NANO GEN2-1110 User manual

GEN2
NITROGEN GENERATOR
USER GUIDE

1. General information 3
1.1. Document introduction 3
1.2. Support and Manufacturers details 3
1.3. Warranty Guidelines 3
Contents Page
2. General safety 4
2.1. Intended Use 4
2.2. Personnel 4
2.3. Safe Handling 4
3. Product Description 5
3.1. TechnicalSpecication 5
4. Product Contents 6
4.1. Packaging 6
4.2. Unpackaging The Equipment 7
5. Product Dimensions 8
6. Equipment Overview 9
7. System Layout 10
7.1. Site Location 11
7.2. Mechanical Installation 11
8. Electrical Control Panel 12
8.1. Remote Alarms 13
8.2. Remote Start/Stop 13
8.3. Start-up Procedure 13
8.4. HMIInterface 14/15
9. Oxygen Analyzer Calibration 16
9.1. GEN2 - 1110, 2110, 3110 16
9.2. GEN2 - 2130, 3130, 4130,6130, 8130, 10130, 12130 17
9.3. Sensor Calibration 18
10. Maintenance 19
10.1. Daily Checks 19
10.2. Cleaning 19
10.3. Service Schedule 20
11. Troubleshooting 21
12. Warranty 22
13. Service Record 22
14. Electrical Schematic 23 / 24
15. Process & Instrumentation diagram 25

Page 317-110-0143
1. General Information
This manual is copyrighted, all rights reserved. It may not, in whole or in part, be copied,
photocopied, reproduced, translated, or reduced to any electronic medium or machine
readable form without prior consent in writing from nano-puricationsolutions. It may not
be distributed through the internet or computer bulletin board systems without prior consent
from nano-purication solutions.
1.1 Document Introduction
This manual provides factory prescribed installation and maintenance procedures for a
nano-puricationsolutionsGEN2nitrogengenerator.Theproceduresillustratedinthis
document are only to be performed by authorized personnel. For further information
regarding the procedures outlined in this document contact your supplier before proceeding.
Read this document carefully before attempting to install or operate the nitrogen generator.
This document should be permanently available at the nitrogen generator installation site
and be kept in an easily accessible place.
NOTES: highlight important sections of
information where particular care and
attention should be paid.
CAUTIONS: indicate any situation or
operation that may result in potential
damage to the product, injury to the
user, or render the product unsafe.
Annotations:
1.2 Support and Manufacturers details
nano-purication solutions inc.
5509DavidCoxRoad
Charlotte
NC 28269
USA
Telephone: +1 (704) 897-2182
Fax: +1(704)897-2183
Internet: www.n-psi.com
E-mail: [email protected]
nano-purication solutions ltd.
Dukesway,
Team Valley Trading Estate,
Gateshead,
NE11 0PZ
United Kingdom
Telephone: +44 (0) 191 497 7700
Fax: +44(0)1914977709
Internet: www.n-psi.co.uk
1.3 Warranty Guidelines
All products are supplied with a 2 year manufacturer’s warranty from the date of purchase
and must be installed and maintained in accordance with the manufacturer’s guidelines.
Onlygenuineservicepartsshouldbeusedandnomodicationsmade.Forfurther
information please contact your supplier.
© 2016 nano-purication solutions.
Products: GEN2 - 1110, 2110, 3110, 2130, 3130, 4130, 6130, 8130, 10130, 12130
Doc No: 17-110-0143
Issue: 009

Page 4 17-110 -0143
2. General safety
2.1 Intended use of the Product
ThegeneratorisexclusivelyintendedfortheproductionofNitrogengasfromcompressedair,whichisfree
from bulk water, oil and solid matter constituents.
The product should be sited within a building (see section 7.1 Site selection). The generator must be operated
only in accordance with the data on the rating label and in accordance with the contractual conditions. Any
operations that do not comply with those stated on the product rating label will render the warranty void.
Nomodicationsmustbemadetotheproduct.Anymodicationsmayreducetheoperationalsafetyofthe
product and invalidate the manufacturer’s warranty, potentially resulting in damage to the product and serious
personal injury.
For your own safety, when carrying out work on this product, all relevant national safety regulations
must be complied with relating to pressurized and electrical systems.
This product is only designed to operate at pressures of between 87 - 145 (6 - 10barg) or
232 psig (16 barg) dependant on the generator model.
2.2 Personnel
Only authorized, competent and trained personnel are permitted to work on the product. This user guide is
intended solely for such personnel and is to be used only as a reference; it should not be used to replace
conventional training.
2.3 Safe handling
Please ensure that relevant safe engineering practices and handling procedures are employed when handling,
installing and operating the product. Ensure that the equipment is depressurized and electrically isolated, prior
tocarryingoutanyofthescheduledmaintenanceinstructionsspeciedwithinthisuserguide.
A suitable lifting aid must be used to minimize the risk of physical injury or damage to the
product.

Page517-110-0143
3. Product Description
3.1 Technical Specication
The nitrogen generator operates on the Pressure Swing Adsorption (PSA) principle to produce a continuous
stream of nitrogen gas from clean dry compressed air.
Pairsofdualchamberextrudedaluminiumcolumns,lledwithCarbonMolecularSieve(CMS),arejoinedvia
an upper and lower manifold to produce a two bed system. Compressed air enters the bottom of the ‘online’
bedandowsupthroughtheCMS.OxygenispreferentiallyadsorbedbytheCMS,allowingnitrogentopass
through.
After a pre-set time the control system automatically switches the bed to equalization mode where the online
bed pressure is equalized with the second regenerated bed. Once equalized the online bed is switched to
regenerativemodeandoxygenisventedfromtheCMS.Asmallportionoftheoutletnitrogengasisexpanded
into the bed to accelerate the regeneration. At the same instant the second bed comes on-line and takes over
the separation process.
The CMS beds alternate between online equalization and regeneration modes to ensure continuous and
uninterrupted nitrogen production.
Whenageneratorisspeciedwithaninternaldryer,eachCMScolumnhasauniqueadsorptionmediatube
technologydryerttedintothebottomofeachcolumn.
The unique intergrated dryer does not require servicing and the life is aligned to the CMS material.
Theintergrateddryerreducesenergyrunningcostsbyeliminatingtheadditionalexternaldryerpurge(typically
20% of the dryer inlet air consumption) and the associated pressure loss across an external dryer. The
compressed air requirement is also reduced accordingly.
Theoxygen concentrationin thenitrogen streamis monitoredcontinuously onmodels ttedwith anoxygen
analyzer.Iftheoutletconcentrationexceedstherequiredproductionlevel,thenitrogenoutletisclosedandthe
gas is vented to atmosphere. Normal operation will resume when the purity recovers.
Parameter Units
Inlet Air Quality ISO8573.1:2010 Class1.2.1/Class1.5.1(whenttedwithAMTintegraldryer)
Minimum Inlet Pressure Barg (psig) 6 (88)
MaximumInletPressure Barg (psig) 10(145)or16(232)
Rated Inlet Temperature °C (°F) 20-25(68-77)
Minimum Inlet Temperature °C (°F) 5(41)-Subjecttocorrectionfactor.
MaximumInletTemperature °C (°F) 40 (104) - Subject to correction factor.
Supply Voltage VAC(50/60Hz) 88-264 VAC
Input Current Amps (VAC) 1.3 / 0.8 (110-230)
IP Rating IP11 / NEMA 2
Noise dB (A) <90

Page 6 17-110 -0143
4. Product Contents
1. GEN2 Series Nitrogen Generator
2. Documentation
• 1xUserGuide
• 1xDeclarationofConformity
3. Packaging
• 1xGeneratorsupportbaseandboxcover
4.1 Packaging
Allproductsaresecurelypackagedinaspecicallydesignedwoodenpackingbox.The
nitrogen generator will be held in a horizontal position by wooden struts used to secure the
producttotheboxbase.Theboxtopcovercanberemovedbyremovingthescrewsand
lifted off in multiple pieces.
Damage to Packaging
Checkimmediatelytoestablishwhetherdamagehasoccurredtotheexternalpackaging
andifthedamageextendstotheproductinside.Ifthereisdamagetoaproduct,contact
the relevant supplier immediately.
The support packing box permits longitudinal stacking; however the central
section of the packing box should not be considered load bearing.
In no circumstances must a damaged product be used in operation. Using
damaged products can lead to irreparable functional faults or cause serious
physical harm.

Page 717-110-0143
4.2 Unpacking the Equipment
The generator is supplied in a wooden crate. It is recommended that the crate be moved into position using a
forklift truck or pallet truck. Remove the generator from the wooden crate using an overhead crane. Use the
following illustrations for correct guidance on safe handling and lifting techniques.
12
3 4
56
7 8

Page 8 17-110 -0143
5. Product Dimensions
MODEL
INLET
PORT SIZE
A B C D E F G
Inches mm Inches mm Inches mm Inches mm Inches mm Inches mm Inches mm
GEN2-1110 1”
22.95 583 8.42 214 47.83 1215 6.37 162 9.92 252 15.43 392 44.58 1132.5
GEN2-2110 1”
29.56 751 15.03 382 47.83 1215 6.37 162 9.92 252 15.43 392 44.58 1132.5
GEN2-3110 1”
36.18 919 21.65 550 47.83 1215 6.37 162 9.92 252 15.43 392 44.58 1132.5
GEN2-2130 1”
29.56 751 15.03 382 71.33 1812 6.37 162 12.48 317 31.57 802 68.20 1732.5
GEN2-3130 1”
36.18 919 21.65 550 71.33 1812 6.37 162 12.48 317 31.57 802 68.20 1732.5
GEN2-4130 1”
42.79 1087 28.26 718 71.33 1812 6.37 162 12.48 317 31.57 802 68.20 1732.5
GEN2-6130 1”
55.90 1420 41.49 1054 71.33 1812 6.37 162 12.48 317 31.57 802 68.20 1732.5
GEN2-8130 1”
69.25 1759 54.72 1390 71.33 1812 6.37 162 12.48 317 31.57 802 68.20 1732.5
GEN2-10130 1”
82.42 2095 67.95 1726 71.33 1812 6.37 162 12.48 317 31.57 802 68.20 1732.5
GEN2-12130 1”
95.59 2428 81.18 2062 71.33 1812 6.37 162 12.48 317 31.57 802 68.20 1732.5
(A)
(B)
(C)
(D)
(E)
(G)
(F)
14.17 [360]
15.74[400]

Page 917-110-0143
6. Equipment Overview
All connection points are clearly marked on the generator and are represented in the diagram below.
(GEN2 1110, 2110, 3110, 2130, 3130, 4130, 6130, 8130, 10130, 12130)
Air Inlet
‘Dimension F’
(1” Port)
1
N2 To Buffer Tank
‘Dimension I’
(1” Port)
2
N2 From Buffer Tank
‘Dimension H’
(1/2” Port)
3
N2 Outlet
‘Dimension G’
(1/2” Port)
4
Main Power
Inlet
5
HMI Screen
Display
6
10
11
12
N2 Outlet pressure
Gauge
Sample Point
(1/8” Port)
Top Cover
13 Silencers/Mufers
Air inlet pressure
Gauge
9
7
8
Column A pressure
Gauge
Column B pressure
Gauge
13
1
2
3
4
5
6
7
8
9
10
11
14 Purge adjustment
14
12
ExternalSamplePointOnlyAvailableon
GEN2 2130-12130 Nitrogen Generators.
Internal Sample Point Available on
GEN2 1110-3110 Nitrogen Generators.

Page 10 17-110 -0143
7. System Layout
Only personnel trained, qualied and approved by the supplier should perform
installation, commissioning, service and repair procedures.
1Compressor (Not Supplied)
With External Desiccant Dryer
With Integrated Dryer
7
28
Buffer Vessel
3
Wet Air Receiver (Not Supplied)
9
Pressure Relief Valve*
4 10
N2 Generator
5
Pre-ltration(1 micron & 0.01 micron)
11
Dust Filter (1 micron)
6
Desiccant Air Dryer Nitrogen Outlet
Pre-ltration(Water Seperator)
Dust Filter (1 micron)
Ref Description Ref Description
(1) It is the customers responsibility to ensure pressure relief valves are tted to the compressed air system. All vessels supplied by nano
come with a pressure relief valves and pressure gauge as standard.
(2) Buffer vessel is used for mixing nitrogen gas, this is not to be used as downdtream storage.
(3) Reference ‘1’ & ‘2’ are supplied separately.
N2 Storage (Optional)
*Note: For service details please see page 20.
1
2
8
34
7
8
9
10
11
1
2
8
34
7
8
9
10
11
6
5
It is essential that the system into which the product is installed is tted with a pressure
limiting/relief device. This device should be between the compressor and the generator.
The device must be set to prevent the maximum working pressure of 145psig (10 barg) or
232 psig (16 barg) from being exceeded.

Page 1117-110-0143
7.1 Site Location
When selecting an installation site for the generator , ensure the following conditions are met:
• Thesiteshouldbelocatedindoorsonaatsurfaceprotectedfromweatherandotherharmfulconditions.
• Theambienttemperaturemustnotdropbelow41°F(+5°C)orexceed122°F(+50°C).
• The installation site should be level and able to support the weight of the product.
• Ensuresufcientspacearoundtheproduct,werecomendatleast1maroundthegeneratortoallow
access for operation and maintenance.
• Takeintoaccountthenoisegeneratedwheninusewhenconsideringthenallocation.
Note:Duetothenatureofoperationthereisapossibilityofoxygenenrichmentsurroundingthegenerator.
Ensure the area surrounding the generator is adequately ventilated.
Once the generator has been located into position, install ball valves and the pipework ready for connection
tothebuffervesselandcompressedairsupply.Thediameterofthepipesmustbesufcienttoallow
unrestricted inlet air supply to the generator and nitrogen supply to the applications shown in the table below.
7.2 Mechanical Installation
A
B
C
D
1
3
2
4
1” Ball Valve
(All GEN2 Models)
1
21” Ball Valve
(All GEN2 Models)
Connection
1/2” Ball Valve
(All GEN2 Models)
3
41/2” Ball Valve
(All GEN2 Models)
1” NB
(All GEN2 Models)
A
B1” NB
(All GEN2 Models)
1/2” NB
(All GEN2 Models)
C
D1/2” NB
(All GEN2 Models)
Pipe Work
It is recommended that the system be protected with suitably rated pressure relief valves
upstream of the generator.
Ensure that all piping materials are suitable for the application, clean and debris free. All outlet piping must
besolidandnon-poroustominimizetheingressofoxygen.Whenroutingthepipesensurethattheyare
adequately supported to prevent unnecessary strain which can lead to damage and leaks in the system. The
nitrogenbuffervesselmustberatedtoatleastthemaximumoperatingpressureofthesystemandmustbe
ttedwithasuitabledrainvalve,pressuregaugeandpressurereliefvalve.

Page 12 17-110 -0143
8. Electrical Control Panel
Electrical Power Requirements
Supply: 88 - 264 VAC
47 -63 Hz
Input Current: 1.3 / 0.8A
(115/230VAC)
Main Power Connection
Remote
Start/Stop
Alarm
Outputs
Main
Connections
g.1
‘RS’
Remote Start Cable
2.0A Fuse
5 x 20 (Thermal) 250v

Page 1317-110-0143
8.1 Remote Alarms
TherearetwoseperateremotealarmsforPressure&PurityandaNovolt/dryercontrolcontact(seeg.1)
A1 Terminal : input (0-24v DC).
A1 Terminal : output (0-24v DC) common alarm output for pressure & purity.
A2 Terminal : input (0-24v DC).
A2 Terminal : output (0-24v DC) for dryer control only.
8.2 Remote Stop/Start
• Tosetuptheremotestopstartfunction,removethelinkmarkedas‘RS’(remotestartg.1)betweenthe
liveterminalandthePLC(seeg.1).Azerovoltswitchfromtheremotecontrolneedstobeinstalledinit’s
place(seeg.2).
• When the connection is made you can start the generator using the HMI screen, the generator will
operate normally. If the connection is broken, i.e. the generator has been remotely switched off, the
generator will commence shut down procedure, stop cycling and go into standby mode this can also be
achieved by using the shutdown feature on the HMI screen, displaying “STANDBY” on the display once
completed.
• Using remote stop / start ensures the correct shut-down sequence is implemented.
8.3 Start Up Procedure
• Ensure that all isolation valves are fully closed before operating.
• Hold down the Start/stop button located on the HMI Screen, this will start the generator.
• Slowly open the air inlet valve (page 11/12) and check for any leaks. Continue to open the air inlet valve
until fully open.
• Allow the generator to cycle at least two times.
• Slowly open the ‘To buffer tank’ isolation valve (page 10/11) until the buffer tank is at full pressure
(this will take a few cycles)
• Slowly open the ‘From buffer tank’ isolation valve (page 10/11). At this point the generator control system
will be able to operate fully.
Beware, it can take up to two hours to clean the buffer tank.
g.1 g.2 Remote
Start/Stop
External Remote
Switch
Factory
Set-up

Page 14 17-110 -0143
8.4 HMI Screen Interface
Alarm Mute
The Alarm mute button will de-activate any active alarm (new alarms will activate independently). Once the
currentfault/Alarmhasbeenrectiedthemutefunctionisre-set.
Charts
This screen shows the Current N2 Purity and Outlet Pressure in graph form indication
(timereq’dxhoursonscreen).
Fault Log
This screen offers read only access to the fault log.
Set Time
This screen allows the end user to enter the correct time and date.
Login
Access to the Menu structures (there are 3 levels of pass-code protection within the screen).
Service Record
This screen offers read only access to the generators service record.
Information
The Information screen indicates the current N2 purity, Outlet pressure, all generator detail & Commissioning
data.
Service Contact
Menu
i
Information
Alarm Mute Charts Fault Log Set Time Login Service Record
User Engineer Distributor
Settings Installation Service Reset Service Details Manual Overide Customer

Page1517-110-0143
There are three levels of pass-code protection, these are User, Engineer and Distributor. To access Level 1
(User) select the menu button on the home screen, then select the login button. From there select ‘User from
the drop down menu and enter password ‘1234’.
Settings (Level 1 Access - Pass-code ‘1234’)
You are able to adjust the following:
- Purity Alarm - Alarm Delay On - Alarm Delay Off
- ES Pressure Low - ES Pressure High - ES Stage Duration
- Inlet Pressure Low Setpoint - Alarm Delay On - Alarm Delay Off
- Outlet Pressure Low Setpoint - Alarm Delay On - Alarm Delay Off
- Outlet Pressure Alarm (on/off)
- Pressure Units (bar/psi)
Installation (Level 2 Access)
You are able to adjust the following:
- Installation date
- Commissioned by
- Company name of commisioning engineer
- Service interval
Service Details (Level 2 Access)
You are able to enter the following information:
- Contact name of prefered service provider
- Telephone number of prefered service provider
- Website of prefered service provider
Manual Overide (Level 2 Access)
You are able to manualy control the following valves:
- Inlet A - Inlet B
-ExhaustA -ExhaustB
- N2 Vent - N2 Outlet
- O2 Isolate - Equalization Valve
- Dryer Contact
Customer (Level 3 Access)
You are able to adjust the following:
- Customer Name (Displayed on main screen)
- Purity Selection
- Replacement Build
Ensure the system is placed in to standby mode prior to entering the manual overide menu.

Page 16 17-110 -0143
9. Oxygen Analyzer Calibration
1. Closeballvalve‘A’(thiswillstopgasowingfromthegeneratortotheoxygenanalyzer).
2. Allowtheoxygenanalyzerprocessarrangementtodepressurizebeforeintroducingthecalibrationgas.
3. Once depressurized (this will be shown on the pressure gauge), connect your calibration gas to the
sample point located on the enclosure (page 9). Once connected open ball valve ‘B’ and introduce calibra-
tiongasat7.25-145psi(0.5-10bar).Allowthedisplaytostablizebeforemovingontothenextstep.
4. Follow the Sensor Calibration Procedure (page 18).
5. Once calibrated, close ball valve ‘B’, remove the calibration gas and re-open ball valve ‘A’ allowing gas to
owfromthegenerator.
6. Follow generator start up procedure (page 13)
9.1 (GEN2 1110, 2110, 3110)
Gas From Nitrogen
Generator External Sample/
Calibration Gas
Ballvalve
‘A’
Ballvalve
‘B’
O2 Sensor (where tted)
It is recommended that the O2sensor(iftted)shouldbecalibratedevery3monthsoryoushould
seek a local calibration authority to discuss further. (See pages 16 - 18 for instructions)

Page 1717-110-0143
9.2 (GEN2 2130, 3130, 4130, 6130, 8130, 10130, 12130)
1. Closeballvalve‘A’(thiswillstopgasowingfromthegeneratortotheoxygenanalyzer).
2. Allowtheoxygenanalyzerprocessarrangementtodepressurizebeforeintroducingthecalibrationgas.
3. Once depressurized (this will be shown on the pressure gauge), connect your calibration gas to the
sample point located on the enclosure (page 9). Once connected open ball valve ‘B’ and introduce calibra-
tiongasat7.25-145psi(0.5-10bar).Allowthedisplaytostablizebeforemovingontothenextstep.
4. Follow the Sensor Calibration Procedure (page 18).
5. Once calibrated, close ball valve ‘B’, remove the calibration gas and re-open ball valve ‘A’ allowing gas to
owfromthegenerator.
6. Follow generator start up procedure (page 13)
Gas From Nitrogen
Generator
External Sample/
Calibration Gas
Ballvalve
‘A’
Ballvalve
‘B’
O2 Sensor (where tted)
It is recommended that the O2sensor(iftted)shouldbecalibratedevery3monthsoryoushould
seek a local calibration authority to discuss further. (See pages 16 - 18 for instructions)

Page 18 17-110 -0143
Press the Enter button ( )
Press the Menu button ( )
Display should read E:1
Press the Menu button ( ) to close the
Menu system. The sensor will revert back to
normal monitoring mode.
UsingtheNext(increment)button()
and the Previous (decrement) button ( ),
set the display to that of the calibration
gas level.
Press the Enter button ( ). This will
“Span” the Sensor.
Thedisplaywillread(----)toconrm
that the Sensor Span been successful
7.25psi
(0.5bar)
250ml/m
9.3 Sensor Calibration Procedure

Page 1917-110-0143
10. Maintenance
Maintenance operations should only be carried out by authorized, competent and
suitably trained personnel.
• Maintenance operations only to be conducted when the system has been shut down, fully depressurized
and isolated completely from the compressed gas and electrical supply.
• Ensure the system is in a safe condition for maintenance to be carried out.
• Dismantle and assemble with care, paying particular attention to the areas that become pressurized.
• Replace with new seals, all gaskets removed during maintenace operations.
• Do not modify or adjust the control settings.
• Onlycertiedandapprovedreplacementpartsfromthemanufactureraretobeused.
• Always check all connections / sealing faces for cleanliness and secure seating prior to assembly.
• Ensureallcomponentsarerettedtotheproductbeforeoperation.
• Gradually build up pressure in the generator and check for any leaks.
• Ensure the generator is left operating in a safe working condition after completion of maintenance.
10.1 Daily checks
Visual and functional check of the generator should be carried out daily.
• Checkthegeneratorforcorrectoperation,anyexternaldamageandleaks.
If defects found, immediately depressurize and isolate product until defects are rectied.
• If the service required display appears on the screen or the alarm signal activates, the generator must be
serviced.
Contact your supplier and request a product service kit.
• Remove any loose dust or dirt from the product , clean with a damp cloth only, all surfaces that appear to
have attracted unwanted contaminants.
• Ensurethegeneratorisoperatingwithinthepurityspecication,parameters,pressure,temperatureand
owrate.
10.2 Cleaning
Cleantheequipmentwithadampclothonlyandavoidexcessivemoisturearoundanyelectricalsockets.
If required you may use a mild detergent, however do not use abrasives or solvents as they may damage/
degrade the warning labels on the equipment.
Beware a characteristic of the CMS could cause the vessel to repressurize slowly up to
2 barg.

Page 20 17-110 -0143
10.3 Service Schedule
Service
Recommended Service Intervals
12 Months
(or 8,000
hours)
24 Months
(or 16,000
hours)
36 Months
(or 24,000
hours)
48 Months
(or 32,000
hours)
60 Months
(or 40,000
hours)
72 Months
(or 48,000
hours)
84 Months
(or56,000
hours)
96 Months
(or 64,000
hours)
AP P P P P P P P
BP P P P
CP P P P
DP P
Service A (A-XXX-1X0): 1”Externalexhaustsilencer/mufer(Available in either BSP or NPT)
NITROGEN
GENERATOR
MODEL
SERVICE CODE
AB C D E F
6 - 10 barg
[87 - 145 psig]
10.5 - 16 barg
[152 - 232 psig]
GEN2- 1110
A-BSP-110
A-NPT-110
A-BSP-130HP
A-NPT-130HP
B-SSVK-130 C-PVSK-130 D-CVK-130
E-GCR-%
E-GCR-PPM
F-ZCR-%
F-ZCR-PPM
GEN2- 2110
GEN2- 3110
GEN2- 2130
A-BSP-130
A-NPT-130
GEN2- 3130
GEN2- 4130
GEN2- 6130
GEN2- 8130
GEN2- 10130
GEN2- 12130
Oxygen Analyzer Recommended Service Intervals
E
Galvanic Cell PPPP
F
Zirconian Cell P
Service A (A-XXX-130HP): 2”Externalexhaustsilencer/mufer(Available in either BSP or NPT)
Note: The Serial/Part number of the nitrogen generator must be supplied when requesting any of
the services listed above, this is to ensure the correct service parts are selected.
Service B (B-SSVK-130): O2Sensor Solenoid Valves (2 required If tted with a Galvanic Cell)
Service C (C-PVSK-130): All piston valve seals are to be replaced
Service D (D-CVK-130): All control valves are to be replaced.
Service E (E-GCR-%): Replace % O2Sensor (Galvanic Cell)
Service F (F-ZCR-%): Replace % O2Sensor (Zirconian Cell)
Service E (E-GCR-PPM): Replace PPM O2Sensor (Galvanic Cell)
Service F (F-ZCR-PPM): Replace PPM O2Sensor (Zirconian Cell)
This manual suits for next models
9
Table of contents
Other NANO Portable Generator manuals
Popular Portable Generator manuals by other brands

Briggs & Stratton
Briggs & Stratton Portable Generator Operator's manual
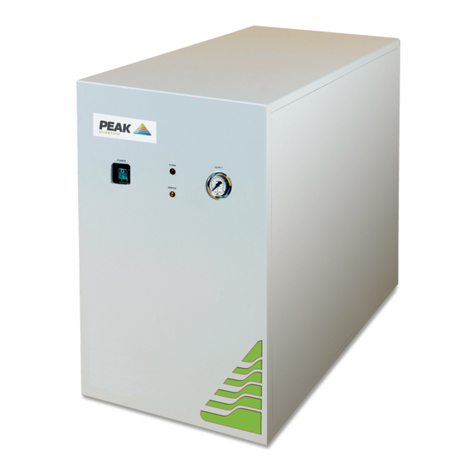
Peak Scientific
Peak Scientific Genius N118LA user manual
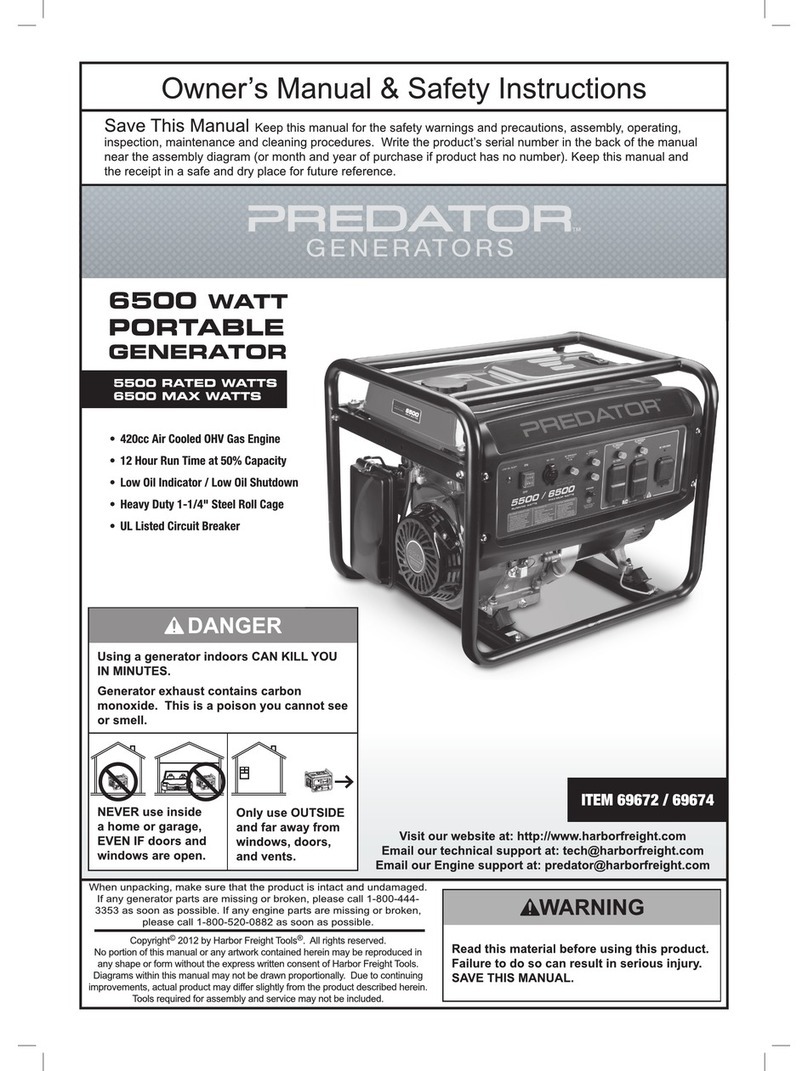
Predator
Predator Predator generators 6500 Watt Owner's manual & safety instructions
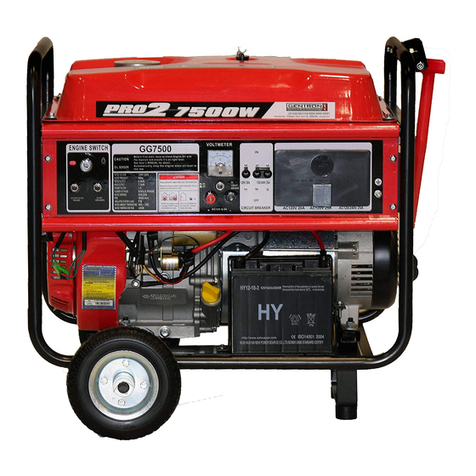
GENTRON
GENTRON PRO2 Series owner's manual

Lifetech
Lifetech mitouch quick start guide

Predator
Predator 69677 Owner's manual & safety instructions