NANO 3 N2 Series User manual

NITROGEN GENERATOR
SERIES 3 N² USER GUIDE:

Page 2
nano-purification solutions.
17-110-0142
Document Contents
Title
1. General Information
1.1 Document Introduction
1.2 Support & Manufacturer’s Details
2. General Safety
3. Description of the Product
3.1 Technical Description
4. Product Contents
4.1 Packaging
4.2 Un-packing the equipment
5. Product Dimensions
6. Equipment Overview
7. System Layout
7.1 Site Location
7.2 Mechanical Installation
7.3 Electrical Installation
8. Generator Operation
8.1 6 Pin Electrical Connector Configuration
8.2 Start Up Procedure
8.3 Shut Down Procedure
8.4 Economy Mode
9. Oxygen Analyser Calibration
10. Maintenance
10.1 Daily Checks
10.2 Cleaning
10.3 Service Schedule
10.4 O2Sensor Calibration
11. Troubleshooting
12. Warranty
13. Service Record
Page
3
3
3
4
5
5
6
7
8
9
10
11
12
13
14
15
16
17
18
18
19
21
21
21
22
22
23
24
25

Page 317-110-0142
1. General Information
This manual is copyrighted, all rights reserved. It may not, in whole or in part, be copied, photocopied,
reproduced, translated, or reduced to any electronic medium or machine readable form without prior consent
in writing from nano-purification solutions. It may not be distributed through the internet or computer bulletin
board systems without prior consent from nano-purification solutions.
1.1 Document Introduction
This manual provides factory prescribed procedures for the installation, operation and maintenance of a nano-
purification solutions Series 3 Nitrogen Generator. The procedures illustrated in this document are only to be
performed by authorized personnel. For further information regarding the procedures outlined in this document
contact nano-purification solutions before proceeding.
Read this document carefully before attempting to install or operate the generator . This document should be
permanently available at the generator installation site and be kept in an easily accessible place alongside the
product.
©2012 nano-purification solutions.
Series 3 Nitrogen Generator
Document number: 17-110-0142
Issue: 001
NOTES: highlight important sections of information where particular care and attention should
be paid.
CAUTIONS: indicate any situation or operation that may result in potential damage to
the product, injury to the user, or render the product unsafe.
Annotations:
1.2 Support
For North American Support please contact:
nano-purification solutions
11330 Vanstory Drive
Huntersville, NC 28078
USA
Telephone: (704) 897-2182
Fax: (704) 897-2183
Internet: www.n-psi.com
E-mail: [email protected]
Manufacturer’s Details
nano-porous solutions limited
Dukesway, Team Valley. Trading Estate,
Gateshead, Tyne and Wear,
United Kingdom, NE11 OPZ.
Telephone: +44 (0) 191 497 7700
Fax: +44 (0) 191 497 7709
Internet: www.n-psl.com
E-mail: [email protected]

Page 4
nano-purification solutions.
17-110-0142
2. General safety
For your own safety, when carrying out work on this product, all relevant national safety
regulations must be complied with relating to pressurized and electrical systems.
Intended use of the Product
The generator is exclusively intended for the production of N2 from compressed air, which is free from bulk
water, oil and solid matter constituents.
The product should be sited within a building and protected (see section 7.1 Site selection). The generator
must be operated only in accordance with the data on the rating label and in accordance with the contractual
conditions. Any operations that do not comply with those stated on the product rating label will render the
warranty void.
This product is only designed to operate at pressures of between 87 - 145 psig (6 - 10 barg).
It is not suitable for pressures in excess of 145 psig (10 barg).
No modifications must be made to the product. Any modifications may reduce the operational safety of the
product and invalidate the manufacturer’s warranty, potentially resulting in damage to the product and serious
personal injury.
Personnel
Only authorized, competent and trained personnel are permitted to work on the product. This user guide is
intended solely for such personnel and is to be used only as a reference; it should not be used to replace
conventional training.
Safe handling
Please ensure the relevant safe engineering practices and handling procedures are employed when handling,
installing and operating the product. Ensure that the equipment is depressurized and electrically isolated, prior
to carrying out any of the scheduled maintenance instructions specified within this user guide.
A suitable lifting aid must be used to minimize the risk of physical injury or damage to the
product.
IMPORTANT: It is essential that the system into which the product is in-
stalled is fitted with a pressure limiting/relief device. This device should
be between the compressor and the generator. The device must be set to
prevent the maximum working pressure of 145 psig (10 barg) from being
exceeded.

Page 517-110-0142
Inlet pressure dewpoint required is ISO8573.1 Class 5 for water 45°F (+7°C)
3 stage inlet filtration is required , e.g. Water separator and 2 high efficiency coalescer filters (see system
layout on page 11) to protect the generator from bulk water, particulate and oil aerosol.
3. Description of Product
3.1 Technical Specification
The n-psi nitrogen generator operates on the Pressure Swing Adsorption (PSA) principle to produce a continuous
stream of nitrogen gas from clean dry compressed air.
Pairs of dual chamber extruded aluminium columns, filled with Carbon Molecular Sieve (CMS), are joined via
an upper and lower manifold to produce a two bed system. Compressed air enters the bottom of the ‘online’
bed and flows up through the CMS. Oxygen is preferentially adsorbed by the CMS, allowing nitrogen to pass
through.
After a pre-set time the control system automatically switches the bed to regenerative mode and oxygen is
vented from the CMS. A small portion of the outlet nitrogen gas is expanded into the bed to accelerate the
regeneration. At the same instant the second bed comes on-line and takes over the separation process.
The CMS beds alternate between separation and regeneration modes to ensure continuous and uninterrupted
nitrogen production.
When a generator is specified with an internal dryer, each CMS column has a unique adsorbtion media tube
(AMT) technology dryer fitted into the bottom of each column.
The unique AMT dryer does not require servicing and the life is aligned to the CMS material.
The internal AMT dryer reduces energy running costs by elminating the additional external dryer purge (typically
20-25% of the dryer inlet air consumption) and the associated pressure loss across an external dryer. The
compressed air supply is also reduced accordingly.
The oxygen concentration in the nitrogen stream is monitored continuously on models fitted with an oxygen
analyser. If the outlet concentration exceeds the required production level, the nitrogen outlet is closed and the
gas is vented to atmosphere. Normal operation will resume when the purity recovers.
Parameter Units
Inlet Air Quality ISO 8573.1:2010 Class 1.2.1 / Class 1.5.1 (when fitted with AMT integral dryer)
Minimum Inlet Pressure psig / (Barg) 88 (6)
Maximum Inlet Pressure psig / (Barg) 145 (10)
Rated Inlet Temperature °F / (°C) 68-77 (20-25)
Minimum Inlet Temperature °F / (°C) 34.7 (1.5)
Maximum Inlet Temperature °F / (°C) 104 (40) - Subject to correction factor.
Supply Voltage VAC (50/60Hz) 88-264 VAC
Input Current Amps (VAC) 1.3 / 0.8 (110-230)
IP Rating IP54 / NEMA 3
Noise dB (A) <80

Page 6
nano-purification solutions.
17-110-0142
4. Product Contents
1. Series 3 N² Nitrogen Generator
2. Documentation
• 1 x User Guide
• 1 x Declaration of Conformity
3. Packaging
• 1 x Generator support base and box cover
• Care Should be taken and inspection undertaken during unpacking to ensure that the product is
not damaged.
• Verify that all component parts have been supplied with the generator

Page 717-110-0142
4.1 Packaging
All products are securely packaged in a bespoke wooden packing box. The generator will be held in a
horizontal position by wooden struts; using straps to secure the product to the box base. The box top cover
can be removed by removing the 4 fixing screws and lifting off in one piece.
The support packing box permits longitudinal stacking; however the central section of the packing
box should not be considered load bearing.
Damage to the packaging
• Check immediately to establish whether damage has occurred to the external packaging and if the
damage extends to the product inside.
• If there is damage to a product, contact the relevant supplier immediately.
In no circumstances must a damaged product be used in operation. Using damaged
products can lead to irreparable functional faults or cause serious physical harm.

Page 8
nano-purification solutions.
17-110-0142
6
43
1 2
5
4.2 Unpacking the Equipment
The generator is supplied in a wooden crate. It is recommended that the crate be moved into position using a
forklift truck or pallet truck. Remove the generator from the wooden crate using an overhead crane. Use the
following illustrations for correct guidance on safe handling and lifting techniques.

Page 917-110-0142
Front Side
5. Product Dimensions
D
E
C
A
F
G
B
H
I
* DEPENDING ON MODEL
MODEL CONNECTION
SIZE
A
ins [mm]
B
ins [mm]
C
ins [mm]
D
ins [mm]
E
ins [mm]
F
mm [ins]
G
ins [mm]
H
ins [mm]
I
ins [mm]
WEIGHT
lbs [KG]
NNG-2110 1/2” 26 [650] 15 [382] 47 [1210] 15.7 [400] 14.2 [360] 10 [262] - - 40 [1009] 242 [110]
NNG-2130 1/2” 26 [650] 15 [382] 71 [1810] 15.7 [400] 14.2 [360] 10 [262] 22 [560] 36 [920] 64 [1625] 365 [116]
NNG-3110 1/2” 32 [820] 22 [550] 47 [1210] 15.7 [400] 14.2 [360] 10 [262] - - 40 [1009] 374 [170]
NNG-3130 1/2” 32 [820] 22 [550] 71 [1810] 15.7 [400] 14.2 [360] 10 [262] 22 [560] 36 [920] 64 [1625] 490 [222]
NNG-4130 1/2” 39 [990] 28 [718] 71 [1810] 15.7 [400] 14.2 [360] 10 [262] 22 [560] 36 [920] 64 [1625] 610 [277]
NNG-6130 1/2” 52 [1320] 41 [1054] 71 [1810] 15.7 [400] 14.2 [360] 10 [262] 22 [560] 36 [920] 64 [1625] 852 [387]
NNG-8130 1/2” 65 [1660] 55 [1390] 71 [1810] 15.7 [400] 14.2 [360] 10 [262] 22 [560] 36 [920] 64 [1625] 1100 [499]
NNG-10130 *1/2” or 1” 79 [2000] 68 [1726] 71 [1810] 15.7 [400] 14.2 [360] 10 [262] 22 [560] 36 [920] 64 [1625] 1350 [610]
NNG-12130 *1/2” or 1” 92 [2330] 80 [2026] 71 [1810] 15.7 [400] 14.2 [360] 10 [262] 22 [560] 36 [920] 64 [1625] 1600 [722]

Page 10
nano-purification solutions.
17-110-0142
6. Equipment Overview
Compressed
Air Inlet
To Buffer
Vessel
From Buffer
Vessel
Nitrogen
Outlet
N² Outlet Port to buffer
All connection points are clearly marked on the generator and are represented in the diagram below. Ports 1-4
are factory set for customer requirement but can be changed internally.
Controller Display Unit Front Shroud
N² Outlet Port
Column A pressure gauge
Column B pressure gauge
N² Outlet pressure gauge
Air inlet pressure gauge
External O² Analyser Sample Point
N² Inlet Port from buffer
Air Inlet Port
5
2
6
3
4
2
1
3
7
8
4
1
1
5 6
3
7 8
2
4
Top Cover
9
9
(1/4” bspp)
Sample

Page 1117-110-0142
7. System Layout
Only personnel trained, qualified and approved by nano-purification solutions should
perform installation, commissioning, service and repair procedures.
1Compressor
With External Desiccant Dryer
With Integrated AMT Dryer
7
28
Buffer Vessel
3
Wet Air Receiver
9
Pressure Relief Valve*
4 10
N²Generator (With Internal Dust Filtration)
5
nano M1, M01 grades
11
Dust Filter
6
Dryer Nitrogen Outlet
nano WS
Dust Filter (Required if Non n-psi dryer is used)
11
10
88
9
7
134
2
11
10
88
9
6
57
2
134
Ref Description Ref Description
*Note: It is the customers responsibility to fit pressure relief valves to the compressed air system.

Page 12
nano-purification solutions.
17-110-0142
7.1 Site Location
When selecting an installation site for the generator , ensure the following conditions are met:
• Installation site should be located indoors on a flat surface protected from the weather and other harmful
conditions.
• The ambient temperature must not drop below 41°F (+5°C) or exceed 122°F (+50°C).
• The installation site should be level and able to support the weight of the product.
• Ensure sufficient space around the product, to allow access for operation and maintenance.
• Take into account the noise generated when in use when considering the final location.
• The generator must be mounted vertically as shown.
Note: Due to the nature of operation there is a possibility of oxygen enrichment surrounding the generator.
Ensure the area surrounding the generator is adequately ventilated.

Page 1317-110-0142
7.2 Mechanical Installation
Once the generator has been located into position, install the ball valves and the pipework ready for
connection to the buffer vessel and compressed air supply.
The diameter of the pipes must be sufficient to allow unrestricted inlet air supply to the generator and nitrogen
supply to the applications shown in the table below.
It is recommended that the system be protected with suitably rated pressure relief valves
upstream of the generator.
Ensure that all piping materials are suitable for the application, clean and debris free. All outlet piping must be
solid and non-porous to minimize the ingress of oxygen.
When routing the pipes ensure that they are adequately supported to prevent unnecessary strain which can
lead to damage and leaks in the system.
The nitrogen buffer vessel must be rated to at least the maximum operating pressure of the generator and
must be fitted with suitable valving pressure gauge and pressure relief valve.
D
A
B
C
3
2
1
4
Compressed
Air Inlet
To Buffer
Vessel
From Buffer
Vessel
Nitrogen
Outlet
1 1” Ball Valve
2 1” Ball Valve
3 1/2” Ball Valve
4 1/2” 3-Way Ball Valve
1” NB
1” NB
1/2” NB
1/2” NB
A
B
C
D
Connection Pipe Work
nano M1
grade filter

Page 14
nano-purification solutions.
17-110-0142
7.3 Electrical Installation
Mains Power Connection
Supplied with 3 metres of cable:
If the cable needs to be replaced:
• Disconnect from mains supply.
• Unscrew the 4 x M5 cap head screws in order to remove the generator top cover.
• Slide 2 x door latch pins together to allow the front cover to swing open on the hinge.
• This will expose the controller back plate and power connection (as shown circled in red).
Electrical Power Requirements
Supply: 88 - 264 VAC
47 -63 Hz
Input Current: 1.3 / 0.8A
(115/230 VAC)
CONTROLLERPOWER
Fuse Holder
(T2A 250V)
Controller Back
Plate

Page 1517-110-0142
Under no circumstances should external voltage/current be applied to pins 1 and 4,
damage to the controller will occur, negating the warranty.
Electrical Connector
• To set up for remote control eco mode.
Remove the link between pins 1 and 4 (3)
in the electrical connector plug. A zero volt
switching signal from the remote control needs
to be connected between pins 1 and 4 (4).
• When the connection is made, the generator
will operate normally. If the connection is
broken, i.e. the generator has been remotely
switched off, the generator will commence
shut down procedure, stop cycling and go into
standby mode, displaying “STANDBY” on the
display once completed.
• Using remote stop / start ensures the correct
shut-down sequence is implemented.
Generator Remote Stop/Start Control (if required)
8. Generator Operation
Locate the electrical connector on the underside of the controller in the shroud.
8.1 6 Pin Electrical Connector Configuration
Links 1/4
Remote stop/start link
1. 2. 3.
4.
1
2
3
6
4
5
Links 2/3
General (no-volt) alarm output
Link 5/6 (-Ve/+Ve)
4-20mA Retransmission
(Optional - where fitted)

Page 16
nano-purification solutions.
17-110-0142
Under no circumstances should external voltage/current be applied to pins 5 and 6,
damage to the controller will occur, negating the warranty.
Care must be taken when assembling all connections in the plug to ensure all terminals
remain completely insulated from each other.
Oxygen Purity 4-20mA Retransmission (where fitted)
Pins 5 and 6 in the electrical connector are dedicated to analgue retransmission of the 02 purity. Pin 5 -ve, Pin
6 +ve 4-20mA signal at 24VDC.
• Pins 2 & 3 on the electrical connector provide a zero volt alarm output for customer control panel
indication. These pins are connected to relay contacts within the controller which will close when the
service or O2 purity (optional) / pressure alarm conditions arise.
General Alarm Output

Page 1717-110-0142
• Ensure the Inlet Air Quality (ISO 8573.1:2010) is Class 1.2.1 or Class
1.5.1 when fitted with AMT integral dryer and the operating pressure
is between 87-145psig (6 -10barg)
• The inlet air temperature is between 34.7 – 104°F (1-40°C).
• Ensure all generator valves are closed prior to start up.
• Open the inlet valve
• Turn on power to the generator.
• When starting without any pressure in the system, partially open the
outlet valve 2 (see page 13) near the top of the generator control
panel, to allow the buffer vessel to fill up gradually. Once the buffer
vessel is at operating pressure, open the buffer outlet valve fully.
8.2 Start-up Procedure
During the first initial 5 cycles of operation, the outlet purity control valve (after the buffer tank) is automatically
diverted from delivering an outlet flow, to flow to atmosphere, allowing conditioning of the generator to improve
purity prior to going on-line.
Once the initial cycles have been completed, the system will start delivering N2 to the outlet to the outlet
receiver. The N2 outlet flow rate is controlled within the system to prevent the generator overflowing
excessively. It would however be advantageous to limit the flow from the generator, into the outlet receiver to
gradually build up receiver pressure, until it is at operating pressure in order to improve system start-up purity.
If at any time during normal operation the purity degrades to below the set point, the outlet will again close
and flow to atmosphere (clean up cycle) until the purity again achieves specification whereby normal outlet
delivery will resume.
DISPLAY PANEL DISPLAY PANEL
HOURS RUN /
COLUMN ONLINE
HOURS RUN /
COLUMN ONLINE
OPERATION LED
ILLUMINATED WHEN
IN OPERATION
ILLUMINATED WHEN
IN OPERATION
OPERATION LED
Once the buffer vessel is at operating pressure, slowly open the generator outlet valve 4 (see page 13) to
allow the outlet received to pressurize slowly, Once at pressure the system is ready to deliver and the outlet
valve can now be opened.
Company Name
Website
Telephone Number
Column B Online
Hours Run
02 Purity
Press (barg)
Column A
00000
004.00
006.00
Online
Hours Run 00000
02 Purity 003.00
Press(psi) 006.00
START UP PROCEDURE

Page 18
nano-purification solutions.
17-110-0142
If the outlet pressure set-point is reached and maintained for a period of 5 minutes, the generator closes the
outlet valves and continues to cycle for a further 5 minutes whilst continuously monitoring outlet pressure,
after which, if pressure is still maintained high, the generator shuts down into economy mode.
If at any point during this time, if the outlet pressure drops below the set-point, normal cycling operation
resumes.
When the generator is shut down remotely, the shut down procedure will commence. The current cycle will
be completed, then both exhaust valves will open for 2 minutes to exhaust the CMS bed. After which the
exhausts will be closed, in effect sealing the generator ready for start up.
The set-points for Pressure and Purity alarm can be modified by the customer.
• To modify the settings, remove the 4 corner screws from the front bezel from the PLC, and taking care
with the LED cables, carefully move to one side to gain access to the front buttons on the PLC.
• Hold down the A & B buttons for 8 seconds to gain access to the adjustments screen as shown below.
• The screen will remain visible for 1 minute before reverting back to operating mode.
• If the 1 minute access is insufficient, again hold down the A & B buttons for another 8 seconds.
• The O2 alarm digits will flash 1st, this can be changed to Press High or Low by using the - & + buttons.
• To modify the flashing setting, press the OK button and adjust by using the - & + buttons, again pressing
OK to set.
• Once the settings have been adjusted, refit the front bezel, taking care not to damage the LED wiring.
•
• To exit the screen at any point press the ESC button.
Adjusting Set-points for Outlet Pressure and Purity Alarm
8.3 Shut Down Procedure
The generator can be shut down remotely (recommended) using remote wiring configuration see section 8,
Note: At this stage, pressure in the columns may increase slightly. This is due to the
natural operating characteristics of the CMS.
8.4 Economy Mode
Press HIGH
Press LOW
02 Alarm
Press Alarm
00090
00082
00006
00004
Pressure High:
When the generator commences energy saving mode.
Pressure Low:
When the generator exits energy saving mode.as shown below.
Press Alarm:
Pressureat which the No-Volt alarm is activated due to low pressure
conditions. This is usually set lower than the Press Low set point to
prevent unnecessary trigger of the alarm.

Page 1917-110-0142
MENU
%02
9. Oxygen Analyser Calibration
Oxygen Analyser
Sensor
Calibration ‘T’ Piece
1. Remove the 2x M5 cap head screws and remove the top cover.
2. Disengage the Front Shroud latches and open the door to reveal N2process enclosure.
3. Identify O2 sensor assembly & calibration ‘T’ piece (see Figure 1.)
4. Remove blank and introduce calibration gas at 7.25 psi (0.5 bar) and a owrate of 250ml/m
5. Follow the Sensor Calibration Procedure (page 20).
6. Once calibrated, re-assemble the blank, close the front shroud and re-assemble the top cover.
7. Follow generator start up procedure (page 17)

Page 20
nano-purification solutions.
17-110-0142
Press the Enter button ( )
Press the Menu button ( )
Display should read E:1
Press the Menu button ( ) to close the
Menu system. The Span value will be
displayed on exit. As a percentage of the
initial calibration value
Using the Next (increment) button ( )
and the Previous (decrement) button ( ),
set the display to that of the calibration
gas level.
Press the Enter button ( ). This will
“Span” the Sensor.
The display will read (- - - -) to conrm
that the Sensor Span been successful
7.25 psi
(0.5 bar)
250ml/m
9.1 Sensor Calibration Procedure
This manual suits for next models
9
Table of contents
Other NANO Portable Generator manuals
Popular Portable Generator manuals by other brands
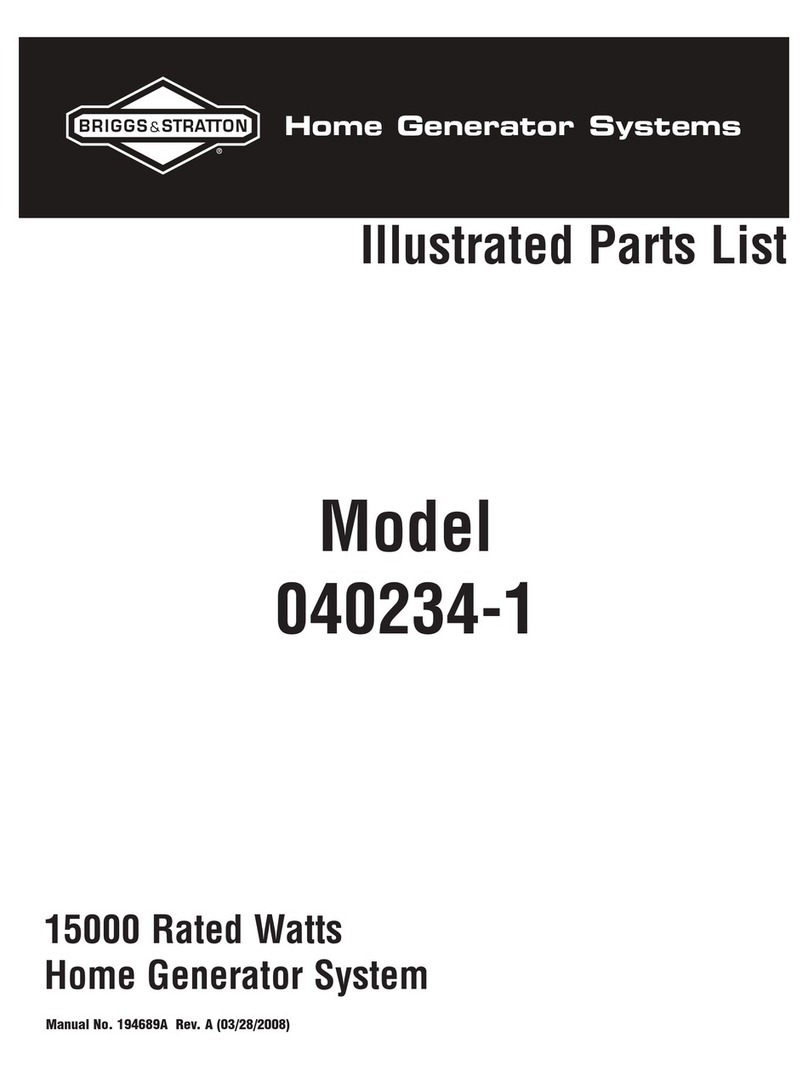
Briggs & Stratton
Briggs & Stratton 040234-1 Illustrated parts list
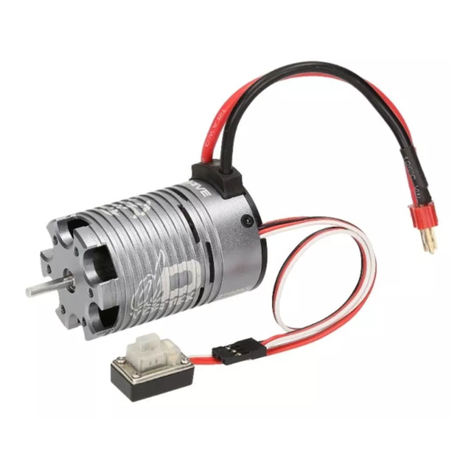
Team Orion
Team Orion dDrive instruction manual
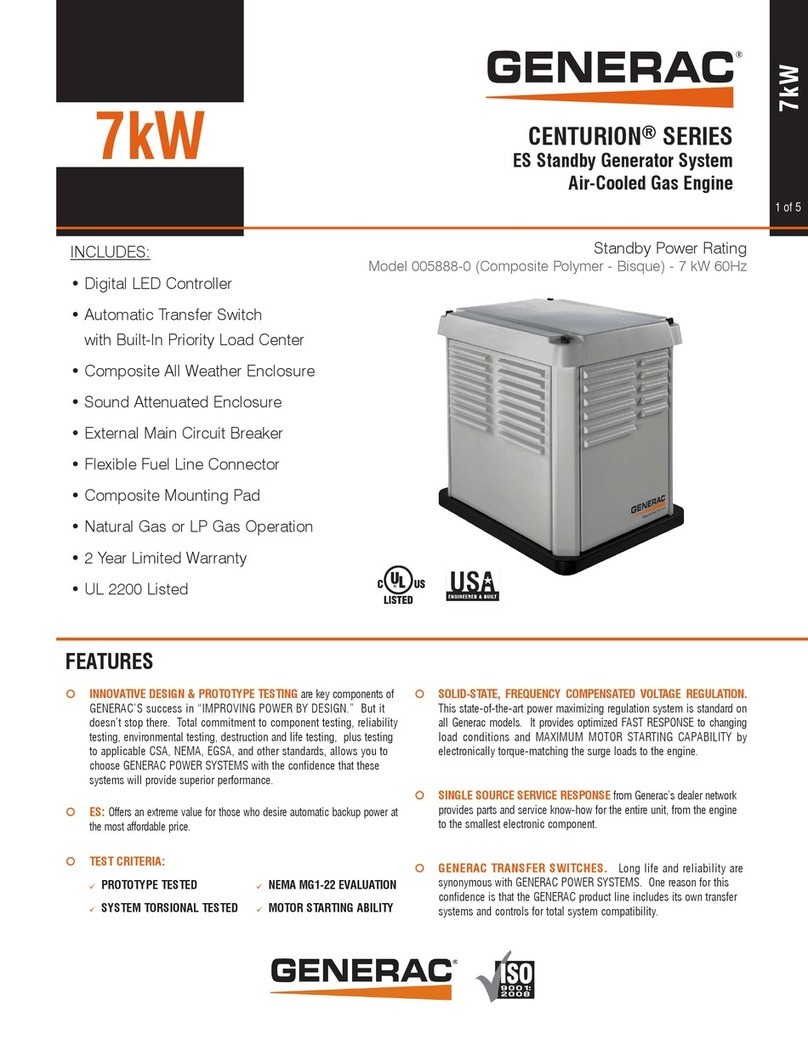
Generac Power Systems
Generac Power Systems CENTURION SERIES specification
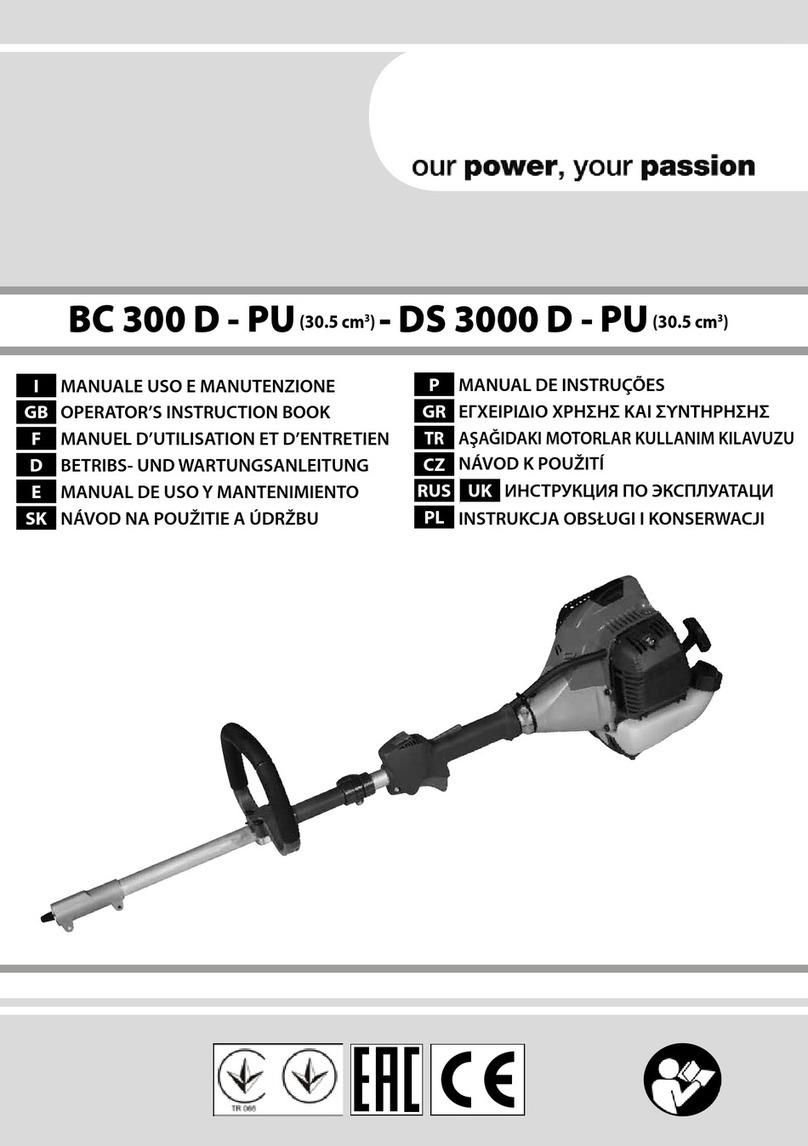
EMAK
EMAK Oleo-Mac BC 300 D-PU Operators instruction book
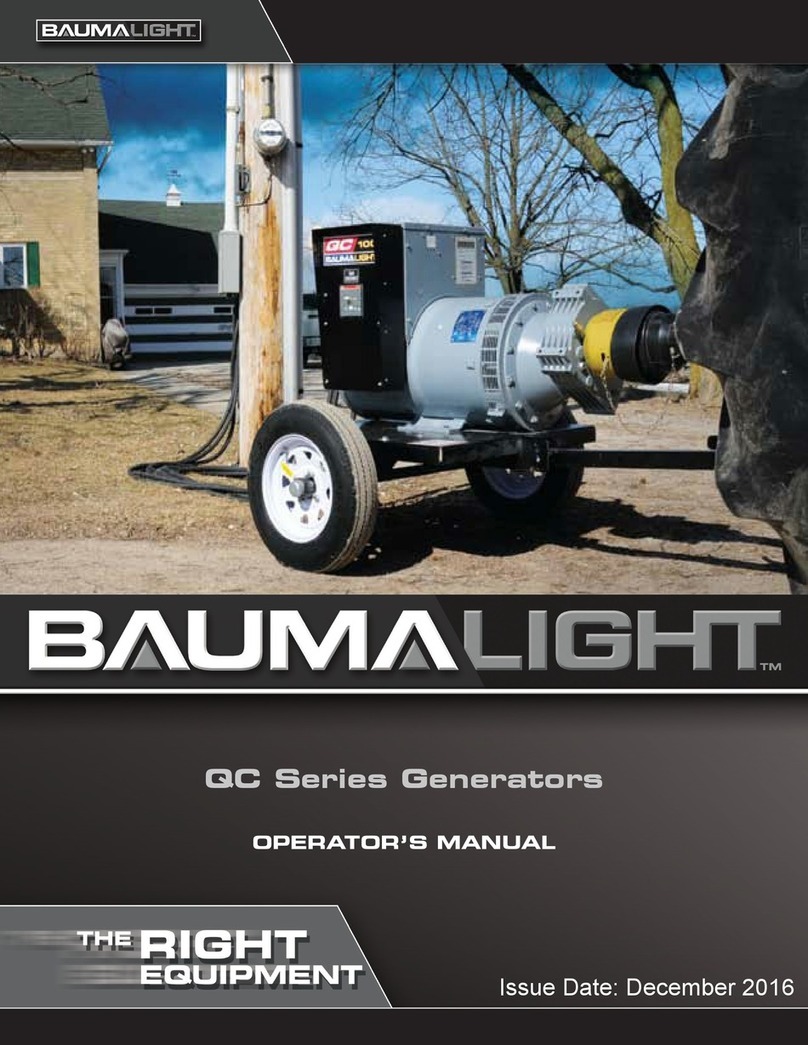
MTB
MTB Baumalight QC Series Operator's manual
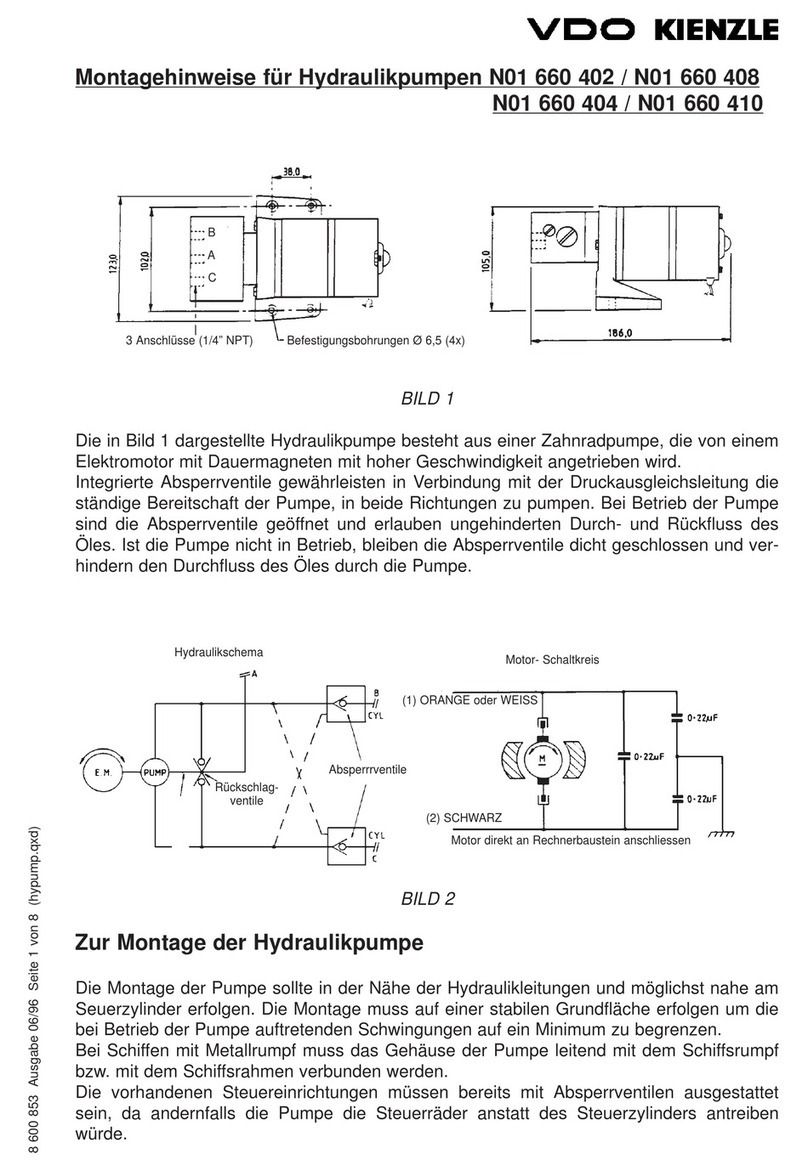
KIENZLE
KIENZLE VDO installation instructions