Nyle L53 Series User manual

www.nyle.com
800-777-6953
Nyle Systems
12 Stevens Rd
Brewer, ME 04412
User Manual
L53 Series
© 2019 Nyle Systems LLC
L53 Manual Version 3.3


Table of Contents
Safety Guidelines............................................................................................................................................................1
Precautions.............................................................................................................................................................................................1
Electrical Grounding............................................................................................................................................................................1
Your Kiln............................................................................................................................................................................2
How your Dehumidication Kiln Works.......................................................................................................................................2
Getting Started................................................................................................................................................................2
Floors......................................................................................................................................................2
Ceilings...................................................................................................................................................2
Doors..............................................................................................................................................2
Construction Guidelines....................................................................................................................................................................3
Equipment Installation.......................................................................................................................................................................4
Chamber Plans.................................................................................................................................................................5
Section View - Section C....................................................................................................................................................................6
Recommended Dimensions.............................................................................................................................................................7
Wall Details..............................................................................................................................................................................................8
Front Elevation......................................................................................................................................................................................9
Door Framing.......................................................................................................................................................................................10
Door Section E....................................................................................................................................................................................11
Door Section F.....................................................................................................................................................................................12
Deectors and Baes.......................................................................................................................................................................13
Door Gasket Installation..................................................................................................................................................................14
Power Vent Wiring Diagram..........................................................................................................................................................15
Power Vent............................................................................................................................................................................................15
Installation...................................................................................................................................................15
Spray System Kit.................................................................................................................................................................................16
Wet and Dry Bulb, Controller Installation and Use..................................................................................................17
Sensor Technology............................................................................................................................................................................17
Dry Bulb Sensor.................................................................................................................................................................................17
Wet Bulb Sensor.................................................................................................................................................................................17
L53 Kiln Controller............................................................................................................................................................................17
How L53 Control Works...................................................................................................................................................................17
Wet Bulb Installation........................................................................................................................................................................18
Using L53..............................................................................................................................................................................................18
Parameters........................................................................................................................................18
Settable Parameters..........................................................................................................................................................................18
Serial Interface....................................................................................................................................................................................19
Alarm Conditions / Messages........................................................................................................................................................19
L53Technical Specications........................................................................................................................................20
Controls Wiring...................................................................................................................................................................................21
L53 Wiring Diagram..........................................................................................................................................................................22
Drying Lumber...............................................................................................................................................................23
Loading the Drying Chamber.........................................................................................................................................................23
Placing Stickers and Loading Lumber........................................................................................................................................23
Insuring Proper Airow...................................................................................................................................................................23
Drying Schedules...............................................................................................................................................................................23
Wood Groups......................................................................................................................................................................................24
LumberTypes.......................................................................................................................................................................................24

Moisture Removal Rates..................................................................................................................................................................24
L53 Drying Schedules......................................................................................................................................................................24
Drying Schedules..........................................................................................................................................................25
Drying Rates (Metric)...................................................................................................................................................26
Drying Rates (North American Measure).................................................................................................................27
Kiln Sample Boards...........................................................................................................................................................................28
Uses for Sample Boards....................................................................................................................................................................28
Taking Samples...................................................................................................................................................................................28
Drying Rate Index (DRI)...................................................................................................................................................................29
Nyle Drying Chart.........................................................................................................................................................31
Drying Tips............................................................................................................................................................................................33
The Kiln Store.................................................................................................................................................................33
Maintenance, Reference Diagrams and Warranty..................................................................................................34
General Maintenance for L53......................................................................................................................................................34
Air Inlet Filters.....................................................................................................................................................................................34
Refrigerant Charging Procedure L53..........................................................................................................................................34
Controller Factory Setting..............................................................................................................................................................35
L 53 Warranty.......................................................................................................................................................................................36
Appendix...............................................................................................................................................37
Terminology...........................................................................................................................................37

1
Do not operate unit if it or any of its parts:
• Have been expose to re.
• Have been submerged in water or exposed to
ooding.
• Have signicant interior or exterior damage.
In the case of any of the above, have the unit serviced by a
qualied professional before continuing operation.
Unit must be grounded.
Failure to ground will result in unreliable performance
or an inoperative unit. Ground by connecting unit
to a grounded metal, permanent wiring system.
Grounding must be in accordance with national and
local electrical codes. Please contact your municipal
oces for more information on building codes.
Safety Guidelines
Precautions
Electrical Grounding
Read through entire manual before installing, operating, or servicing this unit.
Failure to follow any steps or guidelines could result in personal injury, death, destruction
of property or may cause the unit to become inoperable. This manual must be kept with the unit at all times.
Refrigerant!
• Unit contains R-134a refrigerant under high
pressure. Refrigerant must be recovered to relive
pressure before servicing.
• DO NOT use unapproved refrigerants, substitutes
or additives.
• Failure to abide by these guidelines can result in
death, injury and property damages.
• Contact Nyle’s service department for more
information on refrigerant options.
Electrical Shock!
• Turn off power to unit
before service.
•Makesure wires are labeled
before disconnecting.
• Test unit after reconnecting
wires.
• Failure to do the above could result in death or injury.
• DO NOT purge or
pressurize this system with
oxygen to test for leakage.
Using oxygen may cause
explosive reaction.
Explosion Hazard!
High Temperatures!
• Kiln chamber can reach
internal temperatures of
over 90°F. working in these
temperatures can cause heat stroke and minor burns.
• Pregnant women, children, the elderly and those
with signicant health issues are at higher risk of heat
stroke and must be supervised in high temperatures.
• Kiln operators should check for temperature and
take proper safety precautions before entering the
kiln chamber.

2
Thank you for purchasing a Nyle Dehumidication
Kiln and taking the rst step towards making the
lumber industry cleaner and more ecient! Years of
development, innovation and the highest quality
materials have gone into building your kiln, but it’s
our dedication to eciency that sets Nyle System’s
kilns apart from the rest and makes your system the
best on the market.
During kiln drying moisture in green lumber is
evaporated into the air increasing the humidity
inside the chamber. If the air becomes oversaturated
the lumber can’t continue to dry so moisture must
be periodically removed from the chamber. In
a conventional kiln moisture would be expelled
through venting. Venting causes a signicant loss of
heat requiring more energy to bring the kiln back up
to temperature.
Your Nyle Dehumidication Kilns doesn’t waste
energy through venting. Instead a refrigeration
system condenses the excess moisture which is
drained o and the existing heat energy is recovered
to be reused. After the moisture is removed and heat
is reintroduced to the dry air it is pumped back into
the kiln chamber to start the process over. Unlike
conventional kilns the heater in your Nyle Kiln is only
used during the initial warm up and, sometimes,
when temperature increases are desired during the
cycle, saving you time and money. But that’s not all
your new kiln has to oer!
Though Nyle kilns don’t rely on venting to get rid
of moisture, a Vent System is supplied to add extra
control of your kiln temperature. If the internal kiln
temperature exceeds what’s required, these vents
can be opened to remove excess heat and bring the
temperature back to where it needs to be.
And nally Nyle Systems oers a wide variety of
upgrades and accessories to enhance your kiln drying
experience. See the upgrades and accessories section
on page 34 for more information.
Concrete oors with insulation installed underneath
is recommended for best results. However if the
kiln is going to be on an existing concrete oor, the
insulation may be omitted. Concrete must not extend
beyond the kiln walls.
Wood oors may be used but must be built to
construction guidelines (see Pg 3)
If the kiln chamber is a freestanding outside building,
the attic space must be well ventilated through the
eaves. This is done to avoid any moisture buildup
in this space, which will condense on the cold roof,
dripping onto the insulation.
An interior kiln can have the ceiling insulation open
to the atmosphere.
Build ceilings to construction guidelines. (Pg 3)
At the front of the kiln chamber install bay/loading
doors with at least two sides hinges, and a center
door latch to close (recommended). Top hinged or a
lift o doors are also acceptable.
At least one access door should be installed in
the back of the chamber to allow for service of the
dehumidier and/or lumber monitoring.
All installed doors must:
• Be built to construction guidelines. However they
may be lightened by increasing the stud spacing and
using 3/8” plywood. The lighter weight will reduce
the load on the hinges
Please read through carefully as some options
may not apply.
By purchasing a Nyle Kiln you have the support of
Nyle’s service team, the very same professionals that
built and tested your unit. Enjoy your new system!
Your Kiln
Getting Started
How your Dehumidication Kiln Works
Floors
Ceilings
Doors

3
• Have a vapor barrier.
• Have gaskets wherever the door meets the kiln; this
will give a good, airtight t.
• Have a scraper type weather strip to reduce air
leakage if door sill is not present.
• Close tightly against the gasket using turnbuckles,
tarp straps, lag studs with wing nut, etc.
Remember: There will be considerable expansion and
contraction during kiln use, plan door construction
accordingly.
While outside electronic moisture meters can be used
to avoid entering the kiln, during the drying cycle,
Nyle strongly recommends regular checks inside
the kiln to visually inspect the surface or end checks,
mold, stain and to check with a hand held meter.
Step 4: Cover Thermax with one or two layers of 6 mil
polyethylene, then enclose with ½” CDX or marine
grade plywood.
Step 5: Coat CDX interior surface with “mobile home
or metal roong aluminum paint”
Paint is an asphalt based coating with powdered
aluminum and ber for strength, available in
hardware stores. Re-coat as necessary every year.
Step 6: Finish exterior walls to suit your tastes, but
avoid galvanized steel or other ferrous sidings.
Once you have completed construction of the kiln
chamber install the following air deectors and
baes to control the airow within the chamber.
• Corner deector typically made of plywood used to
help turn the airow.
• Hinged bae that falls from the fan wall, to be held
up during load with a nylon rope. Hinged baes
compensate for dierent load sizes, and allow for
shrinkage of the board pile.
• Bae that closes in the open space for lumber that
does not ll the entire width. This bae can be xed
or portable.
Do not underestimate the eect of this baing, as
correct baing will pay o in more even drying and
faster drying. This more than osets the extra time
and eort to correctly place the baes.
Please reference pg 13 for more information on
deectors and baes.
Please reference Chamber Plans for more information
on construction.
Step 1: Build all walls, ceilings and oors with a 2” x
4” framework, with blue or pink Styrofoam (extruded
polystyrene) friction tted between the studs.
Step 2: Cover the interior face of the studs with a 1”
layer of Celotex Thermax (or for better results two
overlapped ½” layers).
Celotex Thermax is foil faced polyisocyanurate
(urethane) board which is orange or yellow in color
and is available in 4’x 8’ sheets of various thicknesses.
Celotex Thermax is a trade name and similar and
acceptable products are available under other trade
names.
If you want to use spray foam insulation, urethane
based only applied at 2.2lb/cu ft. Fiberglass is never
recommended.
Step 3: Caulk joints and nail heads with high
temperature silicone (optional: apply aluminum tape
over silicone)
Construction Guidelines

4
Please reference Chamber Plans for more information
on installation.
Step 1: Place the dehumidier at the center of the
long wall with the inlet lter facing the board pile.
Step 2: Connect an appropriate length drain hose.
The drain must have a trap.
The dehumidier can be elevated any reasonable
amount to help the drain gravity feed. If the drain
hose extends outside (not to a oor drain in the kiln)
the wall opening should be sealed around the hose.
Never have a oor drain.
Step 3: Place the controller at a convenient point
outside the chamber near the dehumidier.
Step 4: Remove the cover
Step 5: Drill holes in the kiln wall to allow control
cables and separately the sensor wires (inside the
controller) to be carefully routed into the chamber.
Do not route control and sensor wires through the
same hole.
Step 6: Mount the Dry Bulb Temperature Sensor 6 to
12 inches from the wall 4 feet o the oor, at least 3
ft from kiln unit, away from the blower outlet, for an
accurate reading.
Step7: Removethe right side panelofthedehumidier
gaining access to the compressor and terminal strip.
Step 8: Securely connect the control cable to the
dehumidier.
Step 9: Carefully connect each wire to their
corresponding terminal. Do not stretch or over stress
the cable.
Wire insulation is marked with the corresponding
terminal number.
Step 10: Seal holes after wires are installed to keep
moisture from the control box. Seal the holes in the
kiln wall.
Step 11: Install the fans in locations over the lumber
see Chamber Plans as a reference.
Step 12: Install and caulk the vents so that they are
on opposite sides of the fans and at opposite ends of
the kiln.
The vents should be located as shown on the
chamber drawings.
Step 13: With the system switch in OFF position, plug
in the power cable (the special receptacle for the L53
is supplied by Nyle).
Equipment Installation

5
Chamber Plans
12"
MIN.
18" MINIMUM
MAX. BY CUSTOMER
FOR ADEQUATE
WORKING ROOM
RIDGE VENT
2" x 6"
SCREENED VENTSCREENED VENT
DOUBLE 2"x4"
TOP PLATE
EXHAUST VENT BY
NYLE (10"x10" R.O.)
INTAKE VENT BY
NYLE (10"x10" R.O.)
PROVIDE AIR SPACE
BETWEEN INSULATION
AND ROOF
1/2" CDX PLYWOOD
BE SURE OUTSIDE WALL
IS WELL VENTILATED
ANCHOR BOLTS
4'-0" O.C. TYP
LUMBER
PACKAGE
4" CONCRETE PAD
REINFORCED AS
NECESSARY
2 LAYERS OF
2" "CELOTEX" FOIL FACED
POLYISOCYANURATE OR EQUIVALENT
(3 LAYERS OPTIONAL) AT LEAST R30
CDX PLYWOOD
OVER 6 MIL POLY
CDX PLYWOOD
OVER 6 MIL POLY
VAPOR BARRIER
2" BLUE STYROFOAM
W/ 1 LAYER 6 MIL POLY
BETWEEN CONCRETE PAD
AND INSULATION
2" "CELOTEX"
COAT WALLS
AND CEILING
W/ FIBERED
ALUMINUM
ROOF COATING
LAYER OF PLYWOOD TO
PROTECT TOP OF LUMBER
AND SEPARATE AIRFLOW
2" BLUE STYROFOAM
AROUND PERIMETER
AIR
INTAKE
2" "CELOTEX" FOIL
FACED PLOYISOCIANURATE
INSULATED BOARD
AIR FLOW
CDX PLYWOOD
SHEATHING W/
ASPHALT SHINGLES
FLASHING
TREATED SILL
WEATHERPROOF
ENCLOSURE TO
HOUSE CONTROLLER
2"x4" LEDGE TO
CARRY EDGE OF
PLYWOOD ALONG
WALL
2" x 6"
2" x 6"
DEHUMID-
IFIER
*FIBERGLASS INSULATION MAY BE USED
BUT WALL INSULATION MUST HAVE AT LEAST
1-1/2" CLOSED CELL INSULATION AS INSIDE
SHEATHING. THE MINIMUM R-FACTOR SHOULD
BE AT LEAST R-30.
AIR FLOW
SHEET
SCALE
TITLE
CHECKED
DRAWN
PROPRIETARY AND CONFIDENTIAL
THE INFORMATION CONTAINED IN
THISDRAWING IS THE SOLE PROPERTY OF
NYLE SYSTEMS. ANY REPRODUCTION IN
PART OR AS A WHOLEWITHOUT THE
WRITTEN PERMISSION OF NYLE SYSTEMS IS
PROHIBITED.
5
4
3
2
1
DWG FILE NAME
CUSTOMER
12 Stevens Road
Brewer, Maine 04412
Tel: 1-207-989-4335 Fax: 1-207-989-1101
Email: [email protected]
1-800-777-6953
REV
1
L53 KILN CHAMBER
SECTION B
REFERENCE
2/11/2013
INTAKE
EXHAUST

6
Section View - Section C
)
&
:22'(16833257
)25'(+80,',),(5
,17$.(9(17
%2;/2&$7,21
(;+$8679(17
%2;/2&$7,21
,167$//%$))/(%(7:((1
(1'2)3,/($1':$//
7235(9(17$,5)/2:
$,5287
'(+80,',),(5
%$))/(
%$))/(
6+((7
6&$/(
7,7/(
&+(&.('
'5$:1
35235,(7$5<$1'&21),'(17,$/
7+(,1)250$7,21&217$,1(',1
7+,6'5$:,1*,67+(62/(3523(57<2)
1</(6<67(06$1<5(352'8&7,21,1
3$5725$6$:+2/(:,7+2877+(
:5,77(13(50,66,212)1</(6<67(06,6
352+,%,7('
':*),/(1$0(
&86720(5
6WHYHQV5RDG
%UHZHU0DLQH
7HO)D[
(PDLOLQIR#Q\OHFRP
5(9
/.,/1&+$0%(5
6(&7,219,(:
5()(5(1&(
INTAKE
EXHAUST

7
Recommended Dimensions
FT. C E F
300 8 3 26 13 7
500 8 3 42 21 7 12 3 28 14 13 7
750 8 4 46 23 8 12 3 42 21 13 7
1000 8 4 62 31 8 7 12 3
54
27 13 8 7
3/4"

8
Wall Details

9
Front Elevation

10
Door Framing

11
Door Section E

12
Door Section F

13
Deectors and Baes
12” Gap

14
GASKETS AND DOOR KITS AVAILABLE FROM NYLE
Door Gasket Installation

15
Place the dehumidier at the center of the long wall
with the inlet lter facing the board pile. Connect an
appropriate length drain hose. The dehumidier can
be elevated any reasonable amount to help the drain
gravity feed. The drain must have a trap. If the drain
hose extends outside (not to a oor drain in the kiln)
the wall opening should be sealed around the hose.
Place the controller at a convenient point outside the
chamber near the dehumidier. Remove the cover.
Be sure controller is in a space that will not reach
temperatures below freezing. A light bulb located
near the controller and left on during the cold weather
is usually a sucient way to keep it above freezing.
Drill 2 holes in the kiln wall to allow control cables
and the sensor wire (coiled up inside the controller)
to be carefully routed into the chamber. Separate the
sensors from the power.
Mount the temperature sensor 6 to 12 inches from
the wall 4 feet o the oor and 3 feet from kiln unit,
for an accurate reading.
Do not place the sensor near the blower outlet.
Remove the right side panel of the dehumidier
gaining access to the compressor and terminal
strip. Securely connect the control cable to the
dehumidier. Note that each wire is marked with
the terminal number to which it is to be connected.
Carefully connect each wire to the similarly marked
terminal. Ground wire is yellow with a green stripe.
Do not stretch or overstress the cable. Seal the hole in
the kiln wall after the system check out is successfully
concluded.
Install and caulk the vents so that they are on opposite
sides of the fans and at opposite ends of the kiln. The
vents can be mounted to open to the inside or the
outside. It is usually more convenient if it opens to the
outside.
With the system switch in OFF position, plug in the
power cable (the special receptacle for the L53 is
supplied by Nyle).
Install the fans in locations over the lumber as
suggested on the chamber drawings.
The unit is now ready for the check out procedure.
Power Vent Wiring Diagram
Installation
The Power Vent is to be secured to the inside of the
kiln wall with the fan side facing the exterior.
Power Vent
POWER VENT KIT FOR L200H
/ L200M / DH4000
1 OF 1
REV
CUSTOMER
DWG FILE NAME
CHECKED
TITLE
AS
SHEETSCALE
DRAWN BY
NTS
12 Stevens Road
Brewer, Maine 04412
Tel: 1-207-989-4335 Int'l: 1-800-777-6953
Fax: 1-207-989-1101 Email: info@nyle.com
1.0
17
3
L1
L2
MAIN TERMINAL
STRIP IN L200
CONTROL BOX
EXHAUST FAN MOTOR
(220V)
WIRING DIAGRAM FOR
POWER VENT KIT 240V
L200H / L200M / DH4000
115V
N

16
Although not standard on Nyle DH Kilns you may choose to add on this optional Spray System Kit which will
provide extra control when drying. The Sprayers are designed to be automatically activated by the system
when needed and help with regulating the relative humidity within the kiln chamber.
Nyle spray systems are designed to inject into kiln air one gallon of water per hour for every 1000 BF. Because
air temperature aects the quantity of water evaporated (warmer air holds more water vapor), we need to
balance the quantity of water vapor to the kiln capacity. DH units with small heaters will require proportionately
less water than larger units with bigger heating capacity. There are options available for every unit so be sure
that the kit you are purchasing matches the specications for the unit that it will be installed in.
Nyle encourages boosting water pressure to 100 psi for the spray system to have the best results. Commonly
this is done with the use of a jet pump, which can be purchased through Nyle if requested. Contact your Nyle
Sales or Service Representative for more information.
Spray System Kit
16
Table of contents
Popular Fan manuals by other brands

Honeywell Home
Honeywell Home TrueFRESH ERV Professional installation guide
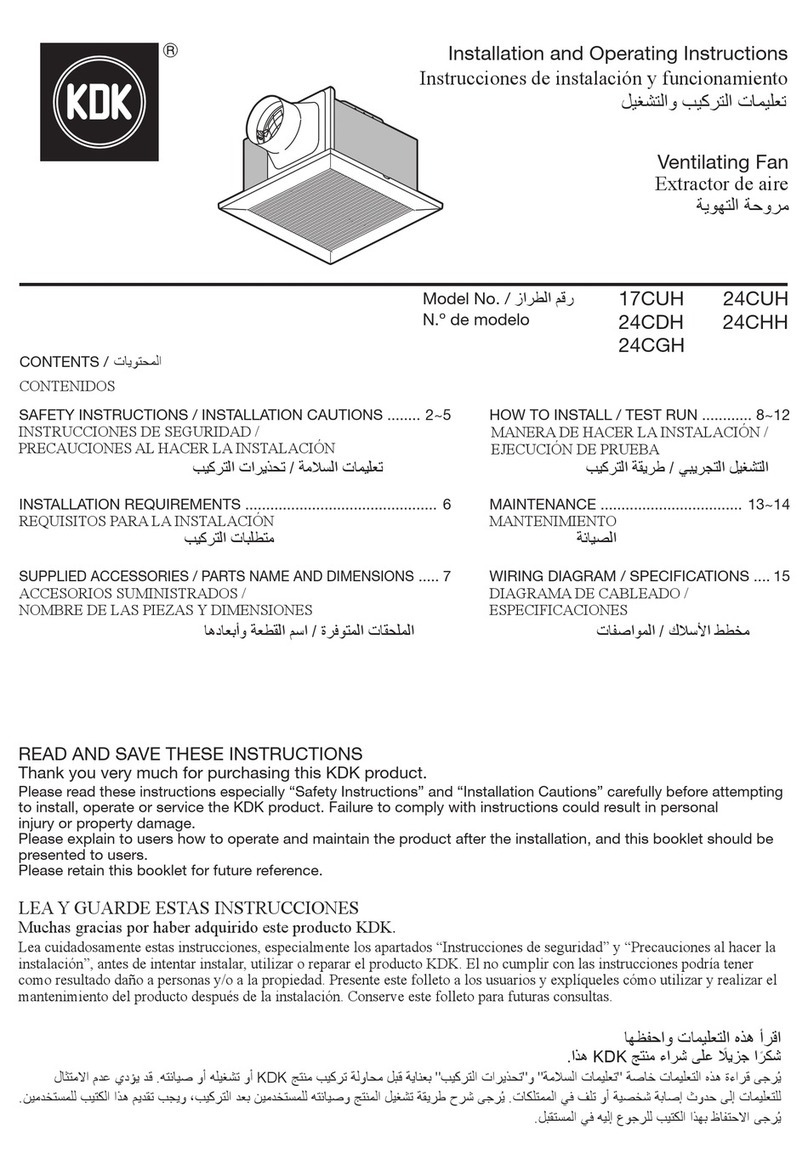
KDK
KDK 17CUH Installation and operating instructions
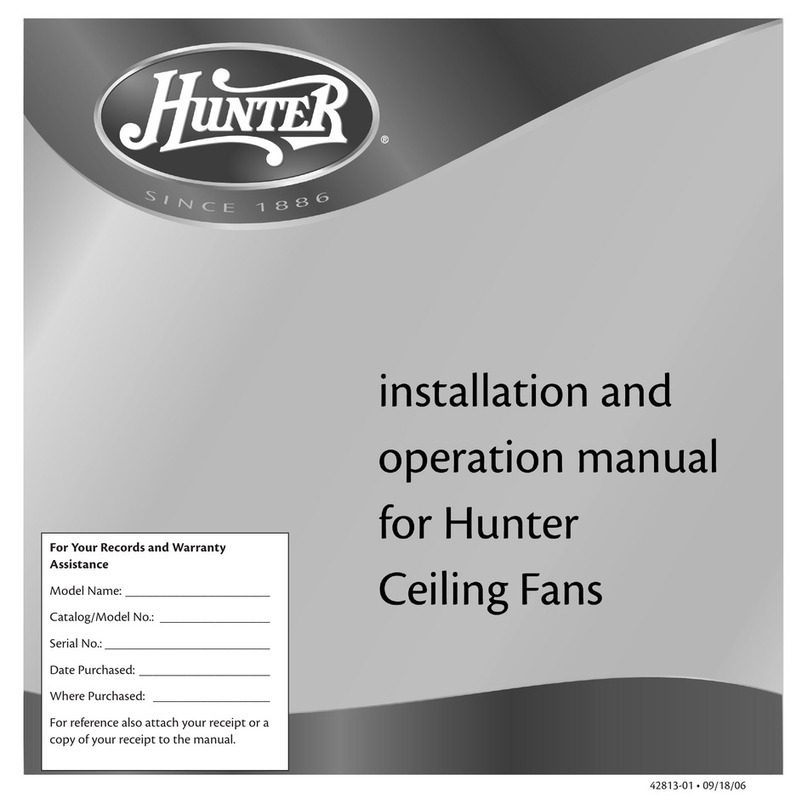
Hunter
Hunter 24852 Installating and operation manual
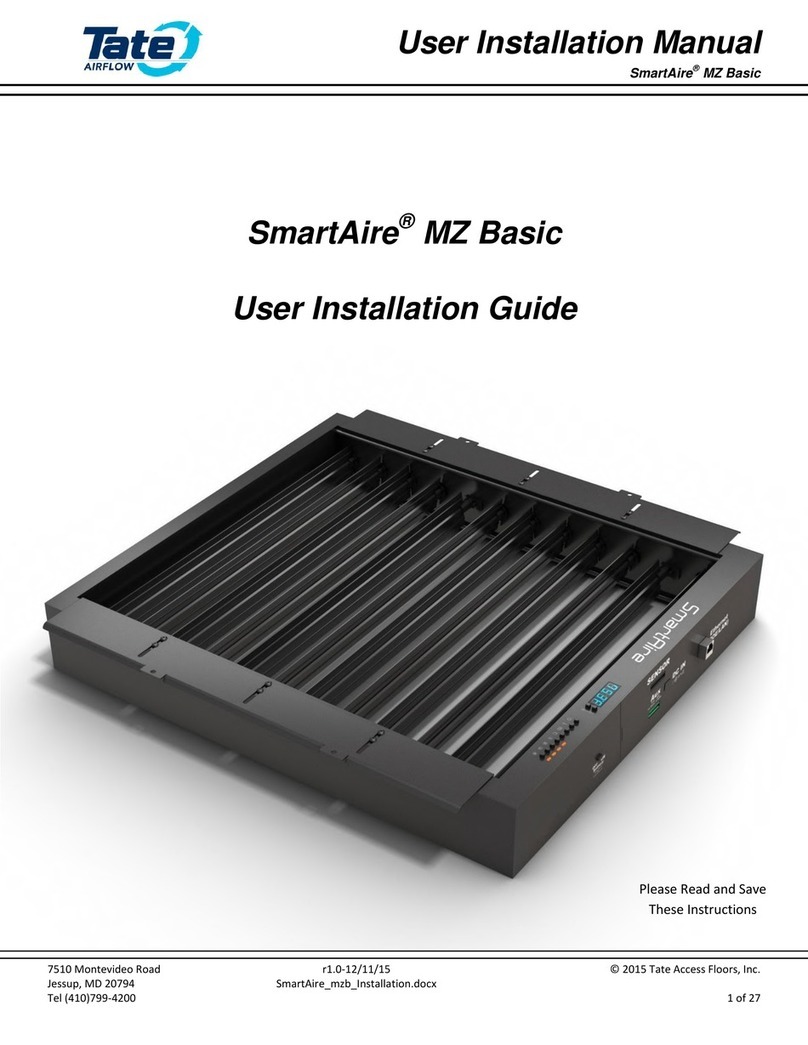
Tate
Tate SmartAire MZ Basic User & installation manual
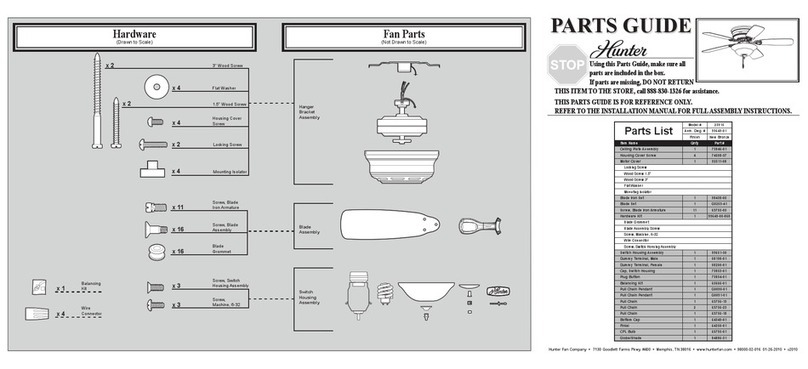
Hunter
Hunter 23915 Parts guide
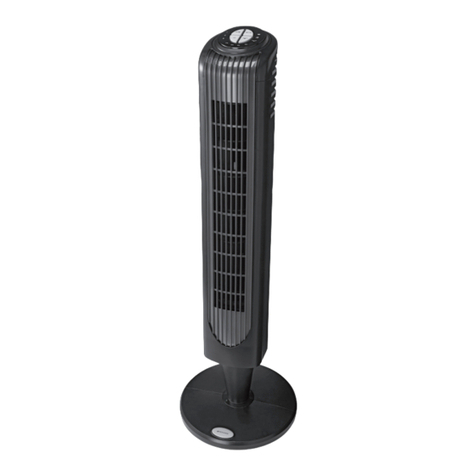
Bionaire
Bionaire BTF3610 Series Instruction leaflet