Ofs Softening Control User manual

Softening Control
Instruction Manual
Version 1.13


3
Index
1. Manufacturer................................................................................................................5
2. Correct usage in accordance with regulations..............................................................5
3. Warranty.......................................................................................................................5
4. Liability........................................................................................................................5
5. Terms of license...........................................................................................................6
6. General safety instructions...........................................................................................6
6.1 Symbols........................................................................................................................6
6.2 Operating personnel.....................................................................................................6
6.3 Safety requirements......................................................................................................7
7. General overview of the device ...................................................................................8
8. Characteristics..............................................................................................................9
9. Installation..................................................................................................................10
9.1 Mechanical installation ..............................................................................................10
9.2 Hydraulic installation.................................................................................................10
9.2.1 Scheme hydraulic installation....................................................................................11
9.3 Electrical installation..................................................................................................12
9.3.1 Connection of power supply ......................................................................................12
9.3.2 Output water hardness by active current loop............................................................12
9.3.3 Connection ON / OFF signal .....................................................................................12
9.3.4 External signalling by potential free contact..............................................................13
9.3.5 Connection external closer for activation of measurement........................................14
9.3.6 Connection of water meter.........................................................................................14
9.3.6.1 Connection mechanical water meter..........................................................................14
9.3.6.2 Connection electronic water meter (turbine with Hall-contacts)...............................14
9.3.7 Overview electrical connections................................................................................15
10. Commissioning ..........................................................................................................16
10.1 Setting of DIP-Switches.............................................................................................16
10.2 Explanation of LED-Display .....................................................................................18
10.2.1 Explanation of LED-status for displaying of water hardness evaluation...................18
10.2.2 Explanation of LED-status for displaying of functional status..................................19
10.3 Operating tests............................................................................................................20
10.3.1 Test of water quality ..................................................................................................20
10.3.2 Test of external signaling...........................................................................................20
10.3.3 Test sensor performance ............................................................................................20
11. Service........................................................................................................................21
11.1 Delivery/Transport/Storage of hardness sensor.........................................................21
11.2 Operating conditions of the sensor.............................................................................22
11.3 Sensor mounting/Sensor replacement........................................................................22
11.4 Malfunction/Breakdown of sensor.............................................................................23
12. Malfunctions and possible causes..............................................................................24
13. Decommissioning.......................................................................................................25
14. Dismounting...............................................................................................................25
15. Sensor system.............................................................................................................25
16. Accessories.................................................................................................................25
17. Technical data ............................................................................................................26
18. EU-Declaration of conformity ...................................................................................27

4

5
1. Manufacturer
OFS Online Fluid Sensoric GmbH
Gesellschaft für analytische und meßtechnische Systeme
Heidelbergweg 9
07580 Ronneburg
Germany
Phone: +49 36602 51 24-0
Fax: +49 36602 51 24-29
www.water-monitoring.com
2. Correct usage in accordance with regulations
Softening Control monitors a parameterizable threshold value of residual water hardness in
soft water of softening plants based on cation exchange. It provides a gradual percentage
monitoring of the water hardness threshold values from 0.25% to 10% of the input water
hardness.
3. Warranty
The manufacturer provides a warranty for its products of 2 years from delivery date.
From this warranty the measuring sensor is excluded.
The warranty expires in the case of:
incorrect installation or operation, resp. maintenance
incorrect or unauthorized intervention of the device or its components
incorrect analytical, mechanical or electrical effects of any kind
damages or subsequent damages due to incorrect operating
damages or subsequent damages due to incorrect or unauthorized connection of systems to
the control circuit
damages or subsequent damages traced back to low sample liquid quality.
4. Liability
The manufacturer accepts no liability for up or down streamed facilities and processes caus-
ing malfunction, failures, damages or subsequent damages, which are directly or indirectly
connected to the control circuit of the device or having or could have an effect and which lead
back to malfunctions or failures of the device.
The liability disclaimer is based on the possibility that electrical impulses and currents, inor-
ganic and organic precipitations, sedimentation of corrosion or oxidation materials, microbio-
logical loads, flocculation or digestion may appear in the sample liquid, unnoticed by the user.

6
5. Terms of license
On purchase, the user acquires an exclusive non-transferable right of use for the installed
software. The use is permitted for the operation of the purchased device only. Any other use,
transmission, copying or recompilation of the software is prohibited. Equal conditions apply
for software updates.
6. General safety instructions
6.1 Symbols
Important information in this manual are marked by the following symbols. This information
are of particular importance for a safe and hazard-free operation of the device.
Caution! With disregarding of so marked information the device or sensor
could be damaged.
Warning! The disregarding of so marked information may cause injuries or
property damages.
Danger of fatal injury or damages from electrical current! Information
marked with this sign must be observed absolutely. The disregarding of this in-
formation may cause damages at the device, fatal injuries or property damages.
6.2 Operating personnel
The unit is to install and operate only by personnel who have been trained and authorized pre-
viously. They must have read and understood this manual. The following safety instructions
must be observed strictly.

7
6.3 Safety requirements
The measuring device is set up as wall mounted unit and must be installed ac-
cording to installation instruction.
It should be operated in rooms with a relative humidity between 20 % and 60
% and an ambient temperature between 5°C and 50°C. It must be ensured that
condensation can not form in the housing.
Operation in connection with ionization or electrolysis units is not permitted.
The device must be protected against liquids and unauthorized mechanical or
electrical intervention.
The device may be operated only with a safety extra-low voltage of 24 V DC
respectively with the wall power supply for 230 V AC provided by the manu-
facturer.
The mechanical installation and commissioning must be carried out with the
power disconnected.
The electrical connection to external control equipment and instrumentation
must not exceed the specified voltage.
The raw water and soft water of the monitored or controlled process must cor-
respond to the relevant drinking water specifications.
During operation a constant water pressure of minimum 1 up to maximum 10
bars on the samplers is to ensure. The difference between raw and soft water
pressure should be as low as possible.
The sample liquids should be free of any particles, otherwise flow filters of ≤
0.1 mm has to be installed up streamed to the sampling units.
The electric power must be disconnected from the unit prior to the removal of
the sensor from the measuring chamber.
The system is under water pressure up to the solenoid valves. The raw and soft
water inlet must be cut off prior to carrying out any maintenance work on the
solenoid valves or dismantling the measuring unit.
Any time the unit is taken out of service, the sensor needs to be removed from
the device and stored correctly.
The Manufacturer reserves the right to make any technical changes to reflect
further developments.

8
7. General overview of the device
Softening Control is an online water hardness measuring system for continuous monitoring of
water hardness differences between process inlet and process outlet of a connected water sof-
tening system based on cation exchange.
By using of bypass technology the device extracts time controlled or flow rate depending
minimal amounts of raw or soft water from the process, evaluates the residual hardness and
alerts with exceeding of a preset threshold value. The threshold value can be parameterized by
DIP-Switches with individually defined steps of 0.25% up to 10% residual hardness in refer-
ence to 100% raw water hardness.
The measurements will be carried out cyclically every 15 minutes in a flow-through chamber
where a selective sensor for calcium and magnesium ions operates in an environment protect-
ed against pressure. In each measurement cycle the water sample stays a preset period in the
measurement chamber and will be evaluated after a preset resting time. The measurement
cycle can be controlled alternatively by impulses of a connected water meter or a potential
free closer.
By automatic opening and closing of the upstream stop valves the water samples will be re-
placed and rejected free of pressure. With exceeding of threshold value a potential free switch
will be activated with a delay of 1or 10 minutes. With recognizing of an interference or need
of sensor exchange a second potential free switch will be activated.
Measuring functions and their results are represented with colored LEDs. At the same time
the measurement value will put out through a current loop 4…20mA.
In intervals of five days the sensor quality will be checked. If the result does not comply with
the predefined minimum requirements, the need for sensor exchange will be signalized.
optional
connection water meter
optional
external signal output
power supply unit
100 … 240 V AC
50 … 60 Hz
reserve connection
raw water
measurement chamber
Ventil RW
Ventil WW
soft water
sensor
valve
raw water
filter
V
softener
raw water
soft water
pressure
free drain
valve
soft water
filter

9
Once a day a sensor forming will take place in row water, which purposes of an increasement
of the sensors service quality. The sensor forming will take 17 minutes. During this time no
water hardness measurement will take place.
The measurement system can set in off-line-mode by a connected potential free closer. In this
mode no measurement will take place.
The measuring system is automatically calibrated by time controlled automatic change over
from soft water to raw water. There is no need for additional indicators or reagents.
8. Characteristics
Water hardness of raw water will be defined automatically with 100%.
Water hardness of soft water will be determined in percentages and rated to a fixed
threshold value, given by a DIP-switch.
The difference value shows the actual efficiency of the softening plant.
The threshold value can be defined individually in steps of 0.25% up to 10% in refer-
ence to the row water hardness.
Displaying of the measurement results by colored LEDs in traffic lights position.
Possibility for connection for monitoring of an external mechanical contact water meter
at outlet of softener system with an impulse sequence ~ 1 second/impulse
Time controlled cyclic measuring with measuring breaks of 15 minutes between two
measurements or process controlled continuous measuring when soft water is being re-
leased and the contact water meter is registering impulses
Parameterizing by DIP-Switches at the device
Detection of high brine concentration in soft water
Self monitoring of hardness sensor with signaling on need for replacement
Output of indicated value through 4 to 20 mA current loop

10
9. Installation
9.1 Mechanical installation
Softening Control must be installed in close proximity to the softening system to be moni-
tored. Installation is possible as wall or base frame mounted device with an installation space
of 300 x 300 x 150 mm (wide x height x depth), preferably at eye level. For installation at the
mounting area the mounting hole at the device case are to be used. Fitting accessories are to
be provided on site.
For sampling of raw and soft water branch pipes with preferable ¼” internal thread and pre-
filter of ≤ 0.1mm should be installed at the process inlet and process outlet of the softening
system. Further it must be pointed out that during operation the device must be provided per-
manently with a water pressure of minimum 1 bar up to 10 bars.
After selection of mounting area and pre-installation of mounting screws and electrical con-
nections by removing the back panel, the device can be installed easily.
9.2 Hydraulic installation
The hydraulic installation of inlets, outlet and hardness sensor is only to be carried out after
the unit has been fixed at the wall resp. frame as following:
1. Push raw water hose Ø 4 mm (blue hose) as far as it will go into the pre-installed plug-in
connector “RW” outside of the casing
2. Push soft water hose Ø 4 mm (black hose) as far as it will go into the pre-installed plug-
in connector “SW” outside of the casing
Do not forget the prefilters!
3. Push the drainage tube Ø 6 mm tightly into the T-fitting at the outlet of the measurement
chamber
4. Plug the sensor socket of the sensor system into the electrical connection of the flow
measurement chamber at the device and fix it with the safety bolt
5. Push the analytical side of the sensor tightly into the T-fitting
Do not touch or damage the electrodes!
6. Open up streamed raw and soft water stop valve and check leak-tightness of the installed
raw and soft water hoses
The system is now subject to water pressure up to the closed valves RW and
WW.
7. If the pressure test is successful, the installation has been completed.

11
9.2.1 Scheme hydraulic installation
Note:
The pre-filters may not be necessary if existing filter systems (≤ 0.1 mm) are able to remove
dirt which would otherwise reach the sampling valves.
optional
connection water meter
optional
external signal output
power supply unit
100 … 240 V AC
50 … 60 Hz
reserve connection
measurement chamber
Ventil RW
Ventil
WW
soft water
fensor
valve
raw water
V
softener
raw water
soft water
pressure
free drain
valve
soft water
3
5
4
2
1
raw water
filter
filter

12
9.3 Electrical installation
For the connection of the operating voltage and the external signal lines the back panel of the
device has to be removed and the four M12 screw joints, placed at the sidewall of the device,
have to be used. The cable ends must be equipped with wire end ferrules with a maximum cross
section of 0.5 mm²and placed in the device according to the following descriptions.
9.3.1 Connection of power supply
The supply voltage of 24 Volt DC will is to connect at the terminals 31/32. An electrical in-
stalled load of 5 Watt is necessary. The terminal 31 has the positive and the terminal 32 the
negative potential. An operation with 230 Volt AC is allowed only with the power supply unit
provided by the manufacturer.
Note:
For applications in industrial surroundings with high electrical leakages current it is recom-
mended to connect the device to an additional protective grounding.
9.3.2 Output water hardness by active current loop
The signal is a coded residual hardness signal and the current of 4 …20 mA represents a re-
sidual water hardness in the range of 0 …2% or 0 …10%. The current loop 4 ... 20 mA is
connected to the terminals 17/18. The terminal 17 represents the positive and terminal 18 the
negative potential.
The following external requirements for electrical connections have to be complied.
External requirements: do not connect external voltage
use passive loop resistance of maximum 250 OHMS
9.3.3 Connection ON / OFF signal
Softening Control is staying in ON-mode as long as there is no short circuit between the ter-
minals 20/21. It will stay on OFF-mode while both terminals are connected. In this state no
measurement will be done. With termination of the OFF-Line mode and before starting of the
normal measurement operation, the sensor stays in soft water for 1 minute.
The OFF-Line mode should be used for some minutes or hours only, for avoid-
ing a non-monitoring of the softening plant as well to protect the sensor system
against germs.
ON-Line-Mode
20 21
OFF-Line-Mode
20 21

13
9.3.4 External signalling by potential free contact
The external threshold value excess alarm and the brine alarm are connected to terminals 1/2-
3, and the external service alarm is connected to terminals 4/5-6.
The service alarm is a summery alarm, which can be caused by:
-low sensor performance
-there is no electrical contact to the sensor
-valves do not work properly.
It is indicated by flashing LEDs, which of the above failure caused the service alarm (see also
chapter “Explanation of LED-status for displaying of functional status” and “Malfunctions
and possible causes”).
The following external electrical requirements must absolutely be fulfilled:
External requirements: maximum connection voltage 24 Volt
maximum current 0.5 Ampere
Contact positions in voltage-free positions:
The logical behavior is shown in the following table:
Signal status
Terminals
Contact
state
Power cut or threshold value exceeding or brine inrush
1/3
closed
Power cut or threshold value exceeding or brine inrush
1/2
open
Power cut or service alarm
4/6
closed
Power cut or service alarm
4/5
open
1 3 2
Switch setting
Threshold value exceeding
or brine solution alarm
4 6 5
Switch setting
service alarm

14
9.3.5 Connection external closer for activation of measurement
Instead of a water meter an external closer can be connected at terminal 23 and 24. Measure-
ments will be carried out as long as the contact is closed. In contrast to the use of the ON/OFF
contact the measurements starts immediately with soft water samples.
The sensor quality will be determined automatically, even if measurements are not activated.
Therefore raw and soft water pressure should be present at the sampling point.
9.3.6 Connection of water meter
For a continuous monitoring during the soft water sampling and to avoid threshold value ex-
ceeding alarm caused of the so-called „hardness breakthrough“ it is recommend to monitor
the soft water sampling not within fixed time distances. Therefore it is possible to connect a
mechanical or electrical water meter to the device.
9.3.6.1 Connection mechanical water meter
The water meter to be connected must be equipped with potential free contacts. The electrical
connection is to realize at terminals 23 and 24 of the controller card. If the measurement
should be activated by a potential free closer, it has to be connected at the same terminals (23
and 24).
9.3.6.2 Connection electronic water meter (turbine with Hall-contacts)
The electronic water meter is to connect at the terminal 24, 25 and 26 of the controller card.
Attention should be paid to the correct polarity.
Terminal 25 + VCC
Terminal 24 GND
Terminal 26 Impulses

15
9.3.7 Overview electrical connections
Terminal
Configuration
Explanation
1
Relay 1 COM
Threshold value alarm
2
Relay 1 S
at alarm: Terminal1/2 open - Terminal 1/3 closed
3
Relay 1 Ö
4
Relay 2 COM
Service alarm
5
Relay 2 S
at alarm: Terminal 4/5 open - Terminal 4/6 closed
6
Relay 2 Ö
17
4 ... 20 mA -
Loop resistor < 250 Ohm
18
4 ... 20 mA +
Loop resistor < 250 Ohm
20
Offline-contact
Potential free contact
21
Offline-contact
Potential free contact
23
Water meter or
potential free closer
Potential free contact
24
Water meter or
potential free closer
Potential free contact
24
Electronic water meter
GND
25
Electronic water meter
+VCC
26
Electronic water meter
Impulse
27
RS 232 - Tx
Optional
28
RS 232 - Rx
Optional
29
RS 232 - GND
Optional
31
Operating voltage
+24 Volt DC
32
Operating voltage
-24 Volt DC

16
10. Commissioning
10.1 Setting of DIP-Switches
Prior to commissioning of Softening Control the correct installation and connections to the
softening system must be checked again. This includes the softener system should be operat-
ing and adequate soft water quality should be available at the outlet.
Then, basically, it is to decide if the device
monitors time or process controlled. Accord-
ing this decision a connection of contact wa-
ter meter and setting of DIP switch 4 is to
realize.
The threshold value to be monitored is to set
up with the DIP-switches 1-3.
The following process parameters are relevant and have to be set as parameters manually us-
ing the DIP-switches:
Process parameter
Value range
DIP-switches
Threshold value
for soft water hardness in %
in reference to raw water hardness
0.25 % to 10 %
1 , 2 , 3
Measuring interval
Time distance
between 2 measurements
time controlled
or
process controlled
4
Current loop resolution
20 mA = 2%
or 10 %
5
DIP-Switches

17
Setting of threshold value in % in reference to the raw water hardness
Setting of measuring cycle
Setting of power circuit
Parameterization external alarm delay
Parameterization activation measurement by connected water meter or external
potential free contact
Precondition: DIP 4 must be set on OFF-position
Note: Parameters marked with “*” are factory settings.
DIP 1
DIP 2
DIP 3
Threshold
value
Example: With a raw water hardness of
5.0 mmol/l alarm will be signalized at:
ON
ON
ON
0.25%
0.013 mmol/l
OFF
ON
ON
0.50%
0.025 mmol/l
OFF
ON
OFF
1.00%
0.05 mmol/l
OFF
OFF
ON
2.00%*
0.10 mmol/l
ON
OFF
ON
4.00%
0.20 mmol/l
ON
ON
OFF
6.00%
0.30 mmol/l
ON
OFF
OFF
8.00%
0.40 mmol/l
OFF
OFF
OFF
10.00%
0.5 mmol/l
DIP 4
Measuring interval
ON
15 Minutes*
OFF
Water meter
DIP 5
Power circuit
ON
20 mA = 2%
OFF
20 mA = 10 %*
DIP 6
Alarm delay
ON
10 minutes
OFF
1 minute*
DIP 7
Activation Measurement
ON
external closer at terminal 23/24
OFF
water meter impulses*

18
10.2 Explanation of LED-Display
The visual display will be shown by green, yellow and red LED, whereas the hardness evalua-
tion will be indicated through luminescent LEDs and the functional status through flashing
LEDs.
10.2.1 Explanation of LED-status for displaying of water hardness evaluation
The optical display and evaluation are based on the pre-set threshold value.
Hereby the row water hardness is committed to 100% as absolute value. The progression of
water hardness will be evaluated accordingly.
LED-Display
Evaluation
Example
green LED lights up
water hardness < 80 % threshold value
threshold value = 1 %
water hardness < 0,8 %
green and yellow LED are lighting up
water hardness < 90 % threshold value
threshold value = 1 %
water hardness < 0,9 %
yellow LED lights up
water hardness reaches the threshold value
threshold value = 1 %
water hardness approx. 1
%
yellow and red LED are lighting up
water hardness < 110 % threshold value
delayed threshold value alarm
according to DIP 6 parameterization
threshold value = 1 %
water hardness < 1 %
red LED lights up
water hardness > 110 % threshold value
released threshold value alarm
according to DIP 6 parameterization
Threshold value = 1 %
Water hardness > 1 %

19
10.2.2 Explanation of LED-status for displaying of functional status
The actual functional status of the measurement device will be shown by flashing LEDs.
LED-Display
Evaluation
Comment
green LED is flashing
Measurement
Measurement for reclassification of
residual hardness is activated
green and yellow LED are flashing
Calibration mode
Measurement system is calibrating
resp. verifying the exceeding of the
threshold value
yellow LED is flashing
OFF-Line-Mode
Measurement system was set exter-
nal into OFF-Line-Mode
No hardness evaluation and moni-
toring will be done
yellow and red LED are flashing
soiled valves / leaking
Service alarm!!!
Inadmissible mixture of the water is
recognized, most likely originated
by soiled valves.
check valves for tightness,
clean or change valves
green and red LED is flashing
sensor not recognized
Service alarm!!!
The measuring system has no elec-
trical contact to the hardness sen-
sor.
check the plug-in connection
from hardness sensor to device
red LED is flashing
brine in soft water detected
immediate threshold value
alarm!!!
Brine in soft water recognized.
check softening plant
Attention: too high and long taking
influences of brine will damage the
hardness sensor!
all LEDs are flashing
low sensor quality
Service alarm!!!
low sensor quality chance sensor
Alternatively malfunction of sof-
tening plant during calibration. In
this case check quality of soft water
and re-start measuring device by
interruption of power supply.
In case of recurrence change sen-
sor.
Note: In case of service alarm no hardness measurement is possible.
Are there recognized several alarms at one time, they will be shown according priorities and
order of their elimination.

20
10.3 Operating tests
10.3.1 Test of water quality
By temporary interruption of power supply Softening Control re-starts the measurement and
proceeds a new calibration independent of preset measuring cycle. Provided that the quality of
soft water is really below the parameterized threshold value, upon completing the measure-
ment result will be displayed by the luminescent green LED and the current loop comes into
operation.
In case of exceeding the threshold value re-calibration will be done. If this results once again
in an exceeding threshold value, an external threshold value alarm will be signalized accord-
ing to the preset alarm delay at DIP 6 and the measurement will be repeated until a lower de-
viation is discoverable cyclically.
10.3.2 Test of external signaling
A threshold value can be initiated, if the soft water supply will be external and manually
closed, whereby the raw water cannot be flushed out of the measuring chamber by the soft
water. With repeated recognition of the exceeded threshold value the relevant threshold value
relay will be switched after expiration of the delay preset at DIP 6 until a lower deviation is
discoverable again.
A service alarm can be initiated by disconnection of the plug-in connection to the hardness
sensor. Upon a short time the green and red LED will be flashing and the relay for service
alarm will be switched until the sensor will be recognized.
10.3.3 Test sensor performance
If, after short operating time of the sensor, sensor alarm is output (all three LED are flashing),
the sensor quality can checked once more by a further calibration. The calibration can be trig-
gered by a short-term interruption of the power supply. If the sensor alarm appears again, the
sensor must be replaced.
If the operating time of the sensor is significantly below the indicated operating time, the sen-
sor should be sent to the manufacturer for review.
Table of contents
Other Ofs Measuring Instrument manuals
Popular Measuring Instrument manuals by other brands

Tektronix
Tektronix 7T11 instruction manual

Simrad
Simrad SAL R1a Easy Tank user manual
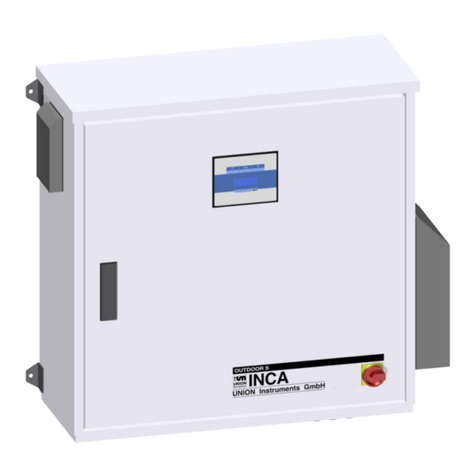
Union Instruments
Union Instruments INCA5051 Translation of the original operating instructions
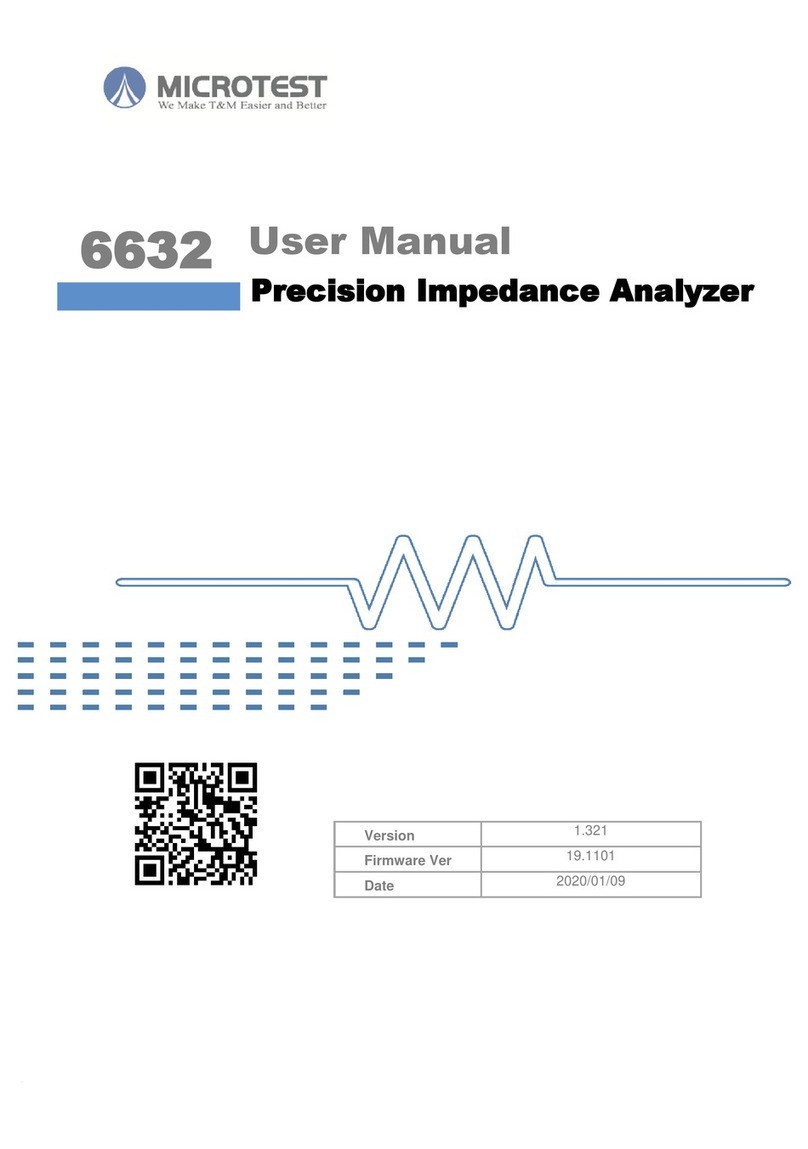
Microtest
Microtest 6632 Series user manual

GREISINGER
GREISINGER GOX 20 operating manual
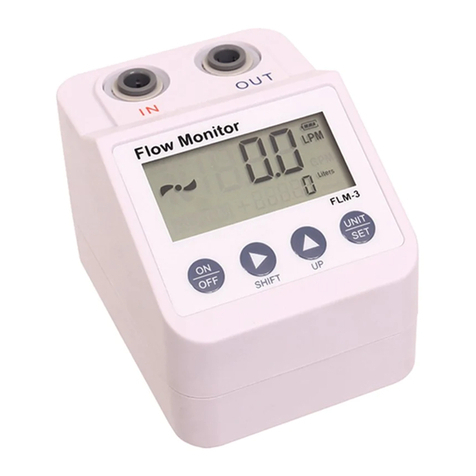
HM Digital
HM Digital FLM-3 user guide