Octopus RS User manual

INSTALLATION MANUAL
OCTOPUS Type RS
Sailboat Drive
OC15276

OCTOPUS –Type RS Sailboat Drive
OC15276VL REV B.doc Subject to change without notice
2

OCTOPUS –Type RS Sailboat Drive
OC15276VL REV B.doc Subject to change without notice
3
Revision History
Revision
Description
A
Released in Book Format
B
See DCR # 1562
© 2009 Octopus Products Inc. All rights reserved.
The information contained in this document is the sole property of Octopus
Products Inc. Any reproduction in part or whole without the written permission of
Octopus Products Inc. is prohibited. Octopus Products Inc will nor be liable for
errors contained herein or for incidental or consequential damages in connection
with the furnishing, performance or use of this document.

OCTOPUS –Type RS Sailboat Drive
OC15276VL REV B.doc Subject to change without notice
4
Contents
A1 System Overview 6
A2 IMPORTANT SAFETY INFORMATION 7
A3 Installation Planning 9
B Planning
B1 Determine Mounting Site for Drive Unit 9
B2 Determine Mounting Site for Connection Kit 11
B3 Determine Routing Path for Steering Cable 12
B4 Determine Length of Custom Steering Cable 13
C Installation
C1 Drive Unit –Steering Cable –Spent Cable Tube 14
C2 Cable Connection Kit 17
C3 Electrical Connections 19
C4 Mechanical Calibration 20
D Dockside Set Up 21
E Sea Trial 21
F Maintenance 21
G Steering Cable Maintenance 21
H Installation Envelope & System Specification 22

OCTOPUS –Type RS Sailboat Drive
OC15276VL REV B.doc Subject to change without notice
5

OCTOPUS –Type RS Sailboat Drive
OC15276VL REV B.doc Subject to change without notice
6
A1. SYSTEM OVERVIEW:
1. The Autopilot Drive System makes it easy and economical to install an
automatic pilot on small to medium size sailboats with access to a quadrant or
tiller. The drive system is powerful and fast - capable of delivering over
450Nm/ 300lbs of cable thrust, with a normal H.O. to H.O. time of 12-15
seconds.
2. The system comprises of a drive unit, a steering cable and a connection kit.
The drive unit can be installed in any convenient location. The steering cable
and connection kit transmit the steering forces to the quadrant or tiller.
Standard system steering cable length is 6 feet (2m) –other lengths available
from factory. The drive unit has a drive motor and solenoid clutch which
allows hand steering when disengaged. The drive unit also has a built in
adjustable thrust limiter and an integral rudder feed back (RFB) device.
3. The Type RS Drive is designed to produce a maximum cable push/pull of over
450Nm/300lbs, which requires a peak power of 90 watts. This makes the unit
capable of handling the vast majority of medium size sailboats up to
6500Kg/14300Ib displacement fully laden and 11m/37ft length.
Note: The definition of Fully Laden = The displacement of the yacht including all
added accessories and crew.
STEERING
MECHANISM
STEERING CABLE
CONNECTION KIT
TYPE RS
DRIVE UNIT

OCTOPUS –Type RS Sailboat Drive
OC15276VL REV B.doc Subject to change without notice
7
A2. IMPORTANT INFORMATION
Ensure that the Helmsperson is made aware of the three following safety
features when using the Autopilot.
1. Drive ‘Manual Release’
2. Drive ‘Manual Override’
3. Drive ‘Quick Release’
1. MANUAL RELEASE
A ‘manual release’ feature is included in the drive in case the Autopilot is
switched to manual mode by mistake creating a dangerous manoeuvre
while under sail on a sailboat or violent movement of the steering wheel
on a Power Boat due to propeller action or a trim issue.
The drive unit will maintain the clutched “engaged” when the Autopilot is
switched to “manual” mode. This helps to stop uncontrolled boat swing,
violent steering wheel movement and potentially dangerous manoeuvres.
Manual Release Procedure
The wheel or tiller is required to be moved slightly to disengage the drive.
A small joggle action (turning the wheel from side to side) will release
the clutch and allow manual control.
IMPORTANT
Under normal use the helmsperson should always be ready to take manual
control of the yacht when the Autopilot is returned to manual mode.

OCTOPUS –Type RS Sailboat Drive
OC15276VL REV B.doc Subject to change without notice
8
2. MANUAL OVERRIDE
In the event of UNCONTROLLED automatic steering or other
EMERGENCY situations, automatic return to MANUAL steering is
provided through the operation of a thrust limiter. It is STRONGLY
advised that the helmsperson be formally familiarized with this
MANUAL OVERIDE procedure.
Manual Override Procedure. The helmsperson can overcome the
steering action of the drive unit by exerting force on the steering wheel in
the opposite direction to the drive. With this action the drive unit thrust
limit will ‘slip’ allowing the helmsperson to take control.
3. QUICK RELEASE
The Cable end that attaches to the steering quadrant or Tiller arm has a
quick release pin that can be used to disengage the cable from the main
steering system therefore releasing the Autopilot drive. It is very
important that the helmsperson is formally familiarized with the location
of this during any passage.
To operate –remove hairpin from clevis pin and pull our clevis pin using
attached chain. Note - there may be some pre-load on the clevis pin.
Quick Release
Clevis Pin
RELEASE
PIN
Tiller Arm
Clevis
Steering Cable
Telescope End
Chain Handle

OCTOPUS –Type RS Sailboat Drive
OC15276VL REV B.doc Subject to change without notice
9
A3. INSTALLATION PLANNING:
When planning an installation, it is recommended that you follow 3 or 4 steps:
STEP 1: Determine mounting site for drive unit.
STEP 2: Determine mounting site for connection kit.
STEP 3: Determine routing path for steering cable.
STEP 4: Determine custom steering cable length (only if required).
B1.STEP 1 –Determine Mounting Site for Drive Unit
1. The mounting site should provide adequate space to accommodate the
drive envelope including the entry and exit points for the steering cable.
The drive can be mounted at any angle. See detailed graphics of drive
envelope and mounting samples below. Note that no access for
maintenance purposes is required.
150m
m
150m
m
225m
m
Reversible Cable
Entry/Exit

OCTOPUS –Type RS Sailboat Drive
OC15276VL REV B.doc Subject to change without notice
10
2. The selection of the steering cable entry/exit port does NOT have a
preference. To provide more flexibility for routing the steering cable, the
entry/exit port arrangement can be reversed. If ports are reversed, the
steering direction will also be reversed. To compensate for this, the
Autopilot software or motor wiring can be adjusted.
Reversible Cable
Entry/Exit
TYPICAL HORIZONTAL
MOUNT
Reversible Cable
Entry/Exit
TYPICAL VERTICAL
MOUNT

OCTOPUS –Type RS Sailboat Drive
OC15276VL REV B.doc Subject to change without notice
11
B2.STEP 2 –Determine Mounting Site for Connection Kit
1. The Connection Kit must be mounted to stable hull structure. Any
orientation is acceptable as long as the HO positions do not force the
connection kit beyond its rotation limits. Ideally the connection kit
should be mounted so that the thrust from the steering cable is
perpendicular to the tiller at mid stroke. It is acceptable to mount the
connection kit without using the base plate. The clevis bracket can be
mounted to a separate tiller arm or directly to the quadrant if a suitable
site is available. A thru hole 0.375 diameter is required to attach the
shoulder bolt that is supplied with the standard clevis.
2. See Page 8 for detailed guide and connection options.
3. Some Steering Systems may have an existing built in connection point for
the autopilot drive unit. Consult the factory for custom clevis solutions.
Threaded Guide Tube
(+/- 3 inches of adjustment)
Clevis Bracket
Universal Hub
(rotable 360 degree about vertical axis
+/- 40 degrees from horizontal plane)
Steering Cable
Mounting Plate Bracket
(use of bracket is optional
hub may be installed directly
onto suitable structure)
CONNECTION KIT INSTALLATION
Quick Release
Pin

OCTOPUS –Type RS Sailboat Drive
OC15276VL REV B.doc Subject to change without notice
12
B3. STEP 3 –Determine Routing Path for Steering Cable
1. After establishing locations for Connection Kit & Drive Unit. Routing for
Steering Cable must be determined.
2. The cable routing should take into consideration the extreme movements
of the steering mechanism during HO to HO steering. Maximize the bend
radius and minimize the total number of bends. It is recommended that
bends are no smaller than the minimum bend radius (6”) and that the total
angle of all bends combined be no larger than 270 degrees. See detailed
graphic showing preferred routing and bend definition.
3. Steering Cable length supplied with standard system is 6 feet (2 metres).
Other lengths are available.
‘A’
Dimension
Mid
Stroke
‘B’
Dimension
Preferred Cable Routing
150 mm Min
Radius

OCTOPUS –Type RS Sailboat Drive
OC15276VL REV B.doc Subject to change without notice
13
B4. STEP 4 –If Required - Determine Length of Custom Steering Cable
1. If suitable site for drive unit based on a 6 foot steering cable is not
available. Use a custom cable length.
2. Use a length of rope or electrical cable to simulate the routing.
3. Measure the total length required. See graphic of cable length definition.
EXAMPLE OF STEERING CABLE LENGTH CALCULATION:
Add ‘A’ + ‘B’ dimensions and subtract 4” for a 90 degree bend. Round UP
result to nearest full foot size.
For steering cable x length in feet: order OC15211-XX
Cable Length
Mid Stroke
CABLE LENGTH
DEFINITION

OCTOPUS –Type RS Sailboat Drive
OC15276VL REV B.doc Subject to change without notice
14
C. INSTALLATION
C1. Installation of Drive Unit - Steering Cable & Spent Cable Tube
Step 1 - Install Drive Unit
i. Remove 2 x lock bolts, nuts and washers from ports and retain.
ii. Position drive unit in final location. Verify position by simulating the
steering cable connection whilst steering cable is NOT connected.
iii. Transfer bolt pattern from the drive base plate (4 x 7 mm diameter
holes) into mounting structure.
iv. Remove drive unit and prepare holes in mounting structure to receive
mounting fasteners. Note that this connection does NOT transmit any
steering loads.
v. Re-position drive unit and install fasteners, tighten and torque.

OCTOPUS –Type RS Sailboat Drive
OC15276VL REV B.doc Subject to change without notice
15
Step 2 - Install Steering Cable
i. Either port can be used for steering cable entry. The most convenient
for the installation should be selected. The spent cable tube attaches to
the opposite port. Steering direction can be reversed either by
reversing the motor brush leads or by software in the course computer
setup.
ii. Install steering cable into drive port. Guide inner cable into port and
exert moderate force using 2 hands to drive cable around the driving
hub. This action will back drive the unit and the inner cable will
appear out of the opposite port. To complete the cable installation, the
cable outer jacket will enter the port and butt against the drive housing.
This will enable the insertion of the lock bolt.
iii. Note that undue force required to drive the inner cable around the
driving hub may be caused by the leading edge of the inner cable
gouging into outer face of the nylon guide. Remove the cable and
inspect the leading edge for sharp edges, if possible, twist the cable and
re insert with sharp edge towards inside of radius or using a burr type
tool remove the sharp edges.

OCTOPUS –Type RS Sailboat Drive
OC15276VL REV B.doc Subject to change without notice
16
Step 3 - Install Spent Cable Tube
i. Install spent cable tube in exit port.
ii. Install 2 x lock bolt, nut and washers into ports. Tighten and torque to
40-45 in-lbs (4Nm).

254
413 105
194
MIN
rudder
connection kit
rudder post
tiller arm
It is desirable that the cable connection kit is
set perpendicular to the tiller arm or quadrant
at mid stroke - as shown.
Steering Cable - Ensure that cable nut is fully
tightened onto Connection Kit - NO axial play
allowed. Note that nut has self locking feature
this can cause nut to feel tight before clamping.
shoulder bolt specification
shoulder
11.1 mm -
0.44 in
grip Length 25.4 mm - 1.0 in
thread neck 0.37-24 UNF x 28 mm - 1.1 in
2 x nylon
bushing
thrust
washer
nylock nut
torque to
250 in lb - 28 Nm
clevis
TILLER CONNECTION
ARRANGEMENT
tiller attach point
10.0 mm 0.38 in
thru hole
Steering Cable
Telescopic End
Clevis
Chain Handle
Quick Release
Clevis Pin
QUICK RELEASE
OC15267 REV A.doc 8 Subject to change without notice
C2: Installation of Cable Connection Kit
OCTOPUS - Type RS Sailboat Drive
The drive system can be fitted into much smaller space than
normal linear drives. For optimum performance - closely
following the layout shown below is recommended.
OC15276 REV B.doc 17 Subject to change without notice
OCTOPUS - Type RS Sailboat Drive
2. MANUAL OVERRIDE
In the event of UNCONTROLLED automatic steering or other EMERGENCY situations,
automatic return to MANUAL steering is provided through the operation of the a thrust
limiter. It is STRONGLY advised that the helmsperson be formally familiarized with this
MANUAL OVERIDE procedure.
MANUAL OVERRIDE PROCEDURE: the helmsperson can overcome the steering
action of the drive unit by exerting force on the steering wheel in the opposite direction
to the drive. With this action the drive unit thrust limit device will 'slip' allowing the
helmsperson to take control.
3. QUICK RELEASE
The Cable end that attaches to the steering Quadrant or Tiller arm has a quick
release pin. Removing this pin will disengage the cable from the main steering system
therefore releasing the Autopilot drive. It is VERY IMPORTANT that the helmsperson
is formally familiarized with the operation of this feature during any passage.
To operate - remove hairpin from clevis pin and pull out clevis pin using attached chain.
Note - there may be some pre-load on the clevis pin.

84
267
±105
RETRACTED
A A
steering cable end
133
29 66.5
14.5
(.26 inches)
4 x 6.6
A-A
BRACKET BOLT
PATTERN
267
±105
RETRACTED
55
steering cable end
washer
washer
nylock nut torque to
250 in lbs - 28 Nm
(1/2-20 UNF thread)
bracket
*
9
MAX Grip
washer
washer
nylock nut torque to
250 in lbs - 28 Nm
1/2-20 UNF thread
OC15276 REV B.doc 18 Subject to change without notice
OCTOPUS - TYPE RS Sailboat Drive
There are 2 options for mounting the Universal Hub.
Option 1 - Bracket Mounting
Option 2 - Direct Mounting
* direct mount option requires a
13.5 - 0.53 inch thru hole in
a suitable structural element
OC15267 REV A.doc 7 Subject to change without notice
OCTOPUS - TYPE RS Sailboat Drive
A2. IMPORTANT INFORMATION
Ensure that the Hlmsperson is made aware of the three following safety
features when using the Autopilot.
Drive 'Manual Release'
1.
Drive 'Manual Override'
2.
Drive 'Quick Release'
3.
A"manual release" feature is included in the drive in case the Autopilot is switched
to manual mode by mistake creating a dangerous maneuver while under sail on a
sailboat or violent movement of the steering wheel on a Power Boat due to a trim
issue or propeller action.
The drive unit will maintain clutche "engaged" when the Autopilot is switched to
"manual" mode. This helps to stop uncontrolled boat swing, violent steering wheel
movement and potentially dangerous maneuvers.
MANUAL RELEASE PROCEDURE: The Wheel/Tiller must be sharply moved a
small amount in both directions to disengage the drive. This small joggle action will
release the clutch and allow manual control.
IMPORTANT: Under normal use the helmsperson should always be ready to take
manual control of the steering when the Autopilot is returned to manual mode.
1. MANUAL RELEASE

OCTOPUS –Type RS Sailboat Drive
OC15276VL REV B.doc Subject to change without notice
19
C3. Electrical Connections
Step 1 - Cable Motor and Clutch Power Supply
i. Following Auto Pilot installation guide and wiring diagram, connect
4 x 10 AWG wires with Auto Pilot junction box.
ii. Following Auto Pilot installation guide, perform electrical tests.
Step 2 - Rudder Feed Back Signal Cable
i. Following Auto Pilot installation guide and wiring diagram, connect
2 x 24 AWG wires + shield core with Auto Pilot junction box. See
Hook Up Table for common autopilots
ii. Following Auto Pilot installation guide, perform electrical tests.
RFB –CABLE HOOK UP TABLE
OCTOPUS
RAYMARINE
NAVMAN
SIMRAD
Red
Red
Orange
Use OC15222
See Separate
Wiring Guide
Black
Blue
Black
White
Green
Blue
Shield
Silver
Black
Clutch (white) -12v
Clutch (Green) + 12v
Motor (Red) +12v
Motor (Black) - 12v
Suppression bead
Do not remove
MOTOR & CLUTCH CABLE
Pot Pin 1 (black)
0 volts
Pot Pin 3 (red)
+5volts
Pot Pin 2 (white)
slider
RFB CABLE

OCTOPUS –Type RS Sailboat Drive
OC15276VL REV B.doc Subject to change without notice
20
C4: MECHANICAL CALIBRATION PROCEDURE
1. Disassemble the RFB
module from the drive housing,
by removing 2 attach screws.
2. Complete the installation of the
drive unit into the vessel and
install the remote steering cable
following the drive installation
guide.
3. Complete the electrical hook up
of the drive following the drive-autopilot installation guide.
4. Complete the electrical hook up of the RFB
module following the drive-autopilot installation
guide.
5. Center the gear on the RFB module by aligning the
red paint mark on the gear with the red paint mark
on the housing as shown in underside view graphic
below.
6. By turning the steering wheel of the helm unit, centre the
rudder.
7. Reassemble the RFB module to the drive housing and
install and tighten the 2 attach screws. Ensure that the
mesh between the RFB module and the drive gear is not
excessive.
8. See autopilot installation guide for instructions on
additional software controlled RFB fine calibration and
HO limitation.
RFB MODULE
UNDERSIDE
VIEW
Align 2 red
dots vertically
COMPLETE
INSTALLATION
Table of contents
Popular DC Drive manuals by other brands
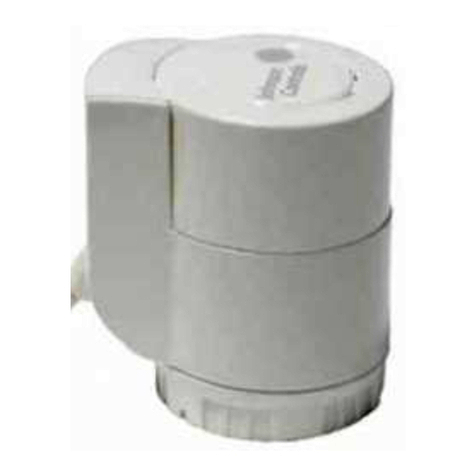
Johnson Controls
Johnson Controls VA-707 Series Fitting instructions

Siemens
Siemens SINAMICS G130 operating instructions

ABB
ABB ACQ580-31 Series Quick installation and start-up guide

Danfoss
Danfoss VLT AQUA Drive FC 200 instruction manual
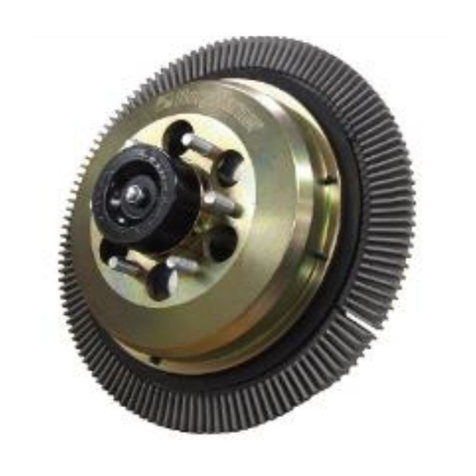
Borg Warner
Borg Warner DuroSpeed Series Installation & service guide
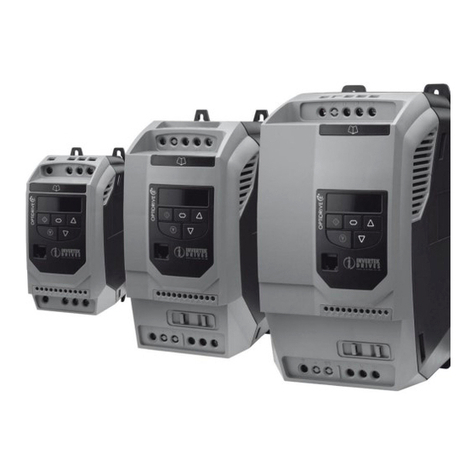
Invertek Drives
Invertek Drives Optidrive ODE-2-12005-1H01 01 Series user guide