller.
1. Clean lter and hoses for maximum air
ow through the system.
2. Reduce load on the motor.
3. Do not use an extension cord. Plug the
collector directly into an outlet.
4. Reduce run time of machine.
5. Reposition machine for better air ow.
Motor stalls or
does not have
full power
Motor runs hot
Motor does not
start
1. Machine not plugged in.
2. Power switch in ‘OFF’ position.
3. Power switch or cord is faulty.
4. Fuse or circuit breaker are open.
5. Low line voltage.
6. Defective motor capacitor.
7. Motor does not work.
1. Plug cord into electrical outlet.
2. Lift switch to ‘ON’ position. The safety
key must be in place. See page 11.
3. Replace switch or cord.
4. Correct overloaded electrical circuit.
5. Correct low line voltage condition.
6. Replace motor capacitor.
7. Repair or replace the motor.
ACCESSORIES
CLEAR PLASTIC BAGS - PACK OF 5 EACH
60-910 Dust Bucket Bag for RIKON 60-1750
60-911 Filter Element Plastic Bag for 60-1750
60-913 Dust Bucket Bag for RIKON 60-2500
60-912 Filter Element Plastic Bag for 60-2500
To order replacement parts or accessories for the
Cyclone Dust Collectors or other RIKON machines,
contact your local RIKON Distributor, or visit the
RIKON website at www.rikontools.com.
8

9
NOTES
Use this section to record maintenance, service and any calls to Technical Support:
MAINTENANCE
Turn the power switch “OFF” and disconnect the plug from the outlet prior to adjusting or maintaining
the machine. DO NOT attempt to repair or maintain the electrical components of the motor. Contact a qualied service
technician for this type of maintenance.
3. Check the duct work and hoses to make sure that
there are no loose connections. Making sure that they
are in proper operating condition will ensure that the dust
collection will be the best possible.
4. Clean the filtering canister on a regular basis to pre-
vent the build-up of dust for better dust collection and air
filtration. Check for abrasion, tears or damage.
WARNING: Always wear a dust mask or respirator while
emptying the collector bags or cleaning the dust collec-
tor. Please refer to the California Proposition 65 warning
on page 6 of this manual regarding hazards from expo-
sure to wood dust. For more detailed information visit
www.P65Warnings.ca.gov/wood or www.oehha.ca.gov.
5. The motor does not need any maintenance as it is
equipped with sealed, lubricated ball bearings.
1. Before each use:
- Check the power cord and plug for any wear or
damage.
- Check for any loose screws or hardware.
- Check the area to make sure it is clear of any misplaced
tools, lumber, cleaning supplies, etc. that could hamper
the safe operation of the machines being used.
2. To avoid a build-up of wood dust, regularly clean all
parts of your machines using a soft cloth, brush or com-
pressed air. A general cleaning should be done after every
use to avoid future problems and ensure the machines
are in ready condition for the next time that they are used.
WARNING: If blowing sawdust, wear proper eye protec-
tion to prevent debris from blowing into eyes.

DC2000APARTS DIAGRAM A
1
2
3
4
5
6
7
9
8
10
11
12
13
14 15
16
17
18
19
202122
23
24
25
26
27
28
29
31
33
35
30
34
36
37
38
39
45
41
42
43
46
40
44
NOTE: Please reference the
Part Number when calling for
Replacement Parts.
For Parts under Warranty, the Serial
Number of your machine is required.
10

DC2000A PARTS LIST A
1
2
3
4
5
6
7
8
9
10
11
12
13
14
15
16
17
18
19
20
21
22
23
24
25
26
27
28
29
30
31
32
33
34
35
36
37
38
39
40
41
42
43
44
45
46
Dust Plenum
Cyclonic Separator
Hex lock nut M6
Hex socket at round hd screw M6X16
Inlet
Muti-Way Connector cover
Collection Drum Cover
Steel ring
Cross recessed pan head screw M5X8
Vertical column
Base plate brace
Collection Drum
Cap nut M8
Spring washer 8
Handle
Hex socket head cap screw M8X30
Clear window
Caster wheel
Hex nut M8
Hose clamps
Pipe
Big washer 8
Compression spring
Threaded rod
Plate
Hex socket countersunk hd scr M6X16
Separator Funnel
Hex lock nut M8
Flat washer 8
Hex socket head cap screw M8X25
Handle
Flat washer 4
Handle sleeve
Hex ange nut M8
Right Support Panel
Left Support Panel
Handle
Hex socket head cap screw M8X30
Flat head hex rivet nut M6X15
Switch box assembly
Washer 5
Spring washer 4
Cross recessed pan hd screw M4X12
Hex head ange bolt M8X16
Panel Cross Brace
End cap
1
1
3
3
1
1
1
4
20
4
2
1
6
2
1
2
3
4
8
2
1
4
2
2
2
2
1
2
6
2
2
1
2
10
1
1
2
4
4
1
1
1
1
26
1
4
QTY.
PART
NO.
DESCRIPTION
KEY
NO.
P60-1750-1A
P60-1750-2A
P60-1750-3A
P60-1750-4A
P60-1750-5A
P60-1750-6A
P60-1750-7A
P60-1750-8A
P60-1750-9A
P60-1750-10A
P60-1750-11A
P60-1750-12A
P60-1750-13A
P60-1750-14A
P60-1750-15A
P60-1750-16A
P60-1750-17A
P60-1750-18A
P60-1750-19A
P60-1750-20A
P60-1750-21A
P60-1750-22A
P60-1750-23A
P60-1750-24A
P60-1750-25A
P60-1750-26A
P60-1750-27A
P60-1750-28A
P60-1750-29A
P60-1750-30A
P60-1750-31A
P60-1750-32A
P60-1750-33A
P60-1750-34A
P60-1750-35A
P60-1750-36A
P60-1750-37A
P60-1750-38A
P60-1750-39A
P60-1750-40A
P60-1750-41A
P60-1750-42A
P60-1750-43A
P60-1750-44A
P60-1750-45A
P60-1750-46A
11

DC2000A PARTS DIAGRAM B
1
6
5
2
3
4
7
8
11
10
9
12
NOTE: Please reference the
Part Number when calling for
Replacement Parts.
For Parts under Warranty, the Serial
Number of your machine is required.
12

DC2000A PARTS LIST B
1
2
3
4
5
6
7
8
9
10
11
12
Cap nut M10
Motor
Hex head ange bolt M8X16
Motor mounting plate
Flat washer 10
Spring washer 10
Hex headed bolt M10X30
Impeller
Big washer 8
Spring washer 8
Hex headed bolt M8X25
Hex socket at end set screw M8X12
4
1
6
1
4
4
4
1
1
1
1
1
QTY.
PART
NO.
DESCRIPTION
KEY
NO.
P60-1750-1B
P60-1750-2B
P60-1750-3B
P60-1750-4B
P60-1750-5B
P60-1750-6B
P60-1750-7B
P60-1750-8B
P60-1750-9B
P60-1750-10B
P60-1750-11B
P60-1750-12B
NOTE: Please reference the
Part Number when calling for
Replacement Parts.
For Parts under Warranty, the Serial
Number of your machine is required.
13

DC2000A PARTS DIAGRAM C
1
2
3
4
5
6
7
8
9
10
11
12
13
14
15
17
18
19
21
22
23
24
25
27
26
28
29
20
16
NOTE: Please reference the
Part Number when calling for
Replacement Parts.
For Parts under Warranty, the Serial
Number of your machine is required.
14

DC2000A PARTS LIST C
1
2
3
4
5
6
7
8
9
10
11
12
13
14
15
16
17
18
19
20
21
22
23
24
25
26
27
28
29
Filter cartridge
Filter cartridge shield
Hex head ange bolt M8X16
Hex lock nut M6
Spring clip
Hex socket at round hd screw M6X12
Handle
Clamping assembly
Hex socket at end set screw M6X10
Hex socket at round hd screw M6X16
Positioning sleeve
Rotation shaft
Shaft sleeve
Hex socket head cap screw M6X20
Guide sleeve
Circlip
Spring washer 6
Big washer 6
Gear
Flat washer 6
Lower support plate
Washer
Sleeve gasket
Bearing
Dust remove shaft
Dust remove plate
Dust remove bracket
Upper xing plate
Cross recessed pan head tapping screw
1
1
8
15
3
4
1
1
1
12
1
1
1
6
1
1
6
3
2
4
1
1
2
1
1
2
4
1
2
QTY.
PART
NO.
DESCRIPTION
KEY
NO.
P60-1750-1C
P60-1750-2C
P60-1750-3C
P60-1750-4C
P60-1750-5C
P60-1750-6C
P60-1750-7C
P60-1750-8C
P60-1750-9C
P60-1750-10C
P60-1750-11C
P60-1750-12C
P60-1750-13C
P60-1750-14C
P60-1750-15C
P60-1750-16C
P60-1750-17C
P60-1750-18C
P60-1750-19C
P60-1750-20C
P60-1750-21C
P60-1750-22C
P60-1750-23C
P60-1750-24C
P60-1750-25C
P60-1750-26C
P60-1750-27C
P60-1750-28C
P60-1750-29C
NOTE: Please reference the
Part Number when calling for
Replacement Parts.
For Parts under Warranty, the Serial
Number of your machine is required.
15

DC2000A PARTS DIAGRAM D
1
2
3
4
DC2000A PARTS LIST D
1
2
3
4
Base bracket
Hex socket at round hd screw M6X16
Caster wheel
Hex ange nut M6
1
16
4
16
QTY.
PART
NO.
DESCRIPTION
KEY
NO.
P60-1750-1D
P60-1750-2D
P60-1750-3D
P60-1750-4D
NOTE: Please reference the
Part Number when calling for
Replacement Parts.
For Parts under Warranty, the Serial
Number of your machine is required.
16

DC2000A NOTES
Use this section to record maintenance, service and any calls to Technical Support:
17

DC3000A PARTS DIAGRAM A
1
2
3
4
5
6
7
9
8
10
11
12
13
14 15
16
17
18
19
202122
23
24
25
26
27
28
29
31
33
35
30
34
36
37
38
39
45
41
42
43
46
40
44
NOTE: Please reference the
Part Number when calling for
Replacement Parts.
For Parts under Warranty, the Serial
Number of your machine is required.
18

DC3000A PARTS LIST A
1
2
3
4
5
6
7
8
9
10
11
12
13
14
15
16
17
18
19
20
21
22
23
24
25
26
27
28
29
30
31
32
33
34
35
36
37
38
39
40
41
42
43
44
45
46
Dust Plenum
Cyclonic Separator
Hex lock nut M6
Hex socket at round hd screw M6X16
Inlet
Muti-Way Connector cover
Collection Drum Cover
Steel ring
Cross recessed pan head screw M5X8
Vertical column
Base plate brace
Collection Drum
Cap nut M8
Spring washer 8
Handle
Hex socket head cap screw M8X30
Clear window
Caster wheel
Hex nut M8
Hose clamps
Pipe
Big washer 8
Compression spring
Threaded rod
Plate
Hex socket countersunk hd scr M6X16
Separator Funnel
Hex lock nut M8
Flat washer 8
Hex socket head cap screw M8X25
Handle
Flat washer 4
Handle sleeve
Hex ange nut M8
Right Support Panel
Left Support Panel
Handle
Hex socket head cap screw M8X30
Flat head hex rivet nut M6X15
Switch box assembly
Washer 5
Spring washer 4
Cross recessed pan hd screw M4X12
Hex head ange bolt M8X16
Panel Cross Brace
End cap
1
1
3
3
1
1
1
4
20
4
2
1
6
2
1
2
3
4
8
2
1
4
2
2
2
2
1
2
6
2
2
1
2
10
1
1
2
4
4
1
1
1
1
26
1
4
QTY.
PART
NO.
DESCRIPTION
KEY
NO.
P60-2500-1A
P60-2500-2A
P60-2500-3A
P60-2500-4A
P60-2500-5A
P60-2500-6A
P60-2500-7A
P60-2500-8A
P60-2500-9A
P60-2500-10A
P60-2500-11A
P60-2500-12A
P60-2500-13A
P60-2500-14A
P60-2500-15A
P60-2500-16A
P60-2500-17A
P60-2500-18A
P60-2500-19A
P60-2500-20A
P60-2500-21A
P60-2500-22A
P60-2500-23A
P60-2500-24A
P60-2500-25A
P60-2500-26A
P60-2500-27A
P60-2500-28A
P60-2500-29A
P60-2500-30A
P60-2500-31A
P60-2500-32A
P60-2500-33A
P60-2500-34A
P60-2500-35A
P60-2500-36A
P60-2500-37A
P60-2500-38A
P60-2500-39A
P60-2500-40A
P60-2500-41A
P60-2500-42A
P60-2500-43A
P60-2500-44A
P60-2500-45A
P60-2500-46A
19

DC3000A PARTS DIAGRAM B
1
2
3
4
5
6
7
8
11
10
9
12
NOTE: Please reference the
Part Number when calling for
Replacement Parts.
For Parts under Warranty, the Serial
Number of your machine is required.
20
This manual suits for next models
1
Table of contents
Popular Dust Collector manuals by other brands

RoboVent
RoboVent VentBoss 300 Series owner's manual
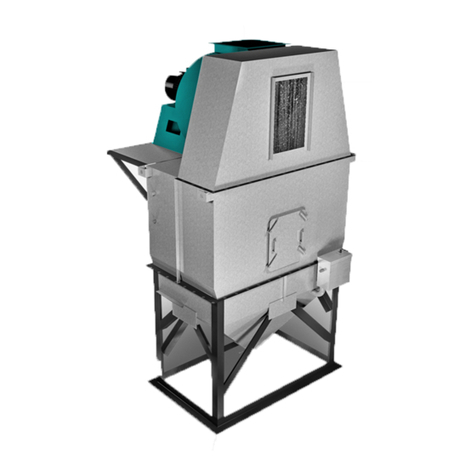
DIVERSITECH
DIVERSITECH Typhoon TY-8000 Operation & maintenance manual
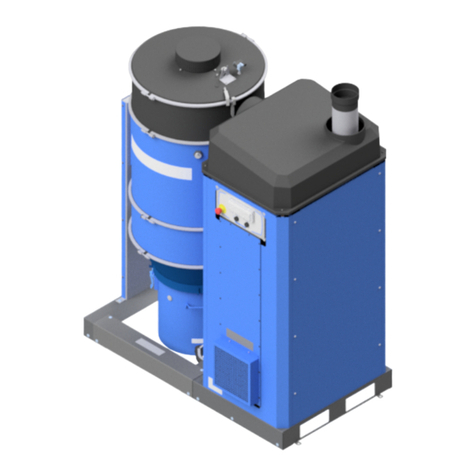
Nederman
Nederman FlexPAK Standard Installation and service manual
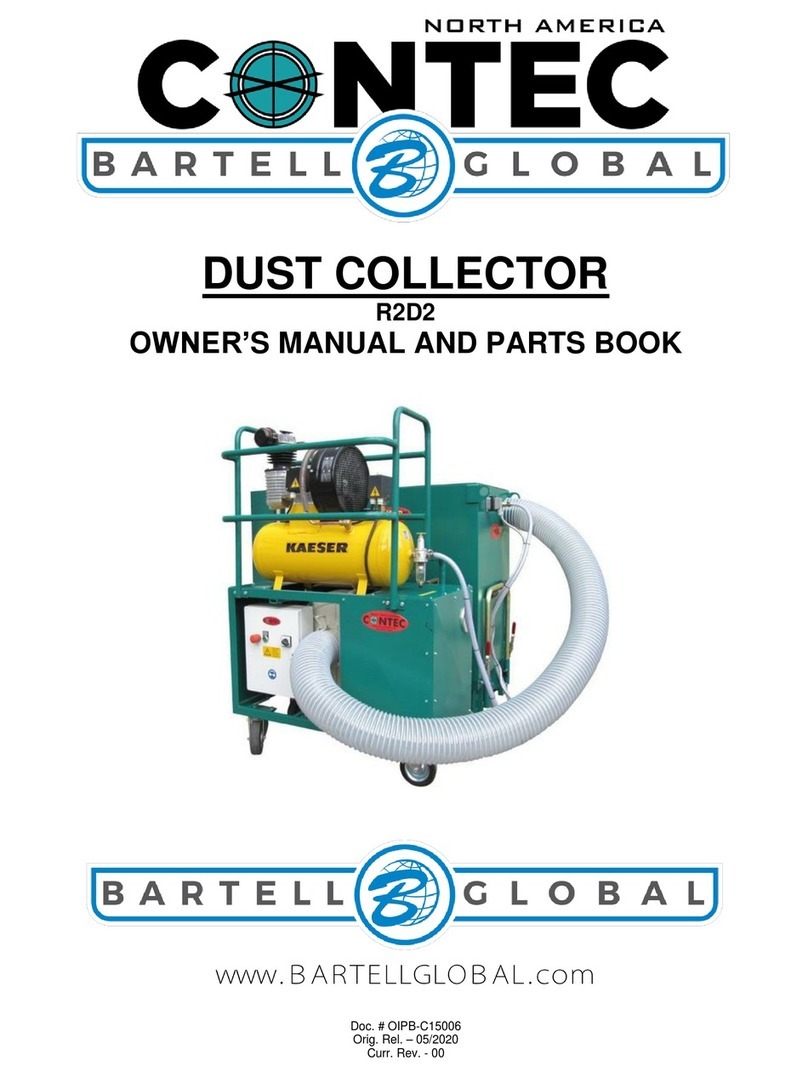
Bartell
Bartell CONTEC KAESER R2D2 Owner's manual and parts book

King Industrial
King Industrial KC-8500C instruction manual
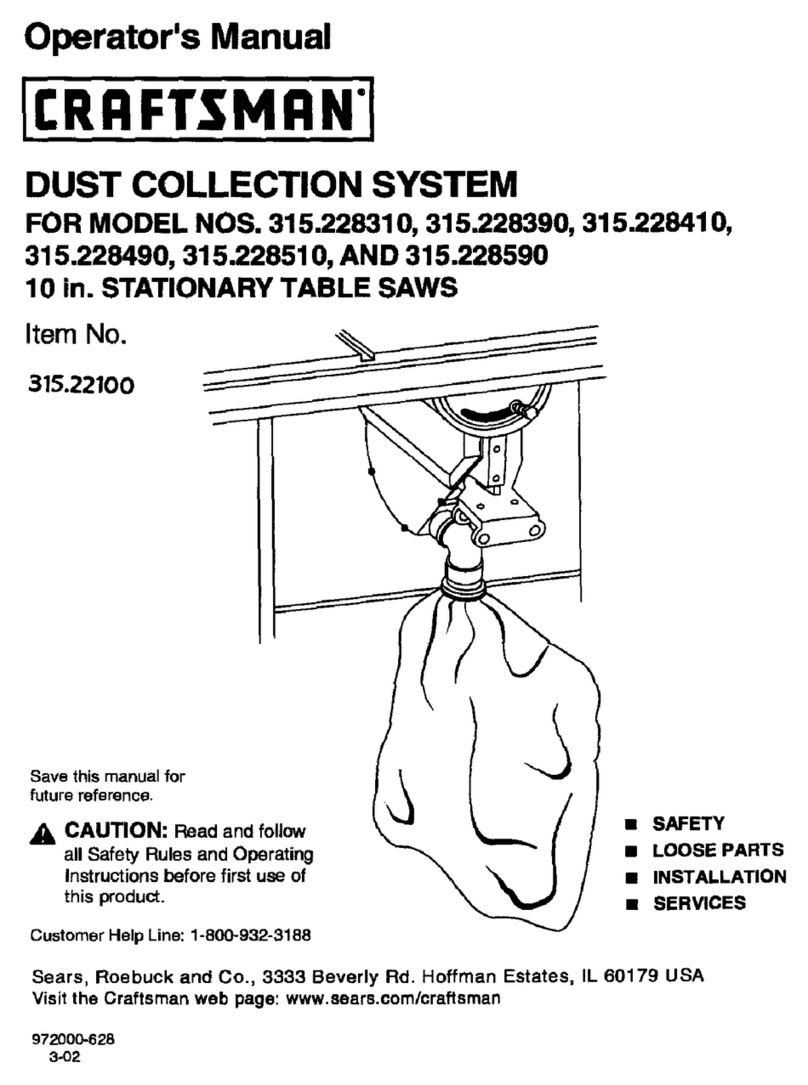
Craftsman
Craftsman 315.22100 Operator's manual